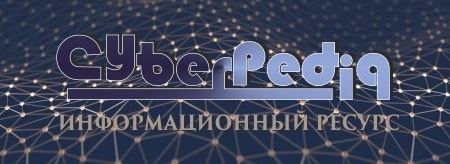
Кормораздатчик мобильный электрифицированный: схема и процесс работы устройства...
История развития пистолетов-пулеметов: Предпосылкой для возникновения пистолетов-пулеметов послужила давняя тенденция тяготения винтовок...
Топ:
Организация стока поверхностных вод: Наибольшее количество влаги на земном шаре испаряется с поверхности морей и океанов...
Характеристика АТП и сварочно-жестяницкого участка: Транспорт в настоящее время является одной из важнейших отраслей народного...
Проблема типологии научных революций: Глобальные научные революции и типы научной рациональности...
Интересное:
Наиболее распространенные виды рака: Раковая опухоль — это самостоятельное новообразование, которое может возникнуть и от повышенного давления...
Берегоукрепление оползневых склонов: На прибрежных склонах основной причиной развития оползневых процессов является подмыв водами рек естественных склонов...
Отражение на счетах бухгалтерского учета процесса приобретения: Процесс заготовления представляет систему экономических событий, включающих приобретение организацией у поставщиков сырья...
Дисциплины:
![]() |
![]() |
5.00
из
|
Заказать работу |
|
|
Оглавление
Введение. 3
1.Исходные данные. 4
2. Описание конструкции свариваемого изделия и условий его эксплуатации. 5
3.Изучение особенности сварки и оценка свариваемости материала изделия. 7
4.Выбор способа сварки. 9
5.Разработка технологического процесса сварки. 17
7.Контроль качества сварочных работ. 24
8.Охрана труда. 29
9.Список использованной литературы. 32
Введение
В современной технике приходится соединять детали из одинаковых и разнородных металлов и сплавов, неметаллов, а также самые различные их сочетания.
Соединения должны быть прочными. Однако к ним нередко предъявляют и специальные требования, ограничивающие допустимое термическое и механическое воздействие сварочного процесса на соединяемые материалы. Иногда задается предельная температура нагрева, ещё не вызывающая неблагоприятных изменений свойств материала, или лимитируется степень пластической деформации и наклепа, которые могут отрицательно влиять на служебные свойства свариваемых материалов, например, полупроводником. В решении этих специальных задач роль сварки давлением очень велика, так как современные её способы позволяют варьировать термические и деформационные параметры процесса в очень широких пределах.
Сварка давлением осуществляется без расплавления соединяемых материалов (в твердом состоянии) или с местным их расплавлением. Расплавленный материал остается в зоне соединения (например, в ядре точнее, сваренной контактным способом) или удаляется из неё (при стыковой сварке оплавлением и радиочастотной сварке). В первом случае, по существу, происходит сварка плавлением, во-втором случае соединение образуется между поверхностями, хотя и оплавленными, но находящимися в твердом состоянии.
|
Физическая природа связей, обуславливающих схватывание и образование прочного соединения при сварке давлением и плавлением одинакова. Однако пути создания условий, необходимых для осуществления таких связей различны. Тип связей, возникающих в соединении, определяется их природой в самих свариваемых материалах. В зависимости от типа связей могут изменяться условия сварки и роль отдельных её параметром. [1]
Исходные данные
Рис.1 – Обечайка
Геометрические характеристики | Материал | ||
δ | D | l | АМг6 |
Программа выпуска 20000 изделий в год. Обечайка предназначена
для транспортировки сыпучих легких материалов. [2]
Выбор способа сварки.
Контактная сварка - это процесс образования соединения в результате нагрева металла проходящим через него электрическим током и пластической деформации зоны соединения под действием сжимающего усилия. ГОСТ 15878-79 «Контактная сварка. Соединения сварные. Конструктивные элементы».
Преимущества контактной сварки перед другими способами:
- Высокая производительность (время сварки одной точки или стыка составляет 0,02... 1,0 с)
- Малый расход вспомогательных материалов (воды, воздуха)
- Высокое качество и надежность сварных соединений при небольшом числе управляемых параметров режима, что снижает требования к квалификации сварщика
Недостатки: относительная сложность оборудования, трудность неразрушающего контроля сварных соединений.
Основные способы контактной сварки - это точечная, шовная (роликовая) и стыковая сварка.
Машины для контактной сварки бывают стационарными, передвижными и подвесными (сварочные клещи). По роду тока в сварочном контуре могут быть машины переменного или постоянного тока от импульса тока, выпрямленного в первичной цепи сварочного трансформатора или от разряда конденсатора. По способу сварки различают машины для точечной, рельефной, шовной и стыковой сварки.
|
Любая машина для контактной сварки состоит из электрической и механической частей, пневмо- или гидросистемы и системы водяного охлаждения (рис. 4).
Электрическая часть включает в себя силовой сварочный трансформатор 1 с переключателем ступеней 2 его первичной обмотки, с помощью которого регулируют вторичное напряжение, вторичный сварочный контур 3 для подвода сварочного тока к деталям, прерыватель 4 первичной цепи сварочного трансформатора 1 и регулятор 5 цикла сварки, обеспечивающий заданную последовательность операций цикла и регулировку параметров режима сварки.
Рис. 4. Типовые схемы машин для контактной точечной (а), шовной (б) и стыковой (в) сварки:
1 - трансформатор; 2 - переключатель ступеней; 3 - вторичный сварочный контур; 4 - прерыватель первичной цепи; 5 - регулятор; 6 - привод сжатия; 7- привод зажатия деталей; 8 - привод осадки деталей; 9 - привод вращения роликов; 10- аппаратура подготовки; 11 - орган включения
Механическая часть состоит из привода сжатия 6 точечных и шовных машин, привода 7 зажатия деталей и привода 8 осадки деталей стыковых машин. Шовные машины снабжены приводом 9 вращения роликов.
Пневмогидравлическая система состоит из аппаратуры 10 подготовки (фильтры, лубрикаторы, которые смазывают движущиеся части), регулирования (редукторы, манометры, дросселирующие клапаны) и подвода воздуха к приводу 6 (электропневматические клапаны, запорные вентили, краны, штуцера).
Система водяного охлаждения включает в себя штуцера разводящей и приемной гребенок, охлаждаемые водой полости в трансформаторе 1 и вторичном контуре 3, разводящие шланги, запорные вентили и гидравлические реле, отключающие машину, если вода отсутствует или ее мало.
Все машины снабжены органом включения 11. У точечных и шовных машин это ножная педаль с контактами, у стыковых - это комплект кнопок. С органов управления поступают команды на сжатие "С" электродов или зажатие "3" деталей, на включение "Т" и отключение "О" сварочного тока, на вращение "В" роликов, на включение "а" регулятора цикла сварки. Эти команды отрабатываются соответствующими блоками машины, обеспечивая выполнение операций цикла сварки.
Кроме универсальных применяются специальные машины, приспособленные для сварки конкретных конструкций и типов размеров изделий. Примером могут служить машины для контактной точечной сварки кузовов автомобилей, встроенные в автоматические линии, машины для стыковой сварки оплавлением продольных швов труб в прокатном производстве.
|
Электроды в контактной сварке служат для замыкания вторичного контура через свариваемые детали. Кроме этого при шовной сварке электроды-ролики перемещают свариваемые детали и удерживают их в процессе нагрева и осадки.
Важнейшая характеристика электродов - стойкость, способность сохранять исходную форму, размеры и свойства при нагреве рабочей поверхности до температуры 600○ С и ударных усилиях сжатия до 5 кг/мм2. Электроды для точечной сварки - это быстроизнашивающийся сменный инструмент сварочной машины. Для изготовления электродов используют медь и жаропрочные медные сплавы - бронзы. Это может быть хромоциркониевая бронза БрХЦрА; кадмиевая БрКд1; хромистая БрХ; бронза, легированная никелем, титаном и бериллием БрНТБ или кремний-никелевая бронза БрКН-1-4. Последние две бронзы обладают повышенной износостойкостью, из них можно изготавливать электроды-губки стыковых машин. Материалы для электродов должны обладать также высокой электро- и теплопроводностью, чтобы их нагрев в процессе сварки был меньше. Температура разупрочнения бронз не превышает 0,5 их температуры плавления, а рабочая поверхность электрода нагревается до 0,6 ТПЛАВ. При таких условиях электродные бронзы относительно быстро разупрочняются. Повысить износостойкость электродов можно, используя технологические факторы. Сварку алюминиевых и магниевых сплавов лучше производить на конденсаторных машинах, а не на машинах переменного тока. Вместо механической зачистки нужна химическая очистка поверхности, травление и пассивация. Расстояние l от рабочей поверхности до дна охлаждающего канала не должно превышать 10...12 мм, увеличение его до 15 мм повышает износ электрода в 2 раза. При сварке черных металлов стойкость электродов можно повысить в 3...4 раза только за счет сферической заточки электрода и снижения темпа сварки до 40...60 точек в минуту.
|
Электрод должен иметь минимальную массу, удобно и надежно устанавливаться на сварочной машине. Диаметр D должен обеспечивать устойчивость электрода против изгиба при сжатии его усилием сварки, а также возможность захвата инструментом для снятия. Внутренний диаметр должен обеспечивать ввод трубки с охлаждающей водой и выход воды, обычно d0 = 8 мм. Длина конусной части для крепления электрода в свече машины l1 <= 1,2 D. Угол конусности 1:10 при D <25 мм и 1: 5 при D> 32 мм. Диаметр рабочей части электрода выбирают в зависимости от толщины кромок свариваемых деталей dЭ = 3S. Стойкость электродов с наружным посадочным конусом обычно не превышает 20 000 сварок.
Электроды-ролики шовных машин имеют форму дисков. Ширина рабочей поверхности ролика В и его толщина Н зависят от толщины S свариваемой детали.
При подготовке поверхностей к контактной сварке должны выполняться три основных требования: в контактах электрод-деталь должно быть обеспечено как можно меньшее электрическое сопротивление КЭ-Д —> min), в контакте деталь-деталь сопротивление должно быть одинаковым по всей площади контакта. Сопрягаемые поверхности деталей должны быть ровными, плоскости их стыка при сварке должны совпадать.
Выбор конкретного способа подготовки поверхностей определяется материалом деталей, исходным состоянием их поверхностей, характером производства. Для штучного и мелкосерийного производства необходимо предусмотреть операции правки, рихтовки, обезжиривания, травления или зачистки, механической обработки. В условиях крупносерийного и массового производства, где обеспечивается высокое качество исходных материалов в заготовительном и штампопрессовом производствах, подготовку поверхностей перед сваркой можно не делать. Исключение составляют детали из алюминиевых сплавов, требующих обработки поверхности не ранее чем за 10 ч до сварки.
Критерием качества подготовки поверхности является величина контактных сопротивлений RЭ-Д и RД-Д. Для их измерения детали зажимают между электродами сварочной машины, но сварочный ток не включают. Сопротивление измеряют микроомметром при помощи щупов. Для сталей сопротивление более 200 мкОм свидетельствует о плохом качестве поверхности. Высокое RЭ-Д приводит к перегреву электродов и подплавлению поверхности деталей, вследствие чего происходит наружный и внутренний выплеск металла и образуется чрезмерная вмятина под электродами.
Шовная сварка – способ, при котором детали, образующие нахлесточные соединения, свариваются в месте соприкосновения. При перекрытии точек образуется прочноплотный шов, а без перекрытия – прочный шов или ряд точек. Шовной контактной сваркой обычно соединяют детали толщиной 0,5–6 мм. Основной тип соединения – нахлесточное. При его выборе следует учитывать свариваемость материала, номинальные размеры ядра точек, шаг между ними и величину нахлестки. Технологический процесс изготовления конструкций способом шовной контактной сварки состоит из следующих операций: предварительная сборка, подготовка поверхности, окончательная сборка, прихватка, сварка точек, антикоррозионная защита, правка и механическая доработка. В зависимости от конкретных условий некоторые операции могут быть исключены.
|
При шовной сварке образование соединения происходит по схеме,
состоящей из трех этапов I–III (рис. 4.1).
Рис. 4.1. Этапы образования соединения при шовной сварке
Первый этап начинается с момента обжатия деталей, вызывающего пластическую деформацию микронеровностей в контактах электрод-деталь. Последующее включение тока и нагрев металла облегчают выравнивание микрорельефа, разрушение поверхностей пленок и формирование электрического контакта. Нагретый металл деформируется преимущественно в зазор между деталями, и образуется уплотняющий поясок.
Второй этап характеризуется расплавлением металла и образованием ядра. По мере прохождения тока ядро растет до максимальных размеров – по высоте и диаметру. При этом происходит перемешивание металла, удаление поверхностных пленок и образование металлических связей в жидкой фазе. Продолжается процесс пластической деформации и тепловое расширение металла. К концу этого этапа отмечается почти полная осадка рельефа.
Третий этап начинается с выключения тока, сопровождающегося охлаждением и кристаллизацией металла. Образуется общее для деталей литое ядро. При охлаждении уменьшается объем металла и возникают остаточные напряжения. Для снижения уровня этих напряжений и предотвращения усадочных трещин и раковин требуются значительные усилия.
При шовной сварке за счет теплопередачи от предыдущих точек процессы пластической деформации при сварке второй и последующих точек на всех трех этапах облегчается. Снижается также скорость кристаллизации ядра, что приводит к уменьшению остаточных напряжений.
Конструктивные элементы сварного соединения при шовной сварке показаны на рис. 4.2.
Рис. 4.2. Конструктивные элементы соединений при шовной сварке:
d – диаметр ядра; h (h1) – величина проплавления; g (g1) – глубина вмятины от электрода; tш – шаг между точками – расстояние между центрами точек; U – величина нахлёстки
Важнейшим условием получения качественного шовного сварного соединения является выбор оптимального режима сварки.
Рекомендуемые режимы, как правило, требуют корректировки в конкретных условиях.
Нарушение параметров технологического процесса приводит к образованию следующих групп дефектов:
· изменение размеров ядра или полное его отсутствие (непровары);
· выплески (выбросы) металла из зоны контактов деталей с деталями и деталей с электродами;
· нарушение сплошности металла ядра или околошовной зон (трещины, раковины, рыхлоты);
· переход металла электродов на поверхность сварных соединений;
· изменение структуры и свойств металла ядра и околошовной зоны.
Для своевременного обнаружения и принятия технических и организационных мер по предупреждению дефектов должен проводиться систематический контроль всех звеньев производства сварной конструкции, а именно: на стадии проектирования, а также при выполнении вспомогательных операций, собственно сварочных операций и сварочного оборудования.
Шовная сварка, выполняемая при непрерывном движении деталей и непрерывном протекании сварочного тока, называется непрерывной. Такую сварку редко применяют из-за сильного перегрева поверхности деталей, контактирующей с роликами. Наибольшее распространение имеет прерывистая шовная сварка, при которой детали перемещаются непрерывно, а ток включается и выключается на определенные промежутки времени и при каждом включении (импульсе) тока образуется единичная литая зона. Перекрытие литых зон, необходимое для герметичности шва, достигается при определенном соотношении скорости вращения роликов и частоты импульсов тока.
Применяют также шаговую сварку, при которой детали перемещаются прерывисто (на шаг), а сварочный ток включается только во время их остановки, что улучшает охлаждение металла в контактах ролик - деталь по сравнению с непрерывным движением свариваемых деталей. Шовная сварка в большинстве случаев производится с наружным водяным охлаждением, что также уменьшает перегрев внешних слоев металла.
Разнообразные виды шовной сварки, встречаемые на практике, в основном различаются способом подвода сварочного тока (односторонний или двусторонний) и расположением роликов относительно свариваемых деталей (рис. 5). Двусторонняя шовная сварка аналогична двусторонней точечной (рис. 5, а-е). Вместо одного из роликов может быть применена оправка, плотно контактирующая с внутренней деталью (рис. 5, г). Для сварки неподвижных деталей кольцевым швом на плоскости служит верхний ролик, который вращается вокруг своей оси, а также вокруг оси шва (рис. 5)
Рис. 5. Способы шовной сварки
Нижняя деталь контактирует с электродом, имеющим форму чашки. Иногда свариваемые детали устанавливают на медную шину; при этом подвод тока может быть двусторонним или односторонним. При сварке на шине возможны варианты подвижной (рис. 4, ж) и неподвижной (рис.4, з) шин, когда два ролика, к которым подведен ток, вращаются вокруг своих осей и катятся по деталям. При односторонней шовной сварке, как и при точечной, наблюдается шунтирование тока в деталь, контактирующую с роликами.
Рис.6. Циклограммы шовной сварки
а - непрерывное выключение тока; б - импульсное включение тока; I - сварочный ток; Р - давление; S - перемещение роликов; t - время.
Шовную сварку применяют при изготовлении различных емкостей с толщиной стенки 0,3 - 3 мм, где требуются герметичные швы - бензобаки, трубы, бочки, сильфоны и др. [2]
Охрана труда.
При установке, монтаже и эксплуатации контактных сварочных машин должны соблюдаться все нормы и правила, необходимые для безопасной работы сварщика и наладчика. При невыполнении этих правил возможны различные случаи травматизма: поражение электрическим током; повреждения рук механизмами сжатия и зажимными устройствами; поражение органов дыхания газами, парами и пылью; ожоги брызгами металла и нагретыми деталями; ушибы тяжелыми деталями и порезы острыми краями металла.
Сварочный контур машины не опасен в смысле возможности поражения электрическим током, так как напряжение на концах вторичного витка трансформатора не превышает 36 в. Такое напряжение недостаточно для того, чтобы через тело человека прошел опасный ток, величина которого превышает 0,1 А. Ток, который может вызвать травму, появляется в сварочном контуре только при повреждении (пробое) первичной обмотки, когда вторичный виток или корпус машины (электрически соединенный со сварочным контуром) оказываются под напряжением питающей сети (127, 220, 380 в).
Для исключения поражения электрическим током сварщику и наладчику необходимо выполнять следующие правила:
1) систематически проверять надежность заземления станины и одного конца вторичного витка сварочного трансформатора;
2) не допускать попадания воды, масла, грязи, пыли и металлических предметов на обмотки трансформатора и вспомогательных электрических устройств;
3) запрещается производить проверку, наладку и ремонт электрических устройств, находящихся под напряжением питающей сети; эти работы выполняет только цеховой электрик;
4) ступени мощности переключать только при отключенной сети; запрещается открывать дверки машины при включенном напряжении;
5) следить за тем, чтобы изоляция питающих проводов и рукояток переключателя не была повреждена;
6) пользоваться резиновым ковриком или сухой деревянной решеткой, находящимися перед машиной;
7) ключи от регулятора времени и прерывателя должны находиться у наладчика или цехового электрика.
Следует помнить, что в шовных машинах, а также в стыковых с моторным приводом особую опасность представляют электродвигатели, питающиеся от сети с напряжением 220 или 380 в, поэтому их необходимо тщательно защищать от попадания воды, масла и брызг расплавленного металла.
Усилие сжатия электродов точечных и шовных машин достигает большой величины (несколько сот килограммов, а иногда и несколько тонн). Значительные усилия развивают и зажимные механизмы стыковых машин. При случайном нажатии кнопки или педали рука сварщика или наладчика может быть зажата между электродами, что вызовет тяжелую травму. Особую опасность представляют пневматические и гидравлические механизмы сжатия.
Для предотвращения повреждения рук при работе на контактных машинах сварщику и наладчику необходимо выполнять следующие правила:
1) следить за исправностью механизмов сжатия и зажимных устройств, не допускать самопроизвольного их срабатывания;
2) выполнять зачистку, заправку и смену электродов только при выключенной машине;
3) не смазывать части машины на ходу;
4) не допускать присутствия посторонних лиц около машины во время работы;
5) своевременно устранять утечки сжатого воздуха и масла из пневматической и гидравлической систем;
6) при остановке машины на продолжительное время перекрывать воздушный вентиль.
При точечной и шовной сварке хорошо очищенных стальных деталей в окружающую атмосферу не выделяются какие-либо вредные пары или газы. При сварке на правильно подобранном режиме также нет опасности загрязнения воздуха металлической пылью. Поэтому устройств местных отсосов воздуха, как правило, не требуется.
Однако на сварку часто подаются детали из горячекатаной стали, арматурный пруток, а также штампованные детали, на поверхности которых имеются масло и эмульсия. Точечная и шовная сварка применяются и для соединения деталей из стали с антикоррозионными покрытиями (свинцом, оловом, цинком и др.) и из цветных металлов. При сварке таких деталей выделяются пары и пыль, имеющие токсические свойства.
При шовной сварке ожог может произойти во время прикосновения к неостывшему шву, а также от горячей воды, стекающей в поддон с охлаждаемого изделия.
Для предупреждения получения ожогов сварщик должен пользоваться рукавицами и специальным инструментом (клещами или щипцами) при снятии горячих деталей. От ожогов глаз брызгами металла применяются защитные очки с простыми прозрачными стеклами. В комплект спецодежды должен входить брезентовый, кожаный или дерматиновый фартук — не промасленный и не пропитанный горючими жидкостями.
Ушибы тяжелыми деталями или порезы острыми краями их возможны в той же степени, как и при работе на любом металлообрабатывающем станке. Необходимо учитывать, что при сварке сложных крупногабаритных узлов некоторой опасности подвергаются рабочие, выполняющие операции на рядом расположенных станках. Поэтому соседние машины должны быть разделены ограждениями или достаточно широкими проходами. Для складирования и перемещения крупногабаритных изделий и деталей должны быть предусмотрены специальные устройства.
Все сварщики и наладчики контактных машин должны обязательно пройти инструктаж по технике безопасности, охватывающий как общие условия работы на данном предприятии (в цехе), так и условия эксплуатации современных контактных машин. [17]
Список использованной литературы.
1. Гельман, А. С. Основы сварки давлением / А. С. Гельман. – Москва: Машиностроение, 1970. – 312 с.
2. Ильященко, Д. П. «Технология и оборудование сварки давлением» Учебное пособие. Лабораторный практикум / Д.П. Ильященко. Юргинский технологический институт. − Томск: Изд-во Томского политехнического университета, 2013. – 151 с.
3. Промформа. Детали, узлы, аппараты для нефтехимии. [Электронный ресурс] / 24 января 2016. – Режим доступа: http://www.promforma.ru/shells
4. Agro shop "Fermash". Транспортировка сыпучих материалов / 24 января 2016. – Режим доступа: http://fermash.com.ua/agrotehnologii/transportirovka-sypuchih-materialov/
5. Справочник химика 21. Химия и химическая технология / 24 января 2016. – Режим доступа: http://chem21.info/info/825470/
6. Renby Limited. RENBY LTD PRODUCT RANGE BROCHURE / 24 января 2016. – Режим доступа: https://www.renby.co.uk/Renby-Ltd-Brochures/renby-ltd-brochures-resources.html
7. DMN-WESTINGHOUSE. Системы пневмотранспорта сыпучих материалов / 24 января 2016. – Режим доступа: http://www.dmn-rus.com/publikatsii/sistemy-pnevmotransporta-sypuchikh-materialov.html
8. СпецМеталл. Алюминий АМг6 / 24 января 2016. – Режим доступа: http://nfmetall.ru/articles/31.html
9. ГОСТ 4784-97. Алюминий и сплавы алюминия деформированные. – Минск: Межгосударственный совет по стандартизации, метрологии и сертификации, 1997. – 32 с.
10. «М-Комплект». Сварка алюминия и его сплавов / 24 января 2016. – Режим доступа: http://metmk.com.ua/1101spr_alum.php
11. Галактионов, А. Т. Электросварщик. Изд-е 2 / А. Т. Галактионов, И.Р. Пацкевич, Г. Д. Стадников. – Москва: Государственное научно-техническое издательство машиностроительной литературы 1954. – 298 с.
12. Николаев, Г. А. Сварка в машиностроении: Справочник в 4-х т./Редкол.: С24 Г.А.Николаев (пред.) и др. – Москва: Машиностроение, 1978. – Т. 1/Под ред. Н.А. Ольшанского. 1978. 504с.
13. Справочник по цветным металлам. Хромовая бронза / 26 января 2016.– Режим доступа: http://libmetal.ru/bronze/chrombronze.htm
14. Куликов В.П. Технология и оборудования сварки давлением. Учебное пособие / В.П. Куликов. – Могилев: ГУ ВПО «Белорусско-Российский университет», 2011. – 19 с.
15. Патон Е.Б. Машиностроение. Энциклопедия в сорока томах. Том 6 Оборудование для сварки / Е.Б. Патон - Москва: Машиностроение, 1999. – 496 с.
16. Древний мир металла. Контроль качества контактной сварки /28 января 2016. – Режим доступа: http://www.drevniymir.ru/dug59.html
17. Древний мир металла. Техника безопасности при работе на контактных машинах /28 января 2016. – Режим доступа: http://www.drevniymir.ru/dug19.html
Оглавление
Введение. 3
1.Исходные данные. 4
2. Описание конструкции свариваемого изделия и условий его эксплуатации. 5
3.Изучение особенности сварки и оценка свариваемости материала изделия. 7
4.Выбор способа сварки. 9
5.Разработка технологического процесса сварки. 17
7.Контроль качества сварочных работ. 24
8.Охрана труда. 29
9.Список использованной литературы. 32
Введение
В современной технике приходится соединять детали из одинаковых и разнородных металлов и сплавов, неметаллов, а также самые различные их сочетания.
Соединения должны быть прочными. Однако к ним нередко предъявляют и специальные требования, ограничивающие допустимое термическое и механическое воздействие сварочного процесса на соединяемые материалы. Иногда задается предельная температура нагрева, ещё не вызывающая неблагоприятных изменений свойств материала, или лимитируется степень пластической деформации и наклепа, которые могут отрицательно влиять на служебные свойства свариваемых материалов, например, полупроводником. В решении этих специальных задач роль сварки давлением очень велика, так как современные её способы позволяют варьировать термические и деформационные параметры процесса в очень широких пределах.
Сварка давлением осуществляется без расплавления соединяемых материалов (в твердом состоянии) или с местным их расплавлением. Расплавленный материал остается в зоне соединения (например, в ядре точнее, сваренной контактным способом) или удаляется из неё (при стыковой сварке оплавлением и радиочастотной сварке). В первом случае, по существу, происходит сварка плавлением, во-втором случае соединение образуется между поверхностями, хотя и оплавленными, но находящимися в твердом состоянии.
Физическая природа связей, обуславливающих схватывание и образование прочного соединения при сварке давлением и плавлением одинакова. Однако пути создания условий, необходимых для осуществления таких связей различны. Тип связей, возникающих в соединении, определяется их природой в самих свариваемых материалах. В зависимости от типа связей могут изменяться условия сварки и роль отдельных её параметром. [1]
Исходные данные
Рис.1 – Обечайка
Геометрические характеристики | Материал | ||
δ | D | l | АМг6 |
Программа выпуска 20000 изделий в год. Обечайка предназначена
для транспортировки сыпучих легких материалов. [2]
Описание конструкции свариваемого изделия и условий его эксплуатации.
Обечайка — деталь цилиндрической формы, в сечении представляет собой кольцо, с торцов не заглушена. Изготовление обечаек происходит методом вальцовки на холодную, либо на горячую сталь из сварной или несварной заготовки. Существуют методы производства обечаек литьем полуобечаек и последующей сваркой, центробежным литьем и т.д. При этом метод вальцовки из листовой заготовки в большинстве случаев наиболее экономичен.
Вальцовка обечаек осуществляется в вальцах — большие толщины деформируются с предварительным подогревом с последующей сваркой и термообработкой.
Обечайка является главным составным элементом корпуса, это наиболее материалоемкий и ответственный узел любого аппарата. Обечайки используются если изготавливается или ремонтируется корпуса сосудов и аппаратов, котлов и емкостей, если прокладываются или монтируются технологические трубопроводы. Колонное оборудование, а также нестандартные трубопроводы изготавливают из обечаек, сваривая их поперечными кольцевыми швами.
Посредством калибровки обечайки после сварки достигается высокая точность геометрических размеров изделия.
Применяемость обечаек повсеместна в машиностроении. Обечайками можно назвать патрубки, переходы от одного диаметра к другому (конические переходы), переходы на разные толщины (переходные кольца), трубы стальные электросварные. [3]
Обечайка, в данном курсовой работе, предназначена для транспортировки сыпучих легких материалови особыми требованиями к эксплуатации, не обладает. Она должна обеспечивать достаточную жесткость и прочность под нагрузкой собственного веса и веса сыпучих материалов.
Примеры сыпучих материалов:
1. песок и мел;
2. цемент, пыли различных материалов;
3. древесные опилки и стружка;
4. минеральный порошок, мраморная пыль;
5. сода, сахар, тальк, мука и др. [4]
Транспортировка сыпучих материалов (особенно таких, как технический углерод (сажа, копоть)) вызывает большие трудности, поскольку большинство их характеризуется повышенной текучестью, большой проникающей способностью и способностью оседать на внутренних поверхностях транспортного оборудования.
Часто устройства транспортировки сыпучих материалов оснащают электронными системами контроля. Например, в одном из устройств под лентой транспортера устанавливается датчик сопротивления, соединенный с тахогенератором. Одновременно с помощью сигнальной системы или тахогенератора измеряется скорость движения ленты. Сигналы, пропорциональные весу и скорости, подаются в измерительный блок, состоящий из механического интегратора и счетчика, фиксирующего суммарный вес прошедшего по конвейеру материала на цифровой шкале. [5]
Транспортировку сыпучих материалов по желобам или трубам можно осуществлять:
- механическим путем
- с помощью потока газа (пневмотранспорт)
- с помощью жидкости
- с помощью пены
Рис.2 – Транспортировка сыпучих материалов механическим путем [6]
Рис. 3 - Транспортировка сыпучих материалов пневмотранспортом [7]
|
|
Эмиссия газов от очистных сооружений канализации: В последние годы внимание мирового сообщества сосредоточено на экологических проблемах...
Состав сооружений: решетки и песколовки: Решетки – это первое устройство в схеме очистных сооружений. Они представляют...
Археология об основании Рима: Новые раскопки проясняют и такой острый дискуссионный вопрос, как дата самого возникновения Рима...
История создания датчика движения: Первый прибор для обнаружения движения был изобретен немецким физиком Генрихом Герцем...
© cyberpedia.su 2017-2024 - Не является автором материалов. Исключительное право сохранено за автором текста.
Если вы не хотите, чтобы данный материал был у нас на сайте, перейдите по ссылке: Нарушение авторских прав. Мы поможем в написании вашей работы!