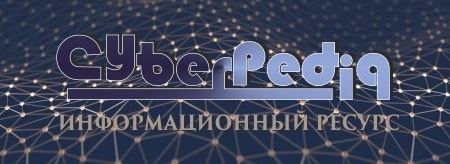
Особенности сооружения опор в сложных условиях: Сооружение ВЛ в районах с суровыми климатическими и тяжелыми геологическими условиями...
История развития хранилищ для нефти: Первые склады нефти появились в XVII веке. Они представляли собой землянные ямы-амбара глубиной 4…5 м...
Топ:
Основы обеспечения единства измерений: Обеспечение единства измерений - деятельность метрологических служб, направленная на достижение...
Генеалогическое древо Султанов Османской империи: Османские правители, вначале, будучи еще бейлербеями Анатолии, женились на дочерях византийских императоров...
Проблема типологии научных революций: Глобальные научные революции и типы научной рациональности...
Интересное:
Как мы говорим и как мы слушаем: общение можно сравнить с огромным зонтиком, под которым скрыто все...
Отражение на счетах бухгалтерского учета процесса приобретения: Процесс заготовления представляет систему экономических событий, включающих приобретение организацией у поставщиков сырья...
Финансовый рынок и его значение в управлении денежными потоками на современном этапе: любому предприятию для расширения производства и увеличения прибыли нужны...
Дисциплины:
![]() |
![]() |
5.00
из
|
Заказать работу |
|
|
РАЗВИТИЕ ТЕПЛОВОЗОСТРОЕНИЯ
Работа над созданием дизельных локомотивов началась еще в конце прошлого века такими видными русскими учеными, как В.И.Гриневецкий, Я.М.Гаккель, Ю.В.Ломоносов, А.Н.Шелест, К.А.Шишкин и др., однако до 1917г. были разработаны только проекты тепловозов и дизелей для них.
По сравнению с паровозом тепловоз не требует большого количества воды, имеет большой пробег между экипировками, а в отличие от электровоза тепловоз - локомотив автономный, т.е. не требует сооружения вдоль дороги подстанций и устройств контактной сети.
Первый в мире тепловоз, построенный по проекту профессора Я.М.Гаккеля, 7 ноября 1924г. вышел на линию Октябрьской ж.д. и совершил свой первый рейс до Обухова и обратно. Этот тепловоз получил название Щэл1, так как по мощности был одинаков с паровозом серии Щ (736 кВт). Тепловоз имел экипаж тележечного типа, электрическую передачу и опорно-осевую подвеску тяговых двигателей.
Постройка тепловозов была организована на Коломенском заводе, электрооборудование поставляли Московский завод «Динамо» и Харьковский электромеханический завод.
С 1930г. по 1937г. Коломенский завод построил несколько десятков тепловозов «Оэл-6; Оэл-7; Ээл-5; Ээл-8; ВМ», которые работали на Ашхабадской дороге, где эксплуатация паровозов была затруднена.
В марте 1937г. Народный комиссариат путей сообщения прекратил заказы на тепловозы, заменив их паровозами.
Сразу же после окончания Великой отечественной войны на базе Харьковского завода транспортного машиностроения началось строительство тепловозов.
В 1947г. завод построил свои первые тепловозы серии ТЭ1.
В 1948г. был создан двухсекционный тепловоз ТЭ2.
С 1955г. ХЗТМ серийно выпускал тепловозы ТЭЗ.
|
Особенно большое развитие тепловозная тяга получила, начиная с 1956г., когда было признано необходимым, заменить паровозы тепловозами и электровозами.
С 1957г. тепловозы ТЭЗ выпускались серийно тремя заводами ХЗТМ; ВТЗ; и КТЗ.
По мере расширения опыта заводы специализировались.
В настоящее время ВТЗ выпускает в основном магистральные грузовые тепловозы.
Коломенский завод выпускает пассажирские тепловозы.
Брянский и Людиновский — маневровые тепловозы.
Муромский завод - промышленные тепловозы.
Калужский завод выпускает маневрово-промышленные тепловозы.
Камбарский завод выпускает тепловозы для узкоколейных дорог.
В начале 60-х годов были разработаны проекты тепловозов мощностью 2206 кВт в секции с дизелем 10Д100. Тепловозы серии ТЭ10 различных модификаций составляли основу грузового тепловозного парка. На Коломенском заводе был налажен выпуск пассажирских тепловозов ТЭП60.
В 80-е годы тепловозостроение ориентировалось на использование четырехтактных дизелей Д49, которые выпускались на КТЗ и были впервые установлены на тепловозе 2ТЭ116. С использованием этих дизелей освоены в производстве тепловозы последнего поколения 2ТЭ121 и ТЭП70 мощностью 3000 кВт в секции.
В 1984г. на Луганском тепловозостроительном заводе построены первые опытные образцы тепловоза ТЭ136 мощностью 4400 кВт с 20-цилиндровым дизелем Д49. На КТЗ разработан тепловоз ТЭП80 такой же мощности.
В 1974г. на Людиновском заводе разработан тепловоз ТЭМ7 с мощностью 1470 кВт который предназначен для маневрово-вывозной и горочной работ.
Специалистами Коломенского завода разрабатывается конструкция четырехтактного тепловозного дизеля большей размерности (диаметр цилиндра и ход поршня составляют 320 мм), что позволит получить мощность порядка 4500 кВт в 16-ти цилиндрах. Но основе нового дизеля на Луганском тепловозостроительном заводе создается тепловоз 2ТЭ126.
ЭКИПАЖНАЯ ЧАСТЬ ТЕПЛОВОЗА
К экипажной части тепловоза относятся: главная рама с ударно-сцепными приборами, кузов, тележки с колёсными парами, буксами, рессорным подвешиванием и опорно-возвращающими устройствами.
|
Если кузов и кабина машиниста, установленные на главной раме тепловоза, не воспринимают никаких нагрузок, то тепловоз называют с несущей рамой.
Если кузов и рама составляют единую цельносварную конструкцию, при которой некоторая часть статической и динамической нагрузок воспринимается кузовом, то тепловоз называют с несущим кузовом.
Оборудование на главной раме должно быть размещено таким образом, чтобы на каждую тележку приходилась одинаковая нагрузка. Одинаковую нагрузку должна нести и каждая колёсная пара. Отклонение допускается не более ±3%.
Связь тележек с главной рамой тепловоза должна обеспечивать поворот их в плане на угол 3-40 градуса, для обеспечения прохождения тепловоза в кривых участках пути.
ГЛАВНАЯ РАМА ТЕПЛОВОЗА
Рама тепловоза служит для размещения на ней дизель - генераторной установки, вспомогательного оборудования, кабины машиниста, а также ударно-тяговых устройств. Кроме статической нагрузки рама также испытывает тяговые и тормозные усилия, ударные нагрузки при сцеплении с составом и ведении поезда.
По конструкции рамы тепловозов имеют незначительные отличия, обусловленные расположением оборудования. У рам основными силовыми элементами являются продольные хребтовые балки.
По концам балки связаны литыми стяжными ящиками, в которых размещаются поглощающие аппараты. Для придания раме жесткости, в неё вварены поперечные перегородки.
Сверху и снизу рама обшита настильными листами с вырезами для монтажа оборудования.
Снизу рамы на специальных коробчатых усилениях приварены два шкворня, представляющие собой стальные отливки. На шкворни насажены и приварены стальные сменные втулки.
Вокруг каждого шкворня расположены боковые опоры рамы. Места расположения опор также имеют жесткие коробчатые усиления.
ЧЕЛЮСТНЫЕ ТЕЛЕЖКИ
БЕСЧЕЛЮСТНЫЕ ТЕЛЕЖКИ
Рама тележки сварная. Ее боковины, поперечные и концевые балки имеют коробчатое сечение. Одна из концевых балок усилена, что связано с расположением тяговых электродвигателей «гуськом». На эту балку передается часть массы ТЭД, а также реактивный момент при его работе. Вторая концевая балка изогнута в средней части для удобства демонтажа поглощающего аппарата автосцепки.
|
К поперечным средним балкам приварена продольная литая шкворневая балка. В средней части балка имеет прямоугольное шкворневое гнездо, подвижное в поперечном направлении. В боковых стенках шкворневой балки имеются отверстия для упоров пружин шкворневого узла.
К нижним листам боковин приварены литые кронштейны буксовых поводков.
Снаружи к боковинам приварены через подкладки корпуса фрикционных гасителей колебаний, кронштейны тормозных цилиндров и имеются сквозные овальные отверстия, усиленные полыми вставками, для прохода горизонтальных рычагов тормозной рычажной передачи.
ЧЕЛЮСТНАЯ БУКСА
Буксы служат для передачи статической нагрузки на шейки осей колесных пар, а также тяговых и тормозных усилий от колесных пар на раму тележки, при движении тепловоза. Кроме того буксы воспринимают боковые усилия, особенно в кривых участках пути.
Сборка буксы осуществляется в следующей последовательности. На шейку оси в горячем состоянии напрессовывают лабиринтное и два внутренних кольца подшипников. Последние разделены дистанционным кольцом. Дополнительно эти кольца фиксируют стопорным кольцом.
Далее корпус буксы с прикрепленной к нему задней крышкой и установленными в него наружными кольцами подшипников с роликами и дистанционным кольцом надевают на шейку оси.
Спереди к корпусу буксы болтами крепится крышка, к которой через регулировочные прокладки крепится осевой упор с бронзовой или капроновой наделкой.
От износа корпус буксы защищен наличниками из износостойкой стали.
Для смазки роликовых подшипников применяют консистентную смазку «БУКСОЛ», в количестве 1,4 кг на одну буксу.
Для смазывания осевого упора применяют дизельное масло, подаваемое войлочным фитилем. Для смазки наличников применяется осевое масло, находящееся в резервуарах, в верхней части буксы.
Буксы крайних колесных пар имеют пружину, расположенную между упором и его крышкой. Пружина предварительно сжата усилим 1500 кг и допускает перемещение упора на 10 – 11 мм. Свободный разбег равен 1,5 - 2 мм.
|
Средние оси имеют жесткие упоры, а их свободный разбег равен 14 мм на сторону.
Рессорное подвешивание предназначено для смягчения толчков и ударов, возникающих при движении тепловоза, для уменьшения воздействия на путь, а также для выравнивания нагрузок между отдельными колесными парами.
Рессорное подвешивание состоит из двух симметрично расположенных с обеих сторон тележки самостоятельных групп. Каждая группа включает в себя: две листовые рессоры, шесть балансиров и шесть винтовых пружин, соединенных между собой подвесками и валиками.
Листовая рессора собрана из восьми листов полосовой стали, которые в средней части стянуты хомутом, надетым на них в горячем состоянии. Два нижних листа рессоры называются коренными, а остальные – наборными.
Рессоры опираются на опоры рессор, которые соединяются при помощи валиков с подвесками, с балансирами. Для фиксации концов рессоры опоры имеют выступы, а коренные листы соответственно углубления. Хомут рессоры при помощи проушин соединяется валиком с опорой пружин.
Балансиры представляют собой стальные полосы толщиной 25 мм закругленной формы. На каждую буксу опираются два балансира, расположенные один снаружи тележки, а другой внутри. В средней части балансир имеет выемку, которой он опирается на корпус буксы через шарообразную опору.
Балансиры, расположенные на концах тележки соединены с концевыми пружинами. Последние с резиновыми амортизаторами подвешиваются на стержнях, имеющих головки.
Через головки проходят валики, соединяющие стержни с балансирами. Передача нагрузки от рамы тележки на колесные пары происходит через резиновые амортизаторы на винтовые пружины и на их опору. Затем усилие передается через валик и хомут на рессору и далее через балансиры на концевые пружины.
КОЛЁСНЫЕ ПАРЫ
ТЯГОВЫЙ РЕДУКТОР
Опорно-возвращающее устройство служит для передачи вертикальной нагрузки на тележки, для удержания тележек в нормальном положении, при котором их продольная ось совпадает с продольной осью рамы и кузова тепловоза, и для возвращения тележек в это положение, при выходе тепловоза из кривого участка пути.
На боковинах рамы тележки установлена четыре комбинированные опоры, состоящие каждая из двух ступеней: нижняя жесткая ступень - роликовая опора качения, а верхняя упругая - блок, содержащий семь резинометаллических элементов.
Для равенства нагрузок от колесных пар на рельсы передние опоры расположены вокруг шкворня на радиусе 1632 мм, а задние - на радиусе 1232 мм.
Нижняя ступень состоит из стального корпуса, в котором имеются нижняя и верхняя опорные плиты. Между плитами помещены два ролика, соединенные обоймами.
|
Поверхности опорных плит, обращенные к роликам, не горизонтальны, а отклонены в обе стороны от среднего положения роликов на угол 20 градуса, и сопряжение этих поверхностей произведено радиусом 65 мм.
Для уменьшения износа рабочие поверхности опорных плит и ролики цементированы и закалены, а внутренняя полость корпуса заполнена осевым маслом.
Каждый элемент упругой ступени представляет собой резиновую шайбу, привулканизированную к стальным пластинам, имеющим кольцевые углубления для предотвращения поперечного сдвига. Резинометаллический блок установлен в коническом опорном стакане главной рамы тепловоза. Комбинированная опора для предотвращения попадания посторонних предметов, влаги, грязи, песка и пыли закрыта брезентовым чехлом, закрепленным хомутами.
На прямом участке пути ролики занимают среднее положение между наклонными плоскостями. При повороте тележки относительно рамы и кузова тепловоза ролики накатываются на наклонные поверхности плит, при этом возникают горизонтальные силы, создающие на радиусе опор возвращающий момент. Ход роликов равен ± 80 мм.
Для передачи силы тяги и торможения с тележек на раму тепловоза применяется упругое шкворневое устройство.
Устройство состоит из прямоугольного ползуна, перемещающегося в направляющих шкворневой балки, и двух стаканов с возвращающими пружинами и упорами. Пружины установлены с зазором 0,5 мм, т.е. - без предварительной затяжки и их жесткость равна 400 кгс/мм2. В цилиндрическую расточку ползуна вварена сменная стальная втулка для шкворня главной рамы. Гнездо шкворня заполнено осевым маслом. Между упорами пружин и ползуном имеется зазор 20 мм на сторону.
Конструкция шкворневого устройства позволяет при вписывании тележки в кривую, перемещаться шкворню на 40 мм в сторону, из которых при перемещении до 20 мм возвращающий эффект создается за счет сдвига резинометаллических элементов, а при перемещении еще на 20 мм - за счет сжатия пружины шкворневого узла. При этом возвращающее усилие пружины равно 8 тонн.
Таким образом, упругое шкворневое устройство в сочетании с комбинированными опорами позволяет уменьшить динамическое воздействие на путь и увеличить допустимую скорость движения тепловоза по стрелочным переводам.
ПЕСОЧНАЯ СИСТЕМА ТЕПЛОВОЗА
ОБЩИЕ СВЕДЕНИЯ О ДВС
Двигатель внутреннего сгорания принадлежит к классу тепловых двигателей, в которых химическая энергия сгорания топлива преобразуется сначала в тепловую энергию, а затем в механическую работу.
ДВС могут быть классифицированы по следующим признакам:
По числу тактов рабочего цикла различают двигатели четырехтактные и двухтактные.
По способу воспламенения рабочей смеси, с самовоспламенением топлива (дизели), и с принудительным зажиганием.
По расположению цилиндров различают двигатели вертикальные, горизонтальные; одно и двухрядные; двигатели с расходящимися поршнями и т.д.
По степени быстроходности двигатели подразделяют (по величине средней скорости поршня) на тихоходные (скорость менее 6 м/с); средней быстроходности (скорость более 6 м/с, но менее 9 м/с) и быстроходные (скорость более 9 м/с, но менее 13 м/с).
Современные тепловозные двигатели представляют собой многоцилиндровые, двух или четырехтактные дизели средней быстроходности и, как правило, с наддувом воздуха.
Сущность наддува состоит в том, что воздух в цилиндры дизеля не засасывается из атмосферы, а нагнетается турбокомпрессором или воздуходувкой. Благодаря наддуву в цилиндры подается на каждый рабочий цикл больше воздуха, чем при всасывании, что одновременно позволяет также подавать в цилиндры и сжигать большее количество топлива, а, следовательно, получать при тех же размерах цилиндров и той же частоте вращения коленчатого вала дизеля большую мощность.
Таким образом, наддув позволяет почти при тех же размерах и массе двигателя увеличить его мощность в 2-3 раза.
При сжатии воздух нагревается, что в значительной степени уменьшает воздушный заряд в цилиндре, обогащённый кислородом. Поэтому в дизелях со средним и высоким наддувом обязательно применяют промежуточное охлаждение наддувочного воздуха. Охлаждение воздуха на каждые 10°С дает увеличение мощности дизеля на 3 - 4%.
ИНДИКАТОРНАЯ ДИАГРАММА
МОЩНОСТЬ и КПД ДИЗЕЛЯ
Рассматривая многоцилиндровые дизели, предполагают, что рабочие процессы в цилиндрах протекают примерно одинаково и мощность дизеля равна сумме мощностей всех цилиндров.
ОСНОВНЫЕ ТРЕБОВАНИЯ К ТЕПЛОВОЗНЫМ ДВС ИХ ОБОЗНАЧЕНИЕ
Дизель является важнейшим силовым агрегатом, который в значительной степени определяет экономичность, надежность и эксплуатационные качества тепловоза. Поэтому тепловозный дизель должен удовлетворять ряду требований.
На габаритные размеры дизеля накладываются жесткие ограничения, обусловленные длиной рамы (21 - 22 метра) и габаритом 1 - Т. Исходя из этого, длина дизеля должна быть в пределах 4500 - 6200 мм, ширина 1500 -1900 мм, высота 2500 - 3200 мм.
Чтобы обеспечить вождение поездов большой массы, мощность дизелей перспективных тепловозов должна составлять 3000 - 6000 кВт.
В последнее время на тепловозах применяют четырехтактные дизели, которые по сравнению с двухтактными лучше приспособлены к локомотивной службе, характеризующейся частыми изменениями режима работы, имеют повышенную топливную экономичность. Наиболее целесообразным является V- образное расположение цилиндров.
Тепловозы работают в широком диапазоне температур и барометрического давления. В этих условиях дизель должен работать устойчиво, без значительного понижения мощности.
Конструкция дизеля должна обеспечивать безопасность при его обслуживании, а также удобство разборки, сборки и возможность ремонта всех его узлов.
Срок службы дизеля до переборки с выемкой поршней должен быть не менее 200 - 250 тыс.км. пробега (или 12000 -15000 часов), а до капитального ремонта (моторесурс) не менее 750 - 800 тыс.км. пробега (45000 - 50000 часов).
Для тепловозных дизелей большое значение имеет развертывание конструкции в мощностной ряд с целью унификации отдельных узлов и деталей, снижения расходов на их ремонт и обслуживание. Мощностные ряды развертываются на базе цилиндров и шатунно-кривошипного механизма одинаковой конструкции и размерности. Изменение мощности дизеля достигается изменением числа цилиндров, их расположением, давлением наддувочного воздуха, частотой вращения коленчатого вала. Примером мощностного ряда являются дизели типа Д49 ПО «Коломенский завод».
Каждый завод, выпускающий дизели, обычно присваивает им условное обозначение (заводскую марку), например 10Д100, 1А-5Д49, ПД1М и т.д.
ГОСТом предусмотрены единые правила обозначения дизеля, учитывающие его основные параметры. Так дизель 1А-5Д49 в соответствии с ГОСТом имеет обозначение 16ЧН26/26, которое расшифровывается так:
16 - число цилиндров;
Ч - четырехтактный (буква Д на этом месте означала бы двухтактный);
Н - дизель с наддувом;
26 - (в числителе) диаметр цилиндра в сантиметрах;
26 - (в знаменателе) ход поршня в сантиметрах;
Обозначение дизелей:
ПД1М по ГОСТу - 6ЧН31,8/33;
10Д100 по ГОСТу – 10ДН20,7/2х25,4.
РАМА ДИЗЕЛЯ ПД1М
РАМА ДИЗЕЛЯ Д49
БЛОК ЦИЛИНДРОВ ДИЗЕЛЯ ПД1М
БЛОК ЦИЛИНДРОВ ДИЗЕЛЯ Д49
Блок цилиндров служит базой для размещения цилиндропоршневой группы, крышек цилиндров, лотка и механизма газораспределения. Он воспринимает усилия от давления газов на поршни и силы инерции деталей шатунпо-кривошипного механизма.
Блок цилиндров представляет собой сварно-литую конструкцию V - образной формы. Нижняя картерная часть блока сварена из литых стоек, а верхняя часть - из листов. Шпильки крепления крышек цилиндров установлены в нижнюю картерную часть, поэтому основные сварные швы верхней части блока разгружены от растягивающих усилий, что обеспечивает их высокую надежность.
К стойкам блока болтами прикреплены штампованные подвески коренных подшипников. Стык стоек и подвесок плоский. Для ограничения перемещения подвесок в поперечном направлении нижняя часть стоек блока и подвесок стянута четырьмя болтами.
Для размещения цилиндровых гильз блок разделен на восемь секций. Для повышения долговечности нижнего пояса блока и предохранения его от коррозии в отверстия блока запрессованы втулки из нержавеющей стали повышенной твердости.
В нижней части боковых продольных листов блока против каждого цилиндра имеются контрольные отверстия герметичности водяных рубашек.
Вода к коллекторам блока поступает через привод насосов по проставкам с уплотнительными кольцами. Для перетока охлаждающей воды из водяных коллекторов к цилиндровым гильзам и предохранения блока цилиндров от коррозии, установлены втулки из нержавеющей стали.
В развале блока образован воздушный ресивер и центральный масляный канал для подвода масла к подшипникам коленчатого вала.
В торцовом листе блока имеется отверстие, по которому масло подводится в центральный масляный канал, откуда по каналам в стойках - на смазку подшипников.
Для слива масла из крышек цилиндров в блоке имеются отверстия, через которые проходят трубки с проставками и уплотнением.
Скопившееся в воздушном ресивере масло сливается в поддизельную раму через отверстие расположенное в торце блока.
Доступ в картер дизеля обеспечивается через люки, закрытые крышками. С правой стороны блока крышки имеют предохранительные клапаны, которые открываются в аварийных случаях при повышении давления в картере.
КРЫШКА ЦИЛИНДРА ДИЗЕЛЯ ПД1M
КРЫШКА ЦИЛИНДРА ДИЗЕЛЯ Д49
Крышка цилиндра отлита из высокопрочного чугуна. Днище крышки в местах между клапанными и форсуночным отверстиями имеет меньшую толщину, что обеспечивает лучшее охлаждение днища, более равномерный его нагрев и снижение уровня термических напряжений.
В корпусе крышки в чугунных направляющих втулках размещены два впускных и два выпускных клапана.
Для обеспечения высокой износостойкости посадочных фасок для выпускных клапанов в крышке установлены плавающие вставные седла, удерживаемые пружинными кольцами. Седла и стопорные кольца изготовлены из жаропрочной стали.
Крышки цилиндров охлаждаются водой, которая поступает из водяной рубашки цилиндровых гильз и отводится в охлаждающую полость выпускных коллекторов. В крышке имеется отверстие для контроля плотности стыка крышки и цилиндровой гильзы.
На верхнюю плоскость крышки установлено закрытие, уплотненное резиновым кольцом и прикрепленное к ней шпильками.
ЦИЛИНДРОВЫЕ ГИЛЬЗЫ
Цилиндровые гильзы дизеля служат в качестве направляющих для перемещения поршней. Они образуют рабочий объем цилиндров, в котором происходит преобразование химической энергии сгорания топлива в механическую работу для вращения коленчатого вала.
Гильза цилиндра дизеля 5Д49 подвесного типа - подвешена на шпильках к крышке цилиндра. Жесткой связи гильзы с блоком дизеля нет, в результате чего газовый стык разгружен от осевых усилий давления сгорания.
Гильза изготовлена их хромомолибденового чугуна, обладающего высокой износостойкостью и необходимыми антифрикционными свойствами.
Стык между гильзой и крышкой цилиндра уплотнен стальным омедненным кольцом. В блоке гильза фиксируется верхним и нижним опорными поясами.
Полость охлаждения создается рубашкой, надетой на гильзу и уплотненной на ней резиновыми кольцами. Рубашка на гильзе фиксируется стопорным кольцом. Полости между гильзами и рубашками сообщаются с водяными коллекторами. Благодаря уплотнениям блок цилиндров защищен от попадания воды, поэтому такой блок называют сухим.
Резиновые кольца не соприкасаются с поверхностью гильзы, и имеют температуру не выше температуры охлаждающей воды.
Для перетока воды в крышку цилиндра, сверху в отверстия гильзы запрессованы втулки, покрытые теплоизолирующим слоем и уплотненные паронитовыми прокладками и резиновыми кольцами.
Гильза цилиндра дизеля ПД1М выполнена с некоторым утолщением от середины к верху, так как в верхней части давление газов значительно больше. Направляющие пояса вверху и внизу гильзы центрируют ее в блоке.
Герметичность установки гильзы обеспечивается в верхней части притиркой опорного бурта гильзы и посадочного места в блоке, а в нижней части - тремя резиновыми кольцами. Такое уплотнение не мешает удлинению гильзы при нагревании.
На верхней торцовой части гильзы проточен кольцевой паз для бурта цилиндровой крышки.
ДИЗЕЛЬ-ГЕНЕРАТОРНАЯ МУФТА
ПОРШЕНЬ ДИЗЕЛЯ ПД1М
Поршень отлит из алюминиевого сплава ПС-12 (силумина), обладающего высоким коэффициентом теплопроводности, что позволяет не применять специального охлаждения. Сверху поршень хорошо охлаждается воздухом, а снизу - брызгами масла. Днище поршня подвержено действию высоких температур, поэтому для улучшения отвода тепла оно выполнено утолщенным.
Круглое углубление в центре днища способствует лучшему смешиванию распыленного топлива с воздухом. Четыре углубления, выфрезерованных по краям днища, обеспечивают зазор (3,5 -4,5 мм), между открытыми клапанами и поршнем, находящимся в ВМТ.
Головка поршня на длине 170 мм проточена на конус, что исключает возможность заклинивания поршня при перегреве.
Внутри поршень имеет приливы (бобышки), в которых расточены отверстия для поршневого пальца плавающего типа. Палец служит для соединения поршня с шатуном. Поршневой палец изготавливается из высоколегированной хромоникелевой стали, а его наружная поверхность цементируется, шлифуется и полируется.
Во внутреннюю поверхность пальца завальцована тонкостенная стальная втулка, образующая с его внутренней поверхностью кольцевой масляный канал для охлаждения и смазки пальца. Для этого в средней части пальца просверлено четыре отверстия, а по краям - восемь.
Отверстия в бобышках поршня имеют выточки, в которые запрессовывают заглушки, удерживающие палец от осевого перемещения.
На поверхности поршня проточены канавки для четырех уплотнительных (компрессионных) и трех маслосъемных колец. Первые обеспечивают уплотнение поршня в цилиндре, а вторые - регулировку подачи масла к трущейся поверхности гильзы. Кольца изготовлены из высокопрочного легированного чугуна.
Верхние уплотнительные кольца кроме температурной, испытывают большую силовую нагрузку. Первое кольцо испытывает 75% давления в цилиндре, второе 20% и третье - 5%. Поэтому первое и второе кольца изготавливают трапециевидной формы и хромируют. Третье и четвертое кольца имеют прямоугольное сечение и для лучшей приработки покрываются слоем полуды.
Маслосъемные кольца имеют двойную скребковую поверхность. У этих колец по окружности профрезерованы 12 радиальных сквозных пазов. Таким образом, кольцо состоит как бы из двух частей - верхней и нижней. Обе части имеют конусный срез в одну сторону, что позволяет кольцу при движении поршня вверх скользить по маслу, а при движении вниз острыми кромками снимать избыток масла со стенок гильзы.
Кольца ставят в канавки поршней с определенным зазором. Постановка кольца с малым зазором может привести к заеданию его в канавке и ухудшению уплотнительных свойств. Если зазор увеличен, то повышается насосное действие колец, которое заключается в том, что кольцо, имея зазор по высоте, при работе поршня попеременно прижимается то к низу, то к верху канавки. При этом масло периодически перекачивается от одной канавки к другой.
Интересно отметить, что потери на трение при работе поршней и колец составляют 50-60% всех механических потерь в дизеле, а тепло полученное поршнем отводится поршневыми кольцами в количестве 75%.
ПОРШЕНЬ ДИЗЕЛЯ Д49
Поршень составной конструкции. Штампованная головка поршня из жаростойкой стали соединена с алюминиевым тронком при помощи шпилек и гаек.
Для улучшения прирабатываемости поверхность тронка покрыта слоем дисульфида молибдена (антифрикционное приработочное покрытие).
В отверстия бобышек тронка установлен поршневой палец плавающего типа. Последний изготовлен из легированной стали, азотирован и цементирован. Осевое перемещение пальца ограничивается стопорными кольцами.
В канавках головки поршня установлены три компрессионных кольца с односторонней трапецией, одно прямоугольное и одно маслосъемное кольцо щелевого типа с пружинным расширителем (экспандером). На юбке тронка (в нижней его части) установлено одно маслосъемное кольцо.
Масло для охлаждения поршня поступает из головки шатуна через отверстие и прижатый к ней пружиной стакан и далее от центра днища по отверстиям в тронке перетекает в периферийную полость охлаждения, откуда по каналу в тронке стекает в картер. Для поддержания уровня масла в полости охлаждения в этот канал запрессована трубка, конец которой возвышается над тронком на 15 мм
ШАТУН ДИЗЕЛЯ ПД1М
Механизм газораспределения предназначен для периодического впуска свежего воздуха в цилиндры дизеля и для выпуска отработавших газов в атмосферу, а также для привода топливных насосов высокого давления.
Базовой деталью газораспределительного механизма является лоток, который состоит из двух половин скрепленных болтами и шпильками. Лоток устанавливается на блоке цилиндров.
С переднего торца лоток закрыт крышкой, в которой размещен редукционный клапан, отрегулированный на давление 2,5+0,3 кгс/см2. В лотке в разъемных алюминиевых подшипниках вращается распределительный вал, изготовленный из легированной стали.
Кулачки распредвала фиксируются при помощи шпонок в соответствии с порядком работы цилиндров.
В8 - А5 - В4 - А7 - В2 - А3 – В6 - А8 - В1 - А4 - В5 - А2 - В7 - А6 - В3 - А1
Усилие от кулачковых шайб передается клапанам через рычаги толкателей, штанги и рычаги клапанов.
Клапаны выполнены из высокопрочной стали. Выпускные клапаны имеют наплавку фасок кобальтовым стеллитом ВЗК, для повышения износостойкости.
Каждая пара клапанов открывается одним рычагом через гидротолкатели. Последние при работе дизеля, ликвидируют зазор между бойком ударника и колпачком клапана, что уменьшает шумность работы дизеля.
Масло из масляной системы дизеля по трубке поступает в полость редукционного клапана и далее в масляный канал лотка. Из этого канала масло поступает:
- на смазку подшипников распределительного вала
- на смазку толкателей топливных насосов
- на смазку привода распредвала
- на смазку привода клапанов и в гидротолкатели
Привод распредвала предназначен для передачи вращения от коленчатого вала распредвалу, приводному валу ОРД, шестерням привода механического тахометра, шестерне вентилятора охлаждения тягового генератора, валу с грузом предельного выключателя, якорю возбудителя и якорю стартер — генератора.
Кроме того привод используется для передачи вращения коленвалу от стартер-генератора при пуске дизеля.
Привод распредвала установлен на заднем торце блока цилиндров и представляет собой зубчатую передачу, состоящую из прямозубых и конических шестерен, помещенных в корпус, который состоит из четырех частей. Шестерни смазываются маслом, выходящим из форсунки, к которой оно поступает из канала лотка.
ТОПЛИВНЫЙ НАСОС ДИЗЕЛЯ Д49
Топливные насосы высокого давления устанавливают в специальные расточки лотка дизеля и крепят к нему четырьмя шпильками. Толкатели насосов одноименных цилиндров правого и левого рядов приводятся в действие одной и той же кулачковой шайбой распредвала.
В корпусе насоса установлены гильза плунжера с плунжером, а также нагнетательный клапан и его седло. Гильза плунжера и седло клапана закреплены в корпусе насоса нажимным штуцером. Гильза плунжера зафиксирована стопорным винтом.
На верхней части плунжера расположены верхняя и нижняя винтовые отсечные кромки, посредством которых регулируется количество топлива, подаваемого в цилиндры. Эти кромки расположены таким образом, что при движении рейки в корпус насоса подача топлива уменьшается.
На цилиндрической поверхности плунжера имеются две кольцевые канавки. Широкая канавка при любом положении плунжера соединена через сверление в гильзе плунжера с полостью всасывания насоса, что исключает попадание топлива по плунжеру в масляную систему.
В гильзе плунжера имеются два отверстия для подвода и отсечки топлива. Также на гильзе установлен зубчатый венец. В зацеплении с венцом находится рейка, посредством которой механизм управления топливными насосами поворачивает плунжер. Максимальный выход рейки ограничивается винтом.
Толкатель состоит из корпуса, в котором на оси установлен цементированный ролик. Сверху в корпус ввернут упор для передачи усилия от толкателя к плунжеру. Движение толкателя направляется бронзовой втулкой, запрессованной в направляющую втулку. Эта втулка крепится болтами к корпусу насоса и на внутренней поверхности имеет три фрезерованных продольных паза для слива масла. Угол опережения подачи топлива регулируют прокладками.
ФОРСУНКИ
Регулятор предназначен для установки числа оборотов коленвала в соответствии с позицией контроллера машиниста, а также для автоматического поддержания заданных оборотов независимо от изменения нагрузки на дизель.
Регулятор состоит из трех корпусов: нижнего, среднего и верхнего. К среднему корпусу прикреплен корпус сервомотора, а к сервомотору прикреплён корпус тягового блок-магнита.
Внутри нижнего корпуса смонтирован привод регулятора, состоящий из приводного и шлицевого валов, соединенных упругой муфтой. Вал привода заплечиками опирается на шарикоподшипник, который в свою очередь опирается на проставочную втулку, а втулка через кольцо на коническую шестерню, укрепленную на нижнем конце вала на шпонке.
Шлицевой вал в верхней части имеет наружные шлицы, входящие во внутренние шлицы ведущей шестерни масляного насоса. Последняя соединена, при помощи двух конических винтов с буксой золотниковой части регулятора. Ведомая шестерня помещена в выточке среднего корпуса и вращается на оси.
В среднем корпусе имеются два колодца (аккумуляторы) давления масла, внутри которых помещены поршни, нагруженные снизу двумя пружинами. Сверху во время работы дизеля на поршни давит масло, подаваемое масляным насосом. В одном из колодцев имеется боковое отверстие, благодаря которому в регуляторе поддерживается постоянное давление масла 3,4 - 5кгс/см2. Свободные полости в среднем корпус служат масляной ванной.
В центре среднего корпуса смонтирована золотниковая часть регулятора, состоящая из чугунной буксы, траверсы, рычагов с грузами, золотниковой втулки и плунжера.
Букса по высоте имеет пять кольцевых проточек с окнами, совпадающими с каналами в среднем корпусе регулятора.
Верхняя проточка совпадает с нагнетательным каналом масляного насоса.
Вторая проточка - с каналом, который идет к полости под силовым поршнем.
Третья и пятая - с каналом соединенным с масляной ванной.
Четвертая - с каналом, сообщающимся с полостью над компенсирующим поршнем.
В буксе установлена золотниковая втулка с поршнем. На хвостовик втулки надеты верхняя и нижняя тарелки и компенсирующая пружина. Вся эта система стянута корончатой гайкой и помещена в стакан, прикрепленный к буксе конусным винтом. Для регулировки затяжки компенсирующей пружины применяют набор прокладок.
Для сообщения внутренней полости золотниковой втулки с проточками в буксе, в стенках золотниковой втулки есть три ряда отверстий; вверху и внизу по четыре, а посредине - восемь.
Плунжер имеет два диска, из них нижний является рабочим. На верхний конец плунжера напрессованы два шарикоподшипника, над которыми
установлена тарелка с буртами, закрепленная корончатой гайкой. Тарелка служит опорой для всережимной пружины.
Корпус сервомотора перегородкой разделен на две полости. В верхней полости помещен силовой поршень, а в нижней - компенсирующий поршень, напрессованные на общий шток и нагруженные пружиной. На нижнем конце штока штифтом укреплена вилка, при помощи которой шток соединен с рычажной передачей управления топливными насосами.
В корпусе блок-магнита один канал соединен с полостью под силовым поршнем, а другой канал - с полостью над силовым поршнем.
При замыкании электрической цепи блок-магнита, якорь через толкатель отжимает клапан вниз, который разобщает полости над и под силовым поршнем сервомотора.
|
|
Кормораздатчик мобильный электрифицированный: схема и процесс работы устройства...
Механическое удерживание земляных масс: Механическое удерживание земляных масс на склоне обеспечивают контрфорсными сооружениями различных конструкций...
Индивидуальные и групповые автопоилки: для животных. Схемы и конструкции...
Адаптации растений и животных к жизни в горах: Большое значение для жизни организмов в горах имеют степень расчленения, крутизна и экспозиционные различия склонов...
© cyberpedia.su 2017-2024 - Не является автором материалов. Исключительное право сохранено за автором текста.
Если вы не хотите, чтобы данный материал был у нас на сайте, перейдите по ссылке: Нарушение авторских прав. Мы поможем в написании вашей работы!