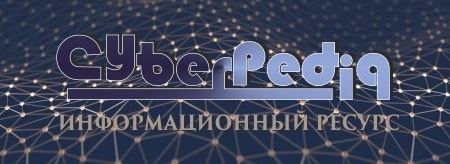
Состав сооружений: решетки и песколовки: Решетки – это первое устройство в схеме очистных сооружений. Они представляют...
Археология об основании Рима: Новые раскопки проясняют и такой острый дискуссионный вопрос, как дата самого возникновения Рима...
Топ:
Когда производится ограждение поезда, остановившегося на перегоне: Во всех случаях немедленно должно быть ограждено место препятствия для движения поездов на смежном пути двухпутного...
Марксистская теория происхождения государства: По мнению Маркса и Энгельса, в основе развития общества, происходящих в нем изменений лежит...
Отражение на счетах бухгалтерского учета процесса приобретения: Процесс заготовления представляет систему экономических событий, включающих приобретение организацией у поставщиков сырья...
Интересное:
Подходы к решению темы фильма: Существует три основных типа исторического фильма, имеющих между собой много общего...
Национальное богатство страны и его составляющие: для оценки элементов национального богатства используются...
Распространение рака на другие отдаленные от желудка органы: Характерных симптомов рака желудка не существует. Выраженные симптомы появляются, когда опухоль...
Дисциплины:
![]() |
![]() |
5.00
из
|
Заказать работу |
Содержание книги
Поиск на нашем сайте
|
|
Минеральными вяжущими веществами называют тонкоизмельченные порошки, образующие при смешивании с водой пластичное тесто, под влиянием физико-химических процессов переходящее в камневидное состояние. Это свойство вяжущих веществ используют для приготовления на их основе растворов, бетонов, безобжиговых искусственных каменных материалов и изделий. Различают минеральные вяжущие вещества воздушные и гидравлические.
• Воздушные вяжущие вещества твердеют, долго сохраняют и повышают свою прочность только на воздухе. К воздушным вяжущим веществам относятся гипсовые и магнезиальные вяжущие, воздушная известь и кислотоупорный цемент, жидкое стекло, глина.
• Гидравлические вяжущие вещества способны твердеть и длительно сохранять свою прочность не только на воздухе, но и в воде. В группу гидравлических вяжущих входят портландцемент и его разновидности, пуццолановые и шлаковые вяжущие, глиноземистый и расширяющиеся цементы, гидравлическая известь. Их используют как в надземных, так и в подземных и подводных конструкциях.
Вяжущие вещества автоклавного твердения, эффективно твердеющие только при автоклавной обработке — давлении насыщенного пара 0,8...1,2 МПа и температуре 17О...2ОО°С. В группу вяжущих веществ автоклавного твердения входят известково-кремнеземистые и известково-нефелиновые вяжущие.
К ним относят:
Кислотоупорные цементы и жидкое стекло
• Кислотоупорные цементы состоят из смеси водного раствора силиката натрия (растворимого стекла), кислотоупорного наполнителя и добавки — ускорителя твердения. В качестве микронаполнителя используют кварц, кварциты, андезит, диабаз и другие кислотоупорные материалы; ускорителем твердения служит кремнефтористый натрий. Вяжущим материалом в кислотоупорном цементе является растворимое стекло — водный раствор силиката натрия Na2O-SiO2 или силиката калия К2О-nSiO2. Величина п указывает на отношение числа молекул кремнезема к числу молекул щелочного оксида и называется модулем стекла, он колеблется от 2,5 до 3,5.
Добавка кремнефтористого натрия также повышает водостойкость и кислотоупорность цемента. Отечественная промышленность выпускает кислотоупорный кварцевый кремнефтористый цемент, состоящий из смеси тонкомолотого чистого кварцевого песка 15...30% и кремнефтористого натрия Na2SiF6 — 4...6% от массы наполнителя.
Кислотоупорные цементы применяют для футеровки химической аппаратуры, возведения башен, резервуаров и других сооружений химической промышленности, а также для приготовления кислотоупорных замазок, растворов и бетонов.
Как указывалось ранее, для приготовления кислотоупорного цемента применяют растворимое стекло. Растворимое стекло получают при сплавлении в течение 7... 10 ч в стекловарочных печах при 1300... 1400°С кварцевого песка, измельченного и тщательно смешанного с кальцинированной содой, сульфатом натрия или с поташом К2СО3. Полученная стекломасса поступает из печи в вагонетки, где быстро охлаждается и распадается на куски. Застывшие куски называют «силикат-глыба». Это стекло растворимо в воде при обычных условиях, но при действии пара высокого давления 0,5...0,6 МПа и температуре около 150°С сравнительно быстро переходит в жидкое состояние.
Твердеет растворимое стекло (довольно медленно) только на воздухе вследствие выделения и высыхания аморфного кремнезема под действием углекислоты воздуха по реакции
Na2Si03 + СО2 + 2Н2О? Si (ОН) 4 + Na2CO3
Однако глубина проникания углекислоты воздуха сравнительно невелика и положительное ее действие наблюдается только на поверхности.
Ускоряет твердение растворимого стекла добавка катализатора — кремнефтористого натрия Na2SiF6. Последний вступает во взаимодействие с растворимым стеклом, в результате чего быстро образует гель кремнекислоты — клеящее вещество, что приводит к быстрому твердению системы:
Na2SiF6 + 2Na2Si03 + 6Н2О -+? 6NaF + 3Si (ОН) 4
Силикат-глыбу можно транспортировать в таре или навалом. Растворимое стекло, имеющее сиропообразную консистенцию, транспортируют в бочках, стеклянных баллонах. Растворимое стекло применяют для приготовления кислотостойких и жароупорных обмазок. Нельзя применять растворимое стекло для конструкций, подверженных длительному воздействию воды, щелочей и фосфорной, фтористо-водородной или кремнефтористо-водородной кислоты.
Кислотоупорный цемент не водостоек; разрушается от воздействия воды и слабых кислот. Для повышения водостойкости в состав цемента вводят 0,5% льняного масла или 2% гидрофоби-зующей добавки. Полученный таким образом гидрофобизованный цемент называют кислотоупорным водостойким цементом (КВЦ).
Для повышения кислотостойкости кислотоупорных бетонов рекомендуется обрабатывать их поверхность разбавленной соляной или серной кислотой, раствором хлористого кальция или хлористого магния.
|
|
Гидравлическая известь
Гидравлическая известь — продукт умеренного обжига при температуре 9ОО...11ОО°С мергелистых известняков, содержащих 6...20% глинистых примесей. При обжиге мергелистых известняков после разложения углекислого кальция часть образующейся СаО соединяется в твердом состоянии с оксидами SiO2; A12O3; Fe2O3, содержащимися в минералах глины, образуя силикаты 2CaO-SiO2, алюминаты СаО-А12О3 и ферриты кальция 2CaO-Fe2O3, обладающие способностью твердеть не только на воздухе, но и в воде. Так как в гидравлической извести содержится в значительном количестве свободный оксид кальция СаО, то она, так же как и воздушная известь, гасится при действии воды, причем чем больше содержание свободной СаО, тем меньше ее способность к гидравлическому твердению.
Строительную гидравлическую известь выпускают в виде тонкоизмельченного порошка, при просеивании которого остаток частиц на сите № 008 не должен превышать 15%. Кроме глинистых и песчаных примесей мергелистые известняки обычно содержат до 2...5% углекислого магния и другие примеси. Для производства гидравлической извести необходимо применять известняки с возможно более равномерным распределением глинистых и других включателей, так как от этого в значительной степени зависит качество получаемого продукта.
Для характеристики химического состава сырья, содержащего известняк и глину, а также готового вяжущего вещества обычно пользуются гидравлическим или основным модулем, который для гидравлической извести составляет 1,7...9:
m=%Ca0/[%(Si02 + Al203 + Fe203)]
Различают гидравлическую известь двух видов: слабогидравлическую с модулем 4,5...9 и сильногидравлическую с модулем 1,7...4,5.
Гидравлическая известь, затворенная водой, после предварительного твердения на воздухе продолжает твердеть и в воде, при этом физико-химические процессы воздушного твердения сочетаются с гидравлическими. Гидрат оксида кальция при испа-' рении влаги постепенно кристаллизуется, а под действием углекислого газа подвергается карбонизации. Гидравлическое твердение извести происходит в результате гидратации силикатов, алюминатов и ферритов кальция так же, как в портландцементе. Предел прочности образцов через 28 сут твердения должен быть не менее: для слабогидравлической и сильногидравлической со-ответственно при изгибе — 0,4 и 1,0 МПа и при сжатии — 1,7и 0,5 МПа.
Гидравлическая известь по химическому составу должна соответствовать требованиям, указанным в табл. 5.7. Она должна выдерживать испытание на равномерность изменения объема. Гидравлическую известь применяют в тонкоизмельченном виде для приготовления строительных растворов, предназначенных для сухой или влажной среды, бетонов низких марок и т. д. Гидравлическая известь дает менее пластичные, чем воздушная, растворы, быстрее и равномернее твердеющие по всей толще стены и обладающие большей прочностью.
Романцемент
Получают обжигом не до спекания известняковых или магнезиальных мергелей содерд более 20% глины. Продукт обжига размалывают и получают гидравл вяжущие. Обр-ся алюминаты, ферриты и силикаты придающие гидравлич. св-ва.А так же Воздушная строительная известь, Магнезиальные вяжущие вещества, Гипсовые вяжущие вещества, Портландцемент
|
Гипсовые вяжущие вещества
Гипсовые вяжущие — группа воздушных вяжущих веществ, в затвердевшем состоянии состоящих из двуводного сульфата кальция (CaSO4 • 2Н2О), включает в себя собственно гипсовые вяжущие (далее для краткости — гипс) и ангидритовые вяжущие (ангидритовый цемент и эстрихгипс).
|
Гипс (в строительной практике иногда используют устаревший термин алебастр от гр. alebastros — белый) — быстротвердеющее воздушное вяжущее, состоящее из полуводного сульфата кальция CaSO4 • 0,5Н2О, получаемого низкотемпературной (< 200° С) обработкой гипсового сырья.
Сырьем для гипса служит в основном природный гипсовый камень, состоящий из двуводного сульфата кальция (CaSO4•2Н2О) и различных механических примесей (глины и др.). В качестве сырья могут использоваться также гипсосодержащие промышленные отходы, например, фосфогипс, а также сульфат кальция, образующийся при химической очистке дымовых газов от оксидов серы с помощью известняка. Все это указывает на то, что проблем с сырьем для гипсовых вяжущих нет.
Получение гипса включает две операции:
- термообработку гипсового камня на воздухе при 150... 160°С; при этом он теряет часть химически связанной воды, превращаясь в полуводный сульфат кальция β-модификации:
CaSO4 • 2Н2О → CaSO4 • 0,5Н2О + 1,5Н2О
- тонкий размол продукта, который можно производить как до, так и после термообработки; гипс - мягкий минерал (твердость по шкале Мооса - 2), поэтому размалывается он очень легко.
Таким способом производится основное количество гипса; обычно для этого используют гипсоварочные котлы. Гипс β-модификации далее для краткости будем называть просто «гипс».
Доступность сырья, простота технологии и низкая энергоемкость производства (в 4...5 раз меньше, чем для получения портландцемента) делают гипс дешевым и привлекательным вяжущим.
Химизм твердения гипса заключается в переходе полуводного сульфата кальция при затворении его водой в двуводный:
CaSO4 • 0,5Н2О + l,5H2O → CaSO4 • 2Н2О
Гипсовые вяжущие вещества делят на две группы: низкообжиговые и высокообжиговые.
• Низкообжиговые гипсовые вяжущие вещества получают при нагревании двухводного гипса CaSO4-2H2O до температуры 15О...16О°С с частичной дегидратацией двуводного гипса и переводом его в полуводный гипс СаSO4-О.5Н2О.
• Высокообжиговые (ангидритовые) вяжущие получают обжигом двуводного гипса при более высокой температуре до 700... 1000°С с полной потерей химически связанной воды и образованием безводного сульфата кальция — ангидрита CaSO4. К низкообжиговым относится строительный, формовочный и высокопрочный гипс, а к высокообжиговым — ангидритовый цемент и эстрих-гипс.
Сырьем для производства гипсовых вяжущих служат природный гипсовый камень и природный ангидрид CaSO4, а также отходы химической промышленности, содержащие двуводный или безводный сернокислый кальций, например фосфогипс.
• Гипсовым вяжущим(ОБЫЧНЫЙ) называют воздушное вяжущее вещество состоящее преимущественно из полуводного гипса и получаемого путем тепловой обработки гипсового камня при температуре 15О...16О°С. При этом двуводный гипс CaSO4*2H2O, содержащийся в гипсовом камне, дегидратирует по уравнению CaSO4*2HO= CaSO4*0.5H2O+1.5HO
В этих условиях образуются мелкие кристаллы полуводного сернокислого кальция бета-модификации; такой гипс обладает повышенной водопотребностью (60...65% воды). Избыточная вода, т. е. сверхпотребная на гидратацию гипса (15%), испаряется, образуя поры, вследствие чего затвердевший гипс имеет высокую пористость (до 40%) и соответственно небольшую прочность. Производство гипса складывается из дробления, помола и тепловой обработки (дегидратации) гипсового камня. Имеется несколько технологических схем производства гипсового вяжущего: в одних помол предшествует обжигу, в других помол производится после обжига, а в третьих помол и обжиг совмещаются в одном аппарате. Последний способ получил название обжига гипса во взвешенном состоянии. Тепловую обработку гипсового камня производят в варочных котлах, сушильных барабанах, шахтных или других мельницах.
При затворении порошка гипса водой полуводный сернокислый кальций CaSO4-0,5H2O, содержащийся в нем, начинает растворяться до образования насыщенного раствора и одновременно гидратироваться, присоединяя 1,5 молекулы воды и переходя в двугидрат CaSO4-2H2O по уравнению
CaSO4-0,5H2O+l,5H2O=CaSO*2H2O
Растворимость двугидрата примерно в 5 раз меньше растворимости исходного порошка — полугидрата CaSO4-0,5H2O. В результате образовавшийся насыщенный раствор полугидрата оказывается пересыщенным по отношению к двугидрату. Пересыщенный раствор в обычных условиях не может существовать — из него выделяются мельчайшие частицы твердого вещества — двуводного сернокислого кальция. По мере накопления этих частиц они склеиваются между собой, вызывая загустева-ние (схватывание) теста. Затем мельчайшие частицы гидрата начинают кристаллизоваться, определяя этим образование проч-ного гипсового камня. Дальнейшее увеличение прочности гипса происходит вследствие высыхания твердеющей массы и более полной кристаллизации при этом. Твердение гипса можно ускорить сушкой, но при температуре не выше 65°С во избежание обратной дегидратации двуводного гипса.
Быстрое схватывание гипса затрудняет в ряде случаев его использование и вызывает необходимость применения замедлителей схватывания (кератинового, известково-кератинового клея, сульфитно-дрожжевой бражки в количестве 0,1...0,3% от массы гипса). Замедлители схватывания уменьшают скорость растворения полуводного гипса и замедляют диффузионные процессы. При необходимости ускорить схватывание гипса к нему добавляют двуводный гипс, поваренную соль, серную кислоту. Одни из них повышают растворимость полуводного гипса, другие (двуводный гипс) образуют центры кристаллизации, вокруг которых быстро закристаллизовывается вся масса.
Применяется гипсовое вяжущее для производства гипсовых, гипсобетонных строительных изделий для внутренних частей зданий (перегородочных плит, панелей, сухой штукатурки, приготовления гипсовых и смешанных растворов, производства декоративных и отделочных материалов, например искусственного мрамора), а также для производства гипсоцементно-пуццолановых вяжущих. (прочн 10-18 МПа)
Высокопрочный гипс(ВЫСОКОПРОЧНЫЙ) является разновидностью полуводного гипса. Этот полуводный гипс а-модификации, который имеет более крупные кристаллы, обусловливающие меньшую водопотреб-ность гипса (40...45% воды), позволяет получать гипсовый камень с большей плотностью и прочностью. Получают его путем нагревания природного гипса паром под давлением 0,2...0,3 МПа с последующей сушкой при температуре 16О...18О°С. Прочность его за 7 сут достигает 15...40 МПа. Высокопрочный гипс выпускают пока в небольшом количестве и применяют в основном в металлургической промышленности для изготовления форм. Однако он успешно может заменить обыкновенное гипсовое вяжущее, обеспечив изделиям высокую прочность.
• Основными характеристиками гипсовых вяжущих являются сроки схватывания, тонкость помола, прочность при сжатии и растяжении, водопотребность и др.
Гипсовое вяжущее является быстросхватывающим и быстротвердеющим вяжущим веществом. По срокам схватывания ГОСТ 125—79 предусматривает выпуск вяжущих:
быстротвердеющего (инд А) с началом схватывания не ранее 2 мин, концом — не позднее 15 мин;
нормальнотвердеющего (индекс Б) с началом схватывания не ранее 6 мин, концом — не позднее 30 мин;
медленнотвердеющего (индекс Б) с началом схватывания не ранее 20 мин, конец схватывания не нормируется.
В зависимости от степени помола различают вяжущие грубого, среднего и тонкого помола с максимальным остатком на сите с размером ячеек в свету 0,2 мм не более 23, 14 и 2% (обозначаемые соответственно индексами I, II и III).
Марку. гипсовых вяжущих характеризуют по прочности при сжатии образцов-балочек 40X40X160 мм в возрасте 2 ч после затворения водой. Например, гипсовое вяжущее с прочностью при сжатии 5,2 МПа, началом схватывания 5 мин, концом схватывания 9 мин и остатком на сите 0,2 мм 9%, т. е. вяжущее марки Г-5 быстротвердеющее, среднего помола, может быть записано в виде сокращенного обозначения Г-5АII.
Гипсовые вяжущие применяют при производстве гипсовой штукатурки, перегородочных стеновых плит и панелей, вентиляционных коробов и других деталей в зданиях и сооружениях, работающих при относительной влажности воздуха не выше 65%. Изделия из них обладают небольшой плотностью, несгораемостью и рядом других ценных свойств, но при увлажнении прочность их снижается.
• Ангидритовое вяжущее получают обжигом природного двуводного гипса при температуре 600...700°С с последующим его измельчением с добавками — катализаторами твердения (известью, смесью сульфата натрия с медным или железным купоросом, обожженным доломитом, основным доменным гранулированным шлаком и др.). Ангидритовое вяжущее можно получить также путем помола природного ангидрита с указанными выше добавками.
CaSO4*2H2O=CaSO4+2H2O
Ангидритовый цемент — это медленно схватывающееся вяжущее вещество с началом схватывания не ранее 30 мин, концом — не позднее 24 ч. Марки ангидритового цемента по прочности при сжатии М50, 100, 150 и 200. Применяют ангидритовые цементы Для приготовления кладочных и отделочных растворов, бетонов, производства теплоизоляционных материалов, искусственного мрамора и других декоративных изделий.
- Высокообжиговый гипс (эстрих-гипс) является разновидностью ангидритовых цементов. Его получают обжигом природного гипса или ангидрита при температуре 8ОО...1ООО°С с последующим тонким измельчением. При этом происходит не только полное обезвоживание, но и частичная диссоциация (разложение) ангидрита с образованием СаО (в количестве 3...5%) по реакции
CaSO4*2H2O=CaSO4+2H2O
CaSO4 = СаО + SO3.
При затворении водой СаО действует как катализатор по схеме твердения ангидритового цемента, рассмотренной выше. Высокообжиговый гипс медленно схватывается и твердеет, но водостойкость и прочность при сжатии (10... 20 МПа) позволяют успешно использовать его при устройстве мозаичных полов, изготовлении искусственного мрамора и др. Изделия из высокообжигового гипса мало-, тепло- и звукопро-водны, они обладают по сравнению с изделиями из гипсового вяжущего более высокой морозостойкостью, повышенной водостойкостью и меньшей склонностью к пластическим деформациям.
|
Воздушная известь
Известь воздушная — минеральное воздушное вяжущее. Готовится на основе карбонатного сырья. В строительстве используется в основном гашённая (гидратная) известь в виде извести-пушонки, известкового молока. Сырьем для получения извести служат широко распространенные осадочные горные породы: известняки, мел, доломиты, состоящие преимущественно из карбоната кальция (СаСО3). Если куски таких пород прокалить на огне, то карбонат кальция перейдет в оксид кальция:
СаСО3 → СаО + СО2↑
Производство. Сырье — карбонатные породы (известняки, мел, доломиты), содержащие не более 6...8 % глинистых примесей, обжигают в шахтных или вращающихся печах при температуре 1000... 1200° С. В процессе обжига СаСО3 и MgCO3, содержащиеся в исходной породе, разлагаются на оксиды кальция СаО и магния MgO и углекислый газ. Неравномерность обжига может привести к образованию в извести недожога и пережога.
Недожог (неразложившийся СаСО3), получающийся при слишком низкой температуре обжига, снижает качество извести, так как не гасится и не обладает вяжущими свойствами.
Пережог образуется при слишком высокой температуре обжига в результате сплавления СаО с примесями кремнезема и глинозема. Зерна пережога медленно гасятся и могут вызвать растрескивание и разрушение уже затвердевшего материала.
Куски обожженной извести — комовая известь — обычно подвергают гашению водой:
СаО + Н2О → Са(ОН)2 + 1160 кДж/кг
Выделяющаяся при гашении теплота резко повышает температуру извести и воды, которая может даже закипеть (поэтому негашеную известь называют кипелкой).
При гашении куски комовой извести увеличиваются в объеме и распадаются на мельчайшие (до 1 мкм) частицы.
В зависимости от количества взятой для гашения воды получают: гидратную известь - пушонку (35…40 % воды от массы извести, т. е. в количестве, необходимом для протекания реакции гидратации — процесса гашения); известковое тесто (воды в 3...4 раза больше, чем извести), известковое молоко (количество воды превышает теоретически необходимое в 8... 10 раз).
Виды воздушной извести. По содержанию оксидов кальция и магния воздушная известь бывает:
• кальциевая — MgO не более 5 %;
• магнезиальная — MgO > 5...20 %;
• доломитовая — MgO > 20...40 %.
По виду поставляемого на строительство продукта воздушную известь подразделяют на негашеную комовую (кипелку), негашеную порошкообразную (молотую кипелку) и гидратную (гашеную, или пушонку).
Негашеная комовая известь предстаатяет собой мелкопористые куски размером 5...10см, получаемые обжигом известняка. В зависимости от содержания, активных СаО + MgO и количества негасящихся зерен комовую известь разделяют на три сорта.
По скорости гашения комовая известь бывает: Быстрогасящаяся -8мин., Среднегасящаяся...25, Медленногасящаяся-25
Негашеную порошкообразную известь получают помолом комовой в шаровых мельницах в тонкий порошок. Часто в известь во время помола вводят активные добавки (гранулированные доменные шлаки, золы ТЭС и т. п.) в количестве 10...20 % от массы извести. Порошкообразная известь, как и комовая, делится на три сорта.
Преимущество порошкообразной извести перед комовой состоит в том, что при затворении водой она ведет себя подобно гипсовым вяжущим: сначала образует пластичное тесто, а через 20...40 мин схватывается. Это объясняется тем, что вода затворения, образующая тесто, частично расходуется на гашение извести.
При использовании порошкообразной извести воды берут 100...150 % от массы извести в зависимости от качества извести и количества активных добавок в ней. Определяют количество воды опытным путем.
Гидратная известь (пушонка) — тончайший белый порошок, получаемый гашением извести, обычно в заводских условиях, небольшим количеством воды (несколько выше теоретически необходимого). При гашении в пушонку известь увеличивается в объеме в 2...2,5 раза. Насыпная плотность пушонки — 400...450 кг/м3; влажность — не более 5 %.
Гашение извести можно производить как на строительстве объекта, так и централизованно. В последнем случае гашение совмещается с мокрым помолом непогасившихся частиц, что увеличивает выход извести и улучшает ее качество.
На строительстве известь гасят в гасильных ящиках (творилах). В ящик загружают комовую известь не более чем на 1/3 его высоты (толщина слоя обычно около 100 мм), поскольку при гашении известь увеличивается в объеме в 2,5...3,5 раза. Быстрогасящуюся известь заливают сразу большим количеством воды, чтобы не допустить перегрева и кипения воды, медленногасящуюся — небольшими порциями, следя за тем, чтобы известь не охладилась. Из 1 кг извести в зависимости ох ее качества получается 2...2,5 л известкового теста. Этот показатель называют «выход теста».
Воздушная известь — единственное вяжущее, которое превращается в тонкий порошок не только размолом, но и путем гашения водой.
Колоссальная удельная поверхность частиц Са(ОН)2 и их гидрофильность обусловливает большую водоудерживающую способность и пластичность известкового теста. После отстаивания известковое тесто содержит около 50% твердых частиц и 50% воды. Каждая частица окружена тонким слоем адсорбированной воды, играющей роль своеобразной смазки, что обеспечивает высокую пластичность известкового теста и смесей с использованием извести.
По окончании гашения жидкое известковое тесто через сетку сливают в известехранилище, где его выдерживают до тех пор, пока полностью не завершится процесс гашения (обычно не менее двух недель). Известковое тесто с размером непогасившихся зерен менее 0,6 мм можно применять сразу. Крупные непогасившиеся зерна опасны тем, что среди них могут быть пережженные зерна (пережог).
Содержание воды в известковом тесте не нормируется. Обычно в хорошо выдержанном тесте соотношение воды и извести около 1:1.
Твердение. Известковое тесто состоит из насыщенного водного раствора Са(ОН)2 и мельчайших нерастворившихся частиц извести; По мере испарения из него воды образуется пересыщенный раствор Са(ОН)2, из которого выпадают кристаллы, увеличивающие содержание твердой фазы. При этом происходит усадка твердеющей системы, которая в определенных условиях (например, при твердении известковой смеси на жестком основании — штукатурный слой) может вызвать растрескивание материала. Поэтому известь всегда применяют с заполнителями (например, известково-песчаные растворы) или в смеси с другими вяжущими для придания материалу пластичности.
Известковое тесто, защищенное от высыхания, неограниченно долго сохраняет пластичность, т. е. у такой извести «отсутствует» процесс схватывания. Затвердевшее известковое тесто при увлажнении вновь переходит в пластичное состояние (известь — неводостойкий материал).
Однако при длительном твердении (десятилетия) известь приобретает довольно высокую прочность и относительную водостойкость (например, в кладке старых зданий). Это объясняется тем, что на воздухе известь реагирует с углекислым газом, образуя нерастворимый в воде и довольно прочный карбонат кальция, т. е. как бы обратно переходит в известняк:Са(ОН)2 + СО2 → СаСО3 + Н2О
Процесс этот очень длительный, и полной карбонизации извести практически не происходит.
Существует мнение, что при длительном контакте извести с кварцевым песком в присутствии влаги между этими компонентами происходит взаимодействие с образованием контактного слоя из гидросиликатов. Это так же повышает прочность и водостойкость бетонов и кирпичной кладки на извести, имеющих возраст более 200...300 лет.
Применение, транспортирование, хранение. Воздушную известь применяют для приготовления кладочных и штукатурных растворов как самостоятельное вяжущее, так и в смеси с цементом; при производстве силикатного кирпича и силикатобетонных изделий; для получения смешанных вяжущих (известково-шлаковых, известково-зольных и др.) и для красок.
Негашеную известь, особенно порошкообразную, при транспортировании и хранении предохраняют от увлажнения. Порошкообразная известь - кипелка гасится даже влагой, содержащейся в воздухе. Максимальный срок хранения молотой извести в бумажных мешках 25 сут, в герметичной таре (металлические барабаны) — не ограничен.
Комовую известь транспортируют навалом в закрытых вагонах и автомашинах, порошкообразную — в бумажных мешках, а также в специальных автоцистернах. В таких же цистернах перевозят пушонку и известковое тесто.
Хранят комовую известь в сараях с деревянным полом, поднятым над землей на 30 см. Недопустимо попадание на известь воды, так как это может вызвать ее разогрев и пожар. На складах извести тушение пожара водой запрещается.
6. Магнезиальное вяжущее. Современной строительной наукой описан своеобразный «портрет» идеального материала будущего: «Он должен быть универсален - обладать одновременно высокими конструктивными способностями и теплоизолирующими свойствами; совершенно обязательно, чтобы он был негорючим, долговечным, влагостойким, экологически чистым и обладал достаточными декоративными качествами, исключающими необходимость в дополнительной наружной и отчасти внутренней отделки зданий и сооружений; желательно, чтобы он был получен из минерального сырья». К этому следует добавить, что подобный материал должен производиться на существующем технологическом оборудовании и, самое главное, быть конкурентоспособным в сравнении с узкопрофильными материалами-аналогами.
Но, как часто это бывает, все новое - это хорошо забытое старое, с которого лишь необходимо стряхнуть «вековую пыль» и слегка модернизировать. Оказывается, предшествующие поколения решили нашу проблему еще 150 лет назад.
Каустический магнезит, получаемый после обжига при относительно невысоких температурах некоторых природных минералов, в составе которых значительное количество карбоната или гидроксида магния (магнезит, доломит), затворенный водным раствором магниевых солей (сульфатом или хлоридом магния - бишофитом) близких по составу к морским, образует пластическую массу, обладающую вяжущими свойствами. Состав и свойства этого вяжущего были описаны еще в середине ХIХ века французским инженером Сорелем, положившим начало его применению в строительстве, а также названию московской производственно-строительной компании «Сорель-Эколоджи». Уникальность магнезиального вяжущего заключается в сочетании его высоких вяжущих свойств и совместимости практически с любыми видами заполнителей, в том числе органического природного и искусственного происхождения.
Цементный камень, образующийся на основе магнезиального вяжущего, является твердым раствором солей сложного состава. Именно на основе магнезиальных вяжущих получают различные камнеподобные материалы с заранее заданными свойствами под общим названием «магнолит».
В зависимости от того, какие наполнители используются, магнолит обладает следующими свойствами:
механической прочностью при сжатии, на уровне самых высокопрочных бетонов, (а при изгибе прочность превосходит бетоны в 3-5 раз! без использования дополнительных армирующих материалов), а также короткими сроками ее набора. Кроме того, это наиболее прочный из всех известных теплоизоляционных строительных материалов на минеральных вяжущих при равной с ними плотности;
· атмосферостойкостью на уровне большинства традиционных строительных материалов;
· абсолютной маслостойкостью и солестойкостю (при воздействие масел, нефтепродуктов, морской воды магнолиты только набирают прочность);
· декоративностью, то есть возможностью достоверно имитировать многие природные материалы (от дерева до малахита), чему способствует совместимость с различными пигментами, отличная полируемость, прозрачность вяжущего в тонком слое;
· пожаробезопасностью - при достаточной массивности конструкции из магнолита выдерживают пожар 5-й категории без деструкции материала и выделения каких-либо канцерогенных веществ;
· фунгицидностью, бактерицидностью и биоцидностью, что не позволяет развиваться грибкам и бактериям, а горько-соленый вкус бишофита препятствует также появлению насекомых и грызунов;
· обладает низкой диэлектрической проницаемостью и электропроводностью, стабильной во времени и мало зависящей от влажности окружающей среды. Для производства конструкций специального назначения, предназначенных для защиты от электромагнитных излучений, этот материал не заменим. Поверхности конструкций из магнезита не электризуются и исключают образование искр.
· магнезиальные напольные покрытия беспыльны, практически не имеют усадки, т.е. устраиваются сплошным покрытием не требуется нарезка деформационных швов, долговечны и высокопрочны, обладают высокой твердостью и низкой истираемостью, устойчивы к ударным нагрузкам. Обладают высокой адгезией практически ко всем видам органических и минеральных заполнителей в составе вяжущего, а также хорошим сцеплением к бетонным, кирпичным, деревянным основаниям.
Помимо прочих достоинств, консервирующие свойства магнолита позволяют применять даже токсичные заполнители при производстве строительных изделий, которые впоследствии будут иметь фон, удовлетворяющий санитарным нормам. А значительное количество химически связанной воды в магнезиальном цементном камне делает магнолит лучшим из существующих бетонов для биологической защиты от радиационного поражения. Магнезиальное вяжущее и изделия на его основе являются биологически инертными, то есть экологически безопасными.
Нет никаких сомнений в том, что у такого материала в России, где сосредоточено более половины мировых запасов магнезиального сырья, могут быть просто блестящие перспективы. И не случайно в последнее время наблюдается значительный всплеск интереса к нему.
Современные технологии позволяют делать из магнолита практически все, что угодно: стеновые материалы, конструкционные брусы, пеномагнолитовые блоки с фасадной облицовкой под кирпич или колотый камень, разнообразные половые покрытия, детали интерьера. Следует отметить, что в домах из магнолитовых конструкций создается благоприятный для человека микроклимат, сочетающий в себе достоинства деревянного дома и соляной пещеры, оказывающей бальнеологический эффект для больных астмой и другими аллергическими заболеваниями.
Большинство препятствий на пути массового применения магнолита как строительного материала уже преодолены. Наряду с действующим предприятием по добыче магнезиального сырья разведаны и подготовлены к добыче ряд новых месторождений магнезитов на Урале и в Восточной Сибири, ведется промышленная добыча бишофита скважинным методом. Бишофит представляет собой уникальный по своему составу экологически чистый минерал - водный хлорид магния MgCl2?6H2O и является продуктом кристаллизации солей замкнутых водных бассейнов. Впервые выявлен в цехштейнових отложениях Германии немецким ученым Густавом Бишофом, в честь которого со временем этот минерал был и назван.
Разработаны и эксплуатируются опытно-промышленные обжиговые агрегаты кипящего слоя, позволяющие получать недорогое магнезиальное вяжущее из самого распространенного магнезиального сырья - доломита.
Однако для широкого внедрения магнезиального вяжущего в строительную практику сегодня потребуется решить ряд проблем федерального масштаба: от разработки государственных стандартов и строительных норм касательно магнезиального вяжущего и строительных материалов на его основе - до организации добычи и переработки магнезиального сырья в промышленных объемах.
Жидкое стекло.
Жидкие стекла- растворы щелочных силикатов натрия и калия. В основном преобадают "стекло натриевое жидкое", "стекло калиевое жидкое", а также смешанные калиево-натриевые и натриево-калиевые жидкие стекла. Жидкое стекло принято характеризовать: по виду щелочного катиона (натриевые, калиевые, литиевые, четвертичного аммония); по массовому или мольному соотношению в стекле SiO2 и M2О (где М- это K, Na, Li или четвертичный аммоний), по абсолютному содержанию в жидком стекле SiO2 и M2O в масс.%; по содержанию примесных оксидов Al2O3, Fe2O3, CaO, MgO, SO3 и др.; по плотности растворов жидкого стекла (г/см3). Практическое использование жидких стекол осуществляется по одному из трех направлений. Первое направление связано с проявлением жидким стеклом вяжущих свойств - способности к самопроизвольному отвердеванию с образованием искусственного силикатного камня. Уникальной способностью жидкого стекла являются также его высокие адгезионные свойства к подложкам различной химической природы. Второе направление предусматривает применение жидких стекол в качестве источника растворимого кремнозема, т.е. исходного сырьевого компонента для синтеза различных кремнеземсодержащих веществ. Третья область относится к применению силикатов щелочных металлов в качестве химических компонентов в составе различных веществ.
|
|
Автоматическое растормаживание колес: Тормозные устройства колес предназначены для уменьшения длины пробега и улучшения маневрирования ВС при...
История развития хранилищ для нефти: Первые склады нефти появились в XVII веке. Они представляли собой землянные ямы-амбара глубиной 4…5 м...
Архитектура электронного правительства: Единая архитектура – это методологический подход при создании системы управления государства, который строится...
Историки об Елизавете Петровне: Елизавета попала между двумя встречными культурными течениями, воспитывалась среди новых европейских веяний и преданий...
© cyberpedia.su 2017-2024 - Не является автором материалов. Исключительное право сохранено за автором текста.
Если вы не хотите, чтобы данный материал был у нас на сайте, перейдите по ссылке: Нарушение авторских прав. Мы поможем в написании вашей работы!