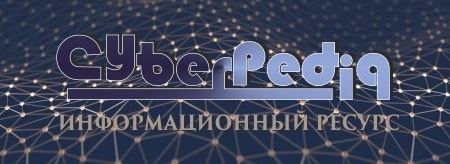
Организация стока поверхностных вод: Наибольшее количество влаги на земном шаре испаряется с поверхности морей и океанов (88‰)...
Историки об Елизавете Петровне: Елизавета попала между двумя встречными культурными течениями, воспитывалась среди новых европейских веяний и преданий...
Топ:
Определение места расположения распределительного центра: Фирма реализует продукцию на рынках сбыта и имеет постоянных поставщиков в разных регионах. Увеличение объема продаж...
Основы обеспечения единства измерений: Обеспечение единства измерений - деятельность метрологических служб, направленная на достижение...
Марксистская теория происхождения государства: По мнению Маркса и Энгельса, в основе развития общества, происходящих в нем изменений лежит...
Интересное:
Принципы управления денежными потоками: одним из методов контроля за состоянием денежной наличности является...
Что нужно делать при лейкемии: Прежде всего, необходимо выяснить, не страдаете ли вы каким-либо душевным недугом...
Уполаживание и террасирование склонов: Если глубина оврага более 5 м необходимо устройство берм. Варианты использования оврагов для градостроительных целей...
Дисциплины:
![]() |
![]() |
5.00
из
|
Заказать работу |
|
|
Физические свойства металлов.
К физическим свойствам относятся плотность, плавление (температура плавления), теплопроводность, тепловое расширение.
Плотность — количество вещества, содержащееся в единице объема.
Плавление — способность металла переходить из кристаллического (твердого) состояния в жидкое с поглощением теплоты.
Теплопроводность — способность металла с той или иной скоростью проводить теплоту при нагревании.
Электропроводность — способность металла проводить электрический ток.
Тепловое расширение — способность металла увеличивать свой объем при нагревании.
Химические свойства металлов.
Химические свойства металлов характеризуют отношение их к химическим воздействиям различных активных сред. Каждый металл обладает определенной способностью сопротивляться этим воздействиям. Основными химическими свойствами металлов являются окисляемость и коррозионная стойкость.
Окисляемость — способность металла вступать в реакцию в кислородом под воздействием окислителей.
Коррозионная стойкость —способность металла сопротивляться коррозии.
Механические свойства металлов.
К механическим свойствам металлов относят твердость, прочность, вязкость, упругость и пластичность.
Твердость — способность металла сопротивляться проникновению в него более твердого тела.
Прочность — способность металла сопротивляться разрушению под действием внешних сил.
Вязкость — способность металла сопротивляться быстро возрастающим ударным нагрузкам.
Упругость — способность металла восстанавливать свою первоначальную форму и размеры после снятия действующей нагрузки.
Пластичность — способность металла, не разрушаясь, изменять свою форму под действием нагрузки и сохранять полученную форму после снятия нагрузки.
|
Технологические свойства металлов.
Технологические свойства металлов определяют их способность подвергаться различным видам обработки. Основными технологическими свойствами металлов являются ковкость, свариваемость, жидкотекучесть, прокаливаемость, обработка резанием.
Ковкость — способность металла изменять свою форму в нагретом или холодном состоянии под действием внешних сил.
Свариваемость — способность двух частей металла при нагревании прочно соединяться друг с другом.
Жидкотекучесть — способность расплавленного металла легко растекаться и хорошо заполнять форму.
Прокаливаемость — способность металла закаливаться на ту или иную глубину.
Обрабатываемость резанием — способность металла подвергаться механической обработке режущим инструментом с определенной скоростью и усилием резания.
№ 2. Конструкционные (углеродистые и легированные) стали. Их маркировка и область применения.
Конструкционная сталь — сталь, которая применяется для изготовления различных деталей, механизмов и конструкций в машиностроении и строительстве и обладает определёнными механическими, физическими и химическими свойствами. Конструкционные стали подразделяются на несколько подгрупп.
Качество конструкционных углеродистых сталей определяется наличием в стали вредных примесей фосфора (P) и серы (S). Фосфор придаёт стали хладноломкость (хрупкость). Сера — самая вредная примесь — придаёт стали красноломкость. Содержание вредных примесей в стали:
Обыкновенного качества — P и S — до 0,05 % (маркировка Ст).
Качественная — P и S — до 0,035 % (маркировка Сталь).
Высококачественная — P и S — до 0,025 % (маркировка А в конце марки).
Особовысококачественная — Р и S — до 0,015 % (маркировка Ш в конце марки).
Стали конструкционные углеродистые обыкновенного качества[править | править вики-текст]
|
Широко применяются в строительстве и машиностроении как наиболее дешёвые, технологичные, обладающие необходимыми свойствами при изготовлении конструкций массового назначения. В основном эти стали используют в горячекатанном состоянии без дополнительной термической обработки с ферритно-перлитной структурой.
В зависимости от последующего назначения конструкционные углеродистые стали обыкновенного качества подразделяют на три группы: А, Б, В.
Стали группы А
Поставляются с определёнными регламентированными механическими свойствами. Их химический состав не регламентируется. Эти стали применяются в конструкциях, узлы которых не подвергаются горячей обработке — ковке, горячей штамповке, термической обработке и т. д. В связи с этим механические свойства горячекатаной стали сохраняются.
Стали группы Б
Поставляются с определённым регламентированным химическим составом, без гарантии механических свойств. Эти стали применяются в изделиях, подвергаемых горячей обработке, технология которой зависит от их химического состава, а конечные механические свойства определяются самой обработкой.
Стали группы В
Поставляются с регламентируемыми механическими свойствами и химическим составом. Эти стали применяются для изготовления сварных конструкций. Их свариваемость определяется химическим составом, а механические свойства вне зоны сварки определены в состоянии поставки. Такие стали применяют для более ответственных деталей.
По степени раскисления
Степень раскисления определяется содержанием кремния (Si) в этой стали. По степени раскисления углеродистые стали обыкновенного качества делятся на:
спокойные (СП) — не менее 0,12 % (Si)
полуспокойные (ПС) — 0.07-0.12 % (Si)
кипящие (КП) — не более 0,07 % (Si)
Маркировка
Основные марки конструкционных углеродистых сталей обыкновенного качества:
Ст1кп2; БСт2пс; ВСт3Гпс; Ст4-2; … ВСт6сп3.
Буква перед маркой показывает группу стали. Сталь группы А буквой не обозначается.
Ст — показывает, что сталь обыкновенного качества.
Первая цифра — номер по ГОСТу (от 0 до 6).
Буква Г после первой цифры — повышенное содержание марганца (Mn) (служит для повышения прокаливаемости стали).
сп; пс; кп — степень раскисления стали (Для стали группы А отсутствие обозначения подразумевает «сп»).
|
Вторая цифра — номер категории стали (от 1 до 6 — основные механические свойства). Сталь 1-й категории цифрой не обозначается.
Тире между цифрами указывает, что заказчик не предъявлял требований к степени раскисления стали.
Применение[править | править вики-текст]
Ст1; Ст2 — проволока, гвозди, заклёпки.
Ст3; Ст4 — крепёжные детали, фасонный прокат.
Ст5; Ст6 — слабонагруженные валы, оси.
Стали углеродистые качественные[править | править вики-текст]
Качественными углеродистыми сталями являются стали марок: Сталь08; Сталь10; Сталь15 …; Сталь78; Сталь80; Сталь85,
Также к этому классу относятся с повышенным содержанием марганца (Mn — 0.7-1.0 %): Сталь 15Г; 20Г … 65Г, имеющие повышенную прокаливаемость.
Маркировка
Сталь — слово «Сталь» указывает, что данная углеродистая сталь качественная. (В настоящее время слово «Сталь» не пишется, указывается только индекс и последующие буквы)
Цифра — указывает на содержание в стали углерода (С) в сотых долях процента.
Применение
Низкоуглеродистые стали марок Сталь08, Сталь08КП, Сталь08ПС относятся к мягким сталям, применяемым чаще всего в отожжённом состоянии для изготовления деталей методом холодной штамповки - глубокой вытяжки. Стали марок Сталь10, Сталь15, Сталь20, Сталь25 обычно используют как цементируемые, а высокоуглеродистые Сталь60 … Сталь85 — для изготовления пружин, рессор, высокопрочной проволоки и других изделий с высокой упругостью и износостойкостью.
Сталь30 … Сталь50 и аналогичные стали с повышенным содержанием марганца Сталь30Г, Сталь40Г, Сталь50Г применяют для изготовления самых разнообразных деталей машин.
Маркировка
В начале обозначения марки автоматной стали всегда стоит буква «А», например А12, А20, А35.
Маркировка
Две цифры в начале маркировки указывают на конструкционные стали. Это содержание в стали углерода в сотых долях процента.
Буква без цифры — определённый легирующий элемент с содержанием в стали менее 1 %.(А — азот, Р — бор, Ф — ванадий, Г — марганец, Д — медь, К — кобальт, М — молибден, Н — никель, С — кремний, Х — хром, П — фосфор, Ч — редкоземельные металлы, В — вольфрам, Т — титан, Ю — алюминий, Б — ниобий)
|
Буква и цифра после неё — определённый легирующий элемент с содержанием в процентах (цифра).
Буква А в конце маркировки — указывает на высококачественную сталь.
Например 38Х2Н5МА — это среднелегированная высококачественная хромоникелевая конструкционная сталь. Химический состав: углерод — около 0,38 %; хром — около 2 %; никель — около 5 %; молибден — около 1 %.
Маркировка
ШХ9, ШХ15. Содержание углерода — около 1 %; Содержание хрома в десятых долях процента (например: ШХ15 — хром — около 1,5 %)
Пороки формы ствола
Сбежистость. Для всех стволов деревьев характерно постепенное уменьшение диаметра в направлении от комля к вершине (сбег). Если на каждый метр высоты ствола (длины сортимента) диаметр уменьшается более чем на 1 см, то такое явление считается пороком — сбежистостью.
Закомелистость. Это такой случай сбежистости, когда наблюдается резкое увеличение диаметра в нижней части ствола.
Овальность. Так называется эллипсовидность формы торца круглых лесоматериалов, при которой наибольший диаметр не менее чем в 1,5 раза превышает меньший.
Наросты. Так называют местные утолщения ствола. Они могут быть с гладкой или бугристой окоренной поверхностью и спящими почками (капы).
Кривизна. Искривление ствола по длине встречается у всех древесных пород. Вследствие потери верхушечного побега и замены его боковой ветвью, из-за наклона дерева в сторону лучшего освещения, при росте на горных склонах и по другим причинам ствол дерева может оказаться искривлённым.
Пороки строения древесины
Наклон волокон. Отклонение волокон от продольной оси сортимента (раньше этот порок назывался косослоем) встречается у всех пород.
Свилеватость. Так называется извилистое и беспорядочное расположение волокон, которое встречается чаще всего у лиственных пород.
Завиток. Это местное искривление годичных слоёв у сучков и проростей. На боковых поверхностях пилопродукции и в шпоне заметны скобообразные, изогнутые или замкнутые концентрические контуры искривлённых годичных слоёв.
Реактивная древесина. В наклонённых и изогнутых стволах и ветвях образуется особая древесина, получившая в мировой ботанической литературе название реактивной. Этот порок возникает под действием силы тяжести, вызывающей перераспределение веществ, стимулирующих или подавляющих ростовые процессы, ветровой нагрузки, напряжений роста, осмотического давления и других факторов.
Крень. Этот порок строения древесины хвойных пород выражается в кажущемся увеличении ширины поздней зоны годичных слоёв. Креневая древесина лишь по цвету напоминает позднюю. Крень образуется преимущественно в сжатой зоне изогнутых или наклонённых стволов, т.е. на нижней, обращённой к земле стороне.
|
Тяговая древесина. Этот порок строения древесины лиственных пород по происхождению родственен крени, но в отличие от крени он образуется в верхней (растянутой) зоне искривлённых или наклонённых стволов и ветвей некоторых пород (бук, тополь и др.).
Ложное ядро. Так называется тёмноокрашенная внутренняя зона древесины лиственных пород (берёзы, бука, ольхи, осины, клёна, граба, липы и др.). Граница ложного ядра обычно не совпадает с годичными кольцами. От заболони оно отделено чаще тёмной, реже светлой (например, у берёзы) каймой.
Внутренняя заболонь. В древесине у дуба, ясеня (иногда и у других лиственных пород) в зоне ядра могут образовываться несколько смежных годичных слоёв, похожих на заболонь по цвету и другим свойствам.
Пятнистость. В древесине растущих деревьев лиственных пород вследствие раневой реакции, воздействия химических факторов, грибов и насекомых образуются сравнительно небольшие по размеру тёмноокрашенные участки древесины (по цвету напоминающие ядро и сердцевину).
Сердцевина. В круглых сортиментах присутствие сердцевины неизбежно, поэтому в них она пороком не считается. В пилопродукции измеряют глубину залегания сердцевины, считая от ближайшей пласти или кромки.
Пасынок представляет собой отставшую в росте или отмершую вторую вершину ствола, которая пронизывает сортимент под острым углом к его продольной оси на значительном протяжении.
Достоинства цепных передач
1. Передача движения зацеплением, а не трением позволяет передавать большие мощности, чем с помощью ремня;
2. Практически не требуется натяжение цепи, следовательно, уменьшается нагрузка на валы и опоры;
3. Отсутствие скольжения и буксования обеспечивает постоянство среднего передаточного отношения;
4. Цепи могут устойчиво работать при меньших межосевых расстояниях и обеспечить большее передаточное отношение, чем ремённая передача;
5. Цепные передачи хорошо работают в условиях частых пусков и торможений;
6. Цепные передачи имеют высокий КПД.
Недостатки цепных передач
1. Износ цепи при недостаточной смазке и плохой защите от грязи;
2. Сложный уход за передачей;
3. Повышенная вибрация и шум;
4. По сравнению с зубчатыми передачами повышенная неравномерность
движения;
5. Удлинение цепи в результате износа шарниров и сход цепи со звёздочек.
Главный элемент цепной передачи – приводная цепь, которая состоит из соединенных шарнирами звеньев.
Основными типами приводных цепей являются втулочные, роликовые и зубчатые, которые стандартизованы и изготовляются специализированными заводами.
В зависимости от передаваемой мощности втулочные и роликовые цепи изготовляют однорядными и многорядными с числом рядов 2…4.
Роликовые цепи состоят из двух рядов наружных и внутренних пластин. В наружные пластины запрессованы валики, пропущенные через втулки, на которые запрессованы внутренние пластины. Валики и втулки образуют шарниры. На втулки свободно надеты закаленные ролики. Зацепление цепи со звездочкой происходит через ролик, который перекатывается по зубу и уменьшает его износ. Кроме того, ролик выравнивает давление зуба на втулку и предохраняет ее от изнашивания. Роликовые цепи имеют широкое распространение.
Втулочные цепи по конструкции аналогичны предыдущим, но не имеют роликов, что удешевляет цепь, уменьшает ее массу, но увеличивает износ. Втулочные цепи применяют в неответственных передачах.
Зубчатые цепи состоят из набора пластин зубообразной формы, шарнирно соединенных между собой. Число пластин определяет ширина цепи В, которая зависит от передаваемой мощности. Рабочими гранями пластин являются плоскости зубьев, расположенные под углом 60, которыми каждое звено цепи садится на два зуба звездочки. Благодаря этой особенности зубчатые цепи обладают минимально возможным шагом и поэтому допускают более высокие скорости. Для устранения бокового спадания цепи со звездочки применяют направляющие пластины, расположенные по середине цепи или по бокам ее. Зубчатые цепи по сравнению с другими работают более плавно, с меньшим шумом, лучше воспринимают ударную нагрузку, но тяжелее и дороже.
Цепи должны быть износостойкими и прочными. Их изготавливают из сталей 50, 40Х.
Звездочки по конструкции отличаются от зубчатых колес только профилем зубьев. Для увеличения долговечности цепной передачи по возможности принимают большее число зубьев меньшей звездочки. При большем числе зубьев большее число звеньев находится в зацеплении. Это повышает плавность передачи, уменьшает износ цепи. Однако при большом числе зубьев даже у мало изношенной цепи в результате радиального сползания по профилю зубьев цепь соскакивает со звездочки. Поэтому максимальное число зубьев большой звездочки ограничено: для втулочной цепи ,для роликовой
,для зубчатой
.Число зубьев малой звездочки z1 принимают из условия обеспечения плавности работы и минимальных габаритов. Для роликовых и втулочных цепей
.
Передаточное число цепной передачи:
Материал звездочек должен быть износостойким и хорошо сопротивляться ударным нагрузкам.
№ 15. Способы распространения тепла и виды теплообмена. Классификация теплообменных аппаратов.
Теплообменом называется перенос тепла от одних тел к другим или одних частей тела к другим, вызываемый разностью температур. Процесс теплообмена – это сложный процесс, он связан с конвективной и молекулярной диффузией и определяется законами аэродинамики, газодинамики, термодинамики, передачи энергии в форме теплоты, передачи лучистой энергии и превращением ее в теплоту и наоборот.
Теплообмен характеризуется выравниванием температуры и осуществляется тремя способами: теплопроводностью, конвекцией, излучением.
Теплопроводность – это передача тепла молекулярной диффузией, т.е. перенос тепловой энергии осуществляется от частиц обладающих большей энергией к частицам с меньшей энергией. Теплопроводность наблюдается только в твердых телах и неподвижных слоях жидкости или газа.
Конвекция – передача тепла потоками жидкости или газа из одной области пространства в другую. Конвекция бывает свободной и вынужденной.
Свободная конвенция возникает из-за разности плотностей нагретой и холодной среды. При вынужденной конвенции движущиеся потоки создаются принудительно – компрессором, вентилятором и т.д.
Конвекция сопровождается переносом тепла теплопроводностью в пограничных слоях. Совместный процесс конвекции и теплопроводности называется конвективным теплообменом.
Излучение – это передача тепловой энергии путем электромагнитных колебаний. Процесс передачи тепла излучением можно условно разделить на 3 этапа: 1. Преобразование внутренней энергии системы в энергию электромагнитных волн; 2. Распространение этих волн в среде, разделяющей источник и приемник. 3.Реакция приемника на излучение.
В реальных условиях названные способы переноса тепла протекают одновременно: такое физическое явление называется сложным теплообменом. Его закономерности могут быть установлены на основе закономерностей простых видов теплообмена.
Два вида теплообмена между телами — конвективный и лучистый.
Конвекцией называется процесс распространения теплоты путем перемещения жидкости или газа в пространстве из области с одной температурой в область с другой. Конвекция в отличие от распространения теплоты теплопроводностью может происходить только в жидкостях и газах и обусловливается перемещением самой среды. Конвекция всегда сопровождается теплопроводностью, поскольку при перемещении жидкости или газа отдельные части тела, имеющие разные температуры, всегда соприкасаются.
При лучистом теплообмене происходит двойное превращение энергии. Внутренняя энергия излучающего тела сначала переходит в лучистую, т.е. в энергию, переносимую излучением, а затем лучистая энергия распространяется в пространстве, пока не встретит непрозрачное тело, которое полностью или частично поглотит эту лучистую энергию. При этом происходит преобразование лучистой энергии во внутреннюю энергию поглощающего тела.
Теплообменные аппараты – устройства, в которых осуществляется процесс передачи теплоты от одного теплоносителя к другому. По принципу действия теплообменные аппараты (теплообменники) разделяются на рекуперативные, регенеративные и смесительные.
В рекуперативных теплообменниках горячая и холодная среда протекают одновременно и теплота передается через разделяющую их стенку (котлы, подогреватели, испарители, конденсаторы и др.). В регенеративных теплообменниках одна и та же поверхность нагрева через определенные промежутки времени омывается то горячим, то холодным теплоносителем. В период контакта стенки с горячим теплоносителем стенка нагревается, а в период подачи холодной среды охлаждается, нагревая среду за счет аккумулированной теплоты. К таким аппаратам относятся воздухоподогреватели газотурбинных установок, мартеновских и доменных печей.
Смесительные теплообменники предназначены для осуществления тепло- и массообмеиных процессов при непосредственном контакте теплоносителей. К таким теплообменникам относятся оросительные полые, иасадочиые и барботажные аппараты. Наибольшее применение в промышленности находят рекуперативные теплообменники, которые по взаимному направлению движения теплоносителей разделяют на прямоточные, противоточные, с перекрестным и смешанным током.
По принципу взаимодействия теплоносителей различают системы: жидкость-жидкость, пар- жидкость, газ-жидкость, пар- пар, пар- газ и газ- газ. По конструктивным признакам рекуперативные теплообменники подразделяются на змеевиковые, трубчатые, труба в трубе, кожухо-трубчатые, спиральные, пластинчатые и специальные. Наиболее доступными и распространенными теплоносителями, применяемыми в теплообменниках, являются вода, водяной пар, воздух, дымовые газы. В ряде случаев более эффективными оказываются кремнийорганическне, жидкометаллические и другие высокотемпературные теплоносители.
№ 16. Характеристика и области применения двигателей внутреннего сгорания. Классификация ДВС. Рабочий процесс в двигателях внутреннего сгорания.
Двигатель внутреннего сгорания – двигатель, в котором топливо сгорает непосредственно в рабочей камере (внутри) двигателя. ДВС преобразует тепловую энергию от сгорания топлива в механическую работу.
По сравнению с двигателями внешнего сгорания ДВС: не имеет дополнительных элементов теплопередачи – топливо, сгорая, само образует рабочее тело; компактнее, так как не имеет целого ряда дополнительных агрегатов; легче; экономичнее; потребляет газообразное или жидкое топливо, обладающее весьма жёстко заданными параметрами (испаряемостью, температурой вспышки паров, плотностью, теплотой сгорания, октановым или цетановым числом), так как от этих свойств зависит сама работоспособность ДВС.
Применение двигателей внутреннего сгорания чрезвычайно разнообразно. Они приводят в движение самолеты, теплоходы, автомобили, тракторы, тепловозы. Мощные двигатели внутреннего сгорания устанавливают на речных и морских судах.
Типы ДВС
Поршневые двигатели – камера сгорания содержится в цилиндре, тепловая энергия превращается в механическую с помощью кривошипно-шатунного механизма.
Газовая турбина – преобразование энергии осуществляется ротором с клиновидными лопатками.
Жидкостный ракетный двигатель и воздушно-реактивный двигатель преобразуют энергию сгорающего топлива непосредственно в энергию реактивной газовой струи.
Роторно-поршневые двигатели – в них преобразование энергии осуществляется за счёт вращения рабочими газами ротора специального профиля (двигатель Ванкеля).
ДВС классифицируют: по назначению – на транспортные, стационарные и специальные. по роду применяемого топлива — лёгкие жидкие (бензин, газ), тяжёлые жидкие (дизельное топливо, судовые мазуты). по способу образования горючей смеси – внешнее (карбюратор) и внутреннее (в цилиндре ДВС). по объёму рабочих полостей и весогабаритным характеристикам – лёгкие, средние, тяжёлые, специальные. по количеству и расположению цилиндров.
Рабочий цикл осуществляется следующим образом. Топливо и воздух в определенных соотношениях перемешиваются вне цилиндра двигателя и образуют горючую смесь. Полученная смесь поступает в цилиндр (впуск), после чего она подвергается сжатию. Сжатие смеси, как будет показано ниже, необходимо для увеличения работы за цикл, так как при этом расширяются температурные пределы, в которых протекает рабочий процесс. Предварительное сжатие создает также лучшие условия для сгорания смеси воздуха с топливом.
Во время впуска и сжатия смеси в цилиндре происходит дополнительное перемешивание топлива с воздухом. Подготовленная горючая смесь воспламеняется в цилиндре при помощи электрической искры. Вследствие быстрого сгорания смеси в цилиндре резко повышается температура и, следовательно, давление, под воздействием которого происходит перемещение поршня от ВМТ к НМТ. Положение поршня в цилиндре, при котором расстояние его от оси вала двигателя достигает максимума, называется верхней мертвой точкой (ВМТ). Нижней мертвой точкой (НМТ) называют такое положение поршня в цилиндре, при котором расстояние его от оси вала двигателя достигает минимума. В процессе расширения нагретые до высокой температуры газы совершают полезную работу. Давление, а вместе с ним и температура газов в цилиндре при этом понижаются. После расширения следует очистка цилиндра от продуктов сгорания (выпуск), и рабочий цикл повторяется.
Физические свойства металлов.
К физическим свойствам относятся плотность, плавление (температура плавления), теплопроводность, тепловое расширение.
Плотность — количество вещества, содержащееся в единице объема.
Плавление — способность металла переходить из кристаллического (твердого) состояния в жидкое с поглощением теплоты.
Теплопроводность — способность металла с той или иной скоростью проводить теплоту при нагревании.
Электропроводность — способность металла проводить электрический ток.
Тепловое расширение — способность металла увеличивать свой объем при нагревании.
|
|
История развития хранилищ для нефти: Первые склады нефти появились в XVII веке. Они представляли собой землянные ямы-амбара глубиной 4…5 м...
Состав сооружений: решетки и песколовки: Решетки – это первое устройство в схеме очистных сооружений. Они представляют...
Эмиссия газов от очистных сооружений канализации: В последние годы внимание мирового сообщества сосредоточено на экологических проблемах...
Индивидуальные очистные сооружения: К классу индивидуальных очистных сооружений относят сооружения, пропускная способность которых...
© cyberpedia.su 2017-2024 - Не является автором материалов. Исключительное право сохранено за автором текста.
Если вы не хотите, чтобы данный материал был у нас на сайте, перейдите по ссылке: Нарушение авторских прав. Мы поможем в написании вашей работы!