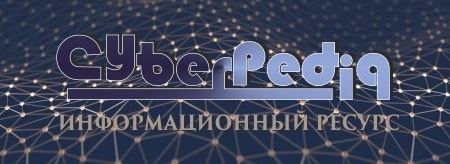
Архитектура электронного правительства: Единая архитектура – это методологический подход при создании системы управления государства, который строится...
Индивидуальные и групповые автопоилки: для животных. Схемы и конструкции...
Топ:
Оснащения врачебно-сестринской бригады.
Генеалогическое древо Султанов Османской империи: Османские правители, вначале, будучи еще бейлербеями Анатолии, женились на дочерях византийских императоров...
Определение места расположения распределительного центра: Фирма реализует продукцию на рынках сбыта и имеет постоянных поставщиков в разных регионах. Увеличение объема продаж...
Интересное:
Средства для ингаляционного наркоза: Наркоз наступает в результате вдыхания (ингаляции) средств, которое осуществляют или с помощью маски...
Наиболее распространенные виды рака: Раковая опухоль — это самостоятельное новообразование, которое может возникнуть и от повышенного давления...
Финансовый рынок и его значение в управлении денежными потоками на современном этапе: любому предприятию для расширения производства и увеличения прибыли нужны...
Дисциплины:
![]() |
![]() |
5.00
из
|
Заказать работу |
Содержание книги
Поиск на нашем сайте
|
|
Содержание
Введение. 2
1 Описательная часть. 3
1.1 Состав и свойства промышленного электролита. 3
1.2 Конструкция электролизера с самообжигающимся анодом.. 4
1.3 Оборудование, применяемые для обработки электролизера. 8
2 Расчётная часть. 11
2.1 Материальный баланс. 11
2.2 Конструктивный расчет электролизера. 13
2.3 Электрический баланс электролизёра. 16
2.4 Тепловой баланс электролизёра. 18
2.5 Расчёт цеха. 21
3 Специальная часть. Виды твердых отходов электролиза алюминия и их переработка. 23
3.1 Виды твердых отходов. 23
3.2 Переработка угольной пены процесса электролиза алюминия. 23
3.3 Утилизация футеровки электролизера. 24
3.4 Обзор предлагаемых технологических схем переработки отходов производства алюминия 25
3.5 Предлагаемый метод переработки твёрдых отходов и шламовых полей. 26
3.6 Результаты и выводы.. 28
4 Экономическая часть. 29
4.1. Расчет производственной программы.. 29
4.2 Расчет численности рабочих. 29
4.3 Расчет фонда оплаты труда рабочих. 32
4.4 Расчет цеховых расходов. 36
4.5 Расчет расходов на содержание и эксплуатацию оборудования (РСЭО) 39
4.6 Расчет себестоимости 1 тонны алюминия и всего объема. 39
4.7 Расчет основных технико-экономических показателей проекта. 40
5 Промышленная безопасность и экология. 44
5.1 Средства коллективной и индивидуальной защиты в электролиз-ных корпусах. 44
5.2 Сохранение экологии при переработке твёрдых отходов электролиза. 47
Заключение. 55
Список использованных источников. 56
Введение
Алюминий — этот важнейший представитель легких металлов, нашел себе исключительно широкое применение в самых разнообразных отраслях современной техники благодаря тому, что обладает такими свойствами, как малый удельный вес, высокая электропроводность, достаточная механическая прочность и большая коррозионная стойкость по отношению к ряду химических веществ.
По масштабам производства и потребления алюминий занимает первое место среди подотраслей цветной металлургии, а среди отраслей металлургии по объёму уступает лишь производству стали. Важнейшими потребителями продукции алюминиевой промышленности являются: авиационная, электротехническая, автомобильная и ряд других отраслей машиностроительной и металлообрабатывающей промышленности, а также строительство, железнодорожный транспорт, химическая, пищевая промышленность. Всего за 2015 год производство первичного алюминия в мире достигло уровня в 57,889 млн. тонн. Технологии прошлого века действуют до сих пор с нормальными показателями, достигнутыми за счет новых видов сырья и его подготовки, интенсификации процесса электролиза, а главное, конструкции электролизеров рассчитанных с помощью информационно-математических моделей.
|
Современное управление большим производством немыслимо без полной механизации и автоматизации производства, и в 21 веке решающее значение имеет управление организацией производства, самим производством, а так же оборудованием и персоналом.
В дипломном проекте приведены расчёты материального, электрического и теплового балансов, расчёты конструктивных элементов электролизёра. Экономические расчеты подтверждают рентабельность и целесообразность проекта цеха электролиза.Так же в дипломный проект входит графическая часть на 4 листах формата А1, выполненная в соответствии с требованиями ЕСКД.
Описательная часть
1.1 Состав и свойства промышленного электролита
Электролит - это среда, в которой протекают основные электрохимические превращения в алюминиевой ванне. К составу электролитавыдвигается целый ряд обязательных условий.
Катодное устройство
Катодное устройство алюминиевого электролизера предназначено для создания условий, необходимых для протекания процесса электролиза в криолитно-глиноземном расплаве. Поскольку электролиз идет в весьма агрессивной среде при 950—1 000 °С, катодное устройство должно быть устойчиво к действию расплавленных фтористых солей; обладать достаточно высокими теплоизоляционными свойствами, чтобы до минимума сократить потери тепла, быть электропроводным в зоне протекания процесса и иметь надежную изоляцию во избежание утечек тока; иметь достаточно жесткую конструкцию, способную выдержать напряжения, возникающие от протекания физико-химических реакций; обеспечивать продолжительную работоспособность между ремонтами и мобильность при замене в целях сокращения простоя электролизера в ремонте. приводится схема катодного устройства современного электролизера.
|
От прочности катодного кожуха в большой степени зависит продолжительность межремонтного срока работы электролизера В связи с ростом единичной мощности электролизеров все большее распространение получают катодные кожухи рамного типа прямо угольной формы без металлического днища и контрфорсного типа с днищем.
Катодное устройствосостоит из стального кожуха футерованого теплоизоляционным кирпичом и углеродистыми подовыми блоками с токоведущими блюмсами, бортовыми блоками.
В результате пропитки футеровки расплавом, натриевого и температурного расширения, объём футеровки возрастает, возникают большие усилия, действующие на стенки катодного кожуха. Это приводит к его деформации, разрушению футеровки и сокращению срока службы электролизёра.
Катодные кожухи
Контрфорсный кожух представляет собой «корыто из листовой стали. С помощью стяжных шпилек прижимаются контрфорсы (от семи и более пар), нижний конец которых упирается в торцы бетонной балки. Возникающие в подине усилия воспринимаются контрфорсами, а распорная балка препятствует деформации, придавая правильную геометрическую форму катоду в процессе его эксплуатации.
Изнутри кожух футеруется угольными с добавками графитного материала, огнеупорными (шамотный кирпич) и теплоизоляционными материалами (пенодиатомитный кирпич, вермикулитовые плиты, шамотная крупка). Днище выполнено из толстолистовой стали 16-18мм, и укреплено усиленной рамой вдоль и поперек 20мм. По периметру борта катодного кожуха усилены швеллерами и двутаврами. Сверху над футеровкой катодного кожуха делается фланцевый лист.
Состав торкретмассы:
75% - шамотная крупка
20% - мертель
5-10% - кремнефтористый Na
жидкое стекло 50-70%.
,
Рисунок 2 – Катодный кожух контрфорсного типа
Угольная футеровка катодного кожухамонтируется на цоколе из теплоизоляционных материалов. Такая футеровка стойка против воздействия криолитового расплава и сравнительно хорошо проводит ток, что особенно важно, так как подина служит катодом электролизера.
Её качество во многом определяет срок службы ванны.
Используемые в промышленности катодные блоки классифицируются:
1 Графитированные. Весь блок (наполнитель и связующее) изготавливается из графитизируемых материалов, подвергается термообработке обычно до 3 000 ˚С.
2 Графитизированные. Изготавливается из тех же материалов, что и графитированные, но обжигается при более низких температурах – до 2 300 ˚С.
3 Полуграфитовые. Наполнитель графитизирован, но коксовое связующее обожжено до 1 200 ˚С.
4 Антрацитовые. Наполнителем является антрацит, зачастую добавляется немного графита.
От прочности катодного кожуха в большой степени зависит продолжительность межремонтного срока работы электролизера. В связи с ростом единичной мощности электролизеров все большее распространение получают катодные кожухи рамного типа прямо угольной формы без металлического днища и контрфорсного типа с днищем.
|
Катодные кожухи с днищем состоят из двух частей: корыта кожуха, сваренного из листовой стали, и балок — контрфорсов. Прочность таких кожухов определяется жесткостью конструкции контрфорсов, число которых зависит от длины электролизера. Бортовой лист, кронштейны для его крепления, окна для катодных стержней в кожухе этого типа выполняются так же, как и в кожухе рамного типа без днища.
Подина
На отечественных алюминиевых заводах подины электролизеров выполняются из обожженных угольных блоков. Подина электролизера служит для отвода тока от жидкого алюминия к катодным стержням и для защиты всего катодного устройства от разрушающего действия расплава.
Подовая масса: служит для набойки межблочных и периферийных швов, для ремонта бортовой футеровки, а также для накатки подушки под подовые блоки. Её изготавливают из антрацита, графита или прокалённого кокса, а в качестве связующего используют каменноугольную смолу, пек, полимеры.
На степень уплотнения подовой массы при набойке швов подины значительное влияние оказывает температура самой массы и катодных материалов.
Подину любого типа перед началом электролиза обжигают, чтобы удалить из подовой массы летучие составляющие связующего материала (пека) и превратить подину в монолитный плотный массив, хорошо проводящий электрический ток. Ток к подине подводится по стальным полосам квадратного или прямоугольного сечения, называемым катодными стержнями—блюмсами. Отечественной промышленностью выпускаются прошивные катодные блоки высотой 400 мм, шириной 550 мм, длиной 600—2 200 мм. Катодные стержни заделывают в угольные блоки специальной углеродистой массой или заливают чугуном. Назначение чугунной заливки или углеродистой набивки — создание механически прочного и хорошо проводящего электричество соединения катодного стержня с угольным блоком. Такая пара образует подовую секцию.
При монтаже подовых секций предусматривается предохранение торцового конца блюмса от проникновения расплавленного алюминия, для чего в эту часть паза блока набивают углеродистую массу (80 — 100 мм).
Подовые блоки изготавливают на мощных прессах продавливанием угольной массы через мундштук, по форме отвечающий нужной конфигурации блока. Специальная насадка позволяет получать блоки с необходимым для заделки блюмсов пазом. Число катодных стержней в подине выбирают таким, чтобы плотность тока в них не превышала 0,18—0,20 А/мм2.
Анодное устройство
Анодное устройство алюминиевого электролизера, являясь одним из электродов, предназначено для подвода тока в зону непосредственного протекания процесса электролиза. Основным материалом анода служит углеродистый материал. По мере протекания процесса электролиза анод постепенно окисляется, и его необходимо периодически опускать. Для этого служит специальный подъемный механизм анодного устройства.
|
Анодное устройствосостоит из собственногоугольного анода с токоведущими сталеалюминиевыми штырями, анодного кожуха, газосборного колокола, анодной рамы с эксцентриковыми зажимами для крепления анодных штырей, основных и вспомогательных механизмов подъёма анода. Основные механизмы предназначены для подъёма анодной рамы, вспомогательные механизмы предназначены для подъёма анодного кожуха. Анодные штыри располагаются в теле анода на нескольких горизонтах. Количество анодных штырей определяется мощностью электролизёра. В нижней части анодного кожуха на пояске по всему периметру навешан газосборный колокол собранный из отдельных литых чугунных секций.
Ошиновка электролизера
Ошиновка предназначена для подвода потенциала плюс к аноду и отвода потенциала минус от катода.
Анодная ошиновка состоит из алюминиевых шин и гибких лент (спусков). Все контакты между элементами ошиновки сварные.
Ошиновка является токонесущим элементом конструкции электролизера и состоит из двух частей — анодной и катодной. Электролизеры, располагаемые рядами один за другим, соединены токопроводами из алюминиевых шин различного сечения и включены в электрическую цепь последовательно: катодные шины одного электролизера соединены с анодными шинами другого. Группа электролизеров, объединенная в одну цепь, называется серией.
В анодную часть ошиновки входят гибкие пакеты, анодные стояки и уравнительные шины, от которых ток при помощи специальных контактов передается к штырям (самообжигающиеся аноды) или штангам (обожженные аноды). Катодная часть ошиновки состоит из гибких лент—катодных спусков, отводящих ток от катодных стержней подины, и катодных шин.
Существует много схем устройства шинопроводов электролизеров. Выбор схемы ошиновки зависит от типа электролизера, его мощности и расположения в корпусе. При выборе ошиновки следует руководствоваться следующими данными: оптимальная плотность тока в ошиновке, наименьшее влияние взаимодействия магнитных полей на процесс электролиза и возможность быстрого отключения и подключения в электрическую печь одного электролизера без нарушения работы остальных.
В связи с ростом единичной мощности электролизеров выбор схемы ошиновки приобретает все большее значение, так как от нее зависит не только стоимость шинопроводов и потери в них электроэнергии, но и состояние расплава в электролизере, что в конечном итоге определяет технологию процесса электролиза. Хорошо известно, что вокруг всех токопроводящих элементов электролизера под влиянием проходящего по ним постоянного тока создаются магнитные поля, а следовательно возникают электромагнитные силы, вызывающие перемещение катодного металла и электролита, и поверхность металла в электролизере перестает быть горизонтальной. Электромагнитные силы действуют во всех конструкциях электролизеров, однако наиболее существенное влияние на процесс электролиза эти силы начинают оказывать при единичной мощности электролизера свыше 100 кА
|
Требования к ошиновке:
- ошиновка должна быть достаточно дешевой;
- алюминиевые шины ошиновки должны быть из алюминия марки не ниже А6;
- все сварные соединения должны быть прочные (аргонная сварка);
- Плотность тока должна быть экономически выгодной;
- Конструкция должна обеспечивать быстрое подключение и отключение ванны в цепь;
Конфигурация ошиновки должна снижать до минимума негативное действие электромагнитных сил на работу электролизёра. Для равномерного отвода тока от подины электролизера и уменьшения горизонтальных токов в металле катодная ошиновка выполнена секционированной.
Машины прорезки периферии анодов (МППА)
МППА предназначена для прорезки и подпрессовки периферии анода электролизёров с самообжигающимися анодами. Прорезка и подпрессовка периферии анода направлена на удаление «припеканий» (анодная масса припёкшаяся к участку анодного кожуха в районе пояска газосборного колокола) и «козырьков» (анодная масса прилипшая к внутренней поверхности вверху анодного кожуха), а также на исключение пустот, образующихся под «козырьками», на обеспечение затекания анодной массы в зазор между кожухом и телом анода.
3 Машины пробивки корки электролита (МПК)
Предназначены для разрушения корки электролита при проведении обработки и выполнении отдельных технологических операций (пробивка лёток для выливки металла, отверстий для отбора проб металла, электролита и др.).
![]() |
Рисунок 3 - Машины пробивки корки электролита в торцах электролизёров
Машина разгрузки глинозёма (МРГ)
Машина МРГ предназначена для внутрицеховой транспортировки глинозёма к электролизёрам и равномерной дозированной загрузки его в электролизёры.
Трактор МТЗ-80
Трактор МТЗ-80 предназначен для механизации комплекса работ: для транспортировки ковшей с металлом из корпусов электролиза в литейное отделение, транспортировки инструмента и различной оснастки при ремонте металлургического оборудования.
Автопогрузчик «Хайстер»
Предназначен для замены секций газосборного колокола электролизёра
Вакуум-ковш ВКА – 5СК
Предназначен для набора металла из электролизёра, транспортировки в литейное отделение и заливки в миксер-копильник.
Кран штыревой
Предназначен для установки анодных штырей без присутствия анодчика и выполнения технологических операций по обслуживанию с верхним токоподводом.
Рисунок 4 – Штыревые краны - манипуляторы
Расчётная часть
Материальный баланс
В процессе электролиза криолитоглинозёмного расплава расходуется глинозём, фтористые соли и угольный анод. При этом образуется расплавленный алюминий и газообразные оксиды углерода.
Расчет веду на основании заданных параметров:
- сила тока I = 177,7 кА
- анодная плотность тока dа= 0,73 А/см2
- выход по току η =88,9 %
Расход сырья N, кг на получение 1 кг алюминия
- глинозем, NГ= 1,928
- фтористый алюминий, NФа= 0,02
- фтористый кальций, NCа= 0,0013
- анодная масса, NМ= 0,530
- количество серии = 4
Проектируемый цех состоит из четырёх серий. Расчёт ведём на один час работы электролизёра.
Расчёт потерь сырья
Теоретический расход глинозема составляет 1,89 кг на 1 кг алюминия. Перерасход глинозема объясняется наличием в его составе примесей и механическими потерями. Тогда потери глинозема составят:
G = PAl * (Nг - 1,89) (2.13)
G =52,55 * (1,928 – 1,89)=2,06 кг
Потери углерод находят по разности прихода анодной массы и расхода углерода, связанного в окислы:
Rуг = Rм - (mcco2 + mcco) (2.14)
Rуг =27,85 – (13,14 + 8,76)= 5,95 кг
Приход фторсолей в электролизёр принимаем равным их расходу.
Таблица 2.1 - Материальный баланс электролизера на силу тока 170кА
Приход | кг | % | Расход | кг | % |
Глинозем | 101,32 | 77,77 | Алюминий | 52,55 | 40,33 |
СО2 | 48,17 | 36,97 | |||
СО | 20,44 | 15,69 | |||
Анодная масса | 27,85 | 21,38 | Потери: | ||
Глинозем | 2,06 | 1,58 | |||
Фтористые соли | 1,12 | 0,86 | |||
Фтористые соли | 1,12 | 0.86 | Анодная масса | 5,95 | 4,57 |
Всего | 130,29 | Всего | 130,29 |
Расчёт катодного устройства
Катодное устройство электролизёра предназначено для создания необходимых условий для протекания процесса электролиза в криолитоглиноземном расплаве. Катодное устройство состоит из
Внутренние размеры шахты электролизера рассчитывают исходя из длины анода (формула 16) и принятых расстояний от анода до стенок боковой футеровки (Рисунок 1). Для электролизёра типа С-8БМ установлено, что расстояние
- от продольной стороны анода до футеровки, а = 65 см
- от торца анода до футеровки, в = 55 см.
![]() |
285 415
55 850 см
960 см
Рисунок 5 - Схема анода и шахты электролизёра
Тогда длина Lш, см и ширина Вш, см шахты определяются:
Lш = Lа + 2*в; (2.21)
Lш =850 + 2 * 55 =960см
Вш = Ва + 2*а (2.22)
Вш =285 + 2*65 = 415 см
Катодное устройство электролизёра имеет сборно-блочную подину, смонтированную швом вперевязку из коротких и длинных прошивных блоков. Отечественная промышленность выпускает катодные блоки высотой hб = 40 см, шириной bб = 55 см, и длиной l б от 110 до 400 см. Применяют катодные блоки:
- короткие l кб = 160 см
- длинные l дб = 220 см
Число секций в подине, Nс определяют исходя из длины шахты:
Nс = (2.23)
где bб – ширина подового блока;
с – ширина шва между блоками, 4 см.
16 шт
Число катодных блоков Nб, равно:
Nб = Nс * 2 (2.24)
Nб = 16*2=32шт
Подина данного электролизера монтируется из 32 катодных блоков, уложенных по 16 штук в два ряда с перевязкой центрального шва. Межблочные швы при монтаже подины набиваются подовой массой. Для отвода тока от подины, в подовые блоки вставлены стальные катодные стержни (блюмсы):
- для блока 160 см длина блюмса 219 см;
- для блока 220 см длина блюмса 279 см.
Ширина периферийных швов от подовых блоков до футеровки будет равна:
- в торцах подины, bт,
Bт = (2.25)
Bт = = 10см
- по продольным сторонам, bп:
bп = (2.26)
bп = см
Глубина шахты электролизёра С-8БМ равна 56,5 см.
Расчёт катодного кожуха
Внутренние размеры катодного кожуха определяются из рассчитанных ранее размеров шахты электролизёра (формулы 2.21, 2.22) и толщины слоя теплоизоляционных материалов.
Длина катодного кожуха Lк, см:
Lк = Lш + 2 (Пу + 3,5), (2.27)
где: Lш - длина шахты, см;
Пу – толщина угольной плиты;
3,5 – толщина теплоизоляционной засыпки в торцах электролизёра, см.
Lк =960 + 2(20+3,5)=987см
Ширина катодного кожуха Вк, см:
Вк = Вш + 2 (Пу + 5), (2.28)
где: Вщ - ширина шахты, см;
5 – толщина теплоизоляционной засыпки в продольных сторонах электролизёра, см.
Вк = 415 + 2 (20 + 5) = 465см
Футеровка днища катодного кожуха выполняется следующим образом (снизу - вверх):
- теплоизоляционная засыпка 3-5 см;
- два ряда легковесного шамота или красного кирпича толщиной 6,5 см;
- три ряда шамотного кирпича по 6,5 см;
- угольная подушка 3-5 см;
- подовый блок 40 см.
Тогда высота катодного кожуха Нк, см будет:
Нк = 5 + 5* 6,5 + 3 + Нш + hб (2.29)
где: Нш - глубина шахты, см;
hб– высота подового блока, см.
Нк = 5 + 5 * 6,5 + 3 + 56,5 + 40 =137см
Принимаю катодный кожух контрфорсного типа с днищем. Число контрфорсов равно, по 24 с каждой продольной стороны. Стенки катодного кожуха изготовлены из листовой стали толщиной 10 мм, днище – 12мм. Кожух снаружи укреплен поясами жесткости из двутавровых балок или швеллеров, а также имеет рёбра жёсткости.
Падение напряжения в подине
Падение напряжения в подине, UП мВ смонтированной из прошивных блоков, определяется по уравнению М.А. Коробова и А.М. Цыплакова:
UП = (2.32)
где lпр - приведенная длина пути тока, см (2.33);
ρбл - удельное сопротивление прошивных блоков принимаем 3,72*10-3 Ом*см;
Вш - половина ширины шахты ванны, см;
Вбл - ширина катодного блока с учётом набивного шва, см (2.34);
a - ширина настыли, равна расстоянию от продольной стороны анода до боковой футеровки, см;
Scт – площадь сечения блюмса, см2 (2.35);
da - анодная плотность тока, А/см2.
Приведенную длину пути тока по блоку lпр, см определяем по уравнению:
(2.33)
где hбл - высота катодного блока;
hст - высота катодного стержня, 14,5 см;
Вст - ширина катодного стержня, 26 см
lпр = 2,5+0,92*40-1,1*14,5+ см
Ширина катодного блока с учетом набивного шва Вбл,см равна:
Вбл = bб + с, (2.34)
где bб – ширина подового блока;
с – ширина набивного шва между блоками.
Вбл = 55+4=59см
Площадь сечения катодного стержня с учетом заделки равна:59см
Sст = hст * Вст (2.35)
Sст = 14,5*26=377см
Тогда падение напряжения в подине UП, мВ составит:
UП = мВ
Расчет прихода тепла
Приход тепла от прохождения электрического тока Qэл, кДж определяется по уравнению:
Q эл = 3 600 * I * Uгр * τ (2.39)
где 3600 – тепловой эквивалент одного кВт*ч, кДж;
I – сила тока, кА;
Uгр – греющее напряжение, В (из таблицы 2);
τ – время, часы.
Q эл = 3 600 * 177,7 * 4,667* 1=2 985 573кДж
Приход тепла от сгорания угольного анода Qан, кДж определяется:
Qан = Р1СО2 * ∆HTCO2 + Р1СО * HTCO (2.40)
где Р1СО2 и Р1СО – число киломолей оксидов углерода; определяется по материальному балансу исходя из формул (2.10 и 2.11);
∆НТСО2 и ∆НТСО – тепловые эффекты реакций образования СО2 и СО из углерода и кислорода при 25°С (298 К):
∆H298СО2 = 394 070 кДж/кмоль
∆H298СО = 110 616 кДж/кмоль
(2.41)
кмоль
(2.42)
кмоль
Qан = 1,09 * 394 070 + 0,73 * 110 616 = 510 286кДж
Расчёт расхода тепла
На разложение глинозема расходуется тепла QГ, кДж:
QГ = R1Г * ∆HTГ (2.43)
где ∆HTГ - тепловой эффект образования оксида алюминия при 25˚С (298 К), равный 1 676 000 кДж/кмоль.
(2.44)
кг/моль
QГ = 0,99 * 1676000 = 1 659 240кДж
Потери тепла с выливаемым из ванны алюминием рассчитываются, исходя из условия, что количество вылитого алюминия соответствует количеству наработанного за то же время.
При температуре выливаемого алюминия 960°С энтальпия алюминия ∆HT1Al составляет 43982 кДж/кмоль, а при 25 °С энтальпия алюминия ∆HT2Al равна 6716 кДж/кмоль. Отсюда, потери тепла QAl, кДж с выливаемым алюминием составят:
QAl = Р1Al * (∆HT1Al - ∆HT2Al) (2.45)
где Р1Al - количество наработанного алюминия, кмоль определяемое по формуле:
(2.46)
Р1Al кг/моль
QAl = 1,95 * (43982 – 6716)= 72 668,7кДж
Унос тепла с газами при колокольной системе газоотсоса рассчитываем, принимая, что разбавление газов за счет подсоса воздуха в систему отсутствует. В этом случае ведем расчет на основные компоненты анодных газов – оксид и диоксид углерода. Тогда унос тепла с газами Qгаз, кДж будет равен:
Qгаз = Р1СО * (HT1CO - HT2CO) + Р1СО2 * (HT1CO2 - HT2CO2), (2.47)
где Р1СО и Р1СО2 – количество CO и CO2, кмоль
HT1CO – энтальпия СО при температуре 550 °С, равна 24 860 кДж/кмоль
HT2CO – энтальпия СО при температуре 25 °С, равна 8 816 кДж/кмоль
HT1CO2 – энтальпия СО2 при температуре 550 °С, равна 40 488 кДж/кмоль
HT2CO2 – энтальпия СО2 при температуре 25°С соответственно, 16 446 кДж/кмоль
HT2CO2 – энтальпия СО2 при температуре 25°С соответственно, 16 446 кДж/кмоль
Qгаз = 0,73 * (24 860-8 816) + 1,09 * (40 488 – 16 446)=37 917,9кДж
Потери тепла в окружающую среду определяются на основании законов теплоотдачи конвекцией, излучением и теплопроводностью. Так как электролизер представляет собой сложную систему, изготовленную из различных материалов, для упрощения расчетов, потери тепла конструктивными элементами электролизёра QП, кДж определяются по разности между приходом тепла и расходом по рассчитанным статьям:
Qп = (Q эл + Qан) - (QГ + QAl + Qгаз) (2.48)
Qп = (2 995 808,76+421 786,62) – (1 659 240+72 668,7+37 917,9)=1 647 750,78кДж
Таблица 2.3 - Тепловой баланс электролизера на силу тока 170 кА
Приход тепла | кДж | % | Расход тепла | кДж | % |
От прохождения электроэнергии | 2 985 573 | 85,4 | На разложение глинозёма | 1 659 240 | 47,5 |
С вылитым металлом | 72 669 | 2,1 | |||
От сгорания угольного анода | 510 286 | 14,6 | С отходящими газами | 37 918 | 1,0 |
Конструктивными элементами и с поверхности электролизёра | 1 726 032 | 49,4 | |||
Итого | 3 495 859 | Итого | 3 495 859 |
Расчёт цеха
В расчёт цеха входит определение числа рабочих электролизёров в серии, число резервных электролизёров, общее число устанавливаемых электролизёров, годовой выпуск алюминия-сырца одной серией и цехом, а также удельный расход электроэнергии.
Расчёт числа рабочих электролизёров определяется величиной среднего напряжения на электролизёре и напряжением выпрямительных агрегатов, питающих серию электролизёра.
КПП обеспечивает серию электролизёров напряжением 850 В. Учитывается резерв напряжения 1 % на колебание во внешности сети, потери напряжения в шинопроводах и т.д.
Для подстанции на 850 В рабочее напряжение серии U, В составит:
U = 850 - (U1 + U2 + U3) (2.49)
U = 850 – (8,5 + 8,5 + 30) = 803 В
Число установленных электролизеров N в серии составит:
N = (2.50)
N
где U - напряжение серии U, В
UСР - среднее напряжение на электролизере, В (из таблицы 2.3);
UАЭ - доля увеличения напряжения от анодных эффектов, В (по формуле 36)
В связи с необходимостью проведения капитальных ремонтов оборудования и обеспечения постоянной производительности серии, рассчитываем количество резервных электролизеров.
Nр= (2.51)
где N – число рабочих электролизёров в серии;
t – длительность простоя ванн в ремонте, по практическим данным 7 дней;
Т – срок службы электролизёра, 4 года;
365 – дней в году.
Nр шт
Принимаем 1 резервный электролизёр на серию, тогда в серии рабочих электролизеров N шт. будет:
N=172 – 1 = 171 (2.52)
где Nу - число установленных электролизеров;
NР - число резервных электролизеров
В 3 сериях будет 6 корпусов, в них установленных электролизёров, NУСТ:
NУСТ = NУ * n (53)
NУСТ = 172 * 4 = 688
Nраб = 171 * 4 = 684ванн
Годовая производительность серии Pс, т рассчитывается по формуле:
Pс = 0,335 * I * η * 8760 * N * 10-3 (2.54)
где 0,335 - электрохимический эквивалент, кг/(кА*ч);
I - сила тока, кА;
η - выход по току, д. е.;
8760 - часов в год;
N - число работающих ванн в серии.
РС = 0,335 * 177,7 * 0,882 * 8760 * 171 * 10-3= 78 650,42 тонн
Годовая производительность цеха Рц, т будет:
Рц = Рс * n (2.55)
Рц = 78650,42 *4 = 314 602т
Удельный расход электроэнергии W, кВт*ч/т рассчитывается по формуле:
(2.56)
кВт*ч/т
Выход по энергии г/кВт*ч
(2.57)
г/кВт*ч
Виды твердых отходов
К основным твёрдым отходам электролизного производства алюминия относятся: хвосты флотации угольной пены, углеродистые шламы и пыль газоочистки, отработанная футеровка электролизеров.
В процессе работы из электролизера выделяется ряд веществ в виде газа, пыли и твердых отходов. Твердые вещества выделяются в основном в виде пыли, содержащей А12O3, фториды, используемые как сырье (Na3AlF6, AlF3, NaF и пр.), а также смолистые соединения (при использовании СОА). Кроме того, большое место в твердых отходах составляют:
- отработанная футеровка электролизеров (~40% С, ~50% F, Al, Si) – уголь выделяют флотацией;
- продукты переработки угольной пены;
- продукты производства регенерированного криолита при применении мокрого способа очистки отходящих газов шлам «мокрой» газоочистки – не перерабатывается осадки,
- производственные отходы, загрязненные продуктами производства алюминия.
Твердые отходы производства представляют собой источник загрязнения окружающей среды. К основным из них относятся:
— потери сырья при разгрузке и транспортировке;
— пыль, увлекаемая вентиляцией и отходящими газами;
— угольная пена, снимаемая с поверхности электролита;
— отходы (хвосты) переработки угольной пены и производства регенерационного криолита (при мокрой очистке отходящих газов);
— отходы, образующиеся при капитальном ремонте электролизеров;
— анодные корки рафинирования алюминия (Ba, Fe, Cu, Mn, Si, Al, Na, F, Cl) – получение сплавов
Результаты и выводы
1. Данный способ переработки твердых отходов электролитического производства алюминия позволяет по сравнению с прототипом и другими известными способами перерабатывать твердые отходы электролитического производства алюминия с низким содержанием алюминия при наличии в них органически связанных соединений углерода.
2 Это решает экологическую и производственную проблему переработки шламовых полей и отвалов алюминиевого производства без выброса в окружающую природную среду токсических соединений.
3 Результаты проведенных исследований с учетом промышленной практики позволили разработать безотходную технологию переработки и утилизации алюминийфторуглеродсеросодержащих отходов алюминиевого производства с получением следующих товарных продуктов: гидроксида алюминия или глинозёма, содопродуктов и флюоритового шлама, пригодного для производства фтористых солей.
Экономическая часть
Расчет численности рабочих
Явочная численность рабочих в одну смену определяется:
, (4.1)
А – количество установленных ванн, шт.
Явочная численность в одни сутки определяется как произведение явочной численности в одну смену на количество смен в сутки (С).
Штатная численность определяется с учетом выходных смен:
(4.2)
где С/ - количество смен на выходном.
Примечание: если работник работает в одну смену, то явочная численность (в смену и в сутки) равняется штатной численности
Списочная численность определяется с учетом коэффициента перехода от штатной к списочной численности, т.е. для ее расчета необходимо рассчитать коэффициент списочного состава на основе планового баланса рабочего времени рабочего.
Расчет коэффициента списочного состава приведен в таблица 4.2.
Таблица 4.2 - Расчет коэффициента списочного состава
Показатели, Ед. изм. | Непрерывное производство | Прерывное производство | |
основное | вспомогательное | ||
Календарный фонд рабочего времени, Ткал, дни | |||
Число выходных и праздничных дней, дни | |||
Номинальный фонд рабочего времени, Тн, дни | |||
Невыходы по причинам: | |||
основные и дополнительные отпуска, дни | |||
болезни, дни | |||
гос. обязанности, дни | |||
отпуск учащимся, дни | |||
отпуск с родами, дни | - | - | |
Эффективный фонд рабочего времени, Тэф, дни/ часы | 175/1 400 | 189/1 512 | 222/1 776 |
Коэффициент списочного состава (Ксс), Тн/Тэф | 1,32 | 1,22 | 1,17 |
Чсп=Чшт*КСС, (4.3)
где КСС – коэффициент списочного состава.
Исходными данными для расчета численности я
|
|
Своеобразие русской архитектуры: Основной материал – дерево – быстрота постройки, но недолговечность и необходимость деления...
Общие условия выбора системы дренажа: Система дренажа выбирается в зависимости от характера защищаемого...
Археология об основании Рима: Новые раскопки проясняют и такой острый дискуссионный вопрос, как дата самого возникновения Рима...
Эмиссия газов от очистных сооружений канализации: В последние годы внимание мирового сообщества сосредоточено на экологических проблемах...
© cyberpedia.su 2017-2024 - Не является автором материалов. Исключительное право сохранено за автором текста.
Если вы не хотите, чтобы данный материал был у нас на сайте, перейдите по ссылке: Нарушение авторских прав. Мы поможем в написании вашей работы!