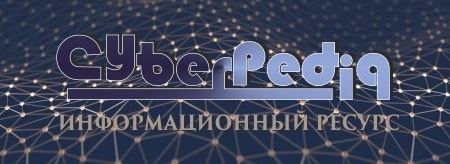
Эмиссия газов от очистных сооружений канализации: В последние годы внимание мирового сообщества сосредоточено на экологических проблемах...
Автоматическое растормаживание колес: Тормозные устройства колес предназначены для уменьшения длины пробега и улучшения маневрирования ВС при...
Топ:
Методика измерений сопротивления растеканию тока анодного заземления: Анодный заземлитель (анод) – проводник, погруженный в электролитическую среду (грунт, раствор электролита) и подключенный к положительному...
Устройство и оснащение процедурного кабинета: Решающая роль в обеспечении правильного лечения пациентов отводится процедурной медсестре...
Отражение на счетах бухгалтерского учета процесса приобретения: Процесс заготовления представляет систему экономических событий, включающих приобретение организацией у поставщиков сырья...
Интересное:
Национальное богатство страны и его составляющие: для оценки элементов национального богатства используются...
Что нужно делать при лейкемии: Прежде всего, необходимо выяснить, не страдаете ли вы каким-либо душевным недугом...
Средства для ингаляционного наркоза: Наркоз наступает в результате вдыхания (ингаляции) средств, которое осуществляют или с помощью маски...
Дисциплины:
![]() |
![]() |
5.00
из
|
Заказать работу |
|
|
ВВЕДЕНИЕ
Удельный вес нефти во всем российском экспорте в прошлом году составил 34,6%. По официальным данным, вклад нефтегазового комплекса в создании ВВП с учетом трубопроводного транспорта составляет 25%, а на весь промышленный сектор страны без нефти и газа - 15%. В нынешнем виде доходная часть бюджета формируется на половину из денег нефти и газа. Еще четыре года назад этот показатель был вдвое меньше (23,4%). Под нефтегазовыми деньгами подразумеваются поступления от пошлин и налогов, в том числе, на прибыль нефтегазовых компаний, дивиденды нефтяных компаний по акциям, принадлежащим государству, доходы от деятельности государственных нефтяных компаний, работающих за рубежом.
В современных условиях минерально-сырьевой сектор экономики (прежде всего - нефтегазовая промышленность) перестал быть «простым» в технологическом отношении. Добыча сырьевых ресурсов ведется с использованием постоянно усложняющихся технологий, в создание которых вкладываются многие миллиарды долларов и над которыми работают интеллектуальные силы многих стран мира. Поэтому можно с полной уверенностью утверждать, что с каждым годом нефть, газ и другие сырьевые продукты становятся во все большей степени продуктами наукоемкими.
Опыт работы вертикально интегрированных нефтяных компаний во всем мире свидетельствует о ключевом значении нефтедобычи в их деятельности. При этом развитие и рентабельность нефтедобычи определяются, в первую очередь, достигнутым технологическим уровнем прорывных технологий. Наибольшее распространение получили технологии строительства горизонтальных скважин. Только в США сегодня ежегодно строят до 1000-1500 таких скважин в год и в ближайшее время могут вообще отказаться от строительства вертикальных скважин в эксплуатационном бурении. Новые технологии, основанные на методе горизонтального бурения, произвели настоящую революцию в практике и теории мировой нефтедобычи, но, к большому сожалению, этот метод у нас пока не нашел должного развития. Достижения технологии горизонтального бурения сделали возможным разбуривание шельфовых месторождений нефти и газа с берега, без строительства дорогостоящих морских оснований и платформ.
|
ТЕХНОЛОГИЧЕСКАЯ ЧАСТЬ
Циркуляционная система буровой установки
Блоки очистки и приготовления буровых растворов БПО
Блоки обеспечивают очистку буровых растворов от частиц размером более 5 мкм с выделением шлама пониженной влажности, регенерацию барита и его многократное использование, выведение из бурового раствора избытка коллоидной фазы, регенерацию барита после завершения бурения скважины, приготовление и утяжеление буровых растворов.
Использование полнокомплектных блоков очистки сокращает объем отходов бурения в 2-3 раза, расход барита и химреагентов на 40-60% и позволяет получить шлам пониженной влажности, пригодный для перевозки в контейнерах или на бортовых транспортных средствах.
1 – укрытие; 2 - вибросито ВС-1,3 – вентилятор;
4 – илоотделитель ИГ-45М; 5 – центрифуга; 6 – электронасосный агрегат; 7 – калорифер; 8 – ситогидроциклонный сепаратор; 9 – емкость; 10 – дегазатор; 11 – блок химической обработки; 12 – смеситель.
Рисунок 6 - Схема блока очистки и приготовления буровых растворов БПО.
Буровые насосы
Насосно-циркуляционный комплекс буровой установки выполняет следующие функции:
- нагнетание бурового раствора в бурильную колонну для циркуляции в скважине в процессе бурения, промывки и ликвидации аварий в количестве, обеспечивающим эффективную очистку забоя и долота от выбуренной породы, и получение скорости подъема раствора в затрубном пространстве, достаточной для выноса этой породы на поверхность;
|
- подвод к долоту гидравлической мощности, обеспечивающей высокую скорость истечения раствора (до 180 м/с) из его насадок для частичного разрушения породы и очистки забоя от выбуренных ее частиц;
- подвод энергии к гидравлическому забойному двигателю;
- очистка бурового раствора от выбуренной породы и газов, поддержание и регулирование заданных его параметров;
- приготовление нового бурового раствора;
- хранение запасного бурового раствора в количестве нескольких
объемов скважины и поддержание его свойств при остановках циркуляции.
Буровые насосы предназначены для нагнетания в скважину промывочной жидкости с целью очистки забоя и ствола от выбуренной породы (шлама) и выноса ее на дневную поверхность; охлаждения и смазки долота; создания гидромониторного эффекта при бурении струйными долотами; приведения в действие забойных гидравлических двигателей.
РАСЧЕТНАЯ ЧАСТЬ
При конструкции буровых насосов прежде всего должны быть определены основные параметры – подача, число цилиндров, число двойных ходов поршней и развиваемые насосом давления при наибольшей и наименьшей подачах.
Элементы бурового насоса рассчитываются на прочность по наибольшим нагрузкам, возникающим при работе, а на долговечность – по эквивалентной нагрузке. Для деталей, подверженных абразивному износу, долговечность теоретически не определяется, сроки службы устанавливаются по опыту эксплуатации аналогичных конструкций в зависимости от условий работы и свойств прокачиваемого бурового раствора.
Гидравлический расчет
Полезная мощность насоса рассчитывается [1]:
(2.1)
где N Д – Мощность приводного двигателя насоса, N Д =600 кВт;
ηНА – общий КПД насосного агрегата от двигателя до выхода насоса и представляет собой произведение объемного ηо, гидравлического ηг и механического ηм коэффициентов полезного действия насосного агрегата.
Общий КПД насоса рассчитывается [1]:
(2.2)
где | ηо– объёмный КПД насоса, ηо = 0,95–0,99; |
ηг– гидравлический КПД, ηг = 0,97–0,98; | |
ηм– механический КПД. |
Механический КПД насоса рассчитывается [1]:
(2.3)
где | η1м– КПД трансмиссионного вала на опорах качения, η1м = 0,99; |
η2м– КПД закрытой зубчатой передачи, η2м = 0,98; | |
η3м– КПД коренного вала на опорах качения, η3м = 0,975; | |
η4м– КПД ползуна и кривошипно-шатунного механизма, η4м = 0,95; | |
η5м–КПД уплотнения штока и поршня, η5м = 0,98 |
|
NПН = 600000· 0,84 = 504000 Вт
Задано максимальное и минимальное давление насоса:
Рmax = 28 МПа;
Рmin = 11,3 МПа.
Рассчитаем максимальную и минимальную подачи насоса, исходя из заданного давления [1]:
(2.4)
(2.5)
м3/с;
м3/с.
Гидравлическая коробка
Напряжения в этих элементах определяются по формулам для расчета толстостенных цилиндрических сосудов [2]:
(2.6)
где | РРi | – вероятное расчетное давление, Па; |
k | – отношение радиусов, k = 0,81; | |
ν | – отношение предела текучести материала при растяжении к пределу текучести при сжатии, ν = 1. |
Вероятное расчетное давление [2]:
PPi = P×kn, (2.7)
где kn – коэффициент, учитывающий вероятность превышения испытательного давления над наибольшим рабочим, kn = 1,68.
PPi = 28∙106∙1,68=47,04∙106 Па
Коэффициент запаса статической прочности [2]:
S = (2.8)
где sТ – предел текучести материала.
Гидравлическая коробка изготовлена из стали 36Л, sТ = 600×106 Па
S = - условие выполняется.
Коэффициент запаса прочности по выносливости [2]:
na = (2.9)
где s-1огр – ограниченный предел выносливости на сжатие при
симметричном цикле Па;
s-1огр = 0,35×sв = 0,35×800×106 = 280×106 Па,
где | sв– предел прочности материала; |
кsд– коэффициент, учитывающий влияние всех факторов на выносливость, кsд = 4; | |
js–коэффициент, учитывающий влияние асимметрии цикла, | |
js= 0,2 |
sа – средняя амплитуда цикла [2];
(2.10)
где sм – среднее напряжение цикла [2];
(2.11)
где smin – минимальное напряжение цикла;
smin = 0,9×sмах = 0,9×250×106 = 225×106 Па,
где sмах = 250∙10 Па;
na = - условие выполняется.
Цилиндровая втулка
Проверка цилиндровых втулок производится по внутреннему диаметру, т. к. напряжение больше на внутренней поверхности. Проверяет втулку минимального диаметра при максимальном давлении.
Эквивалентное напряжение на внутренней поверхности [2]:
|
(2.12)
где | r– внутренний радиус втулки, r =0,06 м; |
s– толщина стенки, s =0,042 м; | |
с– наибольший допустимый износ втулки, м. |
Коэффициент запаса статической прочности [2]:
S =
Цилиндровая втулка изготавливается из стали 65Г, для которой sТ = 750МПа. Цилиндровые втулки не рассчитываются на выносливость, т. к. втулка изнашивается по внутреннему диаметру быстрее, чем может наступить ее усталостное разрушение.
S =
Делам вывод, что коэффициент запаса статической прочности цилиндровой втулки достаточен, для эксплуатации насоса с заданным давлением.
Шток насоса
Шток насоса рассчитывается на устойчивость и усталость. Расчету на усталость подвергаются утонченные участки штока, расположенные в месте свинчивания штока с кронштоком.
Усилие сжатия штока [2]:
Рсж = ,
(2.13)
где, D – диаметр поршня, D = 0,12 м;
Максимальные переменные сжимающие напряжения [2]:
, (2.14)
где | fш – площадь наименьшего поперечного сечения штока; |
d – диаметр штока. |
=160∙10
Па.
Шток изготовлен из стали 40Х sт = 800 МПа.
Коэффициент запаса статической прочности:
S = - условие выполняется.
Коэффициент запаса прочности по выносливости [2]:
(2.15)
где s-1с – предел выносливости на сжатие, для стали 40Х s-1с=1000МПа.
- условие выполняется.
Расчет штоков на продольную устойчивость:
Для составных штоков определяем эквивалентную длину штока ползуна.
Эквивалентная длина штока ползуна [2]:
(2.16)
где | lшт– длина штока ползуна, lшт = 0,395 м; |
d– диаметр штока поршня, d = 0,065 м; | |
d1– диаметр штока ползуна, d1 = 0,110 м. |
Расчетная длина составного штока [2]:
(2.17)
где, lш – длина штока поршня, lш = 0,525 м.
Гибкость штока [2]:
(2.18)
где imin – наименьший радиус инерции штока [3], м
(2.19)
где J – момент инерции [3], м3*м
(2.20)
Т.к. <100, то расчет коэффициента запаса устойчивости ведем по формуле Ф. С. Ясинского [2]:
(2.21)
где, sкр – критическое напряжение сжатия [1], Па
(2.22)
Клапан насоса
Проверим клапан на стук [2]:
(2.23)
где, Dk = 140 мм и D0 = 128 мм – диаметры клапана и отверстия седла;
g = 450 – угол наклона образующей конической посадочной поверхности клапана.
- стука не возникает.
Тарель клапана рассчитывается на прочность и выносливость, как пластина радиуса dk/2 свободно опертая по краям.
Момент изгиба тарели [2]:
(2.24)
где | dT– диаметр тарели, dT = 0,14 м; |
m–коэффициент Пуассона, m = 0,3 |
Максимальные напряжения изгиба при опрессовке [2]:
(2.25)
где dт – толщина тарели, dт = 0,030 м
Тарель клапана изготавливается из стали 20Х2Н4А для которойsт=1100 МПа.
Коэффициент запаса статической прочности [2]:
(2.26)
Коэффициент запаса статической прочности тарели достаточен, для эксплуатации насоса с заданным давлением.
|
ТЕХНОЛОГИЧЕСКИЙ РАЗДЕЛ
Токарная обработка
1. Установить и снять деталь
2. Проточить поверхность №1 до Ø0,236м
Выбор оборудования и инструмента, определение квалификации специалиста
Токарный станок 1А63М, Nст=14квт; силовое оборудование генератор, наплавочный материал СВ-38ХГСА, державка резца 30х45, флюс ЖС-400, заготовка – деталь материал сталь 38-ХГС, специалист токарь 5 разряда.
Определяем глубину резания
(3.1)
где, | D = 0,24м - диаметр до обработки |
d = 0,236м - диаметр после обработки |
Определяем режимы резания
где, | – ![]() |
– ![]() |
Определяем скорость резания
где, | ![]() |
![]() | |
![]() | |
![]() | |
![]() |
частота, корректируем режим резания по паспортам данных станков и принимаем
и
Определяем фактическую скорость резания
Определяем время
- штучное время
- вспомогательное время
- основное время
где, | ![]() |
![]() | |
![]() |
мин
мин
мин
Определяем расход электроэнергии:
(3.2)
где, | ![]() |
![]() | |
![]() |
Наплавка
1.Установить и снять деталь.
2. Наплавить поверхность 2 до Ø 0,248м
где, | ![]() |
![]() |
Выбор оборудования
Установка для наплавки (ток. станок 16К20, мощность N=10кВт, автомат для наплавки Р683, мощность N=0.3кВт, силовое оборудование). Материал для наплавки: проволока наплавочная НП СВ38ХГСА d=0,0016м; флюс ЖС-400; сила тока I=600А; напряжение U=60В скорость наплавки скорость подачи проволоки 2,7-3,2 м/мин, высота наплавляемого слоя – 0,003м, шаг наплавки – 0,003м.
Определяем кол-во проходов:
Принимаем i=1
Определяем частоту вращения детали:
Определяем время:
- основное время
где, | L | – длина обрабатываемой поверхности (0,19 мм) |
S | – шаг наплавки |
- вспомогательное время
- штучное время
Определяем расход электроэнергии:
где, | ![]() |
![]() | |
![]() | |
![]() | |
![]() |
Определение расхода материала
где, - удельный вес (0,00787
)
Токарная обработка
1.Установить и снять деталь.
2.Проточить поверхность 1 до Ø 0,242м.
Выбор оборудования
Токарный санок 1А63М, мощность N=14кВт. Приспособление – патрон, вращающийся центр, для установки детали. Инструмент, режущий – резец проходной упорный (угол в плане - 90 ); пластина из твердого сплава ВК-8; державка 0,02*0,03м; для обработки также нужен измерительный инструмент штангенциркуль ШЦ 0-250; заготовка – деталь. Материал поверхности 38ХГСА, НRC 40…45. Специалист – токарь 5 разряда.
Определяем глубину резанья металла:
где | D– диаметр после наплавки |
d– диаметр после токарной обработки |
Определяем режимы резанья:
Подача:
- табличное значение
Поправочные коэффициенты:
- коэф. учитывающий состояние поверхности детали (с коркой)
- коэф. учитывающий группу материала (VI)
- коэф. учитывающий закаленную поверхность (НRC 40…45)
- расчетная подача
Скорость резанья:
табличное значение
- расчетная скорость
где | ![]() |
![]() | |
![]() ![]() | |
![]() |
Частота вращения детали:
где, D – диаметр после наплавки
Корректируем режимы резанья по паспортным данным станка и принимаем S=0.0005 м/об; n=40 .
Фактическая скорость резанья:
Определяем время:
- основное время
- вспомогательное время
- штучное время
Определяем расход электроэнергии:
где | ![]() | - мощность станка, кВт |
![]() | - коэф. использования оборудования по мощности | |
![]() | -коэф. перевода энергии |
Шлифовальная
1. Установить и снять деталь, шлифовать поверхность №1 до Ø 0,24м.
Выбор оборудования
Станок круглошлифовальный 3А131, мощность N=9кВт (станок оборудован средствами активного контроля); режущий инструмент круг шлифовальный d=0,6м, ширина 0,063 м марка круга ПВ-15А, зернистость 40.
Определяем частоту вращения детали:
Определяем режимы шлифования:
Выбираем величину продольной подачи
Величина врезания
Выбираем поправочный коэффициент на радиальную подачу
Выбираем поправочный коэффициент. на припуск шлифования
Принимаем м
Определяем время:
- основное время
- вспомогательное время
- штучное время
где - коэффициент выталкивания
кВт
где | ![]() |
![]() | |
![]() |
ПРЕДЛАГАЕМЫХ МЕРОПРИЯТИЙ
Расчёты выполняются на основании проведённых технологических расчётов. Рассчитанное штучное время, расход электроэнергии, расход основных и вспомогательных материалов используются для расчёта стоимости ремонта детали и определения экономической эффективности.
Предлагается вместо установки нового вала взамен изношенного производить восстановление изношенных поверхностей наплавкой под слоем керамического флюса.
Технологический маршрут предусматривает следующие технологические операции:
1. Токарная обработка.
2. Наплавка.
3. Токарная обработка.
4. Шлифовальная.
Смета затрат на наплавку
Таблица 8 - Смета затрат на наплавку
Наименование статей | Единица измерения | Всего | Обоснование |
1. Заработная плата. | РУБ | 692.77 | Раздел 6.18. |
2. Страховые взносы | РУБ. | 207,83 | Раздел 6.18. |
3. Электроэнергия. | РУБ. | 297,30 | Раздел 6.19. |
4. Основные и вспомогательные материалы. | РУБ. | 625,27 | Таблица №14. |
5. Прочие затраты. | РУБ. | 182,32 | 10% от 1 + 4. |
6. Прямые затраты. | РУБ. | 2005,52 | 1 + 5. |
7. Накладные расходы. | РУБ. | 100,28 | 5% от 6. |
8. Себестоимость. | РУБ. | 2105,8 | 6 + 7. |
9. Плановые накопления. | РУБ. | 210,06 | 10% от 8. |
10. Стоимость наплавки. | РУБ. | 2315,86 | 8 + 9. |
Себестоимость наплавки одного вала бурового насоса НБТ-600 составляет:
Пз+Нр=2005,52+100,28=2105,8
где, | Пз– прямые затраты |
Нр– накладные расходы |
Стоимость нового вала 150000, следует, что восстановление вала наплавкой под слоем керамического флюса выгодней чем покупка новой детали.
Требования безопасности на объекте
Охрана труда в нашей стране обеспечивается соответствующим законодательством, разветвленным контролем за его выполнением финансированием со стороны государства.
Оснащение в последние годы буровых установок автоматическими буровыми ключами, механизмами спуска и подъема инструмента позволило уменьшить физические нагрузки. Однако с ростом глубины бурения, увеличением его скоростей, оснащением буровых установок сложными пультами управления возросла нагрузка на зрение и на слух работающих, увеличились требования к точности и координации движения, скорости реакции. По мере автоматизации отдельных процессов бурения труд членов буровой бригады становиться все более нагруженным психологически, оставаясь на отдельных операциях тяжелым физическим трудом.
Главными задачами, охраны труда в бурении является: приспособления современных буровых машин, технологических процессов и производственной среды с целью обеспечения высокопроизводительных, здоровых и безопасных условий труда.
Токсичные вещества
Рабочие обслуживающие буровые насосы, как и остальные члены бригады, подвергаются воздействию вредных веществ.
ГОСТ 12.1.005-88 устанавливает предельно допустимые концентрации
(ПДК) в таблице 10. вредных веществ в рабочей зоне и на территории предприятий.
Из перечисленных веществ чаще приходится подвергаться воздействию масел, которые в виде паров попадают в организм человека через слизистую оболочку в легкие, что приводит к осложнениям. Температура вспышки -170°С, температура самовоспламенения - 380°С.
Таблица 10 - ПДК вредных веществ в рабочей зоне.
Вещество | Предельно допустимая концентрация, мг/ м3 | Класс опасности |
Метан | ||
Каустическая сода | 0,5 | |
Масла минеральные | 1,1 -5-10 | |
Сероводород |
Производственное освещение
Принимают совмещенное освещение. Искусственное освещение электрическое общее, равномерное. Используются светильники с лампами накаливания взрывонепроницаемыми. Естественное освещение — боковое. Правилами безопасности установлены нормы общей минимальной освещенности (в лк) для залов насосных - 20.
Шум и вибрация
Работающий буровой насос является источником вибрации и шума (до 92дБ). Звуки одной интенсивности, но разной частоты человек ощущает различно. Сильный шум, действуя на органы слуха, может привести к полной глухоте или к профессиональной тугоухости. При этом нарушается нормальная деятельность сердечно - сосудистой системы, возникают хронические заболевания. Под действием вибрации могут произойти в нервной и косно-суставной системах, падение мышечной силы и массы, артериального давления, нарушения остроты зрения, спазмы сосудов сердца. Эти нарушения проявляются в виде головной боли, головокружения, плохого сна и: самочувствия.
Чрезвычайные ситуации
Стихийные бедствия пока ещё в полной мере не подвластные человеку, наносят экономике государства огромный ущерб. Наиболее характерные стихийные бедствия для региона Республики Коми - наводнения, бури, ураганы и пожары. Стихийные бедствия возникают внезапно и носят чрезвычайный характер.
Основных причин возникновения ЧС две. Во-первых, постоянно усложняется современное производство. В его процессе часто применяются ядовитые и агрессивные компоненты. На малых площадях концентрируется большое количество энергетических мощностей. Во-вторых, упала производственная дисциплина. Невнимательность, грубейшие нарушения правил эксплуатации техники, транспорта, приборов и оборудования. Все это приводит к трагическим последствиям, огромным материальным убыткам.
Для ликвидации последствий, вызванных стихийными бедствиями, могут привлекаться как формирования общего назначения, так и формирования служб МЧС. В отдельных случаях помимо указанных формирований могут привлекаться воинские части ВС РФ.
Характер и порядок действий формирований при выполнении этой задачи зависит от вида стихийных бедствий, аварий, катастроф, сложившейся обстановки, количества и подготовленности привлекаемых сил МЧС, времени года и суток, погодных условий.
Спасательные и аварийно-восстановительные неотложные работы при ликвидации последствий стихийных бедствий, аварий, катастроф следующие:
При наводнениях для проведения спасательных работ привлекают спасательные отряды, команды и группы, а также ведомственные специализированные команды и подразделения, оснащенные плавсредствами, санитарные дружины и посты, разведывательные группы и звенья, формирования строительных, ремонтно-строительных организаций, органы общественного порядка.
Спасательные работы при наводнениях на поиск людей на затопленной территории и эвакуацию в безопасные места.
Для спасения и вывоза большого числа людей используют теплоходы, баржи, баркасы, катера и другие плавсредства. При спасении людей, находящихся в проломе льда, подают конец веревки, доски, лестницы, любой другой предмет и вытаскивают в безопасное место.
Медицинскую первую помощь оказывают спасательные подразделения или санитарные дружины непосредственно в зоне затопления. Первую врачебную помощь оказывают после доставки на причал.
При бурях и ураганах проводятся предупредительные, спасательные, аварийно-восстановительные работы. О времени появления урагана оповещают штабы МЧС объектов, формирования МЧС и население. До подхода ураганного ветра закрепляют технику, отдельные строения, в производственных помещениях и жилых домах закрывают двери, окна, отключают электросети, газ. воду. Население укрывается в защитных или заглубленных сооружениях.
После урагана формирования МЧС совместно со всем трудоспособным населением объекта проводят спасательные и аварийно-восстановительные работы, спасают людей из заваленных защитных и других сооружений и оказывают им помощь, восстанавливают поврежденные здания, линии электропередач и связи, газо- и водопроводы, ремонтируют технику, проводят другие аварийно-восстановительные работы.
При пожарах начальник ГО объекта и его штаб принимают все меры к его ликвидации, на основании данных разведки и других полученных сведениях оценивают пожарную обстановку, принимают решения и ставят задачи формированиям МЧС.
Командир формирования после получения и уяснения задачи, организует выдвижение формирования к указанному участку пожара. Для уточнения обстановки на маршруте и в районе пожара он выполняет разведку, которая выявляет характер пожара и его границы, направление распространения огня и возможные места устройства заградительных опорных полос, наличие и состояние водоисточников, подъездные пути к ним, пути вывода и способы спасения людей, находящихся на участке пожара. Из зоны возможного распространения пожара эвакуируются люди и материальные ценности.
В первую очередь разыскивают людей, оказавшихся в горящих районах, зданиях, сооружениях. В целях безопасности розыск людей осуществляется парами: один разыскивает, а второй страхует его с помощью веревки, находясь в менее опасном месте. В условиях сильного задымления и скопления угарного газа спасатели работают в противогазах с использованием дополнительного патрона.
ЭКСПЛУАТАЦИЯ НАСОСА
Порядок установки
Установить буровой насос на основании и выставить его по уровню, как по длине, так и по ширине. Отклонение от горизонтальной плоскости не более 1,5 мм на длине 1000 мм. Выбрать прокладками зазор между основанием и рамой насосов.
Расположить параллельно валы насоса и привода. Допускаемая не параллельность осей вращения должна быть не более 1 мм на 100 мм длины, а допуск на смещение приводных элементов должен быть не более 2 мм на 1000 мммежцентрового расстояния для шкивов и 0,35 мм для звездочек.
Подготовка к работе
Установить насос в соответствии с действующими правилами монтажа оборудования и мер безопасности в нефтегазодобывающей промышленности.
Расконсервировать насос до его запуска. Снять транспортные заглушки с отверстий трубопроводов паропод
|
|
Индивидуальные очистные сооружения: К классу индивидуальных очистных сооружений относят сооружения, пропускная способность которых...
Эмиссия газов от очистных сооружений канализации: В последние годы внимание мирового сообщества сосредоточено на экологических проблемах...
Историки об Елизавете Петровне: Елизавета попала между двумя встречными культурными течениями, воспитывалась среди новых европейских веяний и преданий...
История создания датчика движения: Первый прибор для обнаружения движения был изобретен немецким физиком Генрихом Герцем...
© cyberpedia.su 2017-2024 - Не является автором материалов. Исключительное право сохранено за автором текста.
Если вы не хотите, чтобы данный материал был у нас на сайте, перейдите по ссылке: Нарушение авторских прав. Мы поможем в написании вашей работы!