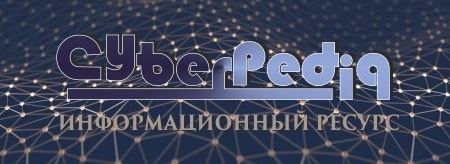
Семя – орган полового размножения и расселения растений: наружи у семян имеется плотный покров – кожура...
Индивидуальные и групповые автопоилки: для животных. Схемы и конструкции...
Топ:
Установка замедленного коксования: Чем выше температура и ниже давление, тем место разрыва углеродной цепи всё больше смещается к её концу и значительно возрастает...
Комплексной системы оценки состояния охраны труда на производственном объекте (КСОТ-П): Цели и задачи Комплексной системы оценки состояния охраны труда и определению факторов рисков по охране труда...
Интересное:
Отражение на счетах бухгалтерского учета процесса приобретения: Процесс заготовления представляет систему экономических событий, включающих приобретение организацией у поставщиков сырья...
Средства для ингаляционного наркоза: Наркоз наступает в результате вдыхания (ингаляции) средств, которое осуществляют или с помощью маски...
Лечение прогрессирующих форм рака: Одним из наиболее важных достижений экспериментальной химиотерапии опухолей, начатой в 60-х и реализованной в 70-х годах, является...
Дисциплины:
![]() |
![]() |
5.00
из
|
Заказать работу |
|
|
Схема расположения отделений цеха
Цех состоит из нескольких пролетов. В цехе имеется трансформаторный пролет шириной 6 м, который располагается на отметке 10 м. Далее за трансформаторным пролетом идет печной пролет. Печной пролет служит для размещения и обслуживания плавильных электропечей. Последние располагаются обычно вдоль цеха в линию. Ширина печного пролета принимается равной 24 м. Он выполняется многоэтажным. [8]
На нулевой отметке пролета расположены фундаменты плавильных печей (для вращающихся печей они заглублены), оборудование и механизмы газоочисток, подсобные помещения.
Для обслуживания летки устанавливается сплошное перекрытие или местная горновая площадка. Здесь расположены устройства для открывания и закрывания летки, узлы для приготовления леточной массы, системы шламосборников, бытовые помещения для отдыха плавильной бригады. В зависимости от мощности печи площадка располагается на высоте 3,1 м. [8]
Рабочая площадка, предназначенная для обслуживания печи, наблюдения за технологическим и электрическим режимами, представляет собой во всех цехах сплошное перекрытие и располагается на уровне 10 м.
Для обслуживания механизмов перемещения и перепуска электродов служит электродная площадка, представляющая собой сплошное перекрытие, расположенное на высоте 17,3 м. В новых цехах с печами, оборудованными гидравлической системой перемещения и перепуска электродов, устанавливаются местные площадки.
Перекрытие на отметке 23,5 м служит для крепления печных карманов, размещения системы конвейеров подачи шихты в них, монтажа вентиляционных установок, наращивания электродных кожухов и загрузки электродной массы с помощью мостового крана. Все перекрытия имеют сквозные проемы по торцам цеха для обеспечения печей электродной массой. Над каждой печью расположены также проемы для выполнения различных транспортных операций при ремонтах.
|
Далее располагается промежуточный пролет, который соединяет собой печной пролет и конвертерный. Промежуточный пролет шириной 15 м. Его основное назначение – пространство для маневров автошлаковозов и металловозов.
Затем за промежуточным пролетом располагается конвертерный, где находятся три конвертера. Ширина конвертерного пролета составляет 15 м.
Склад шихты
Отделение шихтоподготовки ферросплавного цеха предназначено для хранения, подготовки и дозирования шихтовых материалов. На ферросплавных заводах используют два различных варианта проектных решений шихтового хозяйства. На старых заводах каждый цех имеет свой собственный закрытый склад шихты, на открытом заводском складе обычно хранятся лишь те материалы, которые необходимы для работы нескольких цехов. Новые заводы отличаются централизованным хранением, подготовкой и распределением материалов по цехам. [8]
Шихтовое хозяйство современного ферросплавного цеха, оборудованного мощными рудовосстановительными печами с централизованным обеспечением шихтой, включает напольный открытый склад сырых материалов (ССМ), корпус вагоноопрокидывателей (ВО), закрытый склад, корпус подготовки материалов (КПМ), корпус шихтовых бункеров (КШЮ) с подготовленными материалами, дозировочные отделения (ДО) или дозировочные пункты (ДП), которые могут быть совмещены с КПМ или КШБ.
В шихтовом хозяйстве цеха для производства марганцевых и хромистых ферросплавов может быть предусмотрена соответствующая агломерационная (или брикетировочная) фабрика и цех обжига извести.
Напольный открытый склад сырых материалов служит для создания на заводе необходимого запаса сырых материалов, поставляемых из отдаленных районов, а также ведущих рудных материалов, суточный расход которых значителен. Материалы на этом складе хранятся в штабелях, разгружаются из вагонов козловыми грейферными кранами и в дальнейшем подаются железнодорожным транспортом через корпус ВО или по конвейерным галереям в ССМ.
|
При проектировании современных ферросплавных цехов для хранения шихтовых материалов предусматривается три типа складов: закрытый грейферный с железнодорожной колеей, проходящей посередине склада; закрытый безкрановый ангарного типа с конвейерной подачей и выдачей материалов; открытый с конвейерной подачей сырых материалов и мостовым грейферным перегружателем, который принимает, штабелирует и выдает материалы на подготовку.
Корпус ВО представляет собой здание ангарного типа с двумя сквозными железнодорожными путями, На каждом из которых установлен роторный стационарный ВО. С помощью ВО материал из вагона выгружается в подземные бункера, оборудованные тарельчатыми питателями, и далее конвейерами большой производительности, направляется на ССМ
В корпусе ССМ крупных ферросплавных цехов обычно не имеется железнодорожного въезда, а склад оборудован грейферными кранами, с помощью которых материал подается в КПМ.
В КПМ установлено необходимое сушильное, дробильное и классифицирующее оборудование, тип и количество которого определяется видами применяемых шихтовых материалов. На ферросплавных заводах применяется порционное и непрерывное дозирование шихты. При порционном дозировании используют порционные весовые автоматы и вращающиеся барабанные смесители.
На складе шихты, подготовленные шихтовые материалы загружают в отдельные для каждой печи дозировочные установки, оборудованные автодозаторами. Затем компоненты, образующие калошу шихты, выгружают в конвейер или в скиповый подъемник и транспортируют в плавильный корпус цеха к печам. Расчет шихты на определенную навеску ведущего компонента производит решающее устройство, в которое вводят требуемую величину соотношения компонентов шихты.
При скиповой подаче компоненты шихты дозируются в отделении шихтоподготовки, а шихта в плавильный корпус передается скиповым подъемником. При этом обеспечивается автоматическая подача шихты в печные карманы. Каждая печь обслуживается отдельной группой бункеров готовой шихты.
|
Себестоимость хранения, подготовки, дозировки и транспортировки шихтовых материалов в печные карманы при скиповой подаче меньше, чем при конвейерной. При движении шихты по конвейерному тракту за счет истирания образуется дополнительно 310 % коксовой мелочи фракции менее 5 мм. За счет налипания на ленту промасленной стружки и кокса их потери увеличиваются на 4,5 % и 3 % соответственно.
В современных цехах с мощными рудовосстановительными печами применяются в основном конвейерная подача сыпучих материалов. При этом в связи с малым уклоном конвейерных лент (17 %) и большой высотой цеха, галереи подачи сыпучих материалов занимают значительные площади. Применение скиповой подачи сыпучих материалов позволяет приблизить склад шихты и дозировочное отделение к плавильному корпусу.
Шихтовый пролет можно расположить непосредственно в плавильном корпусе, что значительно сокращает занимаемую предприятием площадь, однако, если в одном цехе расположены еще и продольные и поперечные пролеты, это создает неудобства в работе.
Общий запас шихтовых материалов Q в т. или мЗ на складах для ферросплавного цеха рассчитывается, исходя из суточного расхода материалов и установленных норм запаса, по формуле
При установке в цехе однотипных печей суточный расход материалов находят из выражения
Исходя из необходимого общего запаса шихтовых материалов рассчитывают размер складов. Фактически речь идет об определении длины склада при заданных его ширине и высоте штабеля материалов.
Таблица 4.1 – Нормы хранения шихтовых материалов, отходов и попутных материалов на складах ферросплавных цехов
Материал | Содержание основного элемента, % | Плотность, ![]() | Насыпная масса 1 ![]() | Примечание |
Руда хромовая | 45-53-Cr2O3 | 2400-2750 | Фракция 0-20 мм | |
Ферросиликохром | 50-Si | - | 2200-2500 | Фракция 0-25 мм |
Известь | 90 CaO | 600-620 | Фракция 40 мм |
Для выплавки одной тонны феррохром марки ФХ010, как известно, требуется:
· Хромовая руда (50% Cr203) – 1835кг; 44,65%
|
· ФСХ (48% Si) – 611 кг; 14,86%
· Известь (90% СаО) – 1650 кг; 40,15%
Таблица 4.2 - Плотность и насыпная масса шихтовых материалов для производства феррохром ФХ010.
Шихтовые материалы | Нормы хранения, сутки |
Руда хромовая Концентрат марганцевый Агломерат марганцевый неофлюсованный: при изготовлении на заводе при поставке извне Кварцит, коксовый орешек, полукокс, стружка стальная, известняк при поставках на расстояние: не более 200 км более 200 км Доломит Руда железная, оксид хрома, алюминий в чушках, уголь древесный, уголь каменный, плавиковый шпат Известь при изготовлении на заводе Пек каменноугольный, термоантрацит, кокс пековый Отсевы кокса, используемые при агломерации Отсевы кварцита | 15-30 1-2 15-30 |
Суточный расход хромовая руда составляет:
Суточный расход ФСХ составляет:
Суточный расход известь составляет:
Суточный расход электродной массы составляет:
Общий запас хромовая руда на складе:
Общий запас ФСХ на складе:
Общий запас известь на складе:
Общий запас электродной массы на складе:
Длина (м) закрытого грейферного склада с шириной пролета, а=30 м и высотой штабеля h = 3 м, которая по высоте равна высоте закрома 3 м вычисляется по формуле
Насыпная масса шихты рассчитывается по формуле
Длина (м) закрытого грейферного склада с шириной пролета, а=30 м и высотой штабеля h = 3 м, которая по высоте равна высоте закрома 3 м и составляет в общем 6 м и вычисляется по формуле
и учитываем по 6 м с двух сторон склада для простоя и ремонта кранов. В общем, длина склада составляет 36 м.
Длина склада для хранения ФСХ составляет
и учитываем по 6 м с двух сторон склада для простоя и ремонта кранов. В общем, длина склада составляет 18 м.
Склада для хранения известь составляет
и учитываем по 6 м с двух сторон склада для простоя и ремонта кранов.
и учитываем по 6 м с двух сторон склада для простоя и ремонта кранов. В общем, длина склада составляет 15 м.
Плавильный корпус цеха
В общем случае плавильный корпус ферросплавного цеха может состоять из следующих пролетов: печного, разливочного, трансформаторного, шихтового и основного. С расчетом мощности ферросплавных печей.
Плавильный корпус ферросплавного цеха с мощными печами имеет обычно два пролета: печной и разливочный.
Печной пролет служит для размещения и обслуживания плавильных электропечей. Печи располагаются вдоль цеха в линию. Ширину печного пролета принимаем равной 24 м. Длина печного пролета зависит от количества и типаю, расположенных в нем электропечей. В проектируемом цехе будет расположено 6 печи типа РКЗ – 10,5 МВА с внешним диаметром равным Дк = 6,2 м.
|
Общая длина пролета
Длина цеха определяется количеством и диаметром печей:
Lпп = (n·d) + (nмп·d) + (2·d) = 6*6,2+3*13000+2*6000=90м =15.
По проектируемым соображениям принимаем длину пролета 90 м, с шириной пролета 24 м.
На нулевой отметке пролета расположены фундаменты плавильных печей, механизмы выкатки для ковша металла и шлака, механизмы для наклона печи, оборудование и механизмы газоочисток, подсобное помещение.
Рабочая площадка, предназначенная для обслуживания печи, наблюдения за технологическим процессом и электрическим режимами, представляет собой сложное перекрытие и располагается на отметине 4,5-12 м.
Для обслуживания механизмов перемещения и перепуска электродов служит электродная площадка, расположенная на отметке 8,5-22,2 м. Перекрытие на отметке 19,8-30 м служит для крепления печных карманов, размещения системы конвейеров подачи шихты, вентиляционных установок, наращивания электродных кожухов и загрузки электродной массы. Для обеспечения печей электродом по торцам цеха имеются сквозные проемы.
Ширину разливочного пролета принимаем равной 24 м. Ширина пролета зависит от насыщенности оборудования, числа технологических операций со сплавами, количества и объема разливочной посуды.
В проектируемом цехе длина разливочного пролета будет равна 90 м, длине печного пролета.
Расчет кранов в разливочном пролете.
Разливочный пролет ферросплавного цеха оборудуют мостовыми кранами с двумя подъемниками (для кантования разливочного ковша).
В общем случае необходимое количество разливочных кранов в цехе определяется исходя из затрат времени крана на обработку одного ковша и числом выпусков сплава в цехе в сутки и рассчитывается по формуле
где, nк – число ковшей, обрабатываемых краном в сутки (равное числу выпусков). nк – 12.
tкр – затраты времени крана на обработку одного ковша, tкр = 50 мин.
1350 – общее время работы крана в сутки.
крана на 1 печь
При наличии в цехе 6 печей и с учетом резерва принимаем на разливочном пролете 4 крана.
Расчет емкости ковша и грузоподъемности кранов разливочного пролета.
Вместимость ковша определяем из выражения:
Vк = (nвс · t· nкв/24) · 1,15
где, nвс – число выпусков в смену
t – время обработки ковша, ч.
nкв – число ковшей, установленных под выпуск.
м3
Грузоподъемность кранов зависит от мощности печей: масса продуктов плавки, масса транспортируемого ковша.
Масса одной плавки вычисляется по формуле
где, nвс – количество выпусков за сутки.
Масса ковша емкостью 3 м3 = 7 т. Следовательно общая масса сплава с ковшом ~15 т. С учетом резерва выбираем 4 крана грузоподъемностью 20/5 т.
Объем одной изложницы
Количества изложницы
выбираем 28 изложницы
Время на разливку одной плавки определяется из уравнения
Расчет количества ковшей в цехе.
На основании рассчитанных данных по принятой технологии предусматривается под разливку на каждую печь по одному ковшу для сплава.
Учитывая сменную работу в цехе и время на охлаждение ковша после разливки, и другие операции принимаем, что в смену на одну печь приходится два ковша и один резервный, следовательно, на цех получаем ковшей:
С учетом того, что масса плавки иногда из-за технологии может быть больше, принимаем ковш с вместимостью 3 м3 в количестве 24 шт. (по 3 штуки и 1 в резерве)
Склад готовой продукции
Склад готовой продукции обычно представляет собой одно пролетное здание, располагающееся параллельно плавильному корпусу и соединяющееся с ним галереями разливочных машин. Склад оборудован 3 мостовыми кранами грузоподъемностью 30/5 т и устройствами для приема, дробления, сортировки и упаковки готового сплава. Слитки металла с разливочных машин падают в короба, установленные на самоходных тележках. Каждая разливочная машина оснащена двумя-тремя тележками для обеспечения непрерывного приема металла.
При ширине разгрузочной щели 140 мм, производительность дробилок составляет 100-130 м3/ч.Склад обычно оборудуется одними приемными весами, обслуживающими две разливочные машины и платформенными весами для взвешивания отправляемой в вагонах продукции.
Принимаем склад готовой продукции шириной 30 м,а длиной равной плавильному корпусу 90м, и с 3 мостовым краном грузоподъемностью 30/5т.
АВТОМАТИЗАЦИЯ ПРОИЗВОДСТВА
Развитие современного металлургического производства сопровождается интенсификацией технологических и производственных процессов. Создание крупных металлургических агрегатов и их комплексов позволяет более эффективно использовать сырье, топливо, капиталовложения. [2]
Однако осуществлять управление интенсифицированными металлургическими процессами в больших и сложных технологических объектах без использования новейших методов и средств управления неэффективно или вообще невозможно.
Наиболее эффективным средством управления технологическими объектами являются системы централизованного управления, создаваемые на основе теории управления, использующие экономико-математические методы, вычислительную и управляющую технику. Такие системы управления получили наименование автоматизированных систем управления технологическими процессами (АСУ ТП). В эти системы включена большая область систем управления технологическими объектами с разной степенью освобождения человека (оператора) от функций контроля и управления и передачи их автоматическим устройствам.
АСУ ТП представляют собой качественно новую ступень развития средств и методов управления технологическими объектами, так как в них используются технологические и технико-экономические параметры и критерии, а не только технические (физические), как это имело место ранее. В АСУ ТП воплощены достижения локальной автоматики, систем централизованного контроля, электронной и вычислительной техники.
Таким образом, АСУ ТП является также источником объективной и своевременной информации для АСУ вышестоящих уровней, как на металлургическом предприятии, так и в отрасли в целом. Современный металлургический агрегат представляет собой совокупность технологического оборудования и средств управления и образует автоматизированный технологический комплекс. Автоматизированное технологическое оборудование и сам технологический процесс являются технологическим объектом управления (ОУ).
Следовательно, АСУ ТП есть система, реализуемая на базе вычислительной и управляющей техники, обеспечивающая управление ОУ по технологическим и технико-экономическим критериям на основе централизованно обработанной информации, подготавливающая информацию для решения организационно-экономических задач на вышестоящих ступенях управления.
Назначения и функции.
Современные ФСП, особенно высокой и сверхвысокой мощности, должны обязательно оснащаться АСУ ТП, поскольку только в этом случае возможно обеспечить высокую эффективность и экономичность работы печи. Основными задачами автоматизированного управления процессом плавки в ФСП являются:
1. Централизованный контроль технологического процесса и работы печи с выдачей оперативной информации обслуживающему печь персоналу с регистрацией и сигнализацией отклонений от заданных значений основных параметров.
2.Управление технологическим процессом:
– расчет оптимального состава шихты;
– управление загрузкой шихты в соответствии с рассчитанным составом;
– расчет количества легирующих и шлакообразующих материалов, обеспечивающих получение металла заданного состава и качества и экономию материалов;
– управление подачей легирующих и шлакообразующих материалов;
– прогнозирование момента окончания технологических периодов плавки.
3.Управление энергетическим режимом, обеспечивающее максимальное использование мощности печи, минимальный расход электроэнергии и нормальную эксплуатацию печи и ее электрического оборудования - управление тепловым режимом, управление электрическим режимом, управление отводом отходящих из печи газов.
4.Управление вспомогательными операциями - отбором проб металла, замером температуры металла и др.
5.Сбор и отборка информации с выдачей необходимой документации - учет и регистрация расходов шихтовых материалов, электроэнергии, печатание протоколов плавки и др.
6. Контроль работы оборудования с сигнализацией и регистрацией неисправностей.
Для выполнения указанных задач АСУ ТП выплавки ферросплавов в ФСП осуществляет основные функции, перечисленные ниже.
I. Информационные и информационно-вычислительные функции:
Контроль величин - массы компонентов металлошихты, массы ферросплавов, массы шлакообразующих материалов, массы заправочных материалов, массы жидкого металла в ковше, электрической мощности (активной и реактивной), расхода электроэнергии (активной и реактивной), силы токов фаз и напряжения фаз печи; коэффициента мощности, температуры металла в ванне печи, температуры футеровки стен, температуры подины, расхода и давления кислорода, расхода и давления природного газа, давления под сводом рабочего пространства, расхода и состава отходящих газов, расхода и температуры охлаждающей воды, положения кислородной фурмы, окисленности металла в печи, сигнализация отклонения основных параметров от допустимых значений. [25]
1. Расчет - оптимального состава металлической шихты, количества ферросплавов, количества шлакообразующих материалов, количества кислорода на продувку, количества природного газа, параметров электрического режима, температуры металла по мгновенному тепловому балансу, технико-экономических показателей плавки.
2. Прогнозирование - моментов окончания технологических периодов, температуры ванны.
II. Управляющие функции:
1.Управление величинами - электрической мощностью, расходом кислорода, расходом природного газа, давлением по своду печи.
2.Управление процессами - набора и загрузки шихты, дозирования и загрузки ферросплавов, дозирования и загрузки шлакообразующих материалов, продувки ванны кислородом, расплавления шихты, рафинирования металла.
Реальные АСУ ТП могут реализовать не все, а только часть из перечисленных выше функций, но вместе с тем, могут выполнять и некоторые дополнительные функции.
На рисунке 5.1 в качестве примера показана структурная схема АСУ ТП РКЗ-10,5.
В качестве УВК на верхнем уровне используется мини-ЭВМ (например, типа СМ-2 или СМ-4).
Особенностью АСУ ТП является использование микро-ЭВМ (может быть применен и регулируемый микропроцессорный контроллер) в локальной системе управления тепловым режимом на нижнем уровне.
Эта система управляет переключателем ступени напряжения (ПСН) и вырабатывает задание регулятору мощности.
Рисунок 5.1 – Структурная схема АСУ ТП РКЗ-10,5
1 - система автоматического управления (САУ) загрузкой расходных бункеров: 2 - САУ взвешиванием металлошихты; 3 - САУ дозированием и подачей сыпучих материалов и ферросплавов в печь и сталеразливочный ковш; 4 - САУ дозирования заправочных материалов; 5 - САУ продувкой ванны кислородом; 6 - САУ тепловым режимом; 7 - САУ давлением в печи; 8 - автоматизированная система химического анализа; 9 - система определения периодов плавки; 10 - автоматический регулятор мощности; 11 - САУ работой газо-кислородных горелок; 12 - весовая тележка; 13 - бункера с дозирующими устройствами для шлакообразующих материалов и ферросплавов; 14 - конвейер; 15 - корзина для загрузки металлической шихты с весоизмерительным устройством; 16 - сталеразливочный ковш;
17 - устройство контроля расхода и температуры воды для охлаждения стен и свода печи;
18 - устройство контроля температуры подины печи; 19- датчики тока и напряжения фаз печи; 20 - датчик температуры металла; 21 - датчик температуры футеровки печи;
22 - датчики электрических величин на высокой стороне трансформатора; Т - печной трансформатор; ПСН - переключатель ступеней напряжения; УИП - устройство измерения параметров; УВК - управляющий вычислительный комплекс; ВВ - высоковольтный выключатель
СПЕЦИАЛЬНАЯ ЧАСТЬ
Краткое описание
В данной части дипломного проекта рассмотрено «Разработка технических решений по совершенствованию технологии переработки шлаковых гарнисажей от производства рафинированного феррохрома и повышению извлечения из них металла на фабрике пневмопросева Актюбинского завода ферросплавов».
Разработке предшествовали экспериментальные исследования по извлечению магнитных фракций из распадающихся шлаков и пылевидных материалов, выполненные в ОАО «УИМ» на лабораторной установке, в экспериментальных условиях ООО «Эрга Плюс» г. Калуга на промышленном магнитном сепараторе решетчатого типа с пробами шлака рафинированного феррохрома и в системе пневмотранспорта ферропыли фабрики пневмопросева АЗФ.
Результаты выполненных работ позволили сформулировать основные технические требования к конструкции промышленного магнитного сепаратора: обеспечение работоспособности сепаратора в системах пневмотранспорта пыли на ДСУ по переработке отвальных шлаков РФХ; обеспечение эксплуатационной надежности сепаратора в условиях работы с высокой концентрацией пылевидных, абразивных материалов в широком диапазоне магнитных свойств.
Наименование
Сепаратор на основе постоянных магнитов для извлечения ферромагнитных включений в системе пневмотранспорта мелкозернистых и тонкодисперсных материалов.
Цель и назначение
Цель работы - разработка требований к конструкции и условиям эксплуатации промышленных сепараторов для их изготовления и применения в технологических схемах улавливания мелких магнитных продуктов на установке для переработки отвальных шлаков АЗФ - филиала АО «ТНК «Казхром».
Сепаратор предназначен для улавливания и вывода ферромагнитных включений из потока мелкозернистых и тонкодисперсных сыпучих материалов в системах пневмотранспорта пыли и разгрузки их в специальные емкости или на конвейеры.
6.4 Технические требования для изготовления магнитного сепаратора
Состояние вопроса
Технология переработки отвальных шлаков РФХ, включает следующие основные технологические операции:
- отбор негабарита;
- дезинтеграцию агломерированных продуктов распада и очистку кускового шлака от продуктов распада;
- извлечение ценных компонентов ручным и механизированным способом;
- дробление окускованного шлака;
- сортировку шлака по крупности;
- выделение в пневмоклассификаторе материала фракции крупнее 0,3мм;
- пневмотранспорт мелкозернистого пылевидного шлака крупностью менее 0,3мм;
- извлечение ферромагнитных включений из потока шлака крупностью менее 0,3мм в системе пневмотранспорта мелкозернистого пылевидного шлака;
- осаждение в системе улавливания пыли фракционированных порошков различной крупности.
Исследования состава и свойств отсева отвального шлака фракции менее 0,3мм показали, что в нем содержится от 1,4% до 8,91% ферромагнитных включений, состоящих из агломерированных частичек шлака и сплава с различным содержанием хрома и железа, которые, находясь в составе мелкозернистого шлака, не только теряются, но и ухудшают его качество.
Как показали результаты проведенных исследований, извлечение ферромагнитных включений из шлака методами магнитной сепарации достаточно эффективно. Полученный в результате сепарации магнитный продукт может быть непосредственно направлен на переплав, подвержен дальнейшему обогащению на мокром или сухом магнитном сепараторе с получением богатого концентрата, использован в составе рудно -металлических брикетов или непосредственно для рафинирования чугуна и стали.
В общем коллекторе диаметром 710мм, объединяющем четыре секции пневмоклассификатора, на вертикальном участке на фланцах устанавливают один магнитный сепаратор (рисунок 6.1).
0-10мм |
На магнитную сепарацию |
В силосный склад |
1 - секция пневмоклассификатора; 2 - воздуховод; 3 - магнитный сепаратор 4 - течка магнитного продукта; 5 - клапан - мигалка; 6 - емкость для магнитного продукта; 7 - конвейер отгрузочный; 8 - пылеосадитель; 9 - циклон; 10 - шибер; 11 - технологический вентилятор. Рисунок 6.1 - Принципиальная схема размещения магнитного сепаратора для извлечения ферромагнитных включений из потока шлака фракции - 0,3 + 0мм на установке по переработке отвальных шлаков среднеуглеродистого феррохрома |
-10+0,3 мм |
-0,3+0 мм |
Очистка рабочего органа магнитного сепаратора от налипших частиц магнитного продукта должна производиться непрерывно, без остановки технологического процесса. Магнитный продукт выгружают в специальную емкость, или на конвейер и отправляют на склад готовой продукции.
При переработке 300 тыс. т в год отвальных шлаков РФХ расчетный выход магнитного продукта после сепараторов, установленных в системе пневмотранспорта, составит порядка 5% от массы материала крупностью -0,3+0мм. В настоящее время разработаны и изготавливаются постоянные магниты, на основе которых возможно создать конструкцию и изготовить специальный промышленный сепаратор, способный улавливать в тяжелых условиях эксплуатации большое количество ферромагнитных включений в системе пневмотранспорта потока мелкозернистых сыпучих материалов.
Существующие в настоящее время конструкции сепараторов на постоянных магнитах предназначены для обработки материалов, содержащих сравнительно небольшое количество случайных ферромагнитных включений. Их непосредственное применение в технологии переработки распадающихся шлаков и других мелкодисперсных материалов, содержащих более 1% ферромагнитных включений, затруднено без модернизации узла улавливания и разгрузки магнитного продукта, включающего рабочие органы и их привод.
6.4.2 Состав магнитного сепаратора и требования к конструктивному устройству
В состав магнитного сепаратора входят следующие узлы и детали (рисунок 6.2):
- корпус сепаратора 1;
- набор кожухов (рабочих обечаек) 2, выполненный из немагнитных марок стали, смонтированный на приводных валах, обеспечивающий вывод ферромагнитных включений из зоны действия магнитного поля магнитного диска;
- набор магнитных дисков 3 из постоянных магнитов, смонтированных на стационарных валах, соосных приводным валам кожухов;
- скребки - сбрасыватели 4, обеспечивающие принудительный съем ферромагнитных частиц с поверхности кожухов дисков;
- течки 5 для вывода магнитного продукта из рабочей зоны сепаратора;
- трубопровод мелкозернистых и тонкодисперсных пылевидных материалов 6, в который осуществляется врезка магнитного сепаратора;
- привод кожухов (обечаек) магнитных дисков 7;
- манжеты боковые 8 и торцовые 9 для исключения подсоса воздуха и возврата магнитного продукта в рабочую камеру сепаратора при разгрузке магнитного продукта;
- люк ремонтный 10;
- клапаны - мигалки 11 для исключения подсоса воздуха в рабочую камеру сепаратора;
-0,3+0 мм |
М22 |
1 - корпус сепаратора, 2 - кожух магнитного диска, 3 - магнитный диск, набранный из постоянных магнитов, 4 - скребок - сбрасыватель, 5 - течки для вывода магнитного продукта, 6 - трубопровод пыли, 7 - привод кожуха - обечайки, 8 - боковая манжета - обратный клапан, 9 торцевая манжета - обратный клапан, 10 - люк ремонтный, 11 - клапан - мигалка.
Рисунок 6.2 - Принципиальная схема сепаратора с дисковыми постоянными магнитами для извлечения ферромагнитных включений из потока мелкозернистых и тонкодисперсных материалов в системах пневмотранспорта
Корпус сепаратора 1 и кожухи (обечайки) 2 магнитных дисков 3 рекомендуется выполнить из нержавеющих, износоустойчивых, немагнитных марок стали. Постоянные магнитные диски 3 закрепить на параллельных валах в корпусе сепаратора. Набор кожухов (обечаек) магнитных дисков закрепить на полых валах, посаженных на подшипники соосно валам магнитных дисков. Полые валы кожухов соединить с приводом и обеспечить свободное вращение кожухов (обечаек) относительно стационарно закрепленных магнитных дисков навстречу потоку обрабатываемого материала. Принятое направление вращения кожухов, обеспечит вынос слабомагнитных зашлакованных включений металла с поверхности кожухов встречным потоком воздуха и материала, будет способствовать повышению качества магнитного продукта. Зазор между кожухом и магнитным диском принять минимальным из условий обеспечения свободного вращения кожухов относительно магнитных дисков при улавливании и отводе магнитного продукта из рабочей полости сепаратора. Расстояние между кожухами (обечайками) в рабочей полости сепаратора принимается примерно равным ширине кожуха магнитного диска. Количество магнитных дисков зависит от диаметра воздуховода, в который будет встроен сепаратор. В нашем случае - на установке для переработки отвальных распадающихся шлаков РФХ диаметр трубопровода объединенного коллектора от четырех пневмоклассификаторов равен 710мм. Принимая диаметр кожуха (обечайки) магнитного диска примерно равным диаметру воздуховода, т.е. 700мм, а ширину кожуха (обечайки) равной 0,1 диаметра кожуха 70мм, определена общая площадь сечения корпуса классификатора, с учетом площади рабочей поверхности кожухов. Площадь живого сечения классификатора должна быть не меньше площади сечения трубопровода коллектора. В результате расчетов получены следующие результаты. Площадь сечения воздуховода 0,396м2, площадь рабочей поверхности кожухов 0,294м2, площадь сечения рабочей камеры сепаратора 0,690м2. Длина стороны сечения рабочей камеры сепаратора составит 830мм. Для снижения взаимного воздействия магнитных полей зазор между кожухами магнитных дисков принят равным 0,1 диаметра кожуха, т.е. 70мм. Это рекоме
|
|
Типы оградительных сооружений в морском порту: По расположению оградительных сооружений в плане различают волноломы, обе оконечности...
Типы сооружений для обработки осадков: Септиками называются сооружения, в которых одновременно происходят осветление сточной жидкости...
Археология об основании Рима: Новые раскопки проясняют и такой острый дискуссионный вопрос, как дата самого возникновения Рима...
История развития хранилищ для нефти: Первые склады нефти появились в XVII веке. Они представляли собой землянные ямы-амбара глубиной 4…5 м...
© cyberpedia.su 2017-2024 - Не является автором материалов. Исключительное право сохранено за автором текста.
Если вы не хотите, чтобы данный материал был у нас на сайте, перейдите по ссылке: Нарушение авторских прав. Мы поможем в написании вашей работы!