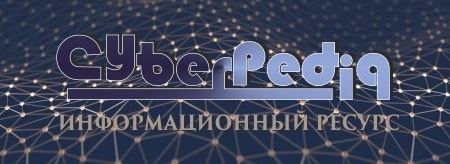
Организация стока поверхностных вод: Наибольшее количество влаги на земном шаре испаряется с поверхности морей и океанов (88‰)...
Общие условия выбора системы дренажа: Система дренажа выбирается в зависимости от характера защищаемого...
Топ:
Основы обеспечения единства измерений: Обеспечение единства измерений - деятельность метрологических служб, направленная на достижение...
Техника безопасности при работе на пароконвектомате: К обслуживанию пароконвектомата допускаются лица, прошедшие технический минимум по эксплуатации оборудования...
Интересное:
Отражение на счетах бухгалтерского учета процесса приобретения: Процесс заготовления представляет систему экономических событий, включающих приобретение организацией у поставщиков сырья...
Финансовый рынок и его значение в управлении денежными потоками на современном этапе: любому предприятию для расширения производства и увеличения прибыли нужны...
Что нужно делать при лейкемии: Прежде всего, необходимо выяснить, не страдаете ли вы каким-либо душевным недугом...
Дисциплины:
![]() |
![]() |
5.00
из
|
Заказать работу |
|
|
ЛАБОРАТОРНЫЕ РАБОТЫ
ПО МАТЕРИАЛОВЕДЕНИЮ
И
ТЕХНОЛОГИИ КОНСТРУКЦИОННЫХ
МАТЕРИАЛОВ
Студент: Сиротенко Никита Анатольевич
Г. Новороссийск
Год.
ЛАБОРАТОРНАЯ РАБОТА № 1
МЕХАНИЧЕСКИЕ ИСПЫТАНИЯ МЕТАЛЛОВ
Цель работы: ознакомление с оборудованием и методами определения механических свойств металлов.
Испытания, в том числе и механические, проводятся, для того чтобы установить свойства материалов. В зависимости от свойств решается вопрос использования их в судостроении, судоремонте или другой области.
Механические свойства определяют сопротивление металлов и сплавов воздействию механических усилий, которые могут прилагаться к исследуемому материалу различными способами.
Механические испытания в зависимости от вида прилагаемой нагрузки (нагрузка возрастает медленно и плавно; нагрузка носит ударный характер; нагрузка переменная и др.) могут быть статическими, динамическими, усталостными и др.
При статических испытаниях - растяжение, сжатие, изгиб и др. определяют поведение материалов при плавно возрастающей нагрузке. Например, при испытаниях на растяжение устанавливают прочностные и пластические свойства материалов.
При динамических испытаниях (например, испытания на ударный изгиб) выявляют склонность металла к хрупкому разрушению, которое оценивается ударной вязкостью. Скорость деформирования металла при динамических испытаниях значительно выше, чем при статических.
Длительное воздействие переменных (циклических) нагрузок может вызывать образование трещин и разрушение металлических деталей при напряжениях ниже предела текучести.
|
Испытание на растяжение
При испытании на растяжение определяют прочность и пластичность материалов.
Под прочностью понимают способность тела сопротивляться деформациям и разрушению.
Под пластичностью понимают способность тела к пластической деформации, т.е. способность получать остаточные изменения формы и размеров без нарушений сплошности.
Испытание металлов на твердость
Твердостью называется способность материала сопротивляться вдавливанию в него другого более твердого тела определенной формы и размеров.
Для испытания материалов на твердость используются специальные приборы, которые называются твердомерами или прессами. Применяются твердомеры различных типов: Бринеля, Роквелла и Виккерса. Отсюда и метод испытания твердости соответственно называют: по Бринеллю, по Роквеллу, по Виккерсу
Испытания на твердость по Роквеллу
Определение твердости по Роквеллу производится путем вдавливания в испытуемый металл стального шарика диаметром 1,59 м или алмазного конического наконечника с углом при вершине 120°
отличие от способа Бринеля твердость по Роквеллу определяют не по площади отпечатка, а по глубине вдавливания стального шарика или алмазного наконечника в испытуемый металл.
Вдавливание шарика или алмаза производится действием двух последовательно прилагаемых нагрузок: предварительной, равной 10 кг и основной, равной 60 кг, 100 кг или 150 кг. На приборе Роквелла вдавливание производится автоматически, а число твердости отсчитывается на циферблате индикатора. Индикатор прибора имеет две шкалы: черную C для испытания алмазным конусом закаленных сталей с нагрузкой 150 кг и красную B для испытания стальным шариком с нагрузкой 100 кг, до которой определяется твердость незакаленной стали, бронзы, латуни. Испытание очень твер-дых материалов производится алмазным наконечником с нагрузкой 60 кг и отсчетом по черной шкале, обозначенной буквой A.
При выражении твердости по Роквеллу к знаку твердости – HR добавляют индекс, обозначающий шкалу по которой производилось испытание, например: HRC, HRB и HRA.
|
Метод Роквелла получил широкое распространение в промышленности.
ЛАБОРАТОРНАЯ РАБОТА № 2
Изучение изломов металла
Изломом называется поверхность, по которой произошло разрушение образца или детали.
В зависимости от режима термической обработки и условий эксплуатации изделия могут разрушаться вязко или хрупко. В соответствии с этим изломы делятся на вязкие, хрупкие и смешанные.
Вязкий излом (волокнистый) имеет пепельно-серый цвет. На поверхности разрушения отсутствуют кристаллические фасетки. Данному разрушению предшествует значительная пластическая деформация. В связи с этим по излому нельзя судить о форме и размере зерна.
Хрупкий излом характеризуется наличием на поверхности блестящих плоских фасеток, образовавшихся в условиях разрушения путем отрыва.
В зависимости от условий эксплуатации и качества металла изломы бывают усталостные, шиферные, нафталинистые.
Усталостный излом, схема излома шатунной шейки
коленчатого вала с типичными знаками (сталь 40ХНМА)
1- фокус излома и зона очага разрушения; 2- вторичные ступеньки и рубцы; 3- усталостные линии; 4- зона ускоренного развития излома; 5- зона долома.
На поверхности излома можно различить пять характерных зон:
- фокус излома - малая локальная зона, близкая к точке возникновения начальной макроскопической трещины усталости;
- очаг разрушения - небольшая зона, прилегающая к фокусу излома. При больших напряжениях может быть несколько очагов разрушения. На поверхности излома эта зона имеет наибольший блеск и гладкость. Усталостные линии на очаге разрушения обычно отсутствуют.
- участок избирательного развития соответствует зоне развившейся трещины усталости;
-участок ускоренного развития трещин является переходной зоной между участками усталостного развитии трещины и зоной долома;
- зона долома характеризуется признаками макрохрупкого разрушения.
Изучение макрошлифов
Макрошлифом называется специальный образец (темплет), вырезанный в определенном месте деталей и имеющий плоскую шлифованную поверхность, которая в зависимости от цели исследования протравливается специальными реактивами.
|
На макрошлифах выявляются и изучаются следующие основные дефекты стали: усадочная раковина, пористость, подкорковые пузыри, зональная и дендритная ликвация, волосовины, неметаллические включения.
Исследование макрошлифов сварных швов позволяет определить качество сварки, надежность сварного шва, макроструктуру наплавленного металла. В сварных швах наблюдают следующие дефекты: непровар, пережог, пористость, трещина.
Непроварами называют отсутствие соединения между основными и наплавленным металлам. Причиной непровара может быть загрязнение поверхности свариваемых деталей пли недостаточная температура разогрева основного металла.
Пережог образуется при нарушении режима сварки и сопровождается окислением основного и наплавленного металла. При этом прочность шва понижается.
Пористость характеризуется наличием газовых пузырей в сварном шве. Трещины вызываются большими внутренними растягивающими напряжениями, которые возникают при охлаждении наплавленного металла.
ЛАБОРАТОРНАЯ РАБОТА № 4
КЛЕЕВЫМИ КОМПОЗИЦИЯМИ
Цель работы: Освоить практические навыки по устранению коррозионных износов судовых механизмов и корпусных конструкций клеевыми композициями, входящими в состав судовой "аптечки".
Уметь определять основные причины и характер износов корпусных конструкций, а также уметь восстановить места износов при помощи материалов, находящихся в судовой "аптечке".
ЛАБОРАТОРНАЯ РАБОТА № 5
РЕЖУЩЕГО ИНСТРУМЕНТА
Цель работы: Научиться определять углы резания токарных резцов и свѐрл, координатные плоскости режущего инструмента и его углы; осуществлять заточку режущего инструмента.
Элементы резца.
Токарный резец состоит из тела А, служащего для закрепления, резца в резцедержателе, и головки Б, предназначенной для осуществления процесса резания
Головка резца образована поверхностями: передней I, главной задней 2, вспомогательной задней 3, опорной 4 и боковыми 5. Пересечение передней и главной задней поверхностей образует главную режущую кромку а; пересечение передней и вспомогательной задней поверхностей образует вспомогательную режущую кромку б; место сопряжения кромок а и б называется вершиной резца
|
Координатные плоскости
Для суждения об относительном положении резца и обрабатываемой де- тали служат координатные плоскости
Основная плоскость I - это плоскость, параллельная направлениям подач и проходящая через опорную поверхность резца; Плоскость резания 2 - это плоскость, касательная к поверхности резания детали и проходящая через главную режущую кромку резца; Главная секущая плоскость 3 - это плоскость, перпендикулярная к основной плоскости и к плоскости резания.
Основные углы резца
Углами резца, подлежащими измерению, являются:
1) углы, измеряемые в главной секущей плоскости (главные углы)
2) углы в плане резца
Элементы спирального сверла
Спиральное сверло состоит из рабочей части, включающей режущую часть с режущими кромками; хвостовика (цилиндрического или конического) для крепления сверла в шпинделе станка; шейки, лапки, служащей упором при выбивании сверла, из гнезда-шпинделя
Режущая часть свѐрла состоит из следующих элементов: двух зубьев, образованными двумя канавками для отвода стружки; сердцевины - средней части сверла, соединяющей оба зуба; двух передних поверхностей, по которым сбегает стружка и которые, воспринимают силу резания; двух ленточек - узких полосок по наружному диаметру сверла, служащих для его направления и центрирования в отверстие, двух главных: режущих кромок, образованных пересечением передних и задних поверхностей и выполняющих основную работу резания; попе- речной кромки или перемычки, образованной пересечением обеих задних поверхностей. Сверло имеет в общей сложности пять режущих кромок, из которых - две главные, две вспомогательные - и одна поперечная.
ЛАБОРАТОРНАЯ РАБОТА № 7
ЛАБОРАТОРНАЯ РАБОТА № 8
КАПИЛлЯРНЫЕ МЕТОДЫ НЕРАЗРУШАЮЩЕГО
КОНТРОЛЯ ОТЛИВОК
Цель работы: Изучить методы капиллярного контроля отливок. Научиться выполнять керосиновую пробу.
Сущность всех методов капиллярной дефектоскопии состоит в том, что на очищенную очистителем поверхность отливки 1 наносят тонкий слой индикаторной жидкости или суспензии – пенетранта, который под действием капиллярных сил проникает в мелкие поверхностные дефекты 2. Избыток пенетранта смывается очистителем, а на высушенную поверхность наносят слой проявителя 3, способного адсорбировать пенетрант, оставшийся в микродефектах. После выдержки, а при необходимости и тепловой сушки, на поверхности изделия образуется так называемый индикаторный след 4 шириной Хи>Хд (Хд – раскрытие дефекта).
|
Схема капиллярного метода
Индикаторный след можно наблюдать невооруженным глазом или с помощью лупы небольшого увеличения. Обнаружение этого следа, повторяющего характер дефекта, обусловлено либо его способностью люминесцировать под действием ультрафиолетового излучения, для чего используют источник ультрафиолетового излучения 5, либо его цветовым контрастом в видимом световом излучении.
Простейшей методикой капиллярного контроля является мыльная проба, предполагающая очистку и обезжиривание контролируемой поверхности с последующим нанесением на нее мыльного раствора. Проникая в капиллярные каналы поверхностных дефектов, мыльный раствор вытесняет из них воздух, который в виде пузырьков выходит на поверхность и очерчивает дефект. Мыльная проба не обеспечивает высокой чувствительности контроля, однако, может оказаться полезной при отсутствии специальных дефектоскопических материалов.
Керосиновую пробу также применяют при отсутствии специальных дефектоскопических материалов. На предварительно очищенную и обезжиренную поверхность отливки наносят слой керосина, обладающего хорошей проникающей способностью. В дальнейшем после протирки ветошью, на поверхность наносят меловое покрытие. Через некоторое время керосин, оставшийся в полостях дефектов впитывается в меловое покрытие и образует на нем хорошо видимые индикаторные следы. Керосиновую пробу применяют также как способ течеискания. При этом поверхность проверяемой отливки со стороны, доступной осмотру, покрывают слоем меловой краски. После ее высыхания поверхность отливки с противоположной стороны обильно смачивают керосином. Через 15 – 60 минут производят осмотр мелового покрытия, на котором в местах сквозных дефектов появляются полосы и пятна.
Цветной метод капиллярного контроля является одним из наиболее чувствительных. Его широко применяют для контроля особо ответственных отливок, например, лопаток газовых турбин.
Поверхность контролируемой отливки тщательно очищают от загрязнений, обезжиривают ацетоном или бензином, а затем сушат в струе теплого воздуха (60-800С). Пенетрант представляет собой насыщенный раствор жирорастворимых красителей («Судан III», «Судан IV» и др.) в смеси керосина, бензина, бензола или скипидара. Через некоторое время после нанесения пенетранта его удаляют с поверхности отливки протиркой сухой или смоченной в смеси керосина и трансформаторного масла ветошью. В качестве проявителя используют разнообразные составы, например, коллодий на ацетоне – 60%; бензол – 40%; цинковые белила – 50 г/л.
Осмотр отливок производят при естественном или искусственном освещении через 1 – 30 мин после нанесения проявителя. Индикаторный след имеет ярко-красную или оранжевую окраску на фоне проявителя.
С целью повышения контрастности индикаторного следа используют явление люминесценции, т.е. свечения некоторых веществ под действием электромагнитного излучения с длиной волны 0,2 – 0,4 мкм. Одним из простых пенетрантов, способных люминесцировать, является смесь 85% керосина и 15% трансформаторного масла.
В качестве проявителей, применяемых при люминесцентно-порошковом контроле, используют мелкодисперсные порошки MgO, CaCO3 или MgCO3.
Через 20-30 минут поверхность осматривают при ультрафиолетовом излучении. Под действием ультрафиолетового излучения в местах расположения дефектов мигрировавший на поверхность пенетрант будет светиться. При отсутствии поверхностных дефектов поверхность отливки останется темной.
ЛАБОРАТОРНЫЕ РАБОТЫ
ПО МАТЕРИАЛОВЕДЕНИЮ
И
ТЕХНОЛОГИИ КОНСТРУКЦИОННЫХ
МАТЕРИАЛОВ
Студент: Сиротенко Никита Анатольевич
Г. Новороссийск
Год.
ЛАБОРАТОРНАЯ РАБОТА № 1
МЕХАНИЧЕСКИЕ ИСПЫТАНИЯ МЕТАЛЛОВ
Цель работы: ознакомление с оборудованием и методами определения механических свойств металлов.
Испытания, в том числе и механические, проводятся, для того чтобы установить свойства материалов. В зависимости от свойств решается вопрос использования их в судостроении, судоремонте или другой области.
Механические свойства определяют сопротивление металлов и сплавов воздействию механических усилий, которые могут прилагаться к исследуемому материалу различными способами.
Механические испытания в зависимости от вида прилагаемой нагрузки (нагрузка возрастает медленно и плавно; нагрузка носит ударный характер; нагрузка переменная и др.) могут быть статическими, динамическими, усталостными и др.
При статических испытаниях - растяжение, сжатие, изгиб и др. определяют поведение материалов при плавно возрастающей нагрузке. Например, при испытаниях на растяжение устанавливают прочностные и пластические свойства материалов.
При динамических испытаниях (например, испытания на ударный изгиб) выявляют склонность металла к хрупкому разрушению, которое оценивается ударной вязкостью. Скорость деформирования металла при динамических испытаниях значительно выше, чем при статических.
Длительное воздействие переменных (циклических) нагрузок может вызывать образование трещин и разрушение металлических деталей при напряжениях ниже предела текучести.
Испытание на растяжение
При испытании на растяжение определяют прочность и пластичность материалов.
Под прочностью понимают способность тела сопротивляться деформациям и разрушению.
Под пластичностью понимают способность тела к пластической деформации, т.е. способность получать остаточные изменения формы и размеров без нарушений сплошности.
|
|
Опора деревянной одностоечной и способы укрепление угловых опор: Опоры ВЛ - конструкции, предназначенные для поддерживания проводов на необходимой высоте над землей, водой...
Семя – орган полового размножения и расселения растений: наружи у семян имеется плотный покров – кожура...
Типы сооружений для обработки осадков: Септиками называются сооружения, в которых одновременно происходят осветление сточной жидкости...
Таксономические единицы (категории) растений: Каждая система классификации состоит из определённых соподчиненных друг другу...
© cyberpedia.su 2017-2024 - Не является автором материалов. Исключительное право сохранено за автором текста.
Если вы не хотите, чтобы данный материал был у нас на сайте, перейдите по ссылке: Нарушение авторских прав. Мы поможем в написании вашей работы!