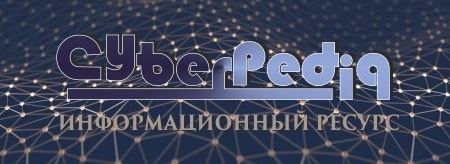
Наброски и зарисовки растений, плодов, цветов: Освоить конструктивное построение структуры дерева через зарисовки отдельных деревьев, группы деревьев...
Археология об основании Рима: Новые раскопки проясняют и такой острый дискуссионный вопрос, как дата самого возникновения Рима...
Топ:
Характеристика АТП и сварочно-жестяницкого участка: Транспорт в настоящее время является одной из важнейших отраслей народного хозяйства...
Особенности труда и отдыха в условиях низких температур: К работам при низких температурах на открытом воздухе и в не отапливаемых помещениях допускаются лица не моложе 18 лет, прошедшие...
Интересное:
Что нужно делать при лейкемии: Прежде всего, необходимо выяснить, не страдаете ли вы каким-либо душевным недугом...
Искусственное повышение поверхности территории: Варианты искусственного повышения поверхности территории необходимо выбирать на основе анализа следующих характеристик защищаемой территории...
Лечение прогрессирующих форм рака: Одним из наиболее важных достижений экспериментальной химиотерапии опухолей, начатой в 60-х и реализованной в 70-х годах, является...
Дисциплины:
![]() |
![]() |
5.00
из
|
Заказать работу |
Содержание книги
Поиск на нашем сайте
|
|
Процессы производства стали представляют собой сложные комплексы физико-химических превращений, происходящих при высоких температурах. Участие в процессах принимают одновременно многие компоненты, находящиеся в различных агрегатных состояниях: в твердом (футеровка плавильных агрегатов, добавочные материалы и т. п.), жидком (металл, шлак) и газообразном (атмосфера печи, продуваемые через металл воздух или кислород и т. п.).
Непрерывно повышаются требования к качеству металла, к уровню технико-экономических показателей того или иного процесса. Для выполнения этих требований необходимо непрерывно углублять знания в области физико-химических методов исследования. Существующие методы контроля позволяют получать информацию о параметрах плавки стали (концентрации взаимодействующих веществ, давлении, температуре и т. д.). Полученная информация дает возможность при использовании законов физической химии определить:
1Направление протекания процесса, реакции; какие продукты образуются в результате протекания процесса.
2. Конечное состояние системы: пределы, до которых может протекать процесс, состояние системы при окончании процесса.
3. Скорость протекания процесса, ее зависимость от отдельных параметров.
Первые две задачи решаются методами термодинамики, третья – современными методами исследования кинетики процесса. Для получения возможно более достоверной информации о процессе желательно сочетание, по крайней мере, трёх методов: расчетного, экспериментального и опытного.
К основным законам физико-химического равновесия гомогенных и гетерогенных систем относятся законы действия масс и распределения.
|
Закон действия масс. Скорость химической реакции прямо пропорциональна произведению концентраций реагирующих веществ, возведенных в степени, равные их стехиометрическим коэффициентам.
Для обратимой реакции aA + bB ↔ dD + eE … скорости прямой и обратной реакций соответственно составляют
; (1.1)
; (1.2)
где С – концентрация вещества в растворе.
В момент равновесия
. (1.3)
При неизменной температуре константы скорости К1 и К2 и, следовательно, К1/ К2=К – величины постоянные. Это отношение называется константой равновесия, а уравнения (1.1) – (1.3) – уравнениями закона действия масс.
При участии в реакциях газообразных веществ концентрации последних в уравнении (1.3) часто выражают через парциальные давления
;
.
Закон распределения. При равновесии двух соприкасающихся несмешивающихся фаз и неизменной температуре отношение концентраций какого-либо вещества, растворенного в одной из фаз, к концентрации этого же вещества в другой есть величина постоянная. Данная закономерность – частный случай закона действия масс.
В зависимости от агрегатного состояния контактирующих фаз и характеристик концентраций распределяемого между ними вещества применяют различные формы выражения закона распределения.
Закон Нернста. При равновесии двух соприкасающихся конденсированных (жидких и твердых) фаз отношение концентраций вещества в первой фазе к его концентрации во второй – величина постоянная при данной температуре
. (1.4)
Так, если в жидком шлаке и металле достигнуто равновесие процесса , то коэффициент распределения серы
есть величина постоянная при неизменной температуре.
Закон Генри. При равновесии газа с разбавленным раствором вещества А в конденсированной (жидкой или твёрдой) фазе концентрация вещества пропорциональна парциальному давлению его пара в газовой фазе
;
. (1.5)
где КА – константа распределения газа, величина постоянная при неизменной температуре.
Закон Сивертса является частным случаем закона Генри. Он учитывает реакцию диссоциации молекул газа на атомы, предшествующую процессу растворения атомов газа в конденсированной фазе. Так, растворение водорода в железе можно описать:
|
;
;
;
;
(1.6)
где КН – константа растворимости водорода в железе.
Закон Рауля. При равновесии газовой фазы с конденсированной давление насыщенного пара растворителя А пропорционально его мольной доле в растворе
, (1.7)
где – равновесное парциальное давление (давление насыщенного пара) растворителя при
.
Для реальных систем применяют те же законы, что и для идеальных, но в уравнения, описывающие эти законы, вводят поправочные коэффициенты, учитывающие взаимодействие частиц реальных растворах.
Применительно к реальным системам вводится понятие активность вещества аi, которая характеризует его способность реагировать с другими веществами. Так как одним из её признаков является склонность вещества выделяться из раствора, то аi пропорциональна парциальному давлению насыщенного пара вещества или активности последнего в какой-либо конденсированной фазе, равновесной с изучаемым раствором.
Коэффициент активности вещества А ( – в концентрированном растворе;
– в разбавленном) учитывает степень отклонения свойств вещества в реальной системе от его свойств в идеальной:
;
. (1.8)
Для реальных систем законы физико-химического равновесия описываются следующими уравнениями:
закон действия масс ; (9)
закон распределения Нернста ; (1.10)
закон Генри ; (1.11)
закон Рауля . (1.12)
Состояние вещества с активностью а=1 называется стандартным. В качестве стандартного состояния чаще всего выбирают чистое вещество, насыщенный или бесконечно разбавленный раствор (в металлургии – однопроцентный).
Коэффициенты активности и
используют при выражении вещества А в молярных (или ионных) долях и в массовых процентах соответственно. Величины
и
могут превышать единицу, а аА – быть больше концентрации.
Отрицательные отклонения от закона Рауля обусловлены взаимодействием между частицами в растворе (взаимным притяжением с выделением тепла), причем энергия смешения отрицательна. Возможны и положительные отклонения от закона Рауля (в случае взаимного отталкивания частиц, когда
).
Особенно значительное отклонение от закона Рауля имеют месс то, когда в растворе образуются прочные химические соединения.
|
Лекция №3. Устройство и конструкции доменной печи. Устройство и конструкции доменной печи. Футеровка печи. Шахта и горн доменной печи. Фундамент и лещадь печи. Заплечики и распар. Летка, шлаковый и фурменный прибор. Колошниковое устройство. Конструкция засыпного агрегата. Особенности расчета конструктивных параметров, ТЭП печи.
Доменный цех включает несколько доменных печей с относящимся к каждой из них и расположенным вблизи них комплексом объектов (литейный двор, воздухонагреватели с газовоздухопроводами, система подачи шихты к колошниковому загрузочному устройству, система газоочистки, иногда установки припечной грануляции и некоторые другие); бункерную эстакаду (иногда отдельные эстакады для каждой печи); систему транспортных путей, газопроводов и ряд общих для цеха или нескольких печей отделений - отделение разливки чугуна, склад холодного чугуна, воздуходувная станция доменного дутья, отделение приготовления огнеупорных масс и ремонта чугуновозов и тепловозов; вспомогательные отделения - ремонтные мастерские, электроподстанция и др.
Для доменных печей характерны большой объем и сложная система грузопотоков. Основными линиями грузопотоков являются: грузопотоки шихтовых материалов к бункерной эстакаде с агломерационных фабрик, фабрик окомкования, коксохимического производства и ряда других источников снабжения за пределами завода; грузопотоки материалов от бункерной эстакады к колошниковому загрузочному устройству; грузопотоки уборки продуктов плавки - чугуна, шлака, колошниковой пыли; уборки коксовой мелочи; грузопотоки материалов, используемых при ремонтах объектов цеха; трубопроводная подача к печам кислорода и природного газа и отвод колошникового газа. Устройство доменного цеха, характер размещения в нем основных объектов во многом определяются выбранной системой грузопотоков и транспорта, и изменение этих систем существенно сказывается на планировании цеха.
Устройство и конструкция доменной печи. Доменная печь — печь шахтного типа (рис. 1). Сверху в печь порциями непрерывно загружают шихтовые материалы агломерат (окатыши) и кокс, которые медленно опускаются вниз; длительность их пребывания в печи составляет 4-6ч. В нижнюю часть печи (верх горна) через фурмы подают дутье нагретый воздух; у фурм за счет кислорода дутья сгорает кокс с выделением тепла, а горячие продукты сгорания движутся через столб шихты вверх, нагревая ее; время пребывания газов в печи составляет 3-12с. При опускании нагревающейся шихты в ней из оксидов восстанавливается железо, которое науглероживается, расплавляется и каплями стекает в горн, формируя чугун, а невосстановившиеся оксиды в нижней части печи (низ шахты, распар) расплавляются, образуя шлак, который также стекает в горн. Накапливающиеся в горне чугун и шлак, имеющие температуру 1450-1500°С, периодически выпускают через чугунные и шлаковые летки.
|
Общий вид доменной печи, оборудованной двухконусным засыпным аппаратом, показан на рис.3.1. Печь опирается на фундамент 1, большая часть которого заглублена в землю. Снаружи печь заключена в сплошной стальной кожух 9. Внутри кожуха находится футеровка 8, охлаждаемая холодильниками, которые крепятся к внутренней поверхности кожуха. В нижней части печи (горне) расположены летки 3 для выпуска чугуна и летки 21 для выпуска шлака. Вокруг печи проложен кольцевой футерованный воздухопровод 6, в который из воздухонагревателей подается горячее дутье (воздух); кольцевой воздухопровод служит для подвода дутья к многочисленным расположенным по окружности печи фурменным устройствам 5, через которые дутье поступает в верхнюю часть горна. Выше колошника печи 10 расположено колошниковое устройство. Оно включает газоотводы 15, 19, служащие для отвода из печи доменного газа; засыпной (загрузочный) аппарат и ряд других механизмов, связанных с загрузкой шихты и отводом газа. Показаны элементы засыпного аппарата: большой конус 11, закрывающий воронку (чашу) 20; малый конус 12, закраивающий воронку 17, и механизм 13, обеспечивающий их вращение; приемная воронка 14, в которую шихтовые материалы высыпают из скипа 16 путем его опрокидывания, причем скип доставляют на колошник по рельсам наклонного моста 18.
Тяжесть кожуха и футеровки верхней части печи передается на фундамент через мораторное кольцо 7 кожуха и колонны 2. Выпускаемый из печи через летки 3 жидкий чугун поступает в располагаемые на рабочей площадке 22 чугунные желоба 4 и по ним в чугуновозные ковши выпускаемый через летки 21 шлак по расположенным на площадке 22 шлаковым желобам стекает в шлаковозные ковши либо на установки припечной грануляции жидкого шлака.
Профиль печи. Профилем доменной печи называют очертание рабочего пространства, ограниченного футеровкой. В горизонтальных (поперечных) сечениях профиль представляет собой окружности переменного диаметра. Профиль печи в вертикальном осевом сечении представлен на рис. 3.2; основные элементы профиля — это горн, заплечики, распар, шахта и колошник, составляющие полезный объем печи, т.е. объем от оси чугунной летки О.Ч.Л. — до низа подвижных элементов засыпного аппарата в опущенном положении (в полезный объем не входят объем 1 нижней части горна от оси чугунной летки до кладки лещади, где находится несливаемый слой жидкого чугуна, и ограниченный куполом 3 печи объем 2, в котором расположены элементы засыпного аппарата).
|
Колошник имеет форму цилиндра и служит для приема загружаемой сверху шихты. Ниже колошника расположена расширяющаяся книзу шахта; это расширение необходимо, чтобы обеспечить свободное опускание шихтовых материалов, объем которых увеличивается в результате нагрева. Распар, представляющий собой короткий цилиндр, служит для создания плавного перехода от расширяющейся шахты к сужающимся заплечикам. Заплечики выполнёны в виде усеченного конуса; такая их форма необходима, поскольку здесь происходит плавление рудной части шихты, в результате чего объем шихты уменьшается, и суживающиеся заплечики не позволяют шихте слишком быстро опускаться в горн. Последний имеет цилиндрическую форму, в нижней его части скапливаются жидкие чугун и шлак, а в верхнюю подают дутье и здесь сгорает топливо (кокс).
Основным размером доменной печи является полезный объем. В нашей стране доменные печи строятся по типовым проектам, в соответствии с которыми предусмотрены следующие величины полезного объема, м3: 1033, 1386, 1513, 1719, 2002, 2300, 2700, 3000, 3200, 4500, 5000 и 5500.
Основные размеры профиля печи — это полезная высота, высота и диаметр отдельных элементов профиля, полная высота печи. Полезной высотой Н (рис.3.2) называют расстояние от оси чугунной летки до низа большого конуса 5 или низа вращающегося распределителя шихты (лотка) в опущенном положении. Полная высота печи Н (рис.3.2) — расстояние от оси чугунной летки до верхней кромки колошникового фланца 4, который служит опорой засыпного аппарата. Оптимальные соотношения между размерами выработаны на основании многолетнего опыта эксплуатации печей.
Фундамент является основанием печи и служит для передачи нагрузки, создаваемой массой печи на грунт. Площадь фундамента рассчитывают с учетом массы печи и того, что давление на грунт не должно превышать 2,5 кг/см2.
Фундамент состоит из двух частей (рис. 3.3): нижней, подземной, называемой подошвой 1, и верхней, называемой пнем 2. Подошву выполняют из бетона, а пень из жароупорного бетона с огнеупорностью 1400—1500 °С. Жаропрочность придается бетону применением огнеупорного наполнителя — боя шамота. В качестве связки применяют портландцемент с тонкомолотыми добавками шамота или огнеупорной глины.
Подошву делают в виде восьмиугольной плиты толщиной 4-6 м, толщина пня составляет 2-3,5 м. От перегрева и термического разрушения фундамент на современных печах предохраняют путем воздушного охлаждения низа лещади (стыка лещади с пнем). На подошву фундамента у большинства печей опираются стальные колонны, передающие нагрузку верхнего строения печи.
Кожух доменной печи представляет собой сварную конструкцию, состоящую из цилиндрических и конических поясов, изготовленных из стального листа. Толщина кожуха в верхней части составляет 20-40, в нижней 40-60 мм. Делают кожух из сталей с высокой ударной вязкостью, прочностью, пластичностью, термостойкостью. Большая часть печей имеет кожух с моратором или мораторным кольцом, т.е. горизонтально расположенным кольцом из стального листа, сваренным с кожухом нижней части шахты и верха заплечиков. Через моратор и колонны нагрузка верхней части печи передается на фундамент; кроме того, моратор служит опорой для кладки шахты и распара.
Холодильники служат для охлаждения футеровки и кожуха печи с помощью, пропускаемой через них холодной технической воды, а при испарительном охлаждении — с помощью кипящей химически очищенной воды. Широко применяются плитовые холодильники, располагаемые вертикально между кожухом и футеровкой. Холодильник — это плита из чугуна с залитой в ней стальной трубкой в виде змеевика для циркулирующей воды. Холодильник крепят к кожуху печи с помощью болтов.
Горн состоит из металлоприемника, где накапливается чугун и шлак, и фурменной зоны, где сгорает кокс. Кладка металлоприемника имеет толщину до 1,5 м и охлаждается, так же как и боковая поверхность лещади плитовыми чугунными холодильниками. Снаружи горн заключен в броню из стальных листов толщиной 30—36 мм. Стены горна выкладывают из высококачественного шамотного кирпича, применяют также графитовые блоки.
Чугунная летка служит для выпуска чугуна. Она расположена на 500 мм выше лещади, ниже ее находится «мертвый» слой жидкого чугуна, предохраняющий лещадь от разрушения каплями и струями чугуна для упрочнения кладки у летки ставят холодильники, укрепленные специальной рамой.
Шлаковые летки расположены на высоте 1,4 - 1,9 м от лещади. Каждая из леток имеет медную коническую водоохлаждаемую фурму с отверстием диаметром 60 - 80 мм. В промежутках между выпусками шлака летки закрывают стопорами — железными пробками. Заплечики, выложенные в один кирпич, снаружи охлаждаются плитовыми холодильниками с залитыми внутри трубками и заключаются в броню. Благодаря интенсивному охлаждению тонкостенных заплечиков на их рабочей поверхности образуется гарниссаж, защищающий кладку от действия жидких продуктов плавки.
Шахта выложена из шамотного кирпича и заключена в металлический кожух, который служит опорой для колошниковых устройств. На высоты от низа шахта охлаждается коробчатыми холодильниками. Давление кладки кожуха и надколошниковых устройств воспринимается опорным кольцом (мораторное кольцо), лежащим на колоннах.
Колошниковые устройства (рис. 3.4) служат для загрузки шихты и отвода газов. Засыпной аппарат имеет малый конус, укрепленный на полой штанге и плотно прижатый к приемной воронке. Большой конус укреплен также на штанге, проходящей внутри штанги малого конуса. Чаша большого конуса крепится на фланце опорного колошникового кольца. Приемная воронка состоит из неподвижной и вращающейся частей. Последняя поворачивается вместе с малым конусом на заданный угол после загрузки очередной шихты, после чего малый конус опускается, и шихта падает на большой конус. Большой конус опускается, когда на нем сосредоточится вся шихта подачи (обычно подача состоит из шести скипов). Периодические повороты приемной воронки и малого конуса на 60, 120, 180, 240 и 300° обеспечивают более равномерное распределение шихтовых материалов по окружности печи.
Лекция №4. Огнеупоры. Основы процесса производства огнеупорных материалов. Назначение. Условия работы огнеупорных изделий в металлургических агрегатах. Основы теории Байкова А.А.: формовка, сушка, обжиг огнеупоров; дисперсность и её значение, перекристаллизация. Требования, предъявляемые к металлургическим огнеупорам: рабочие и физические свойства; классификация и применение, свойства огнеупоров.
Огнеупорные материалы применяют почти во всех отраслях промышленности. Применяют их и в областях новой техники, в атомной промышленности и ракетостроении. Развитие новых способов получения электрической энергии в магнитных гидродинамических генераторах и топливных элементах в значительной мере определяется свойствами огнеупоров. Основное количество огнеупоров потребляется черной металлургией, поэтому народнохозяйственный расход огнеупоров условно относят на тонну стали.
История техники характеризуется непрерывным повышением температур технологических процессов. Уровень температур определяется источником энергии. Когда источником энергии служили дрова, температура была около 1000°С; с применением каменного угля температура поднялась до 1500°С; нефть и природный газ обеспечивают получение температур до 2000°С; электрическая энергия вольтовой дуги до 3000°С и, наконец, в современных промышленных плазменных металлургических печах температур а плазмы составляет 25000°С. И поскольку огнеупоры играют служебную, вспомогательную роль при производстве стали, цемента и т. п., то чем меньше их расход, тем производство основной продукции более эффективно.
Огнеупоры должны не только выдерживать высокие температуры не расплавляясь, но и обладать комплексом других свойств и прежде всего экономить тепло, т. е. быть хорошими теплоизоляторами (а в некоторых случаях, наоборот, проводниками тепла), не разрушаться под действием химического и механического воздействий.
Многообразие условий службы вызывает необходимость производства большого и все увеличивающегося ассортимента огнеупоров с различными свойствами. Большинство огнеупорных изделий выпускают в виде простых изделий типа прямоугольного параллелепипеда массой в несколько килограммов — это универсальная форма для выполнения кладки различной конфигурации. Однако такая кладка — ручная и тяжелая работа, требующая длительного времени. В настоящее время ставится задача заменить там, где это эффективно, кладку из мелкоштучных изделий вручную монтажом футеровки из крупных огнеупорных бетонных блоков и монолитных бетонных набивных или формуемых огнеупорных масс. Это позволит индустриализировать сооружение печей и сократить сроки кладки печных агрегатов. В огнеупорной промышленности происходит уменьшение выпуска огнеупоров в виде простых изделий и соответствующее увеличение производства огнеупорных бетонов и масс.
Научной основой производства огнеупоров является физическая химия тугоплавких оксидов и силикатов. Технология огнеупоров описывается реологическими закономерностями. Реология — наука о деформации и текучести вещества.
Огнеупорами называют материалы, изготовляемые на основе минерального сырья и отличающиеся способностью противостоять, не расплавляясь и не разрушаясь, действию высоких температур, а также другим физико-химическим воздействиям в процессе службы при высоких температурах.
Все огнеупорные материалы согласно классифицируются по различным признакам. В зависимости от степени огнеупорности материалы подразделяются на следующие виды:
1) огнеупорные, обладающие огнеупорностью от 1580 до 1770°С;
2) высокоогнеупорные, с огнеупорностью от 1770 до 2000°С;
3) высшей огнеупорности, с огнеупорностью выше 2000°С.
В зависимости от химико-минералогического состава и технологии производства огнеупорные изделия подразделяют на группы. Отдельные группы по их химической природе объединены общим наименованием.
По химическому характеру огнеупоры делятся на следующие группы:
1) кремнеземистые — динасовые на известковой связке, содержащие 93% SiО2; 2) алюмосиликатные (низко-, средне- и высокоглиноземистые); 3) магнезиальные; 4) магнезиальноизвестковые; 5) магнезиальношпинелидные; 6) магнезиальносиликатные; 7) углеродистые; 8) карбидокремниевые; 9) цирконистые; 10) окисные; 11) некислородные.
Огнеупорные материалы бывают штучными изделиями (блоками) и неформованными. К последним относят наварочные материалы, мертели, засыпки и другие специальные набивные и формуемые массы, в том числе применяемые для производства огнеупорных бетонов и торкретирования.
По форме и размерам различают следующие изделия:
а) прямые и клиновые нормальных размеров, малого и большого форматов;
б) фасонные простые, сложные, особо сложные, крупноблочные, массой свыше 60 кг (простые, сложные и особо сложные);
в) специальные — промышленного и лабораторного назначения (тигли, трубки и т. п.).
Прямые и клиновые изделия нормальных размеров иногда называют кирпичами. Так, различают кирпичи: малого формата — прямые размером 230× (113; 115) × (65; 75) мм, клиновые 230× (113; 115) × (65×55; 65×45; 75×65; 75×55) мм и большого формата — прямые размером 250× (123; 125) × (65; 75) мм, клиновые 250 × (123; 125) × (65×55 65×45; 75×65; 75×55)мм.
Наименование простых по форме огнеупорных изделий кирпичами неправильно, так как сходство их со строительным кирпичом только внешнее, и в отличие от последних такие огнеупоры следует называть изделиями.
В зависимости от пористости %, изделия могут быть:
Особо плотные с открытой пористостью | > 3 |
Высокоплотные | 3—10 |
Плотные | 10—16 |
Уплотненные | 16—20 |
Среднепористые | 20—30 |
Повышеннопористые | > 30 |
Легковесные с общей пористостью | 45—85 |
Ультралегковесные с общей пористостью | > 85 |
Большая часть используемых в промышленности огнеупорных материалов представлена обжиговыми штучными изделиями. Огнеупорные изделия различают также по назначению, например шамотные изделия для кладки доменной печи, сифонной разливки стали и т. п.
Прессование и формование огнеупорных изделий. Целью прессования и формования является придание огнеупорной массе заданных форм и размеров. В результате обработки получают полупродукт – сырец. В технологии огнеупоров различают четыре основных способа прессования и формования изделий.
1. из малопластичных или совсем непластичных масс с влажностью 3-8%; его называют также полусухим способом прессования;
2. из пластичных масс с влажностью 16-20%;
3. литьё из масс с влажностью 35-45% (шликерный способ);
4. литьё из расплавов.
Основными являются полусухой и пластичный. Полусухой способ имеет общее значение, им можно прессовать изделия из всех масс независимо от их химического и фазового состава. Пластичное формование имеет ограниченное применение для изготовления некоторых видов шамотных огнеупоров.
Литьём из шликерных масс можно получать наиболее плотные изделия, так как в этом случае применяют весьма тонко измельчённые порошки, обуславливающие наиболее полное спекание. Недостаток этого способа заключается в большой усадке изделий при обжиге, что существенно ограничивает применение этого метода. Литьём из расплавленных масс пользуются при производстве плавленых муллитовых, циркономуллитовых и некоторых других изделий. После придания формы изделия подвергают сушке и обжигу.
Сушка представляет собой процесс удаления влаги из твёрдых пористых материалов путем испарения при температуре обычно ниже точки кипения. В процессе сушки влажность снижается, а механическая прочность повышается до 200-500 кПа, что обеспечивает сохранность сырца при дальнейшем его транспортировании в печи для обжига.
Огнеупорные изделия при сушке претерпевают усадку, то есть уменьшаются в объеме. Величина усадки зависит от природы материала, способа изготовления, влажности и типа изделий, а также скорости сушки. Чем больше влажность изделий, тем больше их усадка и чем больше скорость сушки, тем меньше усадка.
Обжиг – завершающая стадия производства обожженных огнеупорных изделий. При обжиге некоторых изделий уменьшается пористость и увеличивается прочность, при обжиге других повышается только прочность, а пористость даже увеличивается.
Полнота протекания процессов зависит от температуры обжига, продолжительности, скорости подъема температур и охлаждения, газовой среды, состояния и свойств обжигаемого материала, условий обжига и т.п.
Фактическая продолжительность обжига значительно больше минимального времени, необходимого для получения нормально спеченных изделий без дефектов. Это объясняется главным образом необходимостью выравнивания температур в объеме садки. Обжиг происходит при температурах 1300-1850°С.
Лекция №5. Энергетика сталеплавильных агрегатов (конвертеры). Тепло процесса. Возможность протекания процесса. Потери тепла, использование тепла. Приход и расход тепла. Внутренние источники тепла. Особенности расчетов материального и теплового баланса
- для лома прямоугольного сечения и близкого к нему
F = 0,256·[(1/δ) + (1/в)] + 2·δ·в; (5.5)
- для лома круглого сечения и близкого к нему:
F = (0,51/α) + (πd2/2), (5.6)
где δ – толщина лома, мм; в – ширина лома, мм; α – диаметр куска лома круглого сечения.
Быстрое расплавление легковеса приводит к резкому увеличению охлаждающего эффекта металлозавалки в начальный период продувки.
Легковесный лом содержит много ржавчины и загрязнений, что обуславливает холодный ход плавки и, на первый взгляд, представляется энергетически выгодным: меньше перепад температур и, следовательно, меньше теплопотери в ходе продувки, больше углерода окисляется до СО2. Однако технологические недостатки (переокисление шлаковой фазы с дальнейшими выбросами металла и шлака, вспенивание и переливы шлакометаллической эмульсии, удлинение продувки) усиливаются высокоскоростным процессом расплавления лома в области зоны взаимодействия кислородной струи с металлом.
В связи с этим металлолом толщиной менее 10 мм необходимо пакетировать и использовать в виде тяжеловесных пакетов сечением ~700х1000 мм, длиной ≤1000 мм и плотностью 3,0…3,5 т/м3 и тяжеловесный кусковый лом толщиной от 10 до 300…400 мм и длиной 500 мм.
Тепловые потери конвертеров. Тепловые потери в конвертерах изменяются в широких пределах в зависимости от темпа производства и вместимости агрегатов (1,5…12% суммарного прихода тепла и более).
Теплопотери в конвертерах, по-видимому удобно классифицировать в соответствии с периодом продувки (временем выделения тепла): излучением через корпус конвертера; связанные с аккумуляцией тепла футеровкой; с охлаждающей фурму водой.
При такой классификации теплопотери поддаются учету в производственных условиях, что имеет немаловажное значение для решения ряда технологических и экономических задач. В частности, при оценке затрат тепла на нагрев футеровки в период продувки намного повышается эффективность предварительных расчетов шихты на плавку.
Тепловые потери излучением через футеровку сравнительно невелики и составляют 0,4…0,7% от суммарного прихода тепла за плавку, возрастая по ходу компании конвертера.
Повышение расхода металлолома при сокращении потерь тепла через корпус невелико, особенно для современных большегрузных агрегатов (2,0…2,5 кг/т стали), однако пренебрегать им не следует.
Таким образом, пути уменьшения теплопотерь через корпус конвертера заключаются в увеличении вместимости агрегата, интенсивности продувки, толщины кладки, установки тепловых экранов и теплоизоляции футеровки.
Потери тепла излучением через горловину конвертера анализируются для конкретной проработки путей снижения и оценки их значимости. Принципиально их можно оценить по методике расчета излучения через отверстия в стенах, когда имеет место излучение прямое и отраженное от боковых стен рабочего пространства агрегата:
Q = φ C0 (Тп / 100)4 · Fотв · τ, (5.7)
где C0 – коэффициент излучения абсолютно черного тела, Вт/(м2·К4); Тп – температура в рабочем пространстве, К; Fотв – удельная площадь отверстия, м2/т; φ – коэффициент диафрагмирования отверстия (близок к единицы); τ – продолжительность излучения, с.
Потери тепла излучением через горловину конвертера при общей длительности цикла – 35 минут составляют 1,1…1,4% суммарного прихода тепла и снижаются с увеличением вместимости конвертера.
Повышение расхода лома при уменьшении этих потерь в 2 раза для современных конвертеров может составить 6…7 кг/т стали. Снижение потерь обеспечивается в значительной мере уменьшением диаметра горловины конвертера. При этом одновременно ослабляет эжекцию воздуха в рабочее пространство агрегатов, повышает качество стали (способствует получению стали с меньшим содержанием [N]), но осложняет обслуживание конвертера, завалку металлолома и снижает стойкость футеровки его верхней части. Учет противоположно действующих факторов привел проектировщиков к сравнительно строгому выдерживанию соотношения dг = 0,33·G0,4 (где G – вместимость агрегата, т; dг – диаметр горловины, м).
Потери тепла в межпродувочные периоды приблизительно могут быть приняты равными количеству тепла, поглощаемого футеровкой от металлической ванны в период продувки. Они складываются из теплопотерь излучением через горловину и при свободной конвекции воздуха в рабочем пространстве агрегатов, определяются из соотношения
Qк = αк·ΔT·F·τ, (5.8)
где Qк – тепловые потери конвекцией, кДж/т; αк – коэффициент теплопередачи конвекцией, Вт/м2; ΔT – разность температур поверхности футеровки и поступающего в рабочее пространство воздуха, К; F – удельная площадь поверхности футеровки, м2/т; τ – продолжительность контакта футеровки с воздухом, с.
Величина теплопотерь конвекций близка к величине теплопотерь излучением через горловину конвертера (~1,1…1,4% общего прихода тепла).
Из изложенного ясна важность сокращения потерь тепла в межпродувочном периоде. Пути их уменьшения в сокращении продолжительности загрузочно-вспомогательных операций, организация работы конвертеров без простоев (из-за отсутствия материалов), использование торкретирования.
Тепловые потери с охлаждающей фурму водой могут быть определены по формуле, кДж/т:
Q = Cp·ΔT·gв·τпрод, (5.9)
где Cp – теплоемкость воды, кДж/(кг·К); ΔT – температурный перепад на выходе и входе в фурменное устройство, К; gв – удельный расход воды, кг/(c·т).
Материальный и тепловой балансы. Уровень и структура материальных и энергетических затрат характеризуют состояние технологии и техники процесса, их анализ позволяет вскрыть резервы, определить возможные пути их реализации ориентируясь на то, что материальный и тепловой балансы конвертерных процессов (верхнего, донного и комбинированного дутья) взаимно обусловлены.
При продувке сверху обычного передельного чугуна кислородом выделяется такое количество тепла, которое может обеспечить нагрев ванны к концу процесса без применения охладителей до 1850…1900оС.
Для получения нормальной температуры в конце продувки (1580…1650оС) расход главной из охлаждающих добавок – стального лома – должен составлять 24…28%, чугуна 72…76% от массы металлической шихты в зависимости от его состава и температуры. Превышение оптимального расхода охладителя обусловлено, как правило, увеличением доли тепла реакций окисления железа, в результате чего существенно снижается выход годного.
Применяют и дополнительные охлаждающие добавки (твердые окислители): железную руду, окалину, агломерат, окатыши, известняк, одна массовая единица которых в среднем заменяет три-четыре массовых единицы стального лома. В связи с этим при дополнительном охлаждении твердым окислителем (до 1%) расход лома составляет 20…25% (при расходе чугуна 75…80%).
Таблица 5.1.Материальный баланс плавки (до раскисления) на 100 кг металлошихты (предел чугуна состава, %: 4,2 [C]; 0,75 [Si]; 0,6 [Mn]; 0,15 [P]; 0,05 [S]на сталь при tчуг=1340оС)
|
|
Общие условия выбора системы дренажа: Система дренажа выбирается в зависимости от характера защищаемого...
Археология об основании Рима: Новые раскопки проясняют и такой острый дискуссионный вопрос, как дата самого возникновения Рима...
Папиллярные узоры пальцев рук - маркер спортивных способностей: дерматоглифические признаки формируются на 3-5 месяце беременности, не изменяются в течение жизни...
Кормораздатчик мобильный электрифицированный: схема и процесс работы устройства...
© cyberpedia.su 2017-2024 - Не является автором материалов. Исключительное право сохранено за автором текста.
Если вы не хотите, чтобы данный материал был у нас на сайте, перейдите по ссылке: Нарушение авторских прав. Мы поможем в написании вашей работы!