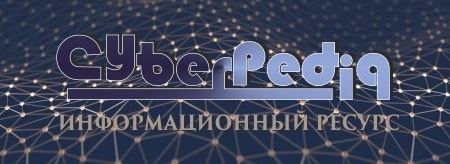
Кормораздатчик мобильный электрифицированный: схема и процесс работы устройства...
Автоматическое растормаживание колес: Тормозные устройства колес предназначены для уменьшения длины пробега и улучшения маневрирования ВС при...
Топ:
Выпускная квалификационная работа: Основная часть ВКР, как правило, состоит из двух-трех глав, каждая из которых, в свою очередь...
Методика измерений сопротивления растеканию тока анодного заземления: Анодный заземлитель (анод) – проводник, погруженный в электролитическую среду (грунт, раствор электролита) и подключенный к положительному...
Интересное:
Как мы говорим и как мы слушаем: общение можно сравнить с огромным зонтиком, под которым скрыто все...
Что нужно делать при лейкемии: Прежде всего, необходимо выяснить, не страдаете ли вы каким-либо душевным недугом...
Влияние предпринимательской среды на эффективное функционирование предприятия: Предпринимательская среда – это совокупность внешних и внутренних факторов, оказывающих влияние на функционирование фирмы...
Дисциплины:
![]() |
![]() |
5.00
из
|
Заказать работу |
Содержание книги
Поиск на нашем сайте
|
|
При обработке на станках гидроабразивной резки возникает проблема, связанная с неровностью обрабатываемого материала. Для решения данной задачи на станок может быть установлена лазерная или ультразвуковая система сканирования материала. Такая система выполняет сканирование материала до обработки с заданным интервалом, что позволяет поддерживать требуемый зазор во время обработки материала и обеспечивает максимальную точность обработки. При работе с маленькими деталями возможно сканирование только точек вреза.
Датчик контроля абразива
Датчик контроля подачи абразива выполняет проверку количества подаваемого абразивного материала во время обработки, что позволяет выполнять рез без постоянного присутствия оператора, что позволяет остановить обработку в случае попадания в режущую головку посторонних материалов, таких как остатки мешковины или посторонней фракции. Диапазон допустимых значений задается непосредственно со стойки оператора и может быть изменен даже в процессе обработки.
Устройство удаления абразива
На гидроабразивный станок может быть установлена система удаления отработанного абразива, состоящая из бак-отстойника и насоса. Отличительной особенностью данной системы является использование мембранного насоса, который максимально приспособлен для работы в агрессивных средах и прост в обслуживании. Для удобства работы бак для отработанного абразива имеет быстросъемные разъемы для подсоединения шлангов и приспособлен для транспортировки кран-балкой или погрузчиком.
Устройства загрузки металла
Гидрорезка (водоструйная резка) – вид резки, при котором материал обрабатывается тонкой сверхскоростной струей воды. При гидроабразивной резке для увеличения разрушительной силы водяной струи в нее добавляются частицы высокотвердого материала – абразива.
|
Общепринятые обозначения
ГАР – гидроабразивная резка
WJC – Water Jet Cutting – резка водяной (или водно-абразивной) струей
AWJC – Abrasive Water Jet Cutting – абразивная водоструйная резка
Сущность процесса
Если обычную воду сжать под давлением около 4000 атмосфер, а затем пропустить через отверстие диаметром меньше 1 мм, то она потечет со скоростью, превышающей скорость звука в 3–4 раза. Будучи направленной на обрабатываемое изделие, такая струя воды становится режущим инструментом. С добавлением частиц абразива ее режущая способность возрастает в сотни раз, и она способна разрезать почти любой материал.
Технология гидроабразивной резки основана на принципе эрозионного (истирающего) воздействия абразива и водяной струи. Их высокоскоростные твердофазные частицы выступают в качестве переносчиков энергии и, ударяясь о частицы изделия, отрывают и удаляют последние из полости реза. Скорость эрозии зависит от кинетической энергии воздействующих частиц, их массы, твердости, формы и угла удара, а также от механических свойств
обрабатываемого материала.
Технология резки
Вода, нагнетаемая насосом до сверхвысокого давления порядка 1000–6000 атмосфер, подается в режущую головку. Вырываясь через узкое сопло (дюзу) обычно диаметром 0,08–0,5 мм с околозуковой или сверхзвуковой скоростью (до 900–1200 м/c и выше), струя воды поступает в смесительную камеру, где начинает смешиваться с частицами абразива – гранатовым песком, зернами электрокорунда, карбида кремния или другого высокотвердого материала. Смешанная струя выходит из смесительной (смешивающей) трубки с внутренним диаметром 0,5–1,5 мм и разрезает материал. В некоторых моделях режущих головок абразив подается в смесительную трубку. Для гашения остаточной энергии струи используется слой воды толщиной, как правило, 70–100 сантиметров.
|
Рисунок. Схема гидроабразивной резки
Рисунок. Схема смешивания частицы абразива
При гидрорезке (без абразива) схема упрощена: вода под давлением вырывается через сопло и направляется на разрезаемое изделие.
Таблица. Характерная область применения технологий резки водой
Гидрорезка | Гидроабразивная резка |
Кожа, текстиль, войлок (обувная, кожаная, текстильная промышленность) | Листы из сталей, металлов |
Пластики, резиновые изделия (автомобильная промышленность) | Различные металлические детали (отливки, шестерни и др.) |
Электронные платы | Сплавы алюминия, титана и др., композитные материалы, толстостенные пластмассы (авиационная и космическая промышленность) |
Ламинированные материалы (авиационная и космическая промышленность) | Бетон, железобетон, гипсовые блоки, твердая брусчатка и др. строительные материалы |
Теплоизоляционные, уплотнительные и шумопонижающие материалы | Камень, гранит, мрамор и др. |
Продукты питания – замороженные продукты, плотные продукты, шоколад, выпечка и др. | Стекло, бронированное стекло, керамика |
Бумага, картон | Комбинированные материалы, материалы с покрытием |
Дерево | Дерево |
Термо- и дуропласт | Армированные пластики |
При гидроабразивной резке разрушительная способность струи создается в гораздо большей степени за счет абразива, а вода выполняет преимущественно транспортную функцию. Размер абразивных частиц подбирается равным 10–30% диаметра режущей струи для обеспечения ее эффективного воздействия и стабильного истечения. Обычно размер зерен составляет 0,15–0,25 мм (150–250 мкм), а в ряде случаев – порядка 0,075–0,1 мм (75–100 мкм), если необходимо получение поверхности реза с низкой шероховатостью. Считается, что оптимальный размер абразива должен быть меньше величины (dс.т. – dв.с.)/2, где dс.т. – внутренний диаметр смесительной трубки, dв.с. – внутренний диаметр водяного сопла.
В качестве абразива применяются различные материалы с твердостью по Моосу от 6,5. Их выбор зависит от вида и твердости обрабатываемого изделия, а также следует учитывать, что более твердый абразив быстрее изнашивает узлы режущей головки.
Таблица. Типичная область применения некоторых абразивных материалов при резке
|
Наименование | Характерная область применения |
Гранатовый песок (состоит из корунда Al2O3, кварцевого песка SiO2, оксида железа Fe2O3 и других компонентов) | Широко распространен для резки различных материалов, в особенности высоколегированных сталей и титановых сплавов |
Зерна электрокорунда (состоит преимущественно из корунда Al2O3, а также примесей) или его разновидности | Искусственные материалы с очень высокой твердостью по Моосу. Используются для резки сталей, алюминия, титана, железобетона, гранита и др. материалов |
Зерна карбида кремния (SiC) – зеленого или черного | |
Кварцевый песок (SiO2) | Резка стекла |
Частицы силикатного шлака | Резка пластика, армированного стекло- либо углеродными волокнами |
Сопла обычно изготавливают из сапфира, рубина или алмаза. Срок службы сапфировых и рубиновых сопел составляет до 100–200 часов, алмазных сопел – до 1000–2000 часов. При гидрорезке не применяются рубиновые сопла, а сапфировые обычно служат в 2 раза дольше.
Смесительные трубки изготавливают из сверхпрочных сплавов. Срок службы – как правило, до 150–200 часов.
Технологические параметры
Основными технологическими параметрами процесса гидроабразивной резки являются:
Скорость резки (скорость перемещения режущей головки вдоль поверхности обрабатываемого изделия) существенно влияет на качество реза. При высокой скорости происходит отклонение (занос) водно-абразивной струи от прямолинейности, а также заметно проявляется ослабевание струи по мере разрезания материала. Как следствие, увеличиваются конусность реза и его шероховатость.
Рисунок. Типичная форма реза в зависимости от условий резки
Рисунок. Занос струи при резке со скоростью выше оптимальной
Разделительная резка может выполняться на скорости, составляющей 80–100% от максимальной. Качественной резке обычно соответствует скоростной диапазон в 33–65%, тонкой резке
|
– в 25–33%, прецизионной резке – в 10–12,5% от максимальной скорости.
Фото. Вид поверхности реза в зависимости от скорости водно-абразивной резки
В некоторых моделях режущих головок используется технология автоматической компенсации конусности, например, Dynamic Waterjet компании Flow. Компенсация конусности достигается в результате программно управляемого динамического наклона режущей головки на определенный градус. Это позволяет повысить скорость резки при сохранении качества реза и, соответственно, сократить производственные расходы.
С уменьшением внутреннего диаметра смесительной трубки (при прочих равных условиях) возрастают производительность и точность резки, уменьшается ширина реза (она примерно на 10% больше внутреннего диаметра трубки). При этом снижается и срок службы трубки. В процессе эксплуатации смесительной трубки ее внутренний диаметр увеличивается примерно на 0,01–0,02 мм за каждые восемь часов работы
Таблица. Примерные размеры абразива при различных режимах резки
Применение | Размер частиц гранатового песка (Garnet) | Внутр. Диаметр водяного сопла | Внутр. Диаметр смесительной трубки | |||
mesh (США) | микрон | дюймов | мм | дюймов | мм | |
Стандартная промышленная конфигурация | 178 (300–150) | 0,013–0,014» | 0,330–0,356 | 0,04» | 1,02 | |
Высокоскоростная резка | 249 (400–200) | 0,014–0,018» | 0,356–0,457 | 0,05» | 1,27 | |
297 (600–200) | ||||||
Точная резка | 125 (200–100) | 0,012–0,013» | 0,305–0,330 | 0,036» | 0,91 | |
178 (300–150) | ||||||
Высокоточная резка | 125 (200–100) | 0,010–0,011» | 0,254–0,279 | 0,03» | 0,76 |
Расход абразива зависит от диаметров смесительной трубки и водяного сопла, условий резки и т. Д. Ориентировочные оптимальные значения приведены в таблице ниже.
Таблица. Оптимальный расход абразивного материала при
некоторых соотношениях диаметров смесительной трубки и сопла
Внутренний диаметр водяного сопла (мм) | Внутренний диаметр смесительной трубки (мм) | Расход абразива (г/мин) |
0,25 | 0,76 | 270–360 |
0,36 | 1,02 | 500–640 |
0,46 | 1,27 | 800–1100 |
Максимальное рабочее давление обычно составляет 3000–3200, 3800, 4150 или 6000 бар. Чем выше давление, тем выше скорость и эффективность резки. В то же время требуется более частая замена прокладок в насосе.
Таблица. Зависимость скорости прямолинейной разделительной (черновой) резки от толщины материала при давлении насоса P = 4100 бар (примерно 4046 атм)
Вид материала | Скорость резки (м/ч)* при толщине | ||||
5 мм | 10 мм | 20 мм | 50 мм | 100 мм | |
Нержавеющая сталь | 52,62 | 28,56 | 13,02 | 3,84 | 1,44 |
Титан | 68,46 | 37,20 | 16,98 | 4,98 | 1,86 |
Алюминий | 142,20 | 77,40 | 35,40 | 10,20 | 3,72 |
Гранит | 251,40 | 137,10 | 62,76 | 18,00 | 6,60 |
Мрамор | 295,20 | 160,80 | 73,50 | 21,24 | 7,80 |
Углепластик | 247,20 | 134,70 | 61,74 | 17,70 | 6,60 |
Стекло | 272,76 | 148,62 | 67,92 | 19,62 | 7,26 |
*: давление – 4100 бар; марка абразива – Kerfjet #80; расход абразива – 250–450 г/мин; внутренний диаметр сопла – 0,25 мм, 0,35 мм; внутренний диаметр смесительной трубки – 0,76 мм, 1,01 мм / данные ООО «ТехноАльянсГрупп», г. Москва, установки ГАР BarsJet |
|
Таблица. Зависимость скорости прямолинейной разделительной (черновой) резки от толщины материала при давлении насоса P = 6000 бар (около 5922 атм)
Вид материала | Скорость резки (м/ч)* при толщине | ||||
5 мм | 10 мм | 20 мм | 50 мм | 100 мм | |
Нержавеющая сталь | 86,64 | 47,16 | 21,48 | 6,12 | 2,40 |
Титан | 112,38 | 61,50 | 28,08 | 8,22 | 3,06 |
Алюминий | 233,76 | 127,44 | 58,44 | 16,92 | 6,24 |
Гранит | 413,46 | 225,42 | 103,08 | 29,70 | 10,92 |
Мрамор | 485,28 | 264,60 | 121,02 | 34,80 | 12,84 |
Углепластик | 406,56 | 221,88 | 101,40 | 29,22 | 10,86 |
Стекло | 448,14 | 244,38 | 111,72 | 32,16 | 11,88 |
*: давление – 6000 бар; марка абразива – Kerfjet #80; расход абразива – 250–450 г/мин; внутренний диаметр сопла – 0,25 мм; внутренний диаметр смесительной трубки – 0,76 мм, 1,01 мм / данные ООО
«![]() |
Фото. Детали, полученные гидроабразивной резкой: из нержавеющей стали толщиной 15 мм; из сплава алюминия толщиной 6 мм; из алюминия толщиной 30 мм; из пластика, армированного волокном, толщиной 20 мм; из инструментальной стали толщиной 60 мм
|
|
Автоматическое растормаживание колес: Тормозные устройства колес предназначены для уменьшения длины пробега и улучшения маневрирования ВС при...
История создания датчика движения: Первый прибор для обнаружения движения был изобретен немецким физиком Генрихом Герцем...
Состав сооружений: решетки и песколовки: Решетки – это первое устройство в схеме очистных сооружений. Они представляют...
Семя – орган полового размножения и расселения растений: наружи у семян имеется плотный покров – кожура...
© cyberpedia.su 2017-2024 - Не является автором материалов. Исключительное право сохранено за автором текста.
Если вы не хотите, чтобы данный материал был у нас на сайте, перейдите по ссылке: Нарушение авторских прав. Мы поможем в написании вашей работы!