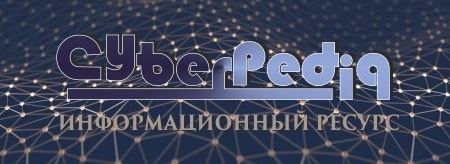
Биохимия спиртового брожения: Основу технологии получения пива составляет спиртовое брожение, - при котором сахар превращается...
Архитектура электронного правительства: Единая архитектура – это методологический подход при создании системы управления государства, который строится...
Топ:
Комплексной системы оценки состояния охраны труда на производственном объекте (КСОТ-П): Цели и задачи Комплексной системы оценки состояния охраны труда и определению факторов рисков по охране труда...
Генеалогическое древо Султанов Османской империи: Османские правители, вначале, будучи еще бейлербеями Анатолии, женились на дочерях византийских императоров...
Эволюция кровеносной системы позвоночных животных: Биологическая эволюция – необратимый процесс исторического развития живой природы...
Интересное:
Искусственное повышение поверхности территории: Варианты искусственного повышения поверхности территории необходимо выбирать на основе анализа следующих характеристик защищаемой территории...
Влияние предпринимательской среды на эффективное функционирование предприятия: Предпринимательская среда – это совокупность внешних и внутренних факторов, оказывающих влияние на функционирование фирмы...
Как мы говорим и как мы слушаем: общение можно сравнить с огромным зонтиком, под которым скрыто все...
Дисциплины:
![]() |
![]() |
5.00
из
|
Заказать работу |
Содержание книги
Поиск на нашем сайте
|
|
Для расчета обычно задают: рабочий объем, диаметр D, высоту Н аппарата и его рабочие параметры (р- рабочее давление, t- температура, c- концентрация распределяемой среды); фазовое состояние перемешиваемой среды и ее физико-механические свойства (r - плотность,m С- динамическая вязкость), а также ее состав по жидкой или твердой фазе.
Расчет выполняют в следующем порядке.
1. В зависимости от назначения процесса перемешивания, вязкости среды (m) и ее фазового состояния выбирают тип перемешивающего устройства и его окружную скорость w (м/с).
2. Зная диаметр аппарата D, определяют диаметр мешалки d
м (таблица1).
3. По типу и диаметру d
м перемешивающего устройства определяют частоту вращения n(об/с) по таблицам.
4. Определяют мощность (Вт), необходимую для перемешивания
, (1.8)
Где Kn- критерий мощности, определяемый по графикам в зависимости от величины центробежного критерия Рейнольдса Re; r - плотность перемешиваемой среды, ; n – частота вращения мешалки, об/с; dм - диаметр мешалки, м.
, (1.9)
где m c - динамическая вязкость, Па? с.
5.Рассчитывают номинальную мощность (Вт) на валу электродвигателя:
, (1.10)
где Nт -мощность, затрачиваемая на трение в уплотнении, часто ею пренебрегают из-за малого значения; h п- КПД привода, определяемый в зависимости от конструкций последнего (для нормализованных приводов h =0,9-0,96)
6.По значению мощности N и угловой скорости w с учетом конструкции аппарата выбирают тип и размеры нормализованного привода.
7.Рассчитывают диаметр вала (м) перемешивающего устройства, что ориентировочно можно выполнить по формуле:
, (1.11)
где Мкр- расчетный крутящий момент, Нм; t доп - допустимое напряжение на кручение для выбранного материала вала; Па.
|
, (1.12)
где w - угловая скорость, с-1.
При числах оборотов более 5 с-1 вал проверяют на жесткость и виброустойчивость.
8.Проверяют мешалку на прочность в опасном сечении из условия работы ее на изгиб. Например, для лопастной мешалки используют формулу:
, (1.13)
где М=0,0813 - изгибающий момент, действующий на лопасть в месте присоединения к ступице, Н·м;
- расчетный момент сопротивления соответствующего сечения лопасти при изгибе ее в направлении сечения,м3.
Лопастные мешалки. Площадь лобовой поверхности лопатки, вытесняющей жидкости, в общем случае определяется выражением:
, (1.14)
где b – длина (вылет) лопасти, м; h – высота лопасти, м; b - угол наклона лопасти к направлению движения.
![]() | ![]() |
Рисунок 11 - Схема горизонтальной лопастной мешалки | Рисунок 12 - Схема вертикальной лопастной мешалки |
Окружная скорость в м/с центра тяжести лопасти:
, (1.15)
Где r0 - расстояние от центра тяжести лопасти до оси вращения, м; n – частота вращения мешалки, об/мин.
Масса жидкости, вытесняемая лопастью:
, (1.16)
где r - плотность жидкости, .
Неподвижная лопасть приводится во вращение с заданной частотой и, сообщив при этом скорость жидкости w 0, совершает работу равную живой силе движущейся массы жидкости:
, (1.17)
где Т – работа, кгс·м/с.
При одной и той же площади лобовой поверхности Fл лопасть совершает различную работу, которая зависит от отношения b/h, поэтому действительная работа в кгс·м/с, затрачиваемая для приведения во вращение одной лопасти с частотой n об/мин:
, (1.18)
Где j - коэффициент, зависящий от формы лопасти.
Для прямоугольных лопаток j определяется отношением b/h
b/h | ||||||
j | 1,1 | 1,15 | 1,19 | 1,29 | 1,4 |
Для промежуточных значений b/h коэффициент j находят методом прямолинейной интерполяции.
Для горизонтальных прямоугольных лопастей при b=D/2, где D – диаметр окружности, сметаемой лопастью мешалки и ω0 = (3ω)/4, где w - окружная скорость конца лопасти. Мощность, потребляемую мешалкой в пусковой период, определяют по уравнению:
|
,(1.19)
Где Nz- кВт; z – число пар лопаток мешалки; h - механический КПД передаточного механизма; w - м/с; D – м.
Рисунок 13 - Схема якорной мешалки
Для вертикальных прямоугольных лопаток при ![]() | ![]() |
, (1.20)
Мощность, потребляемая в пусковой период для якорной мешалки рассчитывают по формуле:
, (1.21)
Где Nя- кВт; R2 и R1 - радиус кривизны соответственно наружней и внутренней частей якоря, м.
Пропеллерные мешалки. Если допустить, что поток жидкости движется параллельно валу пропеллера, как цилиндр с основанием в виде круга, описываемого винтом (ометаемая поверхность), то можно принять, что площадь этого круга:
, (1.22)
Где 0,8 – коэффициент, который вводится для учета сужения струи под действием лопастей пропеллера; D1- диаметр окружности, описываемой крайней точкой лопасти, м.
Фактическая осевая скорость w 0 перемешиваемой жидкости, шаг винта Н и частота вращения n (об/мин) связаны зависимостью (из теории пропеллерных мешалок):
, (1.23)
Где q - угол подъема винтовой линии.
Лопасть пропеллера можно представить в виде винтовой поверхности; жидкость при вращении пропеллера можно уподобить гайке, которая при каждом обороте винта должна подняться на высоту, равную шагу Н. В действительности жидкость частично скользит в обратном направлении. Это обстоятельство учитывает введение коэффициента =0,7 - 0,8. При расчете можно принимать среднее значение этого коэффициента;
=0,75. Поэтому действительную высоту подъема жидкости в течении одного оборота можно считать равной:
, (1.24)
Угол подъема винтовой линии практически принимают равным 25 - 45°. Частота вращения пропеллерных мешалок довольно велика и колеблется в пределах 400 - 1750 об/мин, уменьшаясь с уменьшением диаметра D. При перемешивании вязких жидкостей, жидкостей, содержащих взвеси, а также образующих пену, частота вращения пропеллерных мешалок колеблется в пределах 150 - 500 об/мин.
Наличие в аппаратах, снабженных пропеллерными мешалками, различных устройств, оказывающих сопротивление вращению жидкости (неподвижные лопатки, змеевики, гильзы и т.д.), приводит к повышению расхода электроэнергии.
При расположении вала пропеллерной мешалки под некоторым углом к оси аппарата (10 - 20° к вертикали) интенсивность перемешивания резко возрастает, поэтому рекомендуют устанавливать пропеллерные мешалки наклонно к оси аппарата.
|
Величина шага Н, как известно, является различной для разных сечений лопасти. Имеются винты и с постоянной шагом. Для вычисления шага обычно используют формулу
, (1.25)
где D1- диаметр винта.
В перемешивающих устройствах пропеллер вращается на месте, т.е. не совершает поступательного движения, поэтому скорость вызываемого его вращением движения перемешиваемой жидкости обусловлена только осевой скоростью просасывания жидкости через винт.
При кратности перемешивания жидкости К (в минуту) осевая ее скорость, м/с:
, (1.26)
Где G – количество перемешиваемой жидкости, кг/мин; V- объем перемешиваемой жидкости, м3/мин.
Частоту вращения (об/мин) пропеллерной мешалки можно определить из уравнения (1.20.) с учетом (1.21):
, (1.27)
Где а1=sinq - cosq
Пусть частота вращения (об/сек) пропеллера nc= n/60, тогда мощность, расходуемая пропеллерной мешалкой, кВт:
(1.28)
Обозначив , окончательно получим:
, (1.29)
Значения a1 и a2 для углов q подъема винтовой линии приведены в таблице .
Расчет и построение лопастей пропеллерной мешалки выполняют аналогично расчету судовых винтов.
Турбинные мешалки. Мощность в кВт, расходуемая турбинными мешалками:
, (1.31)
Эта формула справедлива только в ламинарной области при
, (1.32)
В этих формулах: - опытный коэффициент; n - кинематическая вязкость перемешиваемой жидкости, м2/с; n – частота вращения ротора мешалки, с-1; d – диаметр турбинной мешалки, м.
При турбулентном режиме, когда , справедливо уравнение:
, (1.33)
где N – потребляемая мощность, кВт; - опытный коэффициент.
Пневматическое перемешивание.
Пневматическое перемешивание методом барботирования заключается в следующем. С помощью расположенных на дне аппарата трубок с отверстиями (так называемых барботеров) через всю массу обрабатываемой жидкости пропускают воздух, который приводит смешиваемую среду в движение.
Давление воздуха или газа, используемого для барботирования, должно быть достаточным для создания нужного напора в трубопроводе и преодоления местных сопротивлений и гидростатического сопротивления столба перемешиваемой жидкости. Поэтому при расчете пневматических устройств для перемешивания определяют необходимое давление и расход воздуха или газа.
|
Давление воздуха или газа в Па определяют по формуле:
, (1.34)
где Н – высота столба перемешивающей жидкости, м; и
- плотность соответственно воздуха (газа) и перемешивающих жидкости в кг/м3; w - скорость воздуха в трубопроводе (обычно принимают w = 20-40 м/с); S x - сумма коэффициентов гидравлических и местных сопротивлений; Р0 - давление над жидкостью в аппарате, Па.
Если длина воздушных или газовых трубопроводах неизвестна, то ориентировочно давление в Па можно считать по формулам:
, (1.35)
Расход воздуха или давление газа в м3/c на перемешивание (в пересчете на атмосферное давление) находят по уравнению:
, (1.36)
Где К =24 - 60 - опытный коэффициент, зависящий от интенсивности перемешивания (при слабом перемешивании К= 24 - 30, при среднем – К=35 - 45, при интенсивном К = 45 - 60); F- площадь поверхности жидкости в аппарате перед перемешиванием, ; P – давление воздуха (или газа),Па.
При расчете барботёров минутный расход воздуха на 1м2 свободной поверхности смешиваемой жидкости в аппарате можно принимать равным: при слабом перемешивании 0,4 м3, при среднем – 0,8 м3, при интенсивном – 1,0 м3.
Пневматическое перемешивание не требует сложных приспособлений при наличии сжатого воздуха достаточно барботера, присоединенного к воздухопроводу. Пневматическое перемешивание следует применять, когда необходимо сравнительно медленное или глубокое перемешивание жидкостей вязкостью до 0,2 кг/(м . с).
Перемешивание острым паром применяют, когда необходимо одновременно перемешивать и обогревать жидкость. Однако, использование пневматического перемешивания связано с относительно большим расходом энергии, а также с возможностью окисления и испарения продукта. Эти недостатки в значительной мере ограничивают применение пневматическое перемешивание в химической промышленности.
Приводы мешалок
Тихоходные мешалки – лопастные, якорные и т. п. – обычно приводятся во вращение от индивидуального электродвигателя через зубчатую передачу.
Приводы обычно устанавливают на крышках аппаратов, в которых мешалка работает, иногда на балках или рамах, укрепленных на крыше. Если вал длинный, то на днище сосуда монтируется дополнительная опора. В современных конструкциях привод обычно осуществляется непосредственно от электродвигателя, через редуктор.
Для комбинированных мешалок применяются приводы типа, изображенного на рисунке 14.
Рисунок 14 - Привод комбинированной мешалки.
|
От вала 1 вращение передается через две конические зубчатые передачи: через колеса 3 и 5 в одном направлении и через колеса 2 и 4 в обратном направлении. Если передаточные числа обеих пар одинаковы, то валы колес 4 и 5 будут вращаться с одинаковой скоростью, но в разные стороны.
Если комбинированная мешалка состоит из тихоходной и быстроходной мешалок, ставятся два независимых привода. Якорная мешалка приводится во вращение от электродвигателя через пару конических колес, а турбинная – от своего электродвигателя (валы соединены муфтам).
Если места на крышке сосуда или над ней недостаточно, привод располагают под сосудом, что, однако требует установки хорошего сальникового уплотнения.
Приводы пропеллерных мешалок чаще всего осуществляются в зависимости от скорости вращения: 1.от электродвигателя, непосредственно связанного с валом мешалки; 2.от электродвигателя через шестеренчатую передачу; 3.от электродвигателя со встроенным редуктором; 4.от электродвигателя через клиноременную передачу.
Пример привода первого типа для стационарных пропеллеров показан на рисунке 15.
Применяются также электродвигатели с регулируемым числом оборотов, что делает мешалку более универсальной, в тех случаях, когда в процессе перемешивания резко изменяется вязкость системы. Для вертикальных стационарных пропеллеров, при обычных на практике диаметрах и скоростях вращения валов, считают допустимой длину вала до 1,8 м. Если необходимо иметь большую длину, то принимают следующие меры: 1. Устанавливают стабилизаторы в виде наваренных на лопасти пропеллера крылышек (рисунок 16а) или в виде широкого кольца со спицами, укрепляемого на конце вала (рисунок 16б). 2. Устанавливают концевые подшипники, монтируемые на днище сосуда, как это показано на рисунок 17а и б. 3. Устанавливают дополнительный подшипник в приводе (рисунок 18а, или дополнительный вынесенный подшипник (рисунок 18в). | ![]() |
![]() | ![]() |
Рисунок 16 - Приспособления для снижения амплитуды колебаний вала мешалки. | Рисунок 17 - Концевые подшипники мешалок. |
Рисунок 18 - Дополнительные подшипники в приводах мешалок.
Для уменьшения длины вала прибегают к установке привода под сосудом. Более короткие валы имеют также боковые мешалки, привод которых устанавливается или на вертикальной стенке сосуда, или на днище в случае горизонтальных сосудов.
Стойки отливают из чугуна или сваривают из углеродистой стали. Они представляют собой цилиндры или усеченные конусы, снабженные верхним и нижним присоединительными фланцами. В обечайке стоек имеются вырезы для удобства монтажа и демонтажа.
в приводах концевые опоры служат для подвижного закрепления нижнего конца вала перемешивающего органа. Опоры состоят (рисунок 19) из стойки 1, к которой болтами 7 прикреплен подшипник 2, в нем закреплена штифтами 5 неподвижная втулка 4. На нижнем конце вала закреплена болтом 6 подвижная втулка 3, которая вращается вместе с валом внутри неподвижной втулки 4.
Втулки изготавливают из чугуна, графита, капрона, текстолита или фторопласта-4, остальные детали из углеродистой стали для нейтральных сред или из коррозионно-стойких материалов для агрессивных сред. С точки зрения распределения нагрузок наиболее рациональны приводы с концевыми подшипниками, однако, во многих случаях из-за коррозионного или абразивного действия среды их нельзя устанавливать. Концевые подшипники в аппарате работают в очень тяжелых условиях: их невозможно смазывать, они плохо | ![]() |
доступны для осмотра и ремонта. Конструкция подшипника должна обеспечивать свободную циркуляцию жидкости через него. На рисунке 20а показан типовой концевой подшипник (подпятник). Подпятник, показанный на рисунке 20б применяется для футерованных аппаратов. Коническое основание этого подпятника обеспечивает ему высокую жесткость и предохраняет футеровку вблизи подпятника от разрушения.
а) | б) |
а) типовая конструкция; б) подпятник для футерованных аппаратов
Рисунок 20 - Концевые подшипники.
При работе мешалки без концевого подшипника возможно появление крутильных колебаний консольного вала мешалки, являющихся следствием динамических нагрузок на вал от перемешиваемой среды, условий закрепления вала в опорах, конструкции мешалки. При неправильном учете в процессе конструирования таких важных критериев надежности, как жесткость и виброустойчивость, эксплуатация аппаратов с мешалками встречает ряд затруднений. Если вал с мешалкой не отбалансирован и в его подшипниковых опорах имеется люфт d, то возможно отклонение нижнего конца вала на величину s. Схема отклонения вала с двумя подшипниковыми опорами изображена на рисунок 22.
![]() | ![]() |
1- редуктор; 2- продольно-разъемная муфта; 3- стойка привода; 4- уплотнение; 5- опора привода; 6- маслоуловитель; 7- вал; 8- концевой подшипник Рисунок 21 - Привод. | Рисунок 22 - Схема колебаний вала. |
Из подобия треугольников (рисунок 22) получаем соотношение:
, (1.37)
, (1.38)
Т.е. колебания вала зависит от величины люфта d и отношения L/ l.
Если люфт устранить полностью, то величину отношения L/ l можно ограничить. Для надежной работы консольного вала мешалки рекомендуется L/ l 4. Для уменьшения крутильных колебаний вала после крепления мешалки он должен быть статически отбалансирован. При опасности возникновения крутильных колебаний, которые ведут к нарушению работы сальника, или при больших значениях L/ l необходима установка концевого подшипника.
Крутильные колебания вызывают повышенный износ подшипников и сальника. Концевой подшипник устраняет крутильные колебания, улучшая работу сальника и подшипниковых опор. Хотя концевой подшипник работает в агрессивной среде, применение его для нормальной работы аппарата необходимо при большой длине или высокой частоте вращения вала.
Для обеспечения соосности обеих втулок (рисунок 19) может применяться концевой подшипник (рисунок 23), в котором обойма невращающейся втулки имеет шаровую поверхность, что дает возможность устанавливать ось этой втулки в нужном направлении.
1- вал; 2- вращающаяся втулка; 3- невращающаяся текстолитовая втулка; 4- обойма.
Рисунок 23 - Концевой подшипник с шаровой обоймой
Крепление мешалок. В простейших конструкциях лопасти приваривают непосредственно к валу. Однако, элементы крепятся на валу с помощью разъемных соединений. Обычно мешалка состоит из ступицы, к которой привариваются лопасти. Ступица крепится на валу с помощью шпонки и стопорных устройств, препятствующих осевому смещению. В случае установки мешалки в середине вала ее закрепляют стопорным винтом (рисунок 24а), при установке на конце вала – концевой гайкой (рисунок 24б) или с помощью двух полуколец, которые закладываются в кольцевую выточку на валу (рисунок 24.в).
а) стопорным винтом; б) концевой гайкой; в) полукольцами
Рисунок 24 - Способы крепления мешалок на валу.
При конструировании мешалок необходимо учитывать условия их монтажа. Мешалки небольших аппаратов (диаметром 1,2 м и менее) обычно собираются совместно с крышкой и вместе с ней устанавливаются в аппарат. Они должны иметь минимум разъемных соединений. Мешалки для крупногабаритных аппаратов целесообразно делать разъемными из частей таких размеров, которые можно пронести через лаз аппарата. Это дает возможность разбирать мешалку при ремонтных и монтажных работах, не снимая крышку и привод. В цельносварных аппаратах мешалка обязательна должна быть разборной.
Муфты служат для соединения вала привода с валом мешалки. Применяют в основном нормализованные муфты двух типов – продольно-разъемные и зубчатые.
![]() | ![]() |
Продольно-разъемные муфты применяют для жесткого соединения выходного вала редуктора (мотор-редуктор) с валом перемешивающего устройства с промежуточным валом при любом числе промежуточных опор. Муфта состоит (рисунок 25) из корпуса 1 (образующегося двумя половинами), накидных фланцев 2 и шпилек 5 с шайбами и гайками. Соединяемые концы валов имеют кольцевые проточки, на которые надето разрезное кольцо 3, половинки его скрепляются двумя пружинами 4. Сверху надеты на шпонке половины корпуса, после затяжки шпилек фланцев получается жесткое соосное соединение валов.
Зубчатые муфты применяют для соединения выходных валов мотор-редуктора и электродвигателя (гидромотора) с промежуточным валом при двух промежуточных опорах. Муфта состоит (рисунок 26) из зубчатой обоймы 1, укрепленной шпонкой на валу мотор-редуктора, и зубчатой втулки 2, сидящей на шпонке на промежуточном валу. Зубья втулки входят во впадины обоймы. Муфта передает крутящий момент, но не соединяет валы жестко по оси.
Уплотнения
Для создания герметичности между неподвижным корпусом аппарата и вращающимся валом служит уплотнение. В зависимости от физико-химических характеристик и параметров рабочих сред, а также требований производственной санитарии, техники безопасности и пожароопасности аппараты для перемешивания жидких сред комплектуются сальниковыми или торцевыми уплотнениями, гидрозатворами или имеют герметичный привод.
Сальниковое уплотнение состоит из корпуса, грундбуксы, нажимной втулки, сальниковой и стягивающих шпилек (рисунок 27). Уплотнение достигается прижатием сальниковой набивки к вращающемуся валу. Между валом о грундбуксой остается зазор 0,5 - 0,75 мм, а между валом и нажимной втулкой – несколько – больший зазор (1 - 1,5 мм). Эти зазоры устраняют возможность износа вала в указанных местах. Для изготовления грундбуксы и нажимной втулки используется чугун. При отсутствии зазора между валом и грундбуксой последняя должна изготовляться из бронзы.
1 - корпус; 2- нажимная втулка; 3- набивка; 4 - упорное кольцо (грундбукса).
Рисунок 27 - Сальник.
В некоторых случаях сальниковое устройство одновременно является опорой для вала (подшипником скольжения). Тогда зазор между валом и нажимной втулкой делается минимальным, т.е. на посадке скольжения. Нажимная втулка снабжается устройством для подачи и распределения смазки и изготовляется из бронзы или снабжается бронзовым вкладышем.
Cальник (рисунок 28) в середине слоя сальниковой набивки имеет сальниковое кольцо, которое обеспечивает равномерный подвод смазки по всему периметру вала в середину набивки. Для отвода тепла сальник снабжается охлаждающей рубашкой.
1 - корпус; 2- рубашка; 3- нажимная втулка; 4- набивка; 5- смазочное кольцо; 6- упорное кольцо (грундбукса).
Рисунок 28 - сальник со смазывающим кольцом.
В качестве сальниковых набивок чаще всего применяются хлопчатобумажные, пеньковые и асбестовые материалы.
Ниже приведены предельные температуры, при которых могут использоваться набивки.
Таблица 1.2 - Предельные температуры для сальниковых набивок.
Материал набивки | Предельная температура ° С |
Асбестовая набивка: Маслобензостойкая Пропитанная Сухая | |
Асбестопроволочная набивка | |
Пеньковая просаленная набивка | |
Хлопчатобумажная просаленная набивка | |
Фторопласт |
Перечисленные набивки могут применяться при давлениях 0,6-4 Мпа в зависимости от температуры и используемого пропитывающего состава. Пропитка служит для улучшения герметизации и снижения коэффициента трения набивки о вал. Для пропитки набивок применяют сало, парафин, битум, графит, жидкое стекло, тавот, вискозин и т.п.
Из указанных выше набивок следует отметить фторопласт. Он имеет малый коэффициент трения, поэтому срок его службы в несколько десятков раз больше, чем у остальных материалов. Этому способствует также его высокая химическая стойкость. Недостатки фторопласта – сравнительно высокая твердость (что требует больших усилий при затяжке сальника) и высокая стоимость. Эти недостатки устраняются в набивке из асбестового шнура, пропитанного фторопластовой суспензией.
При высоких температурах (t > 300° С) используются сухие набивки. Наиболее распространенная сухая набивка марки АГ-50 состоит из 50% графита, 45% длинноволокнистого асбеста и 5% алюминиевой пудры. Утечка уплотняемой среды в сухих набивках происходит вследствие их пористости. Даже при высоких давлениях прессования набивки (30 - 60 МПа) она остается пористой, так как составляющие её компоненты – асбест и графит – являются пористыми телами.
Сальниковые уплотнения применяют в аппаратах, работающих при давлениях до 0,1 МПа и температуре до 70°. Их нельзя применять при вакууме, переработке в аппаратах ядовитых и взрывоопасных сред. Скорость вала – от 5 до 320 об/мин.
Для нормальной работы сальника необходимо, чтобы усилие прижатия нижних слоев к валу равнялось давлению среды. Усилие прижатия набивки к валу действует в радиальном направлении, тогда как поджим набивки нажимной втулкой производится в осевом направлении. Схема работы сальника изображена на рисунке 29. Если бы набивной служила идеальная жидкость, то осевое и радиальное усилие были бы равны (Рх = Ру) во всех её участках. Однако, поскольку набивка является деформируемым твердым телом, то Рх <= Ру и, кроме того, сила прижатия набивки к валу будет изменяться по высоте сальниковой камеры вследствие трения набивки о вал и корпус при её деформации, т.е. при сжатии.
1 - вал; 2 - нажимная втулка; 3- корпус.
Рисунок 29 - Схема распределения усилий в сальнике.
Связь осевого и радиального усилий можно выразить зависимостью:
, (1.39)
Величина m зависит от материала набивки, давления и лругих факторов и изменяется в пределах от 1,5 до 5.
Закон изменения осевой силы по высоте сальника можно представить следующим образом:
, (1.40)
Где S=(D-d)/2; f=m ТР/m; m ТР – коэффициент трения набивки о вал и корпус сальника.
В нижней части при у=0 справедливо равенство Ру=Р0, а верхней при y=h – равенство Ру=Р0 ехр(2 f h/S). Величина осевого усилия в верхней части позволяет по площади сечения набивки определить усилие затяга и рассчитать стяжные шпильки.
При совместном решении уравнений (1.39) и (1.40) получим закон изменения радиальной силы по высоте набивки, т.е. силы прижатия набивки к валу:
, (1.41)
Эпюра изменения силы прижатия набивки к валу изображена на рисунке 29. При удалении от нажимной втулки эта сила уменьшается. При большой высоте сальниковой набивки уменьшение радиальной силы будет значительным. Эффективное перераспределение радиальной силы может быть достигнуто в конструкции двойного сальника, однако, двойной сальник применения не находит, так как его эксплуатация очень сложна.
Если бы набивка являлась абсолютно твердым телом, то в противоположность допущению об идеальной жидкости, прижатие набивки к валу должно полностью отсутствовать. Для деформируемого твердого тела усилие прижатия набивки к валу будет составлять некоторую часть от осевого усилия. Увеличение силы прижатия можно достигнуть конструктивным приемом – изготовление колец уплотнительной набивки с конусными поверхностями. Для реальных набивок этот прием широко используется.
Определим мощность, теряемую на трение в сальнике. Для элемента набивки высотой dy сила трения равна:
, (1.42)
После подстановки значения Рх из уравнения (1.41) и интегрирования в пределах от 0 до h получаем:
, (1.43)
С учетом f=m тр/m имеем:
, (1.44)
Мощность теряемая на трение, будет равна:
, (1.45)
, (1.46)
Коэффициент трения f при вращении вала имеет меньшее значение, чем при неподвижном вале, кроме того, он изменяется при изменении давления. Учесть все это для разнообразных набивок при использовании уравнения (1.45) сложно, поэтому переходят к эмпирической зависимости (1.46), которая для практических расчетов принимает вид:
, (1.47)
Таблица 1.3 - Влияние геометрических размеров сальниковой набивки на потери мощности.
Геометрические раз- меры сальниковой набивки, h/S | |||||||
Значения коэффици- ента, К | 0,65 | 0,83 | 1,02 | 1,24 | 1,58 | 1,70 | 2,34 |
Ширина сальниковой набивки S,мм определяется по диаметру вала:
, (1.48)
Торцевое уплотнение. В этом уплотнении герметичность достигается за счет плотного поджатия по торцевым плоскостям двух деталей – вращающейся и неподвижной. Герметичность в таком соединении может быть достигнута только при высоком качестве обработке прилегающих поверхностей. Неровности 1мкм нарушают нормальную работу торцевого уплотнения. Поверхности трения подвергаются шлифовке и притирке, и имеют высокую чистоту обработки (№ 10 - № 12), они могут быть плоскими, сферическими или конусными. Плоские поверхности применяются чаще, т.к. при доводке легче получить хорошую чистоту поверхности трения, ширина кольцевой поверхности трения не должна быть большой (меньше 6 - 8 мм).
В химической промышленности торцевые уплотнения применяются не только для реакторов, но и для центробежных насосов. Торцевое уплотнение для герметизации аппаратов представлено на рисунке 30. Кольцо 2 получает вращение от вала через водило 4, состоящее из двух половинок, стягивающих вал, и через шпильки 3. Неподвижное кольцо 7 соединено с сильфоном. Тяги 6 с пружиной дают возможность регулировать силу поджатия колец 2 и 7, сильфон 8 позволяет компенсировать биение вала.
1 - корпус; 2 - вращающееся кольцо; 3 - шпилька; 4 - водило; 5 - пружина; 6 - тяга; 7 - неподвижное кольцо; 8 - сильфон.
Рисунок 30 - Торцевое уплотнение.
уплотнение (рисунок 30) работает при давлении 2* 103 - 1,6* 106 Па, температуре до 250 ° С и частоте вращения до 10 с-1.
Достоинства – меньшие утечки, чем в сальнике, так как при работе под вакуумом подсос воздуха отсутствует, потери мощности составляют десятые доли потерь мощности на трение в сальнике, не требуется обслуживания, что объясняется большой износостойкостью пары трения (а следовательно, долговечностью) и хорошей работой при биениях вала.
Недостатки – высокая стоимость и сложность ремонта.
Основным узлом торцевого уплотнения является пара трения. Материал, из которого она изготовлена, должен обладать износостойкостью и малым коэффициентом трения. Используются следующие материалы: кислостойкая сталь – одно кольцо; углеграфит, бронза или фторопласт – другое кольцо. Фторопласт применяется только в случае небольших давлений и при невысоких скоростях пары трения, так как он обладает хладотекучестью. По конструкции торцевое уплотнение может быть внутренним и внешним, одинарным и двойным. Уплотнение, изображенное на рисунке 30, является внешним.
У внутреннего уплотнения вращающееся кольцо и нажимные пружины расположены внутри аппарата в рабочей среде. Двойное уплотнение имеет две пары трения и практически представляет собой два последовательных одинарных уплотнения. В двойном уплотнении между двумя парами трения помещается запирающая среда, предотвращающая утечки и отводящая тепло трения.
В химической промышленности наиболее распространенными являются следующие типы торцевых уплотнений: а) двойное торцевое уплотнение типа ТД (левая часть рисунок 31), предназначенное для герметизации валов аппаратов для перемешивания взрывоопасных, токсичных, пожароопасных, ядовитых и подобных им сред при давлениях до 0,6 МПа (тип ТД-6) и при давлениях до 3,2 МПа (тип ТД-32); б) двойное торцевое уплотнение ТДП (правая часть рисуно
|
|
Организация стока поверхностных вод: Наибольшее количество влаги на земном шаре испаряется с поверхности морей и океанов (88‰)...
Особенности сооружения опор в сложных условиях: Сооружение ВЛ в районах с суровыми климатическими и тяжелыми геологическими условиями...
Папиллярные узоры пальцев рук - маркер спортивных способностей: дерматоглифические признаки формируются на 3-5 месяце беременности, не изменяются в течение жизни...
Архитектура электронного правительства: Единая архитектура – это методологический подход при создании системы управления государства, который строится...
© cyberpedia.su 2017-2024 - Не является автором материалов. Исключительное право сохранено за автором текста.
Если вы не хотите, чтобы данный материал был у нас на сайте, перейдите по ссылке: Нарушение авторских прав. Мы поможем в написании вашей работы!