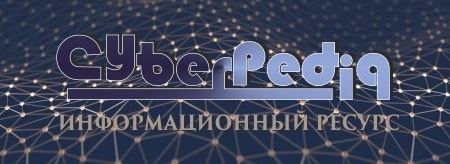
Таксономические единицы (категории) растений: Каждая система классификации состоит из определённых соподчиненных друг другу...
Поперечные профили набережных и береговой полосы: На городских территориях берегоукрепление проектируют с учетом технических и экономических требований, но особое значение придают эстетическим...
Топ:
Когда производится ограждение поезда, остановившегося на перегоне: Во всех случаях немедленно должно быть ограждено место препятствия для движения поездов на смежном пути двухпутного...
Выпускная квалификационная работа: Основная часть ВКР, как правило, состоит из двух-трех глав, каждая из которых, в свою очередь...
Интересное:
Уполаживание и террасирование склонов: Если глубина оврага более 5 м необходимо устройство берм. Варианты использования оврагов для градостроительных целей...
Берегоукрепление оползневых склонов: На прибрежных склонах основной причиной развития оползневых процессов является подмыв водами рек естественных склонов...
Инженерная защита территорий, зданий и сооружений от опасных геологических процессов: Изучение оползневых явлений, оценка устойчивости склонов и проектирование противооползневых сооружений — актуальнейшие задачи, стоящие перед отечественными...
Дисциплины:
![]() |
![]() |
5.00
из
|
Заказать работу |
Содержание книги
Поиск на нашем сайте
|
|
Лекция 1
Табл. 2.14.
Этапы обработки | Оборудование | Получаемый продукт |
Разрыхление / трепание | Разрыхлительно-трепальный агрегат | Холст |
Чесание | Чесальные машины | Лента чесальная |
Выравнивание ленты и параллелизация волокон | сложение / вытягивание | Ленточные машины |
Подготовка к гребнечесанию | Лентосоединительная и холстовытяжная машины | Холстик |
Гребнечесание | Гребнечесальные машины | Лента гребенная |
Изготовление равномерной ленты | Ленточные машины (2-3 перехода) | Лента |
Изготовление ровницы | Ровничные машины (1 или несколько переходов) | Ровница |
Изготовление пряжи - прядение | Прядильные машины | Пряжа |
Табл. 2.15
Этапы обработки | Оборудование | Получаемый продукт |
Разрыхление и трепание отдельных видов сырья | Разрыхлительно-трепальные установки в зависимости от видов сырья | Масса разрыхленного сырья |
Смешивание | Изготовление настилов из компонентов вручную или механически | Смесь волокон |
Чесание и получение ровницы | Чесальный аппарат | Ровница |
Изготовление пряжи | Прядильная машина | Пряжа |
Рис. 2.1. Схема производства в кардной системе прядения хлопка
Рис. 2.2. Схема производства в гребенной системе прядения хлопка
Лекция 2
Разрыхлительно - очистительный агрегат высокой очистительной способности
На рис. 2.4 показана схема разрыхлительно- очистительного агрегата для переработки смесей хлопкового волокна с повышенным содержанием сорных и жестких примесей.
Основная часть агрегата состоит из восьми кипоразрыхлителей РКА-2Х 1, подающих волокно в дозирующие бункеры ДБ-1 3, оснащенные быстроходными конденсорами КБ-3 2.
Дальнейшая обработка волокон происходит на головном питателе ПГ- 5 4 с быстроходным конденсором КБ-3 2, наклонном очистителе ОН-6-3 5, осевом двухбарабанном очистителе ЧО 6 и наклонном очистителе ОН-6-4 7 с конденсером КБ-4 2. Затем волокно с помощью пневматического распределителя волокон РВП-2 8 поступает на трепальную машину МТ 9, где происходит окончательная очистка волокон от сорных примесей и формирование холста.
|
При бункерном питании чесальных машин применяются бесхолстовые трепальные машины ТБ–3 или МТБ, на которых волокно пневматическим распределителем направляется в резервные питатели ПРЧ–2, а из них системой бункерного питания распределяется по кардочесальным машинам.
Рис. 2.4. Схема разрыхлительно - очистительного агрегата для переработки средневолокнистого хлопка
Лекция 3
ЧЕСАНИЕ ВОЛОКНА
После разрыхления, смешивания и трепания смесь хлопка содержит еще часть сорных примесей, волокна полностью не отделены одно от другого, перепутаны и составляют отдельные небольшие клочки. Дальнейшее трепание не позволяет полностью разделить волокна и подготовить хлопок для дальнейших технологических операций изготовления пряжи. Поэтому следующим переходом является процесс чесания волокна.
В процессе чесания происходит разделение клочков хлопка на отдельные волокна; очистка хлопка от оставшихся в нем сорных примесей и частичное удаление коротких волокон; частичное выпрямление и параллелизация волокон и, наконец, утонение продукта, и формирование ленты.
Выполнение этих задач происходит за счет использования в чесальных машинах специальной гарнитуры - пильчатой металлической ленты с зубцами или эластичной ленты с гибкими тонкими иглами. Взаимодействуя между собой и с волокнистой массой, рабочие органы, обтянутые указанной гарнитурой, растаскивают волокна из клочков, отделяют их от сорных примесей, в том числе и цепких, и располагают волокна более или менее параллельно в выходном продукте - чесальной ленте.
|
Чесальный переход оказывает большое влияние на дальнейший процесс изготовления пряжи, так как именно здесь формируется почти готовый полупродукт. Кроме того, на этом процессе заканчивается удаление сорных примесей, и все оставшиеся волокна попадают уже в пряжу. Таким образом, основная задача процесса чесания - это получить продукт - чесальную ленту с минимальным количеством сорных примесей, с высокой степенью разъединенности комплексов и хорошим распрямлением и параллелизацией волокон, а главное, высокой ровнотой ленты.
На прядильных фабриках применяются в основном шляпочные чесальные машины. Применяются также валичные чесальные машины.
Шляпочные чесальные машины
В холстах, полученных с однопроцессных трепальных машин, остается до 40 % сорных примесей и пороков, содержащихся в хлопке (частичек листа хлопчатника, коробочек, стебельков, незрелых семян) и пороков хлопка (кожицы с волокном, завитков, жгутиков и др.). К массе холста эти примеси составляют от 2,5 до 5 % в зависимости от засоренности хлопка. Для удаления посторонних примесей из хлопка необходимо разъединить волокна. Эту операцию нельзя выполнить на трепальных машинах. Для разъединения клочков волокон нужны машины, приспособленные к выполнению операций распутывания. Процесс расчесывания клочков хлопка производится на чесальных машинах. Процесс кардочесания является одним из важнейших процессов в прядильном производстве.
Сущность процесса кардочесания заключается в разъединении волокон, в вычесывании мелких и цепких примесей и пороков волокон, а также в частичной ориентации волокон.
Процесс кардочесания осуществляется с целью обеспечения индивидуального движения волокон в вытяжных приборах ленточных и других машин и получении равномерного продукта и пряжи при ее формировании.
В настоящее время известен один способ кардочесания - механический, в котором на клочки и пучки волокон действуют с противоположных сторон две кардные (игольчатые, цельнометаллические зубья) поверхности. При параллельном расположении игл (зубьев) на кардных поверхностях и их относительном движении осуществляется процесс кардочесания волокон.
Конструкция чесальных машин существенно зависит от свойств перерабатываемого волокнистого материала: в хлопкопрядении применяют шляпочные чесальные машины, для других натуральных волокон - валичные, для химических волокон - те и другие.
|
В зависимости от диаметра главного барабана различают шляпочные чесальные машины:
- малого габарита ЧММ-450-4, ЧММ-14 для переработки средневолокнистого хлопка и химических волокон в кардной системе прядения и ЧММ-14Т для переработки тонковолокнистого хлопка и химического волокна в гребенной системе прядения;
- нормального габарита ЧМ-50 и ЧМ-60 для переработки средневолокнистого и тонковолокнистого хлопка и химических волокон в кардной и гребенной системе прядения.
Малогабаритные чесальные машины могут иметь два главных барабана и называются двухбарабанные.
Перечисленное оборудование выпускает Ивановский завод чесальных машин.
Чесальные машины ЧММ-14, ЧММ-14Т, ЧМ-50, ЧМ-60 могут использоваться при холстовом и бесхолстовом способах питания.
Чесальные машины фирм: «Плат Сако Ловел», «Кросрол» (Англия), «Шуберт и Зальцер» (Германия), «Трючлер» (Германия), «Ритер» (Швейцария), «Марцоли» (Италия), «Холингсворт» (США) работают преимущественно при бесхолстовом питании и автоматическом регулировании линейной плотности чесальной ленты.
Лекция 4
Ленточные машины
Лента, полученная на кардочесальных машинах, имеет ряд недостатков:
- неровноту на коротких и длинных отрезках;
- слабую распрямленность волокон, достигающую лишь 50-60%;
- недостаточную продольную ориентацию многих волокон.
На ленточных машинах осуществляется два процесса: вытягивание и сложение.
Цель вытягивания – распрямление и ориентация волокон, утонение продукта.
Сущность вытягивания заключается в относительном смещении волокон вытягиваемого продукта и в распределении их на большей длине.
При этом между волокнами действуют силы трения и сцепления, благодаря которым волокна распрямляются и располагаются параллельно друг другу вдоль оси продукта.
На ленточных машинах применяется механический способ вытягивания в вытяжном приборе. Интенсивность вытягивания характеризуется вытяжкой, величину которой можно определить как отношение скорости выпуска ленты к скорости ее подачи. Так как на ленточной машине угары практически не выделяются (выделяется только небольшое количество пуха), то для ленточной машины вытяжка и утонение продукта численно равны между собой. Известны также пневматический и пневмомеханический способы вытягивания.
|
На ленточной машине после одновременного вытягивания нескольких лент осуществляется соединение этих лент, то есть процесс сложения.
Сложение осуществляется с целью выравнивания продукта по толщине, составу и структуре.
Сущность сложения заключается в том, что различные по толщине, структуре и другим свойствам участки складываемых продуктов соединяются в самых разнообразных комбинациях.
В процессе сложения происходит смешивание волокон.
Для уменьшения неравномерности ленты по линейной плотности, наряду с процессом сложения нескольких лент на ленточной машине, может применяться автоматическое регулирование вытяжки.
Лекция 5
Ровничные машины
Лента, полученная на ленточной машине последнего перехода, обладает всеми свойствами, необходимыми для получения из нее пряжи: волокна очищены от посторонних примесей, перемешаны, распрямлены и расположены параллельно оси ленты, выровненной по толщине. Чтобы непосредственно из такой ленты получить пряжу на кольцевых прядильных машинах, ее необходимо утонить в вытяжных приборах высокой вытяжки. Однако в этом случае усложняется конструкция вытяжного прибора, затрудняется обслуживание прядильной машины. Поэтому при кольцевом способе формирования пряжи необходимое утонение ленты осуществляют чаще всего в два этапа. Сначала из ленты получают на ровничных машинах более тонкий продукт - ровницу, а затем на кольцевой прядильной машине вырабатывают пряжу требуемой линейной плотности.
При выработке тонкой пряжи в гребенной системе прядения хлопка применяют обычно два перехода ровничных машин: на первом вырабатывают ровницу из ленты, а на втором - тонкую, более равномерную, ровницу, применяя сложение двух ровниц.
Задачей ровничной машины является формирование из ленты более тонкого слегка крученого продукта - ровницы и формирование паковки. На ровничной машине осуществляются процессы: вытягивание, кручение и наматывание.
Вытягивание применяют для утонения поступающего на машину продукта (ленты) и дальнейшего распрямления волокон. В процессе вытягивания получают продукт заданной линейной плотности.
Кручение применяют для упрочнения получаемого в результате вытягивания продукта и формирования ровницы. Мычка, выходящая из выпускной пары вытяжного прибора, состоит из хорошо параллелизованных волокон. При малой толщине прочность мычки настолько мала, что не позволяет использовать ее на последующих машинах. При кручении ровницы волокна располагаются примерно по винтовым линиям. Волокна наружных слоев натягиваются и давят на волокна, расположенные ближе к оси ровницы. Благодаря этому силы трения и сцепления между волокнами увеличиваются, обеспечивая повышение прочности ровницы.
|
Кручение осуществляется веретеном и насаженной на него рогулькой. При вращении веретена образуются витки крутки, которая накладывается на мычку, выпускаемую выпускной парой вытяжного прибора.
Цель процесса наматывания — получить плотную компактную паковку (по возможности большой емкости), удобную для транспортировки, хранения и последующей переработки ровницы без ее повреждения.
Наматывание ровницы осуществляется за счет разницы в частоте вращения катушки и веретена. На всех ровничных машинах хлопкопрядильного производства катушки вращаются с большей скоростью, чем веретена.
Ровница раскладывается вдоль катушки за счет возвратно-поступательного движения катушки вместе с верхней кареткой машины в вертикальном направлении.
Лекция 6
Прядильные машины
Назначение прядения заключается в том, чтобы получить пряжу из полуфабриката (ленты и ровницы), поступающего в прядильный отдел.
Сущность прядения заключается в утонении поступающего полупродукта до заданной линейной плотности, в придании полученному продукту (пряже) посредством кручения требуемой прочности и формировании путем наматывания определенной паковки: початка или бобины.
К прядению как к заключительному этапу получения пряжи предъявляются определенные требования:
- процесс прядения должен обеспечить высокое качество пряжи, удовлетворяющее технологическим и потребительским свойствам;
- процесс по возможности должен идти непрерывно;
- необходимо минимизировать обрывы пряжи при прядении - при высокой обрывности происходит снижение производительности машины и увеличение угаров, плюс к этому, пряжа, выработанная при высокой обрывности на прядильной машине, плохо перерабатывается в ткацком производстве.
В зависимости от способов утонения и формирования продукта (способов прядения) различают кольцевые (веретенные) и безверетенные прядильные машины. Кольцевые прядильные машины в свою очередь, подразделяются на основные и уточные. На основных машинах пряжа наматывается на бумажные патроны в паковки (початки) с массой 60-100г., пряжа с початков перематывается в бобины. На уточных машинах пряжа наматывается на деревянные шпули и используется в таком виде непосредственно на ткацком станке (при использовании в ткачестве челночных ткацких станков).
В последние годы появились прядильные кольцевые машины, обеспечивающие высокую степень утонения продукта (вытяжка до 60 или 100). На такие машины полупродукт может поступать в виде ленты, минуя ровничный переход. Таким образом, кольцевые прядильные машины могут быть ровничные (обычные) и безровничные.
Из безверетенных прядильных машин практическое применение в промышленности нашли машины пневмомеханического действия типа БД-200. Также применяются машины роторного прядения (пневмомеханического), механического, электромеханического и гидравлического способов прядения.
Прядильные машины любого способа прядения предназначены для утонения продукта (ленты или ровницы) посредством его вытягивания на вытяжных приборах различных конструкций, обеспечивающих вытяжку от 10 до 100; формирование из мычки прочной пряжи с помощью крутильного механизма - веретена и бегунка на кольцевых машинах и пневматической камеры на безверетенных машинах и наматывания изготовленной пряжи на паковку - початок (шпулю) или цилиндрическую бобину.
Кольцевые прядильные машины
Кольцевые прядильные машины используют для получения окончательного продукта прядильного производства – пряжи. В настоящее время для получения пряжи в хлопкопрядильном производстве наряду с кольцевыми прядильными машинами применяют пневмомеханические прядильные машины, работающие с большей производительностью. Однако кольцевая прядильная машина продолжает оставаться основной прядильной машиной хлопкопрядильного производства.
На кольцевой прядильной машине осуществляются процессы: вытягивание, кручение и наматывание пряжи.
Вытягивание применяют для утонения поступающей на машину ровницы до требуемой толщины и дальнейшего распрямления и параллелизации волокон. В результате вытягивания получают продукт заданной линейной плотности. Вытягивание осуществляется в вытяжном приборе, состоящем из нескольких вытяжных пар.
Кручение применяют для упрочнения получаемой в результате вытягивания мычки и формирования пряжи. В отличие от ровничной машины на кольцевой прядильной машине мычке сообщается крутка значительно большей величины. Это объясняется тем, что пряжа является конечным продуктом, вследствие чего она должна обладать возможно большей прочностью.
Кручение пряжи осуществляется с помощью веретена. Вращаясь с большой скоростью, веретено закручивает конец пряжи, закрепленный на паковке, установленной на веретене. Благодаря этому участок пряжи между выпускной парой вытяжного прибора и паковкой скручивается.
Наматывается пряжа с целью получения плотной компактной паковки, пригодной для дальнейшего использования в ткацком, трикотажном, крутильном или другом производстве.
Наматывание пряжи на патрон, установленный на веретене, осуществляется за счет разницы в частоте вращения веретена и бегунка, движущегося по кольцу. В связи с тем, что пряжа наматывается на коническую поверхность, диаметр наматывания непрерывно меняется. Вследствие этого меняется и частота вращения бегунка. Пряжа раскладывается вдоль оси патрона за счет возвратно-поступательного перемещения кольцевой планки. В связи с изменением диаметра наматывания скорость перемещения кольцевой планки непрерывно меняется.
Лекция 7
Машины
Технологический процесс формирования пряжи на ППМ осуществляется следующим образом (рис. 5.53). Лента выбирается из таза 1 и протаскивается питающим цилиндром 2 через уплотнительную воронку 3, закрепленную на питающем столике 4. Питающий столик прижимается пружиной 5 к питающему цилиндру, за счет чего создается необходимое усилие для протаскивания ленты через уплотнительную воронку. После уплотнительной воронки лента питающим цилиндром подается к дискретизирующему валику 6.
Дискретизирующий валик обтянут пильчатой гарнитурой, и вращается на современных машинах с частотой 6000-11000 мин-1. Его зубья интенсивно разрабатывают волокнистую бородку и вызывают ее утонение в 3000-10000 раз, т.е. происходит сверхвысокая вытяжка. При этом в сечении продукта остается всего 2-6 волокон, которые не контактируют между собой. Такой поток волокон называется дискретным, а процесс дискретизацией.
Когда волокна выходят из зажима питающего цилиндра со столиком, они захватываются зубьями дискретизирующего валика. При его движении сорные примеси, потерявшие связь с волокнами, подводятся к сороотводящему каналу 7, а волокна - к транспортирующему каналу 8. Сорные примеси и волокна с зубьев барабанчика удаляются воздухом, который движется по этим каналам. Оставшиеся на зубьях волокна сбиваются ножом 9. Воздух, движущийся по транспортирующему каналу, снимает волокна с дискретизирующего барабанчика и в виде непрерывного дискретного потока несет их на сборную поверхность прядильной камеры. Транспортирующий канал выполнен в форме конфузора, следовательно, скорость воздуха в нем увеличивается, что способствует сохранению распрямленности волокон вдоль оси канала. Движение воздуха в транспортирующем канале создается разрежением в камере, так как в стенках камеры сделаны радиальные отверстия, и при вращении она работает как вентилятор.
Далее пряжа проходит через нитеводитель 16 и наматывается на бобину 17. Бобина с пряжей приводится в движение мотальным валиком 18, который обеспечивает постоянную скорость наматывания пряжи. На участке между пряжевыводной трубкой 13 и мотальным валиком на машинах различных фирм могут быть установлены устройства для парафинирования, нитенаблюдатели и нитеочистители 19.
В таблице 5.3 представлена техническая характеристика машины ППМ-120-1АМ.
Для формирования пряжи в камеру вводится заправочный конец пряжи, который через отверстие 13 пряжевыводной трубки засасывается в камеру под действием имеющегося в ней разрежения. Центробежные силы отбрасывают нить к желобу на волокнистую ленточку, и нить соединяется с ней. При вращении прядильной камеры волокна из волокнистой ленточки прикручиваются к заправочному концу пряжи, и волокнистая ленточка снимается по кругу с желоба прядильной камеры со скоростью выпускной пары 14-15.
На участке между линией зажима оттяжной пары и точкой съема волокнистой ленточки с желоба прядильной камеры пряжа получает основную крутку.
Волокнистая ленточка снимается с желоба прядильной камеры в свободном состоянии, вследствие чего способ и получил название «прядение со свободным концом».
Таким образом, одним из основных технологических процессов, осуществляемых на машинах пневмомеханического прядения, является дискретизация (разъединение) питающего продукта на отдельные волокна, т. е. превращение непрерывного полуфабриката, в сечении которого содержатся десятки тысяч волокон, в дискретный поток отдельных, не связанных между собой волокон.
Рис.5.53. Технологическая схема пневмомеханической прядильной машины
Разработка плана прядения
План прядения является основным документом прядильной фабрики, определяющим технологию производства пряжи. Он содержит основные данные, определяющие заправку машин всех переходов для выработки пряжи требуемой линейной плотности и качества. План прядения определяет производительность всех машин и их количество.
Составление плана прядения и выбор технологического оборудования проводят параллельно, так как технические возможности машины влияют на параметры плана прядения. С другой стороны, изменение отдельных параметров плана прядения иногда вызывает необходимость изменения сделанного ранее выбора машины. Разработка плана прядения проводится по следующим этапам (табл. 5.5):
1. Выбор и обоснование линейной плотности всех полуфабрикатов, числа сложений и вытяжек, осуществляемых на машинах всех переходов.
Выбор и обоснование коэффициентов крутки и величины крутки ровницы и пряжи.
Выбор и обоснование скорости выпуска продукта на всех машинах, а также частоты вращения веретен на ровничных машинах и веретен или камер на прядильных машинах.
Расчет теоретической производительности машины, выпуска, веретена.
Расчет коэффициентов полезного времени и коэффициента работающего оборудования.
Расчет теоретической производительности и нормы производительности одной машины и выпуска.
Чтобы обосновать каждый параметр плана прядения, необходимо пользоваться технической литературой, а также знать опыт работы передовых предприятий.
В зависимости от линейной плотности пряжи, ее назначения и требований, предъявляемых к ней, а также в зависимости от качества перерабатываемого хлопкового волокна выбирают современное высокопроизводительное оборудование, обеспечивающее наибольшую эффективность обработки волокна на всех переходах обработки.
Следует стремиться к наибольшему использованию мощностей вытяжных приборов, получению высокой производительности оборудования за счет увеличения частоты вращения выпускающих органов машин. Вытяжку и скорость оборудования следует выбирать в разумных пределах, при которых качество продукта и уровень обрывности в прядении обеспечивали бы экономное расходование сырья, максимальный выход пряжи из смеси хлопка, достаточно высокие зоны обслуживания основных производственных рабочих и, в конечном счете, минимальную себестоимость пряжи.
По теоретической производительности Рт машин каждого перехода определяют фактическую производительность, то есть норму производительности Рн отдельных машин с учетом технологических перерывов (снятие съема, перезаправка, ликвидация обрывов и т.п.) и перерывов по техническим причинам (чистка, смазка и мелкий ремонт с остановом машин), которые учитывает коэффициент полезного времени КПВ.
Норма производительности РН, кг/ч
РН = РТ × КПВ.
Оптимальным, то есть наилучшим планом прядения, является такой, при котором потребуются наименьшие капитальные затраты на оборудование, будут созданы наилучшие условия труда и обеспечено высокое качество продукции.
Лекция 8
МОТАЛЬНОЕ ПРОИЗВОДСТВО
Перемотка нитей и пряжи является связующим технологическим звеном между производством нитей и производством ткани или трикотажа.
Физико-механические свойства нитей должны быть такими, чтобы обеспечить соответствие требованиям, предъявляемым к изделиям, высокопроизводительную работу машин и станков ткацкого и трикотажного производства и непрерывность производственного процесса. Для того чтобы выполнить эти требования, необходимо нити, предназначенные для переработки, соответствующим образом подготовить.
Нити и пряжа поступают на ткацкую или трикотажную фабрику на различных паковках: на шпулях, бобинах, катушках, в мотках. Нити со шпуль и мотков перематывают на бобины. Нить на бобине должна иметь длину, достаточную для последующей переработки. Нити из химических волокон, как правило, поступают на бобинах.
Многие технологические процессы подготовки нитей к дальнейшей переработке относятся к категории сложных, так как характеризуются большим числом взаимосвязанных факторов.
Теоретические расчёты и опыт работы ткацких и трикотажных фабрик показывают, что от правильно выбранных технологических параметров зависит производительность оборудования и труда, а также и качество выпускаемой продукции. Аналитические расчёты параметров позволяют нормализовать технологические процессы и применить комплексную механизацию и автоматизацию.
Цели технологического процесса перематывания:
1. Создание паковки, обеспечивающей проведение последующей
технологической операции с наибольшей производительностью.
2. Контроль толщины нити с частичным удалением мелких пороков
пряжи (сор, шишки, узелки).
Сущность процесса перематывания заключается в последовательном наматывании на мотальную паковку под определенным натяжением пряжи с прядильных початков или мотков, соединяемой узлами.
Требования к процессу перематывания:
- не должны ухудшаться физико-механические свойства пряжи (упругое удлинение, прочность и крутка);
- строение намотки должно обеспечивать мягкость схода пряжи при сматывании;
- длина нити на паковке должна быть максимальной;
- натяжение пряжи должно быть равномерным на всех точках паковки;
- соединение концов пряжи при ликвидации обрывов и сходе ее с паковки должно осуществляться прочным узлом, легко проходящим через устройства машин и станков и не ухудшающим вид ткани;
- производительность процесса перематывания должна быть максимальной,
- отходы должны быть минимальными.
Фланцевая катушка
Она чаще всего представляет собой цилиндрическую прецизионную параллельную намотку на патронах с фланцами. Среднее расстояние между соседними нитями соответствует диаметру нити и по всему диаметру намотки постоянно, таким образом, получается катушка с максимальной удельной плотностью намотки нити. Боковые фланцы создают необходимую стабильность намотки. Угол подъема витков (α) при этом сравнительно мал, причем при увеличении диаметра намотки он уменьшается. На рис. 7.1 представлена фланцевая катушка.
Намотка нити на фланцевую катушку совершается со скоростью 800–1200 м/мин. Ход нитеводителя при этой намотке постоянный и величина его ограничивается расстоянием между фланцами. Максимальным диаметром фланцев определяется и максимальный диаметр намотки. Обычно фланцевые катушки используются при переработке нитей из натурального шелка.
Рис. 7.1. Фланцевая катушка: dн – диаметр нити; dо – диаметр патрона;
lб – длина бобины (высота намотки); α– угол подъёма витка.
Фланцевые катушки используются также в лентоткачестве, производстве швейных ниток, в лубяной и текстильно-галантерейной промышленности.
Диапазон линейных плотностей нитей, наматываемых на фланцевые катушки, составляет от 10 до 500 текс. Размеры катушек различны и зависят от цели применения. Обычно диаметр катушки не более180 мм, а длина – 220 мм. При этом может достигаться объем намотки, превышающий 4000 см3. Несмотря на большой объем и высокую удельную плотность намотки, применение этих катушек ограничено вследствие некоторых недостатков. Самый значительный из них заключается в том, что осевое сматывание возможно в большинстве случаев с применением вспомогательного средства в виде вращающегося нитеводителя.
Однофланцевая катушка
Данная катушка (рис. 7.2)обеспечивает прецизионную намотку на патроны, имеющие такое строение, что внутренняя торцевая поверхность намотки опирается на его коническую насадку. Внешняя торцевая поверхность однофланцевых катушек имеет форму конуса и проходит параллельно внутренней конусной торцевой поверхности патрона.
У однофланцевых катушек величина хода нитеводителя соответствует длине цилиндрической части намотки.
После каждого двойного хода нитеводителя происходит сдвиг хода в направлении к основанию. Плотность намотки на однофланцевых катушках примерно такая же, как и на конических бобинах. Однофланцевая катушка имеет особое значение для намотки синтетических швейных ниток.
Бобины крестовой намотки
Цилиндрическая бобина (рис. 7.3). В данных бобинах наматывание производится на цилиндрические патроны, а нити в каждом последующем слое постоянного диаметра перекрещиваются относительно друг друга под углом 9°45'. В зависимости от принципа привода угол подъема по всему диаметру намотки остается постоянным или же уменьшается. В последнем случае следует иметь в виду, что угол при наматывании на патрон диаметром d0 не должен быть слишком большим, так как в противном случае первый слой не будет держаться на патроне. Кроме того, цилиндрическая бобина крестовой намотки характеризуется тем, что ход нитеводителя по всему диаметру намотки остается постоянным, благодаря чему стороны бобины параллельны друг другу. Заметная на рис. 7.3 небольшая несимметричность (выпуклость) сторон возникает вследствие давления внутренних слоев намотки и для последующей переработки значения не имеет и не влияет на ее стабильность.
Рис. 7.2. Однофланцевая катушка
Рис. 7.3. Цилиндрическая бобина крестовой намотки
Вследствие значительного перекрещивания слоев нити внутри намотки образуются сравнительно большие пустоты, поэтому объем паковки с крестовой намоткой составляет 65 % объема катушек с цилиндрической параллельной намоткой.
Цилиндрические бобины крестовой намотки могут наматываться со скоростью нити до 1800 м/мин. В настоящее время скорость нити ограничивается лишь раскладкой нити вдоль бобины, верхний предел скорости, с точки зрения технологии, еще не определен.
Подобные бобины имеют почти универсальное применение. Они используются главным образом в кручении, где нить сматывается как тангенциально, так и вдоль оси. Цилиндрические бобины крестовой намотки с довольно постоянной плотностью намотки особенно пригодны для крашения, но для этого необходимы специальные перфорированные патроны (для циркуляции раствора).
Линейная плотность наматываемых нитей лежит обычно в диапазоне
6–60 текс для хлопка, вискозы и их смесей. Бобина средних размеров имеет диаметр не более 300 мм при длине около 145 мм, объем составляет около 5500 см3.
Плоская (солнечная) бобина. Плоская бобина в принципе представляет собой цилиндрическую бобину крестовой намотки, которая имеет очень небольшую высоту намотки при сравнительно большом диаметре (рис. 7.4).
Рис. 7.4. Плоская (солнечная) бобина крестовой намотки
Высота намотки составляет около 80 мм при диаметре примерно 220 мм. Скорость наматывания может составлять до 1200 м/мин.
Плоские бобины применяются преимущественно в прядении. Кроме того, их используют в производстве рыболовных сетей в качестве уточных нитей.
Коническая бобина. Вследствие постоянного возрастания скоростей сматывания нитей конические бобины приобрели большое значение. Они представляют собой особую форму бобин крестовой намотки, у которых образующие линии намотки формируют усеченный конус. Образующая линия намотки 1 (рис. 7.5) имеет такой же угол наклона (δ), что и патрон 2, благодаря этому намотка у большого и малого диаметров бобины имеет одинаковую удельную плотность.
Рис. 7.5. Коническая бобина крестовой намотки
Нити двух следующих друг за другом слоев сильно перекрещиваются. В соответствии с видом привода бобины угол подъема (α) в слоях нити либо постоянный, либо переменный. Угол наклона (половина угла конусности) стандартный и составляет 3°30'; 4°20' или 5°57'.
Конические бобины крестовой намотки обычно нарабатываются при скорости около 1200 м/мин, однако возможны также скорости до 1800 м/мин. Предельные скорости при такой форме бобины определяются принципом раскладки нити. Конические бобины применяют в крутильном, ткацком и трикотажном производстве. Как и в случае цилиндрических бобин крестовой намотки, здесь также требуются специальные патроны.
При высоте бобины около 150 мм диаметр намотки обычно не превышает 350 мм. Диапазон линейных плотностей наматываемых нитей из хлопковых, вискозных, шерстяных и химических волокон колеблется от 6 до 100 текс.
Биконическая бобина. Она намотана на конусообразный патрон с образующими в виде усеченного конуса. Оба торца бобины также имеют конусообразную форму (рис. 7.6).
Намотка на таких бобинах сама по себе стабильна, поэтому она применяется преимущественно для синтетических нитей. Наработка этих бобин требует особой конструкции механизма нитеводителя, обеспечивающего постоянное сокращение хода. Осевой привод бобины образует прецизионную намотку нити. Угол наклона образующей линии составляет 3°30'.
Рис. 7.6. Биконическая бобина
Двухконусные бобины крестовой намотки наматываются со скоростью до 1200 м/мин, при этом максимальный диаметр составляет 220 мм при высоте бобины 150 мм. Масса бобины – 1,5 кг, линейная плотность нитей от 2,2 до 22 текс.
Бобины такого вида применяются в основном при переработке химических нитей на круглотрикотажных машинах.
Вариоконическая бобина. Эта бобина представляет собой особую форму конической бобины крестовой намотки. У таких бобин угол наклона патрона и намотки неодинаковый. На рис. 7.7 видно, что намотка на патрон начинается при небольшом угле наклона, который возрастает с увеличением диаметра намотки. У основания конуса он составляет 9°15'.
![]() |
Рис. 7.7. Вариоконическая бобина
В результате вся намотка состоит из конусных слоев, которые образуются благодаря тому, что у основания конуса нити наматываются с большей удельной плотностью, нежели у его вершины.
Продолжения образующих линий всех конусных слоев сходятся в точке О. При сматывании нити в этом месте должен находиться ограничитель баллона. Таким способом обеспечиваются хорошие усло
|
|
История развития пистолетов-пулеметов: Предпосылкой для возникновения пистолетов-пулеметов послужила давняя тенденция тяготения винтовок...
Состав сооружений: решетки и песколовки: Решетки – это первое устройство в схеме очистных сооружений. Они представляют...
История создания датчика движения: Первый прибор для обнаружения движения был изобретен немецким физиком Генрихом Герцем...
Поперечные профили набережных и береговой полосы: На городских территориях берегоукрепление проектируют с учетом технических и экономических требований, но особое значение придают эстетическим...
© cyberpedia.su 2017-2024 - Не является автором материалов. Исключительное право сохранено за автором текста.
Если вы не хотите, чтобы данный материал был у нас на сайте, перейдите по ссылке: Нарушение авторских прав. Мы поможем в написании вашей работы!