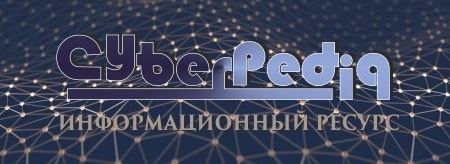
Состав сооружений: решетки и песколовки: Решетки – это первое устройство в схеме очистных сооружений. Они представляют...
Автоматическое растормаживание колес: Тормозные устройства колес предназначены для уменьшения длины пробега и улучшения маневрирования ВС при...
Топ:
Эволюция кровеносной системы позвоночных животных: Биологическая эволюция – необратимый процесс исторического развития живой природы...
Выпускная квалификационная работа: Основная часть ВКР, как правило, состоит из двух-трех глав, каждая из которых, в свою очередь...
История развития методов оптимизации: теорема Куна-Таккера, метод Лагранжа, роль выпуклости в оптимизации...
Интересное:
Подходы к решению темы фильма: Существует три основных типа исторического фильма, имеющих между собой много общего...
Берегоукрепление оползневых склонов: На прибрежных склонах основной причиной развития оползневых процессов является подмыв водами рек естественных склонов...
Наиболее распространенные виды рака: Раковая опухоль — это самостоятельное новообразование, которое может возникнуть и от повышенного давления...
Дисциплины:
![]() |
![]() |
5.00
из
|
Заказать работу |
Содержание книги
Поиск на нашем сайте
|
|
Нужные свойства наплавленного слоя обычно получают легированием, т.е. введением в его состав легирующих примесей. Существует много методов легирования Методы легирования и способы наплавки взаимосвязаны – выбранный способ наплавки диктует рациональный метод легирования, и, наоборот, эффективный метод легирования требует применения соответствующего способа наплавки. С другой стороны, основными признаками, по которым следует оценивать метод легирования, являются: точность (надежность) получения заданного химического состава наплавленного металла при возможных колебаниях режимов наплавки, однородность состава по объему наплавленного слоя, экономичность и удобство применения метода легирования.
Легировать сварочную ванну можно за счет обменных реакций между металлом и шлаком (окислами), через газовую среду и путем введения металлических добавок. Примером легирования за счет обменных реакций являются известные кремние- и марганцевовосстановительные процессы при сварке и наплавке под флюсами АН-348-А, ОСЦ-45, АН-60 и др. Легирование посредством газовой фазы имеет место при дуговой наплавке плавящимся электродом в атмосфере воздуха или азота, когда наплавленный металл содержит заметные количества азота. Благодаря этому повышается износостойкость хромистых сплавов или регулируется количество аустенитной фазы.
При ручной наплавке штучными электродами легирование осуществляется введением легирующих элементов в покрытие электрода или в электродный стержень. Применяют и комбинированный метод легирования, когда легирующие примеси вводят и в стержень, и в покрытие.
Материалы для наплавки
Покрытые электроды. Для наплавки различных деталей применяют электроды, предназначенные для сварки различных сталей и сплавов, и специальные электроды. Общие технические требования к металлическим электродам для дуговой сварки сталей и наплавки регламентированы ГОСТ 9466-60. ГОСТ 10051-62 предусматривает 25 типов электродов, например ЭН-14Г2Х, ЭН-У30Х28С4Н4 и др. В основу деления электродов на типы положен конкретный химический состав наплавленного металла. Каждому типу может соответствовать несколько марок электродов, отличающихся составом стержня, покрытия и сварочно-технологическими свойствами.
|
Плавленые флюсы. Для механизированной дуговой и электро-шлаковой наплавки наиболее широко применяют плавленые флюсы АН-348-А, ОСЦ-45, АН-60, АН-20, 48-ОФ-6, АН-26, АН-15М, АН-8, АН-25. Как и при сварке, качество наплавленного слоя во многих случаях определяется правильным выбором типа и состава флюса. Высококремнистые марганцевые флюсы АН-348-А, АН-348-АМ, ОСЦ-45, ОСЦ-45М и АН-60 обеспечивают хорошее формирование, малую склонность к образованию пор и удовлетворительную отделимость шлаковой корки на наплавке сталей.
Пемзовидный флюс АН-60 рекомендуется применять при наплавке электродной лентой, а также проволокой на больших скоростях. При наплавке среднелегированных и высоколегированных сталей и сплавов применение высококремнистых марганцевых флюсов нецелесообразно, так как они отличаются высокой окислительной способностью, чрезмерно легируют наплавленный металл кремнием и марганцем, образуют плохо отделяющуюся шлаковую корку. В этом случае применяют флюсы АН-26, АН-20, АН-28, АН-70, 48-ОФ-10.
Флюс АН-26 применяют для наплавки аустенитных хромоникелевых сплавов. Преимуществом этого флюса является отличное формирование наплавленного валика и малая склонность наплавленного слоя к порам; недостатком – сравнительно высокая окислительная способность, что приводит в ряде случаев к недопустимому снижению содержания титана и хрома в наплавленном слое и к появлению кристаллизационных трещин. Трещины можно устранить примесью к флюсу 3-4% алюминиевой лигатуры (80% Al и 20% Fe), которая обладает примерно одинаковой с флюсом плотностью.
|
Из низкокремнистых безмарганцевых флюсов для наплавки применяют флюс АН-20. Он обеспечивает высокую стабильность дуги, малую склонность к порам, хорошее формирование валиков. Его недостаток – относительно низкая температура плавления и малая вязкость, что затрудняет наплавку тел вращения малого диаметра, а также сравнительно высокая активность кремнезема, что приводит в ряде случаев к нежелательному обогащению металла кремнием, окислению легирующих элементов и ухудшению отделимости шлаковой корки. Шлаковая корка удовлетворительно отделяется при нагреве детали до температуры не свыше 4500С.
Флюс АН-28 рекомендуется для наплавки высокохромистых чугунов, он безмарганцевый и содержит мало кремнезема. Поэтому не происходит окисления легирующих элементов, достигается хорошая отделимость шлаковой корки. Недостатком флюса является плохое формирование валиков при содержании в наплавленном слое менее 1,0% Si, а также повышенная склонность к порам. Это связано с низким содержанием SiO2 и CaF2 во флюсе.
Наиболее химически нейтральны флюсы АН-70 и 48-ОФ-6, применяемые для наплавки высоколегированных сплавов с высоким содержанием хрома, вольфрама, ванадия и титана. При наплавке под этими флюсами велика опасность образования пор. Если наплавляют порошковой проволокой, то для устранения пор в сердечник обязательно вводят кремнефтористый натрий.
Керамические флюсы. Для наплавки интерес представляют легирующие керамические флюсы, которые позволяют при использовании стандартных и недефицитных проволок получать легированный наплавленный металл повышенной износостойкости. При наплавке под легирующим керамическим флюсом возможно опасное изменение химического состава наплавленного металла при изменении режимов наплавки. Однако этот недостаток относится в основном к флюсам с высоким содержанием легирующих элементов, поэтому высокое легирование наплавленного металла целесообразно осуществлять через проволоку. Наплавка же низколегированного металла возможна и при помощи слаболегирующих керамических флюсов.
Лабораторная разработка рецептур привела к созданию многочисленных марок керамических флюсов: ЖС-400, ЖС-500, ЖСН-1, ЖСН-2, КС-Х12Т, КС-3Х2В8, КС-Р18Б, АНК-18, АНК-19, ФК-45. Однако применение нашли только флюсы АНК-18 и АНК-19, изготовляемые промышленностью.
|
Проволока сплошного сечения. Во многих случаях для наплавки под флюсом и в защитных газах может быть использована стандартная сварочная проволока по ГОСТ 2246-70. Этот ГОСТ предусматривает поставку 6 марок низкоуглеродистой проволоки, 30 марок легированной и 41 марки высоколегированной проволоки.
Велик выбор проволок для восстановительной наплавки, наплавки промежуточных слоев (подслоев) и коррозионностойких сталей. Кроме сварочной проволоки для наплавки, часто используют пружинную проволоку, изготовленную из углеродистой стали с низким содержание серы и фосфора. На ремонтных предприятиях применяется углеродистая проволока по ГОСТ 9389-60, ГОСТ 1071-67 и ГОСТ 14963-69. Чаще всего используют проволоку, которая содержит 0,4-0,5%С, 0,17-0,37% Si и 0,35-0,60% Mn. Химический состав металла, наплавленного этой проволокой, зависит от типа флюса и режим наплавки; твердость наплавленного слоя НВ 200-250. Проволоку из пружинных сталей применяют для вибродуговой наплавки с охлаждением жидкостью. В этом случае твердость наплавленного слоя достигает HRC 50-55.
Порошковая проволока. Изготовление легированной проволоки – дорогой и сложный процесс. Общепринятая технология волочения с малыми переходами от одного диаметра к другому и многократным отжигом после почти каждого прохода связана с большими затратами средств и времени. Поэтому проволока, например, из быстрорежущей стали, примерно в 3 раза дороже, чем прокат, из которого ее изготовляют. Ряд углеродистых легированных сплавов, вообще невозможно изготовить в виде проволоки для автоматической наплавки.
Сравнительно просто задача решается с помощью порошковой проволоки, коротая состоит из оболочки – мягкой ленты (стальной, медной, никелевой, кобальтовой) и сердечника из порошков легирующих компонентов (ферропластов, чистых металлов, карбидов, боридов). В сердечник порошковой проволоки вводят также газо- и шлакообразующие вещества, раскислители и элементы, обладающие большим сродством к азоту. В этом случае наплавку можно вести без флюса и защитных газов. Такую проволоку называют самозащитной.
|
|
Автоматическое растормаживание колес: Тормозные устройства колес предназначены для уменьшения длины пробега и улучшения маневрирования ВС при...
Адаптации растений и животных к жизни в горах: Большое значение для жизни организмов в горах имеют степень расчленения, крутизна и экспозиционные различия склонов...
Архитектура электронного правительства: Единая архитектура – это методологический подход при создании системы управления государства, который строится...
Эмиссия газов от очистных сооружений канализации: В последние годы внимание мирового сообщества сосредоточено на экологических проблемах...
© cyberpedia.su 2017-2024 - Не является автором материалов. Исключительное право сохранено за автором текста.
Если вы не хотите, чтобы данный материал был у нас на сайте, перейдите по ссылке: Нарушение авторских прав. Мы поможем в написании вашей работы!