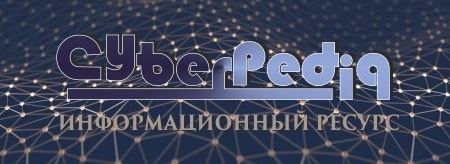
Двойное оплодотворение у цветковых растений: Оплодотворение - это процесс слияния мужской и женской половых клеток с образованием зиготы...
Состав сооружений: решетки и песколовки: Решетки – это первое устройство в схеме очистных сооружений. Они представляют...
Топ:
Основы обеспечения единства измерений: Обеспечение единства измерений - деятельность метрологических служб, направленная на достижение...
Отражение на счетах бухгалтерского учета процесса приобретения: Процесс заготовления представляет систему экономических событий, включающих приобретение организацией у поставщиков сырья...
Интересное:
Инженерная защита территорий, зданий и сооружений от опасных геологических процессов: Изучение оползневых явлений, оценка устойчивости склонов и проектирование противооползневых сооружений — актуальнейшие задачи, стоящие перед отечественными...
Что нужно делать при лейкемии: Прежде всего, необходимо выяснить, не страдаете ли вы каким-либо душевным недугом...
Лечение прогрессирующих форм рака: Одним из наиболее важных достижений экспериментальной химиотерапии опухолей, начатой в 60-х и реализованной в 70-х годах, является...
Дисциплины:
![]() |
![]() |
5.00
из
|
Заказать работу |
Содержание книги
Поиск на нашем сайте
|
|
Лекция 1
Введение
Углеродистые конструкционные стали
Углеродистыми конструкционными называют стали, содержащие 0,1-0,7% C.
Углерод определяет прочность сталей.
В сталях присутствует некоторое количество постоянных примесей. Количество постоянных примесей в углеродистых сталях не превышает 0,8% Mn, 0.35% Si, 0,04% P, 0,05% O2.
В металле могут находиться случайные примеси. Содержание этих элементов не превышает 0,3% Cu, 0,08% As, 0,3% Cr, 0,3% Ni.
Углеродистые конструкционные стали классифицируют по способу изготовления, по качеству и степени раскисления стали. В сварочной технике их классифицируют также и по содержанию углерода.
Углеродистую конструкционную сталь применяют для изготовления сварных конструкций в основном:
-в состоянии поставки (горячекатаном);
-в меньшем объеме после термообработки (нормализации)
- в еще меньшем – в состоянии после термического улучшения (после закалки и отпуска).
В сварочной технике в зависимости от содержания углерода углеродистые конструкционные стали условно разделяются на три группы: низкоуглеродистые, среднеуглеродистые и высокоуглеродистые.
Технология сварки этих сталей различна.
Низкоуглеродистые конструкционные стали.
К низкоуглеродистым конструкционным сталям, по принятой в сварочной технике классификации относят стали с содержанием до 0.25% C.
Особенности сварки.
Низкоуглеродистые стали относятся к числу хорошо сваривающихся металлов.
Для этих сталей технологию сварки выбирают из условий обеспечения комплекса требований, главные из которых:
- достижение равнопрочности сварного соединения с основным металлом;
- отсутствие дефектов в сварном соединении.
|
Для этого механические свойства металла шва, околошовной зоны и сварного соединения в целом должны быть не ниже минимальных механических свойств основного металла.(В ряде случаев допускается снижение требований к отдельным показателям механических свойств сварного соединения.)
В металле швов не должно быть:
- трещин, непроваров, пор, подрезов и других дефектов,
-сварное соединение должно иметь требуемые по чертежу размеры и форму.
-сварное соединение должно быть стойким против перехода против перехода в хрупкое состояни.
- в некоторых случаях дополнительно вводят требования высокой коррозионной стойкости сварных соединений, их работоспособности в условиях вибрационных и ударных нагрузок, повышенных или пониженных температур и другие специальные требования.
Механические свойства металла шва и сварного соединения зависят от его структуры, определяемой химическим составом, условиями остывания сварной конструкции и термообработкой.
При сварке низкоуглеродистой стали металл шва незначительно отличается по составу от основного металла. Это отличие в основном сводится к снижению содержания в металле шва углерода и повышению содержания марганца и кремния.
Снижение прочности металла шва полностью компенсируется за счет увеличения скорости его остывания и легирования металла через проволоку, покрытие или флюс марганцем и кремнием.
Изменение скорости остывания вызывает изменение количества и строения перлитной фазы, что существенно сказывается на механических свойствах металла шва.
Увеличение скорости остывания приводит к возрастанию предела текучести и временного сопротивления и к снижению относительного удлинения и относительного сужения металла шва.
Изменяется также ударная вязкость металла шва. Увеличение скорости остывания приводит к уменьшению ударной вязкости при комнатной температуре.
Сварки низкоуглеродистых конструкционных сталей. Технологические режимы и приемы
|
Сварка под флюсом.
Получение равнопрочных сварных соединений при сварке низкоуглеродистой стали под флюсом достигается за счет применения высококремнистых марганцев флюсов АН-348-А, ОСЦ-45 и низкоуглеродистой сварочной проволоки Св-08 и Св-08А.
При сварке особо ответственных сварных конструкций эти флюсы применяются в сочетании со сварочной проволокой Св-08ГА.
Основной объем работ по автоматической сварке низкоуглеродистой сварке низкоуглеродистой стали выполняется сварочной проволокой диаметром 4 и 5 мм.
Для автоматической сварки тонкого металла используется проволока диаметром 0,8-3 мм. Полуавтоматическая сварка выполняется проволокой диаметром 0,8-2 мм.
Сварка в защитных газах.
Сварку низкоуглеродистых сталей проводят в углекислом газе.
Для автоматической и полуавтоматической сварки плавящимся электродом в углекислом газе металла толщиной 0,8-3 мм и угловых швов с катетами 1-4 мм при любом пространственном положении шва применяют сварочную проволоку диаметром 0,5-1,4 мм.
Сварку проволокой диаметром 1,4-4 мм ведут в нижнем положении и применяют для металла средних толщин, а также для заварки дефектов литья.
Для обеспечения необходимых механических свойств металла шва и высокой стойкости его против кристаллизационных трещин и пор при сварке кипящей и спокойной сталей применяют сварочные проволоки Св-08ГС или Св-08Г2С, легированные кремнием и марганцем.
При сварке спокойной низкоуглеродистых сталей с содержанием углерода, приближающимся к верхнему пределу (0,21-0,25%), следует применить сварочную проволоку Св-08ГС или СвГ2С.
Серьезное влияние на свойства металла шва оказывает качество углекислого газа. Повышенное содержание в нем водяных паров способствует образованию пор.
Дополнительное легирование проволок для сварки в углекислом газе сильными элементами-раскислителями (титаном, алюминием, цирконием и др.) приводит к уменьшению разбрызгивания при сварке.
Устойчивое горение дуги при сварке плавящимся электродом в углекислом газе достигается при плотности тока свыше 100 А/мм2.
При сварке в положениях, отличных от нижнего, применяют только электродную проволоку диаметром 0,5-1,4 мм.
Значения тока и напряжение дуги должны быть минимальными (17-21 В), однако обеспечивающими устойчивое горение дуги. Увеличение напряжение дуги приводит к резкому возрастанию процесса разбрызгивания, особенно при сварке горизонтальных швов.
|
Электрошлаковая сварка.
Электрошлаковую сварку применяют при изготовлении конструкций из низкоуглеродистых сталей большой толщины.
Получение равнопрочного соединения при электрошлаковой сварке низкоуглеродистой стали достигается за счет легирования металла шва через проволоку в основном с повышенным содержанием марганца (Св-10Г2), а иногда также и кремния (Св-08ГС).
Для низкоуглеродистой стали содержанием до 0,18% С равнопрочность металла шва с основным металлом достигается при сварке проволокой Св-08ГА. Можно вести сварку двумя и тремя проволоками разного состава. Обычно применяют флюсы АН-8 или ФЦ-7.
При электрошлаковой сварке (толщина металла более 60мм, флюс АН-8) обеспечивается равнопрочность металла шва и сварного соединения в состоянии как после сварки, так и после термообработки.
Ударная вязкость металла шва и участка перегрева зоны в состоянии после сварки при комнатной температуре находится на нижнем уровне требований, предъявляемых к основному металлу, а при температуре ниже комнатной обычно не удовлетворяет требованиям, предъявляемым к основному металлу. Это связанно с образованием крупнозернистой видманштеттовой структуры. Металл с видманштеттовой структурой обладает пониженной ударной вязкостью и малой стойкостью против перехода в хрупкое состояние
При небольшом количестве закалочных структур их влияние на механические свойства сварных соединений не значительно в связи с равномерным и дезориентированным расположением этих составляющих в мягкой ферритной основе.
Однако при увеличении доли таких структур в шве и околошовной зоне пластичность металла и его стойкость против хрупкого разрушения резко ухудшается.
Дополнительное легирование стали марганцем, кремнием и другими элементами способствует образованию в сварных соединениях закалочных структур.
Режим сварки большинства низколегированных сталей ограничивается более узкими пределами, чем при сварке низкоуглеродистой стали.
|
В ряде случаев, например при микролегировании ванадием, ванадием и азотом, а также другими элементами, склонность низколегированной стали к росту зерна в околошовной зоне при сварке незначительна.
Обеспечение равнопрочности металла шва с основным металлом достигается в основном за счет легирования его элементами, переходящими из основного металла.
Иногда для повышения прочности металл шва дополнительно легируют через сварочную проволоку.
Стойкость металла шва против кристаллизационных трещин при сварке низколегированных сталей несколько ниже, чем низкоуглеродистых, в связи с усилением отрицательного влияния углерода некоторыми легирующими элементами, например кремнием.
Повышение стойкости против образования трещин достигается снижением содержания в шве углерода, серы и некоторых других элементов за счет применения сварочной проволоки с пониженным содержанием указанных элементов, а также выбором соответствующей технологии сварки и рационально конструкции изделия.
Сварка двухслойных сталей.
Двухслойные стали применяются в качестве коррозионностойких в химическом и нефтехимическом производстве. Для облицовочного слоя этих сталей применяют аустенитные стали Х18Н10Т, Х18Н12Т, Х17Н13М2Т, Х23Н28М3Д3Т и хромистые типа 0Х13.Основной слой изготовляют из углеродистых сталей типа ВСт3, а также из качественных, например, 10, 15ХМ. Облицовочный высоколегированный слой расположен внутри корпусной аппаратуры или трубы.
Сварку двухслойных сталей производят раздельно. Основной слой сваривают по обычной для данной конструкционной стали технологии, а коррозионностойкий слой – в один или несколько проходов в зависимости от его толщины.
Чтобы обеспечить минимальное разбавление аустенитного и неаустенитного металлов при переходе от основного слоя к облицовочному и наоборот, сварку производят с применением мер, обеспечивающих наименьшее проплавление нижележащего слоя. К таким мерам относятся: сварка сдвоенным или ленточным электродом, сварка на спуск, применение пемзовидного флюса, сварка постоянным током прямой полярности.
При сварке толстого биметалла с целью предотвращения образования в переходной зоне металла с пониженной пластичнростью проволокой из низкоуглеродистого армко-железа или Св – 08 в сочетании с сильно окисленным флюсом, аустенитной проволокой Св- 10Х16Н25АМ6 или электродами типа ЭА-3М6.
Аппаратуру из двухслойной стали термически не обрабатывают. При необходимости термообработку выполняют с учетом обеспечения требуемой коррозионной стойкости облицовочного слоя.
Лекция 9.
Сварка под флюсом.
Главное преимущество - возможность выполнения сварки без предварительного подогрева свариваемых кромок благодаря тому, что дуга горит во флюсовом пузыре и потери теплоты на излучение минимальны. Кромки подогревают для начала сварки.
|
Сварку меди под флюсом производят постоянным током обратной полярности с применением плавленных флюсов АН-20, АН-26, а также АН-348-А и ОСЦ-45 (для металла толщиной до 20 мм), а также керамического флюса ЖМ-1 и сварочной проволоки М1 и М2. В отдельных случаях используют сварочную проволоку из бронзы марки Бр. КМц3-1. Швы, сваренные этой проволокой, обладают высокой прочностью, однако имеют пониженную теплопроводность и электропроводность.
Сварку стыковых соединений выполняют без разделки кромок и без зазора, за один проход с полным проваром. При толщине металла более 15 мм рекомендуется применять сдвоенный электрод. Такое расположение электродов обеспечивает полное проплавление стыкуемых кромок, улучшает формирование швов и при общей ванне расплавленного металла позволяет избежать образования в сварном шве пор, шлаковых включений и кристаллизационных трещин.
При сварке меди М1 толщиной 20-30мм сварочной проволокой такой же марки под флюсом АН-26 металл шва характеризуется такими свойствами: sв= 170¸ 190МПа, sт= 80¸ 90 МПа, d = 38¸ 42%.
Сварка в защитных газах.
Сварку меди выполняют неплавящимся и плавящимся электродом. В качестве защитных газов для сварки меди применяют аргон, гелий, азот или их смеси. Возможна сварка меди в среде водорода. Наибольшее распространение получила сварка неплавящимся вольфрамовым электродом в аргоне чистоты марок А и Б по ГОСТ 10157-62. Металл толщиной более 4 мм сваривают с предварительным подогревом до температуры 8000 С. Чем больше толщина металла, тем выше температура предварительного подогрева. В качестве присадочного металла применяют сварочную проволоку из хромистой бронзы Бр. Х07 или бронзы Бр. КМц3-1. Основной и присадочный металлы очищают травлением в растворе, состоящем из 75 см3/л серной кислоты и 1 см3/л соляной кислоты.
Для повышения качества шва при сварке в среде защитных газов применяют флюсы на основе борного ангидрида с добавками раскислителей (алюминиевый порошок, феррофосфор, ферромарганец).
Сварку плавящимся электродом выполняют постоянным током обратной полярности. Широкое распространение для меди толщиной 4-5 мм получает многослойная полуавтоматическая сварка проволокой малого диаметра (1,2 – 2,4 мм). Сила сварочного тока достигает 400 А. Металл толщиной до 10 мм можно сваривать лишь с подогревом в начале шва. Детали большей толщины сваривают с начальным и сопутствующим подогревом. При сварке используют проволоку из бронзы Бр. КМц3-1.
Сварка сжатой дугой.
Это эффективный способ соединения деталей из меди больших толщин (30-40 мм), что обусловлено возможностью введения в сварочную ванну тепловых потоков весьма большой величины без ухудшения условий формирования сварного шва и нарушения стабильности горения дуги.
Сварку осуществляют без разделки кромок с двух сторон.
Электроннолучевая сварка.
Применяется при изготовлении электровакуумных приборов. Это обеспечивает высокие физико-механические свойства соединений.
Электроннолучевая сварка связана с определенными затруднениями, это интенсивное испарение металла в вакууме и необходимость значительного тепловложения из-за высокой теплопроводности.
При повышении определенного значения удельной мощности в пятне нагрева получить удовлетворительное качество сварного соединения меди не удается. Поэтому разработана специальная техника сварки. Так, сварку меди толщиной до 2-3мм выполняют неострофокусированным пучком, или перефокусированным, т.е. расположением фокуса пучка несколько выше уровня поверхности изделия.
Сварка разнородных сталей
Одним из путей экономии является изготовление установок, машин и механизмов комбинированными. Такое изготовление вполне возможно, так, как во многих случаях работает не вся конструкция, а лишь отдельные ее узлы или детали. Остальная часть конструкции может быть изготовлена из среднелегированной, низколегированной или даже обычной углеродистой стали.
В комбинированной конструкции необходимо соединять между собой отдельные ее части. При этом необходимо сваривать между собой стали, существенно отличающиеся друг от друга своими физико-химическими свойствами, в связи с чем трудно получить качественное соединение.
Сварка высоколегированных сталей со средне- или низколегированными углеродистыми явилась трудной задачей.
Первая трудность заключается в том, что в процессе изготовления или при его эксплуатации в шве часто образуются трещины, которые проходят по его середине или у границы сплавления.
Вторая трудность обусловлена тем, что в зоне их сплавления может происходить изменение структуры с образованием прослоек, существенно отличающихся от структуры сплавляемых металлов. В результате возможно преждевременное (аварийное) разрушение ответственной конструкции.
Сварные соединения разнородных сталей, в которых структура не изменяется до границы сплавления, являются вполне технологичными и могут надежно работать во всех тех условиях, для которых они предназначены.
Сварка разнородных сталей затруднена еще и тем, что они в подавляющем большинстве случаев отличаются друг от друга величиной коэффициентов линейного расширения. В силу этого сварные соединения таких сталей остаются напряженными даже после их термообработки. В сварных соединениях разнородных сталей, подвергнутых термообработке в зоне сплавления создается резкое изменение (скачок) напряжений. Поэтому сварные соединения разнородных сталей нецелесообразно подвергать термообработке даже в случаях, когда она желательна по другим соображениям. Отмеченные трудности обусловили особенности сварки разнородных сталей. Возникновение трещин в швах сварных соединений разнородных сталей обусловлено появлением в них мартенситной структуры, снижающей пластичность металла. Швы с мартенситной структурой образуются, прежде всего, при чрезмерном разбавлении высоколегированного металла менее легированным, что имеет место в случае большого проплавления свариваемого металла. Непластичные структуры могут образовываться также вследствие того, что в зоне сплавления металлов, сильно отличающихся друг от друга по химическому составу, неизбежно возникновение переходного слоя. В последнем концентрация элементов постепенно изменяется от содержания их в одном из сплавляемых металлов до их содержания в другом. Увеличение этого слоя до определенной ширины и приводит к появлению трещин, наблюдаемых у границы сплавления.
Накоплено не мало сведений о природе и механизме образования в металле шва трещин. Поэтому предотвращение их возникновения не вызывает особых затруднений. Значительно труднее получить сварные соединения разнородных сталей, стойкие против образований в зоне сплавления структурной неоднородности.
Появление структурной неоднородности и степень ее развития определяются всеми факторами, способствующими перемещению углерода из менее легированного металла в более лигированный. Решающие из них: последующий нагрев сварного соединения до температур, вызывающих заметную миграцию углерода; время выдержки сварного соединения при этих температурах и химический состав сплавляемых металлов, в особенности содержание в них углерода и карбидообразующих элементов.
В состоянии после сварки, особенно в соединении с однослойным швом, если даже он выполнен на довольно мощном режиме, в зоне сплавления не обнаруживается перераспределения углерода, характерного для структурной неоднородности. В таких соединениях структурная неоднородность не обнаруживается и тогда, когда менее лигированной сталью в них является обычная углеродистая сталь Ст3, которая совершенно не содержит элементов, связывающих углерод в прочные карбиды.
Структурная неоднородность в зоне сплавления разнородных сталей возникает лишь при нагреве сварного соединения до температуры 3500 С. Однако существенное развитие она получает при более высоких температурах (около 5000С). Наиболее интенсивно развивается эта неоднородность при температуре 600-8000С. До температуры 3500С характерной структурной неоднородности не наблюдается даже в случае применения в качестве менее легированного металла обычной низкоуглеродистой стали ВСт3.
Увеличение продолжительности выдержки также усиливает степень структурной неоднородности, однако не столь интенсивно, как повышение температуры. После длительной выдержки с дальнейшим увеличением ее длительности интенсивность развития структурной неоднородности снижается. Особенно сильно она снижается при температурах ниже 6000С. Вместе с тем при нагреве до температур выше 6000С структурная неоднородность получает заметное развитие даже при выдержках, исчисляемых минутами. Термообработка сварных соединений разнородных сталей нежелательна также из-за возможного при этом образования в зоне сплавления характерной структурной неоднородности.
Если в высоколегированном металле отсутствуют сильные карбидообразующие элементы, структурная неоднородность не образуется даже в зоне сплавления его обычной углеродистой сталью. Наличие же карбидообразующих элементов вызывает появление этой неоднородности и в том случае, если менее легированный металл является технически чистым железом. Образуется она также тогда, когда высоколегированный металл содержит значительно больше углерода, чем менее легированный. Последнее объясняется тем, что перемещение углерода в зоне сплавления разнородных сталей вызывается различием не общего содержания углерода в наплавленном металле, а различием его термодинамических активностей.
Влияние карбидообразующих элементов на образование структурной неоднородности в зоне сплавления разнородных сталей зависит от типа элемента и его содержания, причем влияние типа элемента сказывается сильнее, чем его количества. Интенсивность влияния карбидообразующего элемента усиливается с возрастанием его сродства к углероду и располагается в следующей последовательности: Fe, Mn, Cr, W, V, Nb, Ti. Такая последовательность имеет место лишь при выражении концентрации карбидообразующего элемента в атомах процентах, а не процентах по массе. Поэтому принято считать, что перемещение углерода в зоне сплавления разнородных сталей определяется не общим содержанием карбидообразующих элементов, а свободным их количеством.
Развитию структурной неоднородности в зоне сплавления разнородных сталей способствуют также напряжения, вызываемые различием коэффициентов линейного расширения сплавляемых металлов.
Разнородные стали необходимо сваривать с минимальным их проваром. Во многих случаях даже при минимальном проваре для обеспечения допустимого разбавления наплавленного металла необходимо применять соответствующие сварочные материалы. Например, неаустенитные стали с аустенитными не следует сваривать электродами типа ЭА-1, так как они обеспечивают получение наплавленного металла, содержащего 18% Cr и лишь 8% Ni, в связи с чем он обладает весьма малым запасом аустенитности. В данном случае целесообразно применять электроды, обеспечивающие металл шва с более высоким запасом аустенитности.
Для предотвращения трещин, разнородные стали необходимо сваривать так, чтобы ширина переходного слоя была минимальной. Это достигается снижением силы сварочного тока и напряжения дуги, а также увеличением скорости сварки. Что касается предупреждения образования структурной неоднородности в зоне сплавления разнородных сталей, то общим в решении этой задачи является выполнение сварки с применением мер, снижающих разницу темодинамической активности углерода в сплавляемых металлах. Одним из вариантов практического решения указанной задачи может быть применение в качестве менее легированного металла такой низко- или среднелегированной стали, которая содержит достаточное количество энергичных карбидообразующих элементов. В такой стали углерод будет связан в стойкие карбиды, и, следовательно, существенно уменьшится вероятность перемещения его в более легированную сталь.
Применение сварочных материалов, способствующих получению аустенитного металла шва с высоким содержание никеля, который, как показала практика, обеспечивает вполне стабильную зону сплавления. Преимущество высоколегированного металла состоит также в близости низко- и среднелегированных сталей. В связи с тем, что никель является дефицитным и довольно дорогим элементом, а также элементом, способствующим образованию горячих трещин в сварных швах, в металле последних целесообразно иметь лишь то количество никеля, которое необходимо для предупреждения образования структурной неоднородности в зоне сплавления с менее легированной сталью.
Необходимая концентрация никеля в металле шва существенно зависит от температуры нагрева сварного соединения. Следовательно, эта концентрация зависит от класса используемой в данном сварном соединении менее легированной стали, который и определяет допустимую температуру его эксплуатации. Это обстоятельство позволяет дифференцировать содержание никеля в металле шва и тем самым более экономно его расходовать.
Сварные соединения разнородных сталей делятся на четыре группы: 1) соединения, работающие при температурах до 3500С (содержат в качестве менее легированной стали обыкновенную низкоуглеродистую сталь, допустимая температура эксплуатации которой не превышает 3500С); 2) соединения, работающие при температурах 350-4500С (с качественными углеродистыми и обычными низколегированными сталями); 3) соединения, работающие при температурах 450-5500С (с низко- или среднелегированными хромомолибденовыми сталями); 4) соединения, работающие при температурах выше5500С (с низко- или среднелегированными хромомолибденованадиевыми сталями).
Содержание никеля в металле шва, необходимое для предотвращения структурной неоднородности в зоне сплавления его с менее легированной сталью, в каждой из указанных групп существенно отличается. Для сварных соединений первой группы оно не превышает 10%. В соединениях второй группы никеля в металле шва должно быть около 19%, третьей – 31% и четвертой – 47%. Сильное изменение требуемого содержания никеля в металле шва обусловливает целесообразность применения для каждой из указанных групп сварных соединений своих сварочных материалов. Эти материалы должны отличаться прежде всего содержанием никеля.
Стандартные сварочные проволоки могут быть применены для сварных соединений первой группы. Для соединений второй, третьей и четвертой групп необходимы новые сварочные материалы. В качестве одного из вариантов их могу быть использованы проволоки ЭП622, ЭП673 и ЭП606. Первая из этих проволок предназначена для сварки конструкций, эксплуатируемых при температурах 350-4500С, вторая – 450-5500С и третья – выше 5500С. Каждая из этих проволок может быть использована при изготовлении конструкций, работающих при более низких температурах.
При сварке разнородных сталей указанными проволоками под флюсами АН-26 или АН-15 получается металл шва, стойкий против образования кристаллизационных трещин. Он также не склонен к сигматизации, сравнительно мало охрупчивается при старении и обладает требуемыми механическими свойствами как в обычных условиях, так и в условиях длительного воздействия высоких температур. Металл зоны сплавления в соединениях, выполненных этими проволоками, обладает вполне стабильной структурой и свойствами, если они содержат менее легированную сталь и эксплуатируются при температуре, соответствующей той группе, для которой предназначена используемая проволока.
Ручную сварку разнородных сталей в соединениях первой группы можно производить существующими электродами. Не следует применять электроды типа Эа-1. Для соединений второй, третьей и четвертой группы рекомендуются электроды АНЖР-1, АНЖР-2 и АНЖР-3.
Для заварки дефектов в деталях энергетического оборудования, которое можно отнести к сварным соединениям четвертой группы, ЦНИИТМАШ предлагает применять электроды ЦТ-36, а ЦКТИ им. И.И. Ползунова и Ленинградский металлический завод – электроды ЦТ-28.
Лекция 11
Электрошлаковая сварка.
Электрошлаковая сварка алюминия длительное время не удавалась. Это было обусловлено низкой температурой кристаллизации алюминия, что вынуждает применять легкоплавкие, обычно электропроводные шлаки.
Электрошлаковым способом сваривают металл толщиной 50-200 мм. скорость сварки независимо от толщины металла составляет 6-8 м/ч.
При электрошлаковой сварке имеются благоприятные металлургические факторы, способствующие получению высококачественных сварных соединений – направление кристаллизации снизу вверх, электрошлаковое рафинирование металла шва. Электрошлаковым способом сваривают массивные заготовки прямоугольного и криволинейного сечения, фасонные пресспрофили, пакеты тонких пластин.
Сварка в инертных газах.
Алюминий и его сплавы сваривают неплавящимся вольфрамовым электродом или плавящимся электродом. Сварку вольфрамовым электродом в зависимости от конструкции соединения ведут с присадочной проволокой либо без нее. Состав электродной или присадочной проволоки близок к составу свариваемого металла. В качестве защитного газа применяют аргон марок А и Б, смесь аргона и гелия и гелий повышенной чистоты, содержащий не менее 99,8% основного газа.
Электроннолучевая сварка.
Этот вид сварки обладает рядом преимуществ: высока плотность энергии благодаря малому диаметру луча и его стабильности, малое тепловложение и относительно высокая скорость процесса. В результате достигается минимальное разупрочнение металла в околошовной зоне. Кроме того, в вакууме порядка 1 · 10 -4 мм. рт. ст. сохраняется высокая чистота окружающей среды на два порядка выше, чем, например, при дуговой сварке в аргоне марки А.
Электроннолучевая сварка обеспечивает минимальное коробление изделия вследствие малой ширины шва. Поверхности алюминиевых деталей под электроннолучевую сварку следует подготавливать травлением с последующим шабрением кромок непосредственно перед загрузкой заготовки в вакуумную камеру. В отличие от всех других методов сварки плавлением электроннолучевую сварку алюминиевых сплавов благодаря малому объему сварочной ванны и узкому шву можно выполнять как на весу, так и на подкладках. Сварку сплавов, содержащих легко испаряющиеся элементы, предпочтительнее выполнять на весу, так как в этом случае обеспечивается удаление паров металла и повышается плотность сварных швов.
Погонная энергия при электроннолучевой сварке меньше, чем при дуговой. Так, например, при сварке сплава АМц6 толщиной 10 мм (ускоряющее напряжение 20 кВ, сила тока луча 140 мА, скорость сварки 72 м/ч) погонная энергия в 10 раз меньше, чем при аргонно-дуговой (напряжение дуги 18В, сила тока 480 А, скорость сварки 12 м/ч). Механические свойства соединений, полученных электроннолучевой сваркой, либо превышают, либо равны соответствующим свойствам соединений, полученных аргонно-дуговой сваркой.
Электроннолучевая сварка позволяет выполнять соединения различных типов: стыковые, угловые (тавровые и нахлесточные), с отбортовкой кромок.
Лекция 12
Сварка титановых сплавов
Титан и титановые сплавы применяют в химическом машиностроении, авиапромышленности и др. отраслях производства.
Весьма чистый титан находит ограниченное применение, например, в радиоэлектронике.
Технический титан содержит примеси внедрения, в том числе газы – кислород, азот и водород, которые повышают прочность и снижают пластичность и вязкость металла. В сварных швах они вызывают образование холодных трещин.
Свариваемый технический титан должен содержать ограниченное количество примесей – газов.
Легирование титана позволяет получать свариваемые сплавы, обладающие повышенной прочностью при достаточной пластичности и вязкости.
Легирующие элементы по-разному оказывают влияние на фазовый состав сплавов на основе титана. Такие элементы как алюминий, олово, цирконий не имеют кристаллического строения технического титана, для которого при нормальной температуре характерна α-фаза. Поэтому они называются α – стабилизаторами. Большая группа элементов- марганец, молибден, ванадий, хром – при давлении в титан может сохранить при нормальной температуре высокотемпературную β-фазу. Изменяя количество таких β-стабилизаторов, можно получить двухфазный (α + β)- сплав или даже однофазный β-сплав. Сплав последнего типа получается при высоком содержании элементов β- стабилизаторов.
Сварка технического титана и однофазных α-сплавов.
Большая химическая активность титана и особенно в расплавленном состоянии по отношению к газам затрудняет сварку этого металла. Обязательным условием получения качественного соединения является надежная защита от газов атмосферы не только сварочной ванны, но и остывающих участков металла шва. Необходимо также тщательно защищать и обратную сторону шва, даже в том числе, если слои металла не расплавлялись, а только нагревались выше этой температуры. Дополнительные затруднения при сварке создает большая склонность титана к росту зерен. Низкая теплопроводность титана способствует увеличению времени пребывания шва и околошовной зоны при высоких температурах. Чтобы преодолеть указанное затруднение, сварку выполняют при минимально возможной погонной энергии. На качество сварных соединений титана оказывает влияние состояние поверхности кромок и присадочного металла. При неполном удалении пленки окислов на поверхности титана может сохраниться альфированный слой.
Наиболее частыми дефектами сварных швов являются поры и холодные трещины. В сварных титановых швах механизм образования пор, располагающихся по оси шва и у границ сплавления, практически такой же, как и для стали. Возбудителями пор являются газы и среди них в первую очередь водород. Известны пути борьбы с пористостью в титановых швах. В первую очередь необходимо обеспечить требуемую чистоту основного металла и сварочных материалов, сварку выполнять на оптимальных режимах.
Широкое применение нашел способ сварки титана под флюсом (содержащим фториды щелочных и щелочно-земельных металлов), разработанный в ИЭС им. Е.О. Патона. При таком способе сварки связывание водорода в зоне дуги во фтористый водород полностью исключает возможность образования пор в металле шва.
Холодные трещины возникают при пониженной пластичности разных его участков. К этому приводит чрезмерное содержание примесей внедрения – газов. Трещины такого типа могут возникнуть сразу же после сварки, а также в результате процесса замедленного разрушения. Причиной такого процесса является выделение водорода и возникновение в шве больших внутренних напряжений.
Для соединения деталей из титана и его сплавов применяют дуговую сварку неплавящимся и плавящимся электродами с защитой инертным газом, дуговую сварку под флюсом и электрошлаковую сварку, а в последнее время – и новые способы: электроннолучевую и сварку сжатой дугой, в том числе микроплазменную.
Характерно применение специальных приспособлений, позволяющих защитить зону сварки, остывающие участки шва и околошовную зону, а также корень шва. К ним относятся удлиненные насадки с отверстиями, защитные козырьки, ползушки, обеспечивающие защиту металла шва и участков основного металла, подвергнутых нагреву.
Защиту корня шва можно осуществить несколькими способами: при небольшой протяженности стыковых соединений – плотным поджатием кромок свариваемых деталей к медной или стальной подкладке; подачей инертного газа в подкладку с отверстиями или изготовленную из пористого материала. При сварке сосудов или труб инертный газ пропускать внутрь изделия.
Для сварки находят применение герметичные камеры с контролируемой атмосферой инертного газа. Сварку в камерах можно выполнять автоматами или вручную. Камеры для ручной сварки имеют окна, в которых закреплены резиновые перчатки. Оператор выполняет сварку, продевая руки в перчатки и находясь вне камеры.
Перед заполнением камеры инертным газом при небольшом избыточном давлении (до 0,1 ат) ее вакуумируют до разряжения 1 х 10-3 мм рт. Ст. Сварку в камерах выполняют на режимах, аналогичных тем, которые используют при сварке в среде инертного газа на воздухе.
Важным условием предотвращения охрупчивания металла шва и околошов
|
|
Биохимия спиртового брожения: Основу технологии получения пива составляет спиртовое брожение, - при котором сахар превращается...
История развития пистолетов-пулеметов: Предпосылкой для возникновения пистолетов-пулеметов послужила давняя тенденция тяготения винтовок...
Адаптации растений и животных к жизни в горах: Большое значение для жизни организмов в горах имеют степень расчленения, крутизна и экспозиционные различия склонов...
Поперечные профили набережных и береговой полосы: На городских территориях берегоукрепление проектируют с учетом технических и экономических требований, но особое значение придают эстетическим...
© cyberpedia.su 2017-2024 - Не является автором материалов. Исключительное право сохранено за автором текста.
Если вы не хотите, чтобы данный материал был у нас на сайте, перейдите по ссылке: Нарушение авторских прав. Мы поможем в написании вашей работы!