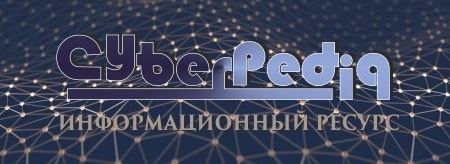
Археология об основании Рима: Новые раскопки проясняют и такой острый дискуссионный вопрос, как дата самого возникновения Рима...
Механическое удерживание земляных масс: Механическое удерживание земляных масс на склоне обеспечивают контрфорсными сооружениями различных конструкций...
Топ:
Техника безопасности при работе на пароконвектомате: К обслуживанию пароконвектомата допускаются лица, прошедшие технический минимум по эксплуатации оборудования...
Оснащения врачебно-сестринской бригады.
Отражение на счетах бухгалтерского учета процесса приобретения: Процесс заготовления представляет систему экономических событий, включающих приобретение организацией у поставщиков сырья...
Интересное:
Подходы к решению темы фильма: Существует три основных типа исторического фильма, имеющих между собой много общего...
Уполаживание и террасирование склонов: Если глубина оврага более 5 м необходимо устройство берм. Варианты использования оврагов для градостроительных целей...
Отражение на счетах бухгалтерского учета процесса приобретения: Процесс заготовления представляет систему экономических событий, включающих приобретение организацией у поставщиков сырья...
Дисциплины:
![]() |
![]() |
5.00
из
|
Заказать работу |
Содержание книги
Поиск на нашем сайте
|
|
Дайте характеристику сталям, предназначенным для изготовления деталей, подвергаемых улучшению.
Стали, подвергаемые термическому улучшению, широко применяют для изготовления различных деталей, работающих в сложных напряженных условиях (при действии разнообразных нагрузок, в том числе переменных и динамических). Стали приобретают структуру сорбита, хорошо воспринимающую ударные нагрузки. Важное значение имеет сопротивление хрупкому разрушению. Улучшению подвергаются среднеуглеродистые стали с содержанием углерода 0,30…0,50 %.
Улучшаемые стали
Улучшаемые углеродистые стали 35, 40, 45 дешевы, из них изготавливают детали, испытывающие небольшие напряжения (сталь 35), и детали, требующие повышенной прочности (стали 40, 45). Но термическое улучшение этих сталей обеспечивает высокий комплекс механических свойств только в деталях небольшого сечения, так как стали обладают низкой прокаливаемостью. Стали этой группы можно использовать и в нормализованном состоянии. Детали, требующие высокой поверхностной твердости при вязкой сердцевине (зубчатые колеса, валы, оси, втулки), подвергаются поверхностной закалке токами высокой частоты. Для снятия напряжений проводят низкий отпуск. Улучшаемые легированные стали применяют для более крупных и более нагруженных ответственных деталей. Стали обладают лучшим комплексом механических свойств: выше прочность при сохранении достаточной вязкости и пластичности, ниже порог хладоломкости. Хромистые стали 30Х, 40Х, 50Х используются для изготовления небольших средненагруженных деталей. Эти стали склонны к отпускной хрупкости, поэтому после высокого отпуска охлаждение должно быть быстрым. Повышение прокаливаемости достигается микролегированием бором (35ХР). Введение в сталь ванадия значительно увеличивает вязкость (40ХФА). Хромокремнистые (33ХС) и хромокремниймарганцевые (хромансил) (25ХГСА) стали обладают высокой прочностью и умеренной вязкостью. Стали хромансилы обладают высокой свариваемостью, из них изготавливают стыковочные сварные узлы, кронштейны, крепежные и другие детали. Широко применяются в автомобилестроении и авиации. Хромоникелевые стали 45ХН, 30ХН3А отличаются хорошей прокаливаемостью, прочностью и вязкостью, но чувствительны к обратимой отпускной хрупкости. Для уменьшения чувствительности вводят молибден или вольфрам. Ванадий способствует измельчению зерна. Стали 36Х2Н2МФА, 38ХН3ВА др. обладают лучшими свойствами, относятся к мартенситному классу, слабо разупрочняются при нагреве до 300…400 oС. из них изготавливаются валы и роторы турбин, тяжелонагруженные детали редукторов и компрессоров.
|
5. Охарактеризуйте свойства, структуру, приведите примеры применения сплавов с особыми тепловыми свойствами.
Для ряда отраслей машиностроения и приборостроения необходимо применение материалов со строго регламентированными значениями в определенных температурных интервалах эксплуатации таких физических свойств, как температурные коэффициенты линейного расширения (ТКЛР) и модуля нормальной упругости
(ТКМУ). Эти коэффициенты определяют характер изменения размеров детали и модуля упругости сплава при нагреве.
Согласно правилу Курнакова, в случае, когда компоненты образуют твердый раствор, ТКЛР сплава изменяется по криволинейной зависимости внутри пределов, ограниченных значениями ТКЛР чистых компонентов. Однако сплавы Fe – Ni не подчиняются общим закономерностям. В области концентраций от 30 до 45 % никеля для них характерны аномалии, связанные с инварным эффектом (рис. 7).
Рис. 7 – Температурный коэффициент линейного расширения сплавов Fe – Ni
Самое низкое значение ТКЛР в диапазоне температур от –100 до +100°С имеет сплав, содержащий 36 % Ni. Этот сплав был открыт в 1897 г. и назван инваром (лат. invariabilis – неизменный) из-за минимальных значений коэффициента теплового расширения.
|
Для металлов с кубической кристаллической решеткой ТКЛР изотропен. Его значения не зависят от направлений кристаллической решетки и преимущественной ориентации текстуры. Термический коэффициент объемного расширения втрое превышает ТКЛР.
Для сплавов Fe – Ni инварного состава, помимо низких значений ТКЛР, характерна еще одна аномалия – аномалия температурного коэффициента модуля упругости. В любых твердых телах, в том числе металлах, при нагреве наблюдается уменьшение модуля упругости, являющегося мерой сил межатомных связей. В сплавах с инварным эффектом модуль упругости растет или остается постоянным с повышением температуры. Характерно, что максимальной величиной ТКМУ обладает тот же Fe – Ni сплав с самым низким значением ТКЛР, содержащий 36 % Ni (рис. 7.1). Подбор определенного химического состава позволяет разработать сплавы, модуль упругости которых практически не зависит от температуры.
Рис. 7.1. – Температурный коэффициент модуля упругости сплавов Fe – Ni
Сплавы, сохраняющие постоянство модуля упругости в широком интервале температур, называют элинварами. Природа аномального изменения ТКЛР инварных сплавов, так же как и модуля нормальной упругости, имеет ферромагнитное происхождение.
6. Для получения отливки детали (рис. 5) из серого чугуна СЧ15 требуется изготовить литейную форму.
На отливки из конструкционных чугунов приходится до 80% всех производимых чугунных отливок. Основными потребителями являются различные отрасли машиностроения (автомобильное,
тракторное и сельскохозяйственное машиностроение, тяжелое машиностроение, станкостроение и др.). Свойства отливок регламентируются ГОСТом 1412-70.
Рис. 8. Влияние сечения отливки на механические свойства чугуна
Вследствие чувствительности чугуна к изменению скоростей охлаждения прочность в различных узлах отливки может отличаться от прочности, характеризующей данную марку. На рис. 1 приведены механические свойства чугунов в отливках различного сечения. Отливки охлаждались в песчано-глинистых формах. Конструктор выбирает марку чугуна, исходя из требуемых механических свойств в наиболее нагруженных сечениях отливки.
|
Литейщик должен выбирать состав чугуна и технологический процесс его получения с учетом влияния различных факторов на структуру чугуна и его механические свойства. При получении чугунов повышенной прочности (СЧ 24-44, СЧ 28-48, СЧ 32-52, СЧ 36-56, СЧ 40-60), также в тех случаях, когда техническими условиями предусматриваются дополнительные требования, задача может оказаться сложной. Например, отливки, подвергающиеся в процессе эксплуатации повышенному износу (отливки металлорежущих станков, детали двигателей и т. п.), требуют повышенной твердости рабочих поверхностей и определенной микроструктуры чугуна (дисперсности перлита, величины и расположения графитовых включений и т. д.).
При производстве чугунов этих и более высоких марок используют раздельно или совместно методы модифицирования, легирования и термообработки.
Модифицированный чугун. В качестве графити-зирующего модификатора применяют ферросилиций Си75 (75% Si), эффективность действия которого повышается при содержании в нем 1-2% А1.
Модификатор в виде кусков размером 5-10 мм вводят в струю чугуна, выпускаемого из плавильной печи. Для данных условий производства устанавливают оптимальный интервал времени от выпуска чугуна из печи до заливки форм, так как при превышении этого времени эффект модифицирования постепенно исчезает.
Высокие механические свойства модифицированного чугуна достигаются благодаря снижению расчетного содержания углерода и кремния, высокого перегрева чугуна в сочетании с модифицированием.
Следует, что по мере повышения требований к механическим свойствам, снижается содержание углерода в чугуне, повышается его перегрев и используется легирующее влияние марганца. Одновременно увеличивается количество модифицирующих добавок для предотвращения отбеливания чугуна и выделения международного графита.
Эффективным и широко используемым методом улучшения структуры и повышения механических свойств чугуна является применение в шихте стального лома. В модифицированном чугуне высших марок стальная часть шихты составляет до 50-70%. Экспериментально установлено, что при сравнении чугунов одинакового химического состава чугуны, выплавленные на шихте со стальным ломом, имеют более мелкий графит и повышенные механические свойства.
|
Положительное влияние присадки стали дополняется и тем, что при этом снижается содержание углерода в шихте, а следовательно, и в выплавленном чугуне.
Хотя модифицирование чугуна и уменьшает его склонность к отбеливанию, однако для каждой марки указаны минимальные толщины стенки отливки, получаемые без структурносвободного Цементита.
Легированный чугун. В качестве конструкционного материала применяют низколегированный чугун (общее содержание легирующих элементов до 3%). Используют в основном рФУющие элементы Cr, Мп (при содержании его свыше 1%).
Рис. 8. Влияние различных легирующих элементов на механические свойства (а) и глубину отбела (б) серого чугуна
Интенсивность и характер влияния каждого элемента оценивают абсолютной величиной коэффициента и знаком перед ним. Сравнение значений Кг различных легированных и нелегированных чугунов облегчает выбор оптимального химического состава, исходя не только из желаемой структуры и прочности в рабочих узлах, но и из условия получения легко обрабатывающегося серого чугуна без отбела в тонких сечениях отливок.
К серому чугуну с пластинчатым графитом со специальными свойствами предъявляют особые требования, связанные с условиями эксплуатации отливок. В некоторых случаях эти требования можно удовлетворить использованием нелегированных или низколегированных чугунов.
Для обеспечения высокой стойкости изложниц оптимальная структура (перлит + феррит + мелкопластинчатый графит) большей частью достигается при применении нелегированного чугуна с низким содержанием фосфора и серы. Повышенные эксплуатационные свойства антифрикционного ‘чугуна для подшипников, втулок и т. д. обеспечиваются малым легированием его Сг, Ni, Си, Ti, sb, Мп и др. (согласно ГОСТу 1585-70).
Немагнитные отливки, применяемые в электромашиностроении, имеют аустенитную структуру и изготовляются из высоколегированного чугуна. Получение заданной структуры достигается легированием 14-22% V до 8% Си и Сг. Вследствие дефицитности никеля его частично или полностью заменяют марганцем. Специальные и механические свойства этих чугунов ниже, чем высоконикелевых.
Отливки из коррозионностойкого чугуна применяют в химическом аппаратостроении и других областях. Коррозионную стойкость можно оценить весом металла (в граммах), превращенного продукт коррозии за единицу времени (1 ч) с единицы поверх-стн И м2) при действии внешней агрессивной (коррозионной) роды (азотной, серной, фосфорной кислоты, соли, щелочи и т. д.).
|
Особое место занимают высококремнистые сплавы типа «Фер. росилида». Благодаря высокому содержанию кремния (14-16%) их можно отнести к чугунам со степенью эвтектичности, близкой к единице.
Изготовление моделей
Модельный состав, состоящий из двух или более легкоплавких компонентов: парафина, стеарина, жирных кислот, церезина и др., в пастообразном состоянии запрессовывают в прессформы (рисунок 9.1, а). В качестве материала прессформ в зависимости от вида производства используют гипс, пластмассы, легкоплавкие металлы, сплавы, сталь или чугун. После затвердевания модельного состава прессформа раскрывается и модель (рисунок 9.2, б) выталкивается в ванну с холодной водой.
Рис. 9.1 – Последовательность операций процесса литья по выплавляемым моделям:
1 – прессформа; 2 – модельный состав; 3 – модель; 4 – модельный блок;
5 – емкость с керамической суспензией; 6 – специальная установка для обсыпки; 7 – кварцевый песок; 8 – бак с водой; 9 – устройство для нагрева воды; 10 – электрическая печь; 11 – оболочки; 12 – жаростойкая опока;13 – ковш с расплавленным металлом
Сборка модельных блоков
Для этого модели собирают в модельные блоки (рисунок 9.3, в) с общей литниковой системой. В один блок объединяют от 2 до 100 моделей. Соединяют модели в кондукторе, механически скрепляя или склеивая их. Одновременно ведется отливка литниковой системы.
Для сборки моделей в блоки в кондукторе выставляют металлические стояки из алюминия, наращивают на них слой модельного состава толщиной 25 мм и крепят к нему модели. Этот прием ведет к повышению прочности блока, сокращению расхода состава, обеспечению удобства транспортирования, хранения и просушивания блоков при нанесении обмазки.
Подготовка литейных форм к заливке
После извлечения из ванны оболочки промывают водой и сушат в шкафах (1,52 ч при 200°С). Затем оболочки ставят вертикально в жаростойкой опоке, вокруг засыпают сухой кварцевый песок и уплотняют его, после чего форму направляют в электрическую печь (рисунок 9.7, ж), в которой ее прокаливают (не менее 2 ч при 900 – 950°С).
В печи частички связующего спекаются с частичками огнеупорного материала, влага испаряется и остатки модельного состава выгорают.
Заливка расплавленного металла из ковша производится сразу же после прокалки в горячую литейную форму (рисунок 9.8, з).
Охлаждение отливок.
После охлаждения отливки форму разрушают. Отливки отделяют от литников и для окончательной очистки направляют на химическую очистку, затем промывают проточной водой, сушат, подвергают термической обработке и контролю.
Участки литья по выплавляемым моделям имеются на многих судостроительных и машиностроительных заводах. На них изготовляют сложные по конфигурации стальные отливки, получение которых другими способами или с применением механической обработки невозможно или привело бы к значительному усложнению технологического процесса и удорожанию продукции. К таким отливкам относятся в основном различные мелкие детали: турбинные лопатки, крыльчатки, решетки, распылители, угольники, кронштейны, рукоятки, ключи и другие детали высокой точности.
Электрошлаковое литье (ЭШЛ) – это способ получения фасонных отливок в водоохлаждаемой металлической литейной форме – кристаллизаторе, основанной на применении ЭШЛ расходуемого электрода. Применяется для получения точных крупных стальных (спец. сплавов) отливок ответственного назначения (фасонные элементы аппаратуры, работающие под давлением).
Сущность заключается в том, что приготовление расплава (плавка) совмещено по месту и времени с заполнением литейной формы Vраспл. = Vкристал.
На диаграмме состояния сплавов Fe-Fe3С укажите температурный интервал горячей обработки давлением для сталей. Определите температуру начала и конца свободной ковки заготовки из стали '40. Обоснуйте выбор температур.
Значение температур начала и конца обработки давлением для сплавов, имеющих основу, резко колеблются в зависимости от содержания в них других компонентов. Например, для различных деформируемых алюминиевых сплавов верхний предел находится между 470 - 500˚С, нижний – между 350 - 400˚С; у медных сплавов верхний предел – между 700 - 900˚С, нижний – между 550 - 800˚С; у магниевых сплавов верхний – 370 - 430˚С, нижний – 300 - 350˚С; у титановых сплавов верхний – 1000 - 1200˚С, нижний – 700 - 950˚С; у стали верхний – 1100 - 1300˚С, нижний – 800 - 950˚С.
Если отметить на диаграмме состояние сплава железо – углерод температурный интервал обработки давлением углеродистых сталей, то его верхний предел будет находиться на кривой, проходящей на 150 - 200˚С ниже линии солидуса. Нижний предел температурного интервала для углеродистых сталей соответствует примерно 800˚С, т.е. приблизительно на 75˚С выше линии PSK. Таким образом, сталь, содержащая от 0.4% до 1% С от начала до конца обработки давлением находится в однофазном состоянии (аустенит).Углеродистую сталь с меньшим содержанием углерода заканчивают обрабатывать при наличии в ней двух фаз: аустенита и феррита. При этом получается некоторый наклеп, который легко снимается последующей термической обработкой.
Приведите упрощенную электрическую схему трехфазного сварочного выпрямителя, вольт - амперные характеристики. Опишите его работу, преимущества, недостатки. Применение технологии сварки постоянным током.
Трансформатор в такой схеме используется для понижения напряжения, формирования необходимой внешней характеристики и регулирования режима. К более современным и совершенным устройствам относятся тиристорные выпрямители, в которых регулирование режима обеспечивается тиристорным выпрямительным блоком, осуществляющим фазовое управление моментом включения тиристоров. Формирование необходимых внешних характеристик производится введением обратных связей по сварочному току и выходному напряжению.
Достоинства и недостатки сварочных выпрямителей. Основное преимущество выпрямителей, по сравнению с трансформаторами, заключается в использовании в них для сварки постоянного тока, обеспечивающего надежность зажигания и устойчивость горения сварочной дуги и, как следствие, более качественный шов. Имеется возможность варить не только углеродистую и низколегированную, но и нержавеющую сталь, и цветные металлы. Немаловажно и то, что сварка выпрямителем дает меньшее количество брызг. В сущности, этих преимуществ вполне достаточно для однозначного ответа на вопрос, какой сварочный аппарат выбрать - трансформатор или выпрямитель. Если, разумеется, не принимать во внимание цен.
К недостаткам следует отнести относительно большой вес аппаратов, потерю части мощности, сильную "просадку" напряжения в сети при сварке. Последнее относится и к сварочным трансформаторам.
Заключение:
Фактически складывается новый механизм принуждения личности: люди искусственно принуждаются к «ничего неделанию», а те, кто не избавился от иллюзий и не согласен с порочной формулой «ты делаешь вид, что работаешь, мы делаем вид, что платим», постепенно склоняются к алкоголизму, «уходят» в восточные верования, наркоманию и т. п. Серьезное же недовольство управленцами рассматривается как антисистемная, «антисоветская» деятельность. Создается порочный круг, выхода из которого нет.
Международное сообщество должно официально признать опасность для дела мира распространения любых тоталитарных доктрин, т.е. доктрин, отрицающих самоценность личности, объявляющих приоритет любых общественных групп, которые выделяются по "анкетным" признакам (принадлежность к нации, расе, классу, религии и т.д.), отвергающих политический плюрализм, нетерпимых к инакомыслию.
Если всякое государство несет зло, то Абсолютное Государство порождает абсолютное зло. Поэтому необходимо сводить государство к допустимому минимуму. Государственное регулирование, столь необходимое для модернизации, не должно вести наше посттоталитарное общество к новым формам его огосударствления. Жесткий контроль за государственным аппаратом может обеспечить только гражданское общество. Его формирование — основная гарантия от тоталитарного перерождения.
Самое главное: путь к тоталитаризму и пути к свободе заложены в самой нашей природе. То, куда мы идем, есть результат прежде всего нашего личного нравственного выбора.
Опишите схему технологии пирометаллургического способа производства рафинированной меди.
Известны два способа извлечения меди из руд и концентратов: гидрометаллургический и пирометаллургический.
Первый из них не нашел широкого применения. Его используют при переработке бедных окисленных и самородных руд. Этот способ в отличие от пирометаллургического не позволяет извлекать попутно с медью драгоценные металлы.
Второй способ пригоден для переработки всех руд и особенно эффективен в том случае, когда руды подвергают обогащению.Основу этого процесса составляет плавка, при которой расплавленная масса разделяется на два жидких слоя: штейн — сплав сульфидов и шлак — сплав окислов. В плавку поступает либо сырая медная руда, либо обожженные концентраты медных руд. Обжиг концентратов осуществляют с целью снижения содержания серы до оптимальных значений.
Жидкий штейн продувают в конвертерах воздухом для окисления сернистого железа, переводя железо в шлак, и выделения черновой меди. Черновую медь далее подвергают рафинированию — очистке от примесей. Упрощенная схема пирометаллургического производства меди показана на рис. 1.
Рис.1. Схема технологии пирометаллургического способа производства рафинированной меди
2. Опишите превращения аустенита при изотермической выдержке 700° С, 650° С, 550° С и при охлаждении до 20° С со скоростью выше критической в стали У8.
Превращения аустенита при изотермической выдержке:
При нагреве стали выше критических температур с образованием аустенита исходной структурой является механическая смесь феррита и цементита - перлит. Превращение можно проследить на примере эвтектоидной стали с содержанием углерода 0,8%.
Превращение перлита в аустенит происходит в соответствии с общими закономерностями фазового превращения в твердом состоянии. Во-первых, движущей силой превращения является стремление системы достичь минимума свободой энергии (рис.2).
Рис.2. Изменение свободной энергии аустенита и перлита.
Зародыши новой фазы - аустенита - образуются на межфазных поверхностях раздела феррита и цементита. Переход перлита в аустенит состоит из двух элементарных процессов: полиморфного превращения Feα → Feγ и растворения в γ-железе углерода. Скорость образования аустенита зависит от разности свободных энергий аустенита и перлита и скорости диффузии атомов углерода, необходимых для образования аустенита.
![]() | ![]() | ![]() | ![]() |
а) | б) | в) | г) |
Рис. 3 Схема превращений эвтектоидной стали при нагреве:а)- исходная перлитная структура; б)- перлит с зародышами аустенита;в)- аустенит с остатками цементита и растворение цементита;
г)- однородный аустенит
Важной структурной характеристикой нагретой стали является величина зерна аустенита. От размера зерна аустенита зависят механические свойства изделия. Особенно чувствительна к размеру аустенитного зерна ударная вязкость, которая заметно падает с укрупнением зерна.
Склонность к росту зерна стали зависит, с одной стороны, от содержания в ней легирующих элементов - почти все легирующие элементы (за исключением марганца) тормозят рост аустенитного зерна. Наиболее сильно замедляют рост аустенитного зерна V, Ti, Al и Zr. Основной причиной такого действия легирующих элементов считается образование в аустените карбидов и оксидов этих элементов, которые являются барьерами для растущего зерна.
С другой стороны, склонность к росту зерна стали сильно зависит от технологии производства и режима раскисления, так как они определяют наличие в стали разного количества мельчайших примесей карбидов, оксидов, сульфидов и нитридов, также затрудняющих рост зерна.
Превращения аустенита при охлаждении:
Аустенит является устойчивым только при температурах выше Ас1. При охлаждении стали ниже критических температур аустенит становится неустойчивым и начинается превращение аустенита в перлит (перлитное превращение). Рассмотрим это превращение на примере эвтектоидной стали.
Чем ниже температура превращения, тем больше степень переохлаждения аустенита и тем быстрее будет происходить превращение аустенита в перлит.
С другой стороны такое превращение носит диффузионный характер и связано с перераспределением углерода, причем чем ниже температура, тем медленнее идет процесс диффузии. Такое противоположное действие обоих факторов (переохлаждения аустенита и диффузии углерода) приводит к тому, что с понижением температуры скорость превращения возрастает, достигает максимума, а затем скорость превращения убывает.
Перлит растет из отдельных центров в виде пластин (рис.4). Зародышем перлитных пластин обычно является цементит (рис.4, а), зарождение которого облегчено на границе аустенитных зерен. При утолщении цементитной пластины вблизи нее аустенит обедняется углеродом и создаются условия для зарождения путем полиморфного γ → α превращения ферритных пластин, примыкающих к цементитной пластине (рис.4,б).
При утолщении же ферритной пластины (малое содержание углерода) он оттесняется в аустенит, в результате чего создаются благоприятные условия для появления новых цементитных пластин. Кроме бокового (рис.4,а, б, в) при превращении А → П имеет место и торцевой рост пластин феррита и цементита (рис.4,г, д).
а | б | в | ||
![]() | ||||
г | д | |||
![]() | ||||
Рис. 4. Схема зарождения и роста перлитных колоний
В зависимости от степени переохлаждения аустенита образуются разные структуры феррито-цементитной смеси. Рассмотрим структуры, образующиеся при диффузионном превращении аустенита.
При температуре 650-700 °С образуется собственно перлит. При перлитном превращении ведущей фазой является цементит. В результате образования пластинок цементита соседние участки аустенита обедняются углеродом, что в свою очередь приводит к образованию пластинок феррита.
При увеличении переохлаждения увеличивается количество зародышей новой фазы. Естественно, что с ростом числа чередующихся пластин феррита и цементита уменьшаются их размеры и расстояния между ними (рис.5). Другими словами, с понижением температуры растет дисперсность (степень измельчения) продуктов распада аустенита. Под степенью дисперсности понимают расстояние между соседними пластинками феррита и цементита. При температуре 600-650 °С образуется структура сорбит, а при 550-600 °С - тростит.
Рис. 5. Схемы феррито-цементитных структур:
а - перлит; б - сорбит; в - тростит
Перлит, сорбит, тростит являются структурами одной природы - механической смесью феррита и цементита и отличаются друг от друга лишь степенью дисперсности. С увеличением степени дисперсности пластин цементита растет твердость и прочность стали. Перлит, сорбит и троститназывают перлитными структурами.
Перлитное превращение с образованием структур перлита, сорбита и троостита носит диффузионный характер и происходит в сталях при невысоких скоростях охлаждения.
Если скорость охлаждения велика, то диффузионное перераспределение углерода невозможно и процесс превращения аустенита носит бездиффузионный характер. При этом меняется только тип решетки γ на α, а весь углерод, содержащийся в аустените, остается в решетке феррита, несмотря на то, что в феррите при комнатной температуре может содержаться только 0,006% С. В результате образуется пересыщенный твердый раствор углерода в α – железе. Такая структура называется мартенсит.
3. Опишите технологию термической обработки закаленного 30 мм, l = 90 мм, для полученияÆпальца, изготовленного из стали 35, минимальной твердости.
Закалка – упрочняющая термическая обработка, при которой сталь нагревают на 30…50 оС выше температуры фазовых превращений (А3 или А1), выдерживают во времени и быстро охлаждают со скоростью выше критической Vкр (рис. 6.1). Для углеродистых сталей Vкр ≈ 150 оС/с, а охлаждение в воде обеспечивает среднюю скорость 200 оС/с.
Целью закалки является получение высокой твердости, прочности и износостойкости стали. Такие свойства обеспечивает образующаяся в ре Мартенсит (М) – пересыщенный твердый раствор углерода в α- железе (назван по имени немецкого металловеда А. Мартенса – Adolf Martens).
Определяющим этапом формирования структуры мартенсита при закалке является охлаждение стали из аустенитной области до комнатной температуры. При быстром охлаждении после полиморфного превращения, т.е. перестройки кристаллической решетки аустенита (ГЦК) в решетку феррита (ОЦК), «лишний» углерод остается в решетке ОЦК вследствие подавления диффузионных процессов. Образуется пересыщенный твердый раствор углерода в α – железе. Перенасыщенность мартенсита углеродом создает в его решетке большие внутренние напряжения, которые приводят к искажению ее формы и превращению из кубической в тетрагональную Уровень внутренних напряжений оценивается степенью тетрагональности, т.е. отношением длины ребра зультате закалки неравновесная (метастабильная) структура мартенсита «с» высоты параллелепипеда к ребру его основания «а». Закалка не является окончательной термообработкой. Чтобы уменьшить внутренние закалочные напряжения, приводящие к хрупкому разрушению, а также получить требуемый комплекс механических свойств, после закалки сталь обязательно подвергают отпуску. (Рис.6 термическая обработка закаливания)
(Рис.6 термическая обработка закаливания)
|
|
История создания датчика движения: Первый прибор для обнаружения движения был изобретен немецким физиком Генрихом Герцем...
Особенности сооружения опор в сложных условиях: Сооружение ВЛ в районах с суровыми климатическими и тяжелыми геологическими условиями...
Историки об Елизавете Петровне: Елизавета попала между двумя встречными культурными течениями, воспитывалась среди новых европейских веяний и преданий...
Семя – орган полового размножения и расселения растений: наружи у семян имеется плотный покров – кожура...
© cyberpedia.su 2017-2024 - Не является автором материалов. Исключительное право сохранено за автором текста.
Если вы не хотите, чтобы данный материал был у нас на сайте, перейдите по ссылке: Нарушение авторских прав. Мы поможем в написании вашей работы!