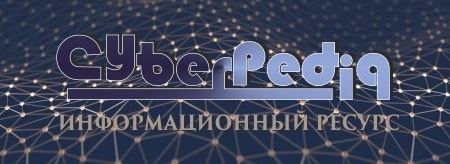
Механическое удерживание земляных масс: Механическое удерживание земляных масс на склоне обеспечивают контрфорсными сооружениями различных конструкций...
Архитектура электронного правительства: Единая архитектура – это методологический подход при создании системы управления государства, который строится...
Топ:
Оценка эффективности инструментов коммуникационной политики: Внешние коммуникации - обмен информацией между организацией и её внешней средой...
Основы обеспечения единства измерений: Обеспечение единства измерений - деятельность метрологических служб, направленная на достижение...
История развития методов оптимизации: теорема Куна-Таккера, метод Лагранжа, роль выпуклости в оптимизации...
Интересное:
Искусственное повышение поверхности территории: Варианты искусственного повышения поверхности территории необходимо выбирать на основе анализа следующих характеристик защищаемой территории...
Распространение рака на другие отдаленные от желудка органы: Характерных симптомов рака желудка не существует. Выраженные симптомы появляются, когда опухоль...
Влияние предпринимательской среды на эффективное функционирование предприятия: Предпринимательская среда – это совокупность внешних и внутренних факторов, оказывающих влияние на функционирование фирмы...
Дисциплины:
![]() |
![]() |
5.00
из
|
Заказать работу |
|
|
Падающий на поверхность вещества световой пучок частично поглощается, а частично отражается. Из оптики известно, что доля энергии отраженного излучения зависит от длины световой волны и состояния поверхности вещества. В табл. 3.2 представлены значения коэффициентов отражения световых волн от чистых, не окисленных полированных поверхностей металлов (при полном отражении этот коэффициент равен единице). Приведенные в табл. 3.2 данные свидетельствуют о том, что значительная доля светового потока отражается от чистой поверхности.
Для реальных поверхностей, покрытых оксидами и имеющих худшую чистоту обработки, значение коэффициента отражения уменьшается. С ростом температуры вещества на его поверхности стимулируется образование оксидов и других соединений, которые также увеличивают поглощение. Подача в зону обработки кислорода или других газов интенсифицирует этот процесс. В результате можно добиться того, что 20...40 % энергии светового пучка будет поглощено веществом.
Еще большего поглощения энергии лазерного излучения можно добиться при нанесении на поверхность веществ с малыми коэффициентами отражения (например, газовой сажи, краски, водорастворимых полимерных покрытий), но в этом случае возможно взаимодействие нанесенного вещества с основным материалом, что не всегда допустимо.
Поглощенное веществом лазерное излучение передает свою энергию электронам вещества, в связи с чем глубина проникания световой энергии в вещество соответствует средней длине свободного пробега электрона, составляющей 5...50 нм для большинства распространенных веществ. Дальнейшая передача энергии из этой зоны в глубь вещества осуществляется вследствие теплопроводности. В отличие от электронного луча энергия лазерного излучения при взаимодействии с веществом в основном превращается в теплоту, а доля возникающего при этом рентгеновского излучения пренебрежимо мала.
|
Лазерное излучение относительно небольшой интенсивности может произвести лишь весьма ограниченные изменения поверхности вещества: экспозицию специальных светочувствительных материалов или выцветание некоторых красок. По мере увеличения плотности мощности лазерного излучения до 104 Вт/см (что достаточно просто и быстро осуществляется путем его фокусировки) возможны нагрев и плавление поверхностных слоев материала. Последующее увеличение плотности мощности приводит к увеличению глубины проплавления; одновременно начинает все больше проявляться эффект испарения веществ.
При увеличении плотности мощности лазерного излучения до значений 105...106 Вт/см2 доля испаренного вещества начинает резко увеличиваться, образуются отдельные капли и частички вещества, которые под действием паров выбрасываются из зоны обработки. Повышение плотности мощности излучения до максимально достижимого значения (примерно до 108 Вт/см2 для лучших систем фокусировки луча) приводит к интенсивному испарению вещества с минимальным количеством жидкой фазы и выносом его в виде паров из зоны обработки. Для некоторых веществ возможна сублимация, т. е. переход из твердого состояния сразу в пар. Схема изменения характера взаимодействия светового потока с веществом в зависимости от плотности мощности излучения приведена на рис. 3.11.
При достаточно высокой плотности мощности излучения в фокальном пятне луча лазера может возникнуть так называемый оптический разряд. Это явление обычно происходит в газах при нормальном давлении и внешне напоминает высокочастотный электрический разряд. Физическая основа образования оптического разряда - возникновение в фокальном пятне термической плазмы вследствие нагрева газа. Неравномерность распределения по объему плазмы заряженных частиц приводит к резкой неравномерности распределения электрического потенциала в этом объеме и как следствие - к электрическому пробою. Пробой имеет характер миниатюрного взрыва и сопровождается яркой вспышкой. Поскольку на образование оптического разряда расходуется большое количество энергии лазерного излучения, в ряде случаев это приводит к нестабильности технологического процесса, в частности сварки; поэтому возникновение оптического разряда стараются предотвратить. Для этого чаще всего прибегают к обдуву лазерного луча в фокальном пятне потоком газа, перпендикулярным направлению луча.
|
К технологическим преимуществам мощного когерентного лазерного излучения следует отнести возможности:
1)передачи энергии в виде светового луча на расстояние (в том числе и через прозрачную разделительную перегородку или по специальному оптическому волноводу);
2)устранения непосредственного силового и электрического контакта источника энергии с изделием в месте обработки;
3)плавного регулирования энергии в пятне нагрева путем изменения фокусировки луча;
4)получения высокой плотности мощности (концентрацию энергии) в пятне нагрева благодаря «острой» фокусировке излучения;
5)достижения высоких температур в зоне воздействия излучения;
6)получения как импульсов энергии весьма малой длительности
(до 10-9 с), так и непрерывного излучения;
7)обеспечения малых зон обработки, размеры которых не превышают нескольких микрометров;
8)оперативного перемещения луча системой развертки при неподвижном объекте обработки с высокой точностью и скоростью;
9)модуляции мощности луча во времени по заданному закону;
10)осуществления технологического процесса в любой оптически прозрачной для излучения среде.
Исследование перечисленных особенностей лазерного излучения привело к возникновению групп технологических процессов, в основе которых лежат те или иные физические явления и эффекты.
Лазерная сварка как технологический процесс, связанный с локальным плавлением, находит все более широкое применение, конкурируя как с традиционными способами сварки, так и с электронно-лучевой сваркой.
|
Импульсные твердотельные лазеры применяют для сварки малоразмерных деталей в микроэлектронике, приборостроении, где важно получать малоразмерные швы с минимальным разогревом окружающего зону сварки материала. Такую сварку можно вести как отдельными точками, так и герметичными швами при последовательном наложении точек с их перекрытием.
Мощные газовые лазеры позволяют проплавлять за один проход, как и при электронно-лучевой сварке, значительную толщину изделий. Экспериментально установлено, что для проплавления стали на глубину до 5 мм требуется 1 кВт мощности излучения на 1 мм толщины изделий. Однако, как следует из рис. 3.12, при дальнейшем увеличении мощности лазерного луча глубина проплавления увеличивается меньшими темпами и для сварки изделий толщиной более 20 мм требуются уже весьма мощные лазеры, потребляющие из сети (с учетом КПД) сотни киловатт электрической мощности. Электроннолучевая сварка пока позволяет сваривать за один проход изделия из металла значительно большей толщины (до 100 мм) при меньшей потребляемой от сети мощности.
Так же, как и электронно-лучевая сварка, лазерная сварка дает узкий шов кинжального типа с малыми деформациями свариваемых деталей, что позволяет применять этот способ для соединения окончательно обрабатываемых узлов и деталей.
Прогресс в создании мощных потоков энергии когерентного лазерного излучения идет по пути наращивания мощности излучения с соответствующим увеличением потребляемой электрической мощности. Это, в свою очередь, ведет к техническому усложнению лазерного сварочного оборудования, снижению его надежности и технико-экономических показателей и в итоге не позволяет в полной мере реализовать принципиальные возможности лазерной технологии. Лазерная сварка получила дальнейшее развитие в виде создания гибридных способов сварки (двухлучевой лазерной, лазерно-дутовой, лазерно-индукционной, лазерно-плазменной, светолазерной), которые находят все большее применение в промышленности вследствие своей высокой технико-экономической эффективности. Соединение различных способов сварки с лазерной в единый технологический процесс позволяет частично устранить недостатки каждого способа и расширить технологические возможности сварочного процесса. Совместное использование источников тепла для гибридных способов сварки дает возможность при значительно меньшей мощности лазерного излучения достичь такой же производительности процесса, как и при обычной лазерной сварке. Необходимо также отметить, что использование гибридных способов сварки позволяет повышать производительность процессов металлообработки не за счет дорогостоящей энергии лазерного излучения, а за счет более дешевой энергии второго источника тепла. В этом состоит одно из основных преимуществ гибридных способов соединения и обработки металлов.
|
Лазерная сварка неметаллических материалов (в основном стекла и керамики) возможна благодаря тому, что излучение лазера на СО2 с длиной волны 10,6 мкм достаточно хорошо поглощается этими материалами и может быть использовано для их нагрева, плавления и последующей сварки. По сравнению с газопламенным нагревом, обычно используемым для сварки и пайки стекла, лазерное излучение позволяет увеличить интенсивность нагрева места сварки или пайки (но не более 100 К/с ввиду возможности термического растрескивания стекла) и уменьшить зону нагрева, что дает возможность создавать миниатюрные стеклянные сварные конструкции.
Резка материалов лазерным излучением может быть основана на локальном плавлении материала и его дальнейшем удалении П0Д действием сил тяжести, конвективного потока или газовой струи. Если же расплавленный материал перегрет и упругость его паров достаточно высока, образующиеся пары могут быть удалены из зоны резки струей инертного газа и процесс резки может происходить более эффективно. При лазерной резке можно получать узкие резы с минимальной зоной термического влияния.
В случае если разрезаемый материал содержит связанную или кристаллизационную воду (органические соединения, минералы), локальный интенсивный нагрев лазерным излучением приводит к разрыву молекулярных связей и испарению воды и других жидких компонентов. В результате испарения этих компонентов внутри материала может возникнуть высокое внутреннее давление, что приводит к образованию микротрещин и выбросу частиц материала. Аналогично протекает процесс резки пористых материалов, содержащих газы, и химических соединений, деструктирующих с образованием газообразных продуктов. На таком принципе основана резка слоистых пластиков, дерева, содержащих кристаллическую воду веществ.
Эффективность резки может быть значительно повышена в результате введения в зону резки активного газа, например кислорода. Экзотермическая реакция между разрезаемым материалом и кислородом значительно увеличивает выделение энергии в месте взаимодействия излучения с материалом. На этом принципе основан процесс газолазерной резки. Кислород в этом процессе осуществляет следующие функции:
|
1)обеспечивает в результате реакции окисления выделение основной части энергии, необходимой для резки;
2)значительно увеличивает поглощательную способность материала вследствие создания на его поверхности оксидов, имеющих меньший коэффициент отражения по сравнению с основным металлом;
3)снижает поверхностное натяжение расплавленных металлов, имеющих жидкотекучие оксиды;
4)благодаря газодинамическому давлению способствует удалению расплавленных оксидов из зоны резки;
5)охлаждает кромки разрезанного материала.
При газолазерной резке металлов лазер непрерывного излучения на углекислом газе мощностью до 5 кВт позволяет в струе кислорода резать листы из малоуглеродистых сталей толщиной до 10 мм, из легированных и коррозионно-стойких сталей - до 6 мм, из никелевых сплавов - до 5 мм, из титана - до 10 мм. Металлы, образующие тугоплавкие оксиды с малой вязкостью, газолазерной резкой разделяются плохо, так как удаление оксидов из зоны резки в этом случае затруднено. К таким металлам относятся алюминий и его сплавы, магний, латунь, хром и целый ряд других металлов, которые выгоднее резать плазменной резкой.
Газовое пламя
Газовое пламя - один из «старейших» источников энергии, используемых в сварочных процессах. Сварочная газовая горелка появилась в начале XX в. как практическое осуществление химической реакции сжигания углеводородного топлива (чаще всего ацетиленового) в чистом кислороде. Сгорание топлива происходит по реакции
2С2Н2 + 5О2 = 4СО2 + 2Н2О + 1300,6 кДж/моль.
В факеле газового пламени кроме СО2 и паров Н2О обычно присутствуют продукты пирогенного распада ацетилена, СО и частично попадающий в зону сварки атмосферный воздух (рис. 3.13).
В связи с этим защитные свойства газового пламени малоэффективны и сварочная ванна в значительной мере насыщается газами, ухудшающими свойства наплавленного металла. Поэтому газовая сварка химически активных металлов (титана, циркония и др.) практически невозможна.
Интенсивность ввода энергии в материал при нагреве его газовым пламенем относительно невелика (см. табл. 1.6), поэтому при газовой сварке сварные швы имеют большую ширину, чем при дуговой.
В последнее время газовая сварка в промышленности практически вытеснена другими, более прогрессивными способами сварки и используется в основном в ремонтных целях. Вместе с тем газопламенная обработка благодаря сравнительной простоте и мобильности процесса широко применяется в промышленности в технологических процессах газовой резки, нагрева, пайки и газопламенного напыления.
Электрошлаковая сварка
Электрошлаковая сварка появилась в свое время как дальнейшее развитие дуговой сварки под флюсом, когда было установлено, что при определенных режимах электрод «закорачивается» на слой расплавленного шлака и выделение теплоты (рис. 3.14) происходит при прохождении электрического тока через жидкую шлаковую ванну. Общее количество теплоты, выделяемое в зоне сварки за 1 с, определяется как q = I 2 R cyм, где R сум - суммарное сопротивление шлаковой и металлической ванн.
При электрошлаковой сварке почти вся электрическая мощность передается шлаковой ванне, а от нее - электроду и свариваемым кромкам. Устойчивый процесс возможен только при постоянной температуре шлаковой ванны. Рабочая температура шлаковой ванны под электродом может достигать2200... 2300К.
При электрошлаковой сварке более равномерное выделение теплоты по объему сварочной ванны по сравнению со сваркой под флюсом позволяет сваривать за один проход детали значительных сечений (до нескольких квадратных метров); это обусловило широкое распространение электрошлаковой сварки в тяжелом машиностроении.
Применяемые при электрошлаковой сварке флюсы отличаются высокой электропроводностью в расплавленном состоянии и низкими стабилизирующими свойствами по отношению к дуговому разряду. Например, флюс АНФ-1 содержит до 92 % плавикового шпата CaF2, являющегося активным дестабилизатором дуги.
После развития начального дугового разряда расплавленный шлак полностью шунтирует дугу и дуговой процесс переходит в так называемый шлаковый. Температура плавления шлака должна быть выше, чем температура плавления свариваемого металла.
Электрошлаковую сварку обычно ведут на переменном токе при низком напряжении (40...50 В) и рабочих токах до нескольких тысяч ампер. Баланс энергии этого сварочного процесса показан на рис. 3.15.
Вследствие большой поверхности контакта теплоносителей -шлаковой и металлической ванн - с основным металлом плотность тепловых потоков в металл невысока, поэтому для электрошлаковой сварки необходима более высокая удельная энергия (от 100 до 200 кДж/см2), чем для большинства способов дуговой сварки.
Термитная сварка
Химическая реакция взаимодействия оксидов железа с алюминием (алюмотермическая реакция) протекает с большим выделением теплоты по следующему уравнению:
3Fe3О4 + 8А1 → 4А12О3 + 9Fe + 3242 кДж.
Такая реакция реализуется в технике при сжигании смесей алюминиевого порошка и железной окалины, получивших название термитов. Сравнительная простота осуществления алюмотермической реакции и доступность применяемых материалов положили начало широкому применению термитов в промышленности, особенно в металлургии и для сварочных процессов.
При термитной сварке сначала производят поджиг термита, происходит его сгорание, а затем разделка кромок обычно заполняется жидким металлом, образующимся в результате алюмотермической реакции. Разогрев и плавление кромок свариваемых деталей при термитной сварке осуществляются за счет теплосодержания жидкого присадочного металла, поэтому его объем выбирают в 2-3 раза большим, чем это необходимо для заполнения разделки.
Одно из основных достоинств процесса термитной сварки - простота осуществления в полевых условиях, что обусловило его применение для сварки рельсов, контактной сети железных дорог и некоторых строительных конструкций.
|
|
Общие условия выбора системы дренажа: Система дренажа выбирается в зависимости от характера защищаемого...
Двойное оплодотворение у цветковых растений: Оплодотворение - это процесс слияния мужской и женской половых клеток с образованием зиготы...
Индивидуальные и групповые автопоилки: для животных. Схемы и конструкции...
Типы сооружений для обработки осадков: Септиками называются сооружения, в которых одновременно происходят осветление сточной жидкости...
© cyberpedia.su 2017-2024 - Не является автором материалов. Исключительное право сохранено за автором текста.
Если вы не хотите, чтобы данный материал был у нас на сайте, перейдите по ссылке: Нарушение авторских прав. Мы поможем в написании вашей работы!