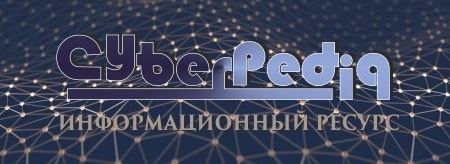
Индивидуальные и групповые автопоилки: для животных. Схемы и конструкции...
Архитектура электронного правительства: Единая архитектура – это методологический подход при создании системы управления государства, который строится...
Топ:
Устройство и оснащение процедурного кабинета: Решающая роль в обеспечении правильного лечения пациентов отводится процедурной медсестре...
Методика измерений сопротивления растеканию тока анодного заземления: Анодный заземлитель (анод) – проводник, погруженный в электролитическую среду (грунт, раствор электролита) и подключенный к положительному...
Основы обеспечения единства измерений: Обеспечение единства измерений - деятельность метрологических служб, направленная на достижение...
Интересное:
Инженерная защита территорий, зданий и сооружений от опасных геологических процессов: Изучение оползневых явлений, оценка устойчивости склонов и проектирование противооползневых сооружений — актуальнейшие задачи, стоящие перед отечественными...
Лечение прогрессирующих форм рака: Одним из наиболее важных достижений экспериментальной химиотерапии опухолей, начатой в 60-х и реализованной в 70-х годах, является...
Отражение на счетах бухгалтерского учета процесса приобретения: Процесс заготовления представляет систему экономических событий, включающих приобретение организацией у поставщиков сырья...
Дисциплины:
![]() |
![]() |
5.00
из
|
Заказать работу |
|
|
1.Выбор типа и марки электрода.
Тип и марка электрода при выполнении сварочных работ выбирается в зависимости от нескольких факторов: главным фактором является получение требуемых механических свойств основного и наплавленного металла. Рассмотрим сварку трещины по сплошному металлу в броневом листе восьмиосной цистерны для перевозки светлых нефтепродуктов.
Ручная дуговая сварка покрытым электродом применяется при выполнении швов небольшой длины на сборочных единицах, особенно при их сплошной пространственной форме и в труднодоступных местах.
При ручной дуговой сварке основными показателями режимов сварки является: тип, марка, диаметр электрода, величина тока, род и полярность тока. Свойства металла сварных швов зависит также от тех электродов, которые были использованы. В настоящее время выпускается большой ассортимент электродов с различными свойствами. Однако, указанные характеристики могут быть получены в том случае, если основной металл не оказывает серьезного влияния на свойства металла шва.
Для ручной дуговой сварки низколегированной стали выбираем тип электрода Э-42А, марки УОНИ -13/45, коэффициент наплавки 8,5 г/а.г, род сварочного тока постоянный, обратной полярности. Расход на 1кг наплавленного металла Кр=1,6 кг.
2. Выбор диаметра электрода.
Диаметр электрода назначают в зависимости от толщины деталей. Толщина броневого листа 12мм. Согласно таблицы № 3 «Выбор диаметра электрода в зависимости от катета шва»
таблица № 3 «Выбор диаметра электрода в зависимости от катета шва»
Катет шва, мм | 3 | 4-5 | 6-9 |
Диаметр электрода, мм | 3 | 4 | 5 |
выбираем диаметр электрода 4мм.
3.Определение площади поперечного сечения наплавленного металла и числа проходов.
|
На рисунке показаны основные геометрические размеры сварного шва.
Рис.1. Поперечное сечение сварного шва о V-образной разделкой кромок.
Площадь поперечного сечения наплавленного металла определяется по формуле:
где, h - глубина проплавления;
b - величина зазора в стыковом шве, b = 0,5-1 мм;
q - высота усиления шва, q= 1+2 мм;
α - угол разделки кромок, α= 60°;
S - толщина свариваемой детали, мм.
Число проходов определяем по формуле:
где F1 – площадь поперечного сечения первого (корневого) прохода, F1=(6+8)dэ; первый проход, как правило, выполняется электродами dэ =3+4 мм;
Fn –площадь поперечного сечения последующих проходов, Fn = (8+12)dэ.
принимаем n =3 проходам.
4. Определение силы тока и напряжения на дуге.
Сила сварного тока определяется по формуле:
Где k – опытный коэффициент, k=(40÷50)А/мм
I cв =(40÷50)*4=(160÷200) А, принимаем I cв =200А.
Напряжение на дуге определяется в зависимости от принятого диаметра электрода и силы сварочного тока:
принимаем Uд = 25В
5. Скорость сварки определяем по формуле:
где Кн – коэффициент наплавки принимается Кн=8,5Г/А*ч;
γ – удельная масса наплавленного металла, γ =0,0078г/мм3;
Fш – площадь поперечного сечения шва Fш =Fн = 107 мм2;
6. Расчет технической нормы времени сварочных работ.
Затраты времени на восстановление деталей сваркой зависит от ряда параметров: от свойств свариваемого металла, марки электрода, количества наплавленного металла, толщины детали, величины сварочного тока, пространственного положения шва и др.
Определение нормы штучного времени на электродуговую сварку.
t0 – штучное время на 1 погонный метр, мин;
tв1- вспомогательное время, связанное с образованием шва, мин;
L- длина шва определенного размера, м;
tв2- вспомогательное время, связанное со сваривариваемым изделием и управлением оборудованием, мин;
К2 - коэффициент, учитывающий время на обслуживание рабочего места, перерывы, отдых и личные нужды; Величина коэффициента К2 принимаются: при ручной сварке К2 =1,11-1,13; при полуавтоматической сварке при удобном положении выполнения работ К2 =1,13 и неудобном положении К2 =1,19; при автоматической сварке и работе на стационарных установках К2 =1,11, а при переносных сварочных машинах К2 =1,15.
|
Основное время на 1 погонный метр шва подсчитывается по следующей формуле(при многопроходной сварке).
где, Fн – площадь поперечного сечения наплавленного металла шва, Fн=107 *10-2 см2;
γ – плотность наплавленного металла, γ=7,8 г/см3;
αн=Кн =8,5г/ А*ч -коэффициент наплавки
I cв1- сварочный ток первого прохода;
I cв2- сварочный ток второго прохода =230А;
Вспомогательное время, связанное с образованием 1м шва, (tв1) определяют по формуле:
где t1 - время на зачистку кромок под шов, t1= 0,5 мин/м;
t2 - время на смену электродов, мин/м;
tэо- время смены одного элекгрода, tэо= 0,17 мин;
lЭ - длина электрода полная, мм
Кр - коэффициент расхода металла электрода в шов;
t3 - время измерения и осмотра шва, t3- 0,35 мин/м;
t4- время зачистки шва, t4 = (0,06+1,2)(п-1),мин/м;
n- количество проходов;
t5 - переход сварщика и подтягивание проводов, t5 -0,3 мин/м;
t6 - время на установку, кантовку и снятие изделия, мин.;
t7 - время на установку клейма сварщика в одном месте, t7 – 0,3 мин.
Вспомогательное время tB2, связанное о управлением оборудованием и независящее от длины шва определяется из таблиц и принимают равным 3+5% от ton.
Определение нормы выработки за смену.
Fд1-фонд времени за смену, Fд1=480мин;
Tn3- подготовительно – заключительное время, требующееся на подготовку приспособлений, рабочего места, накладку оборудования, уборку рабочего места, сдачу работы и т.д. Tn3=10мин;
7. Выбор типа и расчет количества сварочного оборудования.
Расчет потребного количества электросварочных аппаратов для РСД производится по расходу электродов в килограммах на одно изделие по следующей формуле:
N3- заданная программа восстановления деталей в год;
a3- норма расхода электродов на 1 ремонтируемое изделие;
αн=Кн=8,5г/А*ч
ηи =0,4 – коэффициент использования сварочного поста;
Fд – годовой фонд времени работы поста в одну смену;
m=1- число смен работы поста в сутки;
где Fн =[365-(Дв+Дпр)]mtсм-tпр - номинальный фонд времени
Дв- количество выходных дней в году = 104 дн;
Дпр - количество праздничных дней в году =8дн;
|
tсм =8,2 часа – продолжительность смены при 5-ти дневной рабочей недели;
tпр – суммарное число не рабочих часов в предпраздничные и субботнее дни (не учитываются);
Fн =[365-(104+8)]8,2= 2074,6 ч
Кn – коэффициент простоя оборудования в ремонте, принимаем его =0,95;
Принимаем два сварочных трансформатора.
Степень использования оборудования в технологическом процессе определяется коэффициентом загрузки оборудования
8.Технико – экономическое обоснование спроектированного технологического процесса:
Себестоимость изготовления детали сваркой определим по формуле:
Сз- заработная плата производственных рабочих;
См- стоимость материалов (электродов, проволок, газы, флюсы);
Сэ- стоимость эл/энергии для технологических целей;
Са- затраты на содержание и ремонт оборудования;
Ст- затраты на обеспечение технологического процесса (отопление, освещение, уборка помещений);
Сох- затраты на охрану труда;
Сц- цеховые накладные расходы;
Определение заработной платы производственных рабочих:
З0- основная заработная плата;
Зд – дополнительная заработная плата;
Зстр – отчисления на социальное страхование;
Sср – средняя часовая тарифная ставка сварщика, руб/час;
Тшт – штучное время;
Nа – количество изготовленных деталей;
В данном курсовом проекте увеличим величины ставок с учетом инфляции в 35 раз.
Возьмем 4 разряд сварщика, согласно тарифной сетки.
где в - коэффициент дополнительной заработной платы: в= 0,2÷1
Начисления на социальное страхование.
а- коэффициент начисление на социальное страхование, а=0,15
9. Определение стоимости израсходованных материалов
Расход электродов определяется по формуле:
к – коэффициент массы покрытия: к~0,3;
ψ – коэффициент, учитывающий потери электродного металла на угар и разбрызгивание: ψ=0,1;
λ – отношение длины стержня электрода к длине обмазанной его части: λ=1,1;
Qн- масса наплавленного металла, Qн =756,47 г;
Стоимость одной тонны электродов типа Э42А, диаметра 4мм равной 2880 руб/т, а с учетом инфляции 100800руб/т
Определение расходов на эл/энергию.
Icв- сварочный ток, А;
Uд –Напряжение на дуге, В;
|
t0 – основное время, ч;
η – КПД источника питания дуги: η = 0,8;
W0 – мощность холостого хода источника питания = 0,3 кВт;
Т – полное время сварочного цикла, ч;
Стоимость 1кВт*ч силовой энергии на 6.04.2004года составляет 1р 27коп, следовательно затраты на электроэнергию рассчитываются с использованием данного тарифа:
Затраты на содержание и ремонт оборудования
Накладные расходы:
С =8141,8+5699,2+14655,2+6096,51+1174,2+100800=136566,91руб.
|
|
Общие условия выбора системы дренажа: Система дренажа выбирается в зависимости от характера защищаемого...
Архитектура электронного правительства: Единая архитектура – это методологический подход при создании системы управления государства, который строится...
Папиллярные узоры пальцев рук - маркер спортивных способностей: дерматоглифические признаки формируются на 3-5 месяце беременности, не изменяются в течение жизни...
Индивидуальные и групповые автопоилки: для животных. Схемы и конструкции...
© cyberpedia.su 2017-2024 - Не является автором материалов. Исключительное право сохранено за автором текста.
Если вы не хотите, чтобы данный материал был у нас на сайте, перейдите по ссылке: Нарушение авторских прав. Мы поможем в написании вашей работы!