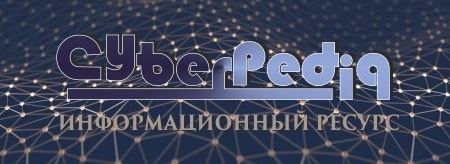
Состав сооружений: решетки и песколовки: Решетки – это первое устройство в схеме очистных сооружений. Они представляют...
Двойное оплодотворение у цветковых растений: Оплодотворение - это процесс слияния мужской и женской половых клеток с образованием зиготы...
Топ:
Устройство и оснащение процедурного кабинета: Решающая роль в обеспечении правильного лечения пациентов отводится процедурной медсестре...
Эволюция кровеносной системы позвоночных животных: Биологическая эволюция – необратимый процесс исторического развития живой природы...
Интересное:
Берегоукрепление оползневых склонов: На прибрежных склонах основной причиной развития оползневых процессов является подмыв водами рек естественных склонов...
Финансовый рынок и его значение в управлении денежными потоками на современном этапе: любому предприятию для расширения производства и увеличения прибыли нужны...
Распространение рака на другие отдаленные от желудка органы: Характерных симптомов рака желудка не существует. Выраженные симптомы появляются, когда опухоль...
Дисциплины:
![]() |
![]() |
5.00
из
|
Заказать работу |
|
|
Восстановление деталей электроконтактной приваркой стальной ленты. Сущность процесса восстановления заключается в приварке мощными импульсами тока к поверхности детали стальной ленты. В сварочной точке, полученной от действия импульса тока, происходит расплавление ленты и поверхности детали. Металл ленты расплавляется не по всей толщине, а лишь в тонком поверхностном слое в месте контакта с деталью. Ленту приваривают по всей изношенной поверхности перекрывающимися точками, которые располагаются по винтовой линии.
Восстановление деталей электроконтактным напеканием порошков. Способ напекания порошков сочетает в себе ряд процессов, протекающих одновременно: прессование и спекание металлического порошка, припекание его к поверхности детали под действием давления и температуры. Сущность способа заключается в том, что между вращающейся деталью, установленной в шпинделе токарного станка, и медным роликом- электродом подают присадочный порошок. Ролик при помощи пневмо -или гидроцилиндра прижимается к детали с усилием 0,75-1,2 кН. При проворачивании детали и ролика и в результате большого электрического сопротивления в месте их контакта порошок нагревается до 1000-4 300°С. Нагретые частицы порошка спекаются между собой и с поверхностью детали. Для напекания порошка применяют большую силу тока (2600-3000 А на 1 см ширины ролика) и низкое напряжение (0,7-1,2 В).
51 Особенности ремонта деталей.
На ремонтных предприятиях, в мастерских хозяйств и организаций ремонт можно вести, сохраняя или не сохраняя принадлежность ремонтируемых составных частей к определенному экземпляру изделия. В зависимости от этого признака получили распространение три метода ремонта: обезличенный, необезличенный и агрегатный.
|
Обезличенный метод ремонта. Этот метод характеризуется тем, что в процессе разборки и дефектации детали одной машины обезличиваются. Процесс сборки составных частей машины происходит из обезличенных, потерявших принадлежность к той или иной машине, деталей и агрегатов. Его основой является взаимозаменяемость деталей.
Преимуществом обезличивания деталей является возможность их восстановления на специализированных предприятиях. При обезличенном ремонте упрощается учет, отпадает необходимость составления ведомостей дефектов на каждый объект, появляется возможность создания заделов и т. д. Недостатком обезличенного ремонта является ускоренный износ годных для дальнейшей эксплуатации деталей, сопряжение которых нарушено.
Необезличенный метод ремонта. Особенностью этого метода является сохранение принадлежности сборочных единиц и основных деталей к ремонтируемой машине. При необезличенном ремонте проводится приремонтное диагностирование, по результатам которого определяется целесообразность разборки. Сопрягаемые пары деталей с износами в допустимых пределах не распаривают, что обеспечивает продление ресурса сопряжений. Применяют необезличенный ремонт при текущем ремонте машин.
Агрегатный метод ремонта. Сущность его заключается в том, что неисправные агрегаты машины заменяют новыми или заранее отремонтированными. Ремонт агрегатов проводится на специализированных предприятиях. Для организации ремонта машин агрегатным методом необходимо создать резервный обменный фонд агрегатов при ЦРМ хозяйств и технических обменных пунктах ремонтно-обслуживающей базы районного уровня.
Агрегатный метод ремонта способствует значительному сокращению времени пребывания машин в ремонте, не требует сложного технологического оборудования и высокой квалификации рабочих. Он позволяет повысить коэффициент технической готовности и снижает затраты на ремонт машин.
|
52 Организационные формы ремонта транспортной техники.
Формы организации производства. На ремонтных предприятиях они тесно связаны со специализацией, основанной на разделении труда. Можно выделить следующие формы организации производства: тупиковую, узловую и поточную.
Тупиковая форма организации производства характеризуется неподвижностью объекта ремонта. Разборочные и сборочные работы выполняют на месте расположения машины.
Ремонт сборочных единиц производится на рабочих местах, оснащенных универсальным оборудованием. Рабочие-ремонтники должны быть универсалами, разносторонне квалифицированными, так как они выполняют комплекс операций по восстановлению широкой номенклатуры деталей. Загрузка рабочих мест и оборудования непостоянная, с редкой повторяемостью одинаковых операций. В выполнении разборочно-сборочных и ряда других работ принимают участие лица, работающие на машинах. Тупиковая форма широко распространена в мастерских хозяйств.
Узловая форма организации производства основана на использовании свойств ма работ каждая сборочная единица или группа после снятия с неподвижной машины ре- монтируется на определенном рабочем месте, которое оснащается специальным оборудованием и инструментом. Специализация рабочего определяется тем рабочим местом, на котором он работает. При такой форме организации производства достигается более глубокая специализация, уровень которой определяется объемом производства и количеством специализированных рабочих мест. Узловая форма организации производства применяется в мастерских общего назначения, на ремонтно-механических заводах. При узловой форме по сравнению с тупиковой повышается производительность труда, улучшается качество ремонта, снижается трудоемкость и себестоимость ремонта.
Поточно-узловая форма организации производства характеризуется выполнением разборочно-сборочных работ по машине в целом на конвейерной линии, а разборочно- сборочные и ремонтные работы по отдельным сборочным единицам — на специали- зированных рабочих местах (как при узловой форме). Для передвижения машины используются тракторные средства различной конструкции.
Поточно-узловая форма организации производства имеет все преимущества узловой и отдельные элементы поточного производства.
|
Поточная форма организации производства основывается на ритмичной повторяемости согласованных во времени основных и вспомогательных операций, выполняемых на специализированных рабочих местах, расположенных в технологической последовательности. Обязательным условием поточного производства является достаточная производственная программа, постоянство номенклатуры объектов ремонта и их ритмичная поставка. Для этой формы организации производственного процесса необходимо наличие поточной линии, которая представляет собой совокупность специализированных рабочих мест, расположенных в соответствии с последовательностью операций технологического процесса, и непрерывная ритмичная их загрузка. Применяется поточная форма на специализированных ремонтных предприятиях.
53 Средства разборов
Оборудование и оснастка для разборки машин. Для разборки машин и сборочных единиц используют стенды, прессы, гайковерты, съемники, подъемно- транспортное оборудование.
Для разборки резьбовых соединений применяют ручной и механизированный инструмент. К ручному инструменту относятся гаечные ключи с открытым зевом двусторонние, кольцевые, двусторонние коленчатые (накладные), торцовые немеханизированные со сменными головками и специальные.
Накладные ключи охватывают все грани гайки, что придает им большую долговечность. Торцовые ключи можно вращать, не переставляя с грани на грань, что сокращает время на отворачивание гайки.
Из специальных ключей при разборке применяют коловоротные ключи и ключи для круглых гаек. Коловоротные ключи рациональны для отворачивания болтов и гаек небольших размеров, производительность труда при этом повышается в 2-5 раз.
Подъемно-транспортное оборудование, используемое при разборке и сборке, подразделяют на подъемное, подъемно-транспортное и транспортное.
|
К подъемному оборудованию относятся ручные и электрические тали, гидравлические и электромеханические домкраты, которые предназначены для подъема машин и их составных частей при текущем ремонте и техническом обслуживании.
Для подъема и перемещения составных частей машин применяют кран-балки, мостовые краны, кон сольно-поворотные краны, краны-штабелеры и манипуляторы.
При подъеме используют специальные захваты и различные приспособления.
К транспортному оборудованию относятся безрельсовые ручные тележки, электрокары. Для перемещения машин, агрегатов сборочных единиц и деталей на специализированных ремонтных предприятиях используют цепные подвесные конвейеры и другое оборудование.
54 Классификация загрязнений и методы очистки
Ремонтируемые машины могут иметь следующие виды загрязнений: отложения нежирового происхождения (пыль, грязь, растительные остатки), остатки ядохимикатов и маслянисто-грязевые отложения; остатки смазочных материалов; углеродистые от- ложения (нагар, лаковые пленки, осадки, асфальтосмолистые вещества); накипь; продукты коррозии, остатки лакокрасочных покрытий; технологические загрязнения, которые появляются при ремонте, сборке и обкатке (металлическая стружка, остатки притирочных паст, продукты износа шлифовальных кругов и др.).
Наибольшее распространение при ремонте машин получили следующие способы очистки: механический, физико-химический и термический. На специализированных ремонтных предприятиях, кроме того, применяют электрохимический, ультразвуковой и термохимический способы.
Удаление твердых отложений. К твердым отложениям относятся нагар, накипь, продукты коррозии и лакокрасочные покрытия. Нагар удаляют механическим, термическим и термохимическим способами. К механическому способу относятся: очистка поверхностей шабером, металлической щеткой, косточковой крошкой, пескоструйная и гидроабразивная обработка. Хорошие результаты дает очистка нагара и накипи обдувом косточковой крошкой (из скорлупы косточковых плодов) на установке ОМ-3181. Перед очисткой детали обезжиривают, чтобы не загрязнять крошку.
Термический способ применяют для удаления нагара из выпускных и всасывающих коллекторов с избытком кислорода или нагревают детали в термопечах.
Термохимический способ удаления нагара и накипи с деталей из черных металлов заключается в погружении их в расплав солей и щелочей.
Очистка от накипи может производиться также механическим и химическим способами. Стальные, чугунные детали очищают от накипи погружением в раствор, состоящий из 100-150 г/л 8-9%-ной соляной кислоты, с последующей промывкой в горячей воде. Детали из алюминиевых сплавов очищают в 6%-ном растворе молочной кислоты при температуре 40°С.
|
Коррозию удаляют механическим или химическим способом. В первом случае детали очищают стальными щетками, наждачной бумагой вручную или специальными приспособлениями, подвергают пескоструйной или абразивно-жидкостной обработке. При химическом способе используют растворы серной, соляной или фосфорной кислот. Краску с кабин и оперения машин удаляют механическим и химическим способом.
55 Виды восстановления деталей давлением
Способом постановки дополнительных ремонтных деталей можно компенсировать износ рабочих поверхностей, а также заменить изношенную или поврежденную часть детали. В первом случае дополнительную ремонтную деталь устанавливают на изношенную поверхность после предварительной механической обработки. Этим способом можно восстанавливать посадочные отверстия под подшипники качения в корпусах коробок передач, задних мостов, в ступицах колес, отверстия с изношенной резьбой и другие детали.
В зависимости от вида восстанавливаемой поверхности дополнительные ремонтные детали могут иметь форму гильзы, кольца, шайбы, резьбовой втулки или спирали.
После постановки и закрепления дополнительной ремонтной детали производят ее окончательную механическую обработку.
Осадка применяется для уменьшения внутреннего или увеличения наружного диаметра полой детали, а также для увеличения наружного диаметра сплошной детали за счет уменьшения ее длины. Осадкой восстанавливают втулки верхних головок шатунов, вилки карданных валов, проушины рычагов и др.
Вытяжку используют для увеличения длины деталей (тяг, штанг, рычагов и др.) за счет уменьшения поперечного сечения. Рабочие органы почвообрабатывающих машин (лемеха, лапы культиваторов и др.) восстанавливают оттяжкой.
56 Восстановление коленчатого вала.
. Коленчатые валы большинства двигателей изготовлены штамповкой из стали 45, 40Х, 50Т и др. У некоторых двигателей валы изготовлены литьем из высокопрочного магниевого чугуна. Основными дефектами коленчатых валов являются износ коренных и шатунных шеек и изгиб вала.
Коленчатый вал выбраковывают при наличии трещин, за исключением небольших продольных трещин на коренных и шатунных шейках длиной до 3 мм. При износе коренных и шатунных шеек, выходящем за пределы последнего ремонтного размера, коленчатые валы дизелей также выбраковывают.
Необходимость восстановления коленчатого вала и замены подшипников определяют по превышению допустимых зазоров в подшипниках.
Перед ремонтом коленчатый вал промывают в моечной машине ОМ-3600. Особенно тщательно промывают полости для центробежной очистки масла и масляные каналы. С помощью магнитного дефектоскопа проверяют наличие трещин на шейках вала.
Изгиб вала устраняют специальной правкой местным наклепом.
Изношенные посадочные места под шестерню или шкив восстанавливают наплавкой в среде углекислого газа проволокой Св-18ХГСА с последующей обработкой под номинальный размер.
Изношенные шпоночные канавки и отверстия под штифты для установки маховика заваривают полуавтоматом в среде углекислого газа проволокой Св-08Г2С. Шпоночную канавку фрезеруют на том же месте, чтобы не нарушить установку распределительных шестерен. Заваренные отверстия после зачистки торцовой поверхности на токарном станке просверливают, зенкуют и развертывают на сверлильном станке.
Наиболее распространенным способом восстановления коренных и шатунных шеек коленчатых валов является шлифование их под ремонтные размеры, установленные для каждой марки двигателя. Перед шлифованием шеек должны быть устранены все другие
дефекты вала. Измеряют шейки в двух сечениях на расстоянии 10 мм от щек и в двух плоскостях: в плоскости кривошипа и перпендикулярно ей.
Для шлифования шеек коленчатых валов применяют универсальный шлифовальный станок ЗА423, на котором можно шлифовать как коренные, так и шатунные шейки, или специализированные станки. Все шейки шлифуют под один ремонтный размер. Сначала шлифуют коренные шейки, а затем шатунные. За установочные базы при шлифовании коренных шеек принимают фаску отверстия под храповик и фаску или отверстие в торце вала под подшипник. Предварительно эти базы проверяют и при необходимости исправляют. Для проверки коленчатый вал уста- навливают в центрах и измеряют его биение по неизношенным поверхностям. Радиальное биение шейки под шестерню и фланца маховика не должно превышать соответственно 0,03 и 0,05 мм.
При шлифовании шатунных шеек за установочные базы принимают шейку под шестерню и наружную цилиндрическую поверхность фланца маховика или прошлифованные крайние коренные шейки.
57 Восстановление распределительного вала.
Валы большинства двигателей изготавливают штамповкой из стали 40 и 45 или отливкой из специального чугуна (двигатель ЗИЛ-130). Основные дефекты распределительного вала: изгиб вала, износ и отколы кулачков и опорных шеек, износ шпоночной канавки и посадочного места под распределительную шестерню, износ или повреждение резьбы.
Вал выбраковывают при трещинах, аварийном изгибе или скручивании, отломах металла на вершине кулачка более 3 мм его ширины.
Изгиб зала устраняют правкой в холодном состоянии на призмах под прессом. Допускаемое биение средних опорных шеек относительно крайних - не более 0,05 мм для большинства двигателей и не более 0,10 мм для двигателей А-41 и А-01М. Биение шейки под распределительную шестерню допускается не более 0,03 мм.
Опорные шейки распределительных валов шлифуют под уменьшенный ремонтный размер в центрах специального станка ЗА433 или на круглошлифовальных станках электрокорундовыми кругами зернистостью 46-60. Перед шлифованием зенкуют масляные отверстия, углубляют масляные каналы. В этом случае в блок цилиндров необходимо устанавливать втулки ремонтного размера.
При значительном износе опорных шеек их наплавляют в среде углекислого газа вибродутовой или плазменной наплавкой, наращивают железнением или газотермическим напылением. Перед наплавкой масляные каналы защищают графитными вставками, а перед железнением - свинцовыми. Наплавленные шейки шлифуют. При необходимости после грубого шлифования проводят закалку на глубину 2-3 мм.
Изношенную шейку под распределительную шестерню восстанавливают наплавкой в среде углекислого газа или железнением и обработкой под номинальный размер. Шпоночную канавку заплавляют электродом Э42 или в среде углекислого газа проволокой Св-18ХГСА и фрезеруют под номинальный размер. Смещение шпоночной канавки относительно диаметральной плоскости допускается не более 0,05 мм.
Изношенную шпоночную канавку можно восстановить фрезерованием под увеличенный размер шпонки. Ремонтную шпонку изготавливают из стали 45 и термически обрабатывают.
Изношенные кулачки шлифуют по копиру на станке ЗА433 до выведения следов износа и восстановления профиля. После шлифования кулачка высота подъема клапана не изменяется. При износе кулачков по высоте больше допустимого значения их наплавляют ручной электродуговой сваркой электродом Т-590 или Т-630, автоматической наплавкой в среде углекислого газа порошковой проволокой при помощи специального копировально- го приспособления с охлаждением вала в процессе наплавки. При ручной электродуговой или газовой наплавке на боковые стороны кулачков устанавливают защитные экраны из меди или графита. Распределительный вал помещают в ванну с водой на подставки так, чтобы половина диаметра вала была в воде. После наплавки проверяют изгиб вала и при необходимости правят. Затем наплавленные кулачки предварительно обрабатывают абра- зивным кругом по шаблону, а после этого окончательно шлифуют на станке ЗА433 по копиру.
Сборка головки цилиндров. Сборка фактически начинается с установки направляющих втулок и подбора клапанов перед притиркой их к гнездам. Втулки с буртиком запрессовывают до упора, а втулки без буртика до высоты, допускаемой техническими условиями. После запрессовки втулки развертывают разжимными развертками, обеспечивая требуемый зазор между стержнем клапана и отверстием втулки. Этот зазор (от 0,05 до 0,12 мм для двигателей различных марок) у выпускных клапанов на 0,01 - 0,02 мм больше, чем у впускных.
Восстановление шатунов.
Ремонт шатунов. Шатуны большинства автотракторных двигателей изготавливают из сталей 45, 40Х, 40Г и др. Основные дефекты шатунов: изгиб и скручивание стержня; износ отверстия нижней головки шатуна, втулки и отверстия верхней головки под втулку; износ опорных поверхностей крышки под гайки шатунных болтов и др.
59 Формы организации сборочных работ
Организационные формы сборки. В машиностроении применяют следующие организационные формы сборки узлов и машин: стационарную, осуществляемую без пооперационного расчленения сборочного процесса и при неподвижном собираемом объекте, и поточную, характеризующуюся расчленением технологического процесса на
операции и осуществляемую как при неподвижном собираемом объекте, так и с перемещением собираемого объекта.
В автомобильной и тракторной промышленности узловая и общая сборка осуществляются поточным методом с перемещением собираемого объекта (сборка на конвейере).
Собираемый объект при поточной сборке передается от одного сборочного места к другому при помощи транспортирующих устройств, которые предназначены только для межоперационного перемещения собираемого объекта. В некоторых случаях при узловой сборке передача собираемого объекта от одного сборочного места к другому осуществляется посредством рольганга.
При использовании конвейера с периодическим перемещением собираемого узла или машины сборка производится в периоды остановки конвейера. Применяются пластинчатые и тележечные конвейеры. При каждом перемещении собираемого объекта на сборочное место (пост) с последнего места сходит сборочная единица (изделие).
При сборке на непрерывно движущемся конвейере собираемый объект перемещается с одного сборочного места на другое с заданной скоростью, которая позволяет выполнить сборочные операции на протяжении каждого сборочного места.
Поточную сборку характеризует действительный темп сборки, который определяет период времени равномерного выпуска собранных изделий
60 Какие соединения составных частей изделия бывают?
Соединения деталей при сборке могут быть неподвижными и подвижными. Оба эти соединения выполняются разъемными и неразъемными. Разъемные соединения разбираются без повреждений деталей и без особых затруднений. Неразъемные соединения не могут быть разобраны без повреждений сопряженных элементов, разрушений скрепляющего шва или крепежных деталей.
Неподвижные разъемные соединения. К неподвижным разъемным соединениям относятся резьбовые, шпоночные и шлицевые, выполненные с переходными посадками, а также с посадками на конус. В резьбовых соединениях обычно используются шпильки,
болты и винты. Шпильки применяют при непосредственном соединении плоских по- верхностей или при соединении поверхностей с помощью прокладок, причем этому предшествует ввертывание шпилек в базовую деталь.
В шпоночных соединениях используются клиновые, призматические и сегментные шпонки. При сборке с помощью клиновой шпонки ось охватывающей детали смещена относительно оси вала. Это смещение обусловлено величиной зазора и является причиной радиального биения охватывающей детали.
Неподвижные шлицевые соединения выполняют с различными посадками центрирующих элементов и бывают туго- и легкоразъемными.
Штифтовые соединения выполняются при помощи конических и цилиндрических штифтов. Кроме соединения, штифты используются также для обеспечения необходимого взаимного положения собираемых деталей.
При сборке деталей с сопрягаемыми коническими поверхностями отверстия под штифт должны обрабатываться в сборе с охватывающей деталью. Отверстие под штифт в охватывающей детали может быть обработано предварительно до сборки.
Неподвижные неразъемные соединения. К неподвижным неразъемным соединениям относят соединения с гарантированным натягом, развальцовку, клепку, сварку, пайку, склеивание и холодную штамповку.
Соединения с гарантированным натягом выполняют с применением прессовых посадок или теплового воздействия на собираемые детали.
Детали, изготовленные по допускам прессовых посадок, собираются под давлением на прессе.
Развальцовывание применяется в том случае, когда требуется обеспечить плотное и герметичное соединение деталей. Развальцовывание осуществляется специальным инструментом – развальцовкой путем пластического деформирования одной из сопрягаемых деталей. В этой связи важен правильный выбор материалов деталей, от которого зависит получение качественного соединения. Развальцовывание осуществляется на сверлильных станках и специальных установках. В автомобильной промышленности развальцовывание применяется в трубопроводах тормозной системы и смазки двигателя.
Клепаные соединения используются в конструкциях, которые подвергаются воздействию высоких температур и коррозии, а также в конструкциях, испытывающих ударные и вибрационные нагрузки. Склепыванию предшествует предварительное соединение сопрягаемых деталей, заключающееся в выравнивании смещенных отверстий посредством их совместной обработки и в скреплении их между собой сборочными болтами и оправками, в пробивке или сверлении отверстий. Процесс клепки механизирован; применяются пневмо- и электроклепальные молотки, полуавтоматические и автоматические прессы (машины). При клепке с использованием полуавтоматов заклепки вставляются подающим устройством. В автоматах выполняется автоматически весь процесс: пробивка отверстий, вставка заклепок и обжатие замыкающих головок.
Сварные соединения находят все более широкое применение при сборке узлов машин, сокращая область применения заклепочных соединений. Применение сварки экономит материал и снижает трудоемкость изготовления. Технологическая особенность процесса сварки позволяет вводить электросварочные машины непосредственно в поточные линии сборки (и механической обработки). Наиболее широкое применение находит электродуговая автоматическая и полуавтоматическая сварка. Применяются различные виды контактной электросварки: стыковая, точечная, рельефная и др.
Контактная стыковая сварка находит применение для соединения деталей, изготовленных из различных материалов: например, жаропрочных и поделочных (выпускные клапаны двигателей внутреннего сгорания) и для деталей с замкнутым контуром (например, венцы зубчатых колес).
Контактная точечная сварка используется для изготовления штампосварных узлов и сварки внахлестку листов и профилей из стали и цветных металлов.
Контактная рельефная сварка применяется для соединения мелких деталей из низкоуглеродистых сталей.
Пайка в автомобилестроении используется для устранения обнаруженных дефектов (например, течь в трубках радиатора).
Подвижные разъемные и неразъемные соединения. Для получения подвижных соединений сопрягаемые детали изготовляют по допускам посадок, обеспечивающих подвижность соединения (зазор). К таким посадкам относятся посадки скольжения, дви- жения, ходовая, легкоходовая и широкоходовая.
Величина зазора соединения устанавливается конструктором при проектировании узла. Технолог обязан разработать такой технологический процесс, выполнение которого обеспечит соблюдение установленных конструктором допусков на размеры, формы и пространственных отклонений.
В подавляющем большинстве случаев подвижные соединения выполняются разъемными.
.
|
|
Папиллярные узоры пальцев рук - маркер спортивных способностей: дерматоглифические признаки формируются на 3-5 месяце беременности, не изменяются в течение жизни...
Опора деревянной одностоечной и способы укрепление угловых опор: Опоры ВЛ - конструкции, предназначенные для поддерживания проводов на необходимой высоте над землей, водой...
Археология об основании Рима: Новые раскопки проясняют и такой острый дискуссионный вопрос, как дата самого возникновения Рима...
История развития хранилищ для нефти: Первые склады нефти появились в XVII веке. Они представляли собой землянные ямы-амбара глубиной 4…5 м...
© cyberpedia.su 2017-2024 - Не является автором материалов. Исключительное право сохранено за автором текста.
Если вы не хотите, чтобы данный материал был у нас на сайте, перейдите по ссылке: Нарушение авторских прав. Мы поможем в написании вашей работы!