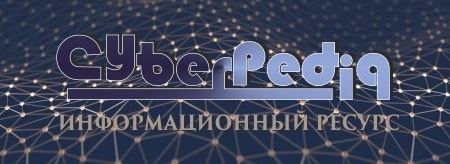
Автоматическое растормаживание колес: Тормозные устройства колес предназначены для уменьшения длины пробега и улучшения маневрирования ВС при...
Организация стока поверхностных вод: Наибольшее количество влаги на земном шаре испаряется с поверхности морей и океанов (88‰)...
Топ:
Устройство и оснащение процедурного кабинета: Решающая роль в обеспечении правильного лечения пациентов отводится процедурной медсестре...
Установка замедленного коксования: Чем выше температура и ниже давление, тем место разрыва углеродной цепи всё больше смещается к её концу и значительно возрастает...
Эволюция кровеносной системы позвоночных животных: Биологическая эволюция – необратимый процесс исторического развития живой природы...
Интересное:
Лечение прогрессирующих форм рака: Одним из наиболее важных достижений экспериментальной химиотерапии опухолей, начатой в 60-х и реализованной в 70-х годах, является...
Отражение на счетах бухгалтерского учета процесса приобретения: Процесс заготовления представляет систему экономических событий, включающих приобретение организацией у поставщиков сырья...
Берегоукрепление оползневых склонов: На прибрежных склонах основной причиной развития оползневых процессов является подмыв водами рек естественных склонов...
Дисциплины:
![]() |
![]() |
5.00
из
|
Заказать работу |
|
|
Технологичность конструкции литых заготовок
Литье является рациональным методом, так как при этом возможно выполнить самые сложные конструктивные формы деталей, подобрать материалы оптимальных характеристик и обеспечить минимальный вес детали. Технологичность конструкции литой детали достигается применением метода литья, соответствующего типу производства.
Отработка на технологичность литой детали включает: 1) использование передовых методов литья; 2) определение плоскости разъема модели с учетом имеющихся выступов или приливов на поверхности детали; 3) выбор базовых поверхностей при отливке с учетом технологических баз для механической обработки; 4) определение необходимого количества стержней, их конструкции и размеров; 5) устранение резких перепадов в толщине стенок и мест скопления металла; 6) установление допусков на черновые размеры и ряд других задач.
Литейные металлы и сплавы должны иметь высокую жидкотекучесть, что способствует хорошему заполнению формы, и обеспечивать требуемые физико-механические свойства детали.
Наибольшее количество литых деталей изготовляется из стали и чугуна. Для изготовления деталей, к которым предъявляются высокие физико-механические требования, применяются легированные стали и специальные чугуны. При отработке литых деталей на технологичность следует избегать применения дорогостоящих легированных сталей и чугунов, а также меди и медных сплавов, заменяя их более дешевыми и недефицитными. Детали из цветных сплавов обладают высокой антифрикционной и коррозионной устойчивостью, но во многих случаях эти сплавы можно заменить более дешевыми материалами, не снижая качества и, надежности детали. Детали из алюминиевых сплавов имеют широкое распространение в авиационной, приборостроительной, автотракторной и других отраслях промышленности. Алюминиевый сплав имеет низкий удельный вес в сравнении с удельным весом черных металлов, высокую жидкотекучесть, незначительные усадки, что способствует получению легких деталей сложной конфигурации. Такое же распространение имеют и магниевые сплавы, так как у них малый удельный вес и высокая устойчивость против коррозии. Применение цинковых сплавов для литья под давлением деталей арматуры автомобилей и тракторов, а также деталей приборов обеспечивает высокую технологичность. При выборе материала для литых деталей необходимо пользоваться тестированными литейными сплавами.
|
Технологичность конструкции горячештампованных заготовок
В условиях индивидуального производства применяется свободная ковка, а в условиях крупносерийного и массового производства – горячая штамповка. Горячештампованные заготовки имеют более высокие качество и чистоту поверхности, более высокую точность формы и размеров. Горячая штамповка выполняется с применением специальной технологической оснастки, поэтому она является высокопроизводительной. При отработке на технологичность горячештампованной детали необходимо предусмотреть свободное удаление отштампованной заготовки из штампа в плоскости, перпендикулярной плоскости разъема штампа. При горячей штамповке необходимо максимальное количество поверхностей получать в готовом виде, без механической обработки. При конструировании правых или левых деталей следует стре- миться к изготовлению их из одной заготовки. У деталей, имеющих форму тел вращения, плоскость разъема штампа должна быть перпендикулярна их оси; лишь при большой длине заготовки плоскость разъема может проходить через ось. Ребра и бобышки следует располагать в плоскости разъема.
Технологичность конструкции холодноштампованных заготовок
|
Холодная штамповка – высокопроизводительный метод, обеспечивающий высокое качество заготовок. Она рентабельна только при крупносерийном и массовом производстве, так как требует дорогостоящих штампов. При мелкосерийном и индивидуальном производстве холодная штамповка может выполняться только на универсальных штампах.
Холодноштампованные детали изготовляются из материалов, обладающих низким пределом текучести, большим удлинением и малой твердостью. Холодноштампованные детали обрабатываются с помощью вырубки или пробивки, гибки, вытяжки, холодной объемной штамповки, холодного выдавливания и т. д. Точность деталей, штампуемых вытяжкой, достигает 3-го класса. Отработка холодноштампованных деталей на технологичность включает: 1) обеспечение наиболее приемлемой формы детали с целью упрощения процесса штамповки, снижения расхода металла, снижения трудоемкости и стоимости изготовления; 2) подбор материала детали по физико-механическим свойствам и размерам, обеспечивающий качественную вытяжку; 3) простановку размеров на чертеже детали с учетом выбора технологических баз и др.
12. Виды заготовок.
В транспортной промышленности применяются следующие основные заготовки: а) отливки из чугуна, стали и цветных металлов; б) поковки и штамповки из стали и некоторых цветных металлов; в) прокат из стали и цветных металлов; г) штампо-сварные из стального проката и других металлов; д) штамповки и отливки из пластмасс; е) металлокерамические (порошковая металлургия).
Методы получения заготовок.
Получение заготовок литьем
Заготовки можно отливать в разовые, полупостоянные и постоянные формы.
Получение заготовок обработкой давлением
Процессы обработки металла давлением отличаются высокой производительностью, относительно малой трудоемкостью, обеспечивают экономное расходование металла и, как правило, способствуют улучшению механических свойств металла.
Заготовки могут быть получены ковкой, горячей штамповкой, холодной объемной штамповкой и холодной листовой штамповкой.
Свободная ковка. Она производится на ковочных молотах. Для получения фасонных заготовок деталей автомобилей и тракторов, изготовляемых из сортового проката, применяют пневматические или паровоздушные молоты. Свободную ковку целесообразно применять только при единичном производстве. Ковку на молотах также производят в подкладных штампах. Применение подкладных штампов позволяет увеличить производительность ковки в 5–6 раз. Применяется этот вид ковки в мелко- серийном производстве. Перед штамповкой в подкладных штампах заготовке придают свободной ковкой форму, близкую к форме заданной поковки. Допуск на размер штамповок, получаемых в подкладных штампах, примерно в 2–3 раза меньше, чем допуск при свободной ковке. В мелкосерийном производстве применяется ковка на радиально- ковочной машине с программным управлением. Точность размеров при холодной ковке колеблется в пределах от ±0,02 до ±0,2 мм и чистота поверхности соответствует 7–9-му классам, при горячей ковке точность колеблется в пределах от ±0,05 до 0,3 мм и чистота поверхности соответствует 1–3-му классам.
|
Горячая объемная штамповка. Горячая объемная штамповка может производиться на молотах, горизонтально-ковочных машинах (ГКМ), штамповочных прессах и ковочных вальцах. Штамповка на молотах применяется в серийном и массовом производстве. Заготовка требуемой конфигурации большей частью получается путем последовательной обработки в нескольких ручьях, выполненных в одном штампе.
Штамповкой на ГКМ изготовляют заготовки весом 0,1–100 кг. На ГКМ можно обеспечить высокое качество поковок за счет расположения волокон материала в наиболее выгодном направлении. Простые по форме заготовки при изготовлении на ГКМ можно получать без облоя, а сложные по форме заготовки – с небольшим облоем, не превышающим 1% веса заготовки. На ГКМ можно получать штампованные заготовки со сквозным отверстием и с глубокими глухими отверстиями. Штампованные заготовки можно получить из прутков и труб повышенной точности.
Штамповка на гидравлических, фрикционных и кривошипных прессах в автотракторной промышленности получила широкое применение. Штамповку на гидравлических прессах применяют для получения заготовок из легких и малопластичных сплавов, требующих небольших скоростей деформирования. Малая производительность гидравлических прессов вследствие их тихоходности повышает себестоимость штампованных заготовок по сравнению с себестоимостью штампованных заготовок, получаемых на прессах других типов. Штамповка на фрикционных прессах применяется в мелкосерийном и серийном производстве для получения заготовок из стали преимущественно в одноручьевых штампах и для резки в двух ручьях и более, а также для точной штамповки сложных заготовок из цветных сплавов.
|
Холодная объемная штамповка. Одним из наиболее экономичных технологических процессов получения заготовок крепежных и других видов мелких деталей (винты, болты, ролики, шарики, толкатели клапанов и т. д.) в больших количествах является холодная объемная штамповка (высадка) на специальных холодно- высадочных прессах-автоматах. Производительность автомата – до 400 шт./мин. Исходным полуфабрикатом для изготовления болтов является бунт проволоки диаметром от десятых долей миллиметра до 10–15 мм или калиброванный пруток диаметром более 8 мм.
Холодная листовая штамповка. В промышленности холодной листовой штамповкой получают основные детали кузова автомобиля, картеры, крышки, колпаки, диски и другие детали. Исходным материалом служат тонкие листы металла и ленты.
Операции холодной штамповки можно разделить на две группы.
1.Разделительные операции, посредством которых одна часть материала полностью или частично отделяется от другой: отрезка, вырубка, пробивка, надрезка, подрезка, обрезка, зачистка и калибровка.
2.Формоизменяющие операции, посредством которых плоская или пространственная заготовка превращается в пространственную деталь заданной формы и размеров: гибка, отбортовка, вытяжка.
Получение заготовок литьем
Получение заготовок литьем
Заготовки можно отливать в разовые, полупостоянные и постоянные формы.
Литье в разовые формы. Этот способ применяется при изготовлении заготовок из черных и цветных металлов с любыми размерами и весами. Производится литье в разовые сырые или сухие песчаные формы, в оболочковые (скорлупчатые) формы и по вы- плавляемым моделям (прецизионное).
Песчаные формы выполняются в опоках или без опок (почвенная формовка). Формы без опок изготовляются ручным способом, а в опоках – ручным и машинным способами.
Сухие (стержневые) формы применяют для получения ответственных отливок сложной конфигурации (цилиндр двигателя, рабочие колеса гидротурбин и т. п.). Форму собирают из стержней по шаблонам и кондукторам; она обеспечивает получение высокой точности заготовки. Заготовки, получаемые литьем в оболочковые формы, изготовленные из песчано-смоляных смесей, имеют более высокие точность размеров и формы и чистоту поверхности по сравнению с отливками, получаемыми при литье в обычные песчаные формы. В оболочковых формах изготовляют отливки из серого, ковкого и сверхпрочного чугуна, стали и цветных сплавов. Этим методом изготовляют обычно сложные и ответственные заготовки деталей весом до 100 кг. Способ отливки в оболочковые формы сокращает потребление литейной земли в 10 раз, повышает производительность труда в 10–15 раз, значительно улучшает условия труда в литейном цехе. Этот способ особенно выгоден для крупносерийного и массового выпуска деталей. Он позволяет получать стальные отливки с толщиной стенок 3 мм, а отливки из алюминиевых сплавов с толщиной стенок 1 мм. Точность отливок соответствует 4–5-му классам точности, а чистота поверхности 3–4-му классам.
|
Литье по выплавляемым моделям позволяет получить заготовки сложной формы, настолько близкой к готовой детали, что в отдельных случаях частично или полностью исключается механическая обработка. По выплавляемым моделям обычно изготовляют отливки небольшого веса (до 3 кг), хотя в отдельных случаях они могут выполняться и значительно большего веса. Минимальная толщина стенок отливок из чугуна составляет 0,15 мм, а из алюминиевых сплавов – 0,8 мм. Можно отливать заготовки зубчатых колес с зубьями, шлицевые валики со шлицами и т. п. Для получения большей плотности металла в отливке применяют центробежный или центробежно-вакуумный способ заливки.
Литье в полупостоянные формы. При этом способе формы изготовляют из гипса, цемента, кирпича и камня. Гипсовые формы применяют для изготовления отливок из чугуна и цветных сплавов весом до 1 т. Отливки в гипсовые формы могут иметь толщину стенок 1–1,5 мм, а отливки из алюминиевых сплавов с использованием вакуума – толщину стенок 0,2 мм.
Этим способом изготовляют отливки зубчатых колес с формообразованием зубьев, шлицевые валы, лопасти турбин и др. Цементные формы и формы из кирпича в автотракторной промышленности не применяются. Формы из камня обеспечивают получение чугунных и бронзовых отливок с чистотой поверхности по 6-му классу и не требуют отбела поверхностного слоя. Формы из талькоактинолитохлоритового сланца применяют вместо металлических кокилей при массовом производстве.
Литье в постоянные формы. Широкое применение имеет литье в металлические формы – кокиль. Этот вид литья позволяет получать отливки с точностью по 4–7-му классам и с чистотой поверхности по 3–4-му классам. В металлические формы можно отливать заготовки из стали, чугуна и цветных сплавов с весом от нескольких граммов до нескольких тонн.
Для повышения стойкости металлических форм их охлаждают водой. Этот метод экономически целесообразно применять при серийном и массовом производстве. Он позволяет повысить производительность труда по сравнению с литьем в песчаные формы в 2 раза и более, уменьшить более чем в 4 раза производственные площади и снизить в 2 раза затраты на формовочные материалы.
Литье под давлением производится в основном в постоянные формы и применяется для изготовления сложных тонкостенных отливок с глубокими плоскостями и сложными пересечениями стенок. Отливки имеют мелкозернистую структуру, что повышает прочность металла в 1,5 раза по сравнению с прочностью отливок, получаемых в песчаных формах.
Себестоимость форм для литья под давлением высокая, поэтому такой способ применяется в крупносерийном и массовом производстве.
Для литья втулок, колец, труб и других деталей вращения применяется центробежное литье на центробежных машинах. Особенностью этого процесса является образование внутренней полости без применения стержней и возможность получения многослойных отливок. Точность стальных и чугунных отливок, полученных центробежным литьем, соответствует 6–8-му классам и чистота поверхности – 3-му классу.
|
|
Своеобразие русской архитектуры: Основной материал – дерево – быстрота постройки, но недолговечность и необходимость деления...
Опора деревянной одностоечной и способы укрепление угловых опор: Опоры ВЛ - конструкции, предназначенные для поддерживания проводов на необходимой высоте над землей, водой...
Таксономические единицы (категории) растений: Каждая система классификации состоит из определённых соподчиненных друг другу...
Индивидуальные очистные сооружения: К классу индивидуальных очистных сооружений относят сооружения, пропускная способность которых...
© cyberpedia.su 2017-2024 - Не является автором материалов. Исключительное право сохранено за автором текста.
Если вы не хотите, чтобы данный материал был у нас на сайте, перейдите по ссылке: Нарушение авторских прав. Мы поможем в написании вашей работы!