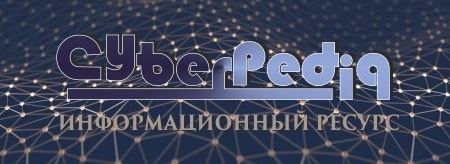
Индивидуальные очистные сооружения: К классу индивидуальных очистных сооружений относят сооружения, пропускная способность которых...
Кормораздатчик мобильный электрифицированный: схема и процесс работы устройства...
Топ:
Устройство и оснащение процедурного кабинета: Решающая роль в обеспечении правильного лечения пациентов отводится процедурной медсестре...
Методика измерений сопротивления растеканию тока анодного заземления: Анодный заземлитель (анод) – проводник, погруженный в электролитическую среду (грунт, раствор электролита) и подключенный к положительному...
Комплексной системы оценки состояния охраны труда на производственном объекте (КСОТ-П): Цели и задачи Комплексной системы оценки состояния охраны труда и определению факторов рисков по охране труда...
Интересное:
Подходы к решению темы фильма: Существует три основных типа исторического фильма, имеющих между собой много общего...
Как мы говорим и как мы слушаем: общение можно сравнить с огромным зонтиком, под которым скрыто все...
Распространение рака на другие отдаленные от желудка органы: Характерных симптомов рака желудка не существует. Выраженные симптомы появляются, когда опухоль...
Дисциплины:
![]() |
![]() |
5.00
из
|
Заказать работу |
|
|
В строительства при выполнении земляных работ находят широкое применение одноковшовые и многоковшовые экскаваторы. Автоматизация современных экскаваторов на базе электронной и микропроцессорной техники позволяет повысить безопасность их эксплуатации, уменьшить расход горюче-смазочных материалов, упростить управление техникой. Современные микропроцессорные устройства позволяют контролировать перегрузки машины, превышение скорости, устойчивость, выполнять основные управляющие функции, обеспечивать необходимое качество и точность производства работ. Основными направлениями их автоматизации являются: защита от перегрузок и аварийных режимов работы; регулирование процесса копания, обеспечивающего максимальное использование мощности двигателя, программное управление отдельными операциями и учет объема выполненной работы.
В настоящее время главное внимание уделяется автоматизации операции копания и защиты экскаватора от аварийных режимов работы. Эта задача решается за счет изменения толщины срезаемого грунта путем регулирования положения стрелы гидроцилиндрами подъема и опускания (рис.3.5). Измерение нагрузки может осуществляться либо путем непосредственного определения усилия резания F р с помощью датчиков, установленных на ковше, либо путем измерения параметров косвенно характеризующих усилие нагрузки на рабочий орган. В гидравлических экскаваторах наиболее простым способом оценки нагрузки на ковш является измерение давления рабочей жидкости в напорной полости гидроцилиндра поворота рукояти. Сигнал сдатчика давления U д подается на вход автоматического регулятора, состоящего из элемента сравнения ЭС и блока управления БУ, где он сравнивается с задающим сигналом U зад,
|
|
Перспективным направлением автоматизации одноковшовых экскаваторов является внедрение на них элементов программного управления. Перевод отдельных операций цикла на программное управление позволяет значительно снизить утомляемость машиниста и поднять эксплуатационную производительность. Задачи программного управления решаются на базе использования микропроцессорной техники. Установка на экскаваторе бортовой управляющей микроЭВМ или микроконтроллера позволяет контролировать основные параметры работы экскаватора, а также после ручного выполнения одного или нескольких циклов работы, запоминать последовательность и основные показатели выполнения отдельных операция и затем многократно повторять их в автоматическом режиме.
Из экскаваторов непрерывного действия в строительстве наибольшее применение нашли траншеекопатели, для которых перспективными являются автоматические устройства управления с использованием лазерного луча в качестве опорной линии. При рытье траншеи в начале разрабатываемого участка устанавливают лазерный излучатель ЛИ, который центрируется над точкой, закрепляющей ось траншеи (рис.3.6). Луч лазера направляется вдоль траншеи с проектным углом наклона. На рабочем органе траншеекопателя устанавливается фотоприемное устройство ФПУ, сигналы с которого поступают на блок управления БУ. Сигнал с блока управления через электрозолотник ЭЗ управляет гидроцилиндром подъема и опускания рабочего органа, поддерживая все время совпадение оптической оси фотоприемника с осью лазерного луча. Задание глубины копания траншеи обеспечивается путем установки фотоприемника в заданное положение. Для этого фотоприемник устанавливается на телескопической штанге и снабжается механизмом перемещения МП и следящей системой управления, которая позволяет дистанционно из кабины машиниста выставлять ФПУ на необходимую высоту H0. В качестве датчика обратной связи используется щуповой датчик ДЩВ.
|
В последние годы большое внимание уделяется разработки и производству систем, позволяющих существенно облегчить процесс выполнения работ по разработки грунта. В первую очередь это системы нивелирования для контроля положения ковша экскаватора. Установив приемник на рукоять экскаватора машинист получает возможность самостоятельно контролировать текущий уровень разработки грунта. В качестве примера рассмотрим систему Level-X, которая представляет собой цифровой индикатор уровня и уклона. Точность позиционирования ковша составляет около 5 см по высоте и 0,1% в уклоне. Данное устройство имеет несколько режимов работы: глубина, глубина и уклон, профиль, режим измерения, режим горизонтирования экскаватора. Неотъемлемой частью системы является лазерный нивелир, по которому задаются начальные значения (нулевые отметки).
Современными системами автоматизации экскаваторов являются 2D системы, которые в отличие от простых лазерных систем, не требует прямой видимости лазерного нивелира. Они могут быть использованы при таких работах, когда не видно ковша и рукояти экскаватора, например при дноуглубительных работах или подготовке глубоких котлованов. К таким системам относится система Proleс Digmaster, работающая в реальном времени и позволяющая пользователю максимально быстро и точно выполнять работу. Эта система не только показывается положение ковша, но с ее помощью могут быть обработаны данные лазерного или GPS приемника для достижения четкого наклона, глубины и профиля. Данные поступающие от датчиков, мгновенно обрабатываются и поступают на дисплей. Если работы ведутся по сигналам приемника лазерного луча или GPS навигатора, то не возникает необходимости создания модели вручную, так как система автоматически примет данные сигнала и передаст их на индикатор в кабине. Система индикации многофункциональна. Она позволяет пользователю панорамировать и изменять масштаб обзора на дисплее, чтобы детально следить за работой ковша или видеть его целиком в совокупности с машиной. Данные на дисплее дают информацию в реальном времени о радиусе, высоте, положении вращения, а также о расстоянии до определенной глубины или заданной позиции.
|
|
|
Акселерометр TS-1 позволяет измеряемые с помощью GPS-приемника координаты редуцировать непосредственно на зубья ковша. Таким образом, на экране бортового компьютера графически отображается точное положение режущей кромки ковша относительно проектной поверхности. Если конструкция экскаватора предусматривает возможность задания поперечного наклона ковша, то в систему может быть включен еще один дополнительный акселерометр. Все датчики образуют единый информационно-измерительный комплекс с использованием интерфейса CAN.
В отличие от классической технологии реализации любого проекта, состоящей из пяти фаз (съемка, проектирование, вынос в натуру, земляные работы, контроль), использование системы 3Dxi позволяет свести ее всего к трем, объединив фазы выноса в натуру, земляных работ и контроля в одну. После загрузки цифрового проекта в бортовой компьютер оператор видит на экране изображение цифрового проекта, положение машины на нем и высотное отклонение ковша от нулевой отметки в графическом и цифровом виде. Таким образом, нет никакой необходимости в выносе в натуру. Использование экскаваторной системы 3Dxi требует наличия на рабочем объекте нескольких закрепленных (опорных) точек с известными координатами в системе координат проекта. Как правило, эти точки располагаются по периметру строительной площадки. Изначально система 3Dxi работает в общеземной системе координат WGS-84. Для того чтобы сделать возможной работу системы в местных координатах проекта выполняют так называемую локализацию. Первым делом выбирают место для установки базовой станции. При выборе места базы учитывают отсутствие вблизи высоких препятствий и источников радиопомех. Основное требование – обеспечение неизменного положения приемной антенны во время работ. Для выполнения локализации антенну подвижного приемника последовательно устанавливают на каждой опорной точке и выполняют измерение. Полученные результаты сразу берутся в расчет параметров локализации. Для каждого проекта достаточно иметь пять планово-высотных точек.
Для обеспечения точного расчета координат зубьев ковша на рабочем объекте выполняется калибровка основных узлов системы. На машине определяется геометрическое положение GPS-антенн относительно оси вращения стрелы, делаются замеры длин стрелы, рукояти, высоты и ширины ковша. Данная информация заносится в память бортового компьютера.
|
|
Таксономические единицы (категории) растений: Каждая система классификации состоит из определённых соподчиненных друг другу...
Своеобразие русской архитектуры: Основной материал – дерево – быстрота постройки, но недолговечность и необходимость деления...
Автоматическое растормаживание колес: Тормозные устройства колес предназначены для уменьшения длины пробега и улучшения маневрирования ВС при...
Опора деревянной одностоечной и способы укрепление угловых опор: Опоры ВЛ - конструкции, предназначенные для поддерживания проводов на необходимой высоте над землей, водой...
© cyberpedia.su 2017-2024 - Не является автором материалов. Исключительное право сохранено за автором текста.
Если вы не хотите, чтобы данный материал был у нас на сайте, перейдите по ссылке: Нарушение авторских прав. Мы поможем в написании вашей работы!