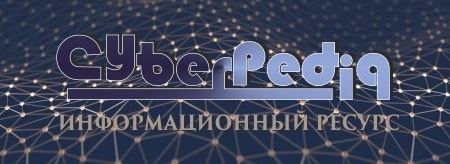
Семя – орган полового размножения и расселения растений: наружи у семян имеется плотный покров – кожура...
Индивидуальные и групповые автопоилки: для животных. Схемы и конструкции...
Топ:
Когда производится ограждение поезда, остановившегося на перегоне: Во всех случаях немедленно должно быть ограждено место препятствия для движения поездов на смежном пути двухпутного...
Установка замедленного коксования: Чем выше температура и ниже давление, тем место разрыва углеродной цепи всё больше смещается к её концу и значительно возрастает...
Устройство и оснащение процедурного кабинета: Решающая роль в обеспечении правильного лечения пациентов отводится процедурной медсестре...
Интересное:
Финансовый рынок и его значение в управлении денежными потоками на современном этапе: любому предприятию для расширения производства и увеличения прибыли нужны...
Уполаживание и террасирование склонов: Если глубина оврага более 5 м необходимо устройство берм. Варианты использования оврагов для градостроительных целей...
Наиболее распространенные виды рака: Раковая опухоль — это самостоятельное новообразование, которое может возникнуть и от повышенного давления...
Дисциплины:
![]() |
![]() |
5.00
из
|
Заказать работу |
|
|
Д.Я. Паршин
ОСНОВЫ АВТОМАТИЗАЦИИ
И РОБОТОТЕХНИКИ
ЛЕКЦИИ
Раздел «Автоматизация и роботизация строительных работ»
Ростов-на-Дону
2013
Автоматизация и роботизаци строительных работ
Средства автоматического управления землеройно-
Транспортными машинами
В строительстве для выполнения большой группы земляных работ, таких как возведение насыпи, рытье котлованов и выемок, профилирование земляного полотна, планировка площадок и др., широко применяют землеройно-транспортные машины. Землеройно-транспортные машины - это многоцелевые машины, используемые для планировки площадок и дорог, перемещения грунта, выполнения других земляных работ. К ним относятся бульдозеры, скреперы, автогрейдеры, экскаваторы.
Основными задачами их автоматизации являются упрощения управления основными механизмами, регулирование нагрузки на режущие органы, обеспечение требуемого качества обрабатываемой поверхности, мониторинг состояния, защита машин при возникновении аварийных моментов во время эксплуатации, а также контроль и учет работы машин.
В основу построения САР режимов копания положен принцип стабилизации нагрузки приводного двигателя от сил сопротивления резанию путем изменения толщины срезаемого слоя. Регулируемым параметром в этих системах является нагрузка на двигатель, а регулирующим - положение рабочего органа. Величина нагрузки контролируется косвенными методами путем измерения крутящего момента, тягового усилия, угловой скорости вала двигателя или степени буксования ведущих колес.
Система простейшей стабилизации тягового усилия прицепного скрепера изображена на рис. 3.1. Она состоит из датчика тягового усилия I, релейного регулятора II и привода управления III. В качестве датчика используется месдоза гидравлического динамометра 1. Входным элементом релейного регулятора служит мерный гидроцилиндр 2. Положение рабочего органа, а значит и толщина срезаемой стружки зависят от положения штока привода. Когда сопротивление грунта соответствует тяговому усилию скрепера, давление в поршневой полости мерного цилиндра 2, связанной непосредственно с месдозой гидравлического динамометра 1, уравновешивается упругостью пружины, шток 3 не перемещается и переключатель 4 находится в среднем положении. В случае несоответствия сопротивления грунта и тягового усилия переключатель 4 подает сигнал управления на один из электромагнитов 5 золотника 6, который включает гидроцилиндр 7 на подъём или опускание ковша.
|
Для машин с колесным движителем используют схему, основанную на зависимости тяговой мощности N т, от величины буксования движителей d. Установлено, что для автогрейдеров полное использование мощности тягового двигателя наступает при степени буксования ведущих колес равной 18–20%. Функциональная схема системы приведена на рис.3.2. Регулируемой величиной здесь служит коэффициент буксования, , который поддерживается САР в заданных пределах за счет изменения толщины срезаемой стружки h. Угловые скорости w1 и w2 ведущего и ведомого колес, измеренные с помощью тахогенераторов ТГ1 и ТГ2, поступают на вычислительное устройство ВУ, которое вырабатывает действительное значение коэффициента буксования d1. Его величина является первичным управляющим сигналом, который затем сравнивается с заданным значением d3 и в зависимости от знака рассогласования Dd включает то или иное исполнительное реле релейного усилителя. Реле воздействуют на гидравлический исполнительный механизм, который выполняет подъём или опускание рабочего органа.
Для бульдозеров, автогрейдеров и скреперов при формировании полотна с заданным поперечным уклоном и продольным профилем применяют системы нивелирования, которые делятся на две категории: индикаторные и автоматические. Индикаторные системы — это простейшие системы, позволяющие оператору машины ориентироваться по индикации светодиодного дисплея приемника, установленного в кабине. Они не освобождают оператора от управления рабочим органом строительной машины, но намного облегчают работу и улучают ее качество. Автоматические системы управления строительной техникой встраиваются в гидравлическую систему управления механизмом и позволяют автоматически удерживать рабочий орган машины в заданном положении.
|
Автоматически системы нивелирования, позволяющие контролировать положение рабочего органа по высоте и поперечному уклону, называются 2D-системами. Для работы с системой необходима высотная привязка машины по месту проведения работ. Находят применение системы нивелирования с использованием ультразвуковых датчиков, лазерных построителей плоскости, твердотельных гироскопов.
Ультразвуковые системы нивелирования относятся к копирным устройствам, в которых в качестве привязки используется копирная струна, разбиваемая на длине захватки через рассчитанные промежутки. После разбивки копирной струны по высотным отметкам рабочий орган машины, с закрепленной на нем системой нивелирования, устанавливается на захватку: отвал устанавливается на поверхность, а ультразвуковой датчик выставляется над копирной струной. С панели управления задается глубина выемки или высота отсыпки грунта, отвал автоматически перемещается на заданную высоту. Машинист начинает проход по захватке, при этом отвал распределяет материал автоматически удерживаясь в проектных отметках благодаря ультразвуковому датчику установленному над струной и в проектном уклоне за счет датчика наклона, установленного на отвале. Недостатком систем с использованием копирной струны является трудность удержания ультразвукового датчика над струной, так как никаких видимых ориентиров кроме датчика, расположенного примерно в 700 мм от копирной струны, нет. Облегчить процесс удержания отвала над копирной струной можно за счет использования ультразвуковых датчиков с несколькими излучателями.
|
Процесс профилирования значительно упрощается при использовании лазерных устройств нивелирования. Обычно радиус лазерной плоскости, создаваемой прибором, составляет 500-700 метров, что позволяет за одну установку прибора, без разбивки и исполнительной съемки, за короткое время спрофилировать чистовой верхний слой. В качестве базовой линии в этих системах нивелирования используется лазерный луч. Такое устройство состоит из лазерного излучателя ЛИ (рис.3.3), устанавливаемого на штативе 4, и фотоприемного устройства ФПУ с механизмом перемещения МП (электродвигатель с редуктором), размещаемых на рабочей машине. Лазерный излучатель имеет лазер с коллиматором, вращающуюся призму 2, электродвигатель с редуктором 3, уровень и микрометрические винты для задания угла наклона базовой линии, который может задаваться от 0 до 3°. Луч лазера диаметром 1—1,5 мм с углом расходимости 7—8' подается на коллиматор, который уменьшает расходимость луча до 30" и увеличивает его диаметр до 3 см. Из коллиматора луч подается на вращающуюся призму 2, где преломляется на 90° и выходит в пространство на высоте h, сканируя плоскость. Питается лазерный излучатель от аккумулятора 5. Фотоприемное устройство (рис.3.3, б) состоит из трех световодов, расположенных один над другим и разделенных между собой экранами. Каждый световод оканчивается фотодиодом ФД, подключенным на вход усилителя У. Световоды имеют возможность принимать сигнал (луч) из любой точки горизонта в диапазоне 360°. Световоды вырабатывают сигнал отклонения координаты рабочего органа машины от заданной, который после усиления подается на управление положением рабочего органа машины. Веерный луч или плоскость могут быть расположены горизонтально или под заданным углом к горизонту. Бортовое оборудование включает фотоприемное устройство (фотодетектор) и устройство обработки данных. Фотодетектор имеет круговой обзор и устанавливается на штанге, прикрепляемой к рабочему органу машины. Лазерные системы контроля обеспечивают необходимую точность и дальность действия, удобна в эксплуатации. При автоматическом управлении положением рабочих органов выходной сигнал фотоприемного устройства подается на электрогидрозолотники, которые управляют работой гидроцилиндров подъема и опускания рабочего органа машины. Для одновременного управления положением отвала по высоте и в поперечной плоскости машин на машине необходимо установить два фотоприемника. Один из них устанавливается на телескопической мачте, располагаемой на продольной оси симметрий машины, а второй — на боковой мачте у края отвала. Центральный фотоприемник обслуживает подсистему управления гидроцилиндрами подъема отвала, а боковой — подсистему управления гидроцилиндрами бокового наклона отвала. Независимое функционирование двух подсистем, управляемых одним лазерным лучом, обеспечивает в совокупности профилирование грунтовой полосы одновременно в продольном и поперечном направлениях.
|
При автоматизации землеройно-транспортных машин интерес представляют комбинированные системы управления, обеспечивающие регулирование режимов работы, контроль и регулирование положение отвала по высоте и в плане. К таким системам относятся отечественные системы автоматизации "Автоплан-10", "Копир-Автоплан-10", "Комбиплан-10Л". Устройство и принцип действия таких систем автоматизации рассмотрим на примере системы "Комбиплан-10ЛП". Она позволяет стабилизировать положение отвала в продольной плоскости в бескопирном и копирном режимах, регулировать положение отвала в поперечной плоскости, а также защищать двигатель от перегрузок. Система состоит из пяти подсистем, каждая из которых имеет замкнутый контур управления. В ней используются лазерная система, а также специальные датчики положения (рис.3.4). Стабилизация углового положения отвала в поперечной плоскости выполняется. подсистемой управления, включающей датчик углового положения ДП, элементы сравнения ЭС1 и усиления УС1 сигналов и исполнительный механизм ИМ1. Измерение угла наклона отвала в поперечной плоскости проводится маятниковым датчиком ДКБ, который преобразует угол между базовой плоскостью и гравитационной вертикалью в электрический сигнал. Чувствительный элемент датчика - маятник выполнен в виде тонкостенного неуравновешенного цилиндра, закрепленного на конце горизонтальной оси. Маятник вращается в подшипниках, а угол его поворота измеряется индуктивным преобразователем. Датчик ДКБ устанавливается на тыльной стороне отвала. При поперечном наклоне отвала информация с датчика преобразуется в управляющие сигналы, которые обрабатываются исполнительным механизмом ИМ1.
Угловое положение отвала в продольной плоскости в автономном режиме стабилизируется аналогичной подсистемой управления, состоящей из маятникового датчика ДКБ, элемента сравнения ЭС2, усилителя УС2 и исполнительных гидроцилиндров ИМ2. Датчик ДКБ, контролирующий угловое положение отвала a0, устанавливается на толкающем брусе бульдозера. Сигнал с выхода датчика сравнивается с опорным сигналом и в случае его несоответствия заданному уровню вырабатывается сигнал ошибки, который подается на исполнительные гидроцилиндры ИМ2, корректирующие положение отвала по высоте. Третья подсистема управления, входящая в состав системы "Комбиплан-10ЛП" служит для стабилизации положения отвала бульдозера по высоте h относительно опорной плоскости, задаваемой лазерным лучом. В нее входит лазерный излучатель ЛИ, фотоприемное устройство ФПУ, контролирующее положение отвала относительно лазерного луча. Устройство ФПУ устанавливается на специальной штанге, которая закрепляется на тыльной стороне отвала. При отклонении фотоприемника ФПУ от оси лазерного луча на его выходе вырабатывается сигнал ошибки, который подается на элемент сравнения ЭС2 подсистемы стабилизации положения отвала в продольной плоскости. Как и в автономном режиме сигнал ошибки через усилитель УС2 воздействует на гидроцилиндры ИМ2.
|
Глубина срезания при заданной опорной лазерной плоскости устанавливается дистанционно из кабина машиниста с помощью подсистемы управления перемещением фотоприемного устройства ФПУ. В эту подсистему входят датчик ДЩВ положения фотоприемника, устройство сравнения ЭСЗ, усилитель УСЗ и механизм перемещения МП, а также задатчик, размещаемый на пульте управления;, При отклонении фотоприемника ФПУ от заданного уровня в подсистеме появляется сигнал ошибки U Dh, который подается на ЭСЗ и отрабатывается механизмом перемещения МП. Датчик положения ДЩБ представляет собой щуповой преобразователь, аналогичный по конструкции маятниковому датчику ДКБ и отличается от него тем, что маятниковый чувствительный элемент в данном случае заменен рычажным щупом. Во время работы машины щуп скользит по копиру или бордюру. Перемещения щупа передаются вторичному индуктивному преобразователю.
В состав аппаратуры "Комбиплан-10ЛП" также входит подсистема, защищающая ходовой двигатель от перегрузок. В случае возрастания усилия резания грунта и превышения им максимально допустимых значений происходит снижение частоты вращения выходного вала двигателя и падение мощности машины. Подсистема автоматической защиты от перегрузок обеспечивает снижение усилия резания грунта до заданного значения путем поднятия отвала бульдозера. В качестве контролируемого параметра, характеризующего загрузку двигателя, в данном случае выбрана частота вращения n дв вала ходового двигателя, которая измеряется тахогенератором ТГ, установленным на валу двигателя. Напряжение с выхода тахогенератора, пропорциональное частоте вращения, сравнивается элементом ЭС4 и результат сравнения D U з подается одновременно на вход подсистем управления положением отвала и фотоприемника.
Рассмотренные разработки послужили основой создания современных микропроцессорных систем управления режимами работы и положением рабочих органов строительно-дорожных машин. Их особенностью является наличие необходимых датчиков контроля состояния машины и ее технологических параметров, автоматический сбор информации с датчиков и ее обработка в соответствии с заложенными законами управления.
Особый интерес для строителей представляют средства автоматизации, позволяющие выполнять контроль работы машин и исключить нецелевое их использование. Мониторинг мобильной строительной техники подвижных позволяет задавать границы рабочих зон, при попытке покинуть которые диспетчер получает SMS-сообщение. Кроме этого, системы слежения дают возможность фиксировать показания датчиков и параметры работы агрегатов, сравнить их с технологической картой строительного объекта.
Новым направлением автоматизации землеройно-транспортных систем являются 3D-системы нивелирования, которые находят активное применение при выполнении земляных работ бульдозерами и экскаваторами, а также при профилировании дорожного полотна автогрейдерами.
3D управление позволяет достигнуть высокой точности выравнивания, обеспечить соответствие геометрии сложной поверхности, управляя ножом грейдера в реальном времени, выравнивая всегда строго по линии и с заданным уровнем высоты. Основной задачей этих систем является подготовка цифровой модели проекта, его загрузка и обучение заказчика тому, как все оборудование должно работать в комплексе, именно поэтому 3D-системы нивелирования считаются не дополнительным оборудованием, а технологией, позволяющей качественно изменить технологию работ. Цифровая 3D система на основе GPS, позволяющая в ручном режиме формировать поверхность любой сложности в соответствии с цифровой моделью проекта. Точность таких системы составляет 1 см в плане, 3 см по высоте. В комплект 3D-систем входят GPS/ГЛОНАСС приемник, базовая GPS/ГЛОНАСС станция, комплект переносного специализированного GPS/ГЛОНАСС приемника для строителей, система позиционирования положения рабочего органа машины панель управления и контроля проведения работ, специализированное программное обеспечение.
Данные о положении машины поступают от системы позиционирования в панель управления, где производится вычисление точного положения режущей кромки рабочего органа машины. Результаты сравниваются с предварительно загруженным в панель проектом формируемой поверхности. При работе в автоматическом режиме система регулирует положение рабочего органа, используя электрогидроклапаны. При работе в ручном режиме оператор ориентируется по информации, представленной на панели управления, и световым индикаторам.
Литература
1. Автоматизация и роботизация строительства: Учеб. пособие / А.Г. Булгаков, В.А. Воробьев, С.И. Евтушенко, Д.Я. Паршин. — М.: РИОР: ИНФРА-М, 2013. — 452 с.
2. Автоматизация строительного производства / А.Г. Булгаков и др. Юж.-Рос. гос. техн. ун-т. — Новочеркасск: ЮРГТУ, 2006. — 268 с.
3. Паршин Д.Я. Основы автоматизации и роботизации / РГСУ — Ростов н/Д, 2013. — 147 с.
Д.Я. Паршин
ОСНОВЫ АВТОМАТИЗАЦИИ
И РОБОТОТЕХНИКИ
ЛЕКЦИИ
Раздел «Автоматизация и роботизация строительных работ»
Ростов-на-Дону
2013
|
|
Кормораздатчик мобильный электрифицированный: схема и процесс работы устройства...
Организация стока поверхностных вод: Наибольшее количество влаги на земном шаре испаряется с поверхности морей и океанов (88‰)...
Архитектура электронного правительства: Единая архитектура – это методологический подход при создании системы управления государства, который строится...
Механическое удерживание земляных масс: Механическое удерживание земляных масс на склоне обеспечивают контрфорсными сооружениями различных конструкций...
© cyberpedia.su 2017-2024 - Не является автором материалов. Исключительное право сохранено за автором текста.
Если вы не хотите, чтобы данный материал был у нас на сайте, перейдите по ссылке: Нарушение авторских прав. Мы поможем в написании вашей работы!