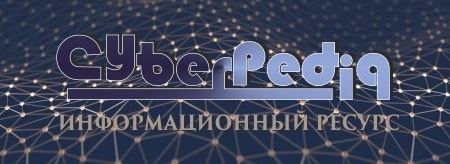
Папиллярные узоры пальцев рук - маркер спортивных способностей: дерматоглифические признаки формируются на 3-5 месяце беременности, не изменяются в течение жизни...
Архитектура электронного правительства: Единая архитектура – это методологический подход при создании системы управления государства, который строится...
Топ:
Комплексной системы оценки состояния охраны труда на производственном объекте (КСОТ-П): Цели и задачи Комплексной системы оценки состояния охраны труда и определению факторов рисков по охране труда...
Отражение на счетах бухгалтерского учета процесса приобретения: Процесс заготовления представляет систему экономических событий, включающих приобретение организацией у поставщиков сырья...
Выпускная квалификационная работа: Основная часть ВКР, как правило, состоит из двух-трех глав, каждая из которых, в свою очередь...
Интересное:
Берегоукрепление оползневых склонов: На прибрежных склонах основной причиной развития оползневых процессов является подмыв водами рек естественных склонов...
Подходы к решению темы фильма: Существует три основных типа исторического фильма, имеющих между собой много общего...
Средства для ингаляционного наркоза: Наркоз наступает в результате вдыхания (ингаляции) средств, которое осуществляют или с помощью маски...
Дисциплины:
![]() |
![]() |
5.00
из
|
Заказать работу |
|
|
О.В. Дорогов
Проектирование ремённых передач
Методические указания для студентов,
выполняющих курсовые работы и проекты
по дисциплинам «Детали машин», «Основы проектирования»
Тверь 2018
УДК 62-2
ББК 34.445я7
Рецензент доцент кафедры МПРМ ТвГТУ к.т.н. Крылов К.С.
Дорогов, О.В. Проектирование ремённых передач: метод. указания / О.В. Дорогов. Тверь: ТвГТУ, 2018. 40 с.
Приводятся общие сведения о конструкции и основных параметрах ремённых передач. Также изложена методика расчета ремённых передач, приведены необходимые справочные материалы и примеры расчетов плоскоремённых и клиноремённых передач по классической методике и с использованием автоматизированного проектирования.
Ориентированы на студентов, выполняющих курсовые работы и проекты по дисциплинам «Детали машин», «Основы проектирования»
Рассмотрены и рекомендованы к изданию на заседании кафедры «Техническая механика» (протокол № 5 от 19.12.2017 г.)
© Тверской государственный
технический университет, 2018
© Дорогов О.В., 2018
СОДЕРЖАНИЕ
Введение | 4 |
1. Описание ремённых передач | 5 |
1.1. Общие сведения | 5 |
1.2. Плоские и клиновые ремни | 6 |
1.3. Шкивы плоскоремённых и клиноремённых передач | 7 |
1.4. Геометрические и кинематические параметры | 8 |
1.5. Силы и напряжения в ветвях ремня | 9 |
2. Проектирование плоскоремённых и клиноремённых передач | 11 |
2.1. Формирование исходных данных | 11 |
2.2. Критерии работоспособности и расчёта | 12 |
2.3. Методика расчёта | 17 |
3. Примеры расчётов | 22 |
3.1. Пример расчёта плоскоремённой передачи | 22 |
3.2. Пример расчёта клиноремённой передачи | 26 |
4. Расчёт ремённой передачи в модуле APM Trans | 31 |
Библиографический список | 36 |
Приложения | 36 |
ВВЕДЕНИЕ
|
Важным этапом успешного освоения дисциплин «Детали машин и основы конструирования», «Основы проектирования», «Прикладная механика» является выполнение курсовых работ и проектов. Объектом курсового проектирования является электромеханический привод исполнительного механизма. В типовых заданиях на проектирование электромеханический привод включает в себя двухступенчатый редуктор или одноступенчатый редуктор и передачу гибкой связью – ремённую или цепную.
В имеющихся учебно-методических разработках проектированию ремённых передач уделяется недостаточно внимания. В результате студенты вынуждены искать необходимую информацию в других источниках, что затрудняет работу над курсовыми работами и проектами. В настоящих методических указаниях приведены общие сведения о конструкции и основных параметрах ремённых передач и изложена методика расчета ремённых передач.
В зависимости от типа ремня различают плоскоремённые, клиноремённые, поликлиновые, круглоремённые и зубчато-ремённые передачи. В настоящей разработке уделено внимание плоскоремённым и клиноремённым передачам как наиболее распространённым в учебном проектировании. Для таких передач приведены необходимые справочные материалы и примеры расчётов по классической методике и с использованием автоматизированного проектирования. Методика проектирования поликлиновых передач приведена в работах [1-2]. В работах [3-4] методика проектирования поликлиновых, круглоремённых и зубчато-ремённых передач проиллюстрирована на конкретных примерах.
Расчёт ремённой передачи включает в себя два основных этапа – проектный, проверочный. Проектный расчёт заключается в определении геометрических параметров передачи, в том числе площади поперечного сечения ремня (плоскоремённая передача), количества ремней (клиноремённая передача). Проверочный расчёт заключается в проверке работоспособности спроектированной передачи при заданных условиях нагружения. После выполнения проектного и проверочного расчётов передачи, а также определения нагрузки на её валы и опоры выполняется конструирование шкивов.
|
Расчёт ремённой передачи связан с расчётом валов и их опор. Геометрические параметры ступицы шкива зависят от величины её посадочного диаметра, который определяется при проектном расчёте вала. Нагрузка на валы и опоры ремённой передачи используется при их проверочном расчёте.
Методика проектирования ремённой передачи, приведённая в данной методической разработке, базируется на положениях, изложенных в литературе [1-4]. Автоматизированный расчёт осуществляется в модуле APM Trans системы APM WinMachine [5].
ОПИСАНИЕ РЕМЁННЫХ ПЕРЕДАЧ
Общие сведения
Ремённая передача состоит из шкивов 1 и 2, установленных на валах, и ремня 3, охватывающего шкивы (Рис. 1 а). Также конструкция ремённой передачи может включать в себя натяжной ролик 4 (Рис. 1 б). Движение осуществляется за счёт трения или зацепления между шкивами и ремнём.
а) б)
Рис. 1. Схемы ремённой передачи
В зависимости от формы поперечного сечения ремня различают плоскоремённые (Рис. 2, а), круглоремённые (Рис. 2, б), клиноремённые (Рис. 2, в), поликлиновые (Рис. 2, г). Также применяют и зубчато-ремённые передачи, которые работают по принципу зацепления зубьев шкивов и зубьев ремня. Зубчатые ремни выполняют плоскими с поперечными зубьями на внутренней поверхности. Зубья могут иметь трапецеидальную (Рис. 3, а) или полукруглую форму (Рис. 3, б).
а) б) в) г)
Рис. 2. Типы ремённых передач
а) б)
Рис. 3. Типы зубчатых ремней
Достоинства: 1. Простота конструкции и низкая стоимость. 2. Возможность передачи движения на достаточно большие расстояния (до 15 м). 3. Возможность работы с большими скоростями вращения шкивов. 4. Плавность и малошумность работы. 5. Смягчение крутильных вибраций и толчков за счет упругой податливости ремня. 6. Предохранение механизмов от перегрузки за счет буксования ремня при чрезмерных нагрузках.
|
Недостатки: 1. Относительно большие габариты. 2. Малая долговечность ремней. 3. Большие радиальные нагрузки, передаваемые на валы и их опоры. 4. Непостоянство передаточного числа за счет скольжения ремня относительно шкивов. 5. Высокая чувствительность передачи к попаданию жидкостей (воды, топлива, масла) на поверхности трения.
Плоские и клиновые ремни
Материалы приводных ремней должны соответствовать следующим требованиям: износостойкость и прочность при циклических нагрузках, малый модуль упругости, эластичность, низкая стоимость.
Этим условиям удовлетворяют высококачественная кожа и синтетические материалы (резина), армированные белтинговым тканевым (ГОСТ 6982-54), полимерным (капрон, полиамид С-6, каучук СКН-40, латекс) или металлическим кордом. Применяются прорезиненные тканевые ремни (ГОСТ 101-54), слоистые нарезные ремни с резиновыми прослойками, послойно и спирально завёрнутые ремни. В сырых помещениях и агрессивных средах применяют ремни с резиновыми прокладками. Описание наиболее распространённых типов ремней приведено в литературе [3-4].
Плоские ремни изготавливают различной ширины, конструкции и материалов. В учебном проектировании рекомендуется применять прорезиненные и синтетические ремни. Характеристики таких ремней приведены в приложениях 1, 2. Площадь поперечного сечения плоских ремней определяется его толщиной δ и шириной b. Прорезиненные ремни выпускают в форме лент конечной длины. Синтетические ремни выпускают бесконечными (в виде замкнутой ленты определённой длины).
Клиновые ремни делятся на три вида: нормального сечения, узкие, широкие. В основу такой классификации легло соотношение b / h. Клиновые ремни нормального сечения (b / h = 1,6) рекомендуются для приводов станков, промышленных установок, стационарных сельскохозяйственных машин. Допускаемая окружная скорость для таких ремней 30 м/с. Узкие клиновые ремни (b / h = 1,2) рекомендуются для приводов вентиляторов автомобилей, тракторов и комбайнов. Допускаемая окружная скорость для таких ремней 40 – 50 м/с. Широкие клиновые ремни (b / h = 2,5) применяются для вариаторов.
|
Клиновые ремни маркируются в соответствии с ГОСТ - прописными русскими буквами, в соответствии с зарубежной системой ISO – прописными латинскими буквами (табл.1):
Таблица 1
Клиновые ремни | ||||||||||
Нормального сечения | Узкого сечения | |||||||||
О | А | Б | В | Г | Д | Е | УО | УА | УБ | УВ |
Z | A | B | C | D | E | EO | SPZ | SPA | SPB | SPC |
Клиновые ремни нормального и узкого сечений выпускаются бесконечными. Их основные характеристики, а также эскиз поперечного сечения приведены в приложении 2.
Методика расчёта
Расчёт ремённой передачи включает в себя два основных этапа – проектный, проверочный. Также расчёт ремённой передачи включает в себя определение нагрузки на её валы и опоры.
Проектный расчёт сводится к определению площади поперечного сечения ремня плоскоремённой передачи или количества клиновых ремней клиноремённой передачи необходимого для обеспечения требуемой тяговой способности.
Проектный расчёт выполняется в следующей последовательности:
1) Выбор тип (типоразмер) ремня.
При проектировании плоскоремённых передач тип ремня выбирают, ориентируясь на его среднюю скорость υ. При υ < 30 м/с выбирают прорезиненные ремни, а при υ ≥ 30 м/с - синтетические. На начальном этапе проектирования скорость ремня неизвестна. Поэтому сначала предварительно выбирают тип ремня, а затем вычисляют его среднюю скорость. Если вычисленная скорость не соответствует рекомендуемому значению для выбранного типа ремня, то выбирают ремень другого типа, или корректируют диаметры шкивов. Также приемлемым является вариант, при котором сначала определяют диаметры шкивов и среднюю скорость ремня, а затем, ориентируясь на вычисленную среднюю скорость ремня, выбирают его тип.
При проектировании клиноремённых передач типоразмер ремня выбирают по известному крутящему моменту Т1 на валу ведущего шкива с помощью приложения 4. Если крутящий момент Т1 неизвестен, то его следует определить с помощью формулы (1). Также для выбора типоразмера ремня таких передач могут быть использованы соответствующие номограммы [1], [3-4].
2) Определение диаметров шкивов
Диаметр ведущего шкива определяется с помощью формулы М.А. Саверина
D 1 = Kd · (28)
Коэффициент Kd в формуле (28) зависит от типа ремённой передачи (табл. 11)
Таблица 11
Тип передачи | Kd |
Плоскоремённая | 55…65 |
Клиноремённая с нормальным ремнём | 30…40 |
Клиноремённая с узким ремнём | 20…25 |
Поликлиновая | 25…30 |
Полученный с помощью формулы (28) результат следует округлить до ближайшего значения по стандартному ряду диаметров шкивов (по ГОСТ 17383-73): 28; 36; 40; 45; 50; (53); 56; 63; (67); 71; (75); 80; (85); 90; (95); 100; (106); 112; (118); 125; (132); 140; (150); 160; (170); 180; (190); 200; (212); 224; (236); 250; (265); 280; (300); 315; (335); 355; (375); 400; (425); 450; 475; 500; (530); 560; (600); (620); 630; (670); 710; (750); 800; (850); 900; (950); 1000; (1060); 1120 и т.д. Для клиноремённых передач размерный ряд начинается с 63 мм.
|
Примечание: размеры, указанные в скобках применяются в технически обоснованных случаях.
Принятый по стандарту диаметр D 1 должен обеспечивать выполнение условий:
1) для всех типов передач:
υ ≤ [ υ ] (29)
где υ, [υ] - соответственно расчётная и допускаемая средние скорости ремня.
2) для клиноремённых передач
D 1 ≥ D 1 min (30)
где D 1 min – минимальный диаметр малого шкива, который соответствует выбранному типоразмеру клинового ремня (приложение 4).
При невыполнении условия (29) или условия (30) (для клиноремённых передач) следует скорректировать значение D 1.
При проектировании плоскоремённых передач диаметр D 1 может быть определён и другими способами [3]:
- из конструктивных соображений, исходя из габаритов передачи или требуемого диаметра D 2 большого шкива;
- из условия выбранной толщины ремня при ограниченном сортаменте ремней;
- из условия минимальной допустимой скорости ремня для малоскоростных передач
При проектировании клиноремённых передач диаметр D 1 может быть определён путём выбора из стандартного ряда диаметров шкивов (по ГОСТ 17383-73). При выборе следует ориентироваться на величину D 1 min и брать на 1 – 2 номера больше. Например, если для выбранного типоразмера ремня D 1 min = 63 мм, значит, следует принимать D 1 = 71 мм или D 1 = 80 мм.
Диаметр ведомого шкива определяем с помощью формулы
D 2 = u рем · D 1 ·(1 - ξ) (31)
Вычисленное по формуле (31) значение D 2 следует округлить до ближайшего значения по стандартному ряду диаметров, что и D 1.
Примечание: рекомендуется округлять D 1 в большую сторону, а D 2 - в меньшую.
После определения диаметров шкивов уточняют передаточное отношение:
=
(32)
где ξ = 0,01…0,02 – коэффициент скольжения.
Вычисленное по формуле (32), передаточное отношение не должно отличаться от u рем более чем на 4 %. В противном случае следует проверить возможность использования других ближайших по стандартному ряду диаметров D 2.
В качестве расчётного диаметра D шкива плоскоремённой передачи принимают диаметр его наружной поверхности, а клиноремённой и поликлиновой передачи – диаметр окружности расположения нейтральной линии ремня.
3. Определение межосевого расстояния и длины ремня
Сначала в зависимости от требований компоновки принимается предварительное межосевое расстояние а и определяется расчётная длина ремня L, которая затем округляется до ближайшего стандартного значения. Для синтетических ремней стандартная величина L принимается по приложению 2, а для плоских прорезиненных и клиновых ремней - по таблице 12.
Таблица 12
1й ряд | 400, 450, 500, 560, 630, 710, 800, 900, 1000, 1120, 1250, 1400, 1600, 1800, 2000, 2240, 2300, 2800, 3150, 3550, 4000, 4500, 5000, 5600, 6300, 7100, 8000, 9000, 10 000, 11 200, 12 500, 14 000, 16 000, 18 000 |
2й ряд | 425, 475, 530, 600, 670, 750, 850, 950, 1060, 1180, 1320, 1500, 1700, 1900, 2120, 2360, 2650, 3000, 3350, 3750, 4250, 4750, 5300, 6000, 6700, 7500, 8500, 9500, 10 600, 11 800, 13 200, 15 000, 17 000 |
Примечание: для узких клиновых ремней длины выбирать только из ряда 1.
Далее вычисляется расчётное число пробегов v (формула (22)) и проверяется условие (21). Если условие (21) не выполняется, то следует увеличить длину ремня L.
Предварительное значение межосевого расстояния а должно соответствовать условиям:
- для плоскоремённых передач amin ≥ 2·(D 1 + D 2)
- для клиноремённых передач 0,55·(D 1 + D 2) + h ≤ a ≤ 2·(D 1 + D 2)
где h – высота сечения ремня (приложение 4).
При расчёте клиноремённой передачи передаточное отношение можно определить с помощью таблицы:
Таблица 13
u рем | 1 | 2 | 3 | 4 | 5 | 6 |
a, мм | 1,5 · D 2 | 1,2 · D 2 | D 2 | 0,95· D 2 | 0,9 · D 2 | 0,85 · D 2 |
По принятому значению длины ремня L уточняется межосевое расстояние a (оно должно согласовываться с его предварительным значением) и проверяется угол обхвата ремнём малого шкива α 1, значение которого должно соответствовать условиям:
- для плоскоремённых передач α1 ≥ 150°
- для клиноремённых передач α1 ≥ 120°
Выполнение этих условий обеспечивает требуемую тяговую способность передачи. При невыполнении какого-либо условия следует скорректировать значения диаметров шкивов и выполнить перерасчёт.
Завершающий этап проектного расчёта рассмотрим отдельно для плоскоремённой и клиноремённой передачи.
Проектный расчёт плоскоремённой передачи завершается определением толщины δ и ширины b поперечного сечения ремня. Толщина прорезиненного ремня определяется из условия:
δ ≤
Вычисленное значение δ округляется до ближайшего большего стандартного (приложение 1).
Для плоских синтетических ремней толщину ремня δ определяют с помощью таблицы 14 по вычисленному диаметру малого шкива.
Таблица 14
![]() | 28 | 36 | 45 | 56 | 63 | 75 | 80 | 90 | 100 |
δ, мм | 0,4 | 0,5 | 0,6 | 0,7 | 0,8 | 0,9 | 1,0 | 1,1 | 1,2 |
С помощью выражения (14) вычисляем ширину ремня:
b = Ft /[ σ t ] ·δ
Вычисленное значение ширины ремня округляется до ближайшего стандартного значения, которое выбирается из стандартного ряда: 10, 16, 20, 25, 32, 40, 50, 63, 71, 80, 90, 100, 112, 125, 140, 160, 180, 224, 250, 312, 335, 400, 450, 500.
Окружная сила Ft вычисляется с помощью формулы (3) или (4). Для определения напряжений [ σ t ] используется формула (5). Коэффициент эксплуатации C э определяется с помощью формулы (6), а напряжения [ σ t ]0 - с помощью выражения (10) или (11) в зависимости от выбранного типа плоского ремня.
После определения толщины δ и ширины b вычисляется площадь поперечного сечения ремня.
Проектный расчёт клиноремённой передачи завершается определением необходимого числа клиновых ремней.
Сначала с помощью формулы (16) или (17) вычисляем ориентировочное число клиновых ремней z, а затем с помощью таблицы 9 назначаем коэффициент Cz и определяем искомое число ремней z '.
Принятое число клиновых ремней z ' должно соответствовать условию (19). Также не рекомендуется принимать z ' = 1. При необходимости уменьшения количества ремней следует увеличить диаметр D 1 или выбрать сечение с большей площадью Az.
Окружная сила Ft определяется также как и для плоскоремённой передачи. Коэффициент эксплуатации C э вычисляется с помощью формулы (7).
Ориентировочное число ремней может быть вычислено через напряжения [ σ t ] и [ σ t ]0 или через силы [ Ft ] и [ Ft ]0. Напряжения [ σ t ]0 вычисляются с помощью формулы (12) или (13) в зависимости от типа сечения клинового ремня. Сила [ Ft ]0 определяется с помощью приложения 5 или 6 для клинового ремня выбранного сечения по диаметру малого шкива и средней скорости ремня. Напряжения [ σ t ] определяются с помощью выражения (5), а сила [ Ft ] - с помощью выражения (18).
Проверочный расчёт осуществляется по долговечности ремня. Он включает в себя проверку ремня на прочность по напряжениям растяжения и по ресурсу.
Проверочный расчёт выполняется в следующей последовательности:
1) Проверка ремня на прочность по напряжениям растяжения
С помощью формул приведённых в п.1.5. определяем максимальные напряжения σ max на ремне и проверяем условие (27). Если условие (27) не выполняется, то следует увеличить диаметр ведущего шкива D 1 или площадь поперечного сечения ремня и выполнить перерасчёт.
2) Проверка ремня на ресурс
Сначала определяем коэффициенты C Н и Cu (формула (26)). Далее с помощью формулы (24) или (25) вычисляем ресурс и проверяем условие (23). Если условие (23) не выполняется, то следует увеличить диаметр ведущего шкива D 1 или плоскоремённую передачу заменить клиноремённой.
Нагрузка на валы и опорыF в ремённой передачи зависит силы предварительного натяжения F 0, окружной силы Ft и угла охвата ремнём малого шкива α1 (п. 1.5). Силы натяжения ветвей ремня F 1, F 2 зависят от сил F 0 и Ft.
Приведённые в п. 1.5. не отражают тяговой способности передачи, которая связана со значением силы трения между ремнем и шкивом. Такая связь установлена Эйлером в виде:
F 1 = F 2 · e f · ά
где f – приведённый коэффициент трения между шкивом и ремнём; ά - угол скольжения (ά ≈ 0,7· α1), рад.
Примем q = e f ·ά. Тогда выражения для вычисления сил натяжения ремня примут вид:
F1 = Ft· + F ц F2 = Ft ·
+ F ц F0 =
·
Для клиноремённой передачи приведённый коэффициент трения определяется с помощью выражения:
f =
В неработающей (находящейся в покое) передаче ветви ремня загружены силой предварительного натяжения F 0. В работающей передаче ветви ремня загружены силами F 1, F 2 соответственно. Следовательно, нагрузка на валы и опоры ремённой передачи может быть определена для двух случаев:
- для неработающей (находящейся в покое) передачи:
F В = 2· F 0 ·sin(α1 /2)
- для работающей передачи:
F В =
Если ремённая передача является наклонной, то величины проекций силы на горизонтальную X и вертикальную Y оси могут быть определены с помощью выражений:
F в X = F0 · sin (θ + β/2) + (F0 + Ft)· sin (θ – β/2)
F в Y = F0 · cos (θ + β/2) + (F0 + Ft)· cos (θ – β/2)
где β – угол между ветвями ремня (п. 1.3); θ - угол наклона лини центров шкивов передачи к горизонту.
После выполнения проектного и проверочного расчётов, а также определения нагрузки на валы и опоры передачи выполняется проработка конструкции шкивов.
Конструирование шкивов осуществляется в соответствии с рекомендациями, приведёнными в п. 1.3. Геометрические параметры ступицы шкива зависят от величины её посадочного диаметра, который определяется при проектном расчёте вала. Ступица шкива соединяется с валом посредством шпоночного, шлицевого или прессового (с натягом) соединения. Следовательно, ширина ступицы зависит от ширины шпонки или шлицев, которые определяются при расчёте соответствующих соединений. Конструирование шкивов со спицами рекомендуется осуществлять в соответствии с [3, с. 45-46] или [4, с 85].
ПРИМЕРЫ РАСЧЁТОВ
Пример расчёта плоскоремённой передачи
Выполнить расчёт плоскоременной передачи при следующих исходных данных: требуемая мощность на валу электродвигателя P 1 = 3,8 кВт; частота вращения вала электродвигателя n 1 = 1430 об/мин; передаточное число u рем = 2; нагрузка — спокойная; работа двухсменная; угол наклона линии центров шкивов к горизонту не превышает 60°.
Проектный расчёт
1.1. Выбор типа ремня
Предварительно выбираем плоский прорезиненный ремень
1.2. Определяем диаметры шкивов
1) Определяем диаметр малого шкива
Диаметр малого шкива вычислим с помощью формулы М.А. Саверина:
D 1 = Kd ·
Согласно таблице коэффициент Kd = 55…65, примем Kd = 60.
Крутящий момент на ведущем шкиве передачи:
Т1 = 9550 · = 9550 ·
= 25,4 Н·м
Тогда диаметр малого шкива:
D 1 = 60 · = 176,4 мм
По стандартному ряду шкивов (ГОСТ 17383-73) принимаем D 1 = 180 мм
2) Вычисляем среднюю скорость ремня
υ = =
= 13,6 м/с
Вычисленная средняя скорость ремня υ меньше допускаемой [υ] =30 м/с для прорезиненного ремня, что соответствует условию (29). Окончательно принимаем D 1 = 180 мм.
3) Определяем диаметр большого шкива
D 2 = u рем · D 1 ·(1 - ε)
Коэффициент скольжения ε = 0,01…0,02, принимаем ε = 0,015, тогда
D 2 = 2·180 ·(1 – 0,015) = 355 мм
По стандартному ряду диаметров шкивов (ГОСТ 17383-73) принимаем D 2 = 355 мм
4) Вычисляем фактическое передаточное отношение
=
=
= 2
Вычисленное передаточное отношение совпало с заданным u рем = 2. Окончательно принимаем D 2 = 355 мм.
1.3. Определяем межосевое расстояние и длину ремня
1) Определяем длину ремня
Предварительно принимаем межосевое расстояние:
a = 2·(D 1 + D 2) = 2·(180 + 355) = 1070 мм
Тогда, расчётная длина ремня:
L = 2 · a + ·(D 1 + D 2) +
= 2 · 1070 +
·(180 + 355) +
=
2140+839,95 + 7,16 = 2987 мм
По таблице 12 принимаем L = 3150 мм
2) Проверяем принятую длину ремня L по числу пробегов ремня
Определяем расчётное число пробегов ремня
v = =
= 4,32 с-1
Вычисленное число пробегов ремня меньше допускаемого [ v ] = 10 с-1, что соответствует условию (21). Окончательно принимаем L = 3150 мм.
3) Определяем уточнённое межосевое расстояние
a = · [2· L – π ·(D 1 + D 2) +
]=
·[2·3150 - 3,14·(180 + 355)+
]= 1248 мм
4) Проверяем угол обхвата ремнём малого шкива
Вычисляем угол обхвата ремнём малого шкива
α1 = 180- 57· = 180- 57·
= 172°
Вычисленный угол обхвата ремнём малого шкива соответствует условию α1 ≥ 150°. Следовательно, требуемая тяговая способность передачи обеспечена
1.4. Определяем площадь поперечного сечения ремня
1) Определяем толщину ремня
Толщина прорезиненного ремня определяется из условия:
δ ≤
D 1 = 180 мм, тогда
δ ≤ = 4,5 мм
По приложению 1 принимаем δ = 4,5 мм, что соответствует ремню из Бельтинга – 820 с тремя прокладками толщиной 1,5 мм.
2) Вычисляем окружную силу
Ft = P 1 ·103/υ =3,8·103 / 13,6 = 280 Н
3) Определяем допускаемые полезные напряжения для базовой (эталонной) передачи:
[ σ t ]0 = S – W ·
Для заданных условий эксплуатации согласно таблице 5 напряжения от силы предварительного натяжения ремня σ 0 = 1,8 МПа. Тогда по таблице 7 принимаем S = 2,5; W = 10. Следовательно:
[ σ t ]0 = 2,5 – 10· = 2,25 МПа
4) Определяем коэффициент эксплуатации
Коэффициент угла охвата ремнем малого шкива
Cα = 1 – 0,003·(180 – α 1) = 1 – 0,003·(180 – 172) = 0,98
Коэффициент, учитывающий влияние скорости:
Cυ = 1,04 – 0,0004· υ 2 = 1,04 – 0,0004·13,62 = 0,97
Коэффициент угла наклона Cθ = 1 (табл. 3); коэффициент режима работы C р = 0,9 (табл.4).
Тогда коэффициент эксплуатации
C э = Cα · Cυ · Cθ · C р = 0,98·0,97·1·0,9 = 0,86
5) Вычисляем допускаемые полезные напряжения для заданной передачи:
[ σ t ] = [ σ t ]0· C э = 2,25·0,86 = 1,94 МПа
6) Определяем ширину ремня
b = Ft /[ σ t ] ·δ = 280/1,94·4,5 = 32 мм
Принимаем b = 32 мм.
7) Вычисляем площадь поперечного сечения ремня
А = b · δ = 4,5·32 = 144 мм2
Проверочный расчёт
2.1. Расчёт ремня на прочность по напряжениям растяжения
Максимальные напряжения на ремне:
σmax = σ и1 + σ 0 + σt / 2+ σ ц
Изгибные напряжения при огибании ремнём малого шкива:
=
·Е
Согласно таблице 10 модуль упругости плоского прорезиненного ремня Е = 80…120 МПа, принимаем Е =120 МПа, тогда
=
· 120 = 3 МПа
Полезные напряжения:
= Ft / А = 280/ 144 = 1,94 МПа
Напряжения от центробежной силы:
σ ц = 10-6· ρ· υ 2
Согласно таблице 10 плотность плоского прорезиненного ремня ρ = 1100…1200 кг/м3, примем ρ =1100 кг/м, тогда
σ ц = 10-6·1100 · 13,6 2 = 0,2 МПа
Следовательно
σmax = 3 + 1,8 + 1,94 / 2+ 0,2 = 5,97 МПа
Допускаемые напряжения растяжения для плоского прорезиненного ремня [ σ р ] = 8 МПа (табл. 10), следовательно, условие (27) выполняется, и выбранный ремень проходит на статическую прочность.
2.2. Расчёт ремня на ресурс
Расчётный ресурс ремня
Lh = ·
Предел выносливости плоского прорезиненного ремня σ-1 = 7 МПа (табл. 10). Коэффициент нагрузки Сн = 2 (будем считать, что нагрузка переменная). Коэффициент, учитывающий влияние передаточного отношения:
Cu = 1,5· - 0,5 = 1,5·
- 0,5 = 1,39
Тогда
Lh = ·
= 2323 часа
Требуемая долговечность плоских ремней [ Lh ] = 2000..3000 часов, следовательно, условие (23) выполняется, и ремень проходит на ресурс.
Пример расчёта клиноремённой передачи
Выполнить расчёт клиноременной передачи при следующих исходных данных: требуемая мощность на валу электродвигателя P 1 = 7,2 кВт; частота вращения вала электродвигателя n 1 = 955 об/мин; передаточное число u рем = 2; нагрузка — спокойная; работа двухсменная; угол наклона линии центров шкивов горизонту не превышает 60°.
Проектный расчёт
1.1. Выбор типоразмера ремня
Вычисляем крутящий момент на ведущем шкиве передачи:
Т1 = 9550 · = 9550 ·
= 72 Н·м
Согласно приложению 4 данным условиям нагружения соответствуют ремни В и SPZ. Выполним расчёт передачи для обоих вариантов ремней с целью выбора оптимального. Сначала, используя соответственно приложения 4-5 и 4,6, выпишем параметры ремней В и SPZ необходимые для проведения расчёта (табл. 15).
Таблица 15
Наименование параметра | Марка сечения ремня | |
В | SPZ | |
Минимальный диаметр малого шкива D 1 min, мм | 125 | 63 |
Площадь поперечного сечения А z,, мм2 | 138 | 56 |
Высота сечения ремня h, мм | 10,5 | 8 |
Базовая длина ремня L 0, мм | 2240 | 1600 |
Расчёт передачи ремнём сечения B рассмотрим подробнее, а для варианта сечения SPZ приведём основные результаты.
1.2. Определяем диаметры шкивов
1) Определяем диаметр малого шкива
Для ремня сечения B минимальный диаметр малого шкива D 1 min = 125 мм. По рекомендациям п. 2.3. принимаем D 1 = 160 мм.
2) Вычисляем среднюю скорость ремня
υ = =
= 8 м/с
Вычисленная средняя скорость ремня υ меньше [υ] = 30 м/с допускаемой для клинового ремня нормальной серии, что соответствует условию (29). Окончательно принимаем D 1 = 160 мм.
3) Определяем диаметр большого шкива
D 2 = u рем · D 1 ·(1 - ε)
Коэффициент скольжения ε = 0,01…0,02, принимаем ε = 0,015, тогда
D 2 = 2·160 ·(1 – 0,015) = 315,2 мм
По стандартному ряду шкивов (ГОСТ 17383-73) принимаем D 2 = 315 мм
4) Вычисляем фактическое передаточное отношение
=
=
= 1,998 ≈ 2
Вычисленное передаточное отношение совпало с заданным u рем = 2. Окончательно принимаем D 2 = 315 мм.
1.3. Определяем межосевое расстояние и длину ремня
1) Определяем длину ремня
По таблице 13 принимаем предварительное межосевое расстояние:
а = 1,2 · D 2 =1,2 · 315 = 378 мм
Расчётная длина ремня
L = 2 · a + ·(D 1 + D 2) +
= 2 · 378 +
·(160 + 315) +
=
= 756 +745,75 + 15,88 = 1527 мм
По стандартному ряду длин (таблица 12) принимаем L = 1600 мм.
2) Проверяем принятую длину ремня L по числу пробегов ремня
Определяем расчётное число пробегов ремня
v =
Общие условия выбора системы дренажа: Система дренажа выбирается в зависимости от характера защищаемого...
История развития хранилищ для нефти: Первые склады нефти появились в XVII веке. Они представляли собой землянные ямы-амбара глубиной 4…5 м...
Папиллярные узоры пальцев рук - маркер спортивных способностей: дерматоглифические признаки формируются на 3-5 месяце беременности, не изменяются в течение жизни...
Двойное оплодотворение у цветковых растений: Оплодотворение - это процесс слияния мужской и женской половых клеток с образованием зиготы...
© cyberpedia.su 2017-2024 - Не является автором материалов. Исключительное право сохранено за автором текста.
Если вы не хотите, чтобы данный материал был у нас на сайте, перейдите по ссылке: Нарушение авторских прав. Мы поможем в написании вашей работы!