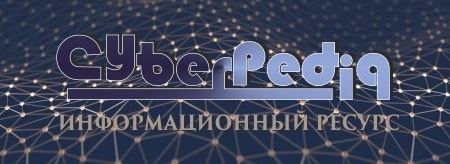
Поперечные профили набережных и береговой полосы: На городских территориях берегоукрепление проектируют с учетом технических и экономических требований, но особое значение придают эстетическим...
Общие условия выбора системы дренажа: Система дренажа выбирается в зависимости от характера защищаемого...
Топ:
Особенности труда и отдыха в условиях низких температур: К работам при низких температурах на открытом воздухе и в не отапливаемых помещениях допускаются лица не моложе 18 лет, прошедшие...
Характеристика АТП и сварочно-жестяницкого участка: Транспорт в настоящее время является одной из важнейших отраслей народного...
Техника безопасности при работе на пароконвектомате: К обслуживанию пароконвектомата допускаются лица, прошедшие технический минимум по эксплуатации оборудования...
Интересное:
Подходы к решению темы фильма: Существует три основных типа исторического фильма, имеющих между собой много общего...
Наиболее распространенные виды рака: Раковая опухоль — это самостоятельное новообразование, которое может возникнуть и от повышенного давления...
Искусственное повышение поверхности территории: Варианты искусственного повышения поверхности территории необходимо выбирать на основе анализа следующих характеристик защищаемой территории...
Дисциплины:
![]() |
![]() |
5.00
из
|
Заказать работу |
|
|
Литье по выплавляемым моделям (ЛВМ)- это процесс получения отливок в разовых неразъемных огнеупорных формах с помощью моделей изготавливаемых из легкоплавких, выжигаемых или растворяемых модельных составов. Используют как оболочковые (керамические), так и монолитные формы. Сущность процесса заключается в следующем. Изготовление моделей отливок и литниково-питающей системы осуществляется из модельных составов в пресс-формах, внутренняя полость копирует наружную поверхность отливки, путем запрессовки с помощью шприц-машины или заливки расплавленного модельного состава.
Промышленное применение этого метода обеспечивает получение из любых литейных сплавов сложных по форме отливок весом от нескольких граммов до десятков килограммов, со стенками толщиной от 0,5-1,0 мм и более, поверхностью, соответствующей 4-6-му классам чистоты (ГОСТ 2789-59), и повышенной точностью размеров.
Растворяемые и выжигаемые составы готовятся в специальных нагревательных установках. Пресс-формы изготавливают из легких сплавов, а для мелкосерийного производства также из неметаллических материалов- пластмасс, резины и др.
Размеры пресс-формы выбираются таким образом, чтобы с учетом усадки модельного состава и сплава получить размеры отливки, отвечающие требованиям чертежа. Пресс-формы делают разъемными, чтобы облегчить извлечение модели. В одной пресс-форме можно получить одну или сразу несколько моделей, а в условиях массового производства применяют пресс-формы для изготовления нескольких моделей, объединенных в модельные звенья, состоящие из нескольких моделей отливок, питателей и участка стояка. Сборка блока моделей (обычно вручную) заключается в объединении моделей на одном стояке литниковой системы методом припайки с помощью нагретого электроножа.
|
В процессе прокаливания из формы выжигаются остатки модельного состава и газотворные примеси оболочки, увеличивается газопроницаемость формы, заканчивается процесс образования керамической оболочки. Если толщина керамической формы не превышает 5-6 слоев, то её заформовывают для прочности в опоку сухим песком или молотым шамотом. Заливка форм расплавом обычно производится из ковшей.
Если сплавы склонны к плёнообразованию, то заливку ведут прямо из печи. Для получения более качественных отливок плавку и заливку расплава производят в вакууме. Для повышения заполняемости форм расплавом используют центробежные с вертикальной осью машины. Залитые формы охлаждаются на заливочных площадках либо на охладительных ветвях конвейера в течении 2-5 часов. Формы с сухим наполнителем освобождаются от наполнителя на специальных опрокидывателях. Обрезка и очистка отливок производится так же, как и при литье в песчаные формы. Для удаления мелких керамических стержней применяют ультразвуковые установки, а также растворение стержней в кислотах.
К преимуществам данного вида литья относятся:
- возможность получения сложных по форме отливок из широкой номенклатуры сплавов с высокой точностью, не требующих дополнительной механической обработки за исключением сопрягаемых поверхностей;
- возможность получения отливок со сложными внутренними полостями, отверстий диаметром до 1 мм, литых резьб и т.п.
Основными недостатками данного вида литья являются его сложность, многооперационность, а следовательно, и высокая себестоимость получаемых отливок.
К основным видам термической обработки стали относится:
Отжиг. Традиционно сложившееся понятие «отжиг» относится к нескольким режимам термообработки, объединенным целью привести сплав в стабильное состояние. Образуется феррито-перлитная структура. Сталь с такой структурой обладает низкой твердостью и высокой пластичностью.
|
Наиболее распространенной разновидностью отжига является обыкновенный отжиг, который производится с целью умягчить сталь перед механической обработкой или подготовить сталь к окончательной термической обработке. Сталь нагревается до температуры на 30-50оС выше линии фазовых превращений GSK, выдерживается при этой температуре до полного завершения структурно-фазовых превращений и охлаждается с очень малой скоростью в камере печи.
Диффузионный отжиг или гомогенизация применяется с целью устранения в легированной стали неоднородности химического состава (ликвации). Нагрев при диффузионном отжиге проводят до максимально высоких температур, так как при этом условии наиболее интенсивно происходят диффузионные процессы выравнивания химического состава сплава. Для легированных сталей температуру нагрева выбирают в интервале 1050-1250оС, выдержка достаточно длинная - 15-20 ч. Отжиг для снятия внутренних напряжений проводят с целью уменьшения остаточных напряжений, образовавшихся в металле при ковке, литье, сварке, и способных вызвать коробление и разрушение детали. Нагрев проводят в интервале 200-500оС с последующим медленным охлаждением. Рекристаллизационный отжиг проводят с целью устранения наклепа холоднодеформированного металла. Температура нагрева в этом виде обжига выбирается на 150-250оС выше температуры начала рекристаллизации обрабатываемого сплава.
Нормализация. Особенностями этого режима являются температура нагрева стали выше температуры полиморфного превращения по линии GSE и охлаждение на спокойном воздухе. Ускоренное, по сравнению с обычным отжигом, охлаждение придает стали более дисперсную феррито-цементитную структуру (сорбит) и более высокую прочность.
Закалка на мартенсит. Закалка стали заключается в нагреве ее выше температуры фазовых превращений (GSK), выдержке для завершения всех превращений и охлаждений с высокой скоростью с целью получения при комнатной температуре неравновесной структуры- мартенсита. Минимальная скорость охлаждения, необходимая для подавления диффузионных процессов и образования мартенсита, называется критической скоростью охлаждения. Скорость охлаждения определяется видом охлаждающей среды. По мере уменьшения охлаждающей способности, среды располагаются в следующем порядке: водные растворы солей, вода, расплавы солей и металлов, минеральные масла, водные растворы полимеров. Легированные стали охлаждают с меньшей скоростью, чем углеродистые стали.
|
Широкое распространение как в нашей стране, так и за рубежом получил разработанный советскими специалистами метод изготовления форм с сухим опорным наполнителем, позволяющий полностью от использования жидких наполнительных формовочных составов с дорогим связующим - гидролизованным раствором этилсиликата. Применение сухого наполнителя, пригодного для многократного повторного использования, позволило не только удешевить изготовление литейной формы, но и сократить продолжительность этого процесса в несколько раз, в том числе в 8-10 раз длительность такой ответственной операции, как тепловая обработка форм перед заливкой.
Основные операции технологического процесса показаны на рисунке 3.
Модель или звено моделей 2 изготовляют в разъемной пресс-форме 1, рабочая полость которой имеет конфигурацию и размеры отливки с припусками на усадку модельного состава и материала отливки, а также обработку резанием (рисунок 3, а). Модель изготовляют из материалов, либо имеющих невысокую температуру плавления (воск, стеарин, парафин), либо способных растворяться (карбамид) или сгорать без образования твердых остатков (полистирол).
Готовые модели или звенья моделей собирают в блоки 3 (рисунок 3, б), имеющие модели элементов литниковой системы из того же материала, что и модель отливки. Блок моделей состоит из звеньев, центральная часть которых образует модели питателей и стояка. Модели чаши и нижней части стояка изготавливают отдельно и устанавливают в блок при его сборке.
Рисунок 3– Последовательность изготовления многослойной оболочковой формы по выплавляемым моделям: а – запрессовка модельного состава в пресс-форму; б – сборка блока; в – нанесение на блок суспензии; г – посыпка огнеупорным зернистым материалом: д – сушка; е – удаление модели; ж – засыпка опорным.материалом; з – прокалка в печи; и – заливка формы расплавом; 1 – пресс-форма; 2 – модель; 3 – блок моделей отливок и литниковой системы; 4 – слой суспензии; 5 – огнеупорный зернистый материал; 6 – пары аммиака; 7 – горячая вода; 8 – опорный материал; 9 – печь; 10 – прокаленная форма; Q – подвод теплоты
|
Для получения оболочковых форм полученный блок моделей погружают в емкость с жидкой формовочной смесью – суспензией, состоящей из пылевидного огнеупорного материала, например, пылевидного кварца или электрокорунда и связующего (рисунок 3, в). В результате на поверхности модели образуется слой суспензии 4 толщиной менее 1 мм. Для упрочнения этого слоя и увеличения его толщины на него наносят слои огнеупорного зернистого материала 5 (мелкий кварцевый песок, электрокорунд, зернистый шамот) (рисунок 3, г). Операции нанесения суспензии и обсыпки повторяют до получения на модели оболочки требуемой толщины (3 – 10 слоев). При этом каждый слой покрытия высушивают на воздухе или в парах аммиака 6, что зависит от связующего (рисунок 3, д).
Задание 2
1. Опишите явления, происходящие в металле при холодном деформировании, и укажите сущность процесса упрочнения.
Холодная деформация— это деформация, которая происходит при температурах ниже температуры рекристаллизации. Такая деформация приводит к наклепу металла или сплава.Т<0,3Тпл
В результате холодной деформации прочностные характеристики и твердость с увеличением степени деформации возрастают, а пластические свойства уменьшаются, вплоть до полного их исчерпания.
При холодном деформированиипроисходит изменение параметров кристаллической решетки, увеличивается концентрация дислокаций (на 3-4 порядка), происходит накопление энергии Энергия, затраченная на деформацию, есть сумма накопленной энергии и энергии деформационного разогрева (накапливается в дислокациях, их силовых полях). Чем больше деформация, тем меньше прирост накопленной энергии.
Энергетическая целесообразность процесса: при малых деформациях накопленная в меди энергия составляет 10%, от затраченной, а при больших - только 3%.
Изменение свойств металла при холодном деформировании широко используют для увеличения сопротивления металла деформации (σт), например, в методах поверхностного упрочнения.
Совокупность изменения свойств металла в процессе пластической обработки называется наклепом или упрочнением.
Различные металлы упрочняются по разному. Поликристаллы упрочняются более интенсивно, чем монокристаллы; металлы с мелкозернистой структурой упрочняется более интенсивно, чем крупнозернистые.
В процессе ОМД наклеп учитывается первое как фактор технологический, определяющий возможность получения изделий данным способом; второе как метод придания изделию необходимых свойств, особенно в сочетании с термообработкой.
|
В условиях холодной обработки, которая выполняется температуры ниже металла, подвижность атомов небольшая, поэтому исключается снятие внутренних напряжений, наблюдается рост твердости металла, предела текучести и прочности, а также уменьшение пластичности.
Наклеп, при холодной обработке металлов, вызывает понижение пластических свойств, всегда появляется опасность появления трещин, расслоений и других дефектов, такое явление проявляется и в некоторых случаях горячей обработки металлов давлением.
При этом холодной обработкой металлов давлением можно в раза увеличить предел прочности и текучести металла.
2. Опишите технологический процесс изготовления поковки способом горячей объемной штамповки на кривошипном горячештамповочном прессе. При выполнении работы следует: 1)описать сущность процесса штамповки и указать область ее применения; 2)изобразить схему молота и описать его работу; 3) описать механизацию процесса штамповки.
Основные операции, которые существуют в объёмной штамповке. Это садка, высадка, протяжка, выдавливание, сгибание, сплющивание, калибровка, намеренное создание углублений, утолщений и выступов. Все эти операции осуществляются на специальных кузнечно-прессовых машинах. К ним можно отнести прессы, молоты и машины, которые имеют специальное назначение. Из штампованных поковок после процесса термической обработки получают весьма большое разнообразие деталей. Среди них можно отметить коленчатые валы, шатуны, лопатки турбин, шары, кольца подшипников и многое другое.
На сегодняшний день существует только два вида объёмной штамповки: холодная и горячая. Процесс холодной штамповки проходит без предварительного нагрева металлической заготовки. В качестве исходного материала при холодной штамповке выступают калиброванные прутики, которые предварительно нарезаются на штучные заготовки.
Процесс горячей объёмной штамповки осуществляется после предварительного разогрева исходного материала до температуры в пределах от 200 до 1300 °С. Стоит запомнить, что температура нагрева зависит только от состава обрабатываемого сплава и условий, в которых он обрабатывается. В качестве исходного материала при горячей объёмной штамповке выступают прокатные прутики, которые предварительно разделяют на вымеренные заготовки. А если точнее, то каждая такая заготовка должна быть равна по объёму будущей поковке. При этом так же обязательно стоит учитывать неизбежные отходы. Масса готовых изделий колеблется от нескольких грамм до шести - восьми тонн. Так же нужно отметить, что точность размеров будущей поковки зависит лишь от её начальной конфигурации и объёма.
Кривошипные горячештамповочные прессы предназначаются для выполнения различных технологических процессов горячей штамповки из сортового металла: открытой и закрытой штамповки, горячего прессования ит.д., в условиях крупносерийного и массового производства. На Рисунке 4 показана типовая конструкция КГШП. К достоинствам этих прессов относится быстроходность, высокая жесткость конструкции, сравнительно небольшие размеры штампового пространства. Большое число ходов пресса обусловлено необходимостью уменьшения продолжительности контакта штампа с заготовкой при обработке горячего металла.
Рисунок 4. Кривошипный горячештамповочный пресс 1 – главный эксцентриковый вал; 2 – шатун; 3 – ползун; 4 – хобот ползуна; 5 – дополнительные направляющие ползуна; 6 – клиновой стол; 7 – механизм верхнего выталкивателя; 8 – механизм нижнего выталкивателя; 9 – приводной вал; 10 – уравновешиватель ползуна; 11 – ресивер; 12 – пневмофрикционная муфта включения; 13 – пневмофрикционный тормоз; 14 – маховик; 15 – станина
Главные особенности КГШП состоят в следующем:
1. жесткая конструкция главных узлов и пресса в целом, что вызвано необходимостью резко уменьшить величину упругой деформации деталей пресса в целях повышения точности штамповки;
2. Усиленные направляющие ползуна, что вызвано необходимостью уменьшения величин перекосов ползуна при внецентренной нагрузке;
3.Увеличенное число ходов ползуна, что обусловлено необходимостью уменьшения продолжительности контакта штампа с заготовкой при обработке горячего металла.
Неподвижная часть штампа крепится на клиновом столе пресса. Такая конструкция стола пресса предназначена для расклинивания главного механизма в случае заклинивания, а также для регулировки закрытой высоты штампового пространства при наладке штампов (Рисунок 5). Вторая часть штампа крепится к ползуну с помощью сменной подштамповой плиты. Ползун имеет направляющие поверхности, образованные на его боковых поверхностях (количество направляющих поверхностей может быть различным, чаще всего 4).
Рисунок 5. Варианты регулировки закрытой высоты в КГШП: а – с помощью клинового стола; б – с помощью эксцентриковой оси в нижней головке шатуна; 1 – наклонная плоскость основания стола; 2 – поперечный клин; 3 – клиновая подушка стола; 4 – эксцентриковый вал; 5 – шатун; 6 – эксцентриковая ось; 7 – ползун
Устройство регулирования закрытой высоты штампового пространства с помощью клинового стола (см. рис. 5 а) имеет ряд недостатков: трудности при наладке; засорение мест скольжения стола по станине; большая металлоемкость стола. Поэтому в современных конструкциях КГШП регулирование закрытой высоты штампового пространства осуществляется при помощи эксцентриковой оси, соединяющей шатун с ползуном, или дополнительной эксцентриковой втулки в этом соединении (см. рисунок 5 б). Большая масса ползуна с шатуном и эксцентриковым валом не позволяет уравновесить массы всех деталей исполнительно механизма. Поэтому уравновешивается только масса ползуна с массой верхней половины штампы.
В агрегатах кривошипных горячештамповочных прессов предусматривают средства механизации, приведенные втабл. 1. От степени механизации зависит производительность пресса и трудоемкость.
Таблица 1.Средства механизации процессов в агрегатах штамповочных молотов
Средства механизации | Назначение | Количество единиц в агрегатепри степени механизации | ||
высокой | средней | низкой | ||
Манипуляторы илиперекладчики | Подача заготовки в штамп, манипулированиеи перекладка из ручья в ручей | 2 | - | - |
Сбрасыватели | Сбрасывание поковок и заусенца от обрезного штампа | 2 | - | - |
Загрузочные механизмы | Загрузка нагревательных установок | 1 | 1 | - |
Разгрузочные механизмы | Разгрузка нагревательных установок | 1 | 1 | - |
Транспортеры | Межоперационные передачи | 3 | 3 | - |
Машины для забивки клиньев | Забивка и выбивка клиньевпри установке штампов | 1 | - | - |
Электрические тележки | Установка штампов | 1 | - | - |
Однорельсовые путис ручными кошками | Межоперационные передачи,подвеска сокола | - | 1 | 2 |
Задание 3
|
|
Архитектура электронного правительства: Единая архитектура – это методологический подход при создании системы управления государства, который строится...
Археология об основании Рима: Новые раскопки проясняют и такой острый дискуссионный вопрос, как дата самого возникновения Рима...
Поперечные профили набережных и береговой полосы: На городских территориях берегоукрепление проектируют с учетом технических и экономических требований, но особое значение придают эстетическим...
Биохимия спиртового брожения: Основу технологии получения пива составляет спиртовое брожение, - при котором сахар превращается...
© cyberpedia.su 2017-2024 - Не является автором материалов. Исключительное право сохранено за автором текста.
Если вы не хотите, чтобы данный материал был у нас на сайте, перейдите по ссылке: Нарушение авторских прав. Мы поможем в написании вашей работы!