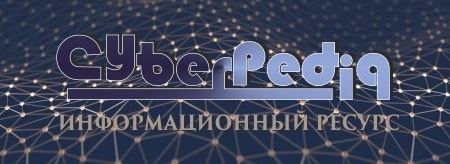
Типы оградительных сооружений в морском порту: По расположению оградительных сооружений в плане различают волноломы, обе оконечности...
Историки об Елизавете Петровне: Елизавета попала между двумя встречными культурными течениями, воспитывалась среди новых европейских веяний и преданий...
Топ:
Устройство и оснащение процедурного кабинета: Решающая роль в обеспечении правильного лечения пациентов отводится процедурной медсестре...
Генеалогическое древо Султанов Османской империи: Османские правители, вначале, будучи еще бейлербеями Анатолии, женились на дочерях византийских императоров...
Интересное:
Отражение на счетах бухгалтерского учета процесса приобретения: Процесс заготовления представляет систему экономических событий, включающих приобретение организацией у поставщиков сырья...
Распространение рака на другие отдаленные от желудка органы: Характерных симптомов рака желудка не существует. Выраженные симптомы появляются, когда опухоль...
Влияние предпринимательской среды на эффективное функционирование предприятия: Предпринимательская среда – это совокупность внешних и внутренних факторов, оказывающих влияние на функционирование фирмы...
Дисциплины:
![]() |
![]() |
5.00
из
|
Заказать работу |
|
|
С повышением температуры активность взаимодействия металлов с атмосферой печи увеличивается. При нагреве сталей на поверхности заготовки образуется слой окислов железа FeO, Fe₂O₃, Fe₃O₄, называемый также окалиной. Толщина слоя окалины зависит от температуры и времени нагрева, расположения заготовок в печи, состава печных газов и химического состава сплава. Наиболее интенсивно стали окисляются при температуре выше 900' С. Так, по сравнению со скоростью окисления при температуре 900' С при 1000' С скорость окисления увеличивается в два раза, при 1200'С – в пять раз. Образование окалины ведет к потерям металла, увеличению припусков на механическую обработку, снижает производительность труда и, являясь твердым веществам, снижает стойкость инструмента при обработке давлением и обработке резанием. Нагрев углеродистых сталей сопровождается выгоранием углерода с поверхностного слоя на глубину до 2 - 4 мм. Уменьшение содержания углерода, называемое обезуглероживанием, ведет к снижению прочности и твердости стали и ухудшению закаливаемости детали.
Понятие температурного интервал обработки металлов давлением и принцип его определения по диаграмме состояния сплава железо-углерод.
При горячей деформации нужно поддерживать необходимую температуру в ходе самого процесса обработки давлением, особенно при производстве изделий небольшого объема и с развитой поверхностью. В этом случае задача усложняется в связи с потерей теплоты при контакте с деформирующим инструментом. Температура нагрева для горячей деформации зависит в первую очередь от природы деформируемого материала - сталь, медные сплавы, алюминиевые сплавы и другие; его химического состава - углеродистая, низколегированная, аустенитная сталь, а также от толщины заготовки.
|
Горячая обработка металлов давлением в зоне установленных температур снижает сопротивление деформированию примерно в 10-15 раз по сравнению с обычным холодным состоянием. Таким образом, при обработке давлением необходимо соблюдать определенный температурный интервал, в котором данный металл обладает минимальной прочностью в сочетании с наибольшей пластичностью. Этот интервал зависит в основном от химического состава сплава и устанавливается на основании диаграммы состояния «железо - углерод». Однако в любых случаях температура нагрева должна быть значительно ниже температуры солидуса сплава.
Рисунок 2 - Диаграмма железо - углерод
На рисунке 2 представлена диаграмма железо-углерод, которую используют для определения видов и температурных интервалов при термической обработке стали и при обработки давлением, температуры плавления и заливки сплава и литейных свойств сплава (жидкотекучести, усадки).
Рисунок 3 - Температурный интервал обработки давлением (ОД) низкоуглеродистых сплавов
температурный интервал ковки и штамповки (рисунок 4)
Рассмотрим температурный интервал ковки и штамповки (рисунок 4). Если отметить на диаграмме состояния сплава железо - углерод температурный интервал ковки-штамповки разных углеродистых сталей, то его верхний предел будет находиться на прямой, проходящей на 150-200°С ниже линии солидуса. Таким образом, при температуре начала ковки весь углерод находится в твёрдом растворе (аустенит). Между указанной прямой и линией солидуса находятся две зоны: вначале перегрева, затем пережога. Нижние пределы температуры ковки для всех углеродистых сталей соответствуют примерно 800°С, т.е. приблизительно на 75°С выше линии РSК. Ковка - штамповка при более низкой температуре приводит к упрочнению (наклепу).
Из диаграммы видно, что стали с меньшим содержанием углерода обрабатываются давлением при более высоких температурах, а стали с повышенным содержанием углерода при несколько пониженных температурах. Все примеси, входящие в сталь, ведут к понижению температур обработки давлением. Сталь, содержащая 0,5%С от начала до конца обработки находится в однофазном состоянии (аустенит). Углеродистую сталь с меньшим содержанием углерода заканчивают обрабатывать при наличии в ней двух фаз: аустенита и феррита. При этом получается некоторый наклеп, который легко снимается последующей термической обработке. Углеродистую сталь, содержащую более 1% С, заканчивают обрабатывать также при наличии в ней двух фаз: аустенита и вторичного цементита. Но в данном случае ковка - штамповка, дробя сетку цементита, оказывает только благоприятное влияние на структуру стали.
|
2.2. Технологический процесс изготовления поковки способом холодной листовой штамповки
Холодная штамповка производится в штампах без нагрева заготовок и сопровождается деформационным упрочнением металла. Холодная штамповка является одним из наиболее прогрессивных методов получения высококачественных заготовок небольших и точных из стали и цветных металлов. Она обеспечивает достаточно высокую точность и малую шероховатость поверхности при малых отходах металла и низкой трудоемкости и себестоимости изготовления изделий. Возможность осуществления холодной штамповки и качество заготовок определяются качеством исходного материала. Большое значение имеет подготовка поверхности заготовок: удаление окалины, загрязнений и поверхностных дефектов. Процессы холодной штамповки часто выполняют за несколько технологических переходов, постепенно приближая форму и размеры заготовок к форме и размерам готовых изделий и осуществляя промежуточный отжиг для снятия наклепа и восстановления пластических свойств металла. В зависимости от характера деформирования и конструкции штампов холодную штамповку делят на объемную и листовую.
а) Штампы широко используются в разных отраслях машиностроения на всех массовых и серийных производствах, для изготовления различного рода деталей, поковок и заготовок. Это инструменты, с помощью которых можно получить одинаковые изделия и детали, поковки и заготовки, методом пластической деформации. Они пластически деформируют заготовку, сообщая ей форму рабочей части штампа. Устанавливаются штампы на оборудование, предназначенное для штамповки (прессы, молоты), оно и приводит его в действие. Производство штампов может происходить либо внутри самого предприятия – в инструментальных цехах, либо их можно заказать по индивидуальным чертежам на предприятиях, имеющих для этого квалифицированный персонал и высокопроизводительное оборудование. Второй вариант экономически выгоден мелким производителям. По технологии: штампы для горячей штамповки и штампы для холодной штамповки. По оборудованию: для прессов, молотовые и для горизонтально ковочных машин - ГКМ. В холодной штамповке используются штампы: разделительные и формоизменяющие - гибочные. Разделительные штампы осуществляют отрезку или вырезку, пробивку или просечку, и т.д. Для гибки, завивки, обтяжки, вытяжки, формовки и т.д. применяют формоизменяющие или как ещё их называют гибочные штампы. Холодная штамповка по исходному материалу разделяется на листовую и объёмную. В листовой используется лист, полоса, лента и иногда проволока. Можно к этому добавить и следующее, что в листовой штамповке допускается использование разных материалов, включая и неметаллические. В объёмной штамповке используется толстая полоса, профильный прокат, пруток.
|
б ) Штамповочное оборудование и области его применения.
Деформирование заготовки происходит в момент соприкосновения частей оборудования. Существуют разнообразные модели штамповочных прессов, что позволяет выбрать подходящий станок для изготовления требуемых деталей.
Прессы для штамповки металла бывают:
кривошипно-шатунного типа - применяются такие однокривошипные пресса листовой штамповки для вырубания, продавливания, пробивания, обрезки и другой холодной штамповки. В конструкции этого оборудования основная деталь – это ползун, осуществляющий возвратно-поступательные действия, образуемые за счет вращения системы передвижения.
Работает открытый кривошипный пресс при помощи ползуна, передающего движение штампу, состоящему из верхней подвижной части – пуансона и неподвижной нижней – матрицы, закрепленной на столе, куда осуществляется подача металлических листов. Подвижная часть штампа прикреплена к ползуну.
|
Гидравлические прессы, широко применяются в промышленности, в слесарных работах и при ремонте различной автомобильной техники.
Сегодня гидравлический пресс можно увидеть, практически на каждой станции технического обслуживания автомобилей, где этому устройству находят очень широкое применение. Обслуживание и ремонт автомобиля без гидравлического пресса, становится невозможным. Основное применение гидравлического пресса это такие работы как запрессовка и выпресовка различных деталей и подшипников. Правка и гибка металлов, прошивка, мелкая штамповка и калибровка. Из-за своей спецификации – когда работы выполняются под высоким давлением, это устройство является весьма опасным, поэтому при работе с гидравлическим прессом большое внимание должно уделяться соблюдению техники безопасности.
Область применения радиально-ковочного типа углеродистые марки стали, быстрорежущие марки стали, инструментальные марки стали, конструкционные марки стали, быстрорежущие марки стали, нержавеющие марки стали, сплавы на основе титана, сплавы на основе никеля, сплавы на основе вольфрама, сплавы на основе молибдена и другие специальные сплавы.
Использовние электромагнитного типа для обработки металлов давлением при импульсной штамповке. Сущность изобретения: электромагнитный пресс содержит корпус с крышкой, в котором неподвижно смонтирована матрица и расположен пуансон. Пуансон имеет возможность осевого перемещения от привода, выполненного в виде двух рабочих обмоток, соединенных между собой гибким проводником. Каждая рабочая обмотка имеет форму плоской спирали. Крышка и пуансон выполнены из магнитомягкого материала и имеют пазы на обращенных одна к другой поверхностях. Обмотки зеркально расположены в упомянутых пазах и закреплены. 1 ил. Изобретение относится к обработке металлов давлением, в частности к устройствам для электромагнитной штамповки.
в) Процесс механизации штамповки
Штамповкой называют процесс, который направлен на пластическую деформацию металлической заготовки, её размеров и общей формы. Обычно процессу штамповки подвергаются металлы или изделия из пластика. На сегодняшний день существует два основных вида штамповки - объёмная и листовая. При листовой штамповке в конце процесса получается деталь, одна из сторон которой пренебрежимо мала по сравнению с другими сторонами. Это свойство касается листов металла, толщиной до 6 миллиметров. В противном же случае штамповка называется объёмной. Для осуществления процесса штамповки используются прессы. Прессы представляют собой устройства, которые позволяют проводить деформацию металлических или пластиковых заготовок при помощи оказанного механического воздействия. Штамповка листовых материалов подразделятся на несколько основных категорий по типу применяемой в процессе оснастки. Самой распространённой категорией является штамповка в инструментальных штампах, так же довольно часто используют штамповка эластичными средами, менее распространенной является импульсная штамповка. Последняя, в свою очередь, так же делится на два основных вида: гидро-импульсная и магнитно-импульсная штамповка. Так же на сегодняшний день используется штамповка взрывом и валковая штамповка.
|
|
Семя – орган полового размножения и расселения растений: наружи у семян имеется плотный покров – кожура...
Историки об Елизавете Петровне: Елизавета попала между двумя встречными культурными течениями, воспитывалась среди новых европейских веяний и преданий...
Поперечные профили набережных и береговой полосы: На городских территориях берегоукрепление проектируют с учетом технических и экономических требований, но особое значение придают эстетическим...
Биохимия спиртового брожения: Основу технологии получения пива составляет спиртовое брожение, - при котором сахар превращается...
© cyberpedia.su 2017-2024 - Не является автором материалов. Исключительное право сохранено за автором текста.
Если вы не хотите, чтобы данный материал был у нас на сайте, перейдите по ссылке: Нарушение авторских прав. Мы поможем в написании вашей работы!