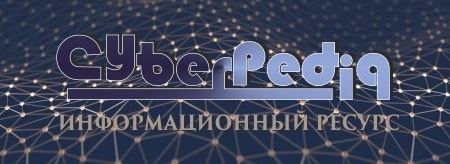
Наброски и зарисовки растений, плодов, цветов: Освоить конструктивное построение структуры дерева через зарисовки отдельных деревьев, группы деревьев...
Своеобразие русской архитектуры: Основной материал – дерево – быстрота постройки, но недолговечность и необходимость деления...
Топ:
Когда производится ограждение поезда, остановившегося на перегоне: Во всех случаях немедленно должно быть ограждено место препятствия для движения поездов на смежном пути двухпутного...
Генеалогическое древо Султанов Османской империи: Османские правители, вначале, будучи еще бейлербеями Анатолии, женились на дочерях византийских императоров...
Выпускная квалификационная работа: Основная часть ВКР, как правило, состоит из двух-трех глав, каждая из которых, в свою очередь...
Интересное:
Мероприятия для защиты от морозного пучения грунтов: Инженерная защита от морозного (криогенного) пучения грунтов необходима для легких малоэтажных зданий и других сооружений...
Средства для ингаляционного наркоза: Наркоз наступает в результате вдыхания (ингаляции) средств, которое осуществляют или с помощью маски...
Инженерная защита территорий, зданий и сооружений от опасных геологических процессов: Изучение оползневых явлений, оценка устойчивости склонов и проектирование противооползневых сооружений — актуальнейшие задачи, стоящие перед отечественными...
Дисциплины:
![]() |
![]() |
5.00
из
|
Заказать работу |
|
|
(контактно-тепловая сварка)
Источники нагрева – разогретые тела (элементы) передают теплоту путем непосредственного соприкосновения с пластмассой.
Способ сварки нагретыми инструментами (контактно-тепловая сварка) имеет следующие разновидности: сварку оплавлением и проплавлением. В первом случае нагреватель соприкасается непосредственно со свариваемыми поверхностями. Переход термопласта в вязкотекучее состояние при этом методе происходит, начиная с поверхностей, подлежащих соединению, и сопровождается в большинстве случаев вытеканием расплава из-под нагревающего инструмента, т.е. соединяемые поверхности оплавляются. Во втором случае тепло к свариваемым поверхностям поступает сквозь толщу деталей, а инструмент контактирует с внешними поверхностями свариваемых деталей. Нагрев может быть одно- или двусторонним. Первый способ используют для сварки деталей значительной толщины (листы, трубы, профиль), второй – для сварки тонких листов и пленок внахлестку. Нагретые инструменты могут быть в виде пластин, дисков, полос, нитей, профилированных планок.
По режиму нагрева деталей при сварке проплавлением различают сварку при длительном нагреве по заранее заданному термическому режиму и сварку термоимпульсную, при которой нагрев деталей осуществляется за счет кратковременного теплового импульса, а скорость охлаждения определяется теплоотводом. Для термоимпульсной сварки используют исключительно малоинерционные нагреватели.
При нагреве всего сечения свариваемых деталей (прямом нагреве) нагретую металлическую пластину 1 помещают между деталями 2. После нагрева свариваемых поверхностей пластину быстро удаляют и сдавливают детали (рис.13). Схватывание расплава с инструментом предотвращают уменьшением времени сварки и повышением температуры нагревателя.
|
При нагреве термопласты в виду низкой вязкости могут налипать на поверхность нагревательного элемента. Прилипшие частицы разлагаются и при последующей сварке продукты разложения попадают в шов, что приводит к снижению качества сварки под влиянием включений, пор и непроваров. Поверхность нагревательных элементов необходимо полировать и защищать антиадгезионными материалами. При нагреве инструментом, изготовленным из стали, порообразование меньше, чем при нагреве медным и алюминиевым инструментом. Хромирование и никелирование нагревателей не оказывает существенного влияния на интенсивность порообразования.
![]() |
Этим методом сваривают встык и внахлестку одновременно всю поверхность соединения. Применяется для сварки профилей и труб из мягкого и твердого ПВХ, твердого полиэтилена, полипропилена, полиацетата.
Основные технологические параметры при сварке оплавлением: температура нагревателя, продолжительность нагрева, усилие прижатия сварочного инструмента к деталям (давление оплавления), давление осадки, продолжительность выдержки под давлением после сварки, скорость оплавления, скорость и величина осадки.
Режим сварки некоторых термопластов приведен в табл.6. Указанное в таблице давление нагретого инструмента является начальным, по мере оплавления поверхностей оно должно снижаться для уменьшения вытекания из зоны контакта расплава. После нагрева и осадки охлаждение по всей свариваемой площади должно происходить равномерно, под постоянным давлением.
Таблица 6
Основные параметры режима контактной сварки
пластмасс оплавлением
Термопласт | Температура инструмента, 0С | Давление, МПа | Время нагрева, с | |
нагрева | осадки | |||
Полиэтилен ВП (ПЭНД) НП (ПЭВД) | 240±10 190 – 220 | 0,2 – 0,5 0,3 – 0,4 | 1,5 – 3,0 1,5 – 2,0 | 30 – 180 30 - 80 |
Винипласт | 230 – 250 | 3,0 – 4,0 | 5,0 – 9,0 | 40 – 60 |
Пластифици-рованный ПВХ | 180 – 200 | 0,1 – 0,3 | 1,0 – 1,5 | 20 – 60 |
Полипропилен | 190 – 240 | 0,3 – 0,4 | 1,5 – 2,0 | 30 – 120 |
Поливинилацеталь | 220 | 0,1 – 0,2 | ~ 1 | 10 - 40 |
Поликарбонат | 350 - 400 | 0,5 – 0,2 | 0,15 – 0,2 | 20 – 40 |
Полистирол | 220 - 250 | 0,5 – 0,1 | 0,3 – 0,35 | 10 - 50 |
Полиамид | 220 - 260 | 0,5 – 0,1 | 0,15 – 0,25 | 15 - 50 |
|
Диаграммы усилий при сварке нагретым инструментом показаны на рис.14.
Граница оплавления не адекватна плоскости нагревателя: в сечении она имеет параболическую форму и выпуклостью направлена в сторону нагревателя. В центре оплавляемой кромки глубина проплавления минимальна, а у поверхности максимальна. Это происходит вследствие теплоизлучения от нагревателя, выступающего за границу кромок деталей, а также за счет теплоты выносимой вытекающим в грат расплавом.
Глубина проплавления растет с повышением температуры и длительности нагрева, одновременно увеличивается кривизна линии проплавления. Интенсивность роста глубины проплавления с увеличением продолжительности нагрева уменьшается.
![]() |
Увеличение давления нагревателя при оплавлении приводит к уменьшению глубины проплавления, так как при этом плавящийся полимер выдавливается в грат.
Течение расплава при осадке способствует активному взаимодействию макромолекул не только за счет удаления экранирующих их ингредиентов, но и вследствие того, что при течении происходит благоприятная взаимная ориентация макромолекулярных слоев, способствующая более полной реализации сил Ван-дер-Ваальса. Чем больше площадь контакта свариваемых деталей, тем на большую глубину необходимо их проплавить, чтобы обеспечить полную эвакуацию ингредиентов, препятствующих сварке. С вытеканием из зоны сварки расплава, нагретого до большей температуры и обладающего в связи с этим минимальной вязкостью, удаляются макромолекулярные слои, обладающие наибольшей термодинамической активностью. Вследствие этого в контакт вступают макромолекулы, обладающие меньшей потенциальной энергией, т.е. слои расплава, обладающие большей вязкостью, что не улучшает условия взаимодействия макромолекул. Следовательно, при сварке необходимо находить оптимальное соотношение давления осадки, объема и вязкости расплава, размеров деталей.
Типичная термомеханическая циклограмма контактной тепловой сварки оплавлением встык представлена на рис.15.
|
Трубы диаметром более 50 мм соединяют встык, диаметром менее 50 мм при толщине стенки 2 мм сваривают враструб. При стыковой сварке торцы труб нагревают плоским инструментом, имеющим форму диска для труб малого диаметра и форму кольца для нагрева труб большого диаметра. Нагрев этих инструментов в зависимости от конструкции можно осуществлять встроенными электронагревателями или газовыми горелками.
При сварке винипласта применяют нагретые инструменты, имеющие ребристую поверхность: высота и шаг пилообразных ребер 0,5 – 1,5 мм. Ориентировочные параметры режима стыковой сварки труб приведены в табл.7.
Соединение враструб – это соединение фасонных деталей полученных литьем под давлением, с трубами, которые должны быть изготовлены из такого же материала, согласованы по посадочному размеру и рассчитаны на одно и тоже номинальное давление. Необходимое сварочное давление можно обеспечить путем прессовой посадки свариваемых деталей, т.е. внутренний диаметр соединительного элемента должен быть меньше наружного диаметра трубы. При этом формирующий инструмент должен обеспечивать оплавление на глубину около 0,2 мм. Соединяемые элементы, нагретые до Тсв, упруго деформируются при введении трубы в раструб соединительного элемента и обеспечивают необходимую для сварки прессовую посадку. Прочность таких соединений составляет 90 – 100 % от прочности материала труб.
При сварке враструб (рис.16) нагревательный элемент имеет гильзу для оплавления конца трубы и дорн для оплавления внутренней поверхности раструба. Дорн и раструб могут иметь цилиндрическую или коническую форму (конусность
Таблица 7 Технологические параметры контактной стыковой сварки оплавлением труб диаметром 100 – 300 мм | Время охлаждения стыка, мин, при температуре окружающей среды, 0С | + 40 | 5 10 12 | 5 10 | 5 10 |
+ 20 | 4 8 11 | 4 8 | 4 8 | ||
0 | 4 6 10 | 4 6 | 4 6 | ||
- 20 | 3 5 8 | 3 5 | 3 5 | ||
Пауза, с | 8 | 5 | 6 | ||
Темпе-ратура нагревателя, 0С | 250±10 | 200±10 | 240±10 | ||
Время нагрева, с | 45 55 65 | 35 50 | 45 55 | ||
Давление, кгс/см2 | осадки | 1,2 – 1,3 1,4 – 1,6 1,8 – 2,0 | 1,2 – 1,3 1,4 – 1,7 | 1,2 1,4 | |
оплавления | 0,2 – 0,3 0,4 – 0,5 0,6 | 0,2 – 0,3 0,4 – 0,5 | 0,3 0,4 | ||
Толщина стенки, мм
| 2 – 6 7 – 10 11 – 15 | 2 – 6 7 – 12 | 2,5 – 5 6,0 – 8,5 | ||
Материал | Полиэтилен высокой плотности | Полиэтилен низкой плотности | Полипропилен |
1/16 – 1/12). Разность диаметров гильзы и дорна у цилиндрического инструмента должна быть 0,5 – 1 мм. Режим сварки враструб приведен в табл.8. Время выдержки под осевой нагрузкой до частичного отверждения оплавленного материала составляет 5 – 15 с, время между снятием инструмента и осадкой – не более 2 с.
Таблица 8
Основные технологические параметры
контактной сварки труб враструб
Параметр | Полиэтилен | |
низкой плотности, цилиндрический раструб | высокой плотности, конусный раструб | |
Температура сварки, 0С | 300 | 250 – 270 |
Время оплавления, с, при толщине стенки, мм: до 4 4 - 5 5 – 8 свыше 8 | 5 – 10 6 – 15 8 – 18 10 – 20 | 7 – 12 10 – 15 15 – 20 - |
На рис.17. приведена схема сварки тавровых и угловых соединений (сварка с отбортовкой кромок).
Угол заточки инструмента зависит от угла загиба детали. При отбортовке края на 900 применяют инструмент с углом при вершине 700.
Сварка в паз. Свариваемые поверхности соединяемых деталей 1 с помощью нагревательного элемента нагревают до Тсв. Нагревательный элемент 2 образует паз соответствующей формы, в который вставляют другую соединительную деталь, после чего прикладывают давление. Размеры нагревательного элемента соответствуют размерам присоединяемой детали (рис.18). Применяется для сварки плит и труб (тройники).
Для изготовления тройников на одной соединяемой детали делают седлообразную подготовку кромок, отверстие выполняют после сварки с помощью кольцевого сверла.
При методе последовательного нагрева свариваемых поверхностей (нагретым клином) нагретый инструмент (паяльник) 1 помещают между свариваемыми плоскостями и по мере размягчения кромок перемещают вдоль линии сварки (или нагретый инструмент закрепляют, а перемещают по нему детали). При нажатии роликом 2 на верхнюю полосу 4 она приваривается к нижней 3. Возможно использование присадочного материала (по составу аналогичного основному), прикатываемого нажимным роликом. При машинной сварке листового материала давление осуществляется протягиванием через валики. Метод применяется при сварке эластичных материалов (рис.19). Преимуществом является простота и возможность непрерывной сварки с высокой скоростью вручную во всех пространственных положениях и машинным способом в нижнем положении. Режимы сварки приведены в табл.9.
![]() |
Разновидностью сварки пластмасс оплавлением является сварка закладными нагревателями. При использовании закладного нагревателя нагрев и оплавление в зоне контакта собранных деталей производится при пропускании тока по металлическому проводнику (проволоке, ленте), который закладывается в зону контакта свариваемых деталей при сборке. Усилие в зоне плавления, необходимое для сварки, создается вследствие расширения расплавляемого материала. Нагреватель (одновременно армирующий элемент) может быть заложен внутрь деталей при их изготовлении (прессовании, отливке) (рис.20).
|
Таблица 9
Ориентировочные параметры сварки пленок толщиной 0,1 – 2 мм нагретым клином внахлестку (скорость сварки 0,04 – 0,3 м/с)
Материал | Температура инструмента, 0С | Давление ролика, МПа |
ПЭНД | 300 – 650 | 30 – 60 |
ПЭВД | ||
ПП | ||
ПВХ | 50 – 60 | |
Пластифицированный полиамид | 400 – 650 |
Соединение в торец полимерных пленок можно получить, оплавляя торцы деталей нагретой проволокой или газовым пламенем (рис.21). В последнем случае способ следует отнести к сварке газовыми теплоносителями. Этот процесс иногда соединяют с разделительной резкой. Так как сварка происходит без давления (с образованием общей зоны плавления), то этот способ можно использовать для тонких профилей, например, пленок с низкой вязкостью расплава.
Схема сварки с нагревом внешних поверхностей (косвенным нагревом) свариваемых деталей (сварка проплавлением) приведена на рис.22. Сварочный инструмент (утюг) 1, нагреваемый электрическим нагревательным элементом 2, перемещают по свариваемым в нахлестку пленкам 3, нагревая их до температуры сварки и сжимая весом инструмента.
![]() |
Основными технологическими параметрами режима контактной сварки проплавлением являются температура нагревателя, давление при нагреве и сварке, продолжительность нагрева и выдержки под давлением после сварки.
Длительность сварки определяется толщиной и теплопроводностью материала, температурой инструмента. Распределение температуры в зоне сварки представлено на рис.23. Этим способом можно сваривать детали ограниченной толщины, зависящей от теплопроводности пластмассы, так как максимальная температура инструмента определяется температурой разложения пластмассы. Возможно сварка пленок из поливинилхлорида толщиной до 80 мкм, из полиэтилена – до 500 мкм.
Применяется для сварки мягкого ПВХ, полиэтилена и полипропилена. Способ используется при производстве упаковки.
При контактной сварке проплавлением кромки пленок или листов можно нагревать с одной стороны или одновременно с двух сторон. При двустороннем нагреве скорость сварки увеличивают.
На рис.24 приведена схема сварки пленок нагретой лентой (проволокой). Лента 1, нагреваемая электронагревателем 2, перемещается роликами 3 и прижимается ими усилием Р к свариваемым внахлестку пленкам 4.
![]() |
Для повышения качества сварного соединения, увеличения скорости сварки, предотвращения коробления материала и образования гофр после нагревателя устанавливают охлаждающее устройство.
Схема роликовой сварки пленок представлена на рис.25. Роликовая сварка позволяет выполнять протяженные, герметичные соединения и автоматизировать процесс сварки. Для предотвращения налипания на поверхность пленок помещают разделительную ленту.
При сварке горячим прессованием теплота передается к месту сварки нагретыми поверхностями специальных прессов (рис.26). Свариваемые поверхности пластмасс 2 зажимают в прессе 1, рабочие поверхности которого нагреваются электронагревателем 3. При достижении заданной температуры производится выдержка под давлением. При этом пресс охлаждается водой, проходящей по каналам 4. Способ сварки проплавлением – прессованием позволяет за один цикл соединять изделие по всей поверхности или проводить шаговую сварку при соединении длинных швов. В прессе можно сваривать встык.
Возможно применение термоимпульсной сварки (односторонний и двусторонний импульс). При этом материал нагревается до температуры сварки практически мгновенно в результате пропускания через нагревательные элементы импульса тока большой величины. Форма нагревательного элемента может быть различной: точечной, полосовой, фигурной. Термоимпульсная сварка при точной дозировке теплоты позволяет избежать перегрева пленочных пластмасс в месте сварки. Применяется для сварки пленок из полиамидов толщиной менее 500 мкм.
При контактной тепловой сварке неармированных пленок проплавлением применяется два основных типа соединений: нахлесточное и Т-образное или рантовое. Типы сварных соединений армированных пленок показаны на рис.27. Переплетения армировки оказывают сопротивление течению расплава, однако под воздействием этого течения перемещаются к кромкам нахлестки, образуя сборки – гофры.
Наличие гофр в околошовной зоне сварных оболочковых конструкций резко снижает их несущую способность, приводя к возникновению значительных деформаций, концентрации
напряжений.
![]() |
Метод сварки нагревательными элементами обеспечивает высокую прочность соединений и достаточную производительность. Этим методом можно сваривать пластмассы, которые не могут быть сварены токами высокой частоты (фторопласт, полиэтилен, полистирол). Наиболее целесообразно применять для стыковых и нахлесточных соединений листовых конструкций небольшой толщины и пленок со швами большой протяженности. При сварке органического стекла в месте соединения сохраняется прозрачность.
Режимы контактной сварки пленок приведены в табл.10.
Таблица 10
Режимы контактной сварки пленок
Материал | Толщина, мкм | Температура инструмента, 0С | Давление, МПа | Выдержка, с |
Полиэтилен низкой плотности | 45 – 80 60 – 90 150 – 200 300 – 500 600 – 800 | 130 – 140 140 – 160 | 0,5 – 0,6 |
2 – 3
5 – 10 |
160 – 180 | ||||
Полиэтилен высокой плотности | 60 – 150 | 200 – 220 230 - 240 | 0,6 – 0,8 до 1,0 | 2 – 3 |
150 - 300 | 160 - 170 | 0,8 – 0,9 | ||
Полипропилен | 60 – 150 150 – 300 | 230 – 240 180 – 200 | до 1,0 0,9 | |
Полиамид | 60 – 150 130 – 200 | 185 – 200 210 – 220 | 0,6 – 0,8 0,4 – 0,5 | 5 – 6 10 – 15 |
Фторопласт | 100 – 200 | 390 – 400 | 0,2 – 0,5 | 120 – 180 |
Термомеханические циклы сварки термопластов проплавлением представлены на рис. 28.
На рис.29 показаны ручные аппараты ROWELD НЕ (фирма «ROTHENBERGER», Германия) для контактно-тепловой сварки пластмассовых деталей (труб) встык. Данные аппараты имеют сменные нагревательные элементы, защиту от перегрева, электронную регулировку температуры, крепление к верстаку; обеспечивают поддержание заданной температуры и ее равномерное распределение по всей поверхности нагревательного элемента.
Для сварки враструб могут быть использованы аппараты ROWELD P 63-3 Sets (фирма «ROTHENBERGER», Герма ния) (рис.30). Данные аппараты снабжаются насадками для сварки труб диаметром 16-125 мм, защитой от перегрева, электронной или термостатической регулировкой температуры, креплением к верстаку.
![]() | ||||||||
| ||||||||
![]() | ||||||||
|
|
Сущность и схемы процесса. Метод основан на подаче в место сварки присадки, находящейся в вязкотекучем состоянии. Нагретый присадочный материал расплавляет кромки свариваемой пластмассы, которая прочно сваривается с экструдируемой присадкой. Возможен дополнительный нагрев кромок деталей газовыми теплоносителями. Этот метод схож со сваркой нагретым воздухом с присадкой и сваркой металлов плавящимся электродом. Во всех случаях сварное соединение образуется за счет сплавления присадочного материала с кромками соединяемых деталей. Различие состоит в том, что металл переходит в жидкую фазу, а полимер остается в вязкотекучем состоянии. Поэтому для получения плотного контакта расплавленного присадочного материала с кромками свариваемых деталей необходимо создавать давление.
![]() |
|
Сварка экструдируемой присадкой может быть выполнена по трем схемам. При сварке открытой струей (экструзионной) присадочный материал непрерывно поступает в зону соединения из сопла экструдера, находящегося на некотором расстоянии. Для обеспечения плотного контакта присадочного материала с соединяемыми кромками применяют специальные прижимные устройства. При контактно-экструзионной сварке нагретое сопло может касаться свариваемых кромок, дополнительно нагревая их (рис.31). В третьем случае расплав подается в зону сварки периодически. Таким способом соединяют штампованные детали, состоящие из двух половин. Сварку производят в собранном виде, в форме, которая имеет специальные каналы, расположенные вдоль линии разъема. По этим каналам продавливается расплав. При передаче части тепла расплава детали плавятся и соединяются по линии разъема. Экструзионную сварку целесообразно применять для сварки пластмасс, имеющих сравнительно невысокую температуру перехода в вязко-текучее состояние, широкий интервал вязкотекучего состояния и способных нагреваться при экструзии значительно выше температуры текучести без деструкции (полиэтилен, полипропилен, пластифицированный ПВХ, полистирол).
| |||
![]() |
Экструзионную сварку можно применять для соединения полимерных пленок и пленочных армированных материалов непрерывным протяженным швом (рис.32). Преимуществом сварки пленок по данной схеме является то, что исключается возможность утонения материала в зоне шва, которое наблюдается при других методах.
|
Характерной особенностью контактно-экструзионной сварки является более высокая стабильность качества соединений, нечувствительность к состоянию поверхности материала.
Технология сварки. Экструдируемой присадкой можно получать стыковые, нахлесточные и угловые соединения. При стыковой сварке можно применять V - образную и Х - образную разделку кромок. Сварку стыковых соединений без подготовки кромок следует выполнять при сборке конструкций из материалов толщиной до 3 мм и только контактно-экструзионным способом, так как в этом случае разделку шва осуществляют мундштуком экструдера в процессе сварки. При сварке встык листов толщиной более 3 мм необходим скос кромок одного или двух свариваемых листов с одной либо двух сторон в зависимости от доступности места стыка.
Прочность сварных соединений полученных с помощью экструзионной и контактно-экструзионной сварки зависит от угла раскрытия шва. Максимальная прочность стыковых соединений с V – образной разделкой кромок достигается при углах раскрытия 70 – 900; соединений с Х – образной разделкой – при углах раскрытия 60 – 800. При оптимальных углах раскрытия швов соединения с Х – образными швами имеют более высокую прочность и требуют меньшего расхода присадочного материала. Поэтому при сварке встык конструкций из листовых материалов толщиной свыше 8 мм, в случае возможности двустороннего подхода к стыку, предпочтительна Х – образная разделка кромок. Угловые и тавровые соединения можно выполнять без предварительной подготовки кромок. Однако скос кромок несколько повышает прочность швов. Для обеспечения проплавления корня шва между кромками следует оставлять зазор 1,5 – 2 мм.
При ручной сварке даже при наличии зазора трудно обеспечить стабильное проплавление корня шва по всей его длине. В этом случае соединение выполняют с подваркой корня шва с обратной стороны. Если обратная сторона недоступна, применяют подкладки (съемные или остающиеся).
В случае двусторонней сварки швом с Х – образной разделкой кромок, перед сваркой второго шва необходимо удалить корень выполненного шва. При этом следует удалять наплавленный материал, врезание в основной материал не допускается. При многопроходной сварке корень шва должен быть тщательно проварен, а последующий валик шире предыдущего.
Разнотолщинность материала в случае стыковых соединений не должна превышать 1 мм, если разность толщин свариваемых листов превышает 1 мм, то на детали большей толщины делается скос под углом 15 ± 50 с одной или двух сторон до толщины более тонкого листа.
Прочность соединений увеличивается при сопутствующей прикатке формируемого шва роликом. Давление ролика в этом случае должно быть 1 – 3 МПа.
В зависимости от толщины соединяемых деталей существуют следующие способы сварки: бесконтактная сварка без предварительной разделки кромок (s = 0,2 ÷ 3 мм); бесконтактная сварка с предварительной разделкой кромок (s = 1 ÷ 3 мм); контактно-экструзионная сварка без предварительной разделки кромок (s = 1 ÷ 4 мм); контактно-экструзионная сварка с предварительной разделкой кромок (s = 2 ÷ 50 мм).
При сварке полимерных пленок экструдируемой присадкой следует применять нахлесточные соединения. Полимерные пленки (ПЭНП, ПЭВП, ПП) толщиной до 0,06 мм могут быть сварены поверх двух слоев; при сварке пленок толщиной более 0,06 мм, а также при сварке армированных пленок присадочный материал необходимо подавать между соединяемыми поверхностями.
Применяется гранулированный пластический присадочный материал, совпадающий по своему составу с основным материалом или близкий к нему. При сварке композиционных материалов, состоящих из нескольких различных полимеров, в качестве присадочного материала используют полимер, входящий в композицию и имеющий наиболее высокую температуру текучести. Он нагревается до пластического состояния в сварочном экструдере и в виде жидко-вязкой массы круглого или квадратного сечения заполняет соединение.
Пространственное положение шва при сварке: нижнее (преимущественно), вертикальное, горизонтальное на вертикальной плоскости, потолочное. Для удержания расплава в зоне сплавления вертикальные швы выполняют при перемещении аппарата сверху вниз при минимальной температуре присадки. Скорость сварки выбирают с таким расчетом, чтобы расплав не затекал перед мундштуком. Потолочные швы и горизонтальные на вертикальной плоскости также выполняют при минимальной температуре присадочного материала.
Режимы сварки экструдируемой присадкой: температура присадочного материала на выходе из экструдера и вносимого в зону шва; сварочное давление; скорость сварки; скорость движения расплава в воздушном зазоре между мундштуком экструдера и материалом; количество присадочного материала, выходящего из экструдера в единицу времени; количество присадочного материала вносимого в зону шва; диаметр присадочного материала; расстояние между мундштуком экструдера и свариваемым материалом.
Ручной пистолет для сварки пластмасс экструдируемой присадкой работает по принципу выдавливания плавящегося конца присадочного прутка, непрерывно толкаемого холодной его частью. Пистолет нагревается электроспиралью. Присадочный пруток подается с помощью роликов, приводимых в движение электродвигателем. Фотографии сварочных экструдеров представлены на рис. 33 и 34.
Ультразвуковая сварка
Этот метод предложен и разработан МВТУ им. Н.Э. Баумана совместно с Московским энергетическим институтом.
Нагрев при УЗС обусловлен поглощением энергии механических колебаний в объеме материала, находящегося под волноводом, в свариваемом контакте и контакте полимерный материал – волновод. Выделение теплоты в объеме полимера обусловлено потерями на внутреннее трение. Наиболее интенсивно поглощение энергии происходит в отдельных несплошностях материала, максимальное скопление которых наблюдается на границе раздела соединяемых материалов. Следовательно, скорость нарастания температуры на границе раздела должна быть значительно выше, чем в объеме материала.
Кроме того, возникающие при сварке поперечные ультразвуковые колебания вызывают поверхностное трение на границе раздела, что также способствует быстрому разогреву материала в этой зоне и переходу его в размягченное состояние.
![]() | ||||||
|
| |||||
Образовавшаяся мягкая прослойка снижает коэффициент механического трения, однако является средой интенсивно поглощающей механические колебания.
На границе раздела из-за наличия микронеровностей могут возникать значительные динамические напряжения. Перечисленные процессы приводят к неравномерному выделению теплоты и распределению температуры в объеме материала. Максимальные температуры достигаются на соединяемых поверхностях, следовательно, образование соединения при УЗС возможно без проплавления всего объема материала.
Роль механических колебаний заключается также в том, что под воздействием мощных импульсов ультразвуковой частоты происходит выравнивание микронеровностей, разрушение и удаление различных поверхностных пленок и загрязнений. Воздействие УЗ – колебаний ускоряет процесс диффузии макромолекул, вызывает интенсивное перемешивание расплава. Это ускоряет процесс образования сварных соединений и обеспечивает возможность получения качественных соединений при температурах более низких, чем в случае других известных способов (иногда ниже температуры текучести).
При сварке мягких полимерных материалов максимальные температуры достигаются не обязательно на границе раздела деталей, в случае УЗС жестких полимеров, наиболее высокие температуры достигаются, как правило, именно на границе. Это объясняется тем, что реальная площадь контакта между свариваемыми деталями обусловлена площадью микронеровностей, по которым происходит соприкосновение соединяемых поверхностей, а так как эта площадь мала, то здесь возникают значительные динамические напряжения, приводящие к интенсивному разогреву и оплавлению.
Особенности УЗС состоят в следующем:
- для сварки не требуется второй электрод, так как процесс односторонний, поэтому вторая деталь может быть неограниченной толщины;
- возможность сварки ультратонких деталей, листовых пакетов;
- возможность ввода ультразвука на значительном расстоянии от места соединения, что позволяет осуществлять сварку в труднодоступных местах;
- максимальный нагрев концентрируется на свариваемых поверхностях, что исключает перегрев пластмасс и обеспечивает высокую производительность процесса;
- загрязнения поверхности не оказывают существенного влияния на процесс сварки;
- не создаются радиопомехи;
- к сварочному инструменту не подводится напряжение;
|
- возможность соединения разнородных полимеров.
C помощью ультразвука сваривают: органическое стекло, ПВХ, полистирол, полиэтилен, синтетические ткани. Данный метод можно применять при сварке упаковочной тары, где мест
|
|
Таксономические единицы (категории) растений: Каждая система классификации состоит из определённых соподчиненных друг другу...
Историки об Елизавете Петровне: Елизавета попала между двумя встречными культурными течениями, воспитывалась среди новых европейских веяний и преданий...
Типы сооружений для обработки осадков: Септиками называются сооружения, в которых одновременно происходят осветление сточной жидкости...
История развития хранилищ для нефти: Первые склады нефти появились в XVII веке. Они представляли собой землянные ямы-амбара глубиной 4…5 м...
© cyberpedia.su 2017-2024 - Не является автором материалов. Исключительное право сохранено за автором текста.
Если вы не хотите, чтобы данный материал был у нас на сайте, перейдите по ссылке: Нарушение авторских прав. Мы поможем в написании вашей работы!