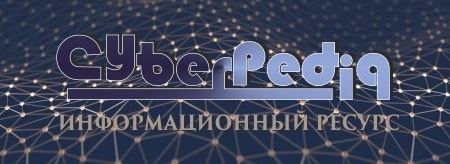
Таксономические единицы (категории) растений: Каждая система классификации состоит из определённых соподчиненных друг другу...
История создания датчика движения: Первый прибор для обнаружения движения был изобретен немецким физиком Генрихом Герцем...
Топ:
Отражение на счетах бухгалтерского учета процесса приобретения: Процесс заготовления представляет систему экономических событий, включающих приобретение организацией у поставщиков сырья...
Основы обеспечения единства измерений: Обеспечение единства измерений - деятельность метрологических служб, направленная на достижение...
Проблема типологии научных революций: Глобальные научные революции и типы научной рациональности...
Интересное:
Средства для ингаляционного наркоза: Наркоз наступает в результате вдыхания (ингаляции) средств, которое осуществляют или с помощью маски...
Мероприятия для защиты от морозного пучения грунтов: Инженерная защита от морозного (криогенного) пучения грунтов необходима для легких малоэтажных зданий и других сооружений...
Влияние предпринимательской среды на эффективное функционирование предприятия: Предпринимательская среда – это совокупность внешних и внутренних факторов, оказывающих влияние на функционирование фирмы...
Дисциплины:
![]() |
![]() |
5.00
из
|
Заказать работу |
|
|
Этот способ сварки позволяет упростить процесс получения и повысить качество сварных соединений трудно свариваемых полимеров (например, фторопласта-4).
Фторопласт-4 – кристаллический полимер с температурой плавления 327 0С и даже при температуре разложения (415 0С) не переходит в вязкотекучее состояние. Сваривают фторопласт-4 в основном термическими методами, при которых нагретые до 390 – 395 0С соединяемые детали выдерживают длительное время, исчисляемое десятками минут. Прочность сварных соединений не превышает 50 – 60 % основного материала. По этим причинам сварка изделий из данного материала затруднена, технологический процесс не обеспечивает достаточной прочности соединений, отличается низкой производительностью и высокой стоимостью.
Разработан процесс термоультразвуковой сварки, при которой рабочий инструмент – волновод и опора используются для передачи тепла от электрических нагревателей к поверхностям деталей.
Цикл сварки имеет три этапа: нагрев полимера до температуры сварки, выдержка соединяемых поверхностей при температуре сварки, охлаждение деталей под давлением (рис.63).
Вследствие низкой теплопроводности термопласта продолжительность первого этапа зависит от толщины свариваемых деталей (для δ = 2 – 6 мм составляет 2 – 4 мин). Сокращение времени нагрева путем повышения температуры нагревателя приводит к деструкции полимера на поверхностях, прилегающих к нагревателям, и к снижению качества соединения. Наложение ультразвуковых колебаний одновременно с введением тепла в зону соединения позволяет сократить время разогрева полимера на 30 – 40 %. При амплитуде ультразвуковых колебаний более 20 мкм нагрев материала в зоне соединения неравномерный, при амплитудах 5 – 15 мкм перегрева отдельных участков полимера не происходит, но температура зоны соединения не достигает сварочной даже при длительном воздействии УЗ – колебаний. При совмещении ультразвукового и теплового нагрева деструкция и перегрев наблюдались уже при амплитудах выше 15 мкм, и лишь в диапазоне 5 – 10 мкм разогрев полимера в зоне соединения происходит равномерно и достижение сварочных температур не сопровождается деструкцией.
|
![]() | |||
![]() |
Рис. 63. Технологический цикл сварки: I – разогрев полимера; II – выдержка при температуре сварки; III – охлаждение под давлением; 1 – тепловая сварка; 2 – сварка теплом с наложением ультразвуковых колебаний
Второй этап цикла сварки фторопласта-4 оказывает основное влияние на прочность и качество соединений. Продолжительность этого этапа определяется скоростью диффузионных процессов, наложение ультразвуковых колебаний и теплового воздействия позволяет ускорить диффузию макромолекул и тем самым сократить время второго этапа сварки, а также повысить качество соединения.
На третьем, последнем этапе сварки после отключения ультразвука и тепловой энергии материал в зоне соединения охлаждается, при этом важным показателем является скорость охлаждения, которая в интервале 390 – 250 0С не должна превышать 50 град/мин, так как при этих температурах укрепляются вновь образовавшиеся межмолекулярные связи и растут надмолекулярные образования. Характер протекания этих процессов заметно влияет на качество соединения, поэтому сокращение данного этапа сварочного цикла нежелательно. Время первого и третьего периодов цикла в допустимых пределах можно сокращать путем более сильного нагрева инструмента и ускоренного принудительного охлаждения шва после сварки.
Данный способ можно использовать для соединения не только блочного фторопласта, но и фторопластовых пленок.
|
Рациональным способом совмещения контактного нагрева с ультразвуковым воздействием является радиационный или индукционный нагрев ультразвукового волновода - инструмента стандартной расчетной формы и его опоры с передачей этого тепла контактным способом к свариваемым деталям. Нагрев УЗ волновода – инструмента и опоры производится путем конвективного и лучистого теплообмена с расположенными на близком расстоянии электронагревателями.
В качестве рабочего элемента конструкции нагревателей радиационного типа могут быть применены электроспираль сопротивления, нихромовая полоса или лента из других высокоомных сплавов (рис.64). Такие нагреватели просты в изготовлении, заданную температуру можно поддерживать, изменяя напряжение их питания. В целях повышения надежности работы электрической спирали и безопасности использования, ее питание обычно должно быть пониженным (24 – 36 В), при этом диаметр проволоки выбирают в пределах 0,8 – 2 мм.
Со стороны обращенной к ультразвуковому инструменту устанавливают экран из хорошо проводящего тепло материала, например, слюды или керамики; с наружной стороны нагреватель защищают асбестовой оболочкой, заключенной в стальной кожух (рис.64). В процессе работы нагреватель не должен контактировать с инструментом, поэтому кронштейн для его закрепления связывают с корпусом ультразвукового преобразователя или с диафрагмой трансформатора колебаний. Ультразвуковые колебания, попадая на электроспираль, находящуюся при температуре 800 – 900 0С, мгновенно разрушают ее.
Для поддержания температуры инструмента постоянной в заданных пределах, при сварке по схеме «на протяг» нагреватель должен обладать достаточной температурной инерцией, т.е. быть массивным. В противном случае температура инструмента при непрерывной сварке вследствие постоянного контакта инструмента со все новыми слоями свариваемого материала снижается, что отрицательно сказывается на качестве сварного соединения. Электрическая мощность нагревателя рассчитывается по теплоемкости материала и его теплосодержанию, определяемому температурой сварки и объемом разогреваемого материала.
Нагреватели опорного элемента, а также нагреватели для сварки трубопроводов в конструктивном отношении аналогичны нагревателям для разогрева ультразвукового инструмента. При использовании вращающейся опоры электрическую спираль размещают на неподвижных частях корпуса с одной или с двух сторон вращающегося опорного ролика (рис.65). Кольцевые нагреватели для сварки фторопластовых трубопроводов выполняют в виде расположенного по окружности трубы набора прямоугольных стержней, подвижно соединенных между собой.
|
При сварке пленочных плавких фторопластов возможно также применение нагревателей в виде нихромовой полосы с поперечным сечением, обеспечивающим ей сохранение жесткости в процессе работы в нагретом состоянии. Полосу помещают между торцом ультразвукового инструмента и свариваемой деталью, передавая к зоне соединения и ультразвуковые колебания, и давление от инструмента. Такие нагреватели надежны в работе, однако требует тщательного экспериментального подбора напряжения питания в зависимости от скорости сварки (рис.66).
![]() | |||||
| |||||
| |||||
5.13.2. Фрикционно-ультразвуковая сварка
Сварка полимеров трением имеет недостатки: в зоне шва создается неравномерный нагрев и напряжения, снижающие качество соединений; большое количество грата и концентрация напряжений; перегрев и деструкция материала; ограниченность применения процесса и др.
Комбинирование трения и ультразвука позволило избежать ряда недостатков, присущих как процессу трения, так и УЗС, и получать новые эффекты процесса сварки, обеспечивающие качественные соединения полимеров, имеющих неудовлетворительную свариваемость, например полиамидов.
Полиамиды относятся к плохо свариваемым полимерам, так как имеют относительно высокую температуру плавления (217 – 222 0С), плавятся в узком интервале температур (5 – 7 0С) и резко переходят в вязкотекучее состояние с низкой вязкостью расплава (200 – 400 Па·с). В расплавленном состоянии полиамиды подвергаются термоокислительной деструкции, вызывающей ухудшение механических свойств материала. Поэтому как сварка трением, так и сварка ультразвуком, применяемые в отдельности, не обеспечивают высокого качества соединений. При сварке трением жидкий маловязкий расплав вытесняется из зоны трения, а в контакт входят более холодные твердые слои, что затрудняет протекание диффузионных процессов и не обеспечивает высокой прочности соединений. При УЗС из-за малого интервала времени сварки полиамидов появляются очаги деструкции и неравномерность нагрева и образования сварного соединения.
|
Основные параметры режима сварки: статическое усилие сжатия образцов при трении; скорость относительного движения деталей (скорость трения); время трения; амплитуда колебаний инструмента; время действия УЗК; давление при действии ультразвука.
Для получения качественных соединений важной является последовательность действия трения и ультразвука, т.е. характер циклограммы процесса сварки. Наиболее эффективной оказалась циклограмма, при которой включение УЗ проводилось в момент, когда в зоне соединения температура достигала 190 – 200 0С. Процесс трения продолжается совместно с действием ультразвука до полного и равномерного расплавления материала по всему стыку. После этого трение и ультразвук выключают одновременно. Такой цикл сварки обеспечивает равномерное распределение температуры по периметру стыка (перепад не превышает 5 – 10 0С). При образовании очагов перегрева и оплавлении полимера, последний, в результате относительного движения деталей попадает на соседние более холодные участки, передавая им тепло. При этом наблюдается не только относительное перемещение свариваемых деталей, но и перемещение по периметру стыка массы расплавленного материала, увлекаемого в результате схватывания, возникающего на отдельных участках шва.
Совместное применение трения и ультразвука позволило снизить давление в зоне соединения и тем самым обеспечить увеличение глубины проплавления материала за счет уменьшения его пластического течения и выдавливания из зоны шва.
Оптимальным диапазоном значений амплитуды смещений волновода – инструмента является диапазон А = (20 ÷ 35) мкм. В этом диапазоне амплитуд наблюдается наибольшее влияние колебаний на тепловую обстановку в зоне шва.
ИК – ультразвуковая сварка
Процесс ИК – ультразвуковой сварки (ИК - УЗС) имеет некоторые особенности: необходимо ИК – излучающий элемент проектировать так, чтобы происходил равномерный нагрев полимера по всему сечению на глубину 0,8 – 1,5 мм до температуры сварки; при получении стыковых соединений УЗ – колебания необходимо вводить так, чтобы в зоне стыка траектории колебаний были ориентированы нормально соединяемым поверхностям; полимерные материалы не допускается длительное время подвергать воздействию высоких температур и перегреву, поэтому предварительный ИК – нагрев должен удовлетворять этим требованиям.
|
ИК – УЗС встык изделий из полиамида выполняется по схеме, представленной на рис.67, и включает следующие этапы: нагрев стыкуемых поверхностей инфракрасными лучами; удаление нагревателя из зоны сварки; сближение стыкуемых поверхностей и их осадка с усилием РОС = (0,09 – 0,11) МПа; включение УЗ и создание импульса длительностью 0,5 – 2 с; выключение УЗ и охлаждение шва под давлением РОС.
В ИК – УЗ процессе важным является получение в зоне шва колебаний частиц среды, направленных нормально к плоскости стыка. Такие колебания получаются в результате расширения (сдвига) полимера под действием сжатия его в зоне, расположенной под УЗ – инструментом. При этом под действием продольных смещений, направленных перпендикулярно направлению распространения основной УЗ – волны, возникают продольные колебания, направленные перпендикулярно направлению распространения основной волны.
УЗ – колебания могут вводиться как в один из свариваемых элементов, так и в оба элемента. При малой площади сечения свариваемых элементов ультразвук следует вводить в один из стыкуемых элементов. При площади стыкуемых элементов, превышающей 7 – 9 см2, колебания вводят в оба элемента.
Ввод ультразвука в подвижный стыкуемый элемент предпочтительнее, так как позволяет устранить подплавление полимера под инструментом путем подачи под инструмент новых холодных участков детали в результате перемещения подвижной детали.
Сущность процесса ИК – УЗС состоит в следующем. На стадии I (рис.67) энергией ИК – излучения полимер прогревается до температуры 190 – 200 0С на глубину до 1,5 мм для создания определенного объема размягченного полимера с целью локализации теплообразования и создания оптимальных условий для протекания реологических процессов под действием УЗ.
Рис.67. Этапы ИК – УЗС полимеров встык: I – ИК – нагрев: II – ультразвуковое воздействие; III – охлаждение; 1 – свариваемые детали; 2 – неподвижные зажимы; 3 – подвижные зажимы; 4 – резиновая опора; 5 – ИК – нагреватель; 6 – ультразвуковой волновод – инструмент; 7 - шов
На стадии II после включения УЗ происходит преимущественно разогрев полимера в зоне размягченной прослойки и повышение температуры на этом участке до 210 – 225 0С, т.е. до температуры сварки и выше. Образующийся расплав под действием давления осадки частично вытесняется в грат. При этом из зоны сварки удаляется полимер, подвергшийся при ИК – нагреве окислительной деструкции, а в зону соединения подводится чистый полимерный материал, подогреваемый энергией УЗ до температуры сварки. Кроме того, ультразвуковые колебания устраняют возникающую ориентацию в зоне стыка. УЗ – колебания создают реологические процессы и ускоряют диффузию.
На стадии III ультразвук отключается, а давление осадки может оставаться неизменным или понижаться до значений, при которых прекращается вытеснение расплава из зоны шва. Происходит охлаждение материала в зоне шва под незначительным избыточным давлением, что исключает появление пор и несплошностей в шве, а также обеспечивает необходимую кристалличность полимера, чем гарантируется прочность и пластичность материала.
ИК – УЗС позволяет получать соединения на таких трудно свариваемых полимерах, как полиамиды ПА-610 и АК80/20. Прочность соединений при этом достигает 90 – 92 % основного материала, а пластичность не отличается от пластичности основного материала.
Данный способ может успешно применяться для получения сварных соединений на изделиях из любых термопластичных полимеров.
Сварка биологических тканей
При выполнении традиционных хирургических операций соединяемые поверхности с целью получения биологических соединений (БС) плотно прижимают друг к другу с помощью внешних устройств (ниточные швы, металлические конструкции и др.) и выдерживают в таком состоянии в течении регенерационного периода. В этом случае исходная прочность БС отсутствует, начинает возрастать с нуля в течение периода регенерации и через определенное время достигает прочности исходной биоткани. Недостатками традиционных операций являются травматичность и длительный цикл регенерации, сложность, а иногда невозможность выполнения многих операций, зависимость от субъективных факторов, низкая надежность.
При УЗС стремятся получить максимально возможную прочность за счет биологических сварных соединений (БСС), ликвидируя внешние удерживающие устройства. Однако, как показала практика, простой перенос положений сварочной науки и техники на живые объекты не приводит к ожидаемым положительным результатам.
Живые ткани, обладая свойствами самосохранения, не терпят вмешательств, нарушающих их состояние, отторгают инородные тела, регенерируют нарушенную физическую, химическую и в целом биологическую исходную целостность. Это приводит к быстрой и значительной потере прочности БСС и его разрушению до появления достаточной биологической прочности. Конкурируют два явления. С одной стороны, монолитность и прочноплотное удержание соединяемых поверхностей ускоряет регенерацию, с другой стороны, регенерация замедляется из-за нарушения биологической целостности прилегающего к соединяемым поверхностям биополимера, подвергавшегося воздействию энергии ультразвука. Определить вклад этих явлений в образование БСС невозможно, поэтому процесс УЗС биополимеров следует считать трудно управляемым, что не позволяет широко применять процесс УЗС в медицине, хотя он обладает значительным потенциалом.
В настоящее время определились три основных направления применения ультразвука в медицине: сварка (соединение), наплавка (воссоздание) и обработка биологических тканей.
При УЗС и наплавке костных тканей используется присадочный материал, состоящий из жидкого полимерного вещества циакрина и наполнителя на основе костной стружки.
Сущность процесса соединения биотканей состоит в том, что УЗ - колебания, вводимые в присадочный материал, ускоряют процессы диффузии и процессы полимеризации циакрина, с образованием твердого костно-циакринового конгломерата, который в процессе заживания раны замещается новообразованными костными клетками. Конструкция сварных соединений при этом ничем не отличается от традиционно применяемых в хирургии.
При сварке мягких биологических тканей присадочный материал не применяется. Соединение образуется за счет расплавления коллагена6 и его диффузии в соединяемые ткани. При этом соединяемые части предварительно сжимают и затем воздействуют на них ультразвуком. С целью повышения прочности БСС и его долговечности в зону соединения вводят «сшивающие» реагенты. Для увеличения содержания в ткани коллагена в зону шва вводят выделенные из живых объектов и синтезированные коллаген, желатин, плазму.
Механизм процесса сварки ультразвуком мягких биологических тканей состоит в следующем. Воздействуя энергией ультразвука на мягкую ткань, содержащую до 40 % коллагена, нагревают биополимер в зоне шва до температуры 60 0С. Нагрев должен быть кратковременным, чтобы не вызывать некроза7 тканей. При температуре 40 – 60 0С коллаген становится жидким и интенсивно диффундирует через соединяемые поверхности живых тканей. Граница раздела исчезает.
__________________
6 КОЛЛАГЕН - (от греч. kolla - клей и...ген) фибриллярный белок, составляющий основу соединительной ткани (сухожилие, кость, хрящ) и обеспечивающий ее прочность.
7 НЕКРОЗ - (от греч. nekrosis - омертвение) омертвение ткани под влиянием нарушения кровообращения, химического или термического воздействия (ожог, отморожение), травмы и др.
Плавится и введенный извне коллаген или желатин, увеличивая процентное содержание коллагена в ткани. После прекращения действия ультразвука зона шва охлаждается, и коллаген приобретает исходную прочность, а шов прочность живой ткани. Однако коллаген подвержен растворению в биологических жидкостях живого организма, и БСС в процессе регенерации быстро теряет прочность. При этом скорость снижения прочности БСС больше скорости увеличения прочности БС. Через 1,5 – 2 сут после операции суммарная прочность БСС + БС не превышает 7 – 10 % от прочности основного материала, что может привести к разрушению БСС.
Ввод в зону шва сшивающего реагента делает коллаген частично нерастворимым и неплавким, что не позволяет получать БСС, равнопрочные основному материалу в момент операции, однако и скорость снижения прочности такого БСС ниже, чем без реагента и стабилизируется при 18 – 20 % от прочности основного материала спустя 6 – 7 сут после операции. За это время БС набирает прочность до 15 – 20 % от основного материала, а суммарная прочность имеет минимальное критическое значение на третьи сутки послеоперационного периода и не уменьшается ниже 30 % от прочности основного материала. В большинстве операций такой прочности достаточно, чтобы не допустить разрушения БСС.
|
|
Индивидуальные и групповые автопоилки: для животных. Схемы и конструкции...
Наброски и зарисовки растений, плодов, цветов: Освоить конструктивное построение структуры дерева через зарисовки отдельных деревьев, группы деревьев...
Двойное оплодотворение у цветковых растений: Оплодотворение - это процесс слияния мужской и женской половых клеток с образованием зиготы...
Механическое удерживание земляных масс: Механическое удерживание земляных масс на склоне обеспечивают контрфорсными сооружениями различных конструкций...
© cyberpedia.su 2017-2024 - Не является автором материалов. Исключительное право сохранено за автором текста.
Если вы не хотите, чтобы данный материал был у нас на сайте, перейдите по ссылке: Нарушение авторских прав. Мы поможем в написании вашей работы!