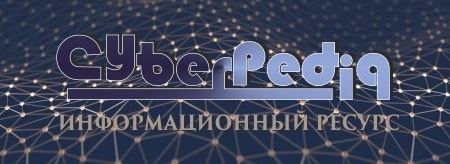
Семя – орган полового размножения и расселения растений: наружи у семян имеется плотный покров – кожура...
Индивидуальные очистные сооружения: К классу индивидуальных очистных сооружений относят сооружения, пропускная способность которых...
Топ:
Основы обеспечения единства измерений: Обеспечение единства измерений - деятельность метрологических служб, направленная на достижение...
Особенности труда и отдыха в условиях низких температур: К работам при низких температурах на открытом воздухе и в не отапливаемых помещениях допускаются лица не моложе 18 лет, прошедшие...
Интересное:
Отражение на счетах бухгалтерского учета процесса приобретения: Процесс заготовления представляет систему экономических событий, включающих приобретение организацией у поставщиков сырья...
Финансовый рынок и его значение в управлении денежными потоками на современном этапе: любому предприятию для расширения производства и увеличения прибыли нужны...
Что нужно делать при лейкемии: Прежде всего, необходимо выяснить, не страдаете ли вы каким-либо душевным недугом...
Дисциплины:
![]() |
![]() |
5.00
из
|
Заказать работу |
|
|
Заключительный этап проектирования производственного процесса — определение трудоемкости его операций, а также расчетной длительности каждой из них и всего производственного цикла изготовления заданного изделия. Эти данные получают в результате технического нормирования трудоемкости операций и времени, затрачиваемого на их выполнение. При проектировании производственных процессов следует учитывать различия в нормировании ручных и- механизированных операций.
При нормировании ручных работ продолжительность каждой операции определяют с учетом числа рабочих, выполняющих одновременно и совместно данную производственную операцию. Применяемые в этом случае единичные нормы представляют собой практически проверенные данные о необходимом количестве труда для выполнения какой-либо единицы работы (сварка 1 м шва либо одного стыка и т. п.) в заданных (или выбранных проектантом) производственных условиях и при соблюдении рациональных технологических режимов данной работы.
В результате нормирования ручных сборочно-сварочных и заготовительных работ получают следующие две величины, характеризующие время и труд, требуемые для выполнения каждой запроектированной операции: tч — продолжительность работ, измеряемую обычно в минутах или часах, и — трудоемкость работ, получаемую путем умножения единичной нормы на число единиц работы, включенных в данную операцию; значения этой веичины выражают в единицах трудоемкости — в человеко - минутах или в человеко-часах (либо в нормо-часах).
Очевидно, что трудоемкость каких-либо ручных работ , подсчитанная по нормам для некоторых определенных производственных условий данного технологического процесса, характеризует необходимое количество труда для их выполнения
|
= const, (6.1)
где — величина постоянная в течение всего времени, пока не изменятся производственные условия или технологический процесс. В то же время продолжительность тех же работ tч представляет собой переменную величину, зависящую от числа рабочих nч, принимающих участие в этих работах:
, (6.2)
Естественно, что трудоемкость и продолжительность ручных работ будут численно равны между собой в тех случаях, когда число рабочих, выполняющих данную операцию, будет равно единице. Во всех остальных случаях числовое значение продолжительности работ значительно меньше числового значения трудоемкости тех же работ.
Число рабочих на одном рабочем месте (на сборочно-сварочном стенде, стеллаже и т. п.), выполняющих работу совместно и одновременно, обозначают термином «плотность работ» и выражают в «человек-место». Таким образом, трудоемкость ручных работ в человеко-минутах или человеко-часах путем деления ее на плотность работ
может быть выражена в других единицах трудоемкости — в место-минутах или в место-часах
, (6.3)
Очевидно, что для каждого отдельного сборочно-сварочного рабочего места продолжительность выполнения сборочно-сварочных операций в минутах или часах всегда численно равна трудоемкости тех же операций, выраженной в место-минутах или в место-часах.
В случаях определения продолжительности работ, производимых на каком-либо станке, руководствуются сведениями о производительности этого станка при оптимальных режимах его работы. Исходя из этих данных подсчитывают единичную норму времени на обработку единицы материала либо на обработку одной детали. Что же касается рабочих, обслуживающих в процессе работы данный станок, что число их обычно не влияет на его производительность и поэтому должно учитываться особо, по соображениям рациональной загрузки их операциями, необходимыми для обслуживания станка.
|
Таким образом, при нормировании технологического процесс станочных работ получают следующие величины, характеризующие время и труд, необходимые для выполнения каждой операции: продолжительность работ, измеряемую в минутах или часах, и трудоемкость работ, получаемую путем умножения единичной нормы трудоемкости на число единиц работы, включаемых в данную станочную операцию; эту величину измеряют в единицах трудоемкости — в станко-минутах или станко-часах.
Очевидно, что для каждого отдельного станка продолжительность выполнения станочных операций в минутах или часах всегда численно равна трудоемкости тех же операций, выраженной станко-минутах или станко-часах.
Более подробные данные по техническому нормированию технологических процессов при проектировании сборочно-сварочных цехов (отделений, участков) приведены в соответствующих нормативных и справочных материалах и источниках.
После определения трудоемкости всех операций по изготовлению заданных изделий могут быть выполнены последующие расчеты. Так, посредством суммирования трудоемкости всех последовательных рабочих операций проектируемого технологического процесса может быть получена суммарная трудоемкость работ по изготовлению одного изделия. При этом понятно, что трудоемкости ручных и станочных работ следует подсчитывать раздельно. Кроме того, путем суммирования трудоемкостей соответствующих операций и умножения их на количество заданных изделий могут быть получены значения трудоемкости работ на всю годовую производственную программу для каждого предусмотренного технологическим процессом типоразмера станка или сборочно-сварочного рабочего места и для каждой профессии и специальности производственных рабочих в отдельности.
Числовые значения указанных величин трудоемкости работ на годовую программу представляют собой исходные данные для расчетов по определению требуемого количества оборудования рабочих мест и числа рабочих для проектируемого цеха. При этом связующим звеном между значениями трудоемкости работ на годовую программу и потребными количествами перечисленных основных элементов производства служат фонды времени оборудования, рабочих мест и рабочих.
|
Полученные в результате технического нормирования всех операций проектируемого производственного процесса (технологических, контрольных и подъемно-транспортных) числовые значения их продолжительности дают возможность определять об-щую продолжительность изготовления заданного изделия, т. е. длительность его производственного цикла. Эта величина служит показателем уровня организации производственного процесса, а следовательно, показателем качества его разработки. Следовательно, чем меньше производственный цикл изготовления изделия, тем больше пропускная способность (производительность) цеха, отделения, участка, тем быстрее оборачиваемость оборотных средств предприятия-изготовителя данных изделий, тем меньше необходимая для выполнения программы сумма оборотных средств производства. Поэтому определение длительности производственного цикла для каждого типа заданных для изготовления в проектируемом цехе изделий имеет весьма существенное значение и является обязательным заключительным этапом разработки проекта производственного процесса.
В случаях изготовления весьма простых изделий, не поддающихся расчленению на отдельные сборочные единицы, длительность производственного цикла Тц. п каждого из них, очевидно, равна сумме продолжительностей всех операций запроектированного производственного процесса (tт — технологических, tK — контрольных и tn — подъемно-транспортных):
, (6.4)
Для изделий достаточно сложных, расчленяемых на отдельные сборочные единицы, изготовление которых может осуществляться одновременно на разных рабочих местах, длительность Тц.спроизводственного цикла всегда меньше указанной выше суммы продолжительностей всех операций запроектированного производственного процесса:
, (6.5)
В подобных случаях величину производственного цикла определяют путем построения графика циклограммы последовательно-параллельного выполнения всех операций (рис. 1). На таком графике по оси ординат откладывают точки, соответствующие предусмотренным в запроектированном производственном процессе рабочим местам (станкам, сборочным стеллажам, испытательным стендам и пр.), а по оси абсцисс — продолжительность операций, т. е. время. При построении графика следует стремиться к получению минимально возможного значения длительности производственного цикла Тц. с, что достигается путем максимального расчленения заданного изделия на отдельные сборочные единицы и одновременного их изготовления.
|
Рисунок 1. Пример циклограммы изготовления сложного изделия
Продолжительность операций
7.Технеко-экономическая оценка вариантов технологии производства
Разработка проекта производственного процесса изготовления заданных изделий, как всякая техническая задача, обычно допускает различные варианты решения возникающих вопросов. Наиболее часто такие варианты относятся к разным технологическим способам изготовления продукции, различной степени механизации производственного процесса, разным типам оборудования и оснастки рабочих мест и т. п. При этом использование каждого варианта в отдельности удовлетворяет требованиям к качеству заданной продукции в соответствии с техническими условиями на ее приемку.
Наиболее целесообразный вариант из числа возможных в практике проектирования определяют на основе технико-экономического их сравнения. В результате такого сравнения выбирают лучший вариант, являющийся применительно к заданной программе выпуска изделий наиболее рациональным в техническом и наиболее рентабельным в экономическом отношении.
Методика сравнительной технико-экономической оценки проектируемых вариантов технологии производства сводится к следующему. Применительно к сварочному производству технические преимущества и недостатки сравниваемых вариантов подлежат оценке по присущим каждому из них значениям указанных ниже основных характеристик и показателей:
прогрессивность технологии производства, определяемая высокой производительностью применяемых сварочных процессов, отсутствием существенных препятствий для комплексной их механизации и автоматизации, возможностью достижения высокого качества заданной продукции и снижения ее трудоемкости при обеспечении безопасности и безвредности выполняемых работ;
длительность производственного цикла изготовления заданной продукции (лучшему варианту присуща наименьшая длительность производственного цикла);
габаритные размеры и масса необходимого технологического оборудования (лучшему варианту присущи наименьшие габаритные размеры и масса оборудования);
площадь и кубатура здания цеха, необходимые для организации производственного процесса (лучший вариант отличается наиболее компактным его размещением в цехе);
|
требуемое число рабочего и обслуживающего персонала для изготовления заданной продукции (лучший вариант требует наименьшего числа указанного персонала);
удельная производительность технологии изготовления заданной продукции, определяемая показателями ее годового выпуска на одного рабочего и на 1 м2 площади, занятой производственным процессом.
Результатов сопоставления между собой сравниваемых вариантов технологии производства заданной продукции по перечисленным выше техническим характеристикам и показателям еще недостаточно для определения оптимального варианта. Последний может быть выявлен путем экономического анализа наиболее прогрессивных и конкурирующих между собой в техническом отношении вариантов. Поэтому техническую оценку сравниваемых вариантов технологии производства всегда дополняют их экономической оценкой.
Согласно утвержденной методике для оценки экономической эффективности применения различных вариантов техники в промышленности следует определять соответствующие каждому варианту годовые приведенные затраты 3 по формуле
3 = С + ЕНК, руб/год, (7.1)
где С — себестоимость годового выпуска продукции, руб.; К. — капитальные вложения в производственные фонды, руб.; Ен — нормативный коэффициент эффективности капитальных вложений, принимаемый в расчетах равным 0,15; ЕНК — сумма ежегодного погашения капитальных вложений, руб.
Лучший вариант характеризуется наименьшей величиной 3 приведенных годовых затрат.
В подсчеты капитальных вложений и себестоимости годового выпуска продукции по сравниваемым вариантам достаточно вводить затраты только по тем элементам капиталовложений и себестоимости, по которым сравниваемые варианты различаются между собой. Такое упрощение расчетов не влияет на действительное соотношение их результатов по сравниваемым вариантам. Указанную «упрощенную» себестоимость продукции называют технологической себестоимостью в отличие от полной себестоимости, в которую входят все без исключения издержки.
В сварочном производстве вообще и особенно при изготовлении деталей, наплавленных износостойкими сплавами, нередко различные варианты технологии сварки (наплавки) обеспечивают разное качество продукции. Последнее выражается обычно эксплуатационными показателями долговечности (срок службы либо износостойкость наплавленных деталей) или показателями удельного расхода на единицу обрабатываемого материала (например, количество расходуемых наплавленных лемехов на каждые 1000 га пашни, обрабатываемой тракторными плугами). В подобных случаях в описанные выше расчетные формулы следует вместо фактической себестоимости Ct годового выпуска продукции вводить его скорректированную себестоимость Ск с учетом изменения качества изделий
В подтверждение этого можно привести немало примеров, когда технологический вариант, отличающийся наиболее низкой цеховой себестоимостью наплавленных деталей, не обеспечивает у потребителя этих деталей наибольший срок их службы сравнительно с деталями, наплавленными с применением более дорогой технологии. Лучший вариант должен быть оптимальным с точки зрения потребителя продукции.
Экономический анализ необходим также тогда, когда имеется всего один вариант технологического процесса. При этом анализ дает возможность выявить недостатки разработанного варианта и пути рационализации предусмотренного производственного процесса либо необходимость замены его другим процессом, экономически более эффективным.
Чаще всего в практике проектирования выполняют экономическое сравнение производственного процесса, разработанного в представляемом на утверждение проекте, с другими вариантами процессов, принятыми в ранее утвержденных проектах аналогичного либо подобного производства. В таких случаях для обеспечения сопоставимости сравниваемых вариантов непременным условием является приведение их программ годового выпуска продукции к одинаковым либо близким количественным значениям. По каждому сравниваемому варианту проекта определяют годовые приведенные затраты после следующих ее преобразований. Входящую в эту формулу себестоимость С годового выпуска продукции для упрощения расчетов представляют в виде цеховой технологической себестоимости, т. е. включающей только те элементы себестоимости, которыми сравниваемые варианты различаются между собой.
Оборудование и оснастка для выполнения производственного процесса, предусмотренного в проекте цеха (отделения, участка), являются одними из основных элементов проектируемого производства. Поэтому при разработке проекта необходимо установить рациональный качественный и количественный состав оборудования и оснастки.
В соответствии с принятыми технологическими способами изготовления деталей, сборки и сварки сборочных единиц и в целом заданных изделий при детальной разработке технологии производства уточняют первоначально намеченные типы оборудования и оснастки для выполнения всех видов работ в проектируемом цехе.
Основными критериями для окончательного выбора рациональных типов оборудования и оснастки должны служить их следующие признаки: техническая характеристика, наиболее отвечающая всем требованиям принятой в разрабатываемом проекте цеха технологии операций, подлежащих выполнению на данном оборудовании или посредством данной оснастки; наибольшая эксплуатационная надежность и относительная простота обслуживания; наибольший КПД и наименьшее потребление энергии при эксплуатации; наименьшие габаритные размеры оборудования, обусловливающие минимальную необходимую площадь для размещения его в цехе; наименьшая возможная масса, что обычно характеризует относительно прямо пропорциональную ей стоимость оборудования; наименьшая сумма первоначальных затрат на приобретение и монтаж в цехе данного оборудования либо оснастки, обеспечивающая минимальный возможный срок их окупаемости.
Для подбора рациональных современных типов оборудования и оснастки, соответствующих перечисленным выше признакам, следует пользоваться новейшими данными справочной и информационной литературы, специальными руководствами по оборудованию для отдельных видов технологии, учебными пособиями и учебниками по специальным курсам сварочного, сборочного, подъемно-транспортного и другого технологического оборудования и оснастки, а также проспектами и каталогами, издаваемыми отдельными ведомствами машиностроительной промышленности, в которых приведены описания, технические характеристики и стоимость отдельных типов оборудования и оснастки, возможных для использования в проектах сборочно-сварочных цехов. При этом особое внимание следует уделять наиболее прогрессивным процессам сварочной техники и необходимым для их выполнения типам оборудования и оснастки, отличающимся высокой производительностью. Выбор такого оборудования, как правило, обеспечивает максимальную пропускную способность проектируемого цеха (отделения, участка) и минимальные сроки окупаемости капитальных затрат на его приобретение.
При окончательном составлении перечня выбранных для проектируемого цеха типов оборудования и оснастки следует включать в него не только технологическое основное и вспомогательное оборудование, устройства и оснастку всех видов, но также требуемое оборудование для всех звеньев запроектированного производственного процесса и контроля качества продукции цеха. В этот перечень следует включать также оборудование общецеховых устройств и производственный инвентарь, необходимые для обеспечения нормальных условий работы в проектируемом цехе.
Количественный состав окончательно выбранных для проектируемого сварочного производства различных типов сборочных стендов (рабочих мест), сварочных установок и прочего оборудования и оснастки устанавливают путем следующих несложных расчетов. Требуемые для выполнения заданной производственной программы числа сборочно-сварочных рабочих мест или стендов пм и станочного оборудования или сварочных установок п0 каждого типа определяют по формулам
, (7.2)
, (7.3)
где Тм — количество место-часов; Тч — количество человеко-часов; Тс — количество станко-часов соответственно трудоемкости работ (на годовую программу), закрепленных за сборочно-сварочным рабочим местом или станочным оборудованием каждого данного типа; — плотность работ, человек/рабочее место; Фм и Фс — действительные годовые фонды времени рабочих мест и оборудования.
Равным образом для определения по тем же формулам требуемого числа постоянных (стационарных) рабочих мест технического контроля качества продукции и необходимого числа испытательных стендов следует при подсчете трудоемкости работ на годовую программу учитывать принятые для каждой контрольной операции значения процентов выборочности.
В случае получения по формулам дробных числовых значений искомых величин их округляют до ближайшего большего целого значения. Делением расчетных значений (пм и п0) на принятые округленные (nп.м. и пп,0) определяют проектные коэффициенты загрузки k3 этих рабочих мест и оборудования
k3 = nм:nn.м или кз = n0:nn,0.
К изложенному выше следует добавить, что при определении общего числа рабочих мест (стендов) в сборочно- сварочных отделениях проектируемого цеха особо рассматривают и решают вопрос об определении числа дополнительных рабочих мест для исправления пороков сварной продукции, выявленных средствами технического контроля в процессе ее изготовления, а также при окончательной приемке-сдаче готовой продукции. Возможное число таких рабочих мест не может быть регламентировано в каком-либо общем виде. Его устанавливает проектант в каждом конкретном случае сообразно со степенью ответственности изготовляемых изделий, характером производственного процесса, обеспечивающего определенную степень однородности качества изделий, и требованиями технических условий на их изготовление и приемку.
При практическом решении рассматриваемой задачи необходимо учитывать, что организация исправления брака, обнаруженного в процессе изготовления отдельных сборочных единиц и комплектов сварных изделий, а также при окончательных испытаниях последних имеет свои отличительные особенности, зависящие от типа производства.
В единичном производстве брак продукции исправляют на рабочих местах рабочие, допустившие брак.
В массовом производстве, отличающемся поточным характером выполнения работ с принудительным ритмом выпуска продукции, сборочные единицы, комплекты и целые изделия немед ленно после обнаружения в них брака снимают с рабочих мест, расположенных на потоке, и отправляют на особые рабочие места вне потока, предназначенные исключительно для работ по исправлению пороков продукции цеха специальными бригадами рабочих. Такая организация исправления брака не нарушает существенно общей стройности поточного производства и является единственно правильной в поточном производстве.
Что касается серийного производства, то в зависимости от большего или меньшего приближения проектируемого производства к типу поточного организация исправления брака продукции может быть осуществлена одним из указанных способов.
Таким образом, при проектировании единичных и непоточных серийных сварочных производств исправление пороков продукции предусматривают за счет соответствующего повышения загрузки сборочно-сварочных рабочих мест цеха (отделения, участка).
В случаях проектирования массовых и серийных поточных производств требуемое число рабочих мест для исправления сварной продукции назначают в соответствии со степенью ответственности изготовляемых изделий, однородности их качества и в зависимости от жесткости технических условий на их изготовление и приемку. Практически в конце каждой поточной линии предусматривают по одному резервному стенду для внепоточного исправления пороков изготовляемой сварной продукции.
Количество различной оснастки для сборочно-сварочных рабочих мест (стендов) и стандартного оборудования (например, разного рода приспособлений, рольгангов, склизов, стационарных консольных кранов и других местных подъемно-транспортных устройств) назначают исходя из практической потребности в них на рабочем месте каждого данного типа. При этом учитывают возможность в некоторых случаях использования этих устройств для обслуживания от двух до четырех рядом расположенных рабочих мест (станков).
Иначе выбирают и подсчитывают требуемое количество средств общего транспорта (электрокаров, автокаров, мостовых кранов и т. д.), обслуживающих пролет или отдельные его участки. При выборе этих средств внутрицехового транспорта необходимо рационально сочетать работу различных видов транспортных устройств и максимально использовать напольные транспортные средства (электрокары, автокары, козловые либо портальные краны и т. п.), поскольку применение мостовых кранов, в особенности большой грузоподъемности, обусловливает существенное увеличение веса колонн, несущих подкрановые пути, что влечет значительное удорожание строительных конструкций здания цеха.
Указанные выше предпосылки должны быть приняты во внимание при выборе средств общего транспорта, получившего наибольшее применение в проектах сварочных производств единичного и серийного типа, в то время как в проектах крупносерийного и особенно массового производства преимущественное применение получают специализированные средства внутрицехового транспорта — различные типы конвейеров, причем нередко автоматизированные. При этом из напольных средств общего транспорта следует предпочитать безрельсовые (электрокары и автокары) как обладающие большей степенью свободы перемещений и не загромождающие площадь цеха устройством рельсовых путей и поворотных кругов.
Выбор типов средств общего внутрицехового транспорта непосредственно связан с распределением грузопотоков по отдельным пролетам цеха, которое вытекает из принятой специализации пролетов в проектируемом цехе. Поэтому прежде всего для выяснения условий работы проектируемого транспорта в соответствии с разработанным ранее производственным процессом и его планировкой составляют ведомость движения грузов (материалов, полуфабрикатов, деталей, сборочных единиц, изделий) по пролетам цеха.
Такая ведомость должна содержать следующие сведения по каждому пролету проектируемого цеха или отделения (участка): название подъемно-транспортной операции с обозначением ее характера (перевозка, подача, съем, поворот и т. д.) и повторности в течение одной рабочей смены либо рабочих суток; наименование перемещаемых грузов (материалов, деталей, сборочных единиц и т. п.) с указанием номеров последних; массу и число каждого груза в одной упаковке; род упаковки, ее массу (вес) и габаритные размеры (если грузы предусмотрено перемещать без упаковки, то указывают габаритные размеры перемещаемых грузов без упаковки); число складочных мест, куда должны доставляться перевозимые грузы; указание номеров мест, откуда должен транспортироваться каждый груз; требуемое число упаковок каждого груза, необходимое для доставки на каждое складочное место в течение одной смены либо одних рабочих суток; подъемно-транспортные средства, которыми предусмотрено в разработанном производственном процессе выполнение погрузки, транспортировки и разгрузки каждого из указанных грузов в упаковке или без нее, и прочие сведения в зависимости от специфических особенностей проектируемого производства.
Как видно из приведенного выше перечня, указанные в подобных ведомостях сведения составляют краткую характеристику грузопотока по каждому пролету проектируемого цеха, отделения или участка, выраженную в цифрах, и предварительный выбор типов подъемно-транспортных средств. Пользуясь этими данными о грузопотоке и разработанным технологическим планом и разрезами здания проектируемого сборочно-сварочного цеха, приступают к расчетам по определению требуемого числа единиц подъемно-транспортного оборудования каждого из намеченных его типов.
Наряду с выше расчетом необходимого числа самоходных тележек, в тех случаях, когда грузоподъемность последних недостаточна для перевозки материалов, изготовляемых сборочных единиц либо изделий, определяют необходимое число козловых, портальных либо мостовых электрических кранов (если целесообразность применения последних обоснована). Требуемое число этих средств общего рельсового внутрицехового транспорта устанавливают в соответствии с интенсивностью грузопотоков в каждом пролете проектируемого цеха. При этом на основании опытных данных проектирования сборочно-сварочных цехов для обслуживания одним краном принимают длину пролета 60—80 м в цеховых складах металла и готовой продукции, 40—60 м в заготовительном отделении и 30—50 м в сборочно-сварочных отделениях цеха. Кроме того, контрольной цифрой допускаемой интенсивности работ каждого электрического крана в сборочно-сварочных отделениях проектируемого цеха служит число циклов работы крана, которое не должно превышать 20 в час.
В дополнение следует отметить, что при составлении проектов сборочно-сварочных цехов массового или крупносерийного производства с поточной организацией работ взаимную увязку во времени подъемно-транспортных и технологических операций производственного процесса осуществляют на основе построения графиков загрузки и работы общего подъемно-транспортного оборудования по каждому пролету цеха.
Таким образом, помимо четкого и наглядного представления о работе предусмотренных проектом подъемно-транспортных устройств, описанные выше графики дают возможность окончательной увязки в работе всего транспорта цеха с запроектированным ходом выполнения технологического процесса производства, установить окончательно необходимый качественный и количественный состав различных типов подъемно-транспортных средств и определить загрузку каждой единицы подъемно-транспортного оборудования.
|
|
Состав сооружений: решетки и песколовки: Решетки – это первое устройство в схеме очистных сооружений. Они представляют...
История развития хранилищ для нефти: Первые склады нефти появились в XVII веке. Они представляли собой землянные ямы-амбара глубиной 4…5 м...
История развития пистолетов-пулеметов: Предпосылкой для возникновения пистолетов-пулеметов послужила давняя тенденция тяготения винтовок...
Таксономические единицы (категории) растений: Каждая система классификации состоит из определённых соподчиненных друг другу...
© cyberpedia.su 2017-2024 - Не является автором материалов. Исключительное право сохранено за автором текста.
Если вы не хотите, чтобы данный материал был у нас на сайте, перейдите по ссылке: Нарушение авторских прав. Мы поможем в написании вашей работы!