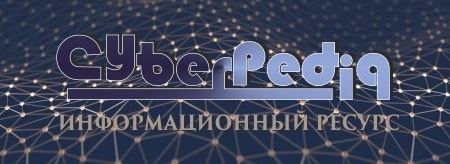
Поперечные профили набережных и береговой полосы: На городских территориях берегоукрепление проектируют с учетом технических и экономических требований, но особое значение придают эстетическим...
Автоматическое растормаживание колес: Тормозные устройства колес предназначены для уменьшения длины пробега и улучшения маневрирования ВС при...
Топ:
История развития методов оптимизации: теорема Куна-Таккера, метод Лагранжа, роль выпуклости в оптимизации...
Характеристика АТП и сварочно-жестяницкого участка: Транспорт в настоящее время является одной из важнейших отраслей народного...
Техника безопасности при работе на пароконвектомате: К обслуживанию пароконвектомата допускаются лица, прошедшие технический минимум по эксплуатации оборудования...
Интересное:
Наиболее распространенные виды рака: Раковая опухоль — это самостоятельное новообразование, которое может возникнуть и от повышенного давления...
Средства для ингаляционного наркоза: Наркоз наступает в результате вдыхания (ингаляции) средств, которое осуществляют или с помощью маски...
Искусственное повышение поверхности территории: Варианты искусственного повышения поверхности территории необходимо выбирать на основе анализа следующих характеристик защищаемой территории...
Дисциплины:
![]() |
![]() |
5.00
из
|
Заказать работу |
|
|
Несмотря на большое разнообразие химических процессов, их аппаратурного оформления, системы автоматического управления отдельными реакторами и целыми установками имеют типовые схемы стабилизации и регулирования основных параметров: расход реагента, уровень реакционной массы, давление, температура в реакторе, состав (концентрация) в реакторе.
Среди перечисленных величин центральное место занимает расход, так как только путем изменения расходов материальных потоков можно регулировать, прямо или косвенно, все прочие параметры.
![]() | ![]() | ||
Рис.6. а – полная схема регулирования расхода,
б - упрощенная схема регулирования расхода.
Схема регулирования расхода (рис. 6 а) включает в себя:
- 1 - датчик, измеряющий расход;
- 2 – преобразователь, вырабатывающий сигнал датчика в унифицированный сигнал;
- 3 - регулятор расхода, в соответствии с законом регулирования осуществляет сравнение унифицированного сигнала с заданным значением;
- 4 - исполнительный механизм, который преобразует управляющий сигнал в механическое воздействие;
- 5 - регулирующий орган, непосредственно воздействующий на регулируемый поток.
В дальнейшем эта схема будет изображаться в упрощенной форме (рис. 6 б).
Регулирование уровня жидкости или сыпучих материалов в емкостях и реакторах производится регуляторами уровня путем изменения расхода входного потока (рис. 7 а, б) или выходного потока (рис. 7 в, г).
![]() | |||||
![]() | |||||
![]() | |||||
Рис. 7. Принципиальные схемы регулирования уровня жидких материалов.
|
На рисунках (7 а, в) представлен вариант прямого регулирования, когда регулятор уровня непосредственно управляет регулирующим органом, установленным на линии входного потока. Предпочтительным является каскадное регулирование (рис. 7 б, г). Здесь подача или отвод продукта регулируется выше рассмотренным регулятором расхода, работа которого корректируется выходным сигналом регулятора уровня.
Главное преимущество каскадного регулирования заключается в улучшении качества работы системы при любых возмущениях по нагрузке. Если возмущения приложены к входу объекта, вторичный регулятор начинает оказывать регулирующее воздействие еще до того, как на выходе системы появится какое-либо отклонение; ошибка при этом может быть уменьшена в 10-100 раз по сравнению с ошибкой в одноконтурной системе. При возмущениях, приложенных к последующим элементам объекта, интегральная ошибка уменьшается в 2-5 раз за счет более высокой собственной частоты каскадной схемы регулирования.
Каскадные схемы часто применяются при регулировании температуры химических реакторов, так как даже небольшие отклонения температуры могут привести к ухудшению качества выходного продукта, а иногда к срыву реакции.
Весьма разнообразными являются схемы регулирования температурного режима процесса. В реакторах с тепловой рубашкой или встроенным теплообменником заданную температуру поддерживают путем изменения расхода теплоносителя (рис. 8 а). При наличии выносных регуляционных теплообменников температурный режим можно поддерживать путем изменения расхода циркулирующего потока (рис. 8 б). На установках с рекуперативным теплообменником преимущественно применяется схема регулирования, предусматривающая управление байпасного потока (рис. 8 в).
При использовании в качестве теплоносителя конденсирующего водяного пара или кипящей жидкости возможно применение трехступенчатой схемы (рис. 8 г). По этой схеме выходной сигнал от регулятора температуры (ТRC) управляет работой регулятора давления (РRC). Выходной сигнал с регулятора давления используется для коррекции расхода теплоносителя путем воздействия на регулятор расхода (FRC). Введение дополнительного контура по давлению способствует стабилизации теплового потока, так как давление в зоне конденсации кипения однозначно определяет температуру теплоносителя.
|
На рис. 8 д показана каскадная схема регулирования, в которой изменение температуры в рубашке реактора осуществляется регулированием давления кипящего хладоагента регулирующим органом, установленным на линии отвода кипящего хладоагента.
Уровень конденсата в рубашке стабилизируется регулирующим органом, установленным на линии подачи кипящего хладоагента.
На рис.8 е дана каскадная схема регулирования температуры в реакторе при осуществлении в нем экзотермической реакции. Регулятор температуры в реакторе TRC1 изменяет задание регулятору температуры TRC2 в рубашке реактора. На вход первичного регулятора поступает разность между заданным и измеренным значениями температуры реактора. Вторичный регулятор изменяет расход охлаждающей жидкости, поддерживая то значение температуры в водяной рубашке реактора, которая задается первичным регулятором. Основная инерция системы определяется аккумулирующей способностью жидкости в рубашке реактора, стенки реактора и жидкости в реакторе.
Рассмотрим реакцию системы на мгновенное увеличение температуры охлаждающей воды. Если предположить, что вода в рубашке хорошо перемешивается, температура в последней мгновенно начинает расти, и в течение нескольких секунд регулирующей клапан открывается, увеличивая расход воды. Колебания температуры в рубашке затухают за несколько циклов, причем период этих колебаний зависит непосредственно от собственной частоты внутреннего контура. Колебания температуры в реакторе будут значительно меньшими, чем в рубашке, благодаря демпфирующему действию стенки и самого реактора.
Если бы вторичный регулятор отсутствовал, изменения температуры воды не обнаружились бы так быстро, потому что сигнал, прежде чем попасть на вход регулятора, должен был бы пройти последовательно через четыре инерционных элемента (клапан, рубашка, стенка, реактор), включая распределенное термическое сопротивление стенки. При этом до начала работы регулятора температура в рубашке стала бы значительно выше, что привело бы к большому отклонению температуры в реакторе.
|
Как максимальное отклонение, так и период колебаний при этом были бы гораздо большими, чем при каскадном регулировании.
Начальный эффект возмущения (изменения расхода и температуры реагента, поступающего в реактор) обнаруживается почти мгновенно первичным преобразователем и первичным регулятором, но регулирующее воздействие прикладывается с инерцией, определяемой другими элементами системы. Максимальное отклонение оказывается при этом значительно большим, чем при эквивалентных возмущениях по изменению нагрузки, и может быть лишь немногим меньше, чем в одноконтурной схеме. Однако период колебаний в каскадной схеме всегда меньше, так как внутренний контур уменьшает инерционность системы, и, таким образом, в случае использование каскадного регулирования интеграл ошибки при возмущении по изменению расхода или температуры реагента также уменьшается.
Применение каскадного регулирования особенно эффективно тогда, когда внутренний контур обладает значительно большим быстродействием, чем внешний, и когда основные возмущения приложены к элементам внутреннего контура.
Давление в реакторах регулируется, как правило, путем изменения расхода газа или жидкости на выходе из аппарата.
![]() | |||
![]() |
Рис.8. Схемы автоматического регулирования температурного режима химических реакторов.
е) по температуре в рубашке
д) по давлению кипящего хладоагента в рубашке.
ОСОБЕННОСТИ РЕГУЛИРОВАНИЯ
ТРУБЧАТЫХ РЕАКТОРОВ
Трубчатые реакторы обычно используют для проведения газофазных высокоэкзотермических процессов. В трубчатых реакторах возможны режимы, при которых велика параметрическая чувствительность реактора, т.е. незначительные колебания параметров процесса – расхода смеси через реактор, температуры хладагента, начальных значений концентраций реагентов, их начальной температуры и др. приводят к существенным изменениям температурного профиля по длине реактора. При этом температура в реакторе может оказаться значительно больше допустимой, и будет соответствовать аварийному режиму работы.
|
На рис. 9 приведены температурные профили для трубчатого реактора полимеризации этилена в области qхл = 337-343 К.
Рис. 9. Температурный профиль для трубчатого реактора полимеризации этилена.
Здесь температурный профиль имеет очень высокую чувствительность (изменение температуры хладагента qхл всего на 1-2 град. приводит к росту qmax температуры в реакторе на 15-20 град), причем чувствительность температуры в реакторе к изменению qхл, существенно меняется по длине аппарата. На рис. 10 приведен график изменения коэффициента чувствительности , по длине реактора. Максимальная чувствительность достигается в области температур, соответствующих перегибу в температурном профиле. Такой характер изменения чувствительности достаточно типичен для трубчатых реакторов и должен учитываться при их автоматизации.
Рис. 10. График изменения коэффициента чувствительности Кч и температуры по длине реактора.
Сложность управления трубчатым реактором заключается в том, что необходимо управлять распределением параметра (температуры) по длине реактора, а управление является сосредоточенным (например, изменением температуры реакционной смеси на входе в реактор или температуры (расхода) теплоносителя в рубашке). В ряде случаев рубашку делают секционной по длине аппарата и температуру в каждой секции регулируют самостоятельно.
В качестве переменной, по которой ведется стабилизация температуры в реакторе, часто берут ее максимальное значение.
При этом в систему регулирования включают специальный блок выбора максимума (обеспечивающий автоматическое подключение к стабилизирующему регулятору датчика максимальной температуры в реакторе, либо подключают к регулятору температурный датчик, установленный по длине реактора в зоне, где обычно достигается максимальная температура.
Более предпочтительна схема (см. рис. 12), в которой значение максимальной температуры по длине реактора используют в системе аварийной защиты, срабатывающей при превышении максимально допустимого значения qmax, а входной величиной регулятора температуры служит значение температуры в точке с максимальной чувствительностью.
При этом необходимо осуществлять автоматический выбор датчиков соответствующих максимальным температуре и чувствительности, что может оказаться достаточно сложным.
Применение средств вычислительной техники позволяет использовать при управлении трубчатыми реакторами интегральные оценки распределенного температурного профиля реактора [7].
|
Применение средств вычислительной техники позволяет использовать при управлении трубчатыми реакторами интегральные оценки распределенного температурного профиля реактора. Так, при аварийной защите трубчатого реактора полимеризации этилена в АСУ «Полимир» используют площадь S под температурным профилем по длине реактора (рис.11). Расчет этой площади осуществляется по показаниям датчиков температуры, установленных по длине реактора. Число таких датчиков составляет около 80.
Рис. 11 Оценка площади под температурным профилем по длине трубчатого реактора для аварийной защиты.
Исследование математической модели этого реактора позволило определить критическое значение площади Sкр., при повышении которого в реакторе возникают неустойчивые режимы. Алгоритм защиты реактора предусматривает сравнение текущего значения площади S с Sкр. При S ³ ³ Sкр. происходит срабатывание системы защиты реактора от аварий.
Важнейшими задачами являются стабилизация качества получаемых продуктов и управление производительностью химических реакторов. Решение этих задач в значительной мере сдерживается отсутствием соответствующих датчиков. Однако применение средств вычислительной техники для контроля и управления химическими реакторами позволяет использовать различные косвенные показатели, по которым с помощью моделей рассчитывают производительность реактора и показатели качества продукта, используемые при управлении процессом. Так, в АСУ «Полимир» математическую модель реактора используют для контроля текущей производительности реактора. В этой же системе качеством получаемого в трубчатом реакторе полимера управляют с помощью специальной адаптивной системы регулирования (рис. 12), в которой качество полимера определяется по математической модели реактора на основе измерения входных параметров в реакторе (расход смеси, температура по длине реактора и др.). Модель для расчета основного показателя качества получаемого полимера – индекса расплава – представляет собой регрессионное уравнение, коэффициенты которого периодически уточняют по данным лабораторных анализов, вводимых в управляющий вычислительный комплекс.
Оперативный расчет производительности осуществляется для каждой зоны реактора с помощью упрощенной модели процесса, представляющей собой уравнения материального баланса для мономера и инициатора:
(12)
(13)
где у1 – концентрация мономера;
у2 – концентрация инициатора;
Р – давление;
q - температура реакционной смеси;
l – текущая длина реактора,
0£ l £ L; L – длина зон реактора;
а1 – а4, k1, k2 – постоянные коэффициенты.
Первоначально проводится опрос основных точек измерения по каждой зоне реактора (давление, дискретный температурный профиль по длине каждой зоны, расход инициатора, положение клапана, регулирующего соотношение расходов этилена в каждую зону). Данные этих измерений используют для расчета и проверки достоверности информации. На основании измерений рассчитывают концентрации инициатора на входе в каждую зону реактора и задают начальные условия для интегрирования системы уравнений (12), (13). Затем температурный профиль, измеренный в ряде точек по длине реактора, аппроксимируют полиномом. Коэффициенты полинома определяют методом наименьших квадратов так, чтобы минимизировать сумму квадратичных отклонений значений полинома от температуры в точках измерения. Далее уравнения (12), (13) интегрируют методом Эйлера по длине каждой из зон и определяют суммарную производительность реактора по обеим зонам. Значения температуры в правых частях уравнений на каждом шаге интегрирования рассчитывают по полученному при аппроксимации полиному.
![]() |
Рис. 12 Адаптивная система регулирования качества полимера в трубчатом реакторе полимеризации этилена.
Программа расчета производительности реактора работает в составе АСУ в реальном масштабе времени. Продолжительность цикла расчета – 5 мин. Результаты расчета выводятся на дисплей оператору-технологу и используются для настройки процесса на максимальную производительность (с учетом ограничений по качеству продукта).
Рис. 13. АСР температуры в трубчатом реакторе и АСЗ.
1- блок выбора max
2- регулятор температуры
3- блок выбора максимума температуры
4- блок аварийной сигнализации.
|
|
Папиллярные узоры пальцев рук - маркер спортивных способностей: дерматоглифические признаки формируются на 3-5 месяце беременности, не изменяются в течение жизни...
Общие условия выбора системы дренажа: Система дренажа выбирается в зависимости от характера защищаемого...
Таксономические единицы (категории) растений: Каждая система классификации состоит из определённых соподчиненных друг другу...
Механическое удерживание земляных масс: Механическое удерживание земляных масс на склоне обеспечивают контрфорсными сооружениями различных конструкций...
© cyberpedia.su 2017-2024 - Не является автором материалов. Исключительное право сохранено за автором текста.
Если вы не хотите, чтобы данный материал был у нас на сайте, перейдите по ссылке: Нарушение авторских прав. Мы поможем в написании вашей работы!