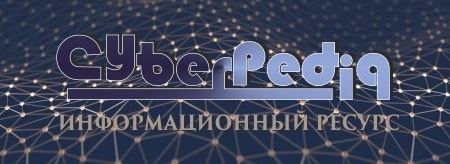
Семя – орган полового размножения и расселения растений: наружи у семян имеется плотный покров – кожура...
Состав сооружений: решетки и песколовки: Решетки – это первое устройство в схеме очистных сооружений. Они представляют...
Топ:
Устройство и оснащение процедурного кабинета: Решающая роль в обеспечении правильного лечения пациентов отводится процедурной медсестре...
Когда производится ограждение поезда, остановившегося на перегоне: Во всех случаях немедленно должно быть ограждено место препятствия для движения поездов на смежном пути двухпутного...
Генеалогическое древо Султанов Османской империи: Османские правители, вначале, будучи еще бейлербеями Анатолии, женились на дочерях византийских императоров...
Интересное:
Отражение на счетах бухгалтерского учета процесса приобретения: Процесс заготовления представляет систему экономических событий, включающих приобретение организацией у поставщиков сырья...
Берегоукрепление оползневых склонов: На прибрежных склонах основной причиной развития оползневых процессов является подмыв водами рек естественных склонов...
Национальное богатство страны и его составляющие: для оценки элементов национального богатства используются...
Дисциплины:
![]() |
![]() |
5.00
из
|
Заказать работу |
Содержание книги
Поиск на нашем сайте
|
|
МЕТОДИЧЕСКИЕ РЕКОМЕНДАЦИИ
И ЗАДАНИЯ ДЛЯ КОНТРОЛЬНЫХ РАБОТ
Форма обучения - заочная
МДК.04.01. Технология обработки на металлорежущих станках
Специальность 15.02.08 Технология машиностроения
Методические указания и задания для контрольных работ для студентов заочного отделения по МДК.04.01. Технология обработки на МРС разработаны на основе Федерального Государственного образовательного стандарта для специальности СПО 15.02.08 Технология машиностроения.
Организация- разработчик: ГБПОУ СПТ им. Б.Г. Музрукова.
СОГЛАСОВАНО Протокол №___ от «__» ________201_г. Председатель МК __________Е.С.Богданович | УТВЕРЖДАЮ Зам. директора по УР _________ О.Н.Тарасова «___»_____________201_г. |
Автор: Точков Д.Ф., мастер п/о ГБПОУ СПТ им. Б.Г. Музрукова
Рецензенты: Киселёва Н.Н., методист ГБПОУ СПТ им. Б.Г. Музрукова
Общие методические указания
Программой МДК.04.01. Технология обработки на МРС предусматривается изучение широко применяемых в технике МРС, режущий инструмент, приспособления, мерительный инструмент технологию обработки на МРС, материалы и их свойства. При изучении методов обработки материалов следует раскрывать значения передовых технологических процессов, позволяющих ускорить изготовление деталей, значительно уменьшить расход материала, повышать качество деталей и снижать себестоимость. В результате изучения данной дисциплины студент должен приобрести навыки технико-экономического обоснования выбора и применения конструкционных, инструментальных материалов. При изучении материала темы следует ознакомиться с программой и методическими указаниями к данной теме, изучить текст по учебнику и кратко законспектировать. В случае затруднений следует обратиться к преподавателю данного курса.
|
Раздел 1. Обработка деталей на металлорежущих станках различного вида и типа (сверлильных, токарных,
фрезерных, копировальных, шпоночных, шлифовальных).
Тема 1.1 Основные сведения при обработке на МРС.
а) Классификация металлорежущих станков. Роль металлорежущих станков в промышленности.
Перспективы развития металлорежущих станков. Требования к профессии станочника. Классификация по
степени универсальности, точности, автоматизации, по расположению шпинделя в зависимости от массы.
Обозначение и расшифровка МРС.
б) Охрана труда. Условия и охрана труда. Производственные санитарно- гигиенические нормы. Правила
техники безопасности при работе на МРС. Организация рабочего места станочника. Оснащение рабочего
места станочника. Технологическая и организационная оснастка.
в) Точность станков и качество обработки. Основные погрешности МРС. Влияние режущего инструмента на качество обработки.
Производительность и надёжность станков. Производительность, надёжность, безотказность, долговечность станков.
г) Пожаро - и электробезопасность. Обеспечение пожаро - и электробезопасности. Организационные и технические мероприятия по обеспечению электробезопасности.
Экология при работе на станках. Экология как наука. Виды загрязнений окружающей среды в машиностроении и металлообработке.
Методические указания.
При изучении этой темы необходимо уяснить, как ведётся правильно обработка материала на МРС.
Изучить устройство металлорежущих станков различных групп, операционные технологии, принятые
для этого оборудования на производстве. Внимание: знать сведения о методах наладки и рациональной эксплуатации наиболее распространённых типов станков в группах. Знать сведения о типовых неисправностях, возникающих при работе на станочном оборудовании.
Конструкции металлорежущих станков изменяются во времени. Появляются новые механизмы,
|
расширяются технологические возможности, повышаются производительность и качество обработки. При выборе типа и модели металлорежущего станка в первую очередь обращается внимание на возможность закрепления в нём заданной детали (расстояние между центрами и наибольший диаметр обрабатываемой детали – у токарных станков, размеры станка и наибольший ход долбяка – у строгальных и долбёжных, наибольший условный диаметр сверления и вертикальное перемещение головки – у сверлильных станков и т. д.). Затем анализируются мощности главных электродвигателей и их предполагаемое соответствие для обработки заданной детали. И, наконец, исследуются диапазоны и число ступеней подач и частот вращения шпинделя. Предпочтение следует отдавать станкам с более широкой разрешающей способностью указанных выше параметров.
В дальнейшем изучая тему пользоваться литературой приведённой в методическом указании.
Вопросы для самоконтроля
1.Что называется металлорежущим станком?
2.Перечислите основные погрешности станка.
3.Что такое надёжность станка?
4.Чем оснащается рабочее место станочника?
5.Что такое гигиена труда рабочего-станочника?
6.Что такое пожарная безопасность?
7.Какое влияние на человека оказывает промышленный шум?
Точение
Точение (токарная обработка) – наиболее распространённый метод обработки поверхностей деталей (типа тел вращения) на токарных станках. Типы токарных станков приведены в прил. 2 табл. 3. Основные виды токарных работ: обработка наружных цилиндрических и конических поверхностей, обработка пазов и уступов, вытачивание пазов и канавок, отрезка заготовок, сверление, зенкерование, развёртывание, нарезание резьб, обработка фасонных поверхностей, накатывание рифлений и др. На рис. 2.1 приведена технологическая схема точения.
Рис. 2.1. Технологическая схема точения
Вращательное движение заготовки называется главным движением резания, а поступательное движение режущего инструмента – движением подачи.
Подачей S, мм/об, (рис. 2.1) называется путь, пройденный режущей кромкой инструмента относительно вращающейся заготовки за один ее оборот. Подача может быть продольной, если инструмент перемещается параллельно оси вращения заготовки, и поперечной, если инструмент перемещается перпендикулярно этой оси.
|
Численные значения подач приводятся в справочной и нормативной документации.
Практически подача для токарной обработки, мм/об, принимается при черновой обработке 0,4…0,8; при чистовой – 0,1…0,3; при прорезании пазов и отрезании – 0,1…0,4.
Выбранная подача должна быть скорректирована по паспорту металлорежущего станка. Необходимо соблюдать условие, чтобы Sст S. При этом принимается ближайшая меньшая ступень.
Глубина резания t, мм, определяется толщиной снимаемого слоя за один рабочий ход резца, измеренной по перпендикуляру к обрабатываемой поверхности детали.
При черновом точении и отсутствии ограничений по мощности станка величина t принимается равной припуску на обработку h; при чистовом точении припуск снимается за два и более проходов. На каждом последующем проходе глубина резания устанавливается меньше, чем при предшествующем.
При отрезке и прорезке глубиной резания является ширина главной режущей кромки, которую можно определить из выражения: b = 0,6 D0,5 мм, где D – диаметр отрезаемой детали.
Скорость резания Vp, м/мин, зависит от конкретных условий обработки. На её величину оказывают существенное влияние следующие факторы: стойкость инструмента, физико-механические свойства обрабатываемого материала, подача и глубина резания, геометрические параметры режущего инструмента, наличие смазочно-охлаждающей жидкости (СОЖ), температура в зоне контакта инструмента и детали, допустимый износ инструмента и др.
При наружном продольном и поперечном точении, а также при растачивании расчётная скорость резания определяется по эмпирической формуле
(2.3)
а при отрезании, прорезании и фасонном точении – по формуле
(2.4)
где – коэффициент, учитывающий условия резания; Т – период стойкости инструмента, мин; S – подача, мм/об;
– корректирующий коэффициент; m, x, y – показатели степени.
Значения , m, x, y приведены в табл. 2.1.
Таблица 2.1
Значения коэффициента
и показателей степени m, x, y при точении
Корректирующий коэффициент определяется по следующей формуле:
(2.5)
где Кmv – коэффициент, учитывающий влияние материала заготовки; Кпv – коэффициент, учитывающий состояние поверхности заготовки; Киv– коэффициент, учитывающий материал режущей части резца; К – коэффициент, учитывающий главный угол в плане резца; Кr – коэффициент, учитывающий величину радиуса при вершине резца (принимается во внимание только для резцов из быстрорежущей стали).
|
Коэффициент Кmv рассчитывается по следующим формулам:
(2.6)
(2.7)
, (2.8)
где – предел прочности материала заготовки, МПа; НВ – твёрдость материала заготовки, МПа.
Показатель nv при обработке резцами из твердого сплава принимается для обработки сталей – 1,0; для обработки чугунов – 1,25. Значения коэффициентов КПV, КИV, К и Кr приведены в табл. 2.2….2.4.
Таблица 2.2
Значения поправочного коэффициента КПV
Состояние поверхности заготовки | ||||
Без корки | С коркой | |||
Прокат | Поковка | Стальные и чугунные отливки при корке | ||
нормальной | сильно загрязнённой | |||
1,0 | 0,9 | 0,8 | 0,80…0,85 | 0,50…0,60 |
Таблица 2.3
Значения поправочного коэффициента КИV
Обрабатываемый материал | Значения Киv в зависимости от марки инструментального материала | ||||||
Сталь конструкционная | Т5К12В 0,75 | Т5К10 0,65 | Р18 0,8 | Т15К6 1,05 | Р6М5 1,15 | Т30К4 1,4 | ВК8 0,4 |
Сталь закалённая | HRC 35 – 50 | HRC 51 – 62 | |||||
T15K6 1,0 | T30K4 1,25 | BK6 0,85 | BK8 0,83 | BK4 1,0 | BK6 0,92 | ВК8 0,74 | |
Серый и ковкий чугун | ВК8 0,83 | ВК6 1,0 | ВК4 1,10 | ВК3 1,15 | – | Р18 0,95 | Р6М3 0,9 |
Медные и алюминиевые сплавы | Р6М5 1,0 | ВК4 2,5 | ВК6 2,7 | 9ХС 0,6 | ХВГ 0,6 | У12А 0,5 | – |
Таблица 2.4
Значения коэффициентов К и Кr
Главный угол в плане, | Коэффициент К | Радиус при вершине резца r, мм | Коэффициент Кr |
1,4 1,2 1,0 0,9 0,8 0,7 | – – | 0,94 1,0 1,03 – 1,13 – |
Для проверки возможности реализации на выбранном станке определяется расчётная частота вращения шпинделя
, 1/мин,
(2.9)
где – диаметр заготовки до обработки.
Полученная сравнивается с имеющимися на станке значениями. Если расчётная частота не совпадает с одной из ступеней, то для дальнейших расчётов принимается та ступень
, которая является ближайшей меньшей к
, т. е. должно выдерживаться условие
.
По принятому значению определяется фактическая скорость резания Vф, м/мин
. (2.10)
В дальнейших расчётах используются только и Vф.
Сила резания Р, Н, раскладывается на составляющие силы, направленные по осям координат станка: тангенциальную Рz, радиальную Py и осевую Рx. При наружном продольном и поперечном точении, растачивании, подрезании эти составляющие рассчитываются по формуле
. (2.11)
При отрезании, прорезании и фасонном точении t – длина режущей кромки резца.
Постоянная Ср и показатели степени x, y, n для каждой из составляющих силу резания приведены в табл. 2.5.
|
Таблица 2.5
Значение коэффициента Ср и показателей степени x, y, n
Поправочный коэффициент Кр представляет собой произведение ряда коэффициентов, учитывающих условия резания:
. (2.12)
Коэффициент для резцов из твердых сплавов при обработке сталей определяется из выражения
(2.13)
при обработке серых чугунов , ковких –
.
Численные значения коэффициентов приведены в табл. 2.6.
Таблица 2.6
Значения коэффициентов для определения Кр
Рz является главной составляющей силы резания, по которой рассчитывается мощность, еобходимая для снятия стружки. Поэтому расчетным путем достаточно определить только Рz, а остальные составляющие можно установить по формулам:
; (2.14)
. (2.15)
Осевая сила Px (сила подачи) сравнивается по паспорту станка с наибольшей допускаемой механизмом подачи и в случае превышения последней, требует повторного расчёта режимов резания.
Мощность резания. Вначале рассчитывается эффективная мощность резания, кВт,
(2.16)
Затем определяется потребная мощность на шпинделе станка, кВт,
, (2.17)
где – кпд станка.
Для выводов об эффективности рассчитанных режимов для принятого станка устанавливается коэффициент его использования по мощности
, (2.18)
где – мощность главного электродвигателя станка (по паспорту), кВт.
Величина коэффициента не должна превышать единицы. Наиболее рациональное значение
= 0,85…0,9.
В случае отклонения от рациональной величины необходимо вновь рассчитать режимы резания, скорректировав при этом параметры, устанавливаемые автором расчётов (S, t, T, тип станка и др.)
Основное технологическое время – время в минутах, затрачиваемое непосредственно для снятия заданного припуска. Оно определяется по формуле
, (2.19)
где L – расчётная длина обработки, мм (см. рис. 2.1); i – количество проходов,
, (2.20)
где l – чертёжный размер обрабатываемой поверхности, мм; l1 – величина врезания резца, мм; l2 – величина перебега резца, мм,
,
В настоящее время на предприятиях железнодорожного транспорта наиболее часто находят применение следующие инструментальные материалы: углеродистые, легированные и быстрорежущие стали; металлокерамические сплавы; сверхтвёрдые материалы и абразивы.
Легированные инструментальные стали (9ХВГ, ХВГ, ХГ, 6ХС, 9ХС и др.) используются для изготовления протяжек, свёрл, метчиков, плашек, разверток. Они имеют красностойкость 250…300 °С и допускают скорость резания 15…25 м/мин.
Более широкое применение находят быстрорежущие стали. Самыми распространёнными являются: Р9, Р12, Р18, Р6М3, Р6М5, Р9Ф5, Р14Ф4, Р18Ф2, Р9К5, Р9К10, Р10К5Ф2, Р10К5Ф5. Твёрдость таких сталей составляет НRC 62…65, красностойкость – 600…630 °С. Обладая повышенной износостойкостью, они могут работать со скоростями до 100 м/мин.
В прил. 2 табл. 1 приведены рекомендуемые области применения для некоторых марок быстрорежущих сталей.
Металлокерамические твёрдые сплавы состоят из карбидов вольфрама, титана и тантала (WC, TiC, TaC), находящихся в металлическом кобальте (Со). Они применяются в виде пластинок, изготовляемых методом порошковой металлургии, закрепляемых на державках режущего инструмента.
Металлокерамический твёрдосплавный инструмент обладает высокими твёрдостью (HRA 80…92), износостойкостью и красностойкостью (800…1000 °С). Это позволяет вести обработку со скоростями до 800 м/мин.
Твёрдые сплавы делятся на следующие группы: однокарбидные (вольфрамовые) – ВК2, ВК3, ВК3М, ВК4, ВК6М, ВК6 и т.д.; двухкарбидные (титано-вольфрамовые) – Т30К4, Т15К6, Т5К10, Т5К12 и др.; трёхкарбидные (титано-танталовольфрамовые) – ТТ7К12, ТТ10К8, ТТ8К6 и др.
Твёрдые сплавы группы ВК используются для обработки твёрдых и хрупких металлов, пластмасс и неметаллических материалов.
Двухкарбидные сплавы рекомендуются для обработки изделий из пластичных и вязких металлов и сплавов.
Трёхкарбидные сплавы отличаются от первых двух повышенной износостойкостью, прочностью и вязкостью и применяются для обработки деталей из труднообрабатываемых сталей аустенитного класса.
В прил. 2 табл. 2 приведены некоторые марки вольфрамовых твёрдых сплавов и области их рационального использования.
Значительную роль при обработке металлов резанием играют тип и геометрия режущей части инструмента, а также период стойкости, т. е. время работы в минутах до затупления и необходимости заточки.
Период стойкости колеблется в широких пределах. Так для резцов из быстрорежущей стали он принимается равным 60 минут; для резцов с пластинами из твердого сплава – 90…120 мин; для сверл диаметром до 20 мм – 25…60 мин, а диаметром более 30 мм – 50…140 мин; для фрез цилиндрических из быстрорежущей стали – 120 мин, а со вставными ножами из твердого сплава – 180…240 мин; для торцевых фрез со вставными ножами из твердого сплава диаметром до 150 мм – 180 мин, а диаметром более 150 мм – 240…400 мин. Стойкость протяжек – 106…500 мин; шлифовальных кругов – 30…40 мин.
где – величина главного угла в плане резца.
Вопросы для самоконтроля.
1.Что такое глубина резания?
2.Углы резца и их влияние на процесс резания.
3Мощность станка и мощность резания.
4.Что такое сталь, чугун, латунь, бронза.
5.Влияние СОЖ на процесс резания, качество обработки.
Классификация станков
Основные определения
Металлообрабатывающий станок – машина для размерной обработки заготовок в основном путём снятия стружки. Кроме металлических заготовок на станках обрабатывают так же детали из других материалов. К станкам относят и технологическое оборудование, использующее для обработки электрофизические и электрохимические методы, сфокусированный электронный или лазерный луч, поверхностное пластическое деформирование и некоторые другие виды обработки.
Помимо основной рабочей операции, связанной с изменением формы и размеров заготовки, на станке необходимо осуществлять и вспомогательные операции для смены заготовок, их зажима, измерения, операции по смене режущего инструмента, контроля его состояния и состояния всего станка.
Собственно станок подразделяется на несколько важнейших частей, обычно называемых узлами.
Главный привод (1) станка сообщает движение инструменту или заготовке для осуществления процесса резания с соответствующей скоростью. У подавляющего большинства станков главный привод сообщает вращательное движение шпинделю, в котором закреплён режущий инструмент или заготовка.
Привод подачи (3) необходим для перемещения инструмента относительно заготовки (или наоборот) для формирования обрабатываемой поверхности. У подавляющего большинства станков привод подачи сообщает узлу станка прямолинейное движение. Сочетанием нескольких прямолинейных, а иногда и вращательных движений можно реализовать любую пространственную траекторию.
Привод позиционирования необходим во многих станках для перемещения того или иного узла станка из некоторой исходной позиции в другую заданную позицию, например, при последовательной обработке нескольких отверстий или нескольких параллельных плоскостей на одной и той же заготовке. Во многих современных станках с числовым программным управлением (ЧПУ) функции приводов подачи и позиционирования выполняет один общий привод.
Несущая система (2) станка состоит из последовательного набора соединённых между собой базовых деталей. Соединения могут быть неподвижными (стыки) или подвижными (направляющие). Несущая система обеспечивает правильность взаимного расположения режущего инструмента и заготовок под воздействием силовых и температурных факторов.
Манипулирующие устройства необходимы для автоматизации различных вспомогательных движений в станке, для смены заготовок, их зажима, перемещения или поворота, смены режущих инструментов, удаления стружки и т.п. Современный многооперационный станок имеет набор манипуляторов транспортёров, поворотных устройств, а в некоторых случаях обслуживается универсальным манипулятором с программным управлением (промышленным роботом).
Контрольные и измерительные устройства необходимы в станке для автоматизации и наблюдения за правильностью его работы. С помощью них контролируют состояние наиболее ответственных частей станка, работоспособность режущего инструмента, измеряют заготовки и изделие. При достаточно высоком уровне автоматизации результаты контроля измерения поступают в управляющее устройство, а оттуда в виде управляющих сигналов корректируют положение узлов станка.
Устройство управления может быть с ручным обслуживанием оператором, с механической системой управления или с ЧПУ. В настоящее время происходит широкое внедрение микропроцессорных устройств ЧПУ для управления всеми видами станочного оборудования.
Вопросы для самоконтроля
1.Как оборудуется рабочее место токаря?
2.Расскажите об основных видах токарной обработки.
3.Какой режущий инструмент применяется при обработке на токарных станках?
4.Как крепится режущий инструмент на токарно- винторезных станках?
5.Назовите основные элементы резьбы?
6.Как измеряют резьбы?
Вопросы для самоконтроля
1.Как происходит процесс изготовления стакана из прутковой заготовки?
2. Какие существуют методы крепления тонкостенных втулок?
3.Какие приспособления применяются при изготовлении деталей типа колец?
Методические указания.
На фрезерных станках обрабатываются плоскости, фасонные поверхности, канавки, нарезаются наружные и внутренние резьбы, зубчатые колёса и многолезвийные инструменты с прямыми и винтовыми зубьями (фрезы, развёртки и др.) Фрезерные станки общего назначения бывают:
1. Консольные (с консольным столом), в том числе а) вертикальные;
б) горизонтальные; в) широкоуниверсальные.
2. Бесконсольные (или иначе с крестовым столом). Они чаще вертикальные, но есть и горизонтальные.
3. Продольно-фрезерные. Они бывают одностоечные и двухстоечные.
1. Специализированные (например, карусельно-фрезерные)
Основным размером фрезерных станков являются ширина стола, которая у консольных станков бывает от 100 до 500 мм; у бесконсольных – от 320 до 1000 мм, у ПФС – от 320 до 5000 мм.
Главное движение резания у всех фрезерных станков – вращение фрезы. Характерной особенностью фрезерных станков является независимость подач от главного движения резания. Размерность подач – мм/мин.
У консольных фрезерных станков стол имеет продольную и поперечную подачи и вместе с консолью перемещается вертикально по направляющим стойки. У бесконсольных станков стол также имеет продольную и поперечную подачи, но расположен на станине, а вертикальное перемещение передано шпиндельной бабке.
У продольно-фрезерных станков столу с тяжёлыми заготовками оставлено только продольное перемещение, а остальные движения подач переданы фрезерным бабкам, т.к. заготовки на этих станках имеют вес от нескольких тонн, до нескольких сотен тонн.
Консольный вертикально-фрезерный станок мод. 6Н12ПБ (рис. 24), например, имеет две кинематические группы приводов шпинделя и подач, а также ручное перемещение шпинделя.
Муфтами Мs и Мб включается рабочая подача или быстрое перемещение движения, включённого одной из трёх муфт М. Реверсирование подач выполняется электродвигателем Дs.
Бесконсольный вертикально-фрезерный станок мод. 654 имеет тоже две кинематические группы (рис. 25).
Регулировка подач бесступенчатая () электродвигателем постоянного тока Дs, а для расширения диапазона регулирования имеется перебор. Быстрые перемещения получаются включением двигателя Дs на максимальные 3000 об/мин. Управление подачами, благодаря использованию электромагнитных муфт, дистанционное, с подвесного пульта.
Отсчёт продольных и поперечных перемещений стола ведётся по линейкам с нониусом, а вертикального перемещения бабки – по лимбу, получающего вращение при перемещении шпиндельной бабки.
Для установочного перемещения фрезы с пинолью вдоль их оси служит кинематическая цепь с ручным приводом. Для возможности фрезерования наклонных плоскостей шпинделя бабка может поворачиваться вокруг горизонтальной оси вручную на угол ± 35º. Размеры стола у этого станка 630×1600 мм. Принадлежностью горизонтально-фрезерных станков часто является делительная головка, а у ВФС – делительный круглый стол.
Делительные головки
Применяют при работе на консольно-фрезерных станках для установки обрабатываемой детали под требуемым углом относительно стола, станка, для поворота детали на определённый угол, для деления окружности на нужное число частей, а так же для непрерывного вращения обрабатываемой детали при фрезеровании винтовых канавок большого шага.
Различают делительные головки для непосредственного деления (делительные приспособления), оптические делительные головки и универсальные делительные головки. Универсальные делительные головки делятся на лимбовые и безлимбовые. Наиболее распространённые лимбовые головки. Рукоятка поворачивается на нужный угол с помощью лимба, который имеет несколько рядов отверстий, равномерно расположенных на концентричных окружностях. Фиксатор (рукоятку) можно вставлять в любое их этих отверстий.
Способ простого деления заключается в том, что вращением рукоятки поворачивают шпиндель не заданный угол. При простом делении делительный диск остаётся неподвижным.
Способ дифференциального деления применяют в тех случаях, когда простое деление осуществить невозможно, т.е. когда нельзя подобрать диск с нужным для простого деления числом отверстий. Он заключается в следующем. Требуемый поворот шпинделя делительной головки получается как совокупность двух поворотов: поворота рукоятки относительно делительного диска и поворота самого делительного диска, которому это движение сообщается принудительно от шпинделя делительной головки через сменный зубчатые колёса гитары.
Вопросы для самоконтроля.
1.Какие операции выполняют на фрезерных станках
2.Расскажите как расшифровать модель фрезерного станка.
3.Какие поверхности обрабатывают фрезерованием.
4.Чем отличаются вертикально-фрезерные станки от горизонтально- фрезерных?
5.Расскажите об инструментальной оснастке фрезерных станков.
Тема1.6 Станки сверлильной группы.
Организация рабочего места сверловщика. Требования Т.Б. при работе на сверлильных станках.
Назначение и классификация сверлильных станков. Режущий инструмент и технологическая оснастка для
обработки на сверлильных станках. Работы выполняемые на сверлильных станках. Нарезание резьб на сверлильных станках. Дефекты обработки и их предупреждения при работе на сверлильных станках.
Методические указания.
Сверлильные станки
Сверлильные станки предназначены для получения сквозных или глухих отверстий, для чистовой обработки отверстий зенкерованием и развёртыванием, для нарезания внутренних резьб метчиками, для зенкования торцовых поверхностей и отверстий.
Существуют следующие типы универсальных сверлильных станков:
1. Настольно-сверлильные; 2. Вертикально-сверлильные (одношпиндельные);
3. Радиально-сверлильные; 4. Многошпиндельные 5. Для глубокого сверления.
Основным характерным размером сверлильных станков является наибольший диаметр сверления в стали средней твёрдости.
Вертикально-сверлильный станок мод. 2А135 (рис. 18, стр.9), например, предназначен для сверления отверстий до диаметра 35 мм. Он имеет приводные кинематические цепи (см. рис.)
Радиально-сверлильные станки предназначены для обработки отверстий в средних и крупных деталях при единичном и серийном производстве. Они позволяют направлять инструмент в любую точку неподвижной детали в зоне хобота станка вокруг колонны и перемещения по его направляющим шпиндельной головки. Высокие детали устанавливаются в яме, сделанной около станка.
Радиально-сверлильный станок мод. 2В56 (рис. 19 стр. 9), например, имеет наибольший диаметр сверления 50 мм, N = 5,5 кВт; n = 55…1140 об/мин, вылет шпинделя до 2100 мм. Кроме кинематической группы привода вращения шпинделя и его подачи, на станке имеется кинематическая группа подъёма хобота.
Для перемещения хобота сверловщик вручную (P r) включает (+) двигатель подъёма (опускания) хобота Дх, но подача хобота Пх начинается только после освобождения зажима хобота Пзаж на колонне, в конце которого движением разжима включается муфта М и начинается перемещение хобота. Для остановки хобота на нужной высоте сверловщик отпускает кнопку, при этом Дх не останавливается, а реверсируется (Р) (-), после чего в начале зажима хобота он через движение Пзаж выключает муфту М, а в конце движения зажима конечным выключателем КВ выключает сам себя. Перемещение шпинделя бабки по хоботу и поворот хобота выполняются вручную. Для обсверловки тяжёлых деталей применяются переносные радиально-сверлильные станки, перемещаемые краном. Они имеют поворот оси шпинделя на любой угол в двух плоскостях. (рис. 21.)
Многошпиндельные сверлильные станки бывают: 1. с неподвижными осями шпинделя; 2. с переставными шарнирными шпинделями (рис. 20)
Первые – станки общего назначения, предназначены для последовательного выполнения ряда переходов различными инструментами, при перемещении вручную заготовки.
Вторые – настраиваются при серийном производстве для одновременного сверления нескольких отверстий. Возможность изменения взаимного расположения осей шпинделей в них обеспечивается двух шарнирным сочленением шпинделей с центральным приводным валом.
Станки для глубокого сверления (рис. 4 стр. 3) применяются в случае, если длинна отверстия во много раз превышает его диаметр. В них вращение подаётся на сверло или на деталь или на то и другое одновременно. Инструмент является пушечное или ружейное сверло. Стружка непрерывно вымывается СОЖ, подаваемой через центральное отверстие сверла под давлением в 5-20 кг/см2.
Расточные станки
Подразделяются на 1. горизонтально-расточные; 2. координатно-расточные; 3. алмазно-расточные; 4. станки для глубокой расточки.
В горизонтально-расточных станках основной размер – диаметр шпинделя. Главное движение резание – вращение шпинделя или вращение планшайбы. К подачам кроме движения стола и бабки относятся ещё осевое движение шпинделя и радиальное движение резцового суппорта на планшайбе. На этих станках могут выполнятся следующие работы: 1. сверление; 2. растачивание отверстий;
3. подрезка торцов; 4. нарезание резьбы; 5. Фрезерование плоскости.
Горизонтально-расточной станок мод. 262 Г (рис 23, стр. 11), например, имеет диаметр шпинделя равный 85 мм. Размеры стола у него 800×1000, n = 20…1000 об/мин у шпинделя и в 2 раза меньше у планшайбы.
Шпиндель за счёт двухскоростного электродвигателя и двух тройных блоков имеет 18 скоростей. Наиболее часто используется осевая подача шпинделя Пос. Подъём бабки Пв.б.кинематически связан с подъёмом опорного люнета Пв.л., чтобы сохранить соосность последнего со шпинделем. Винтовой суммирующий механизм ∑ в приводе Пв.л служит для возможности ручной выверки соосности опорного люнета относительно шпинделя. Все упомянутые движения могут выполнятся также быстро от электродвигателя Дб при выключенной муфте М.
Винторезная кинематическая цепь является формообразующей, но её кинематическая точность не очень велика, т.к. резьбы нарезается только крепёжные. Настройка её на шаг резьбы ведётся гитарой iвинт. При вращении планшайбы Впл шестерня z = 22 привода радиальной подачи будет обкатываться по центральному колесу z = 116 и за счёт этого вращать реечное колесо z = 16 радиальной подачи, т.е тут имеется скрытый суммирующий механизм ∑комп. На него третью ветвь также от планшайбы подаётся компенсирующее вращение.
В координатно-расточных станках основной размер – ширина стола. Эти станки предназначены для обработки точных отверстий при допуске на расстояние между их осями порядка 5…10 мкм. Бывают одностоечные и двухстоечные – станки (КРС).
Координатно-расточной станок мод. 2А450, например, имеет размеры стола 630×1100, он одностоечный. Электродвигатель Д1 имеет бесступенчатое регулирование.
Подача шпинделя также регулируется бесступенчато с помощью механического вариатора с раздвижными коническими шкивами и стальным кольцом. Бесступенчатое регулирование скоростей и подач позволяет на ходу вывести станок из резонанса, обеспечив тем самым малую шероховатость обрабатываемой поверхности. К станку прилагается накладной, поворотный в двух плоскостях стол.
Алмазно-расточные станки обеспечивают тонкое растачивание отверстий с некруглостью
|
|
Типы сооружений для обработки осадков: Септиками называются сооружения, в которых одновременно происходят осветление сточной жидкости...
Автоматическое растормаживание колес: Тормозные устройства колес предназначены для уменьшения длины пробега и улучшения маневрирования ВС при...
История развития хранилищ для нефти: Первые склады нефти появились в XVII веке. Они представляли собой землянные ямы-амбара глубиной 4…5 м...
Биохимия спиртового брожения: Основу технологии получения пива составляет спиртовое брожение, - при котором сахар превращается...
© cyberpedia.su 2017-2024 - Не является автором материалов. Исключительное право сохранено за автором текста.
Если вы не хотите, чтобы данный материал был у нас на сайте, перейдите по ссылке: Нарушение авторских прав. Мы поможем в написании вашей работы!