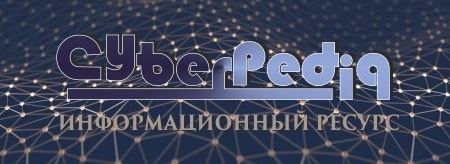
Индивидуальные и групповые автопоилки: для животных. Схемы и конструкции...
Кормораздатчик мобильный электрифицированный: схема и процесс работы устройства...
Топ:
Характеристика АТП и сварочно-жестяницкого участка: Транспорт в настоящее время является одной из важнейших отраслей народного...
Оценка эффективности инструментов коммуникационной политики: Внешние коммуникации - обмен информацией между организацией и её внешней средой...
Установка замедленного коксования: Чем выше температура и ниже давление, тем место разрыва углеродной цепи всё больше смещается к её концу и значительно возрастает...
Интересное:
Мероприятия для защиты от морозного пучения грунтов: Инженерная защита от морозного (криогенного) пучения грунтов необходима для легких малоэтажных зданий и других сооружений...
Уполаживание и террасирование склонов: Если глубина оврага более 5 м необходимо устройство берм. Варианты использования оврагов для градостроительных целей...
Инженерная защита территорий, зданий и сооружений от опасных геологических процессов: Изучение оползневых явлений, оценка устойчивости склонов и проектирование противооползневых сооружений — актуальнейшие задачи, стоящие перед отечественными...
Дисциплины:
![]() |
![]() |
5.00
из
|
Заказать работу |
|
|
ВВЕДЕНИЕ
Контроллеры машиниста служат для дистанционного управления электрической передачей тепловоза: изменения направления движения и регулирования мощности дизель -генератора установки по позициям.
По виду контроллеры делятся на контроллеры с ручным управлением и контроллеры с ручным и электропневматическим управлением. На тепловозах ТЭ3, ТЭМ1, ТЭ1, ТЭ2, ТЭМ2, ТЭ10, 2ТЭ10Л и частично 2ТЭ10В установлены однотипные контроллеры, которые отличаются друг от друга только различным числом позиций и кулачковых элементов, поэтому устройство этих контроллеров рассмотрим на примере контроллера КВ-0801 (рис.1).
На тепловозе 2ТЭ116, 2ТЭ10М, 2 ТЭ10В установлены контроллеры, имеющие вместо главной рукоятки штурвал и контакты мостикового типа. Устройство и работу этих контроллеров рассмотрим на примере контроллера КВ-1552. На тепловозах ТЭМ2, предназначенных для работы в одно лицо, устанавливаются контроллеры с ручным и электропневматическим приводами. Устройство и работу этих контроллеров рассмотрим на примере контроллера КВП-0854М.
При конструировании контроллеров должны быть соблюдены требования, обеспечивающие простоту и легкость пользования ими и наиболее простую кинематику блокировочных механизмов; наименьшие массу и габаритные размеры аппарата; надежность работы его переключающих устройств, удобство осмотра и ремонта всех его деталей.
Распределение функций управления и расположение отдельных рукояток контроллера выполняют так, чтобы обеспечить простоту и удобство пользования ими и не допускать отвлечения машиниста от наблюдения за сигналами, путем и контактной сетью. Механические блокировки в контроллере создают взаимозависимость между рукоятками, что предотвращает ошибочные действия машиниста.
|
В обозначениях контроллеров отечественные тепловозов первые две цифры 08; 15; 16 соответствуют количеству позиций, третья цифра указывает серию контроллера, а последняя цифра - его конструктивные особенности. Буква П обозначает, что контроллер имеет дистанционный электропневматический привод для управления тепловозом одним лицом.
Возможными неисправностями контроллера могут быть подгар и износ контактов, износ фиксирующих роликов и их осей, трещины и отколы кулачковых шайб и изоляторов, поломки и потеря упругости пружинами, износ деталей блокирующего устройства (храповиков, фиксатора, шестерен), валов и их подшипников.
Неисправности контактов, трещины и отколы деталей, поврежденные пружины выявляют при внешнем осмотре. Неисправности контактов могут вызывать нарушение последовательности срабатывания аппаратов, управляемых контроллером („пропадание позиции”). Износ храповиков, роликов и их осей приводит к нечеткой фиксации позиции. Если позиции контроллера плохо фиксируются, то во время работы тепловоза могут наблюдаться отключения аппаратов из-за кратковременного размыкания контактов контроллера машиниста вследствие вибрации.
Контроллер машиниста осматривают на тепловозе. При включенном рубильнике аккумуляторной батареи открывают смотровую дверцу и протирают детали контроллера безворсовыми салфетками, слегка смоченными бензином, а затем сухими. Затем проверяют состояние проводов, подходящих к контроллеру, плотность затяжки их наконечников, покачивая каждый наконечник за „трубку”, наличие бирок на проводах, состояние штурвала, пружин и контактных элементов, а также четкость фиксации позиций
Разборка
С контроллера машиниста снимают кожух. С вертикальных реек снимают контакторные элементы. На верхней крышке снимают и рукоятки. Снимают верхнюю крышку и затем снимают вертикальные стойки. Снимают валы. С валов снимают зубчатый сектор. С нижней крышки снимают главный и тормозной валы, вынимают подшипники.
|
Ремонт контроллера
Контакторный элемент контроллера снимают со стойки, промывают бензином и осматривают. Проверяют состояние и толщину напаек контактов. При толщине серебряных напаек менее 0,8 мм контакты заменяют. Изоляторы с трещинами, сколами и ослаблением в запрессовке армированной втулки заменяют.
Заменяют и гибкие провода, имеющие оплавление залуженной жилы или с обрывом более 10% жил. Ослабшие наконечники гибких проводов приклепывают к неподвижным контактам и места присоединений припаивают припоем ПОС40. Ролики, имеющие износ по диаметру или износ внутреннего отверстия более, чем 0,2 мм заменяют.
Аксиальный зазор в шарнирных соединениях не должен быть более 0,3 мм, а суммарный зазор между роликом и рычагом не более 0,5 мм. Пружины элемента проверяют на соответствие техническим характеристикам.
Серебряный подвижный контакт очищают от копоти бензином. Определяют износ контакта и состояние бронзовой пружинной ленты, на которой он закреплен. При износе контакта до толщины 0,8 мм его заменяют. Заменяют также держатель контакта с трещинами и с потерей пружинных свойств и подвижный контакт с износом серебряной напайки до 0,2 мм.
Кулачковый вал разбирают.
С него снимают детали блокировочного механизма: диски, шестерни. Осматривают состояние деталей и подшипников. Подшипники промывают в бензине. Проверяют посадку шайб и деталей блокировочного механизма навалу. При наличии трещин в обоймах или сепараторах, повреждений поверхности шариков, подшипники заменяют. Диски, шестерни, шейки валов, стальные кулачки проверяют шаблонами и зубомерами. При необходимости восстанавливают наплавкой. Кулачковые шайбы, имеющие износ по диаметру более 4 мм, а также с нарушением профиля заменяют. Валы с биением более 0,5 мм протачивают на токарном станке.
Проверяют посадку шайб и деталей блокировочного механизма на валу.
Механизм блокировки разбирают. Разработанные отверстия в рычагах, дисках восстанавливают запрессовкой бронзовых втулок. При ослаблении оси в рычагах запорного механизма ее заменяют. Профиль блокировочных рычагов и шайб проверяют шаблонами. Износ запорных приливов, звездочек рычага или впадин шайб восстанавливают наплавкой или приваркой накладных пластин.
|
Толщину новой пластины определяют при предварительном осмотре контроллера перед разборкой. Упорные накладки блокировочных звездочек при ослаблении наклепывают. Пружины блокировок проверяют на их соответствие характеристикам.
Рукоятки контроллера КВ-0801 разбирают. Изношенную накладку защелки рычага заменяют. Разработанные отверстия в корпусе заваривают с последующей рассверловкой до чертежных размеров. Изношенный упорный зуб и выступ рычага наваривают. Окончательную высоту выступа пригоняют по месту после установки рукоятки на контроллер. Пружины с отогнутыми концевыми витками, имеющие остаточную деформацию заменяют. Рукоятки промывают бензином и полируют.
Сборка
Собирают контроллер в порядке, обратном разборке. В нижнюю крышку впрессовывают подшипники и устанавливают в них главный и тормозной валы. На промежуточной раме монтируют валы рукояток с укрепленными на них зубчатыми секторами. Нижнюю и верхнюю крышку скрепляют на уголки, образуя каркас. После этого проверяют легкость вращения валов, осей, убеждаются в совпадении осевых линий зубчатых секторов и шестерен, деталей блокировочного механизма. На верхней крышке укрепляют секторы положений и рукоятки. На вертикальных рейках устанавливают контакторные элементы, при этом следят, чтобы паз изолятора плотно прилегал к квадрату рейки.
Регулировка
После смазки всех трущихся частей проверяют четкость работы контроллера и правильность включения и выключения контакторных элементов на каждой фиксированной позиции главной и тормозной рукояток контроллера. Положение контакторных элементов должно соответствовать диаграмме их замыкания (развертке кулачковых шайб). При замкнутом контакторном элементе зазор между роликом контакторного элемента и линией профиля кулачковой шайбы должен быть не менее 1 мм.
При разомкнутых контакторах точка касания ролика с рабочей поверхностью кулачковой шайбы должна находиться до начала линии профиля на расстоянии не менее 0,5 мм. Раствор контактов, равный 4-7 мм, регулируют постановкой прокладок из электрокартона между пазом изолятора и рейкой. Боковое смещение ролика контакторного элемента с кулачковой шайбы устраняют перемещением подвижного рычага контактора. Кулачковые валы в любом положении не должны иметь свободного хода по окружности кулачковых шайб более 25 мм.
|
В пределах свободного хода контакты контакторных элементов не должны перемещаться, а на фиксированных позициях должны быть или полностью включены, или полностью выключены.
После проверки работы контроллера производят подгонку уплотнения кожуха и окраску корпуса и кожуха серой эмалью ГФ-92-ХС.
Инструмент и приспособления
При ремонте контроллеров применяют мерительный, слесарный и механизированный инструмент.
К мерительному инструменту относятся: линейки, складные и ленточные метры, штангенциркули, шаблоны, микрометры, угольники, лекала.
Слесарные инструменты составляют: кувалды, молотки, зубила, крейцмессели, тиски, напильники, пассатижи, набор гаечных ключей, отвертки, циркули, ножовки и т.д.
К механизированному инструменту и приспособлениям относятся: пневматические гайковерты, сверлильные машины, пневмо отвертки, краскораспылители, гидравлические съемники для спрессовки шестерен с валов барабанов, приспособление для выпрессовки подшипников и др.
2.7 ТИ обслуживания
Контролер машиниста тепловоза КВ-0801.
Контроллер машиниста осматривают на тепловозе. При включенном рубильнике аккумуляторной батареи открывают смотровую дверцу и протирают детали контроллера без ворсовыми салфетками, слегка смоченными бензином, а затем сухими.
Затем проверяют состояние проводов, подходящих к контроллеру, плотность затяжки их наконечников, покачивая каждый наконечник за "трубку", наличие бирок на проводах, состояние штурвала 11, пружин 15 и 21 и контактных элементов 2 (Приложение А рис. 1), а также четкость фиксации позиций. При люфте, превышающем 1°, у штурвала подбирают и устанавливают между ним и валом прокладку из латуни размером 9*20 мм и толщиной 0,1-0,6 мм в зависимости от величины люфта. После установки прокладки плотно затягивают гайку штурвала.
В деталях корпуса 3 контроллера не должно быть трещин. Все ролики или шарикоподшипники должны свободно вращаться, пружины не иметь трещин и изломов. При обнаружении нечеткой фиксации позиций проверяют состояние рабочих поверхностей храповика главного барабана, износ ролика или шарикоподшипника и их оси, установленных на рычаге 20, и упругость пружины 20. Неисправные детали заменяют. Если это невозможно сделать на тепловозе, заменяют контроллер и ремонтируют его в электроаппаратном отделении изломов. При осмотре контактных элементов 2 в первую очередь проверяют контакты.
|
При копоти и небольших подгарах контакты зачищают стальной хромированной пластинкой. Допускается зачищать контакты и стеклянной шлифовальной бумагой.
Контактный элемент контроллера КВ-0801.
Рычаг контактный элемент контроллера должен перемещаться свободно и без заеданий. Изолятор с трещинами или отколами заменяют.
При необходимости добавляют в подшипники вала главного барабана смазку ЦИАТИМ-221. В заключение проверяют диаграмму замыканий контактов контактных элементов главного и реверсивного барабанов.
Требования к организации рабочего места
Эксплуатируемое оборудование должно быть в полной исправности. Ограждение или защитные устройства должны быть установлены на место и соответствующим образом закреплены.
Работать на неисправном оборудовании и при отсутствии или неисправном ограждении запрещается.
Вновь установленное или вышедшее из капитального ремонта оборудование может быть пущено в работу только после его комиссионной приемки с участием начальника цеха и инженера по охране труда.
Верстаки, столы и стеллажи должны быть прочными, устойчивыми и безопасными для работы и надежно закреплены на полу.
Ящики верстаков должны иметь стопоры.
Поверхность верстаков должна быть обита гладким материалом, столы и стеллажи не должны иметь выбоин, заусенцев, трещин и др. дефектов.
Полки стеллажей должны иметь наклон внутрь во избежание падения хранящихся предметов.
При обивке верстака нельзя допускать выступающих кромок и острых уголков. Ширина верстака должна иметь не более 0.75м. Расстояние между тисами на верстаках должно соответствовать размеру обрабатываемых деталей и быть не менее 1м между осями тисов.
Для защиты рабочих от отлетающих осколков на верстаке должны быть установлены сетки высотой не менее 1м с ячейками не более 3-х мм.
Детали и материалы, поступившие на обработку, должны размешаться на специальных и четко обозначенных местах.
Передачи (ременные, канатные, цепные, шарнирные и др.) должны иметь прочные предохранительные ограждения. Вращающиеся элементы оборудования и механизмов, находящиеся на высоте ниже 2,5м от пола, должны быть ограждены.
Для каждого работающего должно быть обеспечено удобное рабочее место, не стесняющее его действий во время исполняемой работы. Рабочее место должно быть обеспечено достаточной площадью для размещения вспомогательного оборудования, а так же необходимым инвентарем для хранения инструмента, оснастки заготовок и обрабатываемых изделий (стеллажи, столы, ящики, тумбочки и т.п.).
На рабочем месте под ногами рабочего должен быть исправный деревянный решетчатый настил, у которого расстояние между планками должно соответствовать 25-30мм.
Рабочее место должно быть достаточно освещенным и содержатся в чистоте.
Уборка рабочего места должна производиться в течение рабочего дня и после каждой смены по мере накопления на рабочих местах готовой продукции и отходов
Охрана труда
Дизельный цех должен иметь устройства для отопления и вентиляции, обеспечивающие метрологические условия в соответствии с требованиями «Санитарных норм проектирования предприятий».
Оборудование, где происходит образование пыли и газов, должно быть оборудовано вентиляцией. Осветительная арматура и лампы должны очищаться от загрязнений не реже двух раз в месяц, а стёкла световых проёмов два раза в год. Освещение на рабочих местах должно быть как общее, так и местное. Применение одного местного освещенияне допускается.
Уровень шума не должен быть выше:
-низкочастотный 100 дб;
-среднечастотный 85-90 дб;
-высокочастотный 75-85 дб.
Нормы освещённости:
- общее-местное 500 лк;
-участки осмотра и приёмки колёсных пар – 750лк.
Курение в цехах запрещено. Среднесуточная температура должна быть +18°С - +20°С.
Не допускается загромождение и захламление проходов у рабочих мест. Шкафы, ящики и стеллажи для инструмента и деталей устанавливаются так, чтобы хранимые в них предметы находились в устойчивом положении и не могли упасть. Полы на рабочих местах и проходах должны быть ровными, гладкими и не скользящими, содержаться в чистоте. Производственные отходы, стружки должны своевременно убираться.
Техника безопасности:
Ответственным за выполнение правил техники безопасности в цехе является старший мастер. Сменные мастера и бригадиры несут ответственность за выполнение правил по технике безопасности и промсанитарии по кругу своих обязанностей. Старший мастер цеха проводит инструктаж по соблюдению рабочими инструкции по Технике безопасности и безопасными правилами работы в соответствии с положением «Об организации обучения и проверки знаний по охране труда на железнодорожном транспорте № ЦСР-325 и инструктивными указаниями СТП ССБТ 008-98».
Каждый работник обязан:
- строго соблюдать требования по охране труда, технике безопасности, производственной санитарии, противопожарной охране, предусмотренные соответствующими правилами и инструкциями;
- пользоваться спецодеждой и предохранительными устройствами и приспособлениями;
- содержать в частоте и порядке свое рабочее место, соблюдать чистоту и порядок на участке;
- передавать оборудование, инструмент и приспособления сменщику в исправном состоянии.
В случае повреждения механизмов, приспособлений, оборудования или получения травмы, нарушения техники безопасности, работник должен немедленносообщить руководителю участка.
Выполнение положений по технике безопасности, производственной санитарии обеспечивает безопасность производства и предупреждает возникновение производственного травматизма и профессиональных заболеваний.
Все работники участка обязаны знать и выполнять правила и инструкции по охране труда и техники безопасности, должностные инструкции и положения, руководствоваться ими в своей практической работе и обеспечивать строгое выполнение их в процесс производства. Виновные в нарушении правил техники безопасности привлекаются к ответственности согласно действующему законодательству и стандартов предприятия.
Мастер (сменный, старший) является полноправным руководителем и непосредственным организатором производства и труда на новом участке. Имеет право и обязан не допускать работу на неисправном оборудовании с применением неисправных инструментов, приспособлений и др. На лиц, нарушивших трудовую и производственную дисциплину, мастер вправе налагать дисциплинарные взыскания в соответствии с правилами внутреннего трудового распорядка, а рабочих, систематически нарушающих дисциплину освобождать от работы.
В обязанности мастера входит:
- своевременно обучать и инструктировать рабочих знанию технологических процессов, безопасных методов труда, следить за соблюдением ими правил и инструкций;
- следить за исправным состоянием и правильной эксплуатацией оборудования, инструмента, оснастки, а так же производственного инвентаря;
- обеспечить правильную и безопасную организацию рабочих мест, чистоту и порядок на участке;
- следить за наличием и исправным состоянием ограждений и предохранительных устройств, средств сигнализации;
- следить за надлежащей работой вентиляционных устройств и нормальным освещением рабочих мест;
- следить за наличием и сохранностью инструкций, планов и предохранительных знаков на рабочих местах.
Все виды инструкций и стажировка по технике безопасности должны быть записаны в Журнале регистрации инструктажей по технике безопасности формы ТНУ-19.
Требования к инструменту:
Слесарные молотки должны иметь слегка выпуклую поверхность бойка и быть надёжно укреплены на ручке путём расклинивания. Рукоятки изготавливают из дерева твёрдых пород. Длина ручек слесарных молотков должна быть в пределах 300-400мм.
Ударные инструменты – зубила, бородки не должны иметь трещин, заусениц, наклёпа на ударной части. Наименьшая длина зубила – 150мм. При работе обязательно пользоваться защитными очками, во время работы зубило располагать от себя.
Гаечные ключи должны соответствовать размерам гаек и головок болтов, губки ключей строго параллельны. Удлинение ключей трубами запрещается.
Перед подключением пневматического инструмента необходимо продуть шланг. Работать на шлифовальной машине без защитных очков и ограждений запрещается. Перед работой проверить её исправность. Запрещается использовать шлифовальную машину без прокладок между шлифовальным кругом и планшайбой.
Весь ручной инструмент должен быть исправным и очищенным от масла. Прежде чем начать работу необходимо проверить надёжность их насадки и ручки. К работе с электрическим и пневматическим инструментом допускаются только специально обученные работники.
Требования к оборудованию:
Расположение оборудования должно соответствовать нормам технологического проектирования. Границы проходов, места укладки грузо захватов и тары должны быть отмечены белой краской.
Вновь устанавливаемое и вышедшее после ремонта оборудование должно быть тщательно вымерено и надёжно закреплено. Оборудование должно быть принято с разрешения главного механика и инженера по технике безопасности.
Электробезопасность:
Для предупреждения возможности поражения электрическим током корпуса электродвигателей, индукционных нагревателей, дефектоскопов, моечных машин, металлические кожуха должны надёжно заземляться. Нельзя включать индукционный нагреватель, если его магнитопровод не замкнут с нагреваемым кольцом. Печи для нагрева лабиринтных и внутренних колец должны быть заземлены в двух местах, а так же иметь устройства, автоматически отключающие печь от сети при открывании дверцы. Наряду с защитным заземлением при работе с дефектоскопами и индукционными нагревателями применяются диэлектрические перчатки, коврики и дорожки.
Пусковые кнопки электрических устройств должны быть защищены и утоплены в корпус на 3-5мм. Кнопки остановки должны быть красного цвета, иметь надпись «стоп» и выступать над панелью на 3мм.
Погрузочно-разгрузочные работы:
К управлению подъёмно-транспортным оборудованием допускаются лица не моложе 18 лет, прошедшие медицинское освидетельствование, обученные безопасным методам работы и получившие удостоверение на право управления данным оборудованием.
Подъёмно-транспортным оборудованием разрешается поднимать груз, масса которого вместе с грузозахватными приспособлениями не превышает допустимую грузоподъёмность данного оборудования. Запрещается поднимать груз неизвестной массы, а так же защемлённый, примёрзший или зацепившийся.
Подъёмно-транспортное оборудование при производстве работ должно быть в состоянии, исключающим их самопроизвольное перемещение.
На площадках для укладки грузов должны быть обозначены границы штабелей, проходов и проездов между ними. Не допускается размещать грузы в проходах и проездах. При перемещении груза нахождение людей на грузе и зоне его возможного падения не допускается. Не допускается перемещение груза над помещениями и транспортными средствами, где находятся люди. После окончания и в перерывах между работами груз и грузозахватные приспособления не должны оставаться в поднятом положении.
Дефектоскопия:
На должность дефектоскописта назначаются лица не моложе 18 лет, имеющие специальную подготовку и сдавшие испытания в знании устройства дефектоскопа, правил по электробезопасности.
Дефектоскопная установка должна иметь защитное заземление рамы установки и корпуса пульта управления. Снятие с шейки соленоидов и контактных головок разрешается только при полном разряде конденсаторной батареи.
При каждом, даже кратковременном перерыве в работе, необходимо отключать установку от сети. У пульта управления должен быть положен резиновый диэлектрический коврик и перчатки.
Категорически запрещается: касаться токоведущих частей и движущихся частей электропневматических приводов и вращающихся частей.
Окрасочные работы:
Окрасочные работы должны производиться на специальной площадке, оборудованной вентиляцией.
Составы лакокрасочных материалов следует приготавливать в специальном помещении, оборудованном принудительной вентиляцией и средствами пожаротушения. Окрасочный участок должен быть обозначен сигнальными знаками.
К рабочему месту лакокрасочные материалы должны доставляться в плотно закрывающейся таре. По окончании работы остатки лакокрасочных материалов должны быть возвращены в краско приготовительное отделение и храниться в закрытой таре. К работе с лакокрасочными материалами допускаются лица, прошедшие обучение и инструктаж. Курить, пользоваться открытым огнём при приготовлении краски и выполнении окрасочных работ запрещается.
Экология:
Загрязнение окружающей среды при ремонте блока цилиндров дизеля происходит в процессе окраски и мойки блока цилиндров. При мойки и окраски все вещества доставляются в плотно закрывающейся таре. Промывка технологических отверстий ведется в специальных ваннах для слива мазута, чтобы не загрязнять окружающую среду.
Вывод: в этом разделе курсового проекта были проработаны условия по соблюдению охрана труда и техника безопасности согласно ПТЭ ЖДТ РФ при производстве ремонтных и других видах работ.
ЗАКЛЮЧЕНИЕ
В процессе выполнения работы я подробно изучил назначение и конструкцию контроллеров машиниста КВ-0801, КВ-1552, КВП-0854М, их работу, регулировку, правила эксплуатации, технического обслуживания и ремонта. Я научился безопасным приемам труда, соблюдал меры безопасности при нахождении на железнодорожных путях, правила личной гигиены.
Считаю, что работа над курсовой очень помогла мне освоить что такое контроллер машиниста в целом и данные знания смогу применить в будущем.
СПИСОК ЛИТЕРАТУРЫ
1. Жуков В.И. Охрана труда на железнодорожном транспорте. Учебное пособие для средних профессионально-технических училищ. - М.: Транспорт, 1988.
2. Тепловоз ТЭМ2/Руководство по эксплуатации и обслуживанию/П. М. Аронов, 2-е изд., исправл. и доп. М.: Транспорт, 1983
3. Крутяков В.С. Охрана труда и основы экологии на железнодорожном транспорте. - М.: Транспорт, 1993.
4. Правила технического обслуживания и текущего ремонта тепловозов ТЭ1, ТЭ2, ТЭМ1, ТЭМ2, ТЭМ2А. М.: Транспорт, 1980.
5. Технология ремонта тепловозов, Учебник для техникумов ж.-д. трансп 1 В. П. Иванов, И. Н. Вождаев, Ю. И. Дьяконов, А. Я. Углинский; Под ред. В. П. Иванова. М.: Транспорт, 1987.
6. Тепловоз [Свободная энциклопедия Википедия]. URL: http://ru.wikipedia.org/wiki/Тепловоз (дата обращения: 20.02.2014)
7. Тепловоз 2ТЭ116. [Электронный ресурс] URL: http://teplovoz.ucoz.ru/publ/ustrojstvo_i_remont_dizelja/blok_cilindrov_remont/4-1-0-69 (дата обращения: 20.02.2014)
8. Маневровые тепловозы/Г. И. Белобаев, В. Н. Бурьяница, М. К. Гавриленко и др. Под ред. Назарова Л. С. М.: Транспорт, 1977
9. Дробинский В. А., Егуиов П. М. Как устроен и работает тепловоз. М.: Транспорт, 1980.
10. Тепловозы ТЭМ1, ТЭМ2 1 П. М. Аронов, В. А. Бажинов, Д. А. Батурин н др.; Под ред. Е. Ф. Сдобникова. 2-е изд. исправл. и допол. М.: Транспорт, 1978.
ПРИЛОЖЕНИЕ №1
Рис. 1. Контроллер машиниста КВ-0801:
1 — дно корпуса;
2 — главный барабан;
3 — корпус;
4, 29 — угольники;
5, 20, 31 — рычаги;
6 — главный вал;
7 — кронштейн;
8 — реверсивный вал;
9 — верхняя крышка;
10 — реверсивная рукоятка;
11 — главная рукоятка;
12 — изоляционные стойки;
13 — тяга;
14 — реверсивный барабан;
15, 21, 22, 32 — пружины;
16, 19— храповики;
17— фиксатор;
18, 27— ролики;
23— подвижной контакт;
24, 25 — серебряные пластины;
26 — неподвижный контакт;
28 — пластмассовая шайба;
30 — гибкое соединение
ПРИЛОЖЕНИЕ №2
Рис. 2. Контроллер машиниста КВ-1552:
1—реверсивная рукоятка; 2—штурвал; 3—корпус; 4—реверсивный барабан; 5—кулачковые шайбы; 6—главный вал; 7—контактные элементы; 8, 11- пружины; 9- фиксатор; 10-рычаг; 12-храповик; 13- рычаг контактного элемента; 14- контактные болты; 15- пружина; 16- подвижные контакты; 17; пластмассовый изолятор.
ПРИЛОЖЕНИЕ №3
Рис.3. Контроллер машиниста КВП-0854М.
ПРИЛОЖЕНИЕ №4
ВВЕДЕНИЕ
Контроллеры машиниста служат для дистанционного управления электрической передачей тепловоза: изменения направления движения и регулирования мощности дизель -генератора установки по позициям.
По виду контроллеры делятся на контроллеры с ручным управлением и контроллеры с ручным и электропневматическим управлением. На тепловозах ТЭ3, ТЭМ1, ТЭ1, ТЭ2, ТЭМ2, ТЭ10, 2ТЭ10Л и частично 2ТЭ10В установлены однотипные контроллеры, которые отличаются друг от друга только различным числом позиций и кулачковых элементов, поэтому устройство этих контроллеров рассмотрим на примере контроллера КВ-0801 (рис.1).
На тепловозе 2ТЭ116, 2ТЭ10М, 2 ТЭ10В установлены контроллеры, имеющие вместо главной рукоятки штурвал и контакты мостикового типа. Устройство и работу этих контроллеров рассмотрим на примере контроллера КВ-1552. На тепловозах ТЭМ2, предназначенных для работы в одно лицо, устанавливаются контроллеры с ручным и электропневматическим приводами. Устройство и работу этих контроллеров рассмотрим на примере контроллера КВП-0854М.
При конструировании контроллеров должны быть соблюдены требования, обеспечивающие простоту и легкость пользования ими и наиболее простую кинематику блокировочных механизмов; наименьшие массу и габаритные размеры аппарата; надежность работы его переключающих устройств, удобство осмотра и ремонта всех его деталей.
Распределение функций управления и расположение отдельных рукояток контроллера выполняют так, чтобы обеспечить простоту и удобство пользования ими и не допускать отвлечения машиниста от наблюдения за сигналами, путем и контактной сетью. Механические блокировки в контроллере создают взаимозависимость между рукоятками, что предотвращает ошибочные действия машиниста.
В обозначениях контроллеров отечественные тепловозов первые две цифры 08; 15; 16 соответствуют количеству позиций, третья цифра указывает серию контроллера, а последняя цифра - его конструктивные особенности. Буква П обозначает, что контроллер имеет дистанционный электропневматический привод для управления тепловозом одним лицом.
Возможными неисправностями контроллера могут быть подгар и износ контактов, износ фиксирующих роликов и их осей, трещины и отколы кулачковых шайб и изоляторов, поломки и потеря упругости пружинами, износ деталей блокирующего устройства (храповиков, фиксатора, шестерен), валов и их подшипников.
Неисправности контактов, трещины и отколы деталей, поврежденные пружины выявляют при внешнем осмотре. Неисправности контактов могут вызывать нарушение последовательности срабатывания аппаратов, управляемых контроллером („пропадание позиции”). Износ храповиков, роликов и их осей приводит к нечеткой фиксации позиции. Если позиции контроллера плохо фиксируются, то во время работы тепловоза могут наблюдаться отключения аппаратов из-за кратковременного размыкания контактов контроллера машиниста вследствие вибрации.
Контроллер машиниста осматривают на тепловозе. При включенном рубильнике аккумуляторной батареи открывают смотровую дверцу и протирают детали контроллера безворсовыми салфетками, слегка смоченными бензином, а затем сухими. Затем проверяют состояние проводов, подходящих к контроллеру, плотность затяжки их наконечников, покачивая каждый наконечник за „трубку”, наличие бирок на проводах, состояние штурвала, пружин и контактных элементов, а также четкость фиксации позиций
Раздел 1. Назначение и устройство контроллера машиниста
1.1 Контроллер машиниста КВ-0801.
Технические характеристики:
Напряжение, В (75), Ток длительный, А (20), Нажатие, Н (3,5-,4,5), Раствор, мм (6-8), Провал, мм (2,5-3,5), Угол поворота главного барабана, град (122), Количество шайб главного барабана (9), Количество шайб реверсивного барабана (2), Число положений главной рукоятки (9).
Контроллер КВ-0801 (рис. 1) состоит из верхней крышки 9 и дна корпуса 1 контроллера связанных между собой угольниками 4. В корпусе 3 установлен главный вал 6, один конец которого опирается на дно, а второй проходит через крышку. На верхнем конце вала находится главная рукоятка 11, имеющая девять положений: холостой ход и восемь рабочих. Она может поворачивать только шайбы главного барабана и служит для изменения частоты вращения вала дизеля.
На нижней части вала находится главный барабан 2. На верхнюю часть вала надет реверсивный барабан 14. Он вращается на главном валу и приводится в действие посредством рычага 5 и тяги 13 от реверсивного вала 8.Верхний конец реверсивного вала выведен над крышкой. На него надета головка, а в пазы реверсивного вала вставлена реверсивная рукоятка 10 с положениями «Вперед», «Назад» и нейтральное, предназначенная для изменения направления движения тепловоза.
Нижний конец реверсивного вала вращается в отверстии кронштейна 7, неподвижно закрепленного на корпусе контроллера. С левой и правой стороны от барабанов установлены изоляционные стойки 12. На левой стойке укреплены неподвижные контакты, состоящие из стальной планки и серебряной пластины 25.
Подвижные контакты правой стойки состоят из угольника 29 и рычага 31, на конце которого укреплен контакт 23 с серебряной пластиной 24. В средней части рычага на оси установлен ролик 27. Рычаг под действием пружины 32 прижимается роликом к шайбе 28 главного барабана. Отвод тока от подвижного контакта выполняется с помощью гибкого соединения 30 на контактный винт угольника 29.
Нажатие на контакт осуществляется притирающей пружиной 22. Последовательность замыкания контактов главного барабана зависит от расположения вырезов в шайбах, которые определяются схемой тепловоза. Контакты одной шайбы реверсивного барабана замыкаются только в положении «Вперед», другой — только в положении «Назад». Фиксация главного барабана на каждом положении осуществляется посредством храповика 19 и главного вала, во впадины которого заходят стальные ролики 18, укрепленные на двух рычагах 20. Рычаги 20 при помощи пружин 21 прижимают ролики 18 ко впадинам храповика 19. Фиксация реверсивного барабана выполняется храповиком 16, укрепленным на реверсивном валу, и фиксатором 17, прижимаемым пружиной 15.
¶При большом числе контакторных элементов в контроллере и большом числе позиций валов очень трудно разобраться, на какой позиции должен включаться или отключаться данный контакторный элемент. Для упрощения и наглядности порядок работы контакторных элементов различных валов контроллера изображают графически.
Такой график называют разверткой валов или барабанов и приводят обычно на принципиальных схемах цепей управления. Так, на схеме цепей управления электровоза ВЛ10 в левой части приведены развертки тормозного, реверсивно-селективного и главного валов. С правой стороны развертки указаны контакторные элементы и номера подходящих к ним проводов, а сверху показаны номера или обозначения позиций рукояток.
Включенное положение контакторного элемента на данной позиции отличают на развертке точкой (или широкой линией).
Чтобы исключить ошибочные действия рукоятками контроллера машиниста, их блокируют между собой следующим образом.
Главная и тормозная рукоятки запираются в пулевом положении реверсивно-селективной рукояткой, установленной также в нулевое положение.
Перевод реверсивно-селективной рукоятки в рабочее положение тягового режима М приводит к разблокированию главной рукоятки, и она может быть установлена на любую позицию. При этом реверсивно-селективная рукоятка блокируется и не может быть сдвинута в нулевое положение.
На ходовых позициях (16, 27 и 37-й) главной рукоятки можно переместить тормозную рукоятку на позиции ослабления возбуждения ОП1, ОП2, ОПЗ, ОП4.
При включении ступени ослабления возбуждения на 16-й и 27-й позициях главная рукоятка не может быть перемещена дальше в сторону 37-й позиции, Это можно сделать только после возвращения тормозной рукоятки на нулевую позицию. Перевод главной рукоятки в сторону нуля при нахождении тормозной рукоятки на одной из позиций ОП вызывает переход тормозной рукоятки на нулевую позицию.
Если реверсивно-селективная рукоятка установлена в положение тормозного режима П, или СП, или С, то тормозная рукоятка может быть переведена на 02-ю позицию, после чего появляется возможность передвинуть главную рукоятку на 1-ю позиции и только после этого можно будет передвинуть торм
|
|
Кормораздатчик мобильный электрифицированный: схема и процесс работы устройства...
Археология об основании Рима: Новые раскопки проясняют и такой острый дискуссионный вопрос, как дата самого возникновения Рима...
Организация стока поверхностных вод: Наибольшее количество влаги на земном шаре испаряется с поверхности морей и океанов (88‰)...
Поперечные профили набережных и береговой полосы: На городских территориях берегоукрепление проектируют с учетом технических и экономических требований, но особое значение придают эстетическим...
© cyberpedia.su 2017-2024 - Не является автором материалов. Исключительное право сохранено за автором текста.
Если вы не хотите, чтобы данный материал был у нас на сайте, перейдите по ссылке: Нарушение авторских прав. Мы поможем в написании вашей работы!