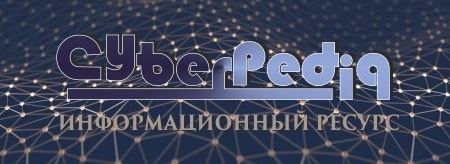
Кормораздатчик мобильный электрифицированный: схема и процесс работы устройства...
Семя – орган полового размножения и расселения растений: наружи у семян имеется плотный покров – кожура...
Топ:
Выпускная квалификационная работа: Основная часть ВКР, как правило, состоит из двух-трех глав, каждая из которых, в свою очередь...
Интересное:
Мероприятия для защиты от морозного пучения грунтов: Инженерная защита от морозного (криогенного) пучения грунтов необходима для легких малоэтажных зданий и других сооружений...
Подходы к решению темы фильма: Существует три основных типа исторического фильма, имеющих между собой много общего...
Отражение на счетах бухгалтерского учета процесса приобретения: Процесс заготовления представляет систему экономических событий, включающих приобретение организацией у поставщиков сырья...
Дисциплины:
![]() |
![]() |
5.00
из
|
Заказать работу |
|
|
СТАНДАРТ ОРГАНИЗАЦИИ
СТО 9701105632-003-2021
ИНСТРУКЦИЯ
ПО ВИЗУАЛЬНОМУ И ИЗМЕРИТЕЛЬНОМУ КОНТРОЛЮ
Москва 2021
ВВЕДЕНИЕ
Настоящий «Стандарт организации» (далее – СТО) является нормативным документом (далее - НД) по визуальному и измерительному контролю основного материала (далее - материала) и сварных соединений (наплавок), разработанным на основании и в развитие действующих НД и государственных стандартов РФ, регламентирующих общие требования и порядок его проведения.
I. ОБЛАСТЬ ПРИМЕНЕНИЯ
Настоящий СТО устанавливает порядок проведения визуального и измерительного контроля основного материала (далее - материала) и сварных соединений (наплавок) и предназначен для организаций, осуществляющих работы при изготовлении, строительстве, монтаже, ремонте, реконструкции, эксплуатации, техническом диагностировании (освидетельствовании) технических устройств и сооружений.
Визуальный и измерительный контроль специальных материалов (например, композитных и полимерных) и специальных сварных соединений (например, выполненных процессом сварки с закладными нагревателями) технических устройств и сооружений проводят в соответствии с требованиями специально разработанной документации.
II. ТЕРМИНЫ И ОПРЕДЕЛЕНИЯ
Настоящий СТО содержит термины и определения, установленные действующими НД и государственными стандартами РФ, перечень которых приведен в приложении А.
III. ОБЩИЕ ПОЛОЖЕНИЯ
3.1 Визуальный и измерительный контроль материала (полуфабрикатов, заготовок, деталей) и сварных соединений проводят на следующих стадиях:
– верификации закупленной продукции;
– изготовления деталей, сборочных единиц и изделий;
|
– подготовки деталей и сборочных единиц к сборке;
– подготовки деталей и сборочных единиц к сварке;
– сборки деталей и сборочных единиц под сварку;
– процесса сварки;
– контроля готовых сварных соединений и наплавок;
– исправления дефектных участков в материале и сварных соединениях (наплавках);
– оценки состояния материала и сварных соединений в процессе эксплуатации технических устройств и сооружений, в том числе по истечении установленного срока их эксплуатации.
3.2. Визуальный и измерительный контроль материалов на стадии верификации закупленной продукции выполняют при поступлении материала (полуфабрикатов, заготовок, деталей) в организацию с целью проверки соответствия качества продукции установленным требованиям и предупреждения запуска в производство или эксплуатацию несоответствующей продукции.
1
3.3. Визуальный и измерительный контроль материалов (заготовок, полуфабрикатов, деталей) на стадии верификации закупленной продукции, изготовления деталей и сборочных единиц и при подготовке их к сборке проводят с целью выявления дефектов, указанных в Приложении А.
3.4. Визуальный и измерительный контроль на стадии верификации закупленной продукции выполняют в соответствии с утвержденным организацией-потребителем перечнем продукции, подлежащей верификации (Приложение Б). Разделы перечня закупаемой продукции, подлежащей верификации, разрабатывают: конструкторские службы - по продукции, предназначенной для комплектации; технологические службы
- по сырью, материалам и полуфабрикатам, предназначенным для производства, ремонта, эксплуатации и обслуживания. Перечни продукции, подлежащей верификации, согласовывают с лицом, ответственным за верификацию продукции и метрологию (в необходимых случаях - с заказчиком, если это будет оговорено в договорах или контрактах на поставку), а также утверждают у уполномоченного лица организации потребителя.
|
П р и м е ч а н и е - при необходимости может осуществляться верификация закупленной продукции, не включенной в перечень.
3.5. Визуальный и измерительный контроль изготовления деталей и сборочных единиц, подготовки их к сборке и сварке выполняют с целью подтверждения соответствия качества их изготовления и подготовки требованиям рабочих чертежей, технологии изготовления (технологии сборки, гиба) и прочей производственно- технологической документации (далее - ПТД), требованиям НД, а также ТУ на изготовление.
3.6. Визуальный и измерительный контроль при сборке свариваемых элементов (заготовок, полуфабрикатов, деталей) проводят с целью выявления и проверки обеспечения допустимых размеров зазоров в корне, линейных и угловых смещений, формы и углов разделки кромок собранных элементов.
3.7. Визуальный и измерительный контроль качества сварных соединений (наплавок) в процессе сварки (наплавки) и готового сварного соединения (наплавки) выполняют с целью подтверждения их соответствия требованиям конструкторской документации (далее - КД), ПТД и (или) НД.
3.8. Визуальный и измерительный контроль выполненных сварных соединений (конструкций, узлов) проводят с целью выявления дефектов, указанных в Приложении А.
3.9. Визуальный и измерительный контроль качества исправления дефектных участков в материале, сварных соединениях и наплавках выполняют с целью подтверждения полноты удаления дефекта, проверки соответствия формы и размеров выборки дефектного участка и качества заварки выборок (в случаях, когда выборка подлежит заварке) требованиям ПТД и НД.
3.10. Визуальный и измерительный контроль технических устройств и сооружений в процессе эксплуатации проводят с целью выявления изменений их формы, поверхностных дефектов в материале и сварных соединениях (наплавках), образовавшихся в процессе эксплуатации.
2
3.11. Визуальный и измерительный контроль при изготовлении (строительстве, монтаже, ремонте и реконструкции) технических устройств и сооружений выполняют в соответствии с требованиями Технологической карты контроля и (или) Карт (схем) операционного контроля (приложения В, Г). Технологические карты и карты операционного контроля разрабатываются организацией, выполняющей контроль, либо специализированной организацией, выполняющей проектно-технологическую подготовку производства работ по контролю.
|
П р и м е ч а н и е - Допускается разработку настоящих документов производить в составе ПТД.
3.12. Визуальный и измерительный контроль при оценке состояния материала и сварных соединений в процессе эксплуатации технических устройств и сооружений выполняют в соответствии с требованиями руководящих документов (методических указаний) по оценке (экспертизе) конкретных технических устройств и сооружений. При этом визуальный и измерительный контроль может выполняться в соответствии с Картами (схемами) операционного контроля, которые разрабатываются в составе Программы технического диагностирования (освидетельствования). В Картах (схемах) указываются места проведения контроля на конкретном техническом устройстве, сооружении, схемы контроля, средства измерения контролируемого параметра, нормы оценки качества, приводятся бланки регистрации результатов контроля.
3.13. Визуальный и измерительный контроль следует проводить всех доступных для этого поверхностей полуфабрикатов, заготовок, деталей, сборочных единиц, изделий.
3.14. Визуальный и измерительный контроль проводят невооруженным глазом и (или) с применением визуально-оптических приборов до 20-кратного увеличения (луп, микроскопов, эндоскопов, зеркал и др.). При контроле материала и сварных соединений (наплавок) при изготовлении (строительстве, монтаже, ремонте и реконструкции) технических устройств и сооружений используют лупы с 2-7-кратным увеличением, а при оценке состояния технических устройств и сооружений в процессе их эксплуатации - лупы до 20-кратного увеличения.
3.15. Визуальный и измерительный контроль выполняют до проведения контроля материалов и сварных соединений (наплавок) другими методами неразрушающего контроля, а также после устранения дефектов.
3.16. Поверхности материалов и сварных соединений (наплавок) перед контролем очищаются от влаги, шлака, брызг металла, ржавчины и других загрязнений, препятствующих проведению контроля.
|
3.17. Измерения проводят после визуального контроля или одновременно с ним. Измерения деталей, подготовленных под сварку, проводятся до их сборки.
3.18. Визуальный и измерительный контроль материалов, сварных соединений (наплавок), подлежащих термической обработке, производят до и после указанной операции. Если контролируемая деталь, конструкция или узел подлежит полной термической обработке (нормализации или закалке с последующим отпуском), контроль проводят после ее выполнения.
3
3.19. Визуальный и измерительный контроль материалов и сварных соединений, подлежащих механической обработке, в том числе с удалением выпуклости сварного шва, или деформированию, проводят до и после указанных операций.
3.20. При визуальном и измерительном контроле сварных соединений контролируемая зона должна включать в себя поверхность металла шва, а также примыкающие к нему участки материала в обе стороны от шва шириной:
– не менее 5 мм - для стыковых соединений, выполненных дуговой и электронно-лучевой сваркой, контактной стыковой сваркой сопротивлением и оплавлением, сваркой нагретым инструментом при номинальной толщине сваренных деталей до 5 мм включительно;
– не менее номинальной толщины стенки детали - для стыковых соединений, выполненных дуговой и электронно-лучевой сваркой, контактной стыковой сваркой сопротивлением и оплавлением, сваркой нагретым инструментом при номинальной толщине сваренных деталей свыше 5 до 20 мм;
– не менее 20 мм - для стыковых соединений, выполненных дуговой и электронно-лучевой сваркой, контактной стыковой сваркой сопротивлением и оплавлением, сваркой нагретым инструментом при номинальной толщине сваренных деталей свыше 20 мм, а также для стыковых, угловых, тавровых и нахлесточных соединений, выполненных газовой сваркой, независимо от номинальной толщины стенки сваренных деталей и при ремонте дефектных участков в сварных соединениях;
– не менее 5 мм (независимо от номинальной толщины сваренных деталей) - для угловых, тавровых, торцевых, нахлесточных и перекрестных сварных соединений и соединений вварки труб в трубные доски, выполненных дуговой и электронно-лучевой сваркой;
– не менее 50 мм (независимо от номинальной толщины сваренных деталей) - для сварных соединений, выполненных электрошлаковой сваркой.
3.21. Дефекты, выявленные при визуальном и измерительном контроле, должны быть устранены до выполнения последующей технологической операции или до приемки объекта контроля. Устранение выявленных дефектов должно выполняться в соответствии с требованиями ПТД. Если дефекты, выявленные при визуальном и измерительном контроле, не препятствуют дальнейшему применению других видов (методов) неразрушающего контроля, эти дефекты могут быть устранены после завершения контроля другими видами (методами) контроля.
|
IV. КВАЛИФИКАЦИЯ ПЕРСОНАЛА
Специалисты, осуществляющие визуальный и измерительный контроль, должны иметь профильное образование и квалификацию дефектоскописта по визуальному и измерительному контролю, а также быть аттестованными в установленном порядке.
V. ТРЕБОВАНИЯ К СРЕДСТВАМ ВИЗУАЛЬНОГО И ИЗМЕРИТЕЛЬНОГО КОНТРОЛЯ
5.1. При визуальном и измерительном контроле применяют:
– лупы, в т.ч. измерительные;
– линейки измерительные металлические;
– угольники поверочные 90° лекальные;
– штангенциркули, штангенрейсмусы и штангенглубиномеры;
4
– щупы;
– угломеры с нониусом;
– стенкомеры и толщиномеры индикаторные;
– микрометры;
– нутромеры микрометрические и индикаторные;
– калибры;
– эндоскопы;
– шаблоны, в том числе специальные и универсальные (например, типа УШС, ШПС-1, или TapiRUS), радиусные, резьбовые и др.;
– поверочные плиты;
– плоскопараллельные концевые меры длины с набором специальных принадлежностей;
– штриховые меры длины (стальные измерительные линейки, рулетки).
Допускается применение других средств визуального и измерительного контроля при условии наличия соответствующих инструкций, методик их применения. Примерный перечень средств визуального и измерительного контроля приведен в приложении Д.
5.2. Для измерения углов разделки кромок, зазоров в корне, собранных под сварку деталей, а также размеров выполненных сварных соединений разрешается применять шаблоны различных типов.
5.3. Погрешность измерений при измерительном контроле не должна превышать величин, указанных в Таблице 1, если в рабочих чертежах не предусмотрены другие требования.
Таблица 1 - Допустимая погрешность измерения при измерительном контроле
Диапазон измеряемой величины, мм | Погрешность измерений, мм |
до 0,5 вкл. | 0,1 |
свыше 0,5 до 1,0 вкл. | 0,2 |
" 1,0 " 1,5 " | 0,3 |
" 1,5 " 2,5 " | 0,4 |
" 2,5 " 4,0 " | 0,5 |
" 4,0 " 6,0 " | 0,6 |
" 6,0 " 10,0 " | 0,8 |
" 10,0 | 1,0 |
5.4. Для определения шероховатости и волнистости поверхности следует применять профилографы-профилометры, аттестованные образцы шероховатости (сравнения), а также другие средства измерения.
5.5. Измерительные приборы и инструменты должны периодически, а также после ремонта проходить поверку (калибровку) в метрологических службах, аккредитованных в установленном порядке. Срок проведения поверки (калибровки) устанавливается НД на соответствующие приборы и инструменты.
VI. ТРЕБОВАНИЯ К ВЫПОЛНЕНИЮ ВИЗУАЛЬНОГО И ИЗМЕРИТЕЛЬНОГО КОНТРОЛЯ
Подготовка мест производства работ
5
6.1.1. Визуальный и измерительный контроль рекомендуется выполнять на стационарных участках, которые должны быть оборудованы рабочими столами, стендами, роликоопорами и другими средствами, обеспечивающими удобство выполнения работ.
6.1.2. Визуальный и измерительный контроль при монтаже, строительстве, ремонте, реконструкции, а также в процессе эксплуатации технических устройств и сооружений выполняется на месте производства работ. В этом случае должно быть обеспечено удобство подхода специалистов, выполняющих контроль, к месту производства контрольных работ, созданы условия для безопасного производства работ, в том числе в необходимых случаях должны быть установлены леса, ограждения, подмостки, люльки, передвижные вышки или другие вспомогательные устройства, обеспечивающие оптимальный доступ (удобство работы) специалиста к контролируемой поверхности, а также обеспечена возможность подключения ламп местного освещения.
6.1.3. Участки контроля, особенно стационарные, рекомендуется располагать в наиболее освещенных местах цеха, имеющих естественное освещение. Для создания оптимального контраста дефекта с фоном в зоне контроля необходимо применять дополнительный переносной источник света, то есть использовать комбинированное освещение. Освещенность контролируемых поверхностей должна быть достаточной для надежного выявления дефектов, но не менее 500 Лк.
6.1.4. Окраску поверхностей стен, потолков, рабочих столов и стендов на участках визуального и измерительного контроля рекомендуется выполнять в светлых тонах (белый, голубой, желтый, светло-зеленый, светло-серый) для увеличения контрастности контролируемых поверхностей деталей (сборочных единиц, изделий), повышения контрастной чувствительности глаза, снижения общего утомления специалиста, выполняющего контроль.
6.1.5. Для выполнения контроля должен быть обеспечен достаточный обзор для глаз специалиста. Подлежащая контролю поверхность должна рассматриваться под углом более 30° к плоскости объекта контроля и с расстояния до 600 мм (Рисунок 1).
Рисунок 1 - Условия визуального контроля
Подготовка к контролю
6.2.1. Подготовка контролируемых поверхностей проводится подразделениями организации, выполняющей работы по визуальному и измерительному контролю, а в процессе эксплуатации технических устройств и сооружений - службами организации, которой принадлежит контролируемый объект.
6
Подготовка контролируемых поверхностей в обязанности специалиста по контролю не входит.
6.2.2. Визуальный и измерительный контроль при техническом диагностировании (освидетельствовании) оборудования, работающего под давлением, следует проводить после прекращения работы указанного оборудования, сброса давления, охлаждения, дренажа, отключения от другого оборудования, если иное не предусмотрено действующей ПТД. При необходимости внутренние устройства должны быть удалены, изоляционное покрытие и обмуровка, препятствующие контролю технического состояния материала и сварных соединений, частично или полностью сняты в местах, указанных в Программе технического диагностирования (освидетельствования).
6.2.3. Перед проведением визуального и измерительного контроля поверхность объекта в зоне контроля подлежит зачистке до чистого металла от ржавчины, окалины, грязи, краски, масла, влаги, шлака, брызг расплавленного металла, продуктов коррозии и других загрязнений, препятствующих проведению контроля (на контролируемых поверхностях допускается наличие цветов побежалости, в случаях, когда это оговорено в ПТД. Зона зачистки должна определяться НД на вид работ или на изготовление изделия. При отсутствии требований в НД зона зачистки деталей и сварных швов должна составлять:
– при зачистке кромок деталей под все виды дуговой, газовой и контактной сварки не менее 20 мм с наружной стороны и не менее 10 мм с внутренней стороны от кромок разделки детали;
– при зачистке кромок деталей под электрошлаковую сварку - не менее 50 мм с каждой стороны сварного соединения;
– при зачистке кромок деталей угловых соединений труб [например, вварка штуцера (патрубка) в коллектор, трубу или барабан] зачистке подлежат: поверхность вокруг отверстия в основной трубе (коллекторе, барабане) на расстоянии 15-20 мм, поверхность отверстия под ввариваемую деталь - на всю глубину и поверхность привариваемого (патрубка) штуцера - на расстоянии не менее 20 мм от кромки разделки;
– при зачистке остающейся подкладки или плавящейся вставки - вся наружная поверхность остающейся подкладки и все поверхности плавящейся вставки.
П р и м е ч а н и е - при контроле окрашенных объектов краска с поверхности в зоне контроля не удаляется, если это специально не оговорено в НД и поверхность объекта не вызывает подозрения на наличие трещин по результатам визуального контроля.
6.2.4. Очистка контролируемой поверхности производится способом, указанным в соответствующих НД (например, промывка, механическая зачистка, протирка, обдув сжатым воздухом и др.). При этом толщина стенки контролируемого изделия не должна уменьшаться за пределы минусовых допусков и не должны возникать недопустимые, согласно НД, дефекты (риски, царапины и др.).
При необходимости подготовку поверхностей следует проводить искробезопасным инструментом.
6.2.5. Шероховатость зачищенных под контроль поверхностей деталей, сварных соединений, а также поверхность разделки кромок деталей (сборочных единиц,
7
изделий), подготовленных под сварку, должна быть не более Ra 12,5 (Rz 80).
IX. ТРЕБОВАНИЯ БЕЗОПАСНОСТИ
Перед допуском к проведению контроля все лица, участвующие в его выполнении, должны пройти соответствующий инструктаж по технике безопасности с регистрацией в специальном журнале.
Инструктаж следует проводить периодически в сроки, установленные приказом по организации.
37
Приложение А
Справочное
Термины и определения основных понятий
А.1. Термины и определения основных понятий, применяемых в тексте настоящего СТО, с указанием источников приведены в таблице А.1.
Таблица А.1 - Термины и определения основных понятий
Термин |
Определение
2
ОБЩИЕ ПОНЯТИЯ
Контроль, при котором первичная информация воспринимается органами чувств
Контроль, осуществляемый с применением средств измерений
Каждое отдельное несоответствие продукции установленным требованиям
Продукция, передача которой потребителю не допускается из-за наличия дефектов
СВАРНЫЕ СОЕДИНЕНИЯ И ШВЫ
Узел, включающий одно сварное соединение или более.
Изделие, составные части которого подлежат соединению между собой на предприятии-изготовителе сборочными операциями (свинчиванием, сочленением, клепкой, сваркой, пайкой, запрессовкой, развальцовкой, склеиванием, сшиванием, укладкой и т.п.).
Соединение двух деталей или более, выполненное сваркой.
Тип соединения, при котором детали лежат приблизительно в одной плоскости напротив друг друга под углом от 135 до 180 градусов (Рис.А.1).
Угловое соединение, при котором детали создают Т- образную форм (Рис.А.2).
Тип соединения, при котором детали практически параллельны друг другу (лежат под углом от 0 до 5 градусов) и перекрывают друг друга (Рис.А.3).
Тип соединения, при котором угол между поверхностями двух деталей в месте перекрытия кромок составляет от 30 до 135 градусов (Рис.А.4).
Тип соединения, при котором угол между поверхностями двух деталей в месте примыкания кромок составляет от 0 до 30 градусов (Рис.А.5).
Тип соединения, при котором две детали лежат друг на друге пересекаясь.
Результат сварки.
Примечание — сварной шов включает в себя металл шва и зону термического влияния
Сварной шов, отличный от углового шва и выполненный со скосом или без скоса кромок.
Сварной шов треугольного сечения между двумя деталями и более в тавровом, в угловом или в нахлесточном соединении.
Сварной шов, который выполняется заполнением
38
присадочным металлом всего круглого или продолговатого отверстия на одной детали таким образом, чтобы соединить ее через отверстие с другой деталью. | |||
Прорезной шов | Сварной шов между двумя расположенными внахлест деталями в виде углового шва, выполненный по контуру отверстия на одной детали таким образом, чтобы соединить ее с поверхностью другой детали. | ГОСТ Р 58904-2020 | 2.1.6.14 |
Непрерывный шов | Сварной шов, протяженный вдоль всей длины соединения. | ГОСТ Р 58904-2020 | 2.1.8.22 |
Прерывистый шов | Ряд участков сварного шва, выполненные с промежутками по длине соединения. | ГОСТ Р 58904-2020 | 2.1.6.15 |
Шахматный прерывистый шов | Двусторонний прерывистый шов у которого заваренные с одной стороны участки находятся против незаваренных участков с другой стороны вдоль соединения (Рис.А.6). Примечание - как правило, это угловые швы в тавровых и нахлесточных соединениях. | ГОСТ Р 58904-2020 | 2.1.6.16 |
Цепной прерывистый шов | Двусторонний прерывистый шов у которого заваренные (незаваренные) участки с обеих сторон расположены друг против друга вдоль соединения (Рис.А.7). Примечание - как правило, это угловые швы в тавровых и нахлесточных соединениях. | ГОСТ Р 58904-2020 | 2.1.6.17 |
Подварочный валик | Последний валик, наплавляемый со стороны корня сварного шва. Примечание — не рекомендуется — уплотняющий валик. | ГОСТ Р 58904-2020 | 2.1.8.21 |
Корень | Зона на стороне, противоположной той, на которой выполнялась сварка (Рис.А.8). Примечание — не рекомендуемый — корень шва. | ГОСТ Р 58904-2020 | 2.1.5.7 |
Проход, валик | Металл, переплавленный или наплавленный за однократное перемещение электрода, сварочной горелки или газовой горелки. Примечание — как правило, термин применяется в отношении свари световым лучом. | ГОСТ Р 58904-2020 | 2.1.8.4 |
Слой | Слой металла шва, состоящий из одного валика или более. | ГОСТ Р 58904-2020 | 2.1.8.13 |
Прихватка | Сварной шов для фиксации правильного положения подлежащих сварке деталей и узлов. | ГОСТ Р 58904-2020 | 2.1.8.31 |
Толщина шва | Толщина металла шва, включая любую выпуклость (Рис.А.9). | ГОСТ Р 58904-2020 | 2.1.7.2 |
Глубина проплавления | Глубина расплавляемой поверхности основного металла. | ГОСТ Р 58904-2020 | 2.1.7.3 |
Толщина проплавления | Толщина металла шва, исключая любую выпуклость. Примечание — не рекомендуемый — толщина основного металла. | ГОСТ Р 58904-2020 | 2.1.7.4 |
Номинальная толщина | Толщина, заданная в стандартах без допусков. | ГОСТ Р 58904-2020 | 2.1.7.7 |
Максимальная толщина углового шва | Значение, измеряемое от самой глубокой точки проплавления углового шва до наивысшей точки выпуклости шва (Рис.А.10). | ГОСТ Р ИСО 17659- 2009 | 3.17 |
Теоретическая толщина углового шва | Высота наибольшего равнобедренного треугольника, который можно вписать в сечение выполненного шва (Рис.А.11). | ГОСТ Р ИСО 17659- 2009 | 3.19 |
Катет углового шва | Расстояние от фактического или предполагаемого пересечения расплавляемых поверхностей до границы углового шва на расплавляемой поверхности (Рис.А.12). | ГОСТ Р 58904-2020 | 2.1.7.5 |
Ширина шва | Наименьшее расстояние между линиями сплавления на лицевой стороне сварного шва (Рис.А.13). | ГОСТ Р 58904-2020 | 2.1.7.1 |
Основной металл | Основной металлический материал. | ГОСТ Р 58904-2020 | 2.1.1.7 |
39
Подготовка кромок | Подготовка поверхности кромок детали к сварки. | ГОСТ Р 58904-2020 | 2.1.5.1 | |||||||||||||
Заостренная кромка | Отсутствие притупления кромки (Рис.А.14). | ГОСТ Р 58904-2020 | 2.1.5.4 | |||||||||||||
Поверхность притупления | Часть расплавляемой поверхности кромки, которая не скошена и не имеет канавок (Рис.А.15). | ГОСТ Р 58904-2020 | 2.1.5.10 | |||||||||||||
Угол скоса кромки | Угол между скошенной поверхностью соединения и плоскостью, перпендикулярной к поверхности соединения (Рис.А.16). | ГОСТ Р 58904-2020 | 2.1.5.12 | |||||||||||||
Угол разделки кромок | Угол между плоскостями расплавляемых поверхностей кромок (Рис.А.17.). | ГОСТ Р 58904-2020 | 2.1.5.13 | |||||||||||||
Зазор в корне | Зазор между поверхностями притупления (Рис.А.18). | ГОСТ Р 58904-2020 | 2.1.5.8 | |||||||||||||
Шов с полным проплавлением | Сварной шов с полной глубиной проплавления. | ГОСТ Р 58904-2020 | 2.1.6.1 | |||||||||||||
Остающаяся подкладка | Металлическая подкладка, которая не удаляется после сварки (Рис.А.19.). Примечание — может частично расплавляться или не расплавляться. | ГОСТ Р 58904-2020 | 2.1.11.12 | |||||||||||||
Плавящаяся вставка | Присадочный материал, помещаемый в корень соединения и полностью переплавляемый в металл шва (Рис.А.20). | ГОСТ Р 58904-2020 | 2.1.10.2 | |||||||||||||
Шов с частичным проплавлением | Сварной шов, глубина проплавления которого заведомо не является полной (Рис.А.21). | ГОСТ Р 58904-2020 | 2.1.6.2 | |||||||||||||
Зона сплавления. | Расплавленная часть основного металла в металле шва, определяемая на поперечном сечении сварного шва. | ГОСТ Р 58904-2020 | 2.1.2.6 | |||||||||||||
Зона термического влияния | Участок не расплавленного основного металла, микроструктура которого не изменилась. | ГОСТ Р 58904-2020 | 2.1.2.2 | |||||||||||||
Рисунок А.21. - Шов с частичным проплавлением Рисунок А.22. - Продольная трещина
Рисунок А.23. - Поперечная трещина
49
Рисунок А.24. - Разветвленная трещина
РисунокА.25. - Радиальная трещина
Рисунок А.26. - Кратерная трещина
Рисунок А.27. Кратерная усадочная раковина
50
Рисунок А.28. - Свищ
Рисунок А.29. - Подрез
Рисунок А.30. - Непровар
51
Рисунок А.31. - Межваликовый подрез
Рисунок А.32. - Неровная поверхность шва
Рисунок А.33. - Протек
52
Рисунок А.34. - Превышение проплава
Рисунок А.35. - Вогнутость корня шва
Рисунок А.36. - Скопление пор
Рисунок А.37. - Линейная пористость
Рисунок А.38. - Превышение выпуклости (стыковой шов)
53
Рисунок А.39. - Превышение выпуклости (угловой шов)
Рисунок А.40. - Неправильный профиль сварного шва
Рисунок А.41. - Натек
Рисунок А.42. - Линейное смещение
54
Рисунок А.43. - Угловое смещение
Рисунок А.44. - Незаполненная разделка кромок
Рисунок А.45. - Асимметрия углового шва
Рисунок А.46. - Плохое повторное возбуждение дуги
55
Рекомендуемое Требования к содержанию Требования к содержанию Требования к содержанию Карты операционного контроля Карта операционного контроля разрабатывается организацией, выполняющей изготовление (монтаж, ремонт) изделия, либо специализированной проектно- технологической организацией и служит для фиксации результатов контроля работ преимущественно при подготовке и сборке деталей под сварку. В Карте должны быть отражены следующие сведения: – наименование организации и службы, выполняющей операционный контроль; – наименование оборудования (конструкции, трубопровода), обозначение чертежа или сварочного формуляра; – наличие маркировки и (или) документации, подтверждающей приемку материала (полуфабриката) при входном контроле; – чистота и отсутствие повреждений на кромках и прилегающих к ним поверхностях деталей; – форма и размеры кромок, расточки (раздачи, калибровки) деталей; – наличие и вид специальных приемов подготовки и сборки деталей (наплавка на кромках и внутренних поверхностях, подгибка); П р и м е ч а н и е - При условии подгибки указываются температура металла при выполнении этой технологической операции и угол подгибки, а при условии наплавки - ее размеры, способ сварки и примененные сварочные материалы с указанием номера партии (наплавки) и стандарта, ТУ или паспорта;
– соответствие требованиям технической документации материала, формы и размеров остающихся подкладок или переплавляемых вставок; – соответствие требованиям технической документации размеров зазоров, линейных смещений (с наружной и внутренней сторон), угловых смещений соединяемых деталей в собранном под сварку соединении; – наличие защитного покрытия на поверхностях деталей (в случаях, оговоренных технической документацией) и ширина зоны его нанесения; – правильность сборки и крепления деталей, размеры собранного узла (последнее - в случаях, указанных в технологической документации); – дата контроля, фамилия и инициалы лица (лиц), выполнявшего операционный контроль, и его (их) подпись; – заключение о подготовке деталей к сборке под сварку. Заключение о качестве подготовки деталей и сборки соединения под сварку подписывается специалистом, выполнявшим контроль, и руководителем службы технического контроля.
58
Рекомендуемое Примерный перечень средств визуального и измерительного контроля Д.1. Примерный перечень средств, применяемые при визуальном и измерительном контроле, приведен в таблицах Д.1, Д2, Д3 и ГОСТ Р ИСО 17637. П р и м е ч а н и е - Допускается применение других средств контроля при условии соответствия диапазонов измеряемых параметров и точности измерений требованиям НД. Таблица Д1 -Типы луп, применяемые при визуальном и измерительном контроле
|