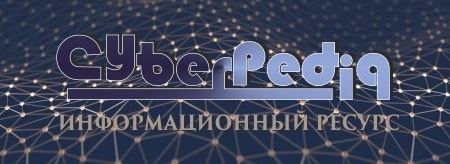
Механическое удерживание земляных масс: Механическое удерживание земляных масс на склоне обеспечивают контрфорсными сооружениями различных конструкций...
Наброски и зарисовки растений, плодов, цветов: Освоить конструктивное построение структуры дерева через зарисовки отдельных деревьев, группы деревьев...
Топ:
Оснащения врачебно-сестринской бригады.
Выпускная квалификационная работа: Основная часть ВКР, как правило, состоит из двух-трех глав, каждая из которых, в свою очередь...
Интересное:
Распространение рака на другие отдаленные от желудка органы: Характерных симптомов рака желудка не существует. Выраженные симптомы появляются, когда опухоль...
Искусственное повышение поверхности территории: Варианты искусственного повышения поверхности территории необходимо выбирать на основе анализа следующих характеристик защищаемой территории...
Аура как энергетическое поле: многослойную ауру человека можно представить себе подобным...
Дисциплины:
![]() |
![]() |
5.00
из
|
Заказать работу |
|
|
Аппараты для перемешивания жидкостей по динамике перемешивающих органов делятся на аппараты статического и динамического принципа действия.
Статические смесители (рис. 2) представляют собой устройства с не- подвижными перемешивающими элементами 1, встроенными в цилиндрическую трубу 2. Перемешивание и диспергирование жидкостей и суспензий осуществляется за счет использования энергии потока при его многократном делении на элементарные струйки и их переориентации.
Рис.2.Схема статического смесителя.
Преимущества статических смесителей перед емкостной аппаратурой с пере-мешивающими устройствами и динамическими (вибрационными) смесителями, при сопоставимых результатах по качеству получаемых смесей, связано с низкой энерго- и металлоемкостью, простотой изготовления и обслуживания, компактностью и дешевизной. Статические смесители находят широкое применение при эмульгировании жидкостей.
Аппараты с мешалками. Механическое перемешивание производят в аппаратах динамического принципа действия, носящих общее название аппаратов с мешалками, В частных случаях они носят названия, исходя из конкретного назначения аппарата (реактор, экстрактор, репульпатор, каустификатор и т. д.). Перемешивание производят с целью создания однородных растворов и суспензий и интенсификации процессов тепло- и массообмена (физического или в сочетании с химической реакцией). Для достижения указанных целей используют мешалки и аппараты различных конструкций с учетом особенностей каждого конкретного процесса.
Сосуды для аппаратов с мешалками имеют цилиндрическую форму и плоское, коническое либо эллиптическое днище. Обычно их устанавливают вертикально. В на-стоящее время химическое машиностроение изготовляет 10 типов стандар-тизированных сосудов для аппаратов с мешалками (ГОСТ 20680-75) вместимостью от 0,01 до 100 м3 и диаметром от 273 до 3200 мм. Они могут работать под вакуумом и под давлением до 6,4 МПа. Корпуса аппаратов изготавливают в 22-х исполнениях. Индекс стандартного аппарата обозначают по ГОСТ 25167-82 следующим образом. Например, индекс 1110-25-0,6У-001-У2 означает, что аппарат имеет эллиптическое днище и приварную эллиптическую крышку - первая цифра (1); гладкую приварную рубашку - вторая цифра (1); рамную мешалку (10); вместимость 25 м3; может работать под давлением 0,6 МПа; выполнен из углеродистой стали - буква У; номер модели - 001; следующая буква У указывает климатическое исполнение, а последняя цифра (2)- категорию размещения.
|
Выбор и заказ стандартных аппаратов с мешалками производят по каталогам.
Корпус аппарата может быть изготовлен цельносварным (рис.3,а) или со съемной крышкой (рис.3,б). На крышке аппарата располагают штуцеры для напол-нения, монтажа контрольно-измерительных приборов, смотровые окна и люк, служа-щий для осмотра внутренней поверхности и ремонта. По требованию монтажных условий аппараты изготовляют с боковыми лапами и нижним штуцером для опорож-нения (рис.3,б) или на стойках, приваренных к днищу и с трубой для передавливания (рис.3,а) сжатым воздухом или инертным газом. Аппараты последней конструкции используют обычно для периодического процесса.
Внутри корпуса аппарата могут быть смонтированы перегородки для предот-вращения завихрения жидкости и образования воронки. Наличие отражательных перегородок в аппарате вызывает значительное увеличение потребляемой мешалкой мощности, но мало влияет на интенсивность массообмена. Поэтому размещение их в
растворителях и кристаллизаторах считается нецелесообразным.
В зависимости от условий ведения технологического процесса аппараты изго-
|
Рис. 3. Реакторы с мешалками:
а - периодического действия с рамной мешалкой и трубой передавливания; б-непрерывного действия с пропеллерной мешалкой и диффузором. 1 - электродвигатель; 2 - редуктор; 3 - сальниковые уплотнения; 4 - люк; 5 - термометр; 6 - штуцер для подачи пара; 7 - штуцер для конденсата; 8 - опорная лапа; 9 - воздушник; 10 - труба передавливания; 11- штуцеры для подачи реагентов; 12 - сливной штуцер; 13 - диффузор; 14 - штуцер опорожнения.
товляют с теплообменной рубашкой или без нее. Если разбавление раствора не играет существенной роли, нагрев его можно производить острым паром, подаваемым через эжектор, введенный в раствор. Использовать аппараты со змеевиками в производстве кристаллических веществ нежелательно из-за быстрого их обрастания осадком и затруд-нения очистки.
При необходимости быстрого смешения двух растворов штуцеры ввода обоих рас-творов размещают в верхней части центральной трубы, охватывающей вал мешалки. Верхняя часть трубы выступает из раствора, а нижняя подходит к пропеллерной мешалке, толкающей раствор вниз. Такая конструкция аппарата позволяет быстро смешивать концентрированные растворы, не разбавляя их прореагировавшим раствором, что важно при проведении процесса с целью получения высокодисперсного осадка (например, в производствах сульфата и карбоната бария).
Быстрое снижение пересыщения (при получении крупнокристаллического осадка) достигается за счет разбавления исходных реагентов прореагировавшей смесью. Для этого растворы вводят в реактор через погружные штуцера до нижнего среза диффузора, в котором расположена пропеллерная мешалка, толкающая раствор вверх (рис.3, б). Имеющаяся в реакторе твердая фаза может служить затравкой для вновь кристаллизующегося вещества.
Хотя конструкции аппаратов с мешалками и относятся к аппаратам идеального смешения, в непрерывных процессах полное смешение не может быть достигнуто в оди- ночном аппарате. Кроме того, при ведении процессов массообмена (растворение, кристаллизация и т. д.), в нем трудно обеспечить необходимое время пребывания твердых частиц. Поэтому аппараты смешения объединяют в многоступенчатые системы, в которых рас-твор перетекает из одного аппарата в другой самотеком. Конструктивно многосту- пенчатые системы оформляют или в виде каскада последовательно соединенных аппаратов (рис.4) или в виде горизонтального аппарата, разделенного на секции перегородками (рис.5).
|
Рис.4. Каскад аппаратов с мешалками (батарея кристаллизаторов).
Рис.5. Реакторы производства экстракционной фосфорной кислоты.
а – цилиндрический секционный экстрактор; б – прямоугольный секционный экстрактор
В аппаратах (секциях) большой вместимости для создания интенсивного перемешивания во всем объеме следует устанавливать несколько мешалок (рис. 5, а).
В случаях, когда выравнивание концентрации раствора по всему объему аппа-рата несущественно, но необходимо продолжительное пребывание частиц (медленно оседающих) в аппарате, используют обычно аппараты с большим отношением высо-ты сосуда H к его диаметру D, снабженные рамными или лопастными мешалками, создающими интенсивную окружную циркуляцию (например, смеситель известного молока с фильтровой жидкостью содового производства или каустификатор первой ступени каустификации в производстве едкого натра известковым способом).
При абсорбции газов можно использовать аппараты, высота которых в несколь-ко раз превосходит диаметр, а на валу расположены несколько турбинных мешалок на расстоянии 0,8 D друг от друга. Такое решение дает возможность обеспечить интен-сивное перемешивание во всем объеме, добиться большого и точно определенного време-ни контакта, что в итоге позволяет достичь большой движущей силы процесса. Расход энергии в этом случае ниже, чем в аппарате большего диаметра с одной мешалкой. При установке на одном валу нескольких мешалок расстояние между ними не должно быть менее диаметра мешалки d и обычно не превышает 3d. Уровень жидкости над верхней мешалкой составляет (1,5 2,0) d.
Конструкция мешалки, как и тип сосуда, играют наиболее важную роль в процессе перемешивания. Так, аппарат с отражательными перегородками обеспечивает режим перемешивания иной, чем аппарат без перегородки, даже если в них установлена одна и та же мешалка.
|
В основной неорганической технологии используют пропеллерные, турбинные, лопастные и рамные мешалки. ГОСТ 20680-75 регламентирует 12 основных типов мешалок. Наиболее часто применяемые типы мешалок показаны на рис.6. .
Рис.6. Типы мешалок:
а, б – турбинные с наклонными лопатками; в - трехлопастная; г, д - турбинные с прямыми лопастями; е - лопастная; ж-u - рамные.
В наиболее общем случае их можно разделить на быстроходные и тихоходные. К быстроходным относят пропеллерные и турбинные мешалки схема работы которых показана на рис.7. Эти мешалки в зависимости от формы лопастей и способа их установки могут создавать радиальный, осевой и радиально-осевой потоки жидкости.
Быстроходные мешалки обычно работают в аппаратах с отражательными пере-городками. Отсутствие перегородок приводит к завихрению жидкости и образованию воронки (рис. 7, в). При этом жидкость плохо перемешивается, снижается турбулентность потока и полезный объем аппарата. Число перегородок в аппаратах составляет обычно четыре, а их ширина - В 0,1D. В случае жидкостей, имеющих вязкость, близкую к вяз- кости воды, перегородки располагают у самой стенки аппаратов. Для жидкостей с повы-
шенной вязкостью ( > 7 Па·с) такое расположение перегородок приводит к образо-ванию застойных зон вокруг перегородок, поэтому в этом случае их располагают на не-котором расстоянии (0,2
0,5) В от стенки аппарата. Роль перегородок, предот-вращающих образование воронок, могут исполнять стойки змеевиков, гильзы термо-метров, погруженные патрубки наполнения и т. д.
К тихоходным относят лопастные и рамные мешалки. Они создают в основном окружной поток жидкости.
Рис. 7. Схема работы турбинной и пропеллерной мешалок:
а - турбинная, аппарат с перегородками; б - пропеллерная, аппарат с перегородками; в – пропеллерная, аппарат без перегородок.
Например, смеситель содового производства и каустификаторы 1 ступени в произ-водстве едкого натра снабжены рамными мешалками, а сборники и напорные баки из-весткового молока - лопастными; пропеллерные мешалки применяют в реакторах и вакуум-кристаллизаторах производства соединений бария, экстракторы фосфорной кислоты оборудованы турбинными мешалками.
Вибросмесители осуществляют перемешивание жидких сред турбулентными струями, возникающими при осевом движении диска (рис. 8) в перемешиваемой среде [5]. Схема конструкции вибросмесителя показана на рис. 8. В корпусе вибро-смесителя помещен перфорированный диск, укрепленный на штоке и совершающий колебания посредством вибровозбудителя. Последний изолирован от опорной конс-трукции при помощи упругой подвески. Для перемешивания пульп диск устанав-ливают на небольшом расстоянии от дна аппарата колебательном движении перфори-рованного (0,3 0,5 длины струи, определяемой опытным путем) для размыва образу-ющегося на дне осадка из наиболее тяжелых частиц пульпы. Конус перфорации при этом направлен большим основанием вниз. Оптимальный угол раствора конуса составляет 970. Диаметр диска обычно не превышает 700
800 мм, при больших диаметрах необходимы конструктивные решения, повышающие жесткость диска. Диаметр штока в современных аппаратах ограничивается размером около 70
100 мм, его длина - 4,5 м. Герметизация крышки аппарата, через которую проходит шток, обеспечивается диафрагмами из листовой резины. В химической промышленности используют вибросмесители с объемом аппаратов 0,2
3 м3.
|
![]() ![]() | Корпус аппарата изготавли-вают из стали, для агрессивных сред - из нержавеющей. Внутрен-няя поверхность может быть футе-рована кислотоупорным кирпи-чом, свинцом или резиной. Дно аппарата для перемешивания жид-костей и легких пульп делают плоским или сферическим, для тяжелых пульп - коническим. В качестве материала штока для уменьшения массы колеблю-щихся частей целесообразно при-менение титана. Число дисков на штоке и число штоков зависит от размеров аппарата. В качестве привода вибро-смесителей используют электромагнитные и дебалансные вибро-возбудители, причем применение первых предпочтительнее из-за большего ресурса работы, возмож- |
ности управления амплитудой колебаний и лучшей уравновешенности системы
2.1. Выбор мешалки [1]
В настоящее время не выработан универсальный критерий, позволяющий выбрать оптимальный вариант мешалки. При выборе мешалки часто руковод-ствуются результатами лабораторных и промышленных опытов. Предварительный выбор мешалки можно сделать по рис. 9, где соответствующая кривая показывает верхнюю границу работы данного типа мешалки.
![]() | ![]() ![]() ![]() |
Одной из наиболее важных характеристик винтовой мешалки является ее шаг, свя-
занный с углом наклона лопасти на радиусе r зависимостью:
а = 2 r tg
. Обычно эти мешалки конструируют с неизменным шагом по радиусу. Наклон лопастей меняется. Минимальный наклон - на наружной поверхности, максимальный - у втулки. Наиболее распространены мешалки с шагом а = d или
=180. Встречаются также мешалки, имеющие угол наклона конца лопастей 450. Эти мешалки имеют шаг а =
d. Они обеспечивают лучшую циркуляцию жидкости в аппарате. Иногда пропеллерные мешалки снабжают диффузором (циркуляционной трубой), который дает возможность обеспечить явно осевую циркуляцию жидкости в аппарате и позволяет устанавливать пропеллер выше, что сокращает длину вала. Пропеллерные мешалки имеют от 2 до 4 лопастей (чаще 3) и частоту вращения 7
40 с-1. При отношении a/d =
пропеллерная мешалка превращается в турбинную мешалку с прямыми лопатками эллиптической конфигурации.
Пропеллерные мешалки наиболее эффективны при необходимости создания значи-тельной циркуляции жидкости в аппарате, особенно в сосудах с выпуклым дном. В аппа-ратах с плоским дном применять их не следует. Диаметр дисперсных частиц не должен превышать 0,5 мм, а их объемная доля 10 %. При перемешивании в очень больших емкос-тях пропеллерные мешалки дают больший эффект, чем турбинные, но они неприемлемы для диспергирования газа в жидкости. Ввиду сложности изготовления винтовых мешалок рекомендуется вместо них использовать трехлопастные мешалки с углом наклона лопаток к плоскости вращения 240 и их шириной b = 0,2 d (см. рис. 6, в). Эти мешалки имеют характеристики, близкие с винтовыми. Турбинные мешалки снабжены 4-8 лопатками (обычно - 6). Отношение d/D, как и для пропеллерных, составляет 0,20 0,33. Частота вращения п = 2
20 с-1, так что окружная скорость и=
dп концов лопаток колеблется в пределах 3
16 м/с.
Турбинные мешалки с прямыми лопатками (см. рис.6 г,д)создают в основном радиальный поток жидкости, а мешалки с наклонными лопатками (см. рис. 6 а, б) - радиально-осевой поток. Угол наклона лопаток составляет обычно 450.
Рекомендуется использовать турбинные мешалки для процессов растворения, теплообмена, суспензирования, абсорбции газов и проведения химических реакций.
В процессах с использованием суспензий предпочтительно применять турбинные мешалки с наклонными лопастями, предупреждающими седиментацию частиц.
Быстроходные мешалки устанавливают в сосуде на высоте 0,3 D. Высота жидкости в аппарате составляет (1,0 1,3) D.
Лопастные мешалки (см. рис. 6, е)отличаются от турбинных отношением d/D, частотой вращения и числом лопастей. Диаметр d и ширину лопастей b обычно прини-мают в пределах d = (0,5 0,8) D и b = 0,l d. Высота установки от дна сосуда h =(0,1
0,3) D, а высота жидкости в сосуде Н = (0,8
1,3) D. Число лопастей состав-ляет обычно 2, редко - 4. Для перемешивания в высоких аппаратах на одном валу можно установить несколько мешалок по высоте, расстояние между которыми выбирают равным 0,3
0,8 d. Окружная скорость их находится в пределах 1,5
5 м/с. Лопасти мешалок располагают обычно вертикально или с наклоном в 450. Наклонные лопасти более интенсивно перемешивают жидкость, чем прямые.
Лопастные мешалки из-за простоты изготовления применяются в тех случаях, когда нет необходимости в интенсивной радиально-осевой циркуляции жидкости в аппа-рате. Они создают главным образом окружную циркуляцию жидкости и лишь незна-чительную радиально-осевую. Их недостаток - слабая интенсивность перемешивания.
Рамные мешалки ( см. рис. 6 ж – и) отличаются низкими значениями частоты вра-щения (0,3 1 с-1) и окружной скорости (0,5
2,5 м/с). Диаметр мешалок приближается к диаметру аппарата, и зазор между лопастью и стенкой сосуда обычно находится в пре-делах (0,005
0,1) D; b = 0,06 d. Рамные мешалки можно использовать для перемешивания жидкостей (суспензий) с высокой вязкостью (до 100 Па·с).
Для усиления турбулентности жидкости и интенсивности перемешивания во всем объеме аппарата внутри рамы могут устанавливаться дополнительные мешалки, лучше всего с наклонными лопастями (см. рис. 6, з).
Используют рамные мешалки при необходимости создания интенсивного переме-шивания за счет окружной циркуляции. Они препятствуют (замедляют) обрастанию сте-нок аппарата твердыми частицами вследствие высоких скоростей жидкости вдоль стенок.
Вибросмесители по сравнению с лопастными смесителями конструктивно более просты и надежны, имеют более высокую производительность, меньшие экс-плуатационные расходы и дают лучшее качество смешения. Так, например, эмульсия парафинового масла в воде, приготовленная в вибросмесителе, начинает расслаи-ваться через 360 с, тогда как та же эмульсия, полученная во вращающемся механическом смесителе, расслаивается через 180 с.
Смесители этого типа можно также успешно использовать при проведении тех-нологических процессов (растворения, выщелачивания, диспергирования и т. д.), при которых необходима подача газообразного компонента. При этом в 2 10 раз улуч-шается абсорбция газа жидкостью (например, хлора известковым молоком) Направ-ление колебаний перфорированных дисков - вертикальное. При частоте 50
100 Гц амплитуда колебаний равна 2
4 мм, для частот 25
30 Гц - 3
4 мм.
Вибросмесители особенно пригодны для суспензий с микробиологичес- кими структурами. Для этой цели выпускается ряд контактных аппаратов объемом от 1 6 л (лабораторный вариант) до 5000 л. Аппараты снабжаются необходимыми изме-рительными устройствами (датчиками рН, рО2 и т. д.), рубашкой с теплоносителем для поддержания рабочей температуры, приборами для автоматического управления.
|
|
Кормораздатчик мобильный электрифицированный: схема и процесс работы устройства...
Своеобразие русской архитектуры: Основной материал – дерево – быстрота постройки, но недолговечность и необходимость деления...
Индивидуальные и групповые автопоилки: для животных. Схемы и конструкции...
История развития хранилищ для нефти: Первые склады нефти появились в XVII веке. Они представляли собой землянные ямы-амбара глубиной 4…5 м...
© cyberpedia.su 2017-2024 - Не является автором материалов. Исключительное право сохранено за автором текста.
Если вы не хотите, чтобы данный материал был у нас на сайте, перейдите по ссылке: Нарушение авторских прав. Мы поможем в написании вашей работы!