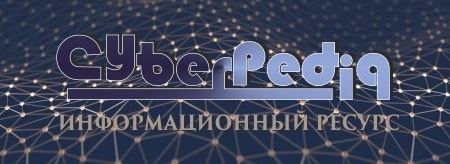
Археология об основании Рима: Новые раскопки проясняют и такой острый дискуссионный вопрос, как дата самого возникновения Рима...
Папиллярные узоры пальцев рук - маркер спортивных способностей: дерматоглифические признаки формируются на 3-5 месяце беременности, не изменяются в течение жизни...
Топ:
Отражение на счетах бухгалтерского учета процесса приобретения: Процесс заготовления представляет систему экономических событий, включающих приобретение организацией у поставщиков сырья...
Установка замедленного коксования: Чем выше температура и ниже давление, тем место разрыва углеродной цепи всё больше смещается к её концу и значительно возрастает...
Марксистская теория происхождения государства: По мнению Маркса и Энгельса, в основе развития общества, происходящих в нем изменений лежит...
Интересное:
Отражение на счетах бухгалтерского учета процесса приобретения: Процесс заготовления представляет систему экономических событий, включающих приобретение организацией у поставщиков сырья...
Уполаживание и террасирование склонов: Если глубина оврага более 5 м необходимо устройство берм. Варианты использования оврагов для градостроительных целей...
Искусственное повышение поверхности территории: Варианты искусственного повышения поверхности территории необходимо выбирать на основе анализа следующих характеристик защищаемой территории...
Дисциплины:
![]() |
![]() |
5.00
из
|
Заказать работу |
Определение и классификация бетонов.
Строительные в.в. являются полуфабрикатами, конечный продукт – строительные растворы, бетоны и железобетоны.
Все они – типичные композиционные материалы, в которых в.в. играют роль пластичной матрицы, а заполнители являются армирующими компонентами (формируют каркас композита).
Основные преимущества:
- высокая прочность (особенно на сжатие);
- надежность;
- долговечность;
- экономичность.
Бетон - искусственный каменный материал, получаемый после затвердевания рационально подобранной, тщательно перемешанной и уплотненной бетонной смеси, состоящей из неорганического в.в.(вяжущего вещества), воды, мелкого и крупного заполнителя и специальных добавок.
Бетонная смесь – рационально составленная и однородно перемешанная смесь компонентов бетона до начала процесса схватывания и твердения.
Структура бетона – крупный заполнитель, зерна которого обволакиваются смесью в.в. и песка.
Классификация бетонов по назначению:
1) Общестроительный (обычный);
2) Гидротехнический – плотины, дамбы, другие гидротехнические сооружения;
3) Дорожный – покрытия дорог, аэродромов;
4) Для транспортного строительства – мосты, эстакады, виадуки, путепроводы;
5) Жаростойкий – конструкции с рабочей температурой выше +200ºС;
6) Конструкционно-теплоизоляционный – наружные стены зданий;
7) Коррозионностойкий - конструкции в агрессивной среде.
Классификация бетонов по структуре:
1) Плотный (слитная структура) – объем пустот (П) <6%, пространство между зернами заполнителей полностью занято затвердевшим в.в.;
2) Крупнопористый – П ≤ 20% (беспесчаный, малопесчаный), значительная часть объема межзерновых пустот не занята цементно-песчаной смесью;
3) Поризованный – пространство между зернами заполнителей занято В.В. повышенной пористости;
4) Ячеистый – нет зерен крупного заполнителя, искусственные ячейки-поры размером 1-2 мм;
Классификация бетонов по объемной массе (средней плотности):
1) Особотяжелые – средняя плотность более 2500 кг/м3;
2) Тяжелые – 2200-2500 кг/м3;
3) Облегченные – 1800-2200 кг/м3;
4) Легкие – 500-1800 кг/м3;
5) Особолегкие – менее 500 кг/м3.
Классификация бетонов по виду вяжущего:
1) Цементные – на основе ПДЦ и глиноземистого цемента, наиболее универсальные бетоны;
2) Известковые – на извести, кварцевом песке, шлаке, золе; наиболее распространены силикатные бетоны автоклавного твердения;
3) Гипсовые – на основе гипсовых в.в., низкая водостойкость → для внутренних перегородок;
4) Шлакощелочные – на доменном шлаке и соде, поташе, жидком стекле;
5) Полимерные – на полиэфирных и эпоксидных смолах, для агрессивных сред;
6) Со смешанным вяжущим.
Классификация бетонов по виду заполнителя:
1) На плотных – средняя плотность заполнителя более 2000 кг/м3 (гранитный щебень, металлургические шлаки);
2) На пористых – средняя плотность менее 2000 кг/м3 (керамзитовый гравий, аглопоритовый щебень, туфы, известняки, органические);
3) На специальных – противорадиационные (лимонит, гемотит), жаростойкие (керамический бой, шамотный щебень).
Классификация бетонов по крупности зерен заполнителя:
1) Крупнозернистые – размеры зерен крупного заполнителя более 10 мм;
2) Мелкозернистые – менее 10 мм.
Классификация бетонов по условиям твердения:
1) Естественного твердения – 15-20ºС при атмосферном давлении, применяют в летних условиях для монолитных конструкций;
2) Подвергающиеся тепловой обработке – 70-90ºС при атмосферном давлении, применяют в зимних условиях или на заводах КПД;
3) Автоклавного твердения – при повышенных температуре 175-200ºС и давлении 0,9-1,6 МПа, применяют на заводах ЖБИ.
Требования к материалам для бетонной смеси. Специальные добавки.
Бетон = ВВ + Н2О + МЗ (мелкий заполнитель) + КЗ (крупный заполнитель)+ СД(специальные добавки)
Качество бетона зависит от правильного подбора компонентов смеси и от качества материалов.
Вода для бетонной смеси не должна содержать вредных примесей.
Чистая питьевая водопроводная – можно применять без проверки.
Остальные виды воды – только после сравнительного анализа.
1. Ускорители твердения – как катализаторы при кристаллизации цементного теста CaCl, NaCl, HCl;
2. Замедлители схватывания – ЛСТ (органические вещества);
3. Противоморозные добавки – для твердения зимой;
4. Поверхностно-активные (пластифицирующие) добавки – образуют на поверхности зерен слои с различными свойствами;
5. Пено- и газообразователи – для пористых и ячеистых бетонов;
6. Комбинированные.
По виду вяжущего
А) Гидравлические – цементные, смешанные;
Б) Воздушные – известковые, гипсовые, глиняные.
По назначению
А) Кладочные – для каменных кладок (фундаменты, стены, столбы, своды);
Б) Монтажные – для заполнения и заделки швов при КПД;
В) Отделочные (штукатурные) – для отделки стен, потолков, фасадов зданий и сооружений, для крепления облицовочных материалов, декоративные штукатурки, мозаичные полы.
Г) Специальные – гидро- и теплоизоляционные, акустические, тампонажные, инъекционные, рентгенозащитные, жаро- и кислотоупорные,
Маркировка труб
На внутренней поверхности каждой трубы на расстоянии 300 – 500 мм (в зависимости от диаметра) от одного из концов несмываемой краской наносят маркировку, включающую следующие обозначения:
· Знак производителя труб;
· Марку или тип стали;
· Номинальные размеры трубы (диаметр и толщина стенки);
· Фактический эквивалент углерода;
· Месяц и год изготовления трубы.
На каждую партию труб Производитель выдаёт сертификат качества, удостоверяющий их соответствующие установленным требованиям со следующими данными:
· Номинальные размеры (диаметр, толщина, длина) и вес трубы;
· Номер стандарта или технических условий, по которым изготовлены трубы;
· марка или тип стали, номер плавки и номер партии;
· результаты механических испытаний;
· химический состав стали по данным анализа ковшевой пробы контрольной пробы металла трубы; эквивалент углерода;
· результаты неразрушающего контроля с указанием каждого вида контроля;
· результаты гидравлических испытаний.
13. Алюминиевые материалы. Краткая историческая справка.
Алюминиевые самородки – явление редкое, так как в чистом виде Al не встречается (высокая химическая активность), преимущественно в виде соединений с O и Si – алюмосиликатов.
1825 г. – Дания – официальное открытие алюминия Гансом Христианом Эрстедом – «серебро из глины». Реакция амальгамы калия и безводного хлорида с получением окиси алюминия.
1827 г. – Фридрих Вёлер – усовершенствовал метод Эрстеда – применил сильны нагрев смеси хлористого алюминия и калия.
1854 г. – Анри Этьен Сент-Клер Девиль – промышленное производство алюминия – способ Вёлера, но вместо калия более дешевый натрий, вместо хлорида алюминия – более стойкий двойной хлорид алюминия и натрия.
1855-1890 гг. – метод Н.Н. Бекетова – получение алюминия из расплавленного криолита с помощью магния.
1886 г. – Метод Холла-Эру – электролитический метод производства алюминия открыт двумя учеными с разницей в 2 месяца.
1841 г. – США – алюминиевые тюбики для масляных красок;
1850 г. – Великобритания – первая упаковочная фольга из алюминия
1858 г. – США – первая алюминиевая пивная банка.
С конца 19 века порошковой алюминий стал обязательным компонентом при фабрикации аммонала – взрывчатого вещества для начинки артиллерийских снарядов, бомб.
1893 г. Австриец К.И. Байер, инженер-химик запатентовал щелочной способ производства глинозема из высокосортных низкокремнистых бокситов – фактически, усовершенствовал переработку алюминиевого сырья и снизил стоимость производства промышленного алюминия.
Стадии получения алюминия:
1) Получение глинозема из руд;
2) Получение алюминия из глинозема;
3) Рафинирования алюминия.
1906 г. – Германия – Альфред Вильм создал сплав алюминия с содержанием 4 % меди и 0,5 % магния. Продал патент, на основе которого был разработан дюралюминий.
1910 г. – Германия – в цехах Хьюго Юнкерса было сконструировано и запатентовано первое цельнометаллическое самолетное крыло из алюминия. В 1919 в воздух поднялся первый дюралевый самолет.
1910-1912 гг. – Россия – профессор Петербургского политехнического института П.П. Федотьев – фундаментальная теория электрометаллургии алюминия.
Классификация чугунов.
В зависимости от состояния углерода чугуны подразделяются:
§ Белый чугун – углерод в химически связанном виде Fe3C (цементит) – высокая твердость, хрупкость, практически не поддаются резанию. В основном идет на выплавку стали и для производства ковкого чугуна.
§ Серый чугун – углерод в свободном состоянии (графит). По форме графитовых включений серый чугун разделяют на:
Ø СЧ – обычный с пластинчатым графитом;
Ø ВЧ – высокопрочный с шаровидным графитом;
Ø КЧ – ковкий чугун с хлопьевидным графитом.
Оксиды условно делят на:
•Стеклообразователи - SiO2
•Модификаторы – Na2O, K2O, CaO.
Недостатки стеклянных труб:
•Хрупкость (коэффициент запаса прочности 8,0);
•Склонность к образованию трещин при механических напряжениях;
•Склонность к образованию трещин при температурных перепадах.
Дальше хз надо или нет
Остеклованные трубы (Ме+стекло)
Стадии изготовления:
1)Подготовка стальной трубы – обжиг, зачистка внутренней поверхности металлическими щетками, продувка сжатым воздухом;
2)Внутрь стальной трубы помещается стеклянный баллон меньшего Ø, запаянный с обоих концов;
3)Сборка, закрытие торцов, помещение в электропечь;
4)В процессе нагрева происходит размягчение стекла и из-за расширения нагретого воздуха внутри баллона – плотное прилегание и спаивание с внутренней поверхностью трубы.
Вопрос 27. Процессы полимеризации и поликонденсации. Примеры соответсвующих материалов.
Полимеризацией называется реакция получения макромолекул, протекающая за счет разрыва кратных связей мономера, без выделения побочных продуктов.
Пример:
nCH2 = CH2 → (──CH2─CH2──)n + Q
этилен полиэтилен
Поликонденсацией называется процесс образования полимеров, при котором взаимодействие молекул мономеров сопровождается выделением побочных низкомолекулярных соединений (воды, спирта). Например, лавсан получают при поликонденсации терефталевой кислоты и этиленгликоля:
nHOOC-C6H4-COOH + n HO-CH2-CH2-OH → (─OC-C6H4-CO-O-CH2-CH2-O─)n + 2n H2O + Q
Вопрос 28. Состав пластмасс. Полимерное связущее. Смолы. Совместимость полимеров.
В состав пластмасс входят:
а) полимерное связующее вещество;
б) наполнители;
в) стабилизаторы;
г) пластификаторы;
д) отвердители;
е) специальные добавки.
Полимерное связующее вещество – основа пластмасс, цементирует
наполнитель и придает композиции пластические свойства = смола или
композиция смол.
Смола – сложная смесь родственных или взаимно растворимых
органических полимеров, находящихся в устойчивом твердо-жидком
состоянии.
Смолы имеют стабильную аморфную стекловидную структуру.
Примеры природных смол – канифоль, янтарь, шеллак.
В качестве полимерного связующего часто используют смеси
полимеров, стремясь достичь оптимального сочетания свойств компонентов, и, следовательно, обеспечить заданный комплекс эксплуатационных свойств
материала.
Должна учитываться термодинамическая совместимость полимеров.
Оптимальные эксплуатационные свойства полимерного материала на
основе смеси полимеров нередко достигаются не при молекулярном
перемешивании компонентов смеси, а при сохранении некоторой степени
неоднородности системы.
Совместимость полимеров – способность образовывать при определенных давлении, температуре и концентрации устойчивую систему из молекулярно диспергированных компонентов.
Диспергирование – (лат. dispergo = «рассеиваю») тонкое измельчение
твердого тела или распыление жидкости с образованием дисперсных систем
(порошки, суспензии, эмульсии, аэрозоли).
Примеры дисперсных систем: грунты, почвы, ткани живых организмов,
пищевые продукты
В состав пластмасс входят:
а) полимерное связующее вещество;
б) наполнители;
в) стабилизаторы;
г) пластификаторы;
д) отвердители;
е) специальные добавки.
Наполнитель - добавки в композиции пластмасс для уменьшения расхода дорогостоящего полмира и улучшения физико-механических свойств.
Увеличивают долговечность, прочность, твердость, ударную вязкость, огнестойкость, теплостойкость, кислотостойкость, теплопроводность, электропроводность или диэлектрические свойства.
Подразделяют на:
-Органические природные наполнители- древесная мука, хлопковые очёсы, целлюлоза, бумага, х/б ткань, стружка, древесный шпон.
-Неорганические природные наполнители- пылевидный кварцевый песок, порошок мела, тальк, асбест, гипс, доломит, каолин, магнезит.
-Неорганические искусственные наполнители- ПДЦ, шлаковый цемент, стеклянная мука, крошки никеля, чугуна, стали, стекловолокно, нейлон.
Могут быть:
1- порошкообразные
2- в виде волокон
3- листовые
4- особую группу составляют армирующий стекловолокнистые материалы
Стабилизаторы - вещества, вводимые в пластмассы для замедления старения и для предотвращение или торможение процессов термической деструкции в период изготовления или переработки.
Подразделяют 2 группы:
1- экранирующие- вступают в взаимодействие с реагентом деструкции быстрее чем полимер
2- блокирующие- быстро реагируют на возникающие свободные радикалы и предотвращают разрушение или старение молекулярных цепей
Стабилизаторы подразделяют:
1- актионксиданты, антиозонаты-
2- антирады- ионизирующие излучение
3- светостабилизаторы- солнечный свет, УФ
Пластификаторы - вещества, вводимые в пластмассы для улучшения технологических свойств (при переработке и эксплуатации) и повышения их эластичности (уменьшение хрупкости). Снижают вязкость системы и температуру стеклования, повышают эластичность и морозостойкость, облегчают введение наполнителей или улучшают формуемость изделий.
Требования к пластификаторам:
1- совместимость с полимером
2- низкая летучесть
3- бесцветность
4- отсутсвие запаха
5- функциональность при низких температурах
6- химическая стойкость (не ниже полимера)
30. Состав пластмасс. Отвердители. Красители. Смазочные вещества.
В состав пластмасс входят:
• полимерное связующее вещество,
• наполнители,
• стабилизаторы,
• пластификаторы,
• отвердители,
• специальные добавки.
Отвердители – химические вещества вводимые в полимерные композиции на определенной стадии производства (или переработки) в небольших количествах с целью «сшивания» линейных молекул в единую трехмерную сетку.
При этом происходят химические реакции и отверждение полимерной композиции – под действием теплоты, излучений высокой энергии, УФ излучения, катализаторов.
Отвердители подразделяются на 3 группы:
- Катализаторы – кислоты, соли, основания;
- Инициаторы – орг. и неорг. перекиси;
Ускорители – вулканизация каучуков.
Требования к отвердителям:
· Растворимость в исходном полимере;
· Нетоксичность;
· Обеспечение необходимой скорости отверждения;
· Обеспечение необходимой скорости поперечного сшивания;
· Сохранение своих свойств длительное время до завершения процесса отверждения.
Красители – вещества, вводимые в пластмассы для придания необходимого колера (окраски), цвет не должен изменяться при изготовлении и эксплуатации ПМ изделия.
Иногда красители дополнительно увеличивают антикоррозионные свойства, уменьшая склонность к образованию статических разрядов.
Красители подразделяются на пигменты:
− неорганические – охра, мумия, сурик, умбра, ультрамарин, оксид
хрома;
− органические – нигразин, хризондин;
− белые – литопон, диоксид титана, оксид цинка;
− синтетические органические красители
Смазочные вещества
Смазки – химические добавки, уменьшающие трение компонентов внутри ПМ композиции при ее переработке в изделия, снижающие вязкость и предупреждающие прилипание ПМ к пресс-форме.
В качестве смазок при производстве ПМ часто используют стеарин, олеиновую кислоту, трансформаторное масло.
31. Состав пластмасс. Ингибиторы. Порообразователи. Модификаторы. Растворители.
Ингибиторы и замедлители – химические вещества, которые прекращают или замедляют процессы полимеризации и поликонденсации.
Применяют: Сера; Гидрохинон; Ароматические амины; Уротропин; Гексаметилентетралин.
Порообразователи – вспенивающие вещества, которые используются для образования ячеистой или пористой структуры материала.
Порообразователи подразделяются на:
Твердые вспенивающие – порофоры = вещества, которые при нагревании разлагаются с выделением газов (CO2, азота, аммиака);
Жидкие порообразователи – выделяющие газы и образующие ячеистую структуру = бензол, изопентан;
Газообразные вспениватели – воздух, инертные газы = гелий, аргон.
Модификаторы – твердые, жидкие или газообразные вещества, под их влиянием происходит направленное изменение свойств полимеров.
Могут быть неорганические и органические,примеры: хлор; кислоты; природные битумы; низкомолекулярный каучук; растительные масла; канифоль; полиэфиры; полиамиды; латексы.
Растворители – жидкие вещества, способные переводить в состояние раствора полимеры или некоторые другие компоненты пластмасс.
В производстве ПМ наиболее часто применяют:
Бензин; уайт-спирит; бензол; метилхлорид; спирты (метиловый, этиловый, бутиловый); керосин; скипидар; толуол; дихлорэтан; сложные эфиры.
Растворители необходимы при производстве лаков, красок, клеев, мастик, полимербетонов, полимеррастворов.
Кроме растворителей различают сходные по функциям разбавители.
Разбавители – жидкие вещества, способные растворять полимеры в присутствии активного растворителя или разбавлять ранее приготовленные растворы полимеров.
32. Способы изготовления пластмассовых труб и изделий.
Состав технологических операций по изготовлению изделий из пластмасс:
1. Подготовительные работы по активации составляющих.
2. Дозирование компонентов и перемешивание в специальных смесителях
3. Формование изделий.
Способы формования изделий из ПМ:
а) Вальцевание
b) Горячее прессование
c) Литье под давлением
d) Центробежное литье
e) Экструзия
f) Вакуумная формовка
g) Намотка из ленты или из отдельных нитей
h) 3D печать
Вальцевание – метод переработки полимеров, заключающийся в
многократном пропускании материала через зазор между нагретыми
металлическими валками, которые вращаются навстречу друг другу.
Под действием температуры и механических усилий в зазоре между
вальцами материал переходит из твердого стеклообразного состояния в вязкотекучее. При этом он подвергается деформациям, размягчается, смешивается и гомогенизируется.
Каландрование – это метод непрерывного формования различных пленочных или листовых изделий, нанесения рельефного рисунка, армирования материалов тканями или сеткой при температуре выше температуры текучести или температуры плавления.
Горячее прессование – это метод изготовления изделий из пластических масс и резиновых смесей в пресс-формах, установленных на прессе (чаще всего гидравлическом). Исходный материал в виде пресс-порошка помещают в разомкнутую пресс-форму, нагретую до заданной температуры, когда форма замыкается, материал в результате нагревания и создаваемого прессом давления растекается и заполняет формующую полость, приобретая размеры и конфигурацию изделия.
Многокомпонентное литье полимеров получило в последнее время
широкое распространение. Заключается в последовательном и/или
одновременном впрыске нескольких различных, но совместимых материалов –поверхностного и базового – в одну формующую полость литьевой формы.
В результате получаются многоцветные или слоистые изделия, имеющие структуру типа «сэндвич», где базовый материал находится между слоями поверхностного. Технология обеспечивает универсальность за счет
оптимального использования свойств каждого из материалов.
Экструзия (от позднелат. Extrusio = выталкивание) – процесс, при
котором заданный профиль изделию придается продавливанием размягченной
пластической массы через формообразующее устройство (экструзионную
головку = дорн).
Намотка из ленты и из отдельных нитей – применяется для
изготовления стеклопластиковых труб и металлопластиковых баллонов для
сжатых газов.
Намотка может быть как периодической, так и непрерывной. Обеспечивается высокое качество внутренней поверхности трубы за счет её формования на наружной поверхности оправки, но качество наружной
поверхности низкое по причине отсутствия снаружи формообразующих элементов, промышленное применение нашли спирально-кольцевой, спирально-ленточный, продольно-поперечный и косослойный продольно-поперечный способы укладки армирующих волокон
Применение 3D принтеров – изготовление сверхточных деталей,
макетов, опытных разработок, медицинских протезов. Технология 3D печати –открытие в 1980-х годах, в 1990-х апробация, в 2000-х коммерческое применение, 2015–2016 гг. начало массового применения.
33. Основные виды пластмассовых труб. Соединения пластмассовых труб и изделий.
Пластиковые или полимерные трубы – это универсальный и распространенный материал. Используется в областях строительства и проведения коммуникаций.
Выделяют полиэтиленовые, полипропиленовые, поливинилхлоридные и металлопластиковые. У каждого вида свои характеристики и сферы применения, которые определяются устойчивостью трубы.
1. Пластиковые трубы для канализации
2. Гофрированные пластиковые трубы
3. Пластиковые трубы для отопления
4. Пластиковые трубы для водопровода
5. Пластиковые трубы для горячей воды
6. Пластиковые трубы для теплого пола
7. Пластиковые трубы высокого давления
8. Морозостойкие пластиковые трубы
9. Газовые пластиковые трубы
10. Квадратные пластиковые трубы
11. Пластиковые трубы для скважин
12. Пластиковые трубы для колодцев
Классификация защитных покрытий трубопроводов. Требования к защитным покрытиям.
Основные виды изоляционных покрытий МТП:
⚫ лакокрасочные (надземные участки)
⚫ битумная изоляция
⚫ пленочная (полимерными лентами)
⚫ заводского нанесения (экструдир. ПЭ и ПП)
При всех способах прокладки, кроме надземной, ТП подлежат комплексной защите от коррозии защитными покрытиями и средствами ЭХЗ, независимо от коррозионной агрессивности грунта. При надземной прокладке ТП защищают от атмосферной коррозии металлическими и неметаллическими покрытиями в соответствии с НТД на эти покрытия.
Классификация теплоизоляционных материалов. Требования к материалам, применяемых для теплоизоляции трубопроводов.
Теплоизоляционные – СМ, которые обладают малой теплопроводностью предназначены для тепловой изоляции строительных конструкций производственных, жилых, и с/х зданий и сооружений, поверхностей производственного оборудования и агрегатов (печей, турбин, ТП, камер холодильников).
Обычно это высокопористые материалы.
Средняя плотность ≤ 600 кг / м3.
Теплопроводность ≤ 0,18 Вт / (м·°С).
Крупные отечественные производители: холдинги «ТехноНИКОЛЬ», «Термостепс», группа компаний «Пеноплэкс», ЗАО «Завод «Минплита».
По теплопроводности (основной теплофизической характеристике) ТИМ делят на три класса: (ед. изм. Вт /(м·°С)
A. - малотеплопроводные (≤0,06),
B. - среднетеплопроводные (0,06-0,115),
C. - повышенной теплопроводности (0,115-0,175).
Требования к материалам:
· Низкий коэффициент теплопроводности;
· Высокая механическая прочность на сжатие и изгиб;
· Способность сохранять теплоизоляционные свойства в широком диапазоне температур и в течении длительного времени;
· Негорючесть;
· Химическая нейтральность;
· Водонепроницаемость;
· Малое водопоглощение (гидрофобность);
· Морозостойкость;
· Биостойкость (грызуны, насекомые, микроорганизмы);
· Нетоксичность;
· Способность выдерживать действие высоких температур и открытого пламени;
· Экономичность, доступность;
· Достаточно высокое электросопротивление.
Определение и классификация бетонов.
Строительные в.в. являются полуфабрикатами, конечный продукт – строительные растворы, бетоны и железобетоны.
Все они – типичные композиционные материалы, в которых в.в. играют роль пластичной матрицы, а заполнители являются армирующими компонентами (формируют каркас композита).
Основные преимущества:
- высокая прочность (особенно на сжатие);
- надежность;
- долговечность;
- экономичность.
Бетон - искусственный каменный материал, получаемый после затвердевания рационально подобранной, тщательно перемешанной и уплотненной бетонной смеси, состоящей из неорганического в.в.(вяжущего вещества), воды, мелкого и крупного заполнителя и специальных добавок.
Бетонная смесь – рационально составленная и однородно перемешанная смесь компонентов бетона до начала процесса схватывания и твердения.
Структура бетона – крупный заполнитель, зерна которого обволакиваются смесью в.в. и песка.
Классификация бетонов по назначению:
1) Общестроительный (обычный);
2) Гидротехнический – плотины, дамбы, другие гидротехнические сооружения;
3) Дорожный – покрытия дорог, аэродромов;
4) Для транспортного строительства – мосты, эстакады, виадуки, путепроводы;
5) Жаростойкий – конструкции с рабочей температурой выше +200ºС;
6) Конструкционно-теплоизоляционный – наружные стены зданий;
7) Коррозионностойкий - конструкции в агрессивной среде.
Классификация бетонов по структуре:
1) Плотный (слитная структура) – объем пустот (П) <6%, пространство между зернами заполнителей полностью занято затвердевшим в.в.;
2) Крупнопористый – П ≤ 20% (беспесчаный, малопесчаный), значительная часть объема межзерновых пустот не занята цементно-песчаной смесью;
3) Поризованный – пространство между зернами заполнителей занято В.В. повышенной пористости;
4) Ячеистый – нет зерен крупного заполнителя, искусственные ячейки-поры размером 1-2 мм;
Классификация бетонов по объемной массе (средней плотности):
1) Особотяжелые – средняя плотность более 2500 кг/м3;
2) Тяжелые – 2200-2500 кг/м3;
3) Облегченные – 1800-2200 кг/м3;
4) Легкие – 500-1800 кг/м3;
5) Особолегкие – менее 500 кг/м3.
Классификация бетонов по виду вяжущего:
1) Цементные – на основе ПДЦ и глиноземистого цемента, наиболее универсальные бетоны;
2) Известковые – на извести, кварцевом песке, шлаке, золе; наиболее распространены силикатные бетоны автоклавного твердения;
3) Гипсовые – на основе гипсовых в.в., низкая водостойкость → для внутренних перегородок;
4) Шлакощелочные – на доменном шлаке и соде, поташе, жидком стекле;
5) Полимерные – на полиэфирных и эпоксидных смолах, для агрессивных сред;
6) Со смешанным вяжущим.
Классификация бетонов по виду заполнителя:
1) На плотных – средняя плотность заполнителя более 2000 кг/м3 (гранитный щебень, металлургические шлаки);
2) На пористых – средняя плотность менее 2000 кг/м3 (керамзитовый гравий, аглопоритовый щебень, туфы, известняки, органические);
3) На специальных – противорадиационные (лимонит, гемотит), жаростойкие (керамический бой, шамотный щебень).
Классификация бетонов по крупности зерен заполнителя:
1) Крупнозернистые – размеры зерен крупного заполнителя более 10 мм;
2) Мелкозернистые – менее 10 мм.
Классификация бетонов по условиям твердения:
1) Естественного твердения – 15-20ºС при атмосферном давлении, применяют в летних условиях для монолитных конструкций;
2) Подвергающиеся тепловой обработке – 70-90ºС при атмосферном давлении, применяют в зимних условиях или на заводах КПД;
3) Автоклавного твердения – при повышенных температуре 175-200ºС и давлении 0,9-1,6 МПа, применяют на заводах ЖБИ.
Таксономические единицы (категории) растений: Каждая система классификации состоит из определённых соподчиненных друг другу...
История развития хранилищ для нефти: Первые склады нефти появились в XVII веке. Они представляли собой землянные ямы-амбара глубиной 4…5 м...
Механическое удерживание земляных масс: Механическое удерживание земляных масс на склоне обеспечивают контрфорсными сооружениями различных конструкций...
Автоматическое растормаживание колес: Тормозные устройства колес предназначены для уменьшения длины пробега и улучшения маневрирования ВС при...
© cyberpedia.su 2017-2024 - Не является автором материалов. Исключительное право сохранено за автором текста.
Если вы не хотите, чтобы данный материал был у нас на сайте, перейдите по ссылке: Нарушение авторских прав. Мы поможем в написании вашей работы!