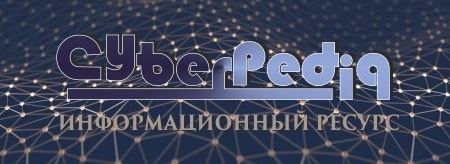
Механическое удерживание земляных масс: Механическое удерживание земляных масс на склоне обеспечивают контрфорсными сооружениями различных конструкций...
Адаптации растений и животных к жизни в горах: Большое значение для жизни организмов в горах имеют степень расчленения, крутизна и экспозиционные различия склонов...
Топ:
Определение места расположения распределительного центра: Фирма реализует продукцию на рынках сбыта и имеет постоянных поставщиков в разных регионах. Увеличение объема продаж...
Методика измерений сопротивления растеканию тока анодного заземления: Анодный заземлитель (анод) – проводник, погруженный в электролитическую среду (грунт, раствор электролита) и подключенный к положительному...
Марксистская теория происхождения государства: По мнению Маркса и Энгельса, в основе развития общества, происходящих в нем изменений лежит...
Интересное:
Уполаживание и террасирование склонов: Если глубина оврага более 5 м необходимо устройство берм. Варианты использования оврагов для градостроительных целей...
Что нужно делать при лейкемии: Прежде всего, необходимо выяснить, не страдаете ли вы каким-либо душевным недугом...
Берегоукрепление оползневых склонов: На прибрежных склонах основной причиной развития оползневых процессов является подмыв водами рек естественных склонов...
Дисциплины:
![]() |
![]() |
5.00
из
|
Заказать работу |
|
|
Заказчик пришел в ателье мод, чтобы сшить себе костюм. Ему предлагают журнал модной одежды. Выбрав какой‑то образец, он не удовлетворяется этим и выставляет закройщику дополнительные требования. Точно так же и заказчик будущего судна предъявляет конструкторскому бюро много требований. Все эти требования объединяются в специальный документ, который называют техническим заданием на проектирование. В нем записано: для чего предназначено судно и, если оно грузовое, сколько груза должно брать, с какой скоростью ходить.
Когда составляют техническое задание, указывают наиболее выгодные характеристики будущего судна, чтобы они были лучше, чем у ранее построенных судов подобного типа. Получив техническое задание, приступают к проектированию. Вначале разрабатывают эскизный проект. В нем определяют главные размерения и водоизмещение судна, его мореходные качества, форму обводов и прочность корпуса, прорабатывают несколько вариантов расположения помещений и механизмов, рассчитывают мощность и выбирают тип главного двигателя. Одновременно выполняют несколько эскизов, дающих общее представление о судне в целом.
При этом конструкторы следуют мудрому совету великого художника и ученого средних веков Леонардо да Винчи:
«Когда имеешь дело с водой, прежде посоветуйся с опытом, а потом с разумом». Они обращаются к опыту уже построенных судов, выбирая среди них подобный тому, который собираются проектировать. Характеристики выбранного судна и являются исходным материалом для проектирования.
Три основных плоскости теоретического чертежа.
Очень важно выбрать подходящую форму корпуса судна. Ведь он не прямоугольный «брусок», прямых линий у него очень мало. Придать криволинейному корпусу плавную, обтекаемую форму – это значит обеспечить судну высокие мореходные качества. Для этой цели вычерчивают так называемый теоретический чертеж.
|
Теоретический чертеж – весьма важный проектный документ. Например, он позволяет вычислить водоизмещение судна, произвести расчеты мореходных качеств: плавучести, остойчивости, непотопляемости, ходкости… По нему изготовляется модель судна, которая испытывается в опытовом бассейне. А во время постройки судна теоретический чертеж – основа для раскройки деталей корпуса.
Объемная схема теоретического чертежа.
По теоретическому чертежу разрабатывают чертежи общего расположения судна. Тут конструкторы проявляют много изобретательности. В самом деле, нелегко разместить многочисленные помещения, механизмы, различные устройства там, где на учете каждый кубический метр объема. На обширной территории фабрики или завода это не вызвало бы никаких затруднений. Особенно сложно разместить оборудование машинного отделения. И не только разместить, но дать возможность удобно их обслуживать и даже ремонтировать. Для этого иногда делают макет машинного отделения Его сооружают в натуральную величину отделения – из дерева. А внутри него, в строгом соответствии с чертежами общего расположения размещают изготовленное из дерева или жести оборудование.
Теоретический чертеж быстроходного грузового судна.
Опытный инженер‑судостроитель хорошо представляет по эскизному проекту контуры будущего судна. Он мысленно проходит по жилым и служебным помещениям, спускается в машинное отделение и трюмы. Правда, отдельные детали судна еще не совсем ясны, многие подробности на чертежах не указаны. Не совсем точно распланированы и помещения. Не беда! Все это можно доделать в следующем этапе проектирования – при разработке технического проекта. Тут окончательно уточняются чертежи общего расположения, производят планировку всех помещений в надстройках, размещают якорное устройство, спасательные шлюпки, мачты с грузовыми стрелами, разрабатывают схемы всех судовых трубопроводов, дополнительно решают многие другие задачи.
|
Быстроходное грузовое судно.
Судно постепенно «строится» на бумаге, приобретает все более законченный вид. Вот оно уже «построено» – в виде чертежей, расчетов, описаний. Однако по этому проекту невозможно изготовлять корпус, механизмы, различные устройства, приборы. Нужны рабочие чертежи. Их изготовление – самая ответственная и трудоемкая работа конструкторов. Рабочие, получив такие чертежи, превращают замыслы проектировщиков в готовые детали, узлы, части корпуса и машин, наконец, в целое судно.
Потом появились скоростные способы размножения чертежей. Например, с помощью специального аппарата можно фотографировать чертежи и рассылать заводам фотопленки. По мере надобности завод сам отпечатает любое количество фотокопий. И что важно, – чертеж фотографируют на фотопленку прямо с карандашного оригинала, выполненного конструктором. Для чертежей создаются портативные картотеки с микрокадрами. С них при помощи электрографической машины можно за несколько секунд отпечатать чертеж в любом масштабе на обычной бумаге.
Рабочих чертежей для одного судна – многие тысячи экземпляров. На заводе не ждут, пока будут готовы все, а приступают к постройке после получения первой партии чертежей.
Постройка судна началась
Каждое судно во время своей постройки переживает три особенно важных события. Это закладка, спуск со стапеля на воду и подъем государственного флага. Между этими событиями бывают разные промежутки времени. Все зависит от размеров и сложности оборудования. У крупных судов каждый промежуток тянется по многу месяцев, у мелких – от закладки до подъема флага проходит всего несколько недель. Закладку производят тогда, когда корпус начинают собирать на стапеле. Внутри корпуса закладывают пластинку, на которой гравер написал: где и когда заложено судно, как его назвали.
Прежде постройку судна начинали с разбивки его корпуса на плазе. Плаз – это огромный зал длиною 200–300 метров. Его деревянный, идеально гладкий пол покрыт светло‑серой масляной краской. На этом полу специальным рейсфедером наносили, согласно теоретическому чертежу, все очертания корпуса судна в натуральную величину. Создавалась как бы гигантская выкройка. А с нее снимали потом выкройки для каждой детали или узла. Такими выкройками служили длинные гибкие рейки, шаблоны, каркасы. Часто выкройки делали, как и при шитье костюма, в виде эскиза на бумаге. Раскройку деталей по этим выкройкам выполняли в корпусообрабатывающем цехе. Каким же образом?
|
Вот разметчик уложил с помощью крана на рабочий стол большой стальной лист. Смотря на лежащий перед ним эскиз, он уверенно наносит на лист линии контура детали, или, наложив шаблон, обводит его острой стальной чертилкой. Подручный разметчика легкими ударами молотка по заостренному книзу стержню – керну – делал эти линии отчетливыми и надолго сохраняющимися. Каждая деталь, намеченная и замаркированная такими точечными линиями, поступала на участок обработки.
Потом теоретический чертеж вычерчивали не на огромном полу, а на стальных, хорошо отшлифованных и покрытых белой эмалью щитах. И не в натуральную величину, а в масштабе одна десятая. Такой чертеж назвали масштабным плазом.
Чертежи‑шаблоны позволили перейти к более точной и скоростной разметке.
Материал для костюма после раскройки разрезают. То же самое делают и с раскроенными листами. Прежде для этого служили пресс‑ножницы. Они резали неточно и долго. Теперь режут газом. Металл в месте разреза сначала нагревают горящей смесью кислорода и ацетилена до температуры воспламенения, а затем он сжигается в кислороде, оставляя чистый рез. В последние годы появились газорезательные машины, которые вырезают детали без разметки. Такую машину я видел на одном судостроительном заводе. И более всего меня удивило то, что человек, обслуживающий машину, не имел никакого отношения к движениям газового резака. Он зажигал смесь газов, укладывал на раскроечный стол лист, снимал готовые детали.
Газорезательная машина вырезает детали не по копир‑чертежам, а по заранее разработанной программе, которая записывается в цифровом виде на магнитную ленту. В программе отражены последовательный порядок операций, а также все необходимые сведения, касающиеся величины, формы и других характеристик деталей. Мало того, что машина обходится без чертежа, она еще выбирает наилучший вариант раскроя и тем самым очень экономит металл.
|
Автоматический газорезательный станок.
Однако не каждая вырезанная из стали заготовка есть уже готовая деталь. Ее иногда нужно согнуть по форме корпуса судна. Простую погибь делают на гибочных вальцах. А для гибки ребер корпуса есть специальные станки. Все это довольно легкие и быстрые операции. Другое дело, когда листу надо дать сложную погибь – и вдоль и по ширине. Раньше такую гибку делали только вручную. Сначала нагревали листы до белого каления, а потом выколачивали тяжелыми молотами по особым каркасам. Это была очень тяжелая и долгая работа. Для ее выполнения требовалась целая бригада самых опытных и сильных гибщиков. Теперь же листы гнут в холодном виде на гидравлических прессах. Такой пресс стоит недалеко от газорезательной машины. Высотой он с двухэтажный дом. На его пульте управления множество всяких ручек и приборов. В передней части пресса движется вверх и вниз большой поршень. Его называют пуансоном. Пуансон с большой силой давит через специальные штампы на стальной лист. Несколько нажимов пуансона – и лист приобретает любую сложную форму погиби. Сила давления у некоторых прессов достигает 2000 тонн.
Обработанные детали проверяет контролер, после чего их сдают на склад. Со склада они, по мере надобности, отправляются в сборочно‑сварочный цех. Там из них собирают конструкции корпуса судна.
Что же случилось нового в судостроении? Что могло ликвидировать множество станков, сократить число операций обработки судостроительной стали и этим самым ускорить постройку судов? Причиной этого явилась электросварка металлов, заменившая собой клепку.
Дуга‑чудесница
Электросварку впервые в мире применил русский изобретатель Н. Н. Бенардос в 1882 году, а его способ усовершенствовал несколько позже другой изобретатель – Н. Г. Славянов. У электросварки большие преимущества перед клепкой и другими способами соединения деталей. Возьмем, к примеру, клепку корпуса судна. Она была невозможна без применения множества соединительных угольников, стыковых планок, стальных прокладок. Уйму металла и средств тратили на изготовление этих вспомогательных деталей. При электросварке они все не нужны. А сколько металла и труда затрачивалось на клепку! Например, при постройке арктического ледокола в его корпус забили до миллиона заклепок. И для этого потребовалось просверлить два миллиона отверстий в деталях корпуса. При электросварке не надо ни отверстий, ни заклепок. Сварной шов гораздо прочнее и плотнее заклепочного шва. Клепку выполняла целая бригада из трех и даже четырех рабочих. А при электросварке работает один рабочий.
|
Представляете теперь, сколько сберегает электросварка металла, рабочей силы и денег?
Еще быстрее и прочнее сваривают части корпуса сварочными автоматами.
А какая большая разница в скорости ручной и автоматической сварки! Говорить об этой разнице – все равно что сравнивать скорость пешехода и автомобиля.
В последние годы для постройки судов все шире и шире применяют специальные высокопрочные стали и легкие алюминиево‑магниевые сплавы. Прежде такие металлы не поддавались обычным способам электросварки. И только появление аппаратов, выполняющих сварку в среде защитных газов, ликвидировали это затруднение судостроителей. Особенно были благодарны этому способу строители атомного ледокола «Ленин». Дело в том, что металлурги нашей страны создали для корпуса арктического богатыря такую марку стали, которая выдерживает любые «объятия» льдов Арктики.
Электросварка совершила полный переворот в судостроении. Она сильно изменила и упростила конструкцию корпуса, намного сократила число операций по изготовлению деталей. Наконец, электросварка помогла разработать новые способы скоростной постройки судов.
Скоростное строительство
Еще сорок лет назад техника постройки парохода была невысокой. Тогда корпус на стапеле собирали из многих тысяч отдельных деталей и узлов. Из множества ребер, подаваемых по очереди, составляли скелет корпуса. Потом на скелете собирали оболочку, опять‑таки из отдельных листов наружной обшивки и палуб. Все части корпуса соединяли заклепками. Условия работы были трудными. Вес машинки для сверления дыр достигал 30 килограммов, а клепального пневматического молотка – 16 килограммов. Такой инструмент приходилось держать на весу, часто изгибаясь в три погибели в тесных отсеках.
Работы шли так: пока судосборщики не соберут тот или иной район корпуса, нельзя работать сверловщикам. А пока не закончили свою работу сверловщики, здесь нечего делать клепальщикам. После клепальщиков приходили на стапель чеканщики. Их дело – обеспечить плотность заклепочных швов и испытать корпус парохода на водонепроницаемость. Металл уплотняли особым инструментом – чеканом, а испытывали так: нальют в отсек воды и смотрят снаружи – нет ли течи в заклепочных соединениях. Если в каком‑либо месте просочилась вода, – это место подчеканивали еще раз. Последними приходили маляры. Они красили испытанные отсеки. Рабочие других специальностей – судомонтажники, электромонтажники, плотники, столяры – приступали к работе только после спуска парохода на воду. Со стапеля сходили в воду почти пустые корпуса, без механизмов, устройств и оборудования. Всем этим «начиняли» судно во время достройки на плаву. Такая постройка тянулась долго – по нескольку лет. С такими темпами нельзя было мириться.
Рабочие и инженеры совместно с учеными взялись за улучшение техники судостроения. И был произведен настоящий переворот. А натолкнул судостроителей на этот переворот новый способ постройки жилых домов. Прежде дома строили по кирпичику. Потом их стали собирать из готовых крупных блоков вместе с оконными рамами и другим оборудованием. Здание растет теперь, словно гриб, – не по дням, а по часам.
Примерно то же произошло и с постройкой судна.
Разбивка корпуса парохода на секции.
Как бы разбить днище, борта и палубы судна на большие куски – секции? Как бы эти секции изготовлять заранее в цехе в удобных условиях, а потом быстро собирать из них на стапеле корпус? Так и сделали. Затем секции стали объединять в более крупные куски – блоки. Блок – это уже полновесный кусок корпуса – от борта до борта и от днища до палубы.
Корпус собирают не из многих тысяч отдельных деталей и узлов, а из нескольких десятков секций и блоков. Для небольшого судна нужно изготовить только 5–6 блоков.
Схема деления небольшого судна на блоки.
А сами секции и блоки собирают и сваривают из отдельных деталей в укрытых от непогоды, просторных и утепленных пролетах цеха. От этого стали лучше и условия труда рабочих и качество работы.
Но вот секция собрана и сварена. Прежде чем отправить эту секцию на стапель, ее нужно испытать на водонепроницаемость. Чтобы убедиться в плотности сварных швов, их испытывают керосином. Керосин скорее других жидкостей найдет себе дорогу среди неплотностей шва. При испытании шов с одной стороны покрывают меловой краской, а с другой – густо смазывают керосином. Если шов неплотный, то керосин выступит с другой стороны шва темной полосой на меловой краске. Такой шов вырубают и снова заваривают. Может быть и такой случай: шов плотный, но внутри него имеются трещины, пустоты, раковины. Такой шов не может быть прочным, но обнаружить внутренние пороки керосин не может. В этом деле человеку помогают разные приборы. Прежде хорошим помощником в проверке качества сварных швов был рентгеновский аппарат. Он просвечивал шов так, как в поликлиниках просвечивают человека. Сейчас появились и более совершенные приборы. Один из таких приборов называется ультразвуковой дефектоскоп. По внешнему виду он совсем простой – в виде небольшого ящика с экраном на передней стенке. Но зато какую чудесную работу проделывает этот прибор! Он направляет в проверяемый шов ультразвуковые лучи‑разведчики. Луч отражается от внутренней поверхности шва и возвращается к приемнику прибора. Если на пути луча‑разведчика встретилась трещина, раковина или другой порок, рабочий контролер по изображению на экране определит, что это за порок и на какой глубине он залегает. Этот прибор тоже доверяют только рабочему со средним образованием.
Сваренные и испытанные секции и блоки на огромных платформах доставляют к стапелю. Когда там соберется достаточное их количество и освободится сам стапель, приступают к сборке корпуса судна.
Изготовление блока в цеху.
Сборка корпуса из секций и блоков намного ускорила и работы на стапеле и достройку судна на плаву. Ведь секции и блоки подаются на стапель не пустыми. Их еще в цехе «начиняют» трубопроводами, вспомогательными механизмами, разными устройствами. А в блоках производят иногда даже оборудование и отделку помещений. Так что в секциях и блоках работают не только судосборщики и сварщики. Рядом с ними трудятся и рабочие других специальностей – судомонтажники, электромонтажники, столяры, маляры. На стапеле фронт работ расширяется еще больше. Здесь устанавливают крупное оборудование и выполняют те операции, которые нельзя было выполнить в цехе. А ведь раньше все это делалось уже на плаву, после спуска судна на воду. И что же получается? Раньше спускали на воду пустые стальные коробки, а теперь судно спускается почти готовым. Остаются отделка да испытания.
Большой переворот произошел и в монтажных работах на стапеле. Возьмем, к примеру, монтаж валопровода. Валопровод – это длинная линия валов, соединяющих двигатель парохода с гребным винтом. На крупных судах общая длина валопровода достигает 100 метров, а отдельных валов – 20 метров.
Еще недавно считали, что валопровод нельзя монтировать до спуска судна на воду. Почему же? Дело в том, что эта работа требует большой точности. Ведь оси валов, в том числе и ось вала двигателя, должны составлять одну совершенно прямую линию. Ось каждого вала не должна отклоняться от этой прямой даже на десятую долю миллиметра. От даже самого небольшого перекоса валы будут плохо вращаться в своих опорах‑подшипниках и быстро изнашиваться. А от большого перекоса может быть и авария. Судостроители боялись того, что установят валопровод, а потом от большого напряжения и изгиба корпуса при спуске судна точность сборки линии валов нарушится. Вот эта боязнь и заставляла монтировать валопровод на плаву. И только после этого устанавливали главный двигатель. При таком способе надолго затягивались монтажные работы. Теперь же главный двигатель устанавливают на стапеле и одновременно с этим ведут монтаж валопровода еще до спуска.
Сборка большого судна на стапеле.
Много сил и времени отнимает у судостроителей монтаж судовых трубопроводов. Мы уже знаем, как много вспомогательных механизмов имеется на пароходе. А от них по всем отсекам тянется множество труб. Если растянуть эти трубы в одну линию, получится длина в несколько десятков километров. Прежде трубы гнули вручную и с нагревом. Теперь эти работы механизированы. Ручную гибку труб заменили холодной на мощных станках. Судостроители придумали и новые, скоростные способы монтажа трубопроводов на самом пароходе.
Сколько времени уходило раньше на подгонку труб по месту их установки! Примерит рабочий трубу – не годится, и опять тащит обратно в цех, чтобы перегнуть или подрезать ее. Сколько таких бесцельных путешествий совершали рабочие – из цеха на судно и обратно! Теперь в цехах применяют специальные макеты. Это дает возможность сразу устанавливать заранее подогнанные по макету трубы на место.
Можно привести еще много примеров работы советских судостроителей по‑новому. Сейчас крупные суда строят в два‑три раза быстрее, чем до войны. Скорость постройки неудержимо растет и в наши дни. Например, построенный у нас первый дизель‑электроход ушел в плавание через двадцать месяцев после закладки его на стапеле. А на постройку такого же электрохода затратили всего четырнадцать месяцев.
В этом большая заслуга не только рабочих.
Ведь в постройке и снаряжении современного судна участвуют десятки, а то и сотни заводов и фабрик. Со всех концов нашей страны присылали они на завод сталь и машины, мебель и трубы, лес и приборы. Все поступало точно в срок.
Без этого скоростное строительство было бы невозможно.
Химия проникает на судно
Наш век часто называют веком атомной энергии. Это верно, но недостаточно. Мы живем и в эпоху бурного развития химии. Здесь особенно велика роль химии полимеров. Химия полимеров! Именно в этой области химическая наука творит чудеса, превращая природный или попутные газы нефтерождений в разнообразные полимерные материалы – каучук, пластмассы, волокна… Этим выполняется требование сегодняшнего дня: заменить, где возможно, дефицитные и дорогостоящие изделия из металла и дерева более дешевыми и не менее прочными изделиями из химических продуктов.
Пластмассы постепенно внедряются в монтаж судовых механизмов и систем. Уже появляются пластмассовые трубопроводы из полиэтилена, винипласта и других пластмасс. Срок их службы в два‑три раза больше, а вес в три‑четыре раза меньше, чем стальных. Из пластмасс строят даже целые суда. В нашей стране построено множество пластмассовых шлюпок, моторных катеров, грузовой теплоход на 15 тонн груза и пассажирское судно вместимостью 65 человек. Что же это за суда и как производится их постройка?
|
|
Папиллярные узоры пальцев рук - маркер спортивных способностей: дерматоглифические признаки формируются на 3-5 месяце беременности, не изменяются в течение жизни...
Поперечные профили набережных и береговой полосы: На городских территориях берегоукрепление проектируют с учетом технических и экономических требований, но особое значение придают эстетическим...
Типы оградительных сооружений в морском порту: По расположению оградительных сооружений в плане различают волноломы, обе оконечности...
История развития хранилищ для нефти: Первые склады нефти появились в XVII веке. Они представляли собой землянные ямы-амбара глубиной 4…5 м...
© cyberpedia.su 2017-2024 - Не является автором материалов. Исключительное право сохранено за автором текста.
Если вы не хотите, чтобы данный материал был у нас на сайте, перейдите по ссылке: Нарушение авторских прав. Мы поможем в написании вашей работы!