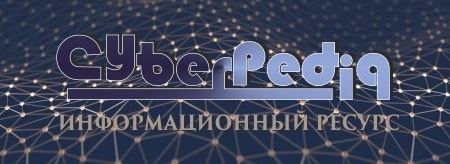
Наброски и зарисовки растений, плодов, цветов: Освоить конструктивное построение структуры дерева через зарисовки отдельных деревьев, группы деревьев...
Эмиссия газов от очистных сооружений канализации: В последние годы внимание мирового сообщества сосредоточено на экологических проблемах...
Топ:
Отражение на счетах бухгалтерского учета процесса приобретения: Процесс заготовления представляет систему экономических событий, включающих приобретение организацией у поставщиков сырья...
Характеристика АТП и сварочно-жестяницкого участка: Транспорт в настоящее время является одной из важнейших отраслей народного...
Интересное:
Средства для ингаляционного наркоза: Наркоз наступает в результате вдыхания (ингаляции) средств, которое осуществляют или с помощью маски...
Влияние предпринимательской среды на эффективное функционирование предприятия: Предпринимательская среда – это совокупность внешних и внутренних факторов, оказывающих влияние на функционирование фирмы...
Мероприятия для защиты от морозного пучения грунтов: Инженерная защита от морозного (криогенного) пучения грунтов необходима для легких малоэтажных зданий и других сооружений...
Дисциплины:
![]() |
![]() |
5.00
из
|
Заказать работу |
|
|
КУРСОВАЯ РАБОТА
ПРОЕКТ ПОДГОТОВИТЕЛЬНЫХ ЦЕХОВ НА БАЗЕ .
тема
МЕДНО-МОЛИБДЕНОВЫХ РУД ЭРДЕНЕТОВСКОГО МЕСТОРОЖДЕНИЯ .
Пояснительная записка
Студент, МФ09-1 __________ Давыдов Д.А
номер группы подпись, дата инициалы, фамилия
Руководитель __________ Усманова Н.Ф
подпись, дата инициалы, фамилия
Красноярск 2012
Федеральное государственное автономное образовательное учреждение высшего профессионального образования
«Сибирский федеральный университет»
Институт цветных металлов и материаловедения
Институт химико-металлургический
Кафедра ОПИ
Специальность Обогащение полезных ископаемых
Группа ОП 09-1
ЗАДАНИЕ
к курсовой работе по учебной дисциплине
«Дробление, измельчение и подготовка руд
к обогащению»
1. Выбрать и обосновать качественную схему дробления и измельчения руды Эрденетовского месторождения.
2. Рассчитать количественную схему дробильного отделения: выбрать, обосновать и рассчитать оборудование для операций дробления и грохочения. При работе принять:
· производительность фабрики по руде 9000000 т/год.,
· крупность поступающей руды 1200 мм,
· руда средняя.
· характеристику крупности продуктов дробления в дробилках 1, 2, 3 стадиях принять по типовым характеристикам.
3. Рассчитать количественную схему отделения измельчения. При расчете принять:
· содержание класса –0,074 мм в продукте измельчения 65 %,
· содержание класса -0,074 мм в руде, типовые размеры, производительность мельниц по исходной руде для фабрики аналога – по литературным данным.
|
ГРАФИЧЕСКАЯ ЧАСТЬ
Технологическая схема
Схема цепи аппаратов
Дата выдачи 3.02.2012
![]() |
Оглавление
1. Характеристика исходной руды.. 2
2. Расчет производительности дробильных цехов и измельчительного отделения обогатительной фабрики. 2
2.1 Выбор и обоснование схемы дробления. 2
2.2 Расчет степени дробления. 2
Конусная дробилка при крупном дроблении. 2
2.3 Выбор и обоснование схемы измельчения. 2
3. Цехи дробления. 2
3.1 Методы расчета гранулометрического состава продуктов дробления. 2
3.3 Выбор и расчет дробилок. 2
3.4 Выбор и расчет грохотов. 2
4 Измельчительное отделение. 2
4.1 Расчет производительности мельниц. 2
4. 2 Расчет мельниц по удельной производительности. 2
5 Расчет оборудования для классификации. 2
5.1 Расчет гидроциклонов. 2
5.2 Схема цепей аппаратов. 2
ЗАКЛЮЧЕНИЕ. 2
Таблица 2‑1. - Расчет производительности цехов фабрики. 2
Таблица 2‑2 Исходные данные для расчета схемы дробления. 2
Таблица 3‑1 Расчет качественно-количественной схемы дробления. 2
Таблица 3‑2 Результаты предварительного выбора дробилок и расчет производительности. 2
Рисунок 2‑1Трехстадиальная схема дробления. 2
Рисунок 2‑2Одностадиальная схема измельчения. 2
Введение
В 1976 году был заложен фундамент обогатительной фабрики (ОФ). В 1978 году введена в эксплуатацию первая очередь мощностью 4 млн. тонн переработки руды в год. В настоящее время фабрика расширена и годовая мощность по переработке составляет 25 млн. тонн руды. В среднем ежегодно выпускается 450 - 530 тыс. тонн медного концентрата в виде отпускаемой продукции. Обогатительная фабрика - основной производственный цех с технологической схемой, обеспечивающий дробление руды, измельчение, флотацию, фильтрацию, сушку и отгрузку товарных медных и молибденовых концентратов.
Обогатительная фабрика состоит из следующих отделений и участков: дробильно-транспортного, корпуса полусамо-измельчения, измель-чительно-флотационного, фильтровально-сушильного, реагентного, хвостового хозяйства, ремонта обогатительного оборудования и грузоподъёмных механизмов и хозяйственной части. Рудоподготовка осуществляется двумя технологическими линиями. Первая, производительностью 18-19 млн. тонн руды в год предусматривает ее трехстадиальное дробление в конусных дробилках, грохочение, далее двухстадиальное измельчение руды в шаровых мельницах до 60 - 65% по классу - 0.074 мм. В ходе проведенной реконструкции дробильного отделения достигнуто снижение крупности дробленного продукта с 20 - 22 мм до 14,2 мм. Вторая технологическая линия рудоподготовки (корпус самоизмельчения) оснащена щековой дробилкой, двумя мельницами самоизмельчения с объемом барабана 140 м3 и двумя шаровыми мельницами второй стадии измельчения МШЦ 5.5 х 6.5. В первой стадии в мельницы загружаются шары диаметром 100 - 120 мм в количестве 10 - 12% объема барабана. Продуктом этой линии является измельченная до 65% по классу- 0.074 мм руда, которая самотечным гидротранспортом направляется в главный корпус на флотационную секцию.
|
Цехи дробления
На основе данных базового расчета выполняется предварительный выбор дробилок и грохотов, далее рассчитывается их производительность в заданных условиях и, в процессе сравнительного анализа, выбирается окончательный вариант установки оборудования. При необходимости производится корректировка базового расчета – режима работы цехов и распределения общей степени дробления по стадиям схемы – и повторный расчет и выбор оборудования.
Выбор и расчет дробилок
Для дробления руд средней крепости и крепких применяются конусные дробилки, а также, на стадии крупного дробления, щековые дробилки с простым качанием щеки. Последние годы за рубежом разработаны и выпускаются также щековые дробилки со сложным качанием щеки с большим размером загрузочной щели для крупного дробления.
Для последующего сравнительного анализа предварительно отбираются дробилки, соответствующие требованиям табл.26 и табл.28 [[1]]. Отбираются дробилки, у которых размер загрузочного отверстия превышает заданный и диапазон регулировки разгрузочной щели включает заданную. У дробилок крупного дробления в каталогах указывается только номинальная разгрузочная щель. В этом случае считается, что диапазон регулировки составляет 40 %.
|
Для предварительно выбранных дробилок рассчитывается производительность в заданных условиях работы. Расчет производится по формуле:
(15)
где - поправочные коэффициенты соответственно на крупность питания, крепость и влажность
Поправочные коэффициенты определяются по следующим выражениям:
(16)
где
- номинальная крупность питания дробилки, мм
f – коэффициент крепости по Протодьяконову
w – влажность руды, %
Окончательный выбор варианта установки дробильного оборудования производится в результате сравнительного технико-экономического анализа, исходные данные и результаты которого сводятся в таблицу (Ошибка! Источник ссылки не найден. 3-3). Количество оборудования для установки определяется по формуле:
(17)
где Qп – нагрузка на дробилку, м3/час
Q – производительность дробилки, м3/час
Коэффициент загрузки оборудования по производительности определяется выражением:
(18)
Количество N дробилок для установки выбираем ближайшим большим целым от n.
Сравнение рассчитанных вариантов производим по общей установленной мощности оборудования и общей массе.
Таблица 3‑1 Расчет качественно-количественной схемы дробления
Номер по схеме | Продукт | Крупность, мм | Разгрузочная щель i, мм | Содержание класса +i в питании стадии, % | Содержание класса крупности -d (мм), % | Выход продукта | ||||||||
5 | 10 | 28 | 57 | 130 | 261 | 1200 | % | м3/час | ||||||
1 | Исходная руда | 1 200 |
|
| 1,2 | 2,3 | 6,4 | 12,4 | 26,2 | 45,6 | 93,9 | 100 | 812,3 | |
| Грохочение | 1 200 |
|
|
|
|
|
|
| 45,6 | 93,9 |
|
| |
2 | Крупнодробленая руда | 261 | 174 | 66,6 | 3,8 | 7,5 | 20,3 | 37,6 | 71,5 | 97,1 |
| 100 | 812,3 | |
4 | Питание дробилок 2 стадии |
|
|
|
|
|
|
|
|
|
| 100,0 | 812,3 | |
6 | Среднедробленая руда | 57 | 30 | 78,8 | 9,8 | 20,5 | 62,8 | 97,0 |
|
|
| 100 | 812,3 | |
7 | Питание грохотов 3 стадии |
|
|
| 28,12 | 56,2 |
|
|
|
|
| 209,2 | 1699,5 | |
8 | Питание дробилок 3 стадии |
|
|
|
|
|
|
|
|
|
| 109,2 | 887,1 | |
10 | Мелкодробленая руда | 12 | 12 | 75,3 | 43,0 | 89,6 |
|
|
|
|
| 100 | 812,3 |
Таблица 3‑2 Результаты предварительного выбора дробилок и расчет производительности
Модель
Рагрузочная щель, ОТ-ДО, мм
Объемная производительность,
ОТ-ДО, м3/час
Производительность дробилки Q при принятых i и B и значениях поправочных коэффициентов
ЩДП 12х15
1200
155
0
310
0
160
116
186
1380
1200
0,80
0,88
328,0
ККД-1200/150
1200
180
0
680
0
320
240
186
1380
1200
0,80
0,88
619,5
КСД-2200Гр
350
60
30
610
360
250
86
29
300
308
0,92
1,01
357,7
КСД-3000Т
475
50
25
850
425
400
217
29
300
308
1,15
1,27
629,1
КМД-1750Гр
130
20
9
130
95
160
53
12
64
56
1,37
1,51
157,9
КМД-1750Т
80
15
5
110
85
160
53
12
64
56
1,11
1,22
124,7
КМД-2200Гр
140
20
10
260
220
250
97
12
64
56
1,40
1,54
352,0
КМД-2200Т1
100
15
5
220
160
250
97
12
64
56
1,24
1,37
276,6
КМД-2200Т2
85
15
7
210
150
320
93
12
64
56
1,15
1,26
236,6
КМД-3000Т
95
20
6
440
320
400
220
12
64
56
1,22
1,34
496,7
Таблица 3‑3 Сравнительный анализ вариантов установки дробильного оборудования
Тип | Параметры дробилки | Нагрузка на дробилку, м3/час | Количество | Характеристика варианта | |||||
Производительность, м3/час | Масса, тонн | Установленная мощность, квт | по расчету | Выбран-ное число | Масса, тонн | Установленная мощность, квт | Коэффициент загрузки | ||
ЩДП 12х15 | 328,0 | 116 | 160 | 812,3 | 2,48 | 3 | 348 | 480 | 0,83 |
ККД-1200/150 | 619,5 | 240 | 320 | 812,3 | 1,31 | 2 | 480 | 640 | 0,66 |
КСД-2200Гр | 357,7 | 86 | 250 | 812,3 | 2,27 | 3 | 258 | 750 | 0,76 |
КСД-3000Т | 629,1 | 217 | 400 | 812,3 | 1,29 | 2 | 434 | 800 | 0,65 |
КМД-1750Гр | 157,9 | 53 | 160 | 887,6 | 5,62 | 6 | 318 | 960 | 0,94 |
КМД-1750Т | 124,7 | 53 | 160 | 887,6 | 7,12 | 8 | 424 | 1280 | 0,89 |
КМД-2200Гр | 352,0 | 97 | 250 | 887,6 | 2,52 | 3 | 291 | 750 | 0,84 |
КМД-2200Т1 | 276,6 | 97 | 250 | 887,6 | 3,21 | 4 | 388 | 1000 | 0,80 |
КМД-2200Т2 | 236,6 | 93 | 320 | 887,6 | 3,75 | 4 | 372 | 1280 | 0,94 |
КМД-3000Т | 496,7 | 220 | 400 | 887,6 | 1,79 | 2 | 440 | 800 | 0,89 |
Выбранный вариант установки дробильного оборудования | |||||||||
ККД-1200/150 | 619,5 | 240 | 320 | 812,3 | 1,31 | 2 | 480 | 640 | 0,66 |
КСД-3000Т | 629,1 | 217 | 400 | 812,3 | 1,29 | 2 | 434 | 800 | 0,65 |
КМД-2200Гр | 352,0 | 97 | 250 | 887,6 | 2,52 | 3 | 291 | 750 | 0,84 |
По результатам таблицы 3-3 предварительно выбраны дробилки:
ККД- 1200/1500 – 2 шт. К=0,66
КСД 3000Т - 2 шт. К=0,65
КМД 2200Гр – 3 шт. К=0,84
3.4 Выбор и расчет грохотов
В цехах дробления рудных обогатительных фабрик используются вибрационные грохоты в среднем и тяжелом исполнении, необходимая площадь грохочения которых рассчитывается по формуле:
(19)
где F – площадь грохочения, м2
Q –нагрузка на грохоты, м3/час
q – удельная производительность грохота, м3/м2час [7]
k, l, m, n, o, p –поправочные коэффициенты [1, табл. 30, стр. 223]
|
Все параметры и результаты расчета сводятся в таблицу (табл.3.4)
Предварительный выбор грохотов из каталога производится по допускаемой крупности исходного материала, числу ярусов сит и размеру отверстий сит. Последний параметр не является жестким ограничением. Результаты сводятся в таблицу.
Таблица 3.4 –значение поправочных коэффициентов и расчет площадь
Условия грохочения, учитываемые коэффициентом | Коэффи-циент | Условия по стадиям | Значения коэффициентов по стадиям | ||
2 | 3 | 2 | 3 | ||
Удельная производительность, м3/м2*час (при заданном размере ячейки грохота, мм) | q | 56 | 12 | 47 | 21 |
Содержание в исходном материале зерен размером менее половины размера отверстий сита, % | k | 18,0 | 28,1 | 0,58 | 0,76 |
Содержание в исходном материале зерен размером более размера отверстий сита, % | l | 66,3 | 43,8 | 1,46 | 1,12 |
Эффективность грохочения, % | m | 85,0 | 85,0 | 1 | 1 |
Форма зерен | n | руда | руда | 1 | 1 |
Влажность материала | o | сухой | сухой | 1 | 1 |
Способ грохочения | p | сухое | сухое | 1 | 1 |
Нагрузка на грохоты, м3/час |
|
|
| 812,3 | 1699,9 |
Площадь просеивающей поверхности, м2 |
|
|
| 20,4 | 94,5 |
Таблица 3.5 –Поправочные коэффициенты для расчета производительности грохотов
Содержание в исходном материале зерен размером менее половины размера отверстий сита, % | 0 | 10 | 20 | 30 | 40 | 50 | 60 | 70 | 80 | 90 |
Коэффициент k | 0,4 | 0,5 | 0,6 | 0,8 | 1 | 1,2 | 1,4 | 1,6 | 1,8 | 2 |
Содержание в исходном материале зерен размером более размера отверстий сита, % | 10 | 20 | 25 | 30 | 40 | 50 | 60 | 70 | 80 | 90 |
Коэффициент l | 0,94 | 0,97 | 1 | 1,03 | 1,09 | 1,18 | 1,32 | 1,55 | 2 | 3,36 |
Эффективность грохочения, % | 40 | 50 | 60 | 70 | 80 | 90 | 92 | 94 | ||
Коэффициент m | 2,3 | 2,1 | 1,9 | 1,65 | 1,35 | 1 | 0,9 | 0,8 | ||
Форма зерен | Дробленый материал разный (кроме угля) | Округленная (например.морская галька) | Уголь | |||||||
Коэффициент n | 1 | 1,25 | 1,5 | |||||||
Влажность материала | Для отверстий сита менее 25 мм | Для отверстий сита более 25 мм | ||||||||
Сухой | Влажный | Комкующийся | В зависимости от влажности | |||||||
Коэффициент o | 1 | 0.75–0.85 | 0.2–0.6 | 0.9–1.0 | ||||||
Способ грохочения | Для отверстий сита менее 25 мм | Для отверстий сита более 25 мм | ||||||||
Сухое | Мокрое с орошением | Любое | ||||||||
Коэффициент p | 1 | 1.25–1.40 | 1 |
Таблица 3.6- Результаты предварительного выбора грохотов
Модель | Площадь одного сита, м2 | Мощность электродвигателя, кВт | Масса грохота, кг | Размеры просеивающей поверхности, мм: | Размеры отверстий сит (решеток), мм: | Допускаемая крупность исходного материала, мм | Количество грохотов | Установленная мощность, т | Масса, т | Коэффициент загрузки | |||
ширина | длина | верхнего | нижнего | расчет | принято | ||||||||
Стадия мелкого дробления |
|
|
| ||||||||||
ГСТ51 | 7,875 |
| 4650 | 1750 | 4500 | Перфорированный лист 30, щелевидное сито 1,6; сетка 10 × 10 | – | 120 | 2,65 | 3 | 0 | 13,95 | 0,88 |
ГСТ61 | 10 |
| 6000 | 2000 | 5000 | 8; 12;16; 20 | – | 200 | 9,45 | 10 | 0 | 60 | 0,94 |
ГСТ61 (259Гр) | 8 |
| 6200 | 2000 | 4000 | 2–25 | – | 100 | 11,81 | 12 | 0 | 74,4 | 0,98 |
ГСТ61 (253Гр) | 10 |
| 5700 | 2000 | 5000 | 2–25 | – | 100 | 9,45 | 10 | 0 | 57 | 0,94 |
ГСТ81 | 18 | 18000 | 3000 | 6000 | - | - | 120 | 5,25 | 6 | 0 | 108 | 0,87 | |
ГИС 62 | 10 | 17 | 5100 | 2000 | 5000 | – | – | 150 | 9,45 | 10 | 170 | 51 | 0,94 |
|
|
|
| ||||||||||
Продолжение таблицы 3.6 | |||||||||||||
Стадия среднего дробления |
|
|
|
| |||||||||
|
|
|
|
| |||||||||
ГИТ 52М | 6,755 | 22 | 1700 | 1750 | 3860 | 8–100 | – | 400 | 13,98 | 14 | 308 | 23,8 | 1,00 |
ГИТ 51 | 6,125 | 22 | 6000–9000 | 1750 | 3500 | 50–300 | – | 400 | 3,40 | 4 | 88 | 32 | 0,85 |
ГИТ 51M | 6,755 | 17 | 800 | 1750 | 3860 | 8–100 | – | 400 | 3,09 | 4 | 68 | 3,2 | 0,77 |
ГИТ 71 | 13,2 | 30 | 1750 | 2500 | 5300 | 25–150 | – | 800 | 1,58 | 2 | 60 | 3,5 | 0,79 |
Таблица 3.7- Окончательный выбор грохотов
Модель | Площадь одного сита, м2 | Мощность электродвигателя, кВт | Масса грохота, кг | Размеры просеивающей поверхности, мм: | Размеры отверстий сит (решеток), мм: | Допускаемая крупность исходного материала, мм | Количество грохотов | Установленная мощность, т | Масса, т | Коэффициент загрузки | |||
ширина | длина | верхнего | нижнего | расчет | принято | ||||||||
Стадия мелкого дробления |
|
|
|
|
|
|
|
|
|
|
|
|
|
ГСТ51 | 7,875 | 0 | 4650 | 1750 | 4500 | Перфорированный лист 30, щелевидное сито 1,6; сетка 10 × 10 | – | 120 | 2,65 | 3 | 0 | 13,95 | 0,88 |
Стадия среднего дробления |
|
|
|
| |||||||||
ГИТ 71 | 13,2 | 30 | 1750 | 2500 | 5300 | 25–150 | – | 800 | 1,58 | 2 | 60 | 3,5 | 0,79 |
Исходя из таблицы расчетов грохотов на 2 дробилки КСД-3000Т выбрал2 грохотаГИТ71.
На 3 дробилки мелкого дробления КМД-2200Гр выбрал 3 грохотовГСТ51.
4 Измельчительное отделение
Расчет гидроциклонов
Расчет производили по методике, указанной в [1].
Определили выход слива (частный)
где при работе мельницы с гидроциклоном принимается велечина с = 200-300. Примем с =230
Выход песков гидроциклона определили по формуле:
Определили содержание твердого в сливе. Предварительно задали содержание твердого в песках для крупности слива 65 % класса –0,074 мм. Содержание твёрдого в песках приняли равным 70%[1,стр 262].
Определили содержание твердого в исходном
Из соотношения Ж:Т нашли разжиженность пульпы:
-исходного
-песков
-слива
По таблице 14 [1] условная крупность слива .
Размер класса, который распределяется по продуктам
В таблице 5.2 привели расчет шламовой схемы
Таблица 5.2 – Расчет шламовой схемы
Продукт | Выход, % | Твердого Q, т/ч | Разжижение R=W/Q | Содержание твердого, % | Расход воды Q·R=W, м3/ч | Объем пульпы
![]() ![]() |
Слив Пески | 30 70 | 351,8 820,8 | 4,56 0,43 | 18 70 | 1245,4 205,2 | 1741,1 1139,1 |
Исходный | 100 | 1172,6 | 1,67 | 37,5 | 1442,3 | 2414,5 |
По таблице 45 [1] подобрали размер гидроциклона. Для данных условий подходит гидроциклон :
-угол конусности ;
-стандартный эквивалентный диаметр питающего отверстия ;
-стандартный диаметр сливного патрубка ;
-диаметр пескового насадка .
Определили условно производительность гидроциклона, приняв условно давление на входе 0,1 МПа
где – производительность, м3/ч;
– поправка на угол конусности гидроциклона. Согласно [1]
,
где D – диаметр гидроциклона, см
– поправка на диаметр гидроциклона
[1];
– диаметр питающего отверстия, см;
– диаметр сливного патрубка, см;
– рабочее давление на входе в гидроциклон, МПа.
Рассчитали число гидроциклонов
Проверили нагрузку гидроциклона по пескам при диаметре пескового насадка (сечение при этом
)
Нагрузка находится в пределах нормы, которая составляет
0,5÷2,5 т/см2·ч[2, С. 264], поэтому к установке приняты 2 гидроциклона ГЦ – 2000 с давлением на подаче Р = 0,1 МПа.
,
По результатам расчета на мельницу МШЦ 6000x8000 установили 4 гидроциклона ГЦ-2000. В случае неисправности 2-ух гидроциклонов в эксплуатацию вступят запасные гидроциклоны.
5.2 Схема цепей аппаратов
Таблица5 –Спецификация основного технологического оборудования
№ | Наименование оборудования | Модель | Кол-во |
1 | Гидравлический молот |
| 1 |
2 | Пластинчатый питатель |
| 1 |
3 | Конусная дробилка крупного дробления | ККД-1200/150 | 2 |
4 | Ленточный конвейер |
| 1 |
5 | Магистральный ленточный конвейер |
| 1 |
6 | Металлоуловитель |
| 1 |
7 | Склад дробленой руды |
| 1 |
8 | Пластинчатый питатель |
|
|
9 | Магистральный ленточный конвейер |
| 1 |
10 | Конусная дробилка среднего дробления | КСД-3000Т | 2 |
11 | Конусная дробилка мелкого дробления | КМД-2200Гр | 3 |
12 | Вибрационный питатель |
| 2 |
14 | Распределительный бункер | 50 м3 | 2 |
13 | Конвейер с разгрузочной тележкой |
| 1 |
14 | Грохот самобалансный | ГСТ81 (253Гр) | 6 |
15 | Ленточный конвейер |
| 1 |
16 | Магистральный ленточный конвейер |
| 1 |
17 | Конвейер с разгрузочной тележкой |
| 1 |
18 | Накопительный бункер | 10 000 м3 |
|
19 | Ленточный конвейер |
| 6 |
20 | Гидроциклон | ||
21 | Шаровая мельница | МШР-6000x8000 | 2 |
22 | Зумпф |
| 6 |
23 | Шаровая мельница | 6000x8000 | 2 |
24 | Гидроциклон | ГЦ-150 |
ЗАКЛЮЧЕНИЕ
![]() |
Запроектировали цех подготовки к обогащению руды Эрденетовского месторождения.
На основании работы действующей обогатительной фабрики и исходных данных, в проекте принята следующая схема подготовки руды к обогащению: трехстадиальное дробление с предварительным грохочением перед средним дроблением, с предварительным и поверочным грохочением перед мелким дроблением и одностадиальная схема измельчения с использованием контрольной классификацией слива мельницы в гидроциклонах. Скальпирующий режим спирального классификатора позволит снизить нагрузки на гидроциклон.
Проектируемая схема измельчения была принята на основании исходных данных и вещественного состава руды. В проекте представлена одностадиальная схема измельчения при работе мельницы в замкнутом цикле с классифицирующим устройством, которая позволяет при достаточно большой производительности обогатительной фабрики получить измельченный продукт крупностью 65 % класса -0,074 мм.
Оборудование для дробления руды выбрано в соответствии с требованиями:
- типоразмер дробилки должен удовлетворять крупности исходного питания и дробленого продукта;
- коэффициент
|
|
История создания датчика движения: Первый прибор для обнаружения движения был изобретен немецким физиком Генрихом Герцем...
Общие условия выбора системы дренажа: Система дренажа выбирается в зависимости от характера защищаемого...
Типы сооружений для обработки осадков: Септиками называются сооружения, в которых одновременно происходят осветление сточной жидкости...
Археология об основании Рима: Новые раскопки проясняют и такой острый дискуссионный вопрос, как дата самого возникновения Рима...
© cyberpedia.su 2017-2024 - Не является автором материалов. Исключительное право сохранено за автором текста.
Если вы не хотите, чтобы данный материал был у нас на сайте, перейдите по ссылке: Нарушение авторских прав. Мы поможем в написании вашей работы!