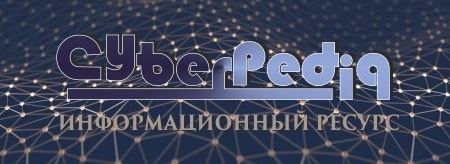
Архитектура электронного правительства: Единая архитектура – это методологический подход при создании системы управления государства, который строится...
Особенности сооружения опор в сложных условиях: Сооружение ВЛ в районах с суровыми климатическими и тяжелыми геологическими условиями...
Топ:
Отражение на счетах бухгалтерского учета процесса приобретения: Процесс заготовления представляет систему экономических событий, включающих приобретение организацией у поставщиков сырья...
Техника безопасности при работе на пароконвектомате: К обслуживанию пароконвектомата допускаются лица, прошедшие технический минимум по эксплуатации оборудования...
Интересное:
Лечение прогрессирующих форм рака: Одним из наиболее важных достижений экспериментальной химиотерапии опухолей, начатой в 60-х и реализованной в 70-х годах, является...
Наиболее распространенные виды рака: Раковая опухоль — это самостоятельное новообразование, которое может возникнуть и от повышенного давления...
Подходы к решению темы фильма: Существует три основных типа исторического фильма, имеющих между собой много общего...
Дисциплины:
![]() |
![]() |
5.00
из
|
Заказать работу |
|
|
РОБОТОТЕХНИЧЕСКИЕ КОМПЛЕКСЫ
КУЗНЕЧНО-ПРЕССОВЫХ ОПЕРАЦИЙ
Основными областями использования промышленных роботов в кузнечно-штамповочном производстве являются: автоматизация холодной листовой штамповки и обслуживание горячештамповочных прессов.
Современные промышленные роботы в холодноштамповочном производстве могут действовать только в хорошо организованной среде.
Наряду с технологическими мероприятиями роль организатора среды в значительной степени выполняют вспомогательные устройства, служащие для подачи заготовокпод робот в ориентированном виде и последующей их передачи без потери ориентации, смазывания заготовок перед штамповкой, удаления отходов, контроля протекания производственного процесса и других операций.
Каждый робототехнический комплекс представляет собой совокупность универсальных автоматических устройств, соединенных между собой электрическими связями и образующих единый механизированный комплекс, который позволяет обрабатывать двух - операционные детали, а также путем наращивания соответствующих составляющих устройств — многооперационные детали. Его можно трансформировать и на две самостоятельные позиции (без дополнительных устройств) для обработки одно - операционных деталей.
РОБОТОТЕХНИЧЕСКИЕ КОМПЛЕКСЫ
ЛИТЕЙНОГО ПРОИЗВОДСТВА И ГАЛЬВАНОПОКРЫТИЙ
Линия с портальными роботами.
Портальные промышленные роботы применяют в случае, если в цехе нет возможности крепить рельсовый путь к его перекрытию, или же в цехах с низким потолком (ниже 4м). Портальные промышленные роботы перемещаются по двух рельсовому пути, укрепленному на кронштейнах непосредственно к бортам ванн или на стойках, установленных рядом с ваннами.
|
К недостаткам линии с портальными роботами относятся:
- увеличение габаритных размеров линии в плане вследствие установки стоек рельсового пути в начале и в конце ее;
- наличие рельсового пути на уровне бортов ванн, что затрудняет доступ к ним при обслуживании и ремонте.
Линия с промышленными роботами консольного типа.
Промышленные роботы двух рельсового исполнения, используемые в линиях только прямолинейной компоновки, как подвесные, так и портальные, имеют идентичный привод горизонтального движения, состоящий из двухскоростного электродвигателя, червячного редуктора и электромагнитного тормоза. Скорость движения манипуляторов изменяется путем переключения частоты вращения электродвигателя. Необходимая точность остановки робота над позициями обеспечивается в результате перехода его в конце пробега на наименьшую скорость.
Подвесные и портальные роботы двух рельсового исполнения имеют идентичные механизмы подъема (опускания) руки, состоящие из электродвигателя, электромагнитного тормоза, червячного редуктора, валов и цепных звездочек с замкнутой цепью, к которым крепится каретка с захватом. Каретка роликами опирается на вертикальные направляющие. В манипуляторе монорельсового исполнения в качестве грузоподъемного механизма используется серийная электродрель.
Принципиального различия в конструкции линий гальванопокрытий с роботами подвесного, консольного и портального типов нет. Разница состоит лишь в условиях применения и в конструктивных особенностях манипуляторов, которыми эти линии оснащены.
РОБОТИЗИРОВАННЫЕ СВАРОЧНЫЕ КОМПЛЕКСЫ
В зависимости от способа получения неразъемного сварного соединения различают сварку плавлением и сварку давлением. В первом случае соединение деталей происходит расплавлением их кромок на небольшом участке, а во втором — сдавливанием соединяемых поверхностей деталей, которые, как правило, нагревают, чтобы снизить деформацию.
|
В машиностроении в основном применяют дуговую и контактную точечную сварку.
РОБОТОТЕХНИЧЕСКИЕ КОМПЛЕКСЫ НАНЕСЕНИЯ
ЛАКОКРАСОЧНЫХ ПОКРЫТИЙ
В настоящее время около 80 % промышленных изделий защищается от коррозии с помощью лакокрасочных покрытий.
При этом 70—80 % покрытий наносят методом распыления, причем основная масса работ выполняется вручную. С созданием промышленных роботов появилась реальная возможность автоматизировать процесс окраски.
На операциях нанесения лакокрасочных покрытий в настоящее время находят применение специализированные и универсальные окрасочные роботы.
Специализированные окрасочные роботы предназначены для окраски плоских и приводимых к ним поверхностей (крышки, фланцы, боковины и др.). Их применяют в машиностроении в условиях крупносерийного и массового производства.
Специализированные окрасочные роботы представляют собой вертикальные или горизонтальные колонны, на каретке которых укреплены электростатические поступательные краскораспылители. Каретка совершает возвратно-поступательные движения, а рабочий орган (краскораспылитель) имеет горизонтальный или вертикальный ход. Характеристика специализированных окрасочных роботов следующая:
- исполнение вертикальное или горизонтальное;
- скорость перемещения распылителей в пределах от 5 до 90 м/мин;
- бесступенчатое регулирование скоростей.
Универсальные окрасочные роботы представляют собой в общем случае многозвенные шарнирно-сочлененные (антропоморфные) конструкции, способные окрашивать сложные пространственные контуры. Они оснащаются контурными числовыми устройствами управления.
Проблема комплексной автоматизации.процесса нанесения лакокрасочных покрытий является достаточно сложной, так как одновременно необходимо автоматизировать и объединить в единый технологический комплекс подготовку поверхности изделия, установку изделия на конвейер или другую транспортную систему, транспортирование, кантование, нанесение покрытия, подготовку и доставку краски, промывку трубопроводов, разгрузку, диспетчирование и управление комплексом, идентификацию изделий, складирование, очистку и удаление отходов производства.
|
Большая часть перечисленных операций решается с помощью окрасочных робототехнических комплексов.
Типовой окрасочный комплекс в общем случае состоит из следующих основных частей:
- окрасочной камеры,
- промышленного робота, оснащенного краскораспылителем,
- кабины оператора,
- системы подачи краски и подготовки воздуха,
- устройств ориентации и опознавания изделий,
- пульта управления,
- шкафа силовых электрических цепей,
- блока электроавтоматики.
Каждая составная часть окрасочного РТК выполняет определенные функции.
Автоматизация нанесения покрытия на объемные изделия в настоящее время сводится к распылению лакокрасочного материала автоматическим распылителем, движущимся по траектории, идентичной траектории перемещения руки опытного маляра. Эта задача решается с помощью промышленных роботов с контурной системой управления.
В режиме обучения нанесение покрытий на изделие осуществляет опытный маляр, который с помощью съемного пульта окрашивает движущееся на подвесном конвейере изделие автоматическим краскораспылителем, установленным на манипуляторе робота. При этом происходит запись траектории движения звеньев манипулятора в память системы управления окрасочного робота. Перемещение краскораспылителя в этом случае представляется как сумма перемещений всех подвижных звеньев манипулятора. В режиме автоматической окраски (в режиме воспроизведения) система управления робота определяет вид поступающего в окрасочную камеру изделия, автоматически выбирает соответствующую программу и управляет работой краскораспылителя, перемещая его в соответствии с записанной траекторией.
Окрасочная камера в составе РТК может быть проходного или тупикового типа.
Кабина оператора служит для размещения и технического обслуживания оборудования комплекса, которая защищает его от воздействия внешних неблагоприятных факторов.
Система подачи краски и подготовки воздуха предназначена для подачи лакокрасочных материалов к краскораспылителю и их распыления.
Пульт оператора управляет работой РТК.
Устройство опознавания изделия позволяет согласовать тип окрашиваемого изделия с соответствующей программой, записанной в режиме "Обучение".
|
Окрасочные роботы используются при автоматизации всех вспомогательных операций, предшествующих процессу окраски и завершающих его.
РОБОТОТЕХНИЧЕСКИЕ КОМПЛЕКСЫ
СБОРОЧНЫХ ОПЕРАЦИЙ
Сборка - завершающий этап производства, во многом определяющий стоимость и качество продукции.
Сборочные работы в различных отраслях машиностроения составляют 40—50 % общей трудоемкости изготовления изделия, что объясняется низким уровнем их автоматизации и механизации. При этом уровень механизации не превышает 25—40 %, а автоматизации, используемой в основном в условиях крупносерийного и массового производства, 5—7 %.
В условиях серийного производства, удельный вес которого в общем валовом продукте составляет 70 %, стоимость сборки существенно выше, чем в массовом производстве, главным образом вследствие большого объема пригоночных и доводочных операций и значительной трудоемкости межоперационного и межцехового транспортирования.
Стоимость сборки можно уменьшить путем организационно-технических мероприятий, сокращения объема пригоночных и регулировочных операций, применения механизированных сборочных приспособлений и инструмента, увеличения объема автоматизации и механизации сборочных процессов. Причем кардинальным решением совершенствования сборочного производства является его автоматизация.
При применении автоматизированного оборудования к объектам сборки предъявляются специфические требования по их технологичности:
- взаимозаменяемость сборочных единиц, которые, в свою очередь, могут быть собраны независимо| друг от друга;
- возможность проведения последовательной сборки, когда с одной или несколькими базовыми деталями последовательно сопрягаются другие детали;
- минимальное число направлений сборки, простота траекторий движений соединения;
- максимальная свобода доступа сборочного инструмента
Изменяя конструкцию деталей, иногда даже незначительно, можно более эффективно использовать автоматическое сборочное оборудование, уменьшить число сборочных головок, сократить операцию сборки, уменьшив количество сборочных операций и упростив их.
В то же время, изменяя конструкцию изделий, можно усложнять технологический процесс изготовления, поэтому окончательное решение по изменению конструкции объектов сборки должно приниматься по результатам технико-экономических расчетов.
К деталям, предназначенным для автоматической сборки, предъявляются следующие требования:
- простота конструкции, обеспечивающая удобство складирования и ориентации;
|
- наличие на сопрягаемых поверхностях направляющих элементов, облегчающих соединение;
- наличие ярко выраженных базовых поверхностей, размеры которых и расположение их относительно сопрягаемой поверхности должны быть выдержаны с необходимой точностью;
- стойкость к повреждениям при воздействии сборочного инструмента и оснастки;
- унификация и стандартизация;
- гарантия качества деталей.
Тип и конфигурация базовой детали определяют конструкцию сборочного приспособления и схему базирования. Условия сборки, выбор базовых поверхностей для захватывания и установки присоединяемой детали, а также последовательность сборки зависят от пространственного расположения поверхностей сопряжения. Наиболее подготовленными к автоматической сборке являются две типовые схемы.
Одна из таких схем представляет собой комплект с охватывающей базовой деталью, в которую последовательно устанавливаются распорные втулки, уплотнительные манжеты, пружинные кольца и другие детали, или предварительно собранные комплекты или изделия, например подшипники качения. В качестве базовой могут служить детали коробчатой формы, фланцы, блоки зубчатых колес и т.п.
Вторая группа комплектов представляет собой сборочную единицу с базовой деталью типа вала - втулки, на которую устанавливаются отдельные детали или предварительно собранные комплекты и изделия.
Выделение из изделий типовых комплектов позволяет применить методы групповой технологии и повысить эффективность автоматизации сборки в серийном производстве.
Таким образом, от того, на каком уровне и с использованием каких принципов будет сконструирован сборочный узел машины и сама машина, зависит успех автоматизации ее сборки. Процесс автоматической сборки с помощью промышленных роботов подразделяется на несколько этапов:
- накопление в различных устройствах (налетах, магазинах, бункерах, кассетах и т.п.), конструкция которых зависит от конфигурации и габаритов объектов сборки;
- захватывание детали (объекта) роботом, оснащенным захватом или сборочным инструментом;
- транспортирование с помощью промышленного робота на позицию сборки и от нее к позиции накопления (выдачи);
- ориентация, которая может происходить как при предварительной подготовке объектов к сборке, так и в ходе технологического процесса;
- сопряжение деталей с помощью промышленного робота или на специальном сборочном оборудовании.
Существует три основные концепции построения робототехнических сборочных систем:
1. Вся сборочная операция расчленяется на элементарные, каждая из которых выполняется узкоспециализированным роботом. Эта концепция нашла широкое распространение при автоматизации массового производства. В этом случае не требуется сложного периферийного оборудования для подачи и ориентации деталей и средств адаптации.
2. Промышленный робот — сборщик располагается в центре комплекса. Вокруг него располагается различное вспомогательное оборудование с необходимым запасом деталей. Робот в соответствии с программой извлекает детали и осуществляет их сборку, используя при этом стационарные монтажные приспособления и оснастку.
3. Весь сборочный процесс расчленяется на группы элементарных операций. При этом для сборки каждой сборочной группы используется специализированный робот. В этом случае работа всех роботов осуществляется центральной управляющей ЭВМ.
Промышленные роботы, применяемые для автоматической сборки изделий машиностроения, выполняют основные и вспомогательные операции, т.е. соединение и транспортирование деталей и изделий.
Для операции соединения промышленные роботы используют захваты, сборочный инструмент и приспособления. Эти устройства вместе с промышленными роботами, а также накопители деталей, транспортирующее, технологическое, контрольное и другое оборудование составляют сборочный РТК. Возможность легкой и быстрой переналадки сборочных| комплексов — главная их особенность, которая является решающей в условиях серийного многономенклатурного производства.
По структурному признаку сборочные РТК подразделяются на однопозиционные и многопозиционные, т.е. с концентрацией или дифференциацией операций процесса сборки.
Компоновка комплекса зависит в первую очередь от числа деталей в сборочной единице, их размеров и массы, а также от годовой программы выпуска и номенклатуры собираемых изделий.
При однопозиционной сборке простых узлов изделий с выпуском 0,5—1 млн. шт / год транспортные операции (такие, как подача деталей из накопителей в сборочное приспособление, установленное на технологическом оборудовании, и удаление собранного изделия) могут осуществляться одним или двумя промышленными роботами с помощью захватов.
При сборке в мелкосерийном производстве узлов изделий в количестве десятков тысяч штук в год предпочтительнее схемы одно- и двухпозиционной сборки, выполняемые одним промышленным роботом последовательно с помощью быстро- сменных захватов и сборочных инструментов. Набор захватов и инструментов, необходимых для сборки партии изделий одного типоразмера, устанавливается в инструментальный магазин при наладке РТК.
Для сборки сложных изделий с годовой программой выпуска порядка нескольких сотен тысяч штук в год может быть применена многопозиционная схема с круговой или линейной траекторией перемещения собираемого изделия соответственно на круглом делительном столе или конвейере, обслуживаемом автоматическими манипуляторами или промышленными роботами, число которых определяется в основном количеством деталей в изделии.
К конструктивным особенностям промышленных роботов для сборки относятся:
- возможность автоматической смены захватов и сборочных инструментов;
- широкий диапазон скоростей перемещения исполнительных звеньев;
- адаптация к определенным условиям захватывания и соединения деталей (возможность встройки различных датчиков и наличие функциональных связей между ними и системой управления промышленным роботом);
- контроль качества сборки (возможность встройки в конечное звено робота датчиков контроля технологических параметров объекта сборки);
- повышенная точность позиционирования или наличие устройств компенсации погрешности позиционирования при соединении деталей.
Специфика условий выполнения операций соединения разнообразных по конструкции деталей с помощью промышленных роботов предопределяет создание специализированного сборочного инструмента достаточно широкой номенклатуры.
В зависимости от области применения используют сменный или быстросменный сборочный инструмент, различающийся местом и способом крепления. С помощью сменного инструмента выполняется одна и та же операция сборки деталей во всей партии собираемых изделий, затем инструмент снимается, и закрепляется в конечном звене промышленного робота вручную при наладке оборудования на сборку очередной партии изделий. Быстросменный инструмент автоматически сменяется в цикле сборки одного изделия и поэтому может применяться для сборки изделий разного типа.
Для успешного соединения деталей с возможно меньшими удельными затратами на единицу продукции и наибольшей производительностью сборочный инструмент для промышленных роботов должен соответствовать следующим требованиям:
- унификация по элементам базирования деталей и месту присоединения к роботу;
- допустимая по условиям сборки погрешность захватывания деталей;
- надежность захватывания и транспортирования детали на сборочную позицию;
- обеспечение компенсации погрешности взаимного расположения сопрягаемых поверхностей перед соединением;
- легкость регулировки и переналадки для присоединения однотипных деталей в установленном диапазоне размеров;
- возможность встраивания элементов контрольных устройств и средств адаптации.
Автоматическое соединение деталей обусловливает высокие требования к точности взаимного расположения сопрягаемых поверхностей и траектории перемещения. Неточность взаимного расположения сопрягаемый поверхностей определяется погрешностями позиционирования подвижных узлов сборочного оборудования, взаимного расположения сопрягаемой и базирующей поверхностей деталей, установки базовой детали в приспособлении и присоединяемой детали в инструменте, базирования деталей в накопителях и транспортно-подающих устройствах.
В связи с трудностью достижения необходимой точности взаимного расположения сопрягаемых поверхностей на переналаживаемом программируемом оборудовании прибегают к компенсации указанных погрешностей.|
Погрешности взаимного расположения деталей при сборке компенсируют двумя принципиально различными способами:
1) активным — с применением датчиков, которые измеряют усилия и моменты, возникающие при сопряжении деталей, и дают команды на дополнительные перемещения узлов робота или оборудования сборочного комплекса;
2) пассивным — с применением кинематических элементов и устройств, устанавливаемых непосредственно на сборочном приспособлении или инструменте и выполняющих автоматический поиск сопрягаемых поверхностей, для чего на сопрягаемых деталях необходимо иметь соответствующие вспомогательные поверхности: фаски, скосы и т.п.
Первый способ наиболее универсален, но применим при оснащении сборочного оборудования соответствующими механизмами перемещения и широким набором средств адаптации. Второй способ менее универсален, но значительно проще и требует меньших затрат времени на выполнение сборочной операции, а средствами очувствления оснащаются лишь устройства поиска детали и контроля ее наличия на сборочной позиции.
Кроме компенсации погрешности расположения деталей при сборке необходим контроль:
- наличия в захватных инструментах сопрягаемых деталей и их правильной ориентации;
- качества сборки, в том числе требуемых усилий сопряжения;
- собираемости деталей, что позволяет осуществить селективную сборку, когда из массы деталей выбираются такие, которые по своим параметрам обеспечивают возможность автоматической сборки. Это также позволяет упростить вспомогательное оборудование, применяя системы, производящие анализ и выбор требуемых деталей в режиме адаптивного управления. Кроме того, используют совместное управление несколькими роботами, согласуя их движения при сборке изделий.
РОБОТОТЕХНИЧЕСКИЕ КОМПЛЕКСЫ
КУЗНЕЧНО-ПРЕССОВЫХ ОПЕРАЦИЙ
Основными областями использования промышленных роботов в кузнечно-штамповочном производстве являются: автоматизация холодной листовой штамповки и обслуживание горячештамповочных прессов.
Автоматизация холодной штамповки
В настоящее время робототехнические комплексы создаются на базе различного кузнечно-прессового оборудования, серийно выпускаемого заводами машиностроительного комплекса. К такому оборудованию относятся:
- прессы однокривошипные открытые простого действия усилием 63—2500 кН;
- прессы однокривошипные закрытые двойного действия усилием 1000/630 кН;
- прессы кривошипно-коленные чеканочные усилием 4000, 10000 кН;
- прессы винтовые с дугостаторным приводом усилием 1000—4000 кН;
- прессы кривошипные горячештамповочные усилием 25000—40000 кН;
- прессы гидравлические для прессования изделий из реактопластов усилием 1600 кН;
- прессы-автоматы для прессования изделий из порошков твердых сплавов усилием 120 кН.
Отличительной особенностью листоштамповочных прессов является их большое быстродействие (до 60 и более ударов в минуту). Пределом быстродействия для выпускаемых в настоящее время промышленных роботов небольшой грузоподъемности можно считать 60—70, для более тяжелых — 10—20 циклов/мин, что в определенной мере ограничивает технические возможности прессов.
В то же время для холодной листовой штамповки, как правило, не требуется промышленных роботов с большим числом степеней подвижности и с высокой точностью. Последнее объясняется тем, что в большинстве случаев точная укладка заготовки достигается элементами штампа-ловителя, трафаретами и др. Обычно для таких роботов используются системы циклового управления.
Широкое использование промышленных роботов при автоматизации процессов холодной листовой штамповки объясняется следующими причинами:
- простотой конструкции механических прессов для холодной листовой штамповки; доработка, как правило, сводится к незначительным изменениям в системе их подключения;
- нет необходимости фиксировать заготовки в зоне обработки с помощью специальных зажимных устройств, как, например, при обработке резанием; следовательно, при автоматизации oneраций холодной листовой штамповки требуется не разработка специальных автоматических зажимных устройств, а лишь незначительное изменение конструкций штампов: введения фасок, дополнительных фиксаторов, трафаретов и т.д.;
- относительно высокой стойкостью штампов, что, как правило, исключает необходимость сплошного контроля качества изделий;
- простотой и однообразием манипуляций, выполняемых с заготовками при работе на универсальных прессах, что позволяет использовать промышленные роботы с цикловой системой управления и двумя — четырьмя степенями подвижности.
В настоящее время наибольший объем деталей штампуется на однокривошипных открытых прессах простого действия усилием 160—2500 кН с количеством вторичных операций 1—3 и более.
На робототехническом комплексе при холодной листовой штамповке выполняются следующие технологические операции:
- подача верхней заготовки из стопы, уложенной в магазине, на уровень захвата ее рукой робота;
- захват заготовки из исходной позиции магазина и перенос ее в рабочую зону пресса;
- укладка заготовки в штамп;
- штамповка изделия;
- вынос отштампованного изделия из рабочей зоны пресса;
- сброс изделия в тару.
При выполнении указанных операций должна быть создана блокировка, исключающая
- захват из исходной позиции неориентированных заготовок;
- захват двух слипшихся заготовок;
- загрузка пресса новой заготовкой до выноса из штамповочного пространства ранее отштампованной заготовки;
- рабочий ход пресса в случае нахождения руки робота с захватом в штамповочном пространстве пресса.
Промышленные роботы, используемые для холодной листовой штамповки, отличаются следующими особенностями:
- В большинстве они имеют одну, чаще две руки. Однорукие промышленные роботы используются при однооперационной штамповке, когда отштампованная деталь удаляется из штампа автоматически с помощью сбрасывателей (механических или пневматических) или выпадает в отверстие матрицы.
Если автоматическое удаление детали из штампа невозможно, применяют двурукие роботы. Одна рука робота транспортирует заготовку из подающего устройства в штамп, другая удаляет деталь из штампа в тару или перемещает ее на транспортирующее устройство.
Применение промышленных роботов с большим числом рук (например, трех) рационально при обслуживании одним роботом двух прессов.
- Как правило, погрешность позиционирования промышленным роботом для холодной листовой штамповки находится в пределах ±0,1—0,5 мм и является вполне приемлемой, так как в штампах, используемых для работы с применением промышленных роботов, устанавливаются дополнительные ловители, фиксаторы.
- Время на переналадку РТК складывается из времени на перепрограммирование, смену захватов, переналадку вспомогательного технологического оборудования. Для отечественных роботов в зависимости от сложности переналадки и типа робота время на переналадку составляет от 20 мин до 1,5 ч. Следовательно, если переналадка выполняется каждую смену, то потери рабочего времени могут достигать 10—20 % и, естественно, требование к сокращению времени на переналадку является одним из важнейших.
- Кроме того, конструкция промышленных роботов для холодной листовой штамповки должна удовлетворять условиям сопряжения робота с основным и вспомогательным технологическим оборудованием РТК по кинематической структуре,
Определение структуры, состава и компоновки робототехнического комплекса начинается с анализа технологического процесса получения детали.
В состав робототехнического комплекса входят:
- основное технологическое оборудование (прессы —один или несколько),
- промышленные роботы (один или несколько),
- устройство подачи заготовок,
- тара для готовых деталей,
- межоперационное устройство,
- устройство управления.
В общем случае структура робототехнического комплекса холодной листовой штамповки определяется следующими основными организационно-технологическими факторами:
- операционностью деталей;
- геометрическими параметрами детали;
- изменением формы заготовки в процессе обработки;
- характером технологического процесса (прерывистый или непрерывный);
- уровнем автоматизации вспомогательных операций.
Робототехнические комплексы бывают одно - операционными и многооперационными.
Одно - операционный робототехнический комплекс представляет собой законченную технологическую систему, включающую все необходимые элементы (питатели, устройства приема готовых деталей и др.) и предназначенную для автоматического выполнения одной однопереходной операции холодной штамповки.
Одно-операционные робототехнические комплексы отличаются:
- простотой структуры,
- относительной технологической простотой создания такой структуры;
- близкими значениями времени обслуживания роботом пресса и времени формообразования детали.
Многооперационный робототехнический комплекс характеризуется более сложной структурой.
Необходимость создания таких комплексов обусловлена наличием многооперационных технологических процессов (пробивка большого числа отверстий, гибка в разных плоскостях и т.д.).
Существенным фактором, оказывающим влияние на структуру робототехнического комплекса, являются геометрические параметры обрабатываемых деталей. Большое значение имеет высота готовой детали, поскольку вертикальное перемещение рук роботов, применяемых в холодной листовой штамповке, как правило, невелико и не превышает 50—100 мм.
В тех случаях, когда высота штампуемых деталей больше вертикального перемещения промышленного робота, штамповая оснастка должна иметь выталкиватели, поднимающие отштампованную деталь на определенную высоту.
Толщина заготовки определяет тип вспомогательного технологического оборудования и, в частности, подающих устройств.
Для заготовок из тонколистового материала (тоньше 0,8 мм) и больших размеров (больше 250х250 мм) затруднительно использовать шиберные подающие устройства, поэтому применяют магазинные устройства с верхней выдачей заготовки. В то же время для толстолистового материала не целесообразно использовать однопозиционные магазинные подающие устройства, так как это приводит к необходимости частого останова РТК для загрузки заготовок в кассету, тогда как в шиберное подающее устройство дополнительная загрузка заготовок может выполняться без останова робототехнического комплекса. В этом случае применяют многопозиционные магазинные подающие устройства.
В некоторых случаях при многооперационной штамповке на роботизированной линии возникает необходимость поворота детали при передаче ее с позиции на позицию. Следовательно, руки промышленного робота должны иметь возможность вращаться (ротации) вокруг своей оси. При однооперационной штамповке необходимость в ротации исключается и, следовательно, могут применяться роботы, имеющие только транспортирующие (региональные) степени подвижности.
Наиболее важной характеристикой промышленных роботов является грузоподъемность, однако выбор модели робота определяется не только массой детали. Так, очень часто габаритные размеры прессового оборудования, на котором штампуется деталь, а также штамповочная оснастка приводят к необходимости применения роботов несколько большей грузоподъемности.
Большое значение для успешной работы робототехнического комплекса холодной листовой штамповки имеет его конструкция, которая должна соответствовать следующим требованиям:
- после окончания процесса штамповки деталь должна оставаться в нижней части штампа, причем без потери ориентации в случае отсутствия механизмов удаления детали из штампа;
- штамп необходимо оснащать фиксаторами типа ловителей или трафаретов, причем угол заходной части фиксаторов может быть равен 30—60°, а высота фиксирующей части 0,75—0,9 толщины заготовки;
- штамп должен иметь автоматические выталкиватели для подъема детали из матрицы и съема ее с фиксаторов;
- выталкивание детали должно быть плавным и происходить без смещения заготовки в горизонтальной плоскости;
- конструкция штампа должна исключать возможность запрессовки отхода в деталь и наоборот (при разделительных операциях);
- по возможности заднее расположение направляющих колонок, что в некоторых случаях значительно сокращает продолжительность цикла штамповки;
- при переднем расположении направляющих колонок заготовка должна проходить с гарантированным зазором;
- штамп должен иметь такую открытую высоту, чтобы захват с заготовкой мог войти в зону штамповки, т.е. расстояние между зеркалом матрицы и верхней частью штампа должно быть равно сумме высоты (толщине) заготовки (детали), высоты захвата и гарантированного зазора;
- в конструкции штампа должна быть предусмотрена возможность контроля положения заготовки в штампе.
Особое значение при создании робототехнического комплекса холодной листовой штамповки имеет конструкция применяемых захватных устройств. Основное их назначение заключается в надежном захватывании заготовок и удержании их в определенном фиксированном положении при транспортировании из подающего устройства в штамп и из штампа в ориентирующее устройство или тару при заданных скоростях перемещения заготовки.
Большое разнообразие форм и свойств деталей обусловливает применение различных видов захватных устройств: вакуумных, механических, электромагнитных и др.
Вакуумные захватные устройства имеют преимущественное применение при работе с плоскими листовыми заготовками, а также с заготовками пространственной формы, имеющими плоские участки поверхностей для захватывания их присосками.
Рабочие поверхности захватов не должны изменять геометрическую форму и качество поверхности деталей при их захватывании.
Работа вакуумного захвата основана на том, что воздух, подаваемый под давлением через эжектор, создает вакуум в объеме, образованном камерой эластичной присоски и плоскостью заготовки. Присоски крепятся с помощью винта и гайки, что позволяет с наименьшими затратами времени их заменить. Такое конструктивное исполнение дает широкую возможность выбора присосок различных диаметров в зависимости от геометрических параметров заготовок.
Механические захваты клещевого типа обычно снабжаются сменными губками, конструкция которых зависит от формы исходных заготовок и получаемых деталей.
Существующая в настоящее время тенденция к дальнейшему повышению уровня механизации и автоматизации листоштамповочного производства позволяет сформулировать дополнительные требования к технологическому оборудованию:
- возможность автоматической перепрограммируемой смены штампов;
- автоматизация сбора и удаления отходов из зоны обработки;
- наличие устройства программируемого изменения хода ползуна;
- наличие автоматизированной системы контроля целостности штамповочной оснастки.
Робототехнические комплексы холодной листовой штамповки условно можно разделить на три группы:
1) роботизированная позиция — РТК, состоящий из одной единицы основного технологического оборудования, обслуживаемого роботами;
2) роботизированный участок — РТК, состоящий из одного робота и обслуживаемых им двух, трех единиц основного технологического оборудования (двух-трех-операционная обработка);
3) роботизированная линия, состоящая из нескольких РТК, соединенных передающими устройствами (многооперационная штамповка).
Простейшая структура роботизированной позиции приведена на рис. 29, а. В такой компоновке применяются роботы с автоматическим удалением отштампованной детали в тару. Такой РТК обладает наибольшей
|
|
Типы оградительных сооружений в морском порту: По расположению оградительных сооружений в плане различают волноломы, обе оконечности...
Археология об основании Рима: Новые раскопки проясняют и такой острый дискуссионный вопрос, как дата самого возникновения Рима...
Семя – орган полового размножения и расселения растений: наружи у семян имеется плотный покров – кожура...
Автоматическое растормаживание колес: Тормозные устройства колес предназначены для уменьшения длины пробега и улучшения маневрирования ВС при...
© cyberpedia.su 2017-2024 - Не является автором материалов. Исключительное право сохранено за автором текста.
Если вы не хотите, чтобы данный материал был у нас на сайте, перейдите по ссылке: Нарушение авторских прав. Мы поможем в написании вашей работы!