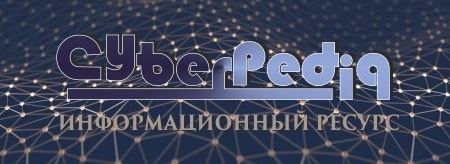
Состав сооружений: решетки и песколовки: Решетки – это первое устройство в схеме очистных сооружений. Они представляют...
Таксономические единицы (категории) растений: Каждая система классификации состоит из определённых соподчиненных друг другу...
Топ:
Проблема типологии научных революций: Глобальные научные революции и типы научной рациональности...
Оснащения врачебно-сестринской бригады.
Марксистская теория происхождения государства: По мнению Маркса и Энгельса, в основе развития общества, происходящих в нем изменений лежит...
Интересное:
Средства для ингаляционного наркоза: Наркоз наступает в результате вдыхания (ингаляции) средств, которое осуществляют или с помощью маски...
Что нужно делать при лейкемии: Прежде всего, необходимо выяснить, не страдаете ли вы каким-либо душевным недугом...
Аура как энергетическое поле: многослойную ауру человека можно представить себе подобным...
Дисциплины:
![]() |
![]() |
5.00
из
|
Заказать работу |
|
|
ВВЕДЕНИЕ
Системное проектирование – это дисциплина, определяющая подсистемы, компоненты и способы их соединения, задающая ограничения, при которых система должна функционировать, выбирающая наиболее эффективное сочетание людей, машин и программного обеспечения для реализации системы.
Оно строится как итеративный процесс, содержащий несколько циклов. Каждый последующий цикл осуществляется на более высоком информационном уровне, чем предыдущий, что обеспечивается использованием информации, накопленной в предыдущем цикле. В число циклов проектирования входят технико-экономическое обоснование, эскизное проектирование, техническое проектирование, разработка конструкторской документации.
В своем полном развитии (т.е. наличие в комплексе программ инженерных расчетов и программ выбора того или иного проектного решения по исходным данным) уже представляет систему проектирования с достаточной степенью автоматизации, причем этот показатель с развитием системы будет все время повышаться.
Системное проектированиеозначает также постоянное совершенствование системы управления качеством продукции. В этом отношении целесообразно иметь в виду следующие перспективы: переход от нормативных систем к автоматизированным системам, построенным на нормативной базе.
Целью данной курсовой работы является, продемонстрировать, как при помощи САПР программ можно спроектировать 3D модели деталей, цех для их производства, сделать расчеты и различные симуляции.
ГЛАВА 1. РАЗРАБОТКА ТЕХНИЧЕСКОГО ЗАДАНИЯ (ТЗ) НА ПРОЕКТИРОВАНИЕ УЗЛА И ТЕХНОЛОГИИ ИЗГОТОВЛЕНИЯ
Техническое задание (ТЗ) – первая стадия разработки любого изделия. Является одним из исходных документов для разработки изделия и документации на него. Составляется на основе технических требований заказчика (заказа – заявки), а также результатов научно-исследовательских и экспериментальных работ, научного прогнозирования, анализа передовых достижений и технического уровня отечественной и зарубежной техники, создания документации (конструкторской, технологической, программной и т. д.) и её состав, а также специальные требования.
|
В данной курсовой работе на рисунке 1 представлен общий 3D вид передней стойки шасси без основных деталей.
Рис. 1 Сборка передней стойки шасси
ТЗ является:
1. спроектировать не достающие детали;
2. выбрать материал, произвести теоретический прочностной расчет, и на основе его, проверить в CAE модуле.
3. разработать конструкторскую документацию;
4. разработать маршрут технологических операций изготовления деталей;
5. проектировка участка металлообрабатывающего цеха.
Область применения
Основной задачей в авиастроении является уменьшение массы летательного аппарата, дабы добиться его максимальной грузоподъемности и дальности полета. Шасси предназначены только для передвижения самолета на земле. За прототип проектирования передней стойки шасси был взят американский легко турбовинтовой самолет Beechcraft King Air B200 (Рис. 1.1.1).
Рис. 1.1.1 самолет Beechcraft King Air B200
Выбрав прототип самолета и наглядно увидев его носовую опору, можно сделать вывод, что в данной курсовой работе предоставлена 3D сборка передней стойки шасси (Рис. 1.1.2) без следующих механизмов:
- механизма поворота колеса, состоящего из 2 – х деталей (А);
- механизма уборки шасси, состоящего из 1 – й детали (Б).
На рисунке 1.1.2, прозрачными областями (А, Б) представлены границы проектирования, поэтому при их эскизном проектировании, габариты не должны выходить за ее границы.
Рис. 1.1.2 Сборка передней стойки шасси
Исходные данные и начальные расчеты
|
Смоделировав 3D модели деталей (см. п. 3.2), посчитаем нагрузки, воздействующие на них.
Основной нагрузкой на носовую опору, в ходе ее работы, действует массовая нагрузка , кг.
Выбрав прототип самолета, который имеет массу G = 40011 Н, определим теперь нагрузку, приходящуюся на переднюю стойку по формуле:
(4.1.1)
где:
a – расстояние от центра тяжести самолета до оси передней стойки, м (Рис. 4.1.1);
b – расстояние от центра тяжести самолета до оси основной стойки, м (Рис. 4.1.1).
Рис. 4.1.1 Элементарная схема самолета
Крутящий момент Мкр, действующий на детали передней стойки рассчитывается по следующей формуле:
(4.1.2)
где:
Fтр – сила трения резиновой покрышки о асфальт, Н;
l1 – расстояние от точки контакта до оси штока основного гидроцилиндра передней стойки, м.
Сила трения Fтр рассчитывается по следующей формуле:
(4.1.3)
где:
µ - коэффициент трения резины и сухого асфальта.
Нарисуем упрощенную схему детали «Рычаг управления» (см. Рис. 4.1.2) для нахождения силы, действующая на ее вовремя эксплуатации.
Рис. 4.1.2 Упрощенная схема детали «Рычаг управления»
Разобьем схема на простейшие составляющие: на участок «а» и участок «b».
Рассмотрим отдельно участок «b» (Рис. 4.1.3) и нарисуем силы, действующие на него.
Рис. 4.1.3 Схема участка «b»
PΔx – сила реакции опоры (заделка), действующая на деталь находится, как произведение продольной силы P, которая действует на деталь при повороте, на синуса угла α = 630, и умноженная на плечо l.
Сумма моментов на данном участки находится как:
Зная крутящий момент и угол, определим продольная силу P, действующую на деталь по формуле:
(4.1.4)
Теперь рассмотрим отдельно участок «а» (4.1.4) и нарисуем силы, действующие на него.
Рис. 4.1.4 Схема участка «а»
Сумма всех сил на данном участке будет находится как:
Определим поперечную силу Q, зная продольную силу P, по следующей формуле:
(4.1.5)
Рассмотренная в пункте элементарная схема детали, и проведя теоретический расчет нагрузок, действующие на них, были оптимизированы конструкции деталей и разработаны чертежи (Приложение 1), для последующего инженерного расчета в CAE модуле пакета прикладных программ SIMENS NX Simulation.
|
ГЛАВА 5. ПРОВЕРОЧНЫЕ ИНЖЕНЕРНЫЕ РАСЧЕТЫ И УТОЧНЕНИЯ ТРЕБОВАНИЙ К ДЕТАЛЯМ
Начальным этапом является проверка конструкций изделий на прочность, на котором определяются действующие на них силы. Главная задача – подобрать наиболее подходящие материалы и размеры для элементов конструкции таким образом, чтобы они могли надежно выдерживать те нагрузки, которые будут действовать на них во время эксплуатации.
Расчет был проведен в программном пакете SIEMENS NX Simulation. Данный пакет дает возможность провести множество инженерных расчетов. Для работы потребовался статический расчет перемещения, напряжения и деформации деталей при их взаимодействии в сборочной единице.
Анализ был начат с задачи деталям им определенных свойств и ограничений, это было сделано, чтобы максимально приблизить работу изделий к реальным условиям.
К деталям был подобран материал, из которого они будут изготавливаться. Им является Сталь 65Г ГОСТ 1577-93, так эта сталь используется для рессорно – пружинных изделий, которая может работать в условиях ударных нагрузок. Далее в пункте «Крепления», была задана поверхность, которая обеспечивает неподвижность детали в сборочной единице. Затем используется параметр «Внешние нагрузки», в котором указываются поверхности, на которые будут воздействовать силы. Завершительным этапом было построение сетки, а также задание тех зон, в которых сетку требуется уплотнить для более точного рассмотрения воздействия нагрузок на детали.
Проведение статического анализа проводилось на детали «Рычаг управления». Первым результатом является показатель напряжения (Рис. 5.1), возникающее в каждой ячейке сетки. Он варьируется в пределах от 1,420е+0,02 – 2,466е+0,08 Н/м2, что находится в пределах границ, отмеченных зеленым цветом.
Рис. 5.1 Результаты напряжения
Вторым результатом является показатель результирующего перемещения (Рис. 5.2), возникающее в каждой ячейке сетки. Он варьируется в пределах от 0,000е+0,00 – 2,073е+0,00 мм, что соответствует допустимым значениям.
|
Рис. 5.2 Результаты результирующего перемещения
Третьим результатом является показатель эквивалентной деформации (Рис. 5.3), возникающее в каждой ячейке сетки. Он варьируется в пределах от 1,454е-0,09 – 9,536е-0,04 мм, что соответствует допустимым значениям.
Рис. 5.3 Результаты эквивалентной деформации
Таким образом, результаты проведенной симуляции показали отсутствие критических показателей напряжения, перемещения и деформации. Это говорит о правильности проведения проектного функционального расчета детали и выбранного материала для ее изготовления.
Проведя прочностной расчет спроектированных деталей и убедившись в том, что данные схемы и геометрические особенности деталей, а также выбранный материал полностью удовлетворяет конструкции сборки (см. Рис. 5.4), можно сделать вывод, что данные детали могут применяться для дальнейшего производств в авиастроении.
Рис. 5.4 Окончательный вид сборки шасси с деталями
Рис. 8.2 Общий вид 5 – и координатного фрезерного станка DMU 60 P duoBLOCK
Основные технические характеристики указаны в таб. № 2:
Макс. ход по оси X | 600 мм |
Макс. ход по оси Y | 700 мм |
Макс. ход по оси Z | 600 мм |
Макс. нагрузка на стол | 700 кг |
Диаметр стола | 630 мм |
Угол поворота стола по оси Z | 3600 |
Макс. высота заготовки | 850 мм |
Частота вращения в стандартном исполнении | 12 000 об/мин |
Макс. частота вращения (опция) | 24 000 об/мин |
Мощность (длительность включения 100 %) | 19 кВт |
Крутящий момент (длительность включения 100 %) | 82 Нм |
Вместимость инструментального магазина | 40 позиций |
Макс вместимость инструментального магазина | 123 позиций |
Ускоренный ход по оси X | 60 м/мин |
Ускоренный ход по оси Y | 60 м/мин |
Ускоренный ход по оси Z | 60 м/мин |
Таблица № 2
ЗАКЛЮЧЕНИЕ
В данной курсовой работе произведено проектирование недостающих узлов, деталей готовой сборочной единицы с помощью САПР. По данной сборке произведен анализ непосредственно недостающих узлов, их приблизительные габариты, расположение на сборке, для полноценного функционирования. Так же предусмотрено конструкционное проектирование деталей, выбор материала заготовки и расчет на прочность. Расчет показал актуальность выбора геометрии детали и материала. Для подтверждения выбора геометрии детали произведена симуляция прочностного расчета полученной заготовка при помощи программного обеспечения SIEMENS NX SIMULETION. Результат проработки показал положительные результаты, деталь после воздействия на нее нагрузок не разрушается и сохраняет свои эксплуатационные свойства, что в свою очередь подтверждает правильность выбранной геометрии детали.
После проектирования конструкции деталей, проведения расчетов проектной функциональности и их проверки, произведена полная разработка рабочей конструкторской документации, включая окончательную сборку, полной спецификации и разработанных недостающих узлов, пошаговых маршрутных технологических процессов изготовления деталей и формирование структуры технологического оснащения тех. процессов с обоснованием выбора парка оборудования для производства и качественного инструмента для обработки, необходимого для изготовления заданных деталей с минимальными издержками.
|
На основании вышеизложенного, можно сделать вывод о том что с помощью конструкторского и технологического проектирования недостающих узлов и сборок в современном производстве представляется возможным производить разработку деталей с помощью САМ проектирования, не применяя многочисленные ручные расчеты и испытания, что в свою очередь сокращает время на изготовления потенциально новых, доработанных деталей, а так же снижает их себестоимость, что является перспективным и основополагающим при инновационной разработки в российском и мировом производстве.
СПИСОК ЛИТЕРАТУРЫ
1. Афанасьев, Александр Сергеевич. Системное проектирование конструкций и технологий изготовления изделий ответственного назначения / А. С. Афанасьев, К. М. Иванов, И. Г. Воронцова; БГТУ "ВОЕНМЕХ". - Электрон. текстовые дан. - СПб.: [б. и.], 2011. - 1 эл.
2. NX Advanced Simulation. Инженерный анализ / П. С. Гончаров [и др.]. - М.: ДМК Пресс, 2012. с. 497-498.
3. Основы NX CAM / П. А. Ведмидь. - М.: ДМК Пресс, 2012.
4. Серебреницкий П. П. Краткий справочник технолога – машиностроителя / В. М. Андрианов, Д. А. Игнатенко, К. М. Иванов. С – Пб: Политехника, 2007 г.
5. Евсеев Л.А., Миронов К.В., Фомичёв П.А. «Расчёт шасси самолёта на прочность». Харьков 1998 г.
6. Каталог Walter. Инструментальная оснастка. [Электронный ресурс]// 2012. URL: http://walter-tools.su/doc/walter-polnyy-katalog-instrumenta-2012.html (Дата обращения: 10.12.2018)
7. Каталог Walter.Твердосплавные сверла и развертки. [Электронный ресурс]// 2012. URL: http://walter-tools.su/doc/walter-dopolnitelnyy-katalog-instrumenta-2013-god.html (Дата обращения: 11.12.2018)
8. Каталог Walter. Фрезерование. [Электронный ресурс]// 2012. URL: https://www.walter-tools.com/ru-ru/search/pages/default.aspx (Дата обращения: 11.12.2018)
Приложение 1
Приложение 2
Приложение 3
ВВЕДЕНИЕ
Системное проектирование – это дисциплина, определяющая подсистемы, компоненты и способы их соединения, задающая ограничения, при которых система должна функционировать, выбирающая наиболее эффективное сочетание людей, машин и программного обеспечения для реализации системы.
Оно строится как итеративный процесс, содержащий несколько циклов. Каждый последующий цикл осуществляется на более высоком информационном уровне, чем предыдущий, что обеспечивается использованием информации, накопленной в предыдущем цикле. В число циклов проектирования входят технико-экономическое обоснование, эскизное проектирование, техническое проектирование, разработка конструкторской документации.
В своем полном развитии (т.е. наличие в комплексе программ инженерных расчетов и программ выбора того или иного проектного решения по исходным данным) уже представляет систему проектирования с достаточной степенью автоматизации, причем этот показатель с развитием системы будет все время повышаться.
Системное проектированиеозначает также постоянное совершенствование системы управления качеством продукции. В этом отношении целесообразно иметь в виду следующие перспективы: переход от нормативных систем к автоматизированным системам, построенным на нормативной базе.
Целью данной курсовой работы является, продемонстрировать, как при помощи САПР программ можно спроектировать 3D модели деталей, цех для их производства, сделать расчеты и различные симуляции.
ГЛАВА 1. РАЗРАБОТКА ТЕХНИЧЕСКОГО ЗАДАНИЯ (ТЗ) НА ПРОЕКТИРОВАНИЕ УЗЛА И ТЕХНОЛОГИИ ИЗГОТОВЛЕНИЯ
Техническое задание (ТЗ) – первая стадия разработки любого изделия. Является одним из исходных документов для разработки изделия и документации на него. Составляется на основе технических требований заказчика (заказа – заявки), а также результатов научно-исследовательских и экспериментальных работ, научного прогнозирования, анализа передовых достижений и технического уровня отечественной и зарубежной техники, создания документации (конструкторской, технологической, программной и т. д.) и её состав, а также специальные требования.
В данной курсовой работе на рисунке 1 представлен общий 3D вид передней стойки шасси без основных деталей.
Рис. 1 Сборка передней стойки шасси
ТЗ является:
1. спроектировать не достающие детали;
2. выбрать материал, произвести теоретический прочностной расчет, и на основе его, проверить в CAE модуле.
3. разработать конструкторскую документацию;
4. разработать маршрут технологических операций изготовления деталей;
5. проектировка участка металлообрабатывающего цеха.
Область применения
Основной задачей в авиастроении является уменьшение массы летательного аппарата, дабы добиться его максимальной грузоподъемности и дальности полета. Шасси предназначены только для передвижения самолета на земле. За прототип проектирования передней стойки шасси был взят американский легко турбовинтовой самолет Beechcraft King Air B200 (Рис. 1.1.1).
Рис. 1.1.1 самолет Beechcraft King Air B200
Выбрав прототип самолета и наглядно увидев его носовую опору, можно сделать вывод, что в данной курсовой работе предоставлена 3D сборка передней стойки шасси (Рис. 1.1.2) без следующих механизмов:
- механизма поворота колеса, состоящего из 2 – х деталей (А);
- механизма уборки шасси, состоящего из 1 – й детали (Б).
На рисунке 1.1.2, прозрачными областями (А, Б) представлены границы проектирования, поэтому при их эскизном проектировании, габариты не должны выходить за ее границы.
Рис. 1.1.2 Сборка передней стойки шасси
ГЛАВА 2. ЭСКИЗНОЕ ПРОЕКТИРОВАНИЕ УЗЛОВ
Эскизное проектирование является один из этапов, в котором выполняются расчеты и эскизные чертежи, которые должны содержать принципиальные конструкторские решения. На этом этапе в соответствии с ГОСТ 2.119 – 73, который включает в себя совокупность конструкторских документов, содержащих принципиальные конструкторские решения и разработки общих видов (компоновок), дающих представление об устройстве разработанного изделия, принципа его действия, габаритах и основных параметров. На этом этапе производятся основные расчеты работоспособности и надежности разработанной конструкции изделия, выбираются или рассчитываются параметры проектируемых процессов.
В данной курсовой работе для создания чертежей, моделирования 3D моделей деталей, а также проведение различных прочностных расчетов с симуляцией использовались такие пакеты прикладных программ как: SolidWorks Simulation, SIEMENS NX, КОМПАС – 3D.
2.1 Разработка 3D компоновочной схемы и определение требований к геометрии, свойствам деталей
Для того чтобы соединить гидравлические цилиндры управления с главной колесной опорой и штоком, нам потребуется две детали сложной геометрической формы, так как шток основного цилиндра стойки во время посадки сжимается, а вовремя взлета происходит его разжатие, поэтому они между собой должны двигаться и иметь достаточное расстояние, зависящее от длины выдвижения штока. Таким образом, при эскизном 3D проектировании, нам необходимо в первую очередь учесть геометрические особенности деталей.
При эскизном 3D проектировании механизма уборки шасси, будет использоваться элементарные геометрические параметры, так как на рис.1 показано, что главная колесная опора будет закреплена с корпусом основного цилиндра стойки жестко.
Назовем и обозначим на рисунке 2.1.1 проектирующиеся детали:
1. Рычаг управления;
2. Складывающийся подкос;
3. Посадочный рычаг.
Основными геометрическим параметром «Рычага управления» является межосевое расстояние между штоками гидроцилиндров, установленных на корпусе основной стойки, равное 360 мм и его длина до соединения со складывающимся подкосом.
Основными геометрическим параметром «Складывающегося подкоса» является его длина, которая зависит, на какую величину будет выдвигаться шток основной стойки шасси. Возьмем длину, равной 600 мм. Также расстояние в проеме колесной опоры в месте крепления штока с деталью, равное 170 мм и расстояние проема, для крепления с рычагом управления.
Основными геометрическим параметром «Посадочного рычага» является межосевое расстояние между креплением на корпусе основной стойки и колесной опорой. Он равно 218 мм.
На рисунке 2.1.1 представлены элементарные 3D модели деталей на 1 этапе проектирования.
Рис. 2.1.1 Эскиз 3D моделей в сборе
|
|
Биохимия спиртового брожения: Основу технологии получения пива составляет спиртовое брожение, - при котором сахар превращается...
Археология об основании Рима: Новые раскопки проясняют и такой острый дискуссионный вопрос, как дата самого возникновения Рима...
Двойное оплодотворение у цветковых растений: Оплодотворение - это процесс слияния мужской и женской половых клеток с образованием зиготы...
Папиллярные узоры пальцев рук - маркер спортивных способностей: дерматоглифические признаки формируются на 3-5 месяце беременности, не изменяются в течение жизни...
© cyberpedia.su 2017-2024 - Не является автором материалов. Исключительное право сохранено за автором текста.
Если вы не хотите, чтобы данный материал был у нас на сайте, перейдите по ссылке: Нарушение авторских прав. Мы поможем в написании вашей работы!