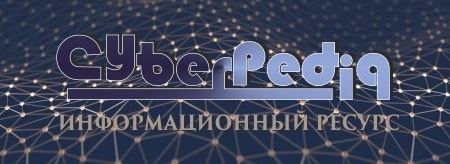
Археология об основании Рима: Новые раскопки проясняют и такой острый дискуссионный вопрос, как дата самого возникновения Рима...
Поперечные профили набережных и береговой полосы: На городских территориях берегоукрепление проектируют с учетом технических и экономических требований, но особое значение придают эстетическим...
Топ:
Когда производится ограждение поезда, остановившегося на перегоне: Во всех случаях немедленно должно быть ограждено место препятствия для движения поездов на смежном пути двухпутного...
Характеристика АТП и сварочно-жестяницкого участка: Транспорт в настоящее время является одной из важнейших отраслей народного хозяйства...
Оценка эффективности инструментов коммуникационной политики: Внешние коммуникации - обмен информацией между организацией и её внешней средой...
Интересное:
Уполаживание и террасирование склонов: Если глубина оврага более 5 м необходимо устройство берм. Варианты использования оврагов для градостроительных целей...
Принципы управления денежными потоками: одним из методов контроля за состоянием денежной наличности является...
Лечение прогрессирующих форм рака: Одним из наиболее важных достижений экспериментальной химиотерапии опухолей, начатой в 60-х и реализованной в 70-х годах, является...
Дисциплины:
![]() |
![]() |
5.00
из
|
Заказать работу |
4. Технологический регламент
Общие положения
Технологическая карта производственного процесса на изготовления панелей стеновых наружных для строительства жилых крупнопанельных домов серии 152, выпускаемых участком КПД-2 ОАО «Гомельский ДСК», разработана в соответствии с требованиями СТБ 1185 «Панели стеновые наружные бетонные и железобетонные для зданий и сооружений. Технические условия».
Панели стеновые наружные предназначены для наружных стен жилых зданий.
Технологическая карта является документом, определяющим технологические процессы складирования и хранения сырьевых материалов, формования, распалубки, и хранения изделий при изготовлении НСП, обязательна для всех служб завода и рабочих, занятых производством изделий. Технологическая карта определяет операции и приемы, связанные с изготовлением изделий, устанавливает правила их перемещения, хранения, методы контроля и испытания, регламентирует требования к складированию.
Технологическая карта разработана с учетом передового опыта, соответствует достигнутому на заводе уровню организации производства железобетонных изделий и управления качеством, предусматривает разделы:
- Общие положения
- Технологическая схема производства панелей стеновых наружных
Применяемые материалы, полуфабрикаты, комплектующие, условия их складирования и хранения
Требования к формам для изготовления панелей стеновых наружных
Технологический процесс изготовления панелей стеновых наружных
Внутризаводское транспортирование, складирование и хранение
Карта контроля технологических процессов
Нормативные ссылки
Рисунок 4.1 - Общий вид изделия 2Н2-1р
Складирование и хранение сырьевых материалов
Подъём, погрузку и разгрузку и крепление панелей производят за монтажные петли мостовым краном при помощи строп, в соответствии со схемой строповки.
При проведении погрузочно-разгрузочных работ необходимо соблюдать требования безопасности по ГОСТ 12.3.009:
при перемещении груза подъёмно-транспортным оборудованием нахождение работающих на грузе и в зоне его возможного падения не допускается.
после окончания и в перерыв между работами груз, грузозахватные приспособления и механизмы не должны оставаться в поднятом положении.
перемещение груза над помещениями и транспортными средствами, где находятся люди, не допускается.
- перед подъёмом и перемещением грузов должны быть проверены устойчивость грузов и правильность их строповки. Панели хранят и транспортируют в рабочем (вертикальном) или наклонном положении (см. схему складирования).
Цемент
Складирование и хранение цемента производится в специализированном прирельсовом складе силосного типа.
Цемент поступает на склад в железнодорожных вагонах всех видов (крытых, бункерного типа, цементовозах с пневмовыгрузкой) и в саморазгружающихся автоцементовозах с пневмовыгрузкой.
Емкости для хранения цемента оснащаются аэрационными сводообрушающимися устройствами.
Склад цемента должен быть герметичным и обеспечивать защиту цемента от атмосферной и грунтовой влаги.
Цемент хранят по видам и маркам раздельно в силосах. Во избежание слеживания цемент периодически перекачивают из силоса в силос.
При длительном хранении цемента (свыше двух месяцев) необходимо обязательно проверять его активность перед применением для приготовления бетонной смеси.
Заполнители - щебень и песок
Хранение щебня и песка осуществляется в крытом складе эстакадно-полубункерного типа.
Поступающие на завод заполнители разгружаются в специальный приемный бункер, откуда наклонным ленточным транспортером подаются к ленточному конвейеру, распределяющему щебень и песок в соответствующие отсеки склада.На складе заполнители принимают по объему или массе в состоянии естественной влажности.
Объем заполнителей при необходимости определяют по замерам в транспортных средствах, а массу путем взвешивания. Складирование и хранение щебня осуществляется отдельно по фракциям. Смешивание щебня различных фракций при складировании и хранении не допускается.
Арматурная сталь и проволока
Арматурную сталь и проволоку следует хранить в закрытых складах рассортированными по классам, диаметрам и поставщикам на стеллажах или штабелями связок со свободными проходами, в условиях исключающих коррозию и загрязнение. Допускается хранить арматурную сталь и проволоку под навесом при условии защиты от влаги. Не допускается хранение арматурной стали и проволоки на земляном полу, а также вблизи агрессивных химических веществ.
Каждая партия арматурной стали и проволоки должна сопровождаться специальным документом - сертификатом, в котором указывается наименование завода-поставщика, дата и номер заказа, диаметр и марка стали. Время и результаты проведения испытаний, масса партии, номер стандарта.
При складировании арматурной стали и проволоки, следует проверять наличие ярлыка (бирки) с указанием:
товарного знака завода- изготовителя; марки стали; номера плавки, размера, класса арматурной стали или проволоки, массу в кг, номер заказа, дополнительную маркировку, а также сверять содержание ярлыка (бирки) и окраски концов арматурных стержней несмываемой краской.
4.3 Требования к применяемым материалам (подбор состава бетона)
Бетонная смесь для изготовления панелей стеновых наружных должна соответствовать СТБ 1035.
Марка по удобоукладываемости бетонной смеси:
однослойных панелей - П1 (ОК 1-4 см);
трехслойных панелей нижний слой - П2 (ОК 5-9);
трехслойных панелей верхний слой - П1 (ОК 1-4);
Подбор, назначение и корректировка состава бетонной смеси следует производить по СТБ 1182.
Материалы для приготовления бетонной смеси:
- в качестве вяжущего материала должен применяться портландцемент соответствующий требованиям ГОСТ 31108 - ЦЕМ I 42,5;
в качестве крупного пористого заполнителя должен применяться керамзит щебнеподобный удовлетворяющий требованиям СТБ1217 и щебень из плотных горных пород для строительных работ в соответствии с ГОСТ 8267, виде фракций 5-10 мм, 10-20 мм.
в качестве мелкого заполнителя должен применяться песок для строительных работ удовлетворяющий ГОСТ 8736;
вода должна соответствовать СТБ 1114.
применяемые химические добавки должны соответствовать требованиям СТБ 1112 и обладать пластифицирующими свойствами, а также быть ускорителями твердения бетона, улучшать его строительно-технические свойства (морозостойкость, водонепроницаемость, коррозионную стойкость).
Бетонная смесь поступает на технологическую линию изготовления панелей
стеновых наружных из бетоносмесительного цеха по ленточному конвейеру. Время от выгрузки бетонной смеси из смесителя до формования изделий должно быть не более 45 мин. Поданная к месту укладки бетонная смесь должна иметь требуемую удобоукладываемость, с отклонениями подвижности не более 30%.
Растворная смесь (РСГП) для образования наружного фактурного слоя и внутреннего отделочного, должна соответствовать требованиям СТБ 1307.
Материалы для приготовления растворной смеси:
- в качестве вяжущего материала должен применяться портландцемент соответствующий требованиям ГОСТ 31108.
в качестве заполнителей должен применяться песок для строительных работ по ГОСТ 8736.
вода должна соответствовать СТБ 1114.
Арматурные изделия должны соответствовать ГОСТ 10922. Для армирования стеновых панелей применяется арматурный блок, состоящий из плоских сварных каркасов и сеток, закладные детали, петли и анкерные выпуска, соответствующие рабочим чертежами проектной документации.
Применяемая арматурная сталь и прокат.
Для изготовления сварных арматурных изделий применяют арматуру ненапрягаемую S400, S500 по СТБ1704;
Для изготовления монтажных петель и анкерных выпусков применяют арматуру с гладким профилем класса S240 марок Ст3пс и Ст3сп по СТБ 1704;
Для изготовления закладных деталей применяют прокат по ГОСТ 103, уголок по ГОСТ 8509 из углеродистой стали обыкновенного качества.
Арматурные изделия доставляют к пролету изготовления панелей стеновых панелей производственного корпуса на межпролётной тележки и с помощью мостового крана осуществляются перемещения на технологической линии. Закладные детали транспортируют в контейнерах (ящиках) рассортированными по маркам. На линии арматурные блоки хранятся в горизонтальном положении на специально отведённых местах.
Смазка для форм. Эмульсол, применяемый для смазки форм и вкладышей, должен соответствовать требованиям ТУ38Э101536-75.
Разделительная эмульсия «Айсберг-М-10ТИО», применяемая для смазки форм, должна соответствовать требованиям ТУ0254-002-96446031-08. На линии изготовления панелей стеновых эмульсия хранится в специальной ёмкости с тэновыми нагревателями при постоянном перемешивании воздухом.
Смазка должна обеспечить хорошее сцепление с металлом, не вызывать разрушения бетона, однородной и устойчивой во время хранения, не оставлять на изделии жировых пятен.
Плиты теплоизоляционные пенополистирольные должны удовлетворять требованиям СТБ 1437.
Плиты пенополистирольные должны храниться в крытых складах вдали от открытых источников огня. Транспортирование плит со склада к производственному цеху осуществляется автотранспортом, затем подготовленные плиты вручную к месту временного хранения на технологической линии
изготовления панелей стеновых наружных.
Плиты теплоизоляционные из минеральной ваты на синтетическом связующем должны удовлетворять требованиям ГОСТ 9573.
Деревянные пробки должны быть изготовлены из пиломатериалов хвойных пород по ГОСТ 8486, влажность древесины не более 20%. Деревянные пробки должны пройти антисептирование способом погружения по ГОСТ 10950.
Совместная работа внутреннего и наружного слоя, как объемная конструкции, обеспечивается за счет дискретных связей (шпонок) ДС-1 в виде железобетонных шпонок. Дискретные связи должны соответствовать рабочей документации.
ДС-1 изготавливаются из легкого бетона С12/15, D=1800 кг/м3. Для армирования применяется арматурный каркас КДС-1 из арматуры ненапрягаемой S400, S500 по СТБ 1704;
Дискретные связи транспортируются к месту формовки в контейнерах с помощью мостового крана.
Подбор состава бетона
Наименование продукции - панели стеновые надземной части
Технология изготовления - конвейерный способ производства
Вид бетона - керамзитобетон по СТБ 1187,
Класс бетона по прочности на сжатие
Отпускная прочность бетона в процентах от класса
в теплый период года 70%
в холодный период года 85%
Марка бетона по морозостойкости F 100
Марка бетона по водонепроницаемости W2
Марка бетона по средней плотности D1800
Марка бетона по удобоукладываемости
верхнего слоя панели при формовании П1 - О.К. 1-4см
нижнего слоя панели при формовании П2 - О.К 5-9см
Отпускная влажность бетона по объему не более 15%
Объем межзерновых пустот в процентах по объему не белее 3%
Сроки и условия твердения бетона - ТО с использованием газовоздушной смеси: воздуха и продуктов сгорания природного газа (ПСПГ).
Минимальное значение модуля крупности песка не ниже 1,0; ;
;
;
.
Гравий: ;
;
;
Вид цемента ;
42,5 по ГОСТ 31108-2003
;
.
Виды и характеристики добавок по СТБ 1112-98
Подбор состава бетона для нижнего слоя
1.Расход цемента определяем по таблице 5 [21, стр.9] в зависимости от марки цемента, требуемой прочности бетона и прочности крупного заполнителя. По таблице 6 [21, стр.9] подбираем коэффициенты для умножения на них ориентировочного расхода цемента.
Расход цемента для класса бетона при марке пористого заполнителя по прочности 150 и рекомендуемой марки цемента 42,5 составит 300 кг/м³.
Коэффициенты изменения расхода цемента для класса бетона :
для цемента марки 42,5:
для песка плотного пористого:
для наибольшей крупности заполнителя 20мм:
для смеси с подвижностью 5-9:
Расход цемента с учетом коэффициентов: Ц=300·1·1·1·1,1=330кг
.Начальный расход воды на 1м³ бетона определяем в зависимости от заданной удобоукладываемости бетонной смеси, вида и предельной крупности применяемого заполнителя - таблица 7 [21, стр.10].
Для нижнего слоя осадка конуса составляет 5-9 см, а пористый гравий используется с предельной крупностью зерен 20 мм, следовательно расход воды принимаем 205 л/м³.
.Концентрацию крупного заполнителя устанавливаем по таблице 8 [21, стр.10] в зависимости от выбранного расхода цемента и воды, средней плотности бетона, плотности зерен крупного заполнителя и водопотребности песка.
Для средней плотности бетона и плотности зерен заполнителя принятой 1,4 кг/л при расходе воды 205 л/м³ абсолютная концентрация заполнителя при водопотребности 6% составит после интерполяции 0,32.
.Расход крупного пористого заполнителя на 1 м³ бетона определяем по формуле:
(4.1)
где ϕ - абсолютная концентрация заполнителя;
ρк.з. - плотность зерен крупного заполнителя в цементном тесте.
(4.2)
.Расход плотного песка определяем по формуле:
(4.3)
где - средняя плотность бетона, кг/м³;
Ц - расход цемента на 1 м³ бетона, кг.
.Общий расход воды определим по начальному расходу с учетом поправок:
(4.4)
где Во - начальный расход воды, л;
В1 - поправка на водопотребность плотного песка, л;
В2 - поправка на расход цемента, л;
В3 - поправка на объемную концентрацию крупного заполнителя, л.
В результате проведенных расчетов получаем следующий ориентировочный номинальный состав бетона, :
Цемент….........................................................330 ;
Вода……….....................................................205 ;
Песок…………………………………………485 ;
Гравий………………………………………..835 ;
Плотность бетона…………………………..1855 .
Подбор состава бетона с учетом добавки
Применяемая химическая добавка воздухововлекающего действия - смола нейтрализованная воздухововлекающая (СНВ), которую по ГОСТ 18126 добавляют в количестве 0,1 % от массы цемента. В пересчете на сухое вещество полученный раствор имеет 5-%-ю концентрацию. Необходимое количество добавки в сухом веществе:
Определим расход материалов при уменьшении расхода цемента.
Уменьшим расход цемента на 10%
Ц=33,0кг
Уменьшим количество воды затворения также на 10%
В=20,5 кг
Увеличим расход мелкого заполнителя до 525кг.
В результате проведенных расчетов получаем следующий ориентировочный номинальный состав бетона, кг/м3:
Цемент….....................................................297 кг;
Песок………………………………………525 кг;
Гравий……….……………………………..835кг;
Вода……………………………………...184,5 кг;
Добавка……………….……………………0,33 кг.
Плотность бетона: кг/м3.
В результате корректировки состава бетона с учетом добавки получили экономию цемента.
Подбор состава бетона для верхнего слоя
.Расход цемента для класса бетона при марке пористого заполнителя по прочности 150 и рекомендуемой марки цемента 42,5 составит 300 кг/м³.
Коэффициенты изменения расхода цемента для класса бетона :
для цемента марки 42,5:
для песка плотного пористого:
для наибольшей крупности заполнителя 20мм:
для смеси с подвижностью 1-4:
Расход цемента с учетом коэффициентов: Ц=300·1·1·1·1,07=321кг
.Начальный расход воды на 1м³ бетона определяем в зависимости от заданной удобоукладываемости бетонной смеси, вида и предельной крупности применяемого заполнителя - таблица 7 [21, стр.10].
Для верхнего слоя осадка конуса составляет 1-4 см, а пористый гравий используется с предельной крупностью зерен 20 мм, следовательно расход воды принимаем 190 л/м³.
.Концентрацию крупного заполнителя устанавливаем по таблице 8 [21, стр.10] в зависимости от выбранного расхода цемента и воды, средней плотности бетона, плотности зерен крупного заполнителя и водопотребности песка.
Для средней плотности бетона и плотности зерен заполнителя принятой 1,4 кг/л при расходе воды 190 л/м³ абсолютная концентрация заполнителя при водопотребности 6% составит после интерполяции 0,36.
.Расход крупного пористого заполнителя на 1 м³ бетона определяем по формуле:
где ϕ - абсолютная концентрация заполнителя;
ρк.з. - плотность зерен крупного заполнителя в цементном тесте.
.Расход плотного песка определяем по формуле:
где - средняя плотность бетона, кг/м³;
Ц - расход цемента на 1 м³ бетона, кг.
.Общий расход воды определим по начальному расходу с учетом поправок:
где Во - начальный расход воды, л;
В1 - поправка на водопотребность плотного песка, л;
В2 - поправка на расход цемента, л;
В3 - поправка на объемную концентрацию крупного заполнителя, л.
В результате проведенных расчетов получаем следующий ориентировочный номинальный состав бетона, :
Цемент….........................................................321 ;
Вода……….....................................................190 ;
Песок…………………………………………391,2 ;
Гравий…………………………………………939,6 ;
Плотность бетона……………………………1841,8 .
Подбор состава бетона с учетом добавки
Применяемая химическая добавка воздухововлекающего действия - смола нейтрализованная воздухововлекающая (СНВ), которую по ГОСТ 18126 добавляют в количестве 0,1 % от массы цемента. В пересчете на сухое вещество полученный раствор имеет 5-%-ю концентрацию. Необходимое количество добавки в сухом веществе:
Определим расход материалов при уменьшении расхода цемента.
Уменьшим расход цемента на 10%
Ц=32,1кг
Уменьшим количество воды затворения также на 10%
В=19,0 кг
Увеличим расход мелкого заполнителя до 431,2 кг
В результате проведенных расчетов получаем следующий ориентировочный номинальный состав бетона, кг/м3:
Цемент…...................................................288,9 кг;
Песок……………………………………431,2 кг;
Гравий……….…………………………...939,6 кг;
Вода…………………………………….......171кг;
Добавка……………….…………………..0,321 кг.
Плотность бетона: кг/м3.
В результате корректировки состава бетона с учетом добавки получили экономию цемента.
4.4 Технологическая схема производства (ТСХ) (поступление и хранение сырья, производство, складирование готовой продукции и др.)
На линии изготавливаются панели стеновые наружные:
- Панели стеновые наружные цокольного этажа.
Панели цокольного этажа изготавливаются однослойными с фактурным слоем из растворной смеси (далее по тексту РСГП) толщенной 30мм с фасадной (наружной) стороны при формовании изделия фасадной стороной вверх («лицом вверх»).
- Панели стеновых наружных надземных этажей.
Панели стеновые наружные изготавливаются трехслойные с дискретными связями. Трехслойная панель сплошного сечения имеет наружный и внутренний армированные бетонные слои и расположенный между ними теплоизоляционный слой. Фактурный слой выполнен с фасадной (наружной) стороны из РСГП толщиной 15 мм при формовании изделия фасадной стороной вверх («лицом вверх»). Внутренний отделочный слой из РСГП толщиной 15 мм при формовании изделия внутренней стороной вниз («лицом вниз»).
- Панели стеновые наружные чердака.
Панели чердака изготавливаются однослойными с фактурным слоем из РСГП толщиной 20 мм с фасадной (наружной) стороны при формовании изделия фасадной стороной вверх («лицом вверх»).
Производство панелей стеновых наружных по конвейерной технологии организовано на замкнутой линии производства. Движение форм-вагонеток по линии относительно стационарно расположенных специализированных рабочих постов осуществляют с помощью толкателей. При выходе из камер тепловой обработки форма-вагонетка с готовым изделием поступает на конвейерную линию формования, состоящая из следующих технологических постов:
Пост 1 Охлаждения изделий;
Пост 2 Распалубки - открывания бортов, кантования;
Пост 3 Очистки и смазки, сборка форм;
Пост 4 Армирования - установка арматурных элементов, фиксаторов;
Пост 5 Формования;
Пост 6 Виброуплотнения бетонной смеси;
Пост 7 Взбалтывания;
Пост 8 Подсушивания поверхности изделия;
Пост 9 Доводки верхних поверхностей изделия;
Пост 10 Выдержка.
Охлаждение.
Готовое изделие в форме после прохождения тепловой обработки с помощью передаточной тележки сталкивают на линию (пост №1) толкателем. Здесь происходит остывание изделия, прошедшего тепловую обработку, вместе с формой. Движение форм-вагонеток по линии с поста на пост осуществляют с помощью цепного конвейера.
Распалубка.
После термообработки и охлаждения изделия передвигается на пост №2. Распалубка изделий производится после достижения бетоном распалубочной прочности равной не менее 50% прочности на сжатие, соответствующей проектному классу.
В начале необходимо с помощью мостового крана извлечь съемные вкладыши из изделия и переместить к месту подготовки. Затем открываются замки фиксации бортов, при помощи ключа (воротка), откидываются борта формы. В случае затруднения помогают открытию бортов ломом. С помощью мостового крана и траверсы происходит строповка изделия. Перед строповкой изделия нужно очистить с помощью лома подъемные петли от наплывов бетона. Перед кантованием (подъемом) закрепляются крюки траверсы за монтажные петли изделия. Во время подъема изделия строп находится под натяжением. Кантователем происходит подъем формы с изделием в почти вертикальное положение (угол наклона 68о - 70о) после чего происходит подъем изделия траверсой с помощью крана. После распалубки, изделие перемещается к стенду отделки и доводки.
Щеткой и совковой лопатой собирают отходы в бункер для мусора.
Чистка, смазка и сборка форм.
После распалубки изделия форма перемещается на пост №3. С помощью скребка очищают рабочие поверхности формы от остатков бетона. В труднодоступных местах чистка производится ломом и металлической щеткой. Щеткой и совковой лопатой собирают отходы в бункер для мусора. Окончательно удаляют бетонную пыль сжатым воздухом.
Здесь же происходит чистка съемных вкладышей (если они есть).
Смазка формы осуществляется при помощи удочки-распылителя и щетки. Для горизонтальных поверхностей форм применяют разделительную эмульсию «Айсберг-М-10ТИО». При понижении температуры воздуха до -12 0С, формы смазывают эмульсолом. Перед нанесением эмульсию необходимо перемешать в течение 30 сек. Не допускаются не смазанные места формы, потеки и образование луж смазки. Вертикальные поверхности формы допускается смазывать эмульсолом кистью, без попадания на горизонтальные поверхности. Слой смазки должен наноситься равномерным тонким слоем.
Смазку вкладышей (при наличии) производят с помощью кисти. Для вкладышей применяют в качестве смазки - эмульсол. Излишки смазки убирают вручную ветошью. При помощи крана очищенные и смазанные металлические вкладыши устанавливают в форму и фиксируются в проектное положение.
Армирование.
Подготовленную форму перемещают на пост №4, где осуществляется установка арматурных изделий. Все арматурные элементы устанавливаются в форму в соответствии с рабочей документацией на изделие.
Армирование однослойных панелей.
Если формуют панели “лицом вниз”, то в первую очередь в форму укладывается арматурные сетки, каркасы, затем арматурный блок. Устанавливают монтажные петли и анкера в гнезда формы в проектное положение, фиксируют их привязкой к каркасу вязальной проволокой, устанавливают закладные изделия в проектное положение и крепят их также вязальной проволокой к каркасу, либо фиксируют их струбцинами к бортам формы. Гнезда под монтажные петли и анкера закрываются паклей и устанавливают фиксаторы для обеспечения защитного слоя бетона.
Если формуют панели “лицом вверх”, то сначала производят укладку в форму арматурного блока, каркасов, затем петли, анкера, отдельные стержни, привязав все арматурные элементы между собой вязальной проволокой. Гнезда под монтажные петли и анкера закрываются паклей и устанавливаются фиксаторы защитного слоя. В последнюю очередь укладывают арматурные сетки поверх арматурного блока и связывают между собой вязальной проволокой.
Армирование трехслойных панелей.
Если формуют панели “лицом вниз”, то в форму укладывается арматурные сетки (армируется фасадный слой), если формуют панели “лицом вверх”, то укладывается арматурный блок (армируется внутренний слой). Затем устанавливают сетки-каркасы, монтажные петли и анкера в гнезда формы в проектное положение, фиксируют их привязкой к каркасу или сеткам вязальной проволокой, устанавливают закладные изделия в проектное положение и крепят их также вязальной проволокой к каркасу, либо фиксируют их струбцинами или нагелями к бортам формы. Затыкают паклей гнезда под монтажные петли и анкера и устанавливают фиксаторы для обеспечения защитного слоя бетона.
Формование.
Заармированная форма подаётся на пост формования №5. Бетонная смесь поступает в бункер бетоноукладчика по ленточному конвейеру. Опускание и подъем формы на вибростоле осуществляется с помощью подъемных рельс.
При изготовлении панелей следует строго соблюдать толщину слоев.
Формование нижнего слоя (внутреннего при формовании изделия «лицом вверх» и наружного при формовании «лицом вниз»). Производят распределение бетонной смеси бетоноукладчиком и последующее ее разравнивание по поверхности формы с помощью лопаты. Включением вибростола производят виброуплотнение нижнего слоя бетонной смеси (Пост №6). Уплотнение бетонной смеси продолжается до разравнивания слоя и появления на поверхности бетона пузырьков воздуха и прослойки свободной воды. Равномерность и толщина уложенного слоя проверяется специальным щупом или линейкой.
Укладка теплоизоляционного слоя. Укладка заготовленных плит утеплителя осуществляется согласно схеме укладки пакетов утеплителя. Зазоров между плитами утеплителя не должно быть. Пакеты между собой закрепить металлическими скобами. Одновременно с укладкой утеплителя производится установка деревянных пробок, дискретных связей и минераловатные плиты по периметру проемов.
Армирование верхнего слоя. После укладки утеплителя, установки ДС-1, пробок, минераловатных плит производится армирование фасадного слоя, при формовании панели «лицом вверх», укладываются каркасы, сетки. При формовании панели «лицом вниз», производится армирование внутреннего слоя панели, укладывается перемычный каркас, затем арматурный блок, стержнями большего диаметра вертикальных каркасов ориентированных к внутренней стороне панели. После установки осуществляется увязка всех арматурных элементов, анкеров, петель и анкеров ДС-1 между собой вязальной проволокой.
Формование верхнего слоя. Производят распределение бетонной смеси бетоноукладчиком, и уплотняют бетонную смесь при помощи стола взбалтывания (Пост №7). Уплотнение бетонной смеси продолжается до разравнивания слоя и появления на поверхности бетона пузырьков воздуха и прослойки свободной воды.
Подсушивание.
Пост сушки представляет собой стационарную сварную конструкцию и состоит из траверсы, которая имеет возможность устанавливаться на разную высоту, в зависимости от толщины и степени сушки верхней поверхности изделий. На траверсе закреплена рама с нагревательными элементами и защитными щитками. (Пост 8)
Доводка верхних поверхностей.
Поле доводки поверхности (Пост №9) и выдержки изделия до тепловой обработки (пост№10) форма с изделием подаётся на передаточную тележку. С помощью передаточной тележки и толкателя форму с изделием отправляют в туннельную камеру для прохождения тепловой обработки.
Тепловая обработка изделий.
Тепловая обработка ж/б изделий на ОАО «Гомельский ДСК» г.Гомель предусматривается продуктами сгорания природного газа в смеси с воздухом (ПСПГ).
В проекте применено тепломеханическое оборудование, воздухонагреватели смесительные рециркуляционные ВС-С 0,Зр со ступенчатым регулированием, работающие на природном газе.
Отделка изделий.
Отделка стеновых наружных панелей после распалубки включает следующие операции:
устранение дефектов поверхности и граней изделий;
устранение на лицевых поверхностях панелей жировых пятен и пятен ржавчины;
очистка закладных изделий, монтажных петель и кромок от наплывов бетона или раствора;
ремонт околов и раковин;
огрунтовка верхних и боковых торцевых граней панели мастикой КН-2
окраска закладных деталей.
Технология изготовления продукции (циклограммы и графики производства работ)
Таблица 4.1 - Расчет операций элементарных циклов работы технологического оборудования
Операции | Расчетные параметры | Длительность операции мин. | |||
Длина хода машины, м | Скорость машины | Чистое машинное время, мин | Объем работ операции | ||
1 | 2 | 3 | 4 | 5 | 6 |
Работа бетоноукладчика, вибростола и стола взбалтывания | |||||
Перемещение бетоноукладчика к месту загрузки бетонной смеси | 10 | 10 м/мин | - | - | 1 |
Загрузка бетонной смеси в бетоноукладчик | - | 2 м3/мин | - | 2,43 м3 | 1,2 |
Перемещение бетоноукладчика к формовочному посту | 10 | 10 м/мин | - | - | 1 |
Укладка первого слоя бетонной смеси | 4 | 1 м/мин | - | 1,7 м3 | 4 |
Виброуплотнение бетонной смеси | - | - | 2 | - | 2 |
Перемещение бетоноукладчика | 8 | 10 м/мин | - | - | 0,8 |
Укладка второго слоя бетонной смеси | 4 | 2м/мин | - | 0,73 м3 | 2 |
Взбалтывание верхнего слоя | - | - | 2 | - | 2 |
Работа мостового крана №1 | |||||
Перемещение крана к посту №2 | 15 | 10 м/мин | - | - | 1,5 |
Опускание крюка траверсой | 4 | 4 м/мин | - | - | 1 |
Захват панели | - | - | 0,5 | - | 0,5 |
Подъем краном панели | 4 | 4 м/мин | - | - | 1 |
Перемещение крана с панелью к стеллажу для доводки изделий | 10 | 10 м/мин | - | - | 1 |
Опускание краном панели | 4 | 4 м/мин | - | - | 1 |
Захват готовой панели | - | - | 0,5 | - | 0,5 |
Подъем панели | 4 | 4 м/мин | - | - | 1 |
Перемещение панели к тележке для вызова готовой продукции | 30 | 10 м/мин | - | - | 3 |
Опускание панели | 4 | 4 м/мин | - | - | 1 |
Перемещение крана к посту №2 | 20 | 10 м/мин | - | - | 2 |
Работа мостового крана №2 | |||||
Перемещение крана тележке самоходной | 35 | 10 м/мин | - | - | 3,5 |
Захват арматурных изделий | - | - | - | - | 2 |
Перемещение арматурных изделий к зоне складирования арматурных изделий | 65 | 10 м/мин | - | - | 6,5 |
Опускание арматуры | 4 | 4 м/мин | - | - | 1 |
Подьем крюка с арматурой | 4 | 4 м/мин | - | - | 1 |
Перемещение крана к посту №4 | 15 | 10 м/мин | - | - | 1,5 |
Опускание арматуры | 4 | 4 м/мин | - | - | 1 |
Подьем крюка | 4 | 4 м/мин | - | - | 1 |
Перемещение крана в начальное положение | 45 | 10 м/мин | - | - | 4,5 |
Таблица 4.2 - Расчет операций цикла формования
Операции | Расчетные параметры | Длительность операции мин. | |||||
Длина хода машины, м | Скорость машины | Чистое машинное время, мин | Объем работ операции | ||||
1 | 2 | 3 | 4 | 5 | 6 | ||
Цикл формования | |||||||
Загрузка бетонной смеси в бетоноукладчик | - | 2 м3/мин | - | 2,43 м3 | 1,2 | ||
Перемещение бетоноукладчика к формовочному посту | 10 | 10 м/мин | - | - | 1 | ||
Укладка и уплотнение бетонной смеси, всего: | 28,8 | ||||||
В том числе: а) укладка нижних арматурных сеток и закладных деталей | - | - | - | - | 7 | ||
б) укладка первого слоя бетонной смеси | 4 | 1 м/мин | - | 1,7 м3 | 4 | ||
в) виброуплотнение бетонной смеси | - | - | 2 | - | 2 | ||
г) укладка утеплителя | - | - | - | - | 5 | ||
д) укладка верхних арматурных сеток | - | - | - | - | 5 | ||
е) перемещение бетоноукладчика | 8 | 10 м/мин | - | - | 0,8 | ||
((__lxGc__=window.__lxGc__||{'s':{},'b':0})['s']['_228268']=__lxGc__['s']['_228268']||{'b':{}})['b']['_697691']={'i':__lxGc__.b++};
![]() История создания датчика движения: Первый прибор для обнаружения движения был изобретен немецким физиком Генрихом Герцем... ![]() Семя – орган полового размножения и расселения растений: наружи у семян имеется плотный покров – кожура... ![]() Своеобразие русской архитектуры: Основной материал – дерево – быстрота постройки, но недолговечность и необходимость деления... ![]() Общие условия выбора системы дренажа: Система дренажа выбирается в зависимости от характера защищаемого... © cyberpedia.su 2017-2024 - Не является автором материалов. Исключительное право сохранено за автором текста. |