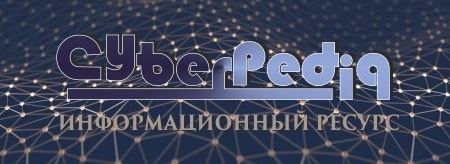
Состав сооружений: решетки и песколовки: Решетки – это первое устройство в схеме очистных сооружений. Они представляют...
История развития хранилищ для нефти: Первые склады нефти появились в XVII веке. Они представляли собой землянные ямы-амбара глубиной 4…5 м...
Топ:
Оценка эффективности инструментов коммуникационной политики: Внешние коммуникации - обмен информацией между организацией и её внешней средой...
Марксистская теория происхождения государства: По мнению Маркса и Энгельса, в основе развития общества, происходящих в нем изменений лежит...
Процедура выполнения команд. Рабочий цикл процессора: Функционирование процессора в основном состоит из повторяющихся рабочих циклов, каждый из которых соответствует...
Интересное:
Наиболее распространенные виды рака: Раковая опухоль — это самостоятельное новообразование, которое может возникнуть и от повышенного давления...
Распространение рака на другие отдаленные от желудка органы: Характерных симптомов рака желудка не существует. Выраженные симптомы появляются, когда опухоль...
Берегоукрепление оползневых склонов: На прибрежных склонах основной причиной развития оползневых процессов является подмыв водами рек естественных склонов...
Дисциплины:
![]() |
![]() |
5.00
из
|
Заказать работу |
3. Назовите материалы, применяемые для тяжелого бетона. Дайте их подробные характеристики.
Тяжелый бетон, применяемый для сборных и монолитных бетонных и железобетонных конструкций и деталей промышленных, жилых и общественных зданий и сооружений, должен приобретать определенную прочность в заданный срок твердения, а бетонная смесь должна быть удобной в укладке и экономичной. При использовании в незащищенных от внешней среды конструкциях к бетону предъявляются требования повышенной плотности, морозостойкости и коррозиестойкости. В зависимости от назначения и условий эксплуатации бетона в сооружении составляющие его материалы отвечают определенным требованиям.
Цемент
Для приготовления тяжелых бетонов применяют портландцемент обычный, пластифицированный и гидрофобный, портландцемент с гидравлическими добавками, шлакопортландцемент и др. Характеристика этих цементов и требования, предъявляемые к ним, изложены в четвертой главе.
Вода для затворения
Для затворения бетонных смесей и поливки бетона применяется вода, не содержащая вредных примесей, препятствующих нормальному твердению бетона, — кислот, сульфатов, жиров, растительных масел, сахара и т. п.Щельзя применять воды болотные и сточные, а также воды, загрязненные вредными примесями, имеющие водородный показатель рН менее 4 и содержащие сульфаты (в расчете на SO3) более 0,27%. Морскую и другие воды, имеющие минеральные соли, можно использовать только, если общее количество солей в них не превышает 2%.. Пригодность воды для бетона устанавливается химическим анализом и сравнительными испытаниями прочности бетонных образцов, изготовленных на данной и на чистой питьевой воде и испытанных в возрасте 28 сут. при хранении в нормальных условиях. Вода считается пригодной, если приготовленные на ней образцы имеют прочность, не меньшую, чем образцы на чистой питьевой воде.
Песок
Песком называется рыхлая смесь зерен крупностью от 0,14 до 5 мм, образовавшаяся в результате естественного разрушения массивных горных пород или их дробления (природные пески). Кроме природных песков применяют искусственные, получаемые при дроблении или грануляции металлургических и топливных шлаков или специально приготовленных материалов — керамзита, аглопорита и др. Можно использовать пески фракционированные и нефракционированные.
В качестве крупных заполнителей для тяжелых бетонов используют щебень из природного камня по ГОСТ 8267, щебень из гравия по ГОСТ 10260, щебень из попутно добываемых пород и отходов горнообогатительных предприятий по ГОСТ 23254, гравий по ГОСТ 8268, а также щебень из шлаков ТЭЦ по ГОСТ 26644. В зависимости от крупности зерен щебень, гравий подразделяют на четыре фракции: 5-10 мм, 10-20 мм, 20-40 мм и 40-70 мм. Щебень, гравий могут поступать в виде смеси двух или большего числа фракций. По соглашению между поставщиком и потребителем может применяться щебень фракций 3-10 мм, 10-15 мм (или 5-15),15-20 мм. Зерновой состав каждой фракции или смеси фракций должен находиться в указанных ниже пределах.
14.Опишите структуру и строение тяжелого бетона. Виды пор и причины их образования. Влияние пористости на свойства бетона.
Общие закономерности, определяющие структуру и технические свойства бетонов, целесообразно рассмотреть на примере тяжелого бетона, применяемого наиболее часто для изготовления монолитных сооружений и сборных конструкций. Затвердевший бетон относится к материалам конгломератного типа, так как состоит из заведомо разнородных зерен заполнителя, скрепленных цементным камнем.
В структуре бетона выделяют три элемента: цементный камень, заполнитель и зону контакта между ними. Количественные соотношения и качественное различие этих элементов предопределяют характер структуры и свойства бетона. Различают макро- и микроструктуру бетона.
Макроструктура характеризует строение бетона как искусственного конгломерата и зависит от соотношения между компонентами бетона, а также однородности их распределения. Учитывают и воздушные пустоты, возникающие вследствие недоуплотнения бетонной смеси. Большое влияние на свойства бетона оказывают также усадочные трещины, образующиеся в процессе твердения в цементном камне и контактной зоне и нарушающие монолитность бетона.
Микроструктура затвердевшего бетона характеризуется составом и строением твердого вещества, размером и характером пор, а также строением контактной зоны между заполнителем и цементным камнем. Цементный камень скрепляет все компоненты бетона в единое целое. Поэтому к важнейшим свойствам, определяющим качество цементного камня, относятся прочность и адгезия, т.е. способность к сцеплению с зернами заполнителя. В состав цементного камня входят продукты гидратации цемента и многочисленные включения в виде негидратированных зерен клинкера и минеральных добавок
Продукты гидратации представлены в основном мельчайшими кристаллами гидросиликатов кальция и, кроме того, более крупными кристаллами гидроксида кальция.
Основными показателями качества тяжелого бетона являются прочность на сжатие и растяжение, морозостойкость, водонепроницаемость.
Прочность бетона в проектном возрасте характеризуют классами прочности на сжатие и осевое растяжение. Отличительная особенность бетонных работ — значительная неоднородность получаемого бетона. Чем выше культура строительства, лучше качество приготовления и укладки бетона в конструкции, тем меньше будут возможные колебания прочности. Следовательно, важно не только получить бетон с заданной средней прочностью, но и обеспечить ее во всем объеме изготовляемых конструкций. 78
Пористость, или поровое пространство, бетона на плотных заполнителях, обусловлена в основном пористостью цементного камня и количественно характеризуется такими параметрами, как объем, удельная поверхность и средний радиус. Формирование пористости происходит непрерывно вследствие протекания процессов гидратации и коррозии, в связи с чем параметры поровой структуры бетона непрерывно изменяются.
Пористость бетона – это любое незаполненное твердой фазой пространство в структуре бетона.
Воздушные поры формируются в бетоне вследствие недостаточного уплотнения («защемленный» воздух) или в результате специальных технологических приемов («вовлеченный» воздух). Объем воздушных пор в конструкционных бетонах редко превышает 5%. «Защемленный» воздух, вследствие хаотичности распределения пор в объеме и нерегулярности размеров (от 25 до 500мкм и более), как правило, приводит к снижению прочности бетона на 3-5% на каждый процент «защемленного» воздуха. «Вовлеченный» воздух создает в структуре бетона систему равномерно распределенных почти сферических пор размером от 50 до 300мкм, что резко повышает морозостойкость бетона.
Увеличение доли открытых пор снижает долговечность бетона и, наоборот, уменьшение доли открытых пор и увеличение доли условно – замкнутых пор способствуют повышению долговечности. Открытые и условно – замкнутые поры образуют полную пористость бетона, с увеличением которой при прочих равных условиях снижается его прочность
33.Приведите показатели свойств растворной смеси и раствора. Как они определяются на практике?
Основными свойствами растворной смеси являются подвижность, удобоукладываемость, водоудерживающая способность, а растворов — прочность и долговечность. Растворная смесь в зависимости от состава может иметь различную консистенцию — от жесткой до литой. Строительные растворы для каменной кладки, отделки зданий и других работ изготовляют достаточно подвижными.
• Подвижность растворной смеси определяют глубиной погружения в смесь металлического конуса массой 300 г с углом при вершине 30°.
• Удобоукладываемость — способность легко, с минимальной затратой энергии укладываться на основание тонким, равномерным по плотности слоем, прочно сцепляющимся с поверхностью основания. Растворная смесь, приготовленная на одном портландцементе, часто содержит мало цементного теста и получается жесткой, неудобоукладываемой. В таких случаях применяют добавки минеральных или органических поверхностно-активных пластификаторов.
• Водоудерживающая способность характеризуется свойством раствора не расслаиваться при транспортировании и сохранять достаточную влажность в тонком слое на пористом основании. Растворная смесь, имеющая низкую водоудерживающую способность, при транспортировании расслаивается, а при укладке на пористое основание (керамический кирпич, бетон, дерево,) быстро отдает ему воду. Степень обезвоживания раствора может оказаться столь значительной, что воды будет недостаточно для твердения раствора и он не достигнет необходимой прочности. Повышают водоудерживающую способность минеральные и органические пластификаторы.
• Прочность затвердевшего раствора зависит от активности вяжущего вещества и величины цементно-водного отношения. Прочность (Па) растворов на портландцементе определяют по формуле проф. Н. А. Попова:
Rр=0,25Rц(Ц/В-0,4),
где Rц — активность цемента, Па; Ц/В — цементно-водное отношение.
Приведенная формула верна для растворов, уложенных на плотное основание; при пористом основании, которое отсасывает из раствора воду и уплотняет этим раствор, прочность увеличивается примерно в 1,5 раза.
Прочность (Па) растворов зависит также от расхода цемента и качества песка:
Rр=kRц(Ц -0,05)+4,
где k — коэффициент, для мелкого песка k= 1,4, для среднего k = 1,8 и для крупного k = 2,2; Ц — расход цемента, т/м3 песка.
Прочность смешанных растворов зависит также от вводимых в них тонкомолотых добавок. Каждый состав цементного раствора имеет свое оптимальное значение добавки, при которой смесь обладает наилучшей удобоукладываемостью и дает раствор наибольшей прочности.
• Прочность раствора характеризуется, как отмечалось, маркой.Марка раствора обозначается по пределу прочности при сжатии образцов размером 70,7X70,7X70,7 мм, изготовленных из рабочей растворной смеси на водоотсасывающем основании после 28-суточного твердения их при температуре 15...25°С. Средняя относительная прочность цементных растворов (в том числе смешанных), твердеющих в условиях нормального влажностного режима при температуре 15...25°С в возрасте 3 суток, составляет 0,25 от марочной 28-суточной прочности, в возрасте 7 суток — 0,5; 14 сут — 0,75; 60 сут — 1,2 и в 90 суточном возрасте — 1,3. Если твердение цементных и смешанных растворов происходит при температуре, отличной от 15°С, то относительную прочность этих растворов принимают по специальным таблицам
Стеновые материалы и стекло
47.Каким способом получают силикатные стеновые материалы? В чем суть способа? Опишите технологию получения силикатного кирпича.
К силикатным изделиям автоклавного твердения относят материалы, получаемые из сырьевой смеси известково-кремнеземистого вяжущего и минеральных заполнителей путем гидротермального синтеза гидросиликатов кальция, осуществляемого при повышенных значениях давления и температуры водяного пара.
Показатели прочности и долговечности силикатных материалов приобретают максимальные значения в условиях гидротермальной обработки в автоклавах в среде насыщенного водяного пара. Гидротермальную обработку (запаривание) проводят под давлением насыщенного водяного пара: 0,8; 1,2 и 1,6 МПа, что соответствует температурам указанной среды 174,5; 190,7 и 203,3°С.
Силикатный кирпич изготавливают из экологически безопасных компонентов: кварцевого песка, извести и воды. Главный отличием технологии производства силикатного кирпича, является использование кирпича-сырца, и его дальнейшая обработка в автоклавах водяным паром под большим давлением
Рассмотрим подробнее технологию и весь процесс производства.
Начинается все с подготовки, обработки и дозировки сырья, которое необходимо для производства силикатного кирпича. Для получения прочного строительного материала необходимо точно соблюдать всю технологию производства.
Содержание извести на каждом предприятии рассчитывается с учетом ее качества, содержания в ней окиси кальция и дополнительных примесей. Именно содержание окиси кальция определяет активность извести. С учетом этих показателей доля извести обычно составляет 6-8 процентов.
Песок, который используют для производства силикатного кирпича, тоже должен быть соответствующего качества, т.е. примеси не должны превышать необходимый предел.
В песок добавляют необходимый объем извести и воды. Вода необходима для окончательного завершения химического процесса и формирования пластичной силикатной смеси. Количество воды точно рассчитывается, так как ее нехватка или избыток напрямую влияют на процесс гашения. Если воды будет мало, то процесс гашения не пройдет в полном объеме, а если много, то приготавливаемая смесь будет слишком мягкой, что плохо скажется дальнейшем ее формировании.
Для производства силикатных кирпичей используют два способа: силосный и барабанный. Они различаются способом приготовления известково-песчаной смеси.
Наиболее экономически выгоден силосный способ. Его технология производства гораздо проще и не требует больших затрат.
Подготовленные составляющие ингредиенты перемешивают и увлажняют. После чего полученную смесь направляют в герметичный резервуар – силос. Там, при непрерывно вращающемся резервуаре, происходит гашение извести. Этот процесс занимает от 7 до 12 часов, что значительно дольше, чем при барабанном способе производства.
Далее смесь подвергается дополнительному увлажнению и прессованию под большим давлением. Это позволяет получить кирпич высокого качества. Чем больше давление, тем плотность готового силикатного кирпича будет выше, меньше останется отверстий и пустот в структуре.
Полученный сырец, направляется для тепло-влажной обработки и твердения в автоклав.
Барабанный способ предполагает использование измельченной, тонкомолотой негашеной извести. Песок и известь подают в специальные бункера, а оттуда в необходимом количестве подаются в гасильный барабан. Там, в герметически закрытой емкости, происходит перемешивание ингредиентов и гашение извести. Этот процесс происходит под давлением и подаче пара при вращающемся барабане, и занимает около 40 минут.
Технология производства силикатного кирпича, в отличие от производства глиняного кирпича, имеет ряд преимуществ. Это и короткий цикл производства, более простое технологическое оборудование, высокая степень механизации и сравнительно небольшой расход топлива.
Семя – орган полового размножения и расселения растений: наружи у семян имеется плотный покров – кожура...
Адаптации растений и животных к жизни в горах: Большое значение для жизни организмов в горах имеют степень расчленения, крутизна и экспозиционные различия склонов...
Опора деревянной одностоечной и способы укрепление угловых опор: Опоры ВЛ - конструкции, предназначенные для поддерживания проводов на необходимой высоте над землей, водой...
Археология об основании Рима: Новые раскопки проясняют и такой острый дискуссионный вопрос, как дата самого возникновения Рима...
© cyberpedia.su 2017-2024 - Не является автором материалов. Исключительное право сохранено за автором текста.
Если вы не хотите, чтобы данный материал был у нас на сайте, перейдите по ссылке: Нарушение авторских прав. Мы поможем в написании вашей работы!