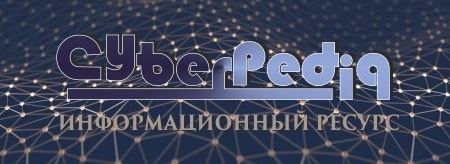
Индивидуальные очистные сооружения: К классу индивидуальных очистных сооружений относят сооружения, пропускная способность которых...
Биохимия спиртового брожения: Основу технологии получения пива составляет спиртовое брожение, - при котором сахар превращается...
Топ:
Определение места расположения распределительного центра: Фирма реализует продукцию на рынках сбыта и имеет постоянных поставщиков в разных регионах. Увеличение объема продаж...
Установка замедленного коксования: Чем выше температура и ниже давление, тем место разрыва углеродной цепи всё больше смещается к её концу и значительно возрастает...
Методика измерений сопротивления растеканию тока анодного заземления: Анодный заземлитель (анод) – проводник, погруженный в электролитическую среду (грунт, раствор электролита) и подключенный к положительному...
Интересное:
Что нужно делать при лейкемии: Прежде всего, необходимо выяснить, не страдаете ли вы каким-либо душевным недугом...
Распространение рака на другие отдаленные от желудка органы: Характерных симптомов рака желудка не существует. Выраженные симптомы появляются, когда опухоль...
Наиболее распространенные виды рака: Раковая опухоль — это самостоятельное новообразование, которое может возникнуть и от повышенного давления...
Дисциплины:
![]() |
![]() |
5.00
из
|
Заказать работу |
|
|
МЕТОДИЧЕСКИЕ УКАЗАНИЯ №2
ПО ВЫПОЛНЕНИЮ ЛАБОРАТОРНЫХРАБОТ №12-24
ПО УЧЕБНОЙ ДИСЦИПЛИНЕ
«ТЕХНИЧЕСКАЯ ЭКСПЛУАТАЦИЯ АВТОМОБИЛЕЙ»
Специальность: 2-37 01 06 “Техническая эксплуатация автомобилей”
(по направлениям)
Квалификация специалиста: Техник-механик
Разработчик: ____________А.Е.Будько, преподаватель
Рассмотрено
на заседании ПЦК
протокол №5
от 18.01.2016 г.
Председатель ПЦК ____________ Н.В.Козлова
Перечень лабораторных работ
по учебной дисциплине «Техническая эксплуатация автомобилей»
Лабораторная работа №12
Диагностирование, техническое обслуживание и текущий ремонт двойных главных передач.
Лабораторная работа №13
Проверка эффективности работы подвески. Проверка и регулировка углов установки управляемых колес.
Лабораторная работа №14
Выполнение вулканизации камер, ремонт автомобильных покрышек.
Лабораторная работа №15
Проведение экспертизы автомобильных шин и составление рекламаций.
Лабораторная работа №16
Диагностирование, техническое обслуживание и текущий ремонт тормозной системы с гидравлическим приводом.
Лабораторная работа №17
Диагностирование, техническое обслуживание и текущий ремонт тормозной системы с пневматическим приводом
Лабораторная работа №18
Диагностирование и техническое обслуживание стояночных тормозных систем.
Лабораторная работа №19
Техническое обслуживание свечей зажигания и прерывателя-распределителя.
Лабораторная работа №20
Техническое обслуживание и текущий ремонт генератора и стартера
Лабораторная работа №21
Проверка и регулировка направления света фар. Устранение неисправностей внешних световых приборов.
|
Лабораторная работа №22
Диагностирование двигателя с помощью мотор-тестера.
Лабораторная работа №23
Изучение технологического процесса диагностирования автомобиля на станции диагностики.
Лабораторная работа №24
Определение удельного расхода топлива, токсичности отработавших газов.
Лабораторная работа №12
Тема программы: «Техническое обслуживание и текущий ремонт трансмиссии».
Тема работы: «Диагностирование, техническое обслуживание, текущий ремонт двойных главных передач».
Цель работы: изучить устройство главной передачи автомобиля МАЗ 5551, научиться диагностировать главную передачу, научиться регулировать главную передачу.
Оборудование: ключ гаечный, люфтомер КИ-4832, подъемник, предельный ключ, динамометрический ключ, шайбы регулирования, автомобиль МАЗ 5551, стенд, КИ-4872, стенд для закрепления главных передач, съемники, плакаты.
Последовательность выполнения работы
Теоретическая часть
Главная передача служит для передачи крутящего момента от карданной передачи на полуоси заднего моста. Главная передача представляет собой одноступенчатый редуктор с конической спиральной парой шестерен и межколесным коническим деффиринциалом.
Детали центрального редуктора монтируются в картере, изготовленного из ковкого чугуна. Редуктор устанавливается в окне балки заднего моста и крепится к ней при помощи шпилек. Ведущая шестерня изготовлена за одно с валом, имеет 12 зубьев, установлена на 3-х роликовых подшипниках: двух конических и цилиндрических. Между внутренними обоймами конических подшипников имеется распорное кольцо и регулировочная шайба, толщина которой подбирается таким образом чтобы обеспечивался необходимый преднатяг в подшипниках. В распорке средней перегородки картера редуктора устанавливается цилиндрический роликовый подшипник ведущей конической шестерни. На шлицах шестерни устанавливается маслоотражательная шайба и фланец. Ведомая коническая шестерня с помощью заклепок крепиться к чашке дифференциала. Для предотвращения деформации ведомой шестерни в картере редуктора установлен ограничительный болт. Между фланцем картера подшипников и картером редуктора установлен набор регулировочных прокладок различной толщины для регулировки зацепления конических шестерен. Дифференциал заднего моста – конической с четырьмя сателлитами и установлен на 2-ух роликовых конических подшипниках, регулировка которых осуществляется с помощью гаек. Отверстия под крестовину обрабатывается при собранных и замена производиться только комплектом колец. На крестовину устанавливается четыре сателлита и упорные сферические шайбы. В цилиндрических расточках чашек устанавливается шестерни полуосей, между шестернями и чашками устанавливается бронзовые шайбы. Полуосевые шестерни внутри имеют эвольвентные шлицы в которые входят полуоси. Для обеспечения смазки подшипников ведущей шестерни с боку в картере редуктора отлит масляной карман, который соединен каналом с подшипниками ведущей конической шестерни. Масло, находящееся в кармане захватывается зубьями шестерни и забрасывается в масленый карман, а оттуда самотеком поступает по каналу к подшипникам и через специальный паз отводиться назад в картер редуктора.
|
Масло для смазки зубьев и опорных поверхностей шестерни дефферинциала поступает из картера моста через окна в лапках дефферинциала. В двух отверстиях лашки установлены маслосборники, способствующие улучшению смазки дифференциала. Конические шестерни редуктора перед сборкой прикатывается и подается в паре.
Уход за редуктором заднего моста заключается в поддержании необходимого уровня и своевременной смене смазки в картере, проверке уплотнений и подтяжке всех болтовых соединений.
В большинстве случаев неисправности редуктора можно легко обнаружить при систематическом наблюдении за его работой, так как они сопровождаются появлением нагрева, стуков и излишних шумов. Повышенный нагрев может иметь место при работе нового редуктора, при работе под большими нагрузками, при продолжительном буксовании автомобиля, а также недостаточном или излишнем количеством смазки, слишком тугим зажатием подшипников качения, отсутствием необходимых зазоров в зацеплении шестерен или между поверхностями трения. Повышенный шум может возникать в случае плохой регулировки зацепления зубьев конических шестерен. Продиагностировать главную передачу можно на автомобиле, стоящем на смотровой канаве. Для этого необходимо установить автомобиль на смотровую канаву, оборудованную стендами КИ-4872. Выполнить операцию диагностирования главной передачи согласно следующей схеме: установить автомобиль на смотровой канаве чтобы ведущий мост был над подъемником, поднять ведущий мост подъемником, запустить двигатель, при 600-800 оборотах коленчатого вала. Прослушать стетоскопом работу главной передачи. Заглушить двигатель.
|
Стуки и резкий шум при работе главной передачи не допускается. Проверить суммарный угловой зазор в главной передаче. Рычаг переключения передач установить в нейтральное положение. Затормозить задние колеса определить суммарный угловой зазор при помощи прибора КИ-4832. Он должен быть не больше максимально допустимого. Далее необходимо снять главную передачу с заднего моста автомобиля используя съемники, сняв главную передачу установить ее на стенд. Затем изучить работу главной передачи.
Практическая часть
1. Проверка регулировочных параметров с последующей регулировкой. Проверка предварительного натяга подъемников. Регулировка подшипников ведущей шестерни производится путем уменьшения толщины регулировочной шайбы с обеспечением предварительного натяга 0,03-0,05 мм, при этом величина момента, необходимого для проварачивания вала ведущей шестерни в подшипниках должна быть равна 0,1-0,2 кгм. И так для регулировки необходимо разобрать стояночный тормоз и снять суппорт с картера. Слить масло, отвернуть гайки шпилек крепления картера подшипников ведущей шестерни и с помощью демонтажных болтов вынуть картер с ведущей конической шестерней в сборке. Закрепив картер в тисках определить индикатором осевой люфт подшипников. Зажать ведущую коническую шестерню в тисках. Отвернуть гайку фланца, снять шайбу и фланец. Снять маслоотражатель, внутреннее кольцо переднего подшипника и регулировочную шайбу. Замерить толщину регулировочной шайбы и рассчитать до какой величины необходимо уменьшить ее для устранения осевого люфта и получения предварительного натяга. Установить требуемую шайбу и другие детали, кроме крышки с сальником, которую ставить не следует, так как трение сальника о шейку фланца не позволит точно измерить момент. Проварачивания шестерен в подшипниках. Проверить предварительный натяг подшипников по величине момента проварачивания ведущей шестерни. Определить момент, можно динамометрическим ключом на гайке.
|
2.Проверка затяжки подшипников дифференциала осуществляется с помощью гаек, которые нужно заворачивать с обеих сторон на одинаковую глубину до получения предварительного натяга в подшипниках предварительный натяг должен походить в пределах 0,2-0,3 кгм (при снятой ведущей шестерне). Ограничительный болт заворачивается сначала до упора в шестерню, а затем отворачивается на 1/10 оборота, что соответствует зазору между ними 0,17-0,2 мм, после чего стопориться контргайкой. В картер главной передачи заднего моста заливается масло трансмиссионное автотранспортное летнее или зимнее в зависимости от сезона эксплуатации. Предварительный натяг подшипников определяется величиной момента, требуемого для поворота дифференциала, который должен быть в пределах 0,2-0,3кгм. Этот момент определяется динамометрическим ключом.
3.Проверка и регулировка зацепления конических шестерен следующий. Насухо протирают зубья конических шестерен и смазывают 3,4 зуба ведущей шестерни тонким слоем краски по всей их поверхности. Устанавливают в картер редуктора картер с ведущей шестерней, завертывают гайки на четыре накреслежащих шпильки и поворачивают за фланец ведущую шестерню. По отпечаткам (пятнам контакта), полученные на зубьях ведомой шестерни, устанавливают правильность зацепления шестерен и характер регулировки зацепления. Регулируют зацепление изменением количества прокладок под фланцем картера подшипников ведущей шестерни и с помощью гаек, не нарушая регулировки подшипников дифференциала. Для того чтобы отодвинуть ведущую шестерню от ведомой, необходимо под фланец картера подложить дополнительно регулировочные прокладки. Для перемещения ведомой шестерни пользуются гайками, завертывая или отвертывая их на один и тот же угол. При регулировке зацепления (по пятну контакта) на зубьях шестерен сохранять боковой зазор между зубьями, величина которого у новой пары шестерен должна быть в пределах 0,2-0,5 мм. После окончания регулировки зацепления шестерен затянуть все гайки шпилек крепления картера подшипников к картеру редуктора, поставить стопоры гаек подшипников, завернуть ограничитель так, чтобы получить минимальный зазор 0,15-0,2 мм между сухарем и ведомой шестерней (мин. зазор устанавливается при повороте ведомой шестерни на один оборот). После этого ограничитель ведомой шестерни застопорить контргайкой.
|
Рабочее место № 1 (Регулировка главной передачи)
1. Установить а/м на смотровую канаву.
1.1. Поднять ведущий мост подъемником.
1.2. Запустить двигатель при 600-800 оборотах.
1.3. Прослушать стетоскопом работу главной передачи.
2. Проверить суммарный угловой зазор в главной передаче.
2.1. Затормозить задние колеса.
2.2. Определить суммарный угловой зазор при помощи прибора КИ-4832.
3. Снять главную передачу с заднего моста автомобиля, используя съемники.
4. Установить ее на стенд.
5. Проверка предварительного натяга подшипников.
5.1. Слить масло.
5.2. Отвернуть гайки шпилек крепления картера подшипников ведущей шестерни и с помощью демонтажных болтов вынуть картер с ведущей конической шестерней в сборке.
5.3. Закрепив картер в тисках, определить индикатором осевой люфт подшипников.
5.4. Зажать ведущую коническую шестерню в тисках и отвернуть гайку фланца, снять шайбу и фланец, маслоотражатель, внутреннее кольцо переднего подшипника и регулировочную шайбу.
5.5. Замерить толщину регулировочной шайбы и расчитать до какой величины необходимо уменьшить ее для установления осевого люфта и получения предварительного натяга.
5.6. Установить требуемую шайбу и другие детали.
5.7. Проверить предварительный натяг подшипников по величине момента проварачивания ведущей шестерни с помощью динамометрического ключа на гайке.
6. Проверить затяжку подшипников дифференциала.
6.1. Провернуть дифференциал динамометрическим ключем.
6.2. Проверка конических шестерен.
7. Протереть зубья шестерен.
7.1. Смазать 3 зуба ведущей шестерни тонким слоем краски по всей поверхности.
7.2. Установить в картер редуктора картер с ведущих шестерней.
7.3. Провернуть за фланец ведущую шестерню.
7.4. По отпечаткам на ведомой шестерне установить правильность зацепления шестерен.
Содержание отчета
1. Цель работы
2. Оборудование
3. Ход работы. (Результаты выполнения работы по каждому пункту)
4. Вывод (техническое заключение)
Контрольные вопросы
1. Перечислите основные неисправности главной передачи и их причины.
2. Перечислите операции, выполняемые при техническом обслуживании главной передачи.
3. Объясните последовательность операций при диагностировании главной передачи.
4. Расскажите, с помощью чего регулируют зацепление зубчатых колес и конические подшипники с повышенными износами и зазорами.
Лабораторная работа №13
Тема программы: «Техническое обслуживание и текущий ремонт ходовой части автомобиля, автомобильных шин».
Тема работы: «Проверка эффективности работы подвески. Проверка и регулировка углов установки управляемых колес».
Цель работы: Сформировать умение проверять эффективность работы подвески на стенде, проверять и регулировать углы установки управляемых колес.
Оборудование рабочего места: стенд для проверки углов установки колес автомобиля СКО-1.
Теоретическая часть
Существенную роль в повышении эффективности эксплуатации автомобилей играет оптимальная установка управляемых колес. Опыт показывает, что нередко из-за несоблюдения заданных углов установки колес снижается срок службы шин в 1,5-2 раза, а иногда и более, а так же существенно ухудшается управляемость автомобиля.
Установку колес проверяют по углам схождения и развала управляемых колес, углам продольного и поперечного наклонов оси поворота управляемых колес, по соотношению (разности) углов развала правого и левого колеса и соотношению углов поворота управляемых колес.
Ниже будет рассмотрен стенд углов установки колес СКО-1, основанный на световом излучении.
Чтобы правильно осуществить измерение углов наклона колес необходимо, чтобы колес автомобиля стояли горизонтально. Там где стоят заднее колеса автомобиля, то должен быть горизонтальным и поверхность поворотных дисков должна находиться в одной плоскости с полом.
Автомобиль должен заехать точно на поворотные риски, как можно ближе к оси их вращения, затем его ставят на ручной тормоз, контролируют давление воздуха во всех четырех шинах, если имеется предписание надо загрузить автомобиль.
На ножках опорных балок установить лапки, закрепив их разворотом канавки относительно стопорного винта на 180º. Рукояткой вращения ходового винта установить лапки по ободу колеса.
На измерительные приборы левый и правый закрепить соответственно шкалы. Опорные балки с закрепленными на их оси измерительными приборами установить последовательно на передних колесах, закрепить за бортовую закраину обода с внутренней стороны.
После этого передние колеса поднять, обеспечив их свободное вращение. Измерительные приборы подключить к источнику питания.
Далее надо совместить с опорной балки с осью вращения колеса, осуществляя коррекцию вращательного движения изменением наклона оси опорной балки при помощи трех компенсаторных винтов. Для этого на измерительном приборе корпус измерителя угла наклона легким поворотом установить в фиксированное положение перпендикулярное колесу.
Рукоятку фиксации измерительного прибора на оси опорной балки несколько ослабить. Медленно вращать колесо. Если вращательное движение колеса не в порядке, тогда световой указатель в пятне проектируемого круга на шкале перемещается вверх и вниз. Следовательно, надо закручивать либо верхний, либо нижний компенсаторный винт до тех пор, пока световой указатель не будет стремиться к неподвижному состоянию. Если невозможно отрегулировать при помощи одного винта, вращают и оба других.
Коррекция вращательного движения прекращается тогда, когда при вращении колеса световой указатель в пятне проектируемого круга находиться на шкале в одном из неподвижных положений.
И так коррекция вращательного движения с обоими световыми приборами завершена.
Производят проверку правильности установки поворотных дисков под колесами и их поправку.
Затем колеса а/м медленно опускают посередине поворотных дисков, при этом направляющие и ходовой винт опорных балок должны быть расположены вертикально, а для автомобилей с диском 12 дюймов – горизонтально.
Заблокировать передние колеса, установить тормозное приспособление на ножной тормоз. Поворотные диски на подставках зафиксировать путем извлечения штифтов. И так подготовка изделия к работе завершена и после переходим непосредственно к изменению углов установки колес.
Измерение схождения передних колес.
Установить передние колеса в направлении прямолинейного движения. Оба измерительных прибора выставить по уровню и зафиксировать относительно оси опорной балки при помощи рукоятки.
Поворотом рукоятки блока зеркала направить изображения световых указателей приборов на соответствующие шкалы закрепленные снизу на корпусах проекторов измерительных приборов.
Вершина светового указателя должна находиться на горизонтальной линии одной из шкал, которая соответствует величине обода колеса проверяемого автомобиля.
Колеса вращают пока вершина светового указателя на одной из шкал не встанет на нулевую отметку. Тогда величину общего схождения передних колес можно прямо прочитать на другой шкале.
Развал колес.
Отгоризонтировать измерительные приборы по встроенному уровню. Установить измеритель угла наклона перпендикулярно колесу и ввести фиксатор в канавку.
Установить рычажок измерителя в фиксированное положение РАЗВАЛ КОЛЕС.
Передние колеса вращают, пока оба на будут иметь одинаковое схождение.
Снимать показания величины развала колес по шкале справа.
Угол развала другого колеса обнаруживается таким же образом.
Измерение продольного и поперечного наклона оси поворота колес. Левое колесо повернуть внутрь на 20º. Установка прибора для измерения угла продольного наклона оси поворота колес показана на рисунке.
Рычажок измерителя углов наклона вывести из канавки и передвинуть в положение для измерения угла, пока стрелка в пятне проектируемого круга не установиться на нулевую отметку на шкале. После этого левое колесо повернуть наружу на 20º. Угол продольного наклона оси поворота колеса прочитать по левой шкале измерителя углов наклона.
Правое колесо измеряется аналогично. Установка прибора для измерения угла поперечного наклона оси поворота показана на рисунке.
Повернуть измеритель угла как показано на рисунке пока он не введется в канавку параллельно колесу. Левое колесо повернуть внутрь на 20º.
Ослабить винт крепления измерительного прибора к опорной балке и прибор раскачать, пока стрелка в пятне проектируемого круга не займет положение на нулевой отметке шкалы. Снова затянуть винт крепления прибора. Колесо повернуть наружу на 20º. Необходимо следить за тем, что бы настройка измерителя не менялась
Показания угла поперечного наклона оси поворота колеса считываем по левой шкале измерителя углов. На рисунке показана величина 3º положительного поперечного наклона оси поворота колеса.
Если продольный или поперечный наклон оси поворота колеса больше чем 8º, надо зафиксировать стрелку в пятне проектируемого круга не на 0, а на -3º.
Фактически угол, поэтому соответственно будет на 3º больше, чем считываемый со шкалы.
Практическая часть
Регулировка углов установки управляемых колес
1.Установить автомобиль точно на поворотные циски.
2.Затормозить а/м ручным тормозом.
3.Закрепить измерительные приборы.
3.1.Установить лапки по ободу колеса.
3.2.На измерительный прибор левый и правый закрепить шкалы.
3.3.Опорные балки с закрепленными на оси измерительными приборами установить последовательно на передних колесах.
3.4.Измерительные приборы подключить к источнику питания.
3.5.Совместить ось опорной балки, с осью вращения колеса.
3.6.Поворотные диски на подставках зафиксировать путем извлечения штифтов.
4.Измерение схождения колес.
4.1.Установить передние колеса в направлении прямолинейного движения.
4.2.Измерительные приборы выставить по уровню.
4.3.Направить изображения световые украшения приборов на шкалы.
4.4.Калеса вращают пока вершина светового указателя на шкале не встанет на нулевую отметку, и величину общего схождения снимают с другой шкалы.
5.Измерение развала колес.
5.1.Отрегулировать измерительные приборы.
5.2.Установить измеритель угла наклона перпендикулярно колесу.
5.3.Установить рычажок измерителя в положение РАЗВАЛ КОЛЕС.
5.4.Передние колеса вращают, пока оба не будут иметь одинаковое схождение.
5.5.Снимать показания величины развала колес по шкале справа.
6.Измерение продольного и поперечного наклона от поворота колес.
6.1.Левое колесо повернуть внутрь на 20º.
6.2.Установить прибор для измерения продольного наклона оси поворота колес.
6.3.Рычажок измерителя углов наклона вывести из канавки и перевернуть в положение для измерения угла, пока стрелка не станет на нулевую отметку.
6.4.Повернуть наружу левое колесо на 20º.
6.5.Угол продольного наклона прочитать по левой шкале.
6.6.Установить прибор для измерения угла поперечного наклона оси.
6.7.Повернуть измеритель угла, пока он не введется в канавку параллельно колесу.
6.8.Левое колесо повернуть внутрь на 20º.
6.9.Установить стрелку прибора на нулевую отметку.
6.10.Колесо повернуть наружу на 20º.
6.11.Угол поперечного наклона оси поворота колес считывается по левой шкале.
Содержание отчета
1. Цель работы.
2. Оборудование.
3. Ход работы. (Результаты выполнения работы по каждому пункту)
4. Вывод (техническое заключение).
Контрольные вопросы
1. Объясните влияние технического состояния ходовой части автомобиля на безопасность движения.
2. Назовите диагностические параметры и нормативы углов установки управляемых колес на грузовых, легковых автомобилях и автобусах.
3. Перечислите последовательность операции при диагностировании углов установки колес.
4. Назовите основные неисправности ходовой части.
5. Перечислите операции, выполняемые при техническом обслуживании ходовой части.
Лабораторная работа №14
Тема программы: «Техническое обслуживание и текущий ремонт ходовой части автомобиля, автомобильных шин».
Тема работы: «Выполнение вулканизации камер, ремонт автомобильных покрышек».
Цель работы: Выработать умение выполнять вулканизацию камер, ремонт автомобильных покрышек.
Оборудование рабочего места: электровулканизационный аппарат, шлифовочный круг, прослоечная камерная резина, бензин, сырая камерная резина, ножницы, ролик, кисточка, шероховальный станок, протекторная резина, пластыри, манжеты, прослоечная камерная резина, прорезиненный корд.
Теоретическая часть
Шины являются сложными и ответственными деталями автомобиля, от которых в значительной степени зависят многие эксплуатационные свойства автомобиля. Немалую роль при этом играет автомобильные камеры, которые задерживают воздух в шине, обеспечивая прочное прилегание и крепление диска колеса с покрышкой. Своевременный и качественный ремонт камер и шин способствует повышению долговечности покрышек.
Технологический процесс ремонта камер и покрышек включает в себя следующие операции: очистка и мойка, сушка, подготовка к ремонту, подготовку починочного материала, шероховку, намазку клеем, заделка, вулканизация, отделка и контроль.
Порядок выполнения.
Очистка и мойка производится в специальных моечных машинах или вручную теплой водой, при помощи жестких волосяных щеток.
Сушку производят для покрышек в течении 2...24 часа в специальных сушильных камерах, оборудованных вентиляцией при температуре 40-60ºС, или в течении 2...3 суток при комнатной температуре без специальной сушилки. Сушка является сложнейшей операцией, так как оставшаяся влага может образовать паровые мешки при вулканизации, которые приводят к расслоению каркаса.
Подготовка камеры сводиться к закреплению краев в местах разрыва (прокола). При повреждении камеры в месте установки вентиля этот участок вырезают для постановки заплаты, а для вентиля пробивают отверстие в другом месте. В местах проколов камеру не вырезают.
Подготовка поврежденных участков покрышки предусматривает удаление из покрышки инородных тел и вырезку поврежденных участков. Вырезку производят для выравнивания ремонтируемого участка и очистки его от поврежденных резины и корда. Применяют следующие способы вырезки. Наружным конусом, внутренним конусом, встречным конусом и в рамку. Контур вырезки должен быть минимален, неповрежденный материал не удовлетворяют. Края повреждения срезают под углом 45º к центру колеса. Поврежденные участки вырезают остро заточенными ножами, смоченными водой, на верстаке с применением борторасширителя, металлических вставок. После вырезки контролируют влажность каркаса в месте ремонте. Если влажность превышает установленный предел (6%), то покрышку подвергают сушке. Влажность измеряют специальным индикатором.
Подготовка починочного материала для камеры. В зависимости от размера разрыва используют сырую резину (разрывы до 30мм, проколы) или части утильных камер (разрывы более 30мм). Починочный материал шерохуют с внутренней стороны. Размер заплаты должен быть на 20-30мм больше вырезки и не достигать границы шероховки на 2...3мм. Для замены поврежденных частей камеры длинной более 500мм заготавливают из старых камер того же размера сектора; их длинна, должна быть на 80...100мм больше удаляемой части камеры. Фланцы крепления вентиля вырезают из старой камерной резины и нового чефера и собирают вместе на резиновом клее.
Подготовка починочного материала для покрышки заключается в предварительной заставке пластырей, манжет, подманжетников в форме вырезки. Манжеты подвергаются шероховке со всех сторон.
Шероховку производят для улучшения промазки ремонтируемого места резиновым клеем и увеличения поверхности контакта его с починочным материалом. Места повреждения в каркасе и брекере шерохуют дисковой проволочной щеткой, а в протекторе и боковине – фигурными шераховками, закрепленными на конце гибкого вала шероховального станка, а затем очищают пылесосом от пыли.
При шероховке каркаса во избежании повреждения корда щетка должна передвигаться вдоль нитей корда от края к центру повреждения. Границы шероховки помечают мелом с учетом превышения размеров вырезки на 5...10мм во все стороны. После шероховки поверхность должна быть матовой, иметь ровный ворс, не должно быть следов подгорания, разлохмаченных нитей, резких переходов.
Промазка клеем и сушка. Клей приготавливают растворением клеевой резины в бензине. Применяют клей малой концентрации, в котором соотношение резины и бензина (по массе) составляет 1:8 и высокой концентрации с соотношением составляющих 1:5. Наносят клей пульвилизатором или кистью из тонкой щетины тонким равномерным слоем. Первоначально клеем малой концентрации покрывают ремонтируемые участки, а так же починочный материал. Последующую сушку производят в сушильном шкафу при температуре 30-40ºС в течении 25-30 мин. Для покрышки и 10-15 мин для камеры или при комнатной температуре в течении часа. Вторичную промазку осуществляют клеем высокой концентрации с просушкой при той же температуре только в течении 35-40 мин покрышки и 25-30мин камеры.
Заделка повреждения заключается в наложении заплаты и прикатывании ёё роликом для камеры. На поверхность камеры, покрытую клеем, по периметру стыка или отверстия, накладывают полоски прослоенной резины шириной 15-20 мм и толщиной 0,9-1,2мм.
Заделка повреждений покрышки начинается с внутренней стороны покрышки и заканчивается с наружной. При заделке сквозных повреждений стенки отверстия обкладывают прослоечной резиной толщиной 0,7мм. Такой же резиной обкладывают починочный материал: манжет, подманжетник, пластырь. Прослоечная резина обеспечивает хорошую связь ремонтируемого участка с починочным материалом. После обкладки прослоечной резиной поврежденный участок заделывают протекторной резиной поврежденный участок заделывают протекторной резиной (в протекторе, брекере) и прослоечной резиной толщиной 2мм (в каркасе). Манжеты и пластыри накладывают так, чтобы направление нитей корда их наружного слоя совпадало с направлением нитей наружного слоя покрышки. Их накладывают постепенно (для предотвращения воздушных пузырей), затем прикатывают роликом, а края покрывают прослоечной резиной толщиной 0,7мм. Затем проверяют плотность прилипания починочного материала, а места вздутий прокалывают шилом для выпуска воздуха. При заделке наружных повреждений покрышки все ремонтируемое место обкладывают прослоечной резиной толщиной 0,7мм, а по углублениям в каркасе – прослоечной резиной толщиной 2мм. поврежденный участок протектора заполняют протекторной резиной. Починочная резина должна быть выше поверхности покрышки на 2..3мм со скосом на краях для обеспечения опресовки при вулканизации. Края наложенных манжет, пластырей и вставок корда следует перекрывать ленточной прослоечной резиной толщиной 0,7мм.
Вулканизация ведется при температуре 143ºС и давление 0,5Мпа. Камеру накладывают заплаткой на предварительно нагретую плиту, припудренную тальком, так чтобы центр заплаты был совмещен с центром прижимного винта, затем на участок камеры накладывают резиновую прокладку и прижимную плитку, которая должна перекрывать края заплаты на 10...15мм. Процесс вулканизации состоит из времени нагрева материала и времени самого процесса и продолжается от 30 до 180 мин в зависимости от толщины ремонтируемого участка и вида повреждения.
Отделка камер включает в себя срезание краев заплаты и стыков заподлицо с поверхности камеры, шлифование наплывов, заусенцев и других неровностей.
Отделка покрышек – процесс удаления излишков резины и заусенцев, снятие всех неровностей при помощи шероховки.
Контроль качества ремонта осуществляется внешним осмотром. На отремонтированном участке не должно быть отслоений починочного материала, утолщений, искажение формы, недовулканизации, складок. Камеры еще проверяют на герметичность воздухом под давлением 0,15 Мпа в ванне с водой.
Содержание операции и технического условия.
1. Снятие путевых заплат осуществляется при нагреве на вулканизационной плите (2-3мин.) с последующей вырезкой.
2. Подготовка камеры к ремонту. Сводиться к обработке поврежденных мест: края закругляют ножницами или вырезают сектор.
3. Шероховка производиться шарошками или шлифовальным кругом на ширину 20-25мм по всему параметру вырезки.
4. Подготовка починочного материала сводиться к вырезанию заплат из сырой резины или утильной камеры ножницами с последующей шероховкой. Размер заплаты должен быть на 20...30мм больше вырезки.
5. Намазка клеем и сушка осуществляется 2 раза. Первый клеем малой концентрации. Второй высокой концентрации. Сушка производиться после намазки при температуре 30..40ºС в течении 25..30мин.
6. Заделка включает наложение заплаты и прикатывании ёё роликом, а так же по параметру стыка накладывают полоски прослоенной резины шириной 15...20мм и толщиной 0,9...1,2 мм.
7. Вулканизация ведется при температуре 143ºС и давлением 0,5Мпа в течении 10...20мин.
8. Отделка камеры сводиться к обработке заплаты заподлицо с поверхностью камеры при помощи шлифования и ножниц.
9. Контроль осуществляется наружным осмотром, а также в ванне с водой на герметичность под давлением 0,15Мпа.
Практическая часть
Ремонт автомобильных камер
1. Очистка и мойка.
2. Обнаружение прокола визуально или подкачав камеру в водяной ванне.
3. Отметить прокол мелом.
4. Очистить с помощью щетки от грязи.
5. Помыть вручную с помощью щетки или в моечной машине.
6. Сушка.
7. Просушить в специальных камерах в течении 2...24ч при температуре 40...60ºС или при комнатной температуре в течении 1...3 суток.
8. Проверить оставшуюся влагу с помощью индикатора или визуально.
9. Подготовка.
10. Подготовка камеры.
11. Закругляем края в местах разрыва ножницами.
12. Вырезаем место установки вентиля (при повреждении).
13. Пробиваем отверстие для вентиля в другом месте.
14. Подготовка покрышки.
15. Удаляем из покрышки инородные тела с помощью щетки.
16. Вырезаем поврежденные участки остро заточенными ножами.
17. Контролируем влажность каркаса в месте ремонта с помощью индикатора в пределе 6%.
18. Подготовка починочного материала.
19. Для камеры.
20. Вырезаем латку из сырой резины, если размер разрыва др. 30 мм, или из утильной камеры при размере разрыва более 30мм, размер заплаты должен быть больше на 5...10мм.
21. Латку шерохуем с помощью шлифовального круга с внутренней стороны.
22. Для покрышки.
23. Приготовить пластырь, манжет, подманжетник в форме вырезки.
24. Манжеты прошероховать со всех сторон.
25. Шероховка покрышки.
26. Обозначить границы шероховки на 5...10мм больше размеров вырезки.
27. Шерохуем дисковой проволочной щеткой повреждения в каркасе и брекере, причем щетка должна ходить вдоль нитей корда.
28. Шерохуем протектор и боковины с помощью фигурных шарошек.
29. Промазка клеем.
30. Приготавливаем клей, растворением клеевой резины в бензине, леалой восковой концентрации.
31. Промазать ремонтируемые участки и начиночный материал тонким равномерным слоем малой концентрации.
32. Просушить в сушильном шкафу при температуре 30-40ºС в течении 25-30 мин, или при комнатной температуре в течении 1 часа.
33. Промазать клеем высокой концентрации.
34. Просушить при той же температуре только в течении 40-45минут или при комнатной температуре 1,5 часа.
35. Заделка повреждения камеры.
36. Накладываем заплаты и обжимаем руками.
37. Прикатываем заплату роликом.
38. Заделка повреждения покрышки начинается с внутренней стороны, а заканчивается с наружной.
39. Обложить стенки повреждений прослоечной резиной.
40. Такой же резиной обкладываем поделочный материал (манжеты подманжеты, пластырь).
41. Заделываем поврежденный участок в протекторе и брекере протекторной резиной и прослоечной резиной в каркасе.
42. Накладываем манжеты и пластырь так, чтобы направление нижней совпадало с направлением нитей корда. Накладывать постепенно для предотвращения воздушных пузырей.
43. Прикатываем роликом.
44. Проверить плотность прилегания материала.
45. Из мест вздутий выпустить воздух с помощью шила.
46. Вулканизация ведется при тем
|
|
Типы оградительных сооружений в морском порту: По расположению оградительных сооружений в плане различают волноломы, обе оконечности...
Механическое удерживание земляных масс: Механическое удерживание земляных масс на склоне обеспечивают контрфорсными сооружениями различных конструкций...
Кормораздатчик мобильный электрифицированный: схема и процесс работы устройства...
Опора деревянной одностоечной и способы укрепление угловых опор: Опоры ВЛ - конструкции, предназначенные для поддерживания проводов на необходимой высоте над землей, водой...
© cyberpedia.su 2017-2024 - Не является автором материалов. Исключительное право сохранено за автором текста.
Если вы не хотите, чтобы данный материал был у нас на сайте, перейдите по ссылке: Нарушение авторских прав. Мы поможем в написании вашей работы!