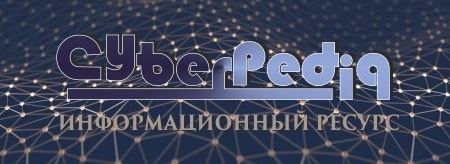
Архитектура электронного правительства: Единая архитектура – это методологический подход при создании системы управления государства, который строится...
Особенности сооружения опор в сложных условиях: Сооружение ВЛ в районах с суровыми климатическими и тяжелыми геологическими условиями...
Топ:
Техника безопасности при работе на пароконвектомате: К обслуживанию пароконвектомата допускаются лица, прошедшие технический минимум по эксплуатации оборудования...
Марксистская теория происхождения государства: По мнению Маркса и Энгельса, в основе развития общества, происходящих в нем изменений лежит...
Когда производится ограждение поезда, остановившегося на перегоне: Во всех случаях немедленно должно быть ограждено место препятствия для движения поездов на смежном пути двухпутного...
Интересное:
Наиболее распространенные виды рака: Раковая опухоль — это самостоятельное новообразование, которое может возникнуть и от повышенного давления...
Что нужно делать при лейкемии: Прежде всего, необходимо выяснить, не страдаете ли вы каким-либо душевным недугом...
Подходы к решению темы фильма: Существует три основных типа исторического фильма, имеющих между собой много общего...
Дисциплины:
![]() |
![]() |
5.00
из
|
Заказать работу |
|
|
Тема лекции: Шлицевые (зубчатые) соединения
Вопросы лекции:
1. Классификация шлицевых соединений
2. Структура условного обозначения
3. Достоинства и недостатки шлицевых соединений
4. Рекомендации по конструированию шлицевых соединений
5. Изображение шлицевых валов, отверстий и их соединений
6. Расчет на прочность прямобочных шлицевых соединений
7. Последовательность проверочного расчета шлицевых соединений
Литература
1. Тюняев А. В. Детали машин [Текст]: учебник / А. В. Тюняев, В. П. Звездаков, В. А. Вагнер; рец. А. Ю. Иванов [и др.]. - 2-е изд., испр. и доп. - СПб.; М.; Краснодар: Лань, 2013. - 736 с.
2. Андриенко Л.А. Детали машин: учебник для вузов / [Л.А. Андриенко, Д., Б.А. Байков, М. Н. Захаров и др.]; под ред. О. А. Ряховского. 4-е изд., перераб. и доп. — Москва: Издательство МГТУ им. Н. Э. Баумана, 2014. — 465, [7] с.: ил.
3. Рукодельцев, А.С. Детали машин: конспект лекций для стул. техн. специальностей оч. и заоч. обуч. / А.С. Рукодельцев, И.В. Никитаев, О.В. Сидорова. - Н. Новгород: Изд-во ФБОУ ВПО «ВГАВТ», 2012. - 204 с.
4. Гулиа Н. В., Детали машин: Учебник / Н.В. Гулиа, В. Г. Клоков, С.А. Юрков //Под общ. ред. д. т. н., проф. Н. В. Гулиа. — 3-еизд., стер. — СПб.: Издатель ство «Лань», 2013. — 416 с.: ил. — (Учебники для вузов. Специальная литература).
Шлицевые соединения можно рассматривать как многошпоночные, в которых шпонки как бы изготовлены заодно с валом. Рабочими поверхностями являются боковые стороны зубьев. В последние годы, в связи с общим повышением напряжений в деталях машин, шлицевые соединения получили самое широкое распространение взамен шпонок. Этому способствует оснащение промышленности специальным оборудованием - шлицефрезерными и протяжными станками. Некоторые авторы называют их зубчатыми соединениями.
|
Классификация шлицевых соединений
Шлицевые соединения образуются выступами - зубьями на валу, ходящими во впадины соответствующей формы в ступице. Вал и отверстие в ступице обрабатывают так, чтобы боковые поверхности зубьев или участки цилиндрических поверхностей (по внутреннему или наружному диаметру зубьев) плотно прилегали друг к другу. Соответственно различают шлицевые соединения с центрированием по боковым поверхностям зубьев, по внутреннему или наружному диаметру. Центрирование по диаметрам обеспечивает более высокую соосность вала и ступицы, а центрирование по боковым граням обеспечивает более равномерное распределение нагрузки по зубьям. По характеру соединения различают: неподвижные – для закрепления детали на валу; подвижные - допускающие перемещение детали вдоль вала (например, блока шестерен коробки передач станка).
В зависимости от профиля зубьев различают три основных типа соединений:
- с прямобочными (рис. 16, а) зубьями - число зубьев Z = 6, 8, 10, 12 для диаметров валов 14≤d≤125 мм;
- с эвольвентными (рис. 16, б) зубьями - число зубьев Z = 12, 16 и до 82 для диаметров валов 4≤d≤500 мм;
- с треугольными (рис. 16, в) зубьями - число зубьев Z = 24, 36 и более.
Прямобочные шлицы в поперечном сечении имеют боковые стенки в виде прямой линии, боковая поверхность эвольвентных шлицов в поперечном сечении образует эвольвенту, а треугольные шлицы в поперечном сечении имеют форму треугольника со срезанной вершиной.
По направлению продольной оси шлицы бывают: прямолинейные, продольная ось которых направлена вдоль образующей несущего цилиндра, и винтовые, имеющие продольную ось, направленную по винтовой линии под некоторым углом к образующей несущего цилиндра.
Рис. 16. Типы зубчатых (шлицевых) соединений: а — прямобочные зубья; б — эвольвентные зубья;
В — треугольные зубья
Рис. 17. Прямобочные зубья (шлицы)
Шлицевые валы изготавливаются в массовом производстве по технологии, аналогичной технологии изготовления зубчатых колёс (метод обкатки, способ – нарезание посредством червячных фрез), в штучном и мелкосерийном производстве используется метод копирования (требует наличия специального инструмента), а в случае отсутствия специнструмента валы изготавливаются методом фрезерования на универсальных фрезерных станках. Возможно также изготовление таких валов на обрабатывающих центрах с числовым программным управлением.
|
Шлицевые пазы в отверстиях ступиц при массовом производстве изготавливаются методом протягивания (инструмент – протяжка) или долблением специальными долбяками. В штучном производстве изготовление ведётся только долблением.
Наибольшее распространение в машиностроении имеют прямобочные зубчатые соединения (рис.17). Их применяют в неподвижных и подвижных соединениях. Стандартом предусмотрены три серии прямобочных зубчатых соединений — легкая, средняя и тяжелая, отличающиеся одна от другой высотой и числом зубьев (чаще применяют соединения с шестью-десятью зубьями).
Прямобочные шлицевые соединения различают также по способу центрирования:
- по наружному диаметру D (наиболее точный способ центрирования) (рис.18,а). Центрирование по наружному диаметру наиболее технологично и рекомендуется при твердости внутренней поверхности ступицы НВ 350. Калибровку центрирующих поверхностей ступицы выполняют протягиванием, а калибровку вала – шлифованием. Этот способ применяется при изготовлении неподвижных соединений в серийном и массовом производствах. Соединение (рис.18,а), во избежание термических короблений, требует чистовой протяжки ступицы после термообработки, поэтому твердость ступицы не может быть выше HRC=30.
- по внутреннему диаметру d (при закаленной ступице) (рис.18,б). Центрирование по внутреннему диаметру рекомендуется при высокой твердости материала ступицы, когда калибровка отверстия протяжкой невозможна. В этом случае центрирующие поверхности ступицы и вала доводят шлифованием. Применяется в индивидуальном и мелкосерийном производствах. Соединение (рис.18,б) требует шлифовки вала по посадочному диаметру на специальных станках, зато ступица может быть твердой, так как посадочный диаметр шлифуется на обычных внутришлифовальных станках.
|
- по боковым граням (при реверсивной работе соединения и отсутствии жестких требований к точности центрирования) (рис.18,в). Центрирование по боковым поверхностям обеспечивает более равномерное распределение нагрузки по зубьям. Рекомендуется для передачи больших переменных ударных нагрузок при пониженной точности центрирования. Соединение (рис.18,в) допускает твердые шлицы на валу и на ступице, однако для обеспечения сборки, считаясь с возможных короблением шлицов при закалке, зазоры в соединении должны быть увеличенными. Зазор в контакте поверхностей: центрирующих практически отсутствует, нецентрирующих значительный. Центрирование по боковым сторонам шлицов эффективно в том случае, когда точность совпадения геометрических осей не имеет существенного значения, но требуется обеспечить прочность соединения в процессе эксплуатации (например, карданные валы в автомобилях) или когда по условиям работы требуются минимальные зазоры по b (например, при действии знакопеременного момента). Этот способ не обеспечивает высокой точности центрирования и применяется редко.
Рис. 18. Центрирование прямобочных зубчатых соединений а – по наружному диаметру; б – по внутреннему диаметру;
в – по боковым граням; г – форма сечения ступицы; д, е – форма сечений вала исполнений б, в
Структура условного обозначения шлицевого прямобочного соединения должна иметь следующий вид:
где 1 - обозначение поверхности центрирования;
2 - числа шлицов соединения;
3, 6, 9 - номинальные размеры d, D и b;
4, 7, 10, 5, 8, 11 - обозначения полей допусков отверстий и валов по диаметрам d, D и по боковым сторонам шлицов b.
В обозначении допускается не указывать допуски нецентрирующих диаметров.
Допуски и посадки прямобочных шлицевых соединений приведены в таблицах.
Пример условного обозначения соединения, втулки и вала:
- для шлицевого соединения с числом шлицев z=8, внутренним диаметром d=42 мм, наружным диаметром D=46 мм, шириной шлица b=8 мм, с центрированием по d, с посадками по d - H7/f7 и по b - D9/h9:
- для отверстия этого же соединения:
d-8×H7×46×8D9,
|
- для вала этого же соединения:
d-8×42f7×46×8h9.
По ГОСТ 1139-80 предусматривается три серии соединений с прямобочным профилем зубьев: легкую, среднюю и тяжелую (табл. 3), которые отличаются высотой и числом зубьев z. Легкая серия рекомендуется для неподвижных соединений, средняя – для подвижных, при перемещении ступицы не под нагрузкой. Тяжелая серия имеет более высокие зубья с большим числом. Рекомендуется для передачи больших вращающих моментов, а также для подвижных соединений при перемещении ступицы под нагрузкой.
Соединения с эвольвентным профилем зубьев тоже стандартизованы и используются так же, как и прямобочные, в подвижных и неподвижных соединениях. Угол профиля образующей рейки α= 30°. Высота шлица (0,8… 1,0)m. Ножка зуба усилена. Соединения выполняются по ГОСТ 6033-80 с центрированием по боковым поверхностям зубьев (рис.19,а), реже по наружному диаметру (рис.19,б).
Рис.19. Эвольвентное зубчатое зацепление: а – центрирование по боковым граням;
Рис. 20. Шариковое шлицевое соединение
Допускаемый момент (Нм) для шарикового шлицевого соединения (твердость вала и ступицы не менее 60 НRС):
где Zшл – число рабочих выступов (шлиц);
l – рабочая длина соединения, мм;
d, Dср – диаметры шариков и окружности расположения центров шариков, мм.
Зубчатые соединения изготовляют из сталей с временным сопротивлением σв= 500 МПа.
Рекомендации по конструированию шлицевых соединений
1. Для подвижных соединений рекомендуют рабочую длину ступицы принимать не менее диаметра вала, т.е. lp<d. При коротких ступицах (lp<d) возможно защемление от перекоса при перемещении вдоль вала.
2. В длинных ступицах (lp>1,5d) необходима расточка отверстия выхода стружки при протягивании (см. рис. 21).
3. Для облегчения входа протяжки и сборки соединения в отверстии предусматривают заводные фаски (см. рис. 21).
4. В соединениях, воспринимающих радиальные нагрузки (зубчатые и червячные колеса, звездочки, шкивы), зубья шлицевого соединения желательно располагать симметрично относительно венцов.
5. Для уменьшения изнашивания следует уменьшать зазоры в соединении, повышать точность изготовления и твердость рабочих поверхностей.
6. Число Z и размеры шлицев принимаются в зависимости от диаметра вала по соответствующему ГОСТ. Длина зубьев определяется длиной ступицы, а если ступица подвижная – величиной хода её перемещения.
Рис.21
Эффективными средствами повышения износостойкости шлицевых соединений являются:
1) уменьшение углов перекоса;
2) увеличение твердости контактирующих поверхностей путем азотирования, цементации, обдувки дробью;
3) уменьшение зазоров в шлицевом соединении, применение более плотных посадок, центрирование по вспомогательным поверхностям и затяжка соединений;
|
4) применение бочкообразных зубьев;
5) подача смазки в зону контакта;
6) снижение коэффициента трения путем покрытий (серебром, медью, кадмием, молибденом).
Основными критериями работоспособности шлицов являются:
- сопротивление боковых поверхностей смятию (расчёт аналогичен шпонкам);
- сопротивление износу при фреттинг-коррозии (малые взаимные вибрационные перемещения).
Рис.22
Рис.23
Образующие поверхности впадин на продольных разрезах вала и отверстия показывают сплошными основными линиями (рис.22, рис. 24).
На проекции вала и отверстия на плоскость, перпендикулярную их оси, а также в поперечных сечениях и разрезах окружности впадин показывают сплошными тонкими линиями (рис. 24).
Рис.24
Делительные окружности и образующие делительных поверхностей на изображениях деталей шлицевых эвольвентных соединений показывают штрихпунктирной тонкой линией (рис. 22-24).
Границу шлицевой поверхности вала, а также границу между шлицами полного профиля и сбегом показывают сплошной тонкой линией (рис. 22).
На изображениях, полученных проецированием на плоскость, перпендикулярную оси шлицевых вала и отверстия, изображают профиль одного шлица и двух впадин. Допускается изображать большее число шлицов и впадин.
Если секущая плоскость проходит через ось шлицевых вала и отверстия, то на разрезах и сечениях валов шлицы условно совмещают с плоскостью чертежа и показывают нерассеченными (см. рис. 22), а на разрезах и сечениях отверстий впадины условно совмещаются с плоскостью чертежа (см. рис. 23 и рис. 24).
При изображении шлицевых вала или отверстия в разрезе или сечении линии штриховки проводят:
- в продольных разрезах и сечениях – до линий впадин (см. рис. 22, 24, 25);
- в поперечных разрезах и сечениях – до линий выступов (см. рис. 24, 25).
Если секущая плоскость проходит через ось шлицевого соединения, то при его изображении на разрезе показывают только ту часть поверхности шлицов отверстия, которая не закрыта валом (рис. 101).
Рис.25
Радиальный зазор между шлицами и впадинами вала и отверстия не показывают (рис. 25).
На изображениях шлицевых валов, полученных проецированием на плоскость, параллельную оси указывают длину шлицев полного профиля L 1 до сбега (см. рис. 22).
Допускается дополнительно указывать полную длину шлицев L, или наибольший радиус инструмента R, или длину сбега L 2.
На чертеже детали стандартизированного шлицевого соединения указывают в технических требованиях или на полке линии-выноски (рис. 25), условное обозначение шлицевого вала или шлицевого отверстия по соответствующему стандарту.
Рис. 26. К расчету прямобочного шлицевого соединения
При расчете допускают, что по боковым поверхностям зубьев нагрузка распределяется равномерно, но из-за неточности изготовления в работе участвует только 75% общего числа зубьев (т.е. коэффициент неравномерности распределения нагрузки между зубьями (шлицами) ψ = 0,75).
По аналогии с условием (3)
где Т — вращающий момент на валу, Нмм; ψ= 0,75; z — число зубьев (выбирают в зависимости от d по табл.3); h – высота поверхности контакта зубьев; L – длина поверхности контакта зубьев; dcp — средний диаметр соединения, мм; l — рабочая длина зубьев, мм; D, l, r (см. рис. 26) — выбирают в зависимости от d по табл. 3; [σ]см - допускаемое напряжение на смятие боковых граней зубьев из сталей, имеющих σв> 500 МПа ([σ]см принимают по табл. 4). В таблице 4 приведены значения [σ]см для изделий общего машиностроения и подъемно-транспортных устройств, рассчитанных на длительный срок службы. В каждой отрасли машиностроения рекомендуют свои значения с учетом специфики эксплуатации (срок службы, режим нагрузки и пр.), качества изготовления, прочности материалов и др.
Например, в станкостроении рекомендуют более низкие значения: [σ]см = 12 – 20 МПа для неподвижных соединений и [σ]см = 4 – 7 МПа для подвижных без нагрузки – здесь учитывают влияние соединений на точность станков; в авиации для соединений валов с зубчатыми колесами рекомендуют более высокие значения [σ]см = 50 – 100 МПа – для получения легких конструкций.
Для прямобочных шлицев h=0,5(D-d)-2f; dср=0,5(D+d),
где f- величина фаски зуба.
для эвольвентных шлицев h=θm; dср=D-1,1m,
где θ=1 - при центрировании по боковым поверхностям и θ=0,9 при центрировании по наружному диаметру;
m - модуль шлицев;
d - диаметр делительной окружности.
Для треугольных шлицов h=0,5(D-d); dcp=d=mz.
При проверке соединения на износ действующие напряжения, вычисленные по (9), проверяются на выполнение соотношения
где – коэффициент, учитывающий число циклов нагружения, а допускаемые напряжения по износу [σ]изн зависят от параметров внешней нагрузки и термообработки рабочих поверхностей шлицов. Для шлицов, закалённых до поверхностной твёрдости HRC 60, принимают [σ]= 40…85 МПа, а для шлицованных деталей без термохимической обработки – [σ]изн = 25…50 МПа.
Предельный вращающий момент, передаваемый соединением, равен Тmax=0,5σсмzhψldср
Таблица 3. Зубчатые прямобочные соединения, размеры, мм
Номинальные размеры z х d х D | b | l | r, не более | Серия |
6 х 26 х 30 | 6 | 0,3 | 0,2 | Легкая |
8 х 32 х 36 | 6 | 0,4 | 0,2 | |
8 х 36 х 40 | 7 | 0,4 | 0,3 | |
8 х 42 х 46 | 8 | 0,4 | 0,3 | |
8 х 46 х 50 | 9 | 0,4 | 0,3 | |
8 х 52 х 58 | 10 | 0,5 | 0,5 | |
6 х 11 х 14 | 3 | 0,3 | 0,2 | Средняя |
6 x 21 х 25 | 5 | 0,3 | 0,2 | |
6 х 26 х 32 | 6 | 0,4 | 0,3 | |
8 х 36 х 42 | 7 | 0,4 | 0,3 | |
10 х 16 х 20 | 2,5 | 0,3 | 0,2 | Тяжелая |
10 х 18 x 23 | 3 | 0,3 | 0,2 | |
10 x 21 х 26 | 3 | 0,3 | 0,2 | |
10 x 23 x 29 | 4 | 0,3 | 0,2 | |
10 x 26 x 32 | 4 | 0,3 | 0,2 | |
10 x 28 x 35 | 4 | 0,4 | 0,3 | |
10 x 32 x 40 | 5 | 0,4 | 0,3 | |
10 x 36 x 45 | 5 | 0,4 | 0,3 | |
10 x 42 x 52 | 6 | 0,4 | 0,3 |
Таблица 4. Допускаемые напряжения смятия [ 𝛔 ]см на рабочих гранях зубьев (шлицев)
Соединение | Условия эксплуатации | [σ]см на рабочих гранях зубьев | |
без термической обработки | с термической обработкой | ||
Неподвижное | Тяжелые Средние Легкие | 35-40 60-100 80-120 | 40-70 100-140 120-200 |
Подвижное ненагруженное | Тяжелые Средние Легкие | 15-20 20-30 25-40 | 20-36 30-40 40-70 |
Подвижное под нагрузкой | Тяжелые Средние Легкие | — | 3-10 5-15 10-20 |
Примечания: тяжелые условия эксплуатации означают, что нагрузка знакопеременная с ударами; вибрации большой частоты и амплитуды; плохие условия смазки в подвижных соединениях; невысокая точность изготовления.
Вопросы для самопроверки
- Определите по рисунку тип зубьев (шлицев) на валах.
- Дайте классификацию шлицевых соединений.
- Какими достоинствами обладают шлицевые соединения по сравнению со шпоночными?
- Какие существуют способы центрирования шлицевых прямобочных соединений?
- Как производят проверочный расчет прямобочного шлицевого соединения?
- Каковы виды шлицевых соединений и способы их центровки?
- Как проводится расчет на прочность шлицевых соединений?
- Каковы назначение, виды и методы расчета штифтов?
- Какова конструкция и основное назначение шлицевых соединений?
- Каковы виды нагружения и критерии расчёта шлицов?
- Каково назначение шлицевых соединений? Их разновидности. Какие шлицевые соединения стандартизованы?
- Каким достоинствами обладают шлицевые соединения по сравнению со шпоночными?
- Какими применяют способы центрирования шлицевых прямоточных и эвольвентных соединений? Чем обусловлен выбор способа центрирования?
- В чем преимущества шлицевого соединения по сравнению со шпоночным?
- Критерии работоспособности шлицевых соединений? Почему они изнашиваются и как это учитывают при расчете?
- Каковы основные критерии работоспособности шлицевых соединений? Как устанавливают размеры шлицевых соединений?
Тема лекции: Шлицевые (зубчатые) соединения
Вопросы лекции:
1. Классификация шлицевых соединений
2. Структура условного обозначения
3. Достоинства и недостатки шлицевых соединений
4. Рекомендации по конструированию шлицевых соединений
5. Изображение шлицевых валов, отверстий и их соединений
6. Расчет на прочность прямобочных шлицевых соединений
7. Последовательность проверочного расчета шлицевых соединений
Литература
1. Тюняев А. В. Детали машин [Текст]: учебник / А. В. Тюняев, В. П. Звездаков, В. А. Вагнер; рец. А. Ю. Иванов [и др.]. - 2-е изд., испр. и доп. - СПб.; М.; Краснодар: Лань, 2013. - 736 с.
2. Андриенко Л.А. Детали машин: учебник для вузов / [Л.А. Андриенко, Д., Б.А. Байков, М. Н. Захаров и др.]; под ред. О. А. Ряховского. 4-е изд., перераб. и доп. — Москва: Издательство МГТУ им. Н. Э. Баумана, 2014. — 465, [7] с.: ил.
3. Рукодельцев, А.С. Детали машин: конспект лекций для стул. техн. специальностей оч. и заоч. обуч. / А.С. Рукодельцев, И.В. Никитаев, О.В. Сидорова. - Н. Новгород: Изд-во ФБОУ ВПО «ВГАВТ», 2012. - 204 с.
4. Гулиа Н. В., Детали машин: Учебник / Н.В. Гулиа, В. Г. Клоков, С.А. Юрков //Под общ. ред. д. т. н., проф. Н. В. Гулиа. — 3-еизд., стер. — СПб.: Издатель ство «Лань», 2013. — 416 с.: ил. — (Учебники для вузов. Специальная литература).
Шлицевые соединения можно рассматривать как многошпоночные, в которых шпонки как бы изготовлены заодно с валом. Рабочими поверхностями являются боковые стороны зубьев. В последние годы, в связи с общим повышением напряжений в деталях машин, шлицевые соединения получили самое широкое распространение взамен шпонок. Этому способствует оснащение промышленности специальным оборудованием - шлицефрезерными и протяжными станками. Некоторые авторы называют их зубчатыми соединениями.
|
|
Механическое удерживание земляных масс: Механическое удерживание земляных масс на склоне обеспечивают контрфорсными сооружениями различных конструкций...
Состав сооружений: решетки и песколовки: Решетки – это первое устройство в схеме очистных сооружений. Они представляют...
Адаптации растений и животных к жизни в горах: Большое значение для жизни организмов в горах имеют степень расчленения, крутизна и экспозиционные различия склонов...
Особенности сооружения опор в сложных условиях: Сооружение ВЛ в районах с суровыми климатическими и тяжелыми геологическими условиями...
© cyberpedia.su 2017-2024 - Не является автором материалов. Исключительное право сохранено за автором текста.
Если вы не хотите, чтобы данный материал был у нас на сайте, перейдите по ссылке: Нарушение авторских прав. Мы поможем в написании вашей работы!