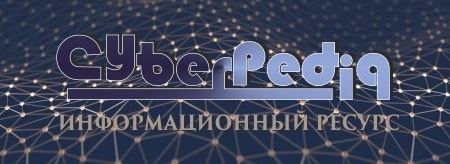
Историки об Елизавете Петровне: Елизавета попала между двумя встречными культурными течениями, воспитывалась среди новых европейских веяний и преданий...
Опора деревянной одностоечной и способы укрепление угловых опор: Опоры ВЛ - конструкции, предназначенные для поддерживания проводов на необходимой высоте над землей, водой...
Топ:
Методика измерений сопротивления растеканию тока анодного заземления: Анодный заземлитель (анод) – проводник, погруженный в электролитическую среду (грунт, раствор электролита) и подключенный к положительному...
Характеристика АТП и сварочно-жестяницкого участка: Транспорт в настоящее время является одной из важнейших отраслей народного...
Особенности труда и отдыха в условиях низких температур: К работам при низких температурах на открытом воздухе и в не отапливаемых помещениях допускаются лица не моложе 18 лет, прошедшие...
Интересное:
Уполаживание и террасирование склонов: Если глубина оврага более 5 м необходимо устройство берм. Варианты использования оврагов для градостроительных целей...
Аура как энергетическое поле: многослойную ауру человека можно представить себе подобным...
Лечение прогрессирующих форм рака: Одним из наиболее важных достижений экспериментальной химиотерапии опухолей, начатой в 60-х и реализованной в 70-х годах, является...
Дисциплины:
![]() |
![]() |
5.00
из
|
Заказать работу |
|
|
Введение
В соответствии с учебной программой дисциплина «Строительство промышленных зданий и сооружений» входит в блок «Строительное дело». При изучении данного курса студенты выполняют работы по следующим темам:
- земляные работы;
- бетонные работы;
- сваи.
Предлагаемые работы включают типичные наборы инженерных задач. Порядок их выполнения следующий: формируется блок исходных данных с выделением условий и параметров, определяются наиболее важные показатели, по которым можно найти оптимальное решение, проводятся расчеты и выполняются чертежи.
В ходе выполнения работ студент получает навыки выбора способов производства земляных работ, типов бетонов и оборудования, овладевает методиками расчета параметров производства бетонных работ и обустройства свайного поля.
Методические указания содержат пять работ, которые надо выполнить в течении одного семестра.
Каждая работа содержит краткие теоретические сведения, задачи и задания, выполняемые студентами самостоятельно в соответствии с вариантами, определенными преподавателем.
Отчет по каждой работе должен содержать цель работы, условия задач и их решения, а также выводы, самостоятельно сформулированные студентом.
При защите отчета студент должен продемонстрировать теоретические знания по рассматриваемой тематике и методике решения задач.
Лабораторная работа №1
Лабораторная работа №2
Производство свайных работ
Необходимая глубина забивки свай фундамента и допустимая на них расчетная нагрузка устанавливаются на основании материалов инженерно-геологических изысканий в соответствии с конструктивными особенностями фундамента, действующими на него вертикальными и горизонтальными нагрузками, допустимыми величинами деформаций здания. При этом учитываются результаты зондирования грунта и испытания пробных свай, опыт эксплуатации построенных вблизи зданий, а также обстоятельства, способные повлиять на несущую способность свай и величину их осадок под нагрузкой (наличие слоя слабого грунта, подсыпка территории, рытье грунта вблизи свай и т.д.).
|
Напряжения в материале свай от действующих на них вертикальных и горизонтальных нагрузок и изгибающих моментов, с учетом допустимого отклонения свай от проектного положения, не должны превышать величин, нормируемых
СП 63.13330.2012 "Бетонные и железобетонные конструкции. Основные положения".
При производстве свайных работ специализированная организация производит забивку каждой сваи фундамента до сопротивления, обеспечивающего указанную в проекте несущую способность сваи, определяемую динамическим методом в соответствии с главой СП 24.13330.2011 "Свайные фундаменты".
Выбор типа свайного фундамента.
В зависимости от конструктивного решения сооружения и нагрузок свайные фундаменты могут устраиваться в виде:
а) одиночных свай – под колонны или отдельно стоящие опоры при вертикальной нагрузке на фундамент;
б) кустов – под колонны с размещением двух и более свай, связанных с ростверком;
в) лент – под стены зданий и сооружений с расположением свай в один, два ряда или в шахматном порядке;
г) сплошного свайного поля – под тяжелые сооружения небольших размеров в плане, если по расчету ширина ростверка близка к шагу колонн.
Размеры свай (длина и поперечное сечение) выбираются в зависимости от грунтовых условий строительной площадки и нагрузок на фундамент. Сваи по условиям работы в грунте (в зависимости от свойств грунтов, залегающих под нижним концом) подразделяются на сваи стойки и висячие сваи. Сваи, которые передают нагрузку нижним концом на практически несжимаемые грунты, относят к сваям стойкам.
|
Выбор оборудования для погружения свай.
В данной работе необходимо подобрать сваепогружающее оборудование. Оборудование выбирается исходя из начальных условий: необходимая длина сваи; грунт, в который погружается свая и требуемое количество свай, погружаемых за смену.
Порядок подбора сваепогружающего оборудования следующий:
1. По таблице 2.2 находят несущую способность сваи Ф и её массу.
2. По формуле 2.1 вычисляют минимальную энергию молота Эр.
3. По таблице 2.1 подбирают дизель-молот и по формулам 2.3- 2.4 определяют его энергию удара;
4. По формуле 2.2 производят проверку выбранного типа молота, при необходимости выполняют корректировку;
5. По таблице 2.3 производят подбор копровой установки.
Сваепогружающее оборудование выбирают таким образом, чтобы обеспечить погружение свай на проектные расчетные отметки. Минимальную энергию удара молота Эр, необходимую для погружения свай, определяют по формуле
Эр ≥ 1,75·a·Ф, Дж, (2.1)
где а – коэффициент, равный 25 Дж/кН;
Ф – заданная несущая способность сваи, кН.
Принятый тип молота с расчетной энергией удара Эр должен удовлетворять условию
, (2.2)
где Мп – полный вес молота, Н;
Мс – вес сваи, H;
К – коэффициент, принимаемый для трубчатых дизель-молотов равным 6, для штанговых дизель-молотов – 5;
Эр – энергия удара молота, определяемая по формулам 2.3-2.4
для трубчатых дизель-молотов
Эр=0,9·М·h, (2.3)
для штанговых дизель-молотов
Эр=0,4·М·h, (2.4)
где М – вес ударной части молота, Н;
h – фактическая высота падения ударной части молота, м; принимается равной для трубчатых дизель-молотов – 2,5-2,8; для штанговых дизель-молотов 1,7-2,2 (табл. 2.1).
Таблица 2.1 - Технические характеристики дизель – молотов
Тип и марка молота | Масса ударной части, т | Энергия одного удара, кДж | Общая масса молота, т | Число ударов в мин. | Высота падения ударной части, м | |
Штанговые дизель - молоты | ||||||
С-222 | 1,2 | 5,25 | 2,3 | 50-55 | 1,79 | |
С-266 | 1,8 | 16 | 3,1 | 50-55 | 2,1 | |
С-330 | 2,5 | 20 | 4,2 | 42-50 | 2,3 | |
С-330А | 2,5 | 20 | 4,5 | 42-50 | 2,5 | |
Трубчатые дизель - молоты;
С воздушным охлаждением | ||||||
С-858 | 1,25 | 33 | 3,0 | 47-55 | 3,0 | |
С-859 | 1,8 | 48 | 3,5 | 43-55 | 3,0 | |
С-949 | 2,5 | 67 | 5,8 | 47-55 | 3,0 | |
С-945 | 3,5 | 94 | 7,3 | 43-55 | 3,0 | |
Трубчатые дизель - молоты; С водяным охлаждением | ||||||
С-995 | 1,25 | 33 | 2,6 | 43-55 | 3,0 | |
С-996А | 1,8 | 48 | 3,6 | 43-55 | 3,0 | |
С-1047 | 2,5 | 67 | 5,5 | 43-55 | 3,0 | |
С1048 | 3,5 | 94 | 7,65 | 43-55 | 3,0 |
С учетом этого время на погружение одной сваи Тсваи составляет, мин
, (2.5)
где Пкоп.см . - сменная производительность копровой установки;
8,2 – продолжительность смены, ч.
Таблица 2.2 – Характеристики и несущая способность свай, конструкции ростверков, фундаментов
Длина свай, м | Марк. | Сечение мм×мм | Масса свай, кг | Несущая способность, т | Высота ростверка, м | Высота нижней ступени | Масса арматуры, кг | Толщина стенки стакана ростверка, мм | Высота фундамента, м | Высота нижней ступени, м | Размеры нижней ступени в плане | ||
песков | полутв. глин | Гор. сетки | Верт. сетки | ||||||||||
5,0 | С5-30 | 300×300 | 1140 | 28,0 | 44,0 | 1,6 | 0,6 | 20-30 | 30-40 | 20 | 2 | 0,8 | 1,5×1,5 |
6,0 | С6-30 | 1280 | 33,0 | 51,0 | 4 | 1,2 | 2,0×2,0 | ||||||
7,0 | С7-30 | 1610 | 38,0 | 57,0 | 0,8 | 30-40 | 40-50 | 25 | 6 | 1,6 | 2,4×2,4 | ||
8,0 | С8-30 | 1820 | 43,0 | 63,0 | 1,8 | ||||||||
9,0 | С9-30 | 2060 | 46,0 | 70,0 | |||||||||
10,0 | С10-30 | 2290 | 50,0 | 76,0 |
Таблица 2.3 – Технические характеристики самоходных копровых установок
Тип и марка уст. | Радиус дейст., м | Базовая машина | Макс. длина погруж. сваи, м | Груз-ть, т | Масса устан-ки, т | Произв-сть в смену сваи |
На базе тракторов-трубоукладчиков | ||||||
С-878К | С одной стоянки забивается одна свая | Т-100-М | 8,0 | 7,0 | 17,8 | 24 |
С-870 | С-100 | 8,0 | 6,5 | 17,0 | 22 | |
С-714 | Т-100-М | 8,0 | 7,0 | 18,0 | 24 | |
СП-49К | Т-100-МВГП | 12,0 | 7,0 | 23,8 | 20 | |
СП-67 | Т-100-М | 10,0 | 8,5 | 19,1 | 22 | |
СП-28А | Т-100-М | 8,0 | 5,4 | 14,0 | 24 | |
КО-16 | Т-160-П | 16,0 | 15,0 | 38,9 | 24 | |
На базе кранов-экскаваторов | ||||||
С-860 | 6,0 | 20-4111Б | 8,0 | 10,0 | 27,0 | 20 |
СП-250 | 6-8,0 | 2-10011 | 12,0 | 10,0 | 45,0 | 16 |
СП-51 | 6-8,0 | 206111Б | 16,0 | 15,0 | 60,0 | 16 |
КМ-12 | 6,0 | 2-10011Д | 12,0 | 14,0 | 45,0 | 16 |
Э-1252 | 6,0 | 20-6112Б | 8,0 | 14,0 | 45,0 | 20 |
Таблица 2.4- Исходные данные для расчета
Вариант | Длина свай, м | Грунт | Необходимая производительность шт/см |
1 | 6,0 | Песок | 20 |
2 | 5,0 | Глина | 17 |
3 | 9,0 | Песок | 22 |
4 | 10,0 | Глина | 24 |
5 | 5,0 | Песок | 20 |
6 | 6,0 | Глина | 16 |
7 | 7,0 | Песок | 18 |
8 | 8,0 | Глина | 20 |
9 | 9,0 | Глина | 24 |
10 | 10,0 | Песок | 24 |
|
Лабораторная работа №3
Расчет состава бетона
Проектирование состава имеет цель установить такой расход материалов на 1 м3 бетонной смеси, при котором наиболее экономично обеспечивается получение удобоукладываемой бетонной смеси и заданной прочности бетона, а в ряде случаев необходимой морозостойкости, водонепроницаемости и специальных свойств бетона.
Состав бетонной смеси выражают в виде соотношения по массе (реже по объему) между количествами цемента, песка и щебня (или гравия) с указанием водоцементного отношения.
Различают два состава бетона: номинальный (лабораторный), принимаемый для материалов в сухом состоянии, и производственный (полевой) — для материалов с естественной влажностью. К моменту расчета состава бетонной смеси нужно определить качество исходных материалов: цемента, воды, песка и щебня (гравия) — согласно требованиям ГОСТов.
Состав тяжелого бетона рассчитывают по методу «абсолютных объемов», разработанному проф. Б.Г. Скрамтаевым и его школой. В основу этого метода положено условие, что тяжелый бетон, уплотненный в свежем состоянии, приближается к абсолютной плотности, т.е. сумма абсолютных объемов исходных материалов в 1 м3 равна объему уплотненной бетонной смеси. Исходными данными для расчета состава бетона являются заданная прочность бетона R6, характеристика бетонной смеси по степени подвижности или жесткости, а также характеристика исходных материалов — активность цемента Rц, плотности песка, Щебня или гравия и пустотность щебня или гравия.
В зависимости от условий, в которых будет находиться бетон в сооружении или конструкции, к нему могут предъявляться также и другие требования, например степень морозостойкости, стойкость к воздействию агрессивных вод, водонепроницаемость. Высокая морозостойкость и непроницаемость плотно уложенного бетона регулируются водоцементным соотношением и расходом вяжущего, отсюда вытекает необходимость нормирования В/Ц в гидротехническом, дорожном и других специальных бетонах. Состав бетонной смеси, т.е. количество цемента, воды, песка и щебня (гравия), вначале устанавливают ориентировочно методом расчета, а затем уточняют испытанием пробных замесов бетонной смеси.
Расчет состава бетона производят в следующем порядке - определяют водоцементное соотношение, обеспечивающее получение бетона заданной прочности и расход воды; рассчитывают потребный расход цемента, а затем щебня (или гравия) и песка проверяют подвижность (жесткость) бетонной смеси при отклонениях этих показателей от проекта; производят корректирование состава бетонной смеси; приготовляют образцы для определения прочности и испытывают в заданные сроки; пересчитывают номинальный состав бетонной смеси на производственный. Определение расхода воды. Оптимальное количество воды в бетонной смеси (водосодержание, л/м3) должно обеспечивать необходимую подвижность (или жесткость) бетонной смеси. Количество воды для затвердения 1 м3 бетонной смеси для всех расчетов в соответствии с ОНТП 07—85 принимается равным 200 л независимо от вида, жесткости и подвижности бетонных смесей.
|
Определение расхода цемента. Расход цемента на 1 м3 бетона должен быть не ниже минимального. Если расход цемента на 1 м3 бетона окажется менее допустимого, то необходимо довести его до нормы или ввести тонкомолотую добавку. Определение расхода заполнителей (песка и щебня или гравия) на 1 м3 бетона. Проверка подвижности бетонной смеси. После произведенного предварительного расчета состава бетона делают пробный замес и определяют осадку конуса или жесткость. Если бетонная смесь получилась менее подвижной, чем требуется, то увеличивают количество цемента и воды без изменения цементно-водного отношения. Если подвижность будет больше требуемой, то добавляют небольшими порциями песок и крупный заполнитель, сохраняя соотношения их постоянными. Таким путем добиваются заданной подвижности бетонной смеси.
Уточнение расчетного состава бетона на пробных замесах. Производят опытные замесы бетона при трех значениях водоцементного отношения, из которых одно принимают расчетное, а два других больше или меньше на 10...20%. Количество цемента, воды, песка и щебня (гравия) для бетона с водоцементным отношением, не равным расчетному, определяют по вышеизложенному методу. Из каждой приготовленной смеси готовят по три образца куба размером 20×20×20 см, которые выдерживают в нормальных условиях и испытывают в возрасте 28 сут при определении класса бетона (или в другие сроки). По результатам испытаний строят график зависимости прочности бетона от цементно-водного отношения, с помощью которого выбирают Ц/В, обеспечивающее получение бетона заданной прочности.
При пробных замесах проверяют также подвижность или жесткость бетонной смеси (она должна удовлетворять проектной), определяют ее плотность и по результатам испытания пробных замесов вносят соответствующие коррективы в рассчитанный состав бетона. При изменении содержания песка и щебня(гравия) учитывают их влажность. Количество влажных заполнителей изменяется настолько, чтобы содержание в них сухого материала было равно расчетному, а количество вводимой в замес воды уменьшалось на величину, равную содержанию воды в заполнителях.
При перемешивании бетонной смеси мелкие зерна компонентов ее располагаются между более крупными, а пустоты в песке заполняются цементным тестом. Объем бетонной смеси поэтому будет всегда меньше, чем сумма насыпных объемов составляющих его сухих материалов. Коэффициент выхода бетона является технико-экономической характеристикой качества заполнителей и бетона. Чем выше коэффициент выхода, тем экономичнее бетон. Обычно для крупнозернистых бетонов р = 0,67...0,70 и для мелкозернистых р = 0,70...0,80.
Проектирование состава бетона проводится по расчетно-экспериментальному методу, предлагаемому «Руководством по проектированию составов тяжелого бетона» (М., Стройиздат, 1979 г.).
Состав бетона для пробных замесов рассчитывают в следующей последовательности: вычисляют В/Ц отношение, расход воды, расход цемента, после чего определяют расход крупного и мелкого заполнителя на 1 м3 бетонной смеси.
Водоцементное отношение В/Ц вычисляют исходя из требуемой марки бетона, активности цемента и с учетом вида и качества составляющих по следующим формулам:
Для бетонов с водоцементным отношением В/Ц ≥ 0,4
В/Ц = A × RЦ /(Rб + 0,5 А × RЦ) (3.1)
Для бетонов с водоцементным отношением В/Ц < 0,4
В / Ц = A1 × R Ц /(R б – 0,5 ×A1 × R Ц), (3.2)
где Rб – марка бетона, кг/см2,
Rц – активность цемента, кг/см2,
А и А1 – коэффициенты, учитывающие качество материалов, принимаются по таблице 3.1
Таблица 3.1 -
Качество заполнителей и цемента | А | А1 |
Высококачественные | 0,65 | 0,43 |
Рядовые | 0,6 | 0,4 |
Пониженного качества | 0,55 | 0,37 |
Примечание: 1. К высококачественным материалам относятся щебень из плотных горных пород высокой прочности, песок оптимальной крупности и портландцемент высокой активности без добавок или с минимальным количеством добавок, заполнители должны быть чистые и фракционные. 2. К рядовым материалам относятся заполнители среднего качества, в т.ч. гравий, портландцемент средней активности или высокомарочный шлакопортландцемент. 3. К материалам пониженного качества относятся заполнители низкой прочности, мелкие пески, цемент низкой активности.
Расход воды (водопотребность), л/м3, ориентировочно определяют исходя из заданной удобоукладываемости бетонной смеси по таблице, которая составлена с учетом вида и крупности зерен заполнителя:
Таблица 3.2 – Определение расхода воды по заданной удобоукладываемости
Жесткость стандартн., с | ОК, см | Расход воды, л/м3 при крупности, мм на 1 м3 бетона | |||||||
гравия | щебня | ||||||||
10 | 20 | 40 | 70 | 10 | 20 | 40 | 70 | ||
31 | - | 150 | 135 | 125 | 120 | 160 | 150 | 135 | 130 |
21-30 | - | 160 | 145 | 130 | 125 | 170 | 160 | 145 | 140 |
11-20 | - | 165 | 150 | 135 | 130 | 175 | 165 | 150 | 145 |
5-10 | - | 175 | 160 | 145 | 140 | 185 | 175 | 160 | 155 |
1-4 | 190 | 175 | 160 | 155 | 200 | 190 | 175 | 170 | |
5-9 | 200 | 185 | 170 | 165 | 210 | 200 | 185 | 180 | |
10-15 | 215 | 205 | 190 | 180 | 225 | 215 | 200 | 190 | |
12-16 | 225 | 220 | 205 | 195 | 235 | 230 | 215 | 205 |
Примечание: Таблица составлена для цемента с нормальной густотой теста 26-28 % и песка Мкр = 2. При изменении нормальной густоты цементного теста на каждый процент в меньшую сторону расход воды следует уменьшать на 3-5 л/м3, в большую сторону – увеличивать на то же значение. В случае изменения модуля крупности песка в меньшую сторону на каждые 0,5 его значения – необходимо увеличивать, а в большую сторону – уменьшать расход воды на 3-5 л/м3.
Если применяют песок с водопотребностью свыше 7 %, то расход водыувеличивают на 5 л. на каждый процент увеличения водопотребности, если ниже 7% - то уменьшают на 5 л. за каждый процент. При расходе цемента свыше 400 кг расход воды увеличивают на 100 л. на каждые 100 кг. цемента. В целом водопотребность песка и щебня можно посчитать по методике, предложенной в (1, стр.42).
Водопотребность легкого песка и щебня определяют в растворе и бетоне через 30 мин после их изготовления. Водопотребность легких заполнителей колеблется в широких пределах и может достигать для песка 30%, а для щебня —20%. Влияние заполнителя на прочность раствора и бетона можно приблизительно оценить по результатам испытаний раствора и бетона, приготовленных на исследуемых заполнителях (при прочих равных условиях), и по значению коэффициента прочности А в известной формуле прочности бетона
(3.3)
По расходу воды определяется расход цемента:
(3.4)
Если расход цемента на 1 м3 бетона снижается меньше минимально допустимого (см. таблицу), то из условия получения плотного нерасслаиваемого бетона расход цемента увеличивают до нормы или вводят тонкомолотую добавку:
Таблица 3.3 -
Смесь | Минимальный расход цемента, кг/м3, при крупн. запол. | |||
10 | 20 | 40 | 70 | |
Особо жесткая (Ж>20c) | 160 | 150 | 140 | 130 |
Жесткая (Ж=10…20с) | 180 | 160 | 150 | 140 |
Малоподвижная (Ж=5…10) | 200 | 180 | 160 | 150 |
Подвижная (ОК=1…10см) | 220 | 200 | 180 | 160 |
Очень подвижная (ОК=10…16см) | 240 | 220 | 210 | 180 |
Литая (ОК>16cм) | 250 | 230 | 200 | 190 |
В качестве тонкомолотых добавок рекомендуется использовать молотую золу, молотый кварцевый песок, известняковую муку и др. Для экономичного расходования цемента необходимо, что бы его марка превышала заданную марку бетона (см. гл. 2). Расход заполнителей (песка, щебня или гравия), кг/м3 бетона вычисляют исходя из двух условий:
- сумма абсолютных объемов всех компонентов бетона равна 1 м3 уплотненной бетонной смеси, т.е.:
или
(3.5)
- цементно – песчаный раствор заполняет пустоты в крупном заполнителе с некоторой раздвижкой зерен, т.е.:
или
(3.6)
где Q – коэффициент раздвижки зерен щебня (гравия).
Коэффициент раздвижки зерен щебня (гравия) принимается по таблице в зависимости от расхода цемента на 1 м3 бетонной смеси и В/Ц отношения:
Таблица 3.4 – Зависимость коэффициента раздвижки зерен щебня (гравия) от расхода цемента
Расход цемента, кг/м3 | Оптимальное значения коэфф. Q при В/Ц | ||||
0,4 | 0,5 | 0,6 | 0,7 | 0,8 | |
250 | --- | --- | 1,26 | 1,32 | 1,38 |
300 | --- | 1,3 | 1,36 | 1,42 | --- |
350 | 1,32 | 1,38 | 1,44 | --- | --- |
400 | 1,4 | 1,46 | --- | --- | --- |
500 | 1,5 | 1,56 | --- | --- | --- |
Примечание: 1. При других значениях Ц и В/Ц коэффициент Q находят интерполяцией. 2. Значения коэффициента Q даны при водопотребности песка равном 7 %; если водопотребность используемого мелкого песка более 7 %, коэффициент Q уменьшают на 0,03 на каждый процент увеличения водопотребности, если водопотребность крупного песка менее 7 %, коэффициент Q увеличивается на 0,03 на каждый процент уменьшения водопотребности песка.
Для жестких бетонных смесей при расходе цемента менее 400 кг/м3 коэффициент Q следует принимать 1,05-1,15 (в среднем 1,1). Меньшее значение – 1,05 принимается в случае использования мелких песков.
Решая совместно уравнения 3.5 и 3.6, находят формулу для определения расхода щебня (гравия) в кг на 1 м3 бетона:
или
(3.7)
После определения расхода щебня (гравия) рассчитывают расход песка, кг,/м3:
или
(3.8)
После выполнения расчета состава бетона готовят пробный замес и определяют его подвижность или жесткость. Если бетонная смесь получилась менее подвижной, чем требуется, то увеличивают количество цемента порциями по 10% первоначального и добавляют в соответствии с В/Ц необходимое количество воды. В том случае, когда подвижность смеси получилась более требуемой, добавляют небольшими порциями песок и крупный заполнитель, сохраняя соотношение их постоянным.
Для уточнения состава бетона рекомендуется готовить по два пробных замеса при изменении В/Ц на 15...30 % в большую сторону и соответственно два замеса – в меньшую сторону. Для этих четырех дополнительных составов производят расчет аналогично приведенному выше. Затем из бетонных смесей каждого замеса изготавливают по три контрольных образца, которые испытывают на сжатие через 28 сут. нормального твердения. По результатам испытаний строят график Rб = f(В/Ц), по которому выбирают В/Ц, обеспечивающее получение бетона заданной марки.
Пример. Определить состав бетона марки М 300 при жесткости бетонной смеси 15 по стандартному вискозиметру.
Материалы: портландцемент марки 375 кг/см2, истинной плотностью 3100 кг/см3, песок средней крупности с водопотребностью 7 % и истинной плотностью 2630 кг/см3, гранитный щебень крупностью 40 мм, пустотностью 0,43, и истинной плотностью 2600 кг/см3.
Насыпная плотность гранитного щебня определяется по формуле
плпщ = (1- V ПЩ) × плПЩ = (1-0,43)×2600 = 1482 ≈ 1480 кг/см3. (3.9)
По формуле 3.1 определяем водоцементное отношение для В/Ц≥0,4:
В/Ц = А × RЦ /(Rб + 0,5А × RЦ )
В зависимости от качества материалов по таблице 3.1 принимаем коэффициент
А = 0,6, тогда
В/Ц = 0,6 × 375 /(300 + 0,5×0,6 × 375) = 0,54
По таблице 3.2 определяем расход воды для данной жесткости и крупности щебня 155 л.
Определяем расход цемента по формуле 3.4:
Ц = В: В/Ц = 155: 0,54 = 287 кг/м3
Коэффициент раздвижки для жесткой бетонной смеси принимаем равным Q = 1,1.
Определяем расход щебня по формуле 3.7:
Щ = 1/[(Q×VПЩ /плпщ) + 1/плПЩ] = 1/[(1,1×0,43/1480) + 1/2600] = 1428,6 кг/м3
Определяем расход песка по формуле 3.8:
П = [1-(Ц/плЦ + В/плВ + Щ/плЩ)] × плП = [1-(287/3100 + 155/1000 +1428,6/2600)]*2630 = 534 кг/м3
Расчетная масса бетонной смеси составляет:
Ц + В + П + Щ = 287+155+1429+534=2405 кг/м3. (3.10)
Таблица 3.5 – Исходные данные
Вариант | Марка бетона | Цемент | Щебень | Песок | ||||
Марка, кг/см2 | Истинная плотность, кг/см3 | Истинная плотность кг/см3 | Крупность, мм | Пустотность | Истинная плотность, кг/см3 | Водопотребность, % | ||
1 | М100 | 300 | 2800 | 2600 | 30 | 0,4 | 2580 | 5,5 |
2 | М150 | 350 | 3000 | 2900 | 40 | 0,45 | 2730 | 7,3 |
3 | М200 | 375 | 2650 | 2700 | 50 | 0,5 | 2600 | 8,3 |
4 | М250 | 300 | 2900 | 2650 | 45 | 0,38 | 2650 | 10,1 |
5 | М300 | 400 | 3100 | 2750 | 55 | 0,47 | 2700 | 9,7 |
6 | М350 | 450 | 3300 | 2650 | 40 | 0,41 | 2610 | 6,8 |
7 | М400 | 475 | 3500 | 2850 | 35 | 0,35 | 2660 | 11,4 |
8 | М450 | 500 | 3600 | 2600 | 55 | 0,52 | 2630 | 9,6 |
9 | М550 | 550 | 3100 | 2850 | 40 | 0,43 | 2720 | 7,8 |
10 | М600 | 700 | 3300 | 2700 | 35 | 0,39 | 2590 | 6,5 |
Лабораторная работа №4
Лабораторная работа №5
Лабораторная работа №6
Строповка грузов
Строп - грузозахватное приспособление, выполняемое обычно из каната или цепи (одна или несколько ветвей), снабженное на конце крюком, скобой, кольцом и т.п. Грузовые стропы должны изготавливаться в соответствии с требованиями РД 10-231-98, Правил устройства и безопасной эксплуатации грузоподъемных кранов, а также конструкторской документации, утвержденной в установленном порядке.
Проектирование и изготовление грузовых стропов проводится в организациях и на предприятиях, имеющих разрешение (лицензию) органов Росехнадзора РФ и располагающих квалифицированными специалистами и техническими средствами, обеспечивающими проектирование и изготовление стропов в полном соответствии с требованиями настоящего нормативного документа.
Расчет канатов и цепей стропов, используемых как для непосредственной обвязки груза, так и для захвата последнего с помощью концевых звеньев, производят на растяжение.
Определение усилий в канатах и цепях двух-, трех- и четырехветвевых стропов при отсутствии дополнительных требований производят исходя из условия, что углы между ветвями не превышают 90°(рис.1).
Рисунок 6.1 - Строповка груза двух- (а), трех- (б) и четырехветвевыми (в) стропами
Расчет трех- и четырехветвевых стропов при отсутствии гарантии равномерности распределения нагрузок между ветвями производят исходя из условия, что груз удерживается только двумя ветвями.
При расчете на действие номинальной нагрузки запас прочности для канатов и цепей по отношению к разрушающей нагрузке, указанной в их сертификате, должен быть не менее 6,0 и 5,0 соответственно.
Отклонение длины ветвей, используемых для комплектации одного стропа, не должно превышать 1% длины ветви.
В канатных стропах должны применяться круглопрядные канаты двойной свивки, изготавливаемые по техническим условиям ГОСТ 3241.
Применяют канат крестовой свивки с сердечником из пеньки, сизаля и хлопчатобумажной пряжи. Допустимо применение канатов с сердечниками из других материалов с учетом температурного режима использования стропов.
Рекомендуется применять канаты по ГОСТ 3071, ГОСТ 3079, ГОСТ 2688 и ГОСТ 7668, а для перемещения грузов, имеющих температуру до 400 °С, - по ГОСТ 7669.
Пример:
Подобрать диаметр стального каната для подъема железобетонной шатровой панели весом 4,5 т самоуравновешивающимся стропом при отклонении ветвей его от вертикали на 45°. Расчетный предел прочности проволок троса 150 кгс/мм2.
Усилие в одной ветви стропа
, Н, (6.1)
где Q – вес поднимаемого груза, Н;
α – угол отклонения ветвей стропа от вертикали, град;
n – количество рабочих ветвей каната, шт.
, Н,
Расчетное разрывное усилие каната определяется условием
, (6.2)
где К – коэффициент запаса прочности (для стропов с крюками К=6; для универсальных стропов К=8).
, Н.
Принимаем для стропов канат типа ТК с органическим сердечником (ГОСТ 3071-88). По таблице 6.2 подбираем ближайшее значение разрывного усилия 110 000Н, а по нему – диаметр каната 15,5 мм.
Задание: Подобрать диаметр стального каната для подъема железобетонной шатровой панели. Исходные данные принять по вариантам табл. 6.1.
Таблица 6.1 – Исходные данные по вариантам
Вариант | Вес груза, т | Угол отклонения ветвей от вертикали, град | Количество рабочих ветвей стропа, шт. |
1 | 2,75 | 45 | 4 |
2 | 3,1 | 25 | 3 |
3 | 4,8 | 35 | 4 |
4 | 5,6 | 30 | 2 |
5 | 4,12 | 27 | 4 |
6 | 1,58 | 40 | 3 |
7 | 8,3 | 37 | 4 |
8 | 3,5 | 22 | 2 |
9 | 6,79 | 50 | 3 |
10 | 5,8 | 46 | 4 |
Таблица 6.2 – Прочностные свойства канатов различных сечений согласно ГОСТ 3071-88
Диаметр, мм | Расчетная площадь сечения всех проволок в канате, мм2 | Ориентир. масса | Маркировочная группа, Н/мм2 (кгс/мм2) | |||||||||||||||||
каната | проволоки | 1570 (160) | 1670 (170) | 1770 (180) | 1860 (190) | 1960 (200) | 2060 (210) | 2160 (220) | ||||||||||||
центральной | в слоях | Расчетное разрывное усилие, Н, не менее | ||||||||||||||||||
6 проволок | 216 проволок | суммарное всех проволок в канате | каната в целом | суммарное всех проволок в канате | каната в целом | суммарное всех проволок в канате | каната в целом | суммарное всех проволок в канате | каната в целом | суммарное всех проволок в канате | каната в целом | суммарное всех проволок в канате | каната в целом | суммарное всех проволок в канате | каната в целом | |||||
5,0 | 0,24 | 0,22 | 8,48 | 82,5 | - | - | - | - | 14950 | 12250 | 15750 | 12900 | 16600 | 13600 | 17460 | 14300 | 18250 | 14950 | ||
5,4 | 0,26 | 0,24 | 10,08 | 98,1 | - | - | - | - | 17750 | 14550 | 18750 | 15350 | 19750 | 16150 | 20700 | 16950 | 21700 | 17750 | ||
5,8 | 0,28 | 0,26 | 11,84 | 115,5 | - | - | - | - | 20850 | 17050 | 22000 | 18000 | 23200 | 19000 | 24350 | 19950 | 25500 | 20900 | ||
6,3 | 0,30 | 0,28 | 13,73 | 134,0 | - | - | - | - | 24200 | 19800 | 25550 | 20950 | 26900 | 22050 | 28250 | 23150 | 29600 | 24250 | ||
6,7 | 0,32 | 0,30 | 15,75 | 153,5 | 24650 | 20200 | 26200 | 21450 | 27750 | 22750 | 29300 | 24000 | 30850 | 25250 | 32400 | 26550 | 33950 | 27800 | ||
7,6 | 0,36 | 0,34 | 20,22 | 197,0 | 31700 | 25950 | 33650 | 27550 | 35650 | 29200 | 37600 | 30800 | 39600 | 32450 | 41600 | 34100 | 43550 | 35700 | ||
8,5 | 0,40 | 0,38 | 25,25 | 246,0 | 39550 | 32400 | 42050 | 34450 | 44500 | 36450 | 47000 | 38500 | 49450 | 40500 | 51950 | 42550 | 54400 | 44600 | ||
9,0 | 0,45 | 0,40 | 28,10 | 273,5 | 44050 | 36120 | 46800 | 38350 | 49550 | 40600 | 52300 | 42850 | 55050 | 45100 | 57800 | 4735
![]() Общие условия выбора системы дренажа: Система дренажа выбирается в зависимости от характера защищаемого... ![]() История развития хранилищ для нефти: Первые склады нефти появились в XVII веке. Они представляли собой землянные ямы-амбара глубиной 4…5 м... ![]() Организация стока поверхностных вод: Наибольшее количество влаги на земном шаре испаряется с поверхности морей и океанов (88‰)... ![]() Поперечные профили набережных и береговой полосы: На городских территориях берегоукрепление проектируют с учетом технических и экономических требований, но особое значение придают эстетическим... © cyberpedia.su 2017-2024 - Не является автором материалов. Исключительное право сохранено за автором текста. |