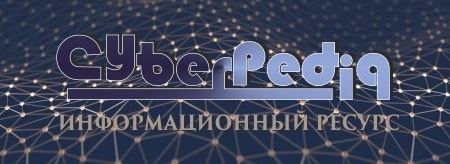
Состав сооружений: решетки и песколовки: Решетки – это первое устройство в схеме очистных сооружений. Они представляют...
Индивидуальные очистные сооружения: К классу индивидуальных очистных сооружений относят сооружения, пропускная способность которых...
Топ:
Когда производится ограждение поезда, остановившегося на перегоне: Во всех случаях немедленно должно быть ограждено место препятствия для движения поездов на смежном пути двухпутного...
Проблема типологии научных революций: Глобальные научные революции и типы научной рациональности...
Интересное:
Влияние предпринимательской среды на эффективное функционирование предприятия: Предпринимательская среда – это совокупность внешних и внутренних факторов, оказывающих влияние на функционирование фирмы...
Инженерная защита территорий, зданий и сооружений от опасных геологических процессов: Изучение оползневых явлений, оценка устойчивости склонов и проектирование противооползневых сооружений — актуальнейшие задачи, стоящие перед отечественными...
Уполаживание и террасирование склонов: Если глубина оврага более 5 м необходимо устройство берм. Варианты использования оврагов для градостроительных целей...
Дисциплины:
![]() |
![]() |
5.00
из
|
Заказать работу |
Для определения вида и метода получения заготовки предварительно использованы коды четырех основных показателей детали:
- код материала;
- код конструктивной формы;
- код серийности;
- код массы.
Все значения представлены из таблицы справочника. Полученные данные сведены в таблицу 7.
Таблица 7 – Основные показатели детали
Коды | |||
Материал | Конструктивная форма | Серийность | Масса |
1 | 6 | 3 | 5 |
Виды заготовки:
– Сортовой горячекатаный прокат;
– Литье по выплавляемым моделям.
Для выбора и обоснования метода получения заготовки выполняется сравнительная характеристика методов получения заготовки и рассчитывается коэффициент использования материалов (см. таблицу 8).
Таблица 8 – Сравнительная характеристика методов получения заготовки.
Характеристика методов | Методы получения заготовки | |
Сортовой горячекатаный прокат | Литье по выплавляемым моделям | |
Качественные и количественные показатели заготовки | ||
Достигаемая точность | 9 – 14 класс | 16 – 17 класс и выше |
Шероховатость поверхностей заготовки | Rz 2,5 – 20 | Rz 2,5 - 20 |
Величина припусков | 1 – 12 мм | 3 – 5 мм |
Область применения: по материалу
по типу производства | Сталь, чугун, цветные металлы и сплавы | Высоко-легированные трудно-обрабатываемые стали. |
Все типы производства | Серийное и массовое | |
Производительность метода | 50-70% выход готовой заготовки | 10-20% выход готовой заготовки |
Для принятия окончательного решения выбора метода получения заготовки рассчитан коэффициент использования материала для каждого вида заготовки:
Ким= , (5)
где - масса детали, кг;
mз – масса заготовки, кг.
Масса заготовок определена путем анализа 3D модели детали в системе автоматизированного проектирования «Компас 3D»:
1) для сортового горячекатаного проката масса – 68,23 кг;
2) для литья по выплавляемым моделям масса – 61,05 кг.
Коэффициент использования материала:
- Сортовой горячекатаный прокат:
Ким= =
=0,76*100=76 %;
- Литье по выплавляемым моделям;
Ким= =
=0,85*100=85 %.
Все значения представлены в таблице 9.
Таблица 9 – Сравнительная таблица коэффициентов использования материала при выбранных методах получения заготовки
Показатели | Сортовой горячекатаный прокат | Литье по выплавляемым моделям |
Масса детали, кг | 51,95 | 51,95 |
Масса заготовки, кг | 68,23 | 61,05 |
Коэффициент использования, % | 76 | 85 |
Вывод: расход материала при литье по выплавляемым моделям меньше, чем при сортовом горячекатаном прокате; масса заготовки у литья по выплавляемым моделям меньше, чем у сортового горячекатаного проката, т.к. по выплавляемым моделям по форме приближено к готовой детали. Но использование заготовок из литья по выплавляемым моделям нецелесообразно по причине своей дороговизны изготовления. Исходя из полученных данных выбран метод сортового горячекатаного проката.
Особенности сооружения опор в сложных условиях: Сооружение ВЛ в районах с суровыми климатическими и тяжелыми геологическими условиями...
Организация стока поверхностных вод: Наибольшее количество влаги на земном шаре испаряется с поверхности морей и океанов (88‰)...
Наброски и зарисовки растений, плодов, цветов: Освоить конструктивное построение структуры дерева через зарисовки отдельных деревьев, группы деревьев...
Двойное оплодотворение у цветковых растений: Оплодотворение - это процесс слияния мужской и женской половых клеток с образованием зиготы...
© cyberpedia.su 2017-2024 - Не является автором материалов. Исключительное право сохранено за автором текста.
Если вы не хотите, чтобы данный материал был у нас на сайте, перейдите по ссылке: Нарушение авторских прав. Мы поможем в написании вашей работы!