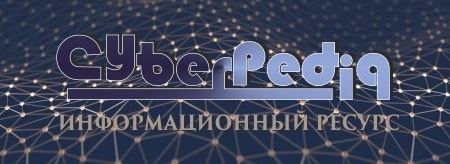
История создания датчика движения: Первый прибор для обнаружения движения был изобретен немецким физиком Генрихом Герцем...
Состав сооружений: решетки и песколовки: Решетки – это первое устройство в схеме очистных сооружений. Они представляют...
Топ:
Теоретическая значимость работы: Описание теоретической значимости (ценности) результатов исследования должно присутствовать во введении...
Комплексной системы оценки состояния охраны труда на производственном объекте (КСОТ-П): Цели и задачи Комплексной системы оценки состояния охраны труда и определению факторов рисков по охране труда...
Эволюция кровеносной системы позвоночных животных: Биологическая эволюция – необратимый процесс исторического развития живой природы...
Интересное:
Распространение рака на другие отдаленные от желудка органы: Характерных симптомов рака желудка не существует. Выраженные симптомы появляются, когда опухоль...
Национальное богатство страны и его составляющие: для оценки элементов национального богатства используются...
Как мы говорим и как мы слушаем: общение можно сравнить с огромным зонтиком, под которым скрыто все...
Дисциплины:
![]() |
![]() |
5.00
из
|
Заказать работу |
|
|
Бункера для хранения сырьевых материалов
Расходные количества кусковых или порошкообразных материалов обычно хранят в железобетонных или стальных бункерах. Форму и размеры бункеров, угол наклона стенок и размер выходного отверстия выбираем в соответствии со свойствами материала, подлежащего хранению.
Требуемый геометрический объем бункера V0 определяется по формуле:
,
где Кз – коэффициент заполнения (принимается равным 0,85 – 0,90).
При помоле влажных материалов часовую производительность мельницы по данному компоненту необходимо пересчитать на влажный материал:
,
где Qисп – производительность установки по исходному материалу, т/ч; w1 и w2– соответственно начальная и конечная влажность материала, %.
Для известняка:
[т/час]
Для глины:
[т/час]
Полезная емкость бункера Vб рассчитывается по формуле:
,
где Q – часовая производительность мельницы по данному компоненту, т/час; – насыпная масса, т/м3; τ – нормативное время запаса материала в бункере, час. (2 – 10 ч.).
Для известняка:
[м3]
Для глины:
[м3]
Тогда требуемый геометрический объем бункера равен:
Для известняка:
[м3]
Для глины:
[м3]
Так как угол естественного откоса глины и известняка равен 450, то угол наклона стенок бункера должен быть не менее 600.
Дозаторы и питатели материалов
Точное дозирование отдельных компонентов сырьевой смеси является одним из факторов, определяющих качество конечного продукта – портландцемента. Равномерная и бесперебойная подача сырьевых материалов обеспечивает однородность состава сырьевой смеси, высокопроизводительную работу мельниц и минимальный расход электроэнергии на помол.
Мелкокусковые и дисперсные непластичные материалы дозируют объемным или весовым методом.
|
Тип питателя выбирается в соответствии с требуемой производительностью, размером куска подаваемого материала, его физико-механическими свойствами, а также в соответствии с необходимой точностью дозирования. Наибольшее распространение для дозирования сырьевых материалов в цементной промышленности получили тарельчатые, ленточные или пластинчатые питатели объемного дозирования, а также автоматические ленточные дозаторы-питатели весового дозирования.
Для данной технологической линии выбираем тарельчатые питатели, так как они просты в обслуживании и регулировании количества подаваемого материала.
Тарельчатый питатель
Тип тарельчатого питателя выбирается по его объёмной производительности, а затем его массовая производительность проверяется по формуле:
,
где - производительность питателя, т/ч;
- радиус диска питателя, м;
- радиус верхней кромки конуса материала, м;
;
- высота кольца материала, сбрасываемого ножом с диска, м;
м;
- скорость вращения диска питателя, мин-1;
- насыпная масса материала, т/м3;
Для известняка:
Выбираем тарельчатый питатель ДЛ-10А со следующими характеристиками:
Параметр | Тип питателя |
ДЛ-10А | |
Диаметр диска, мм | 1000 |
Скорость вращения диска питателя, мин-1 | 7 – 11 |
Производительность, м3/ч | 28 |
Максимальный размер куска материала, мм | 50 |
Габаритные размеры, мм: | |
высота | 1300 |
длина | 1250 |
ширина | 1150 |
Мощность электродвигателя, кВт | 2,2 |
Масса питателя, т | 1,30 |
т/ч, что больше требуемой производительности (39,6 т/ч).
Для глины:
Выбираем тарельчатый питатель ДЛ-8А со следующими характеристиками:
Параметр | Тип питателя |
ДЛ-8А | |
Диаметр диска, мм | 800 |
Скорость вращения диска питателя, мин-1 | 7 – 11 |
Производительность, м3/ч | 13 |
Максимальный размер куска материала, мм | 40 |
Габаритные размеры, мм: | |
высота | 1150 |
длина | 1050 |
ширина | 1000 |
Мощность электродвигателя, кВт | 1,5 |
Масса питателя, т | 0,60 |
|
т/ч, т/ч, что больше требуемой производительности (13,7 т/ч)
Внутрицеховой транспорт
Для работы основного технологического оборудования необходимо обеспечить бесперебойный и непрерывный внутрицеховой транспорт перерабатываемых материалов. Выбор вида внутрицехового транспорта зависит от расстояния и направления транспортировки, а также от физических свойств перемещаемых материалов.
Наибольшее распространение в качестве внутрицехового транспорта в цементной промышленности получили ленточные конвейеры, скребковые транспортеры, ковшовые элеваторы, винтовые транспортеры (шнеки) и пневматические транспортные желоба (аэрожелоба).
Ленточный конвейер
Для транспортирования сыпучих и кусковых материалов в горизонтальной и наклонной плоскостях в цементной промышленности широко используют ленточные конвейеры с плоской и желобчатой лентой. Ширина ленточных конвейеров, выпускаемых промышленностью, нормализована: 400, 500, 650, 800, 1000, 1200, 1400, 1600, 2000, 2500 и 3000 мм.
Для транспортирования материалов после дозаторов выбираем конвейер с желобчатой лентой, так как при её использовании отсутствует риск просыпания материала в процессе движения.
Ширина желобчатой ленты рассчитывается по формуле:
, м
где ν – скорость движения ленты, м/с; γн – насыпная масса материала, т/м3;
Массовая производительность конвейера:
, т/ч
Расчетная производительность
, т/ч
, т/м3
, м
Выбираем транспортер с шириной ленты 400 мм.
Винтовой транспортер
Винтовые транспортеры (шнеки) применяются для транспортирования пылевидных, порошкообразных и мелкокусковых (реже) материалов на расстояние до 100 метров по горизонтали и под углом до 20˚ к горизонту. Шнеками нецелесообразно транспортировать липкие, уплотняющиеся, а также высокоабразивные материалы.
Внешний диаметр шнека нормализован. Промышленностью выпускаются шнеки диаметром 100, 125, 160, 200, 320, 400, 500, 600, 650 и 800 мм. Шаг винтовых лопастей составляет 0,8 – 1,0 от диаметра шнека. Диаметр шнека должен не менее чем в 4 раза превышать максимальные размеры куска транспортируемого материала.
Винтовой транспортер выбирается по диаметру шнека, а затем его производительность проверяется по формуле:
,
где Q – производительность транспортера, т/час; D – диаметр шнека, м; S – шаг шнека, м; n – число оборотов вала, мин-1; ψ – коэффициент заполнения желоба (0,25 – 0,40); γн – насыпная масса материала, т/м3; К – коэффициент, зависящий от угла наклона транспортера.
|
Выбираем шнек для транспортировки крупки из сепаратора в мельницу.
,
где Qвх – количество материала на входе в сепаратор; Qт.ф. – количество тонкой фракции (готового продукта); Ц – циркуляционная нагрузка сепаратора.
Qвинт. тр. = Qт.ф.(Ц – 1) = 52∙(1,5 – 1) = 26 т/ч.
Диаметр шнека 320 мм.
Производительность транспортера:
т/час
Выбираем шнек для транспортировки сырьевой муки из циклонов НИИОГаз и электрофильтра в силос..
Необходимая производительность транспортера Q = 52 т/ч
Расчетная производительность Qрасч = 52 ∙ 1,3 = 67,6 т/ч
Диаметр шнека 400 мм.
Производительность транспортера:
т/час
6.3.3 Пневмовинтовой насос.
Для подачи готовой сырьевой смеси в силос выбираем пневмовинтовой насос, т.к. он позволяет перемещать материал на расстояние до 450 м, и высоту до 35 м. Преимуществами пневмовинтового насоса являются герметичность и гибкость трасс, независимость от погодных условий, возможность полной автоматизации процесса и небольшие капитальные затраты на строительство. Также достоинствами этого устройства являются непрерывность процесса транспортирования, небольшие габариты, простота управления.
Необходимая производительность насоса Q = 52 т/ч
По данным таблицы 23 выбираем насос ТА–40. Его характеристики:
Производитель- ность, т/ч | Дальность транспортировки, м | Максимальная высота подачи, м | Диаметр трубопровода, мм | Давление воздуха, МПа | Мощность двигателя, кВт |
63 | 230 | 30 | 175 | 0,3 | 55 |
Сепаратор
Для разделения материала на фракции в помольно-сушильных установках используются воздушно-проходные и центробежные сепараторы. Важнейшими характеристиками сепаратора являются циркуляционная нагрузка и коэффициент полезного действия сепаратора. Циркуляционная нагрузка сепаратора определяется как отношение количества материала на входе в сепаратор Qвх. к количеству тонкой фракции Qтф., которая для большинства схем равна заданной производительности мельницы Q:
|
В данной схеме помола необходимо использовать воздушно-проходной сепаратор, т.к. материал из мельницы в сепаратор выносится потоком сушильного агента. Достоинством данного агрегата является крайняя простота устройства
Выбор воздушно-проходного сепаратора производится по его объему и диаметру входного патрубка, которые рассчитываются по формулам:
;
,
где – объем сепаратора, м3;
г – объем газов, проходящих через сепаратор, м3/ч;
г принимается равным часовому расходу сушильного агента; q – напряжение объема сепаратора по газу, м3/(м3∙ч); в зависимости от тонкости помола сырья при остатке на сите № 008 1-5% q = 2000, 5-10% - 2500, 10-15% - 3000 и 15-20% - 3500; d – диаметр входного патрубка, м; Vсек – скорость газов в верхней части внешнего корпуса сепаратора, м/с.
м3,
м.
Характеристики выбранного ВПС:
Объем сепаратора – 22 м3;
Диаметр сепаратора – 4 м;
Диаметр входного патрубка – 0,95 м
6.5 Оборудование для обеспыливания воздуха и газов
Дробильные, помольные, обжиговые и прочие агрегаты цементной промышленности снабжаются устройствами для очистки и обеспыливания аспирационного воздуха или отходящих газов. Гранулометрический состав пыли очень разнообразен. Наряду с крупными (более 100 мкм) частицами обычно присутствуют и мелкие (менее 1 – 10 мкм) частицы пыли, что делает необходимым установку нескольких обеспыливающих агрегатов, работающих последовательно. Применение того или иного обеспыливающего агрегата зависит от целого ряда факторов:
· объема обеспыливающего воздуха или газа;
· температуры, влажности и запыленности воздуха или газа;
· физико-химических свойств пыли;
· степени очистки газов в агрегате и т. п.
Все пылеулавливающие устройства характеризуются степенью очистки газа или коэффициентом полезного действия:
,
где и
– концентрация пыли в газах соответственно до и после аппарата, г/м3.
Циклоны
Циклоны используются, как правило, для предварительной очистки газов, хотя некоторые из них, например батарейные, имеют высокий коэффициент полезного действия и могут применяться для окончательной очистки запыленных газов.
Наибольшее распространение в цементной промышленности получили циклоны типа ЦККБ и НИИОГаз.
Циклоны типа ЦККБ устанавливают на первом этапе пылеочистки. Они характеризуются сравнительно малой высотой цилиндрической и конической части. Коэффициент полезного действия циклонов ЦККБ не превышает 75 – 80%.
6.5.1.1 Расчет камеры предварительной подсушки (циклон ЦККБ).
Внутренний диаметр:
м,
Высота циклона:
м,
Ширина входного патрубка циклона:
м.
Расчет циклонов НИИОГаз
Так как эффективность групповых циклонов выше по сравнению с одиночными, то выбираем группу из 4-х циклонов НИИОГаз.
|
Диаметр циклонов:
м.
Общая высота циклона составляет:
м.
Электрофильтр
Для окончательной очистки газов используем электрофильтр, т.к. газы содержат большое количество трехатомных газов (H2O, CO2), которые легко ионизируются, повышая эффективность пылеочистки.
Площадь активного сечения электрофильтра:
м2,
где W – скорость газов в сечении фильтра.
По данным таблицы 30 выбираем электрофильтр УГ2–3–37. Его характеристики:
Площадь активного сечения, м2 | Число полей | Площадь осадительных электродов, м2 | Габариты, длина×высота×ширина, м |
37 | 4 | 3150 | 18,6×15,4×6,0 |
Дымососы
Вентиляторы предназначены для эвакуации из дробилок, мельниц, силосов и т. п. запыленного воздуха. По принципу действия различают вентиляторы осевые и центробежные. Осевые применяют для перемещения относительно больших количеств воздуха при небольшом давлении (разрежении) – до 500 – 700 Па, а центробежные используются при значительных давлениях (разрежениях) – до 3 кПа. При выборе вентилятора или дымососа их производительность может быть увеличена за счет изменения числа оборотов ротора:
,
где – необходимая производительность, м3/час;
– паспортная производительность, м3/час; n2 – необходимое число оборотов ротора, мин-1; n1 – паспортное значение числа оборотов ротора, мин-1.
Выбираем мельничный вентилятор типа ДН–19,5. Технические характеристики вентилятора:
Тип вентилятора | ДН–19,5 |
Производительность, м3/ч | 82000 |
Напор, кПа | 270 |
Мощность двигателя, кВт | 72 |
Частота вращения ротора, мин-1 | 750 |
Необходимое число оборотов ротора дымососа
об/мин
|
|
Двойное оплодотворение у цветковых растений: Оплодотворение - это процесс слияния мужской и женской половых клеток с образованием зиготы...
Архитектура электронного правительства: Единая архитектура – это методологический подход при создании системы управления государства, который строится...
Индивидуальные очистные сооружения: К классу индивидуальных очистных сооружений относят сооружения, пропускная способность которых...
Наброски и зарисовки растений, плодов, цветов: Освоить конструктивное построение структуры дерева через зарисовки отдельных деревьев, группы деревьев...
© cyberpedia.su 2017-2024 - Не является автором материалов. Исключительное право сохранено за автором текста.
Если вы не хотите, чтобы данный материал был у нас на сайте, перейдите по ссылке: Нарушение авторских прав. Мы поможем в написании вашей работы!