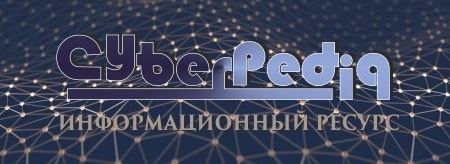
Архитектура электронного правительства: Единая архитектура – это методологический подход при создании системы управления государства, который строится...
Механическое удерживание земляных масс: Механическое удерживание земляных масс на склоне обеспечивают контрфорсными сооружениями различных конструкций...
Топ:
Отражение на счетах бухгалтерского учета процесса приобретения: Процесс заготовления представляет систему экономических событий, включающих приобретение организацией у поставщиков сырья...
Основы обеспечения единства измерений: Обеспечение единства измерений - деятельность метрологических служб, направленная на достижение...
Выпускная квалификационная работа: Основная часть ВКР, как правило, состоит из двух-трех глав, каждая из которых, в свою очередь...
Интересное:
Берегоукрепление оползневых склонов: На прибрежных склонах основной причиной развития оползневых процессов является подмыв водами рек естественных склонов...
Подходы к решению темы фильма: Существует три основных типа исторического фильма, имеющих между собой много общего...
Отражение на счетах бухгалтерского учета процесса приобретения: Процесс заготовления представляет систему экономических событий, включающих приобретение организацией у поставщиков сырья...
Дисциплины:
![]() |
![]() |
5.00
из
|
Заказать работу |
|
|
ПОЯСНИТЕЛЬНАЯ ЗАПИСКА
к курсовому проекту на тему:
«Агрегатно-поточная линия помола сырья с одновременной сушкой производительностью 52 т/ч (схема №3)»
Выполнил:
студент гр. С-43
Котов В. А.
Проверил:
Сивков С. П.
Москва 2011
Содержание
| стр. | ||||||
Введение | ……………………………………………………………………………………... | 3 | |||||
1 | Выбор рациональной технологической схемы помола сырьевых материалов……... | 4 | |||||
2 | Предварительный расчёт и выбор типоразмера помольно-сушильной установки… | 5 | |||||
3 | Проверочный расчёт мельницы………………………………………………………... | 6 | |||||
4 | Теплотехнический расчёт помольно-сушильной установки………………………… | 9 | |||||
4.1 | Расчёт процесса горения топлива………………………………………………... | 9 | |||||
4.2 | Расчёт параметров сушильного агента…………………………………………... | 10 | |||||
4.3 | Расчёт теплового баланса процесса сушки……………………………………… | 12 | |||||
5 | Технологическая схема помола сырья с одновременной сушкой…………………… | 16 | |||||
6 | Выбор и проверочный расчёт вспомогательного оборудования…………………….. | 17 | |||||
6.1 | Бункера для хранения материалов……………………………………………….. | 17 | |||||
6.2 | Дозаторы и питатели материалов………………………………………………… | 18 | |||||
6.2.1 | Тарельчатый питатель…………………………………………………….. | 18 | |||||
6.3 | Внутрицеховой транспорт………………………………………………………...
| 20 | |||||
6.3.1 | Ленточный конвейер…...………………………………………………….. | 20 | |||||
6.3.2 | Винтовой транспортер…………………………………………………….. | 21 | |||||
6.3.3 | Пневмовинтовой насос……………………………………………………. | 22 | |||||
6.4 | Сепаратор………………………………………………………………………….. | 22 | |||||
6.5 | Оборудование для обеспыливания воздуха и газов…………………………….. | 23 | |||||
6.5.1 | Циклоны……………………………………………………………………. | 24 | |||||
| 6.5.1.1 | Расчет камеры предварительной подсушки (циклон ЦККБ)…... | 24 | ||||
| 6.5.1.2 | Расчет циклонов НИИОГаз………………………………………. | 24 | ||||
6.5.2 | Электрофильтр…………………………………………………………... | 24 | |||||
6.6 | Дымососы………………………………………………………………………….. | 25 | |||||
7 | Материальный баланс агрегатно-поточной линии…………………………………… | 26 | |||||
8 | Описание работы агрегатно-поточной линии………………………………………… | 28 | |||||
9 | Список литературы……………………………………………………………………... | 30 | |||||
Введение
Производство портландцемента слагается из следующих основных процессов: приготовление сырьевой смеси, ее обжига и размола обожженного продукта в порошок.
Существует два основных способа производства портландцемента – мокрый и сухой. Эти способы различаются по методу приготовления сырьевой смеси. По мокрому способу сырьевую смесь приготовляют путем измельчения и смешения сырьевых материалов с водой. Получаемая при этом сметанообразная жидкость, называемая шламом, содержит 32-45% воды. По сухому способу сырьевые материалы предварительно высушивают, а затем измельчают и смешивают; полученный тонкий сухой порошок называют сырьевой мукой.
При мокром способе производства для обжига сырьевой смеси применяют вращающиеся печи, а при сухом – как вращающиеся, так и шахтные.
При производстве портландцемента по сухому способу применяют не только вращающиеся печи с циклонными теплообменниками, но и вращающиеся печи с конвейерным кальцинатором, а также вращающиеся печи без запечных теплообменных устройств. При производстве портландцемента по сухому способу в шахтных печах топливо размалывается совместно с сырьевыми материалами, и сырьевая смесь, а также полученные из нее гранулы приобретают черный цвет.
|
При мокром способе производства наблюдается меньшее пылеобразование, но требуется значительно больший расход топлива. Этот способ применяется в том случае, если сырьевые материалы отличаются очень пестрым составом, высокой влажностью, мягкой структурой и легко диспергируется водой. Если в глине есть посторонние примеси, для удаления которых необходимо размучивание, целесообразен мокрый способ производства. Сухой способ применяют при сырье с меньшей влажностью и более однородным составом. Он же практикуется в случае, если вместо глины в сырьевую смесь вводится гранулированный основный доменный шлак. Главное преимущество сухого способа производства – значительно меньший расход топлива.
В последнее время удельный вес сухого способа производства все увеличивается. Объясняется это серьезными усовершенствованиями технологии и оборудования при этом способе производства. Наряду с меньшим расходом топлива появилась возможность получения однородной сырьевой смеси при более пестром химическом составе, использования тепла отходящих газов вращающихся печей для сушки сырьевых материалов, применения сырьевых материалов повышенной влажности и установки печей весьма большой производительности при сравнительно меньших размерах.
Предварительный расчет и выбор типоразмера помольно-сушильной установки
Типоразмер мельницы, используемой для процесса помола, определяется ее внешним диаметром D и длиной корпуса L. Предварительный выбор мельницы осуществляется по заданной производительности агрегатно-поточной линии по сухому материалу. Диаметр барабанной мельницы (отношение L:D = 2) определяется по формуле:
,
где D – диаметр барабана, м; Q – производительность мельницы, т/ч; q – удельная производительность мельницы, т/(кВт∙ч); K – поправочный коэффициент на тонкость помола;
м,
где 0,95 – коэффициент, учитывающий отделение тонкой фракции в камере предварительной подсушки.
|
Примерная длина барабана мельниц рассчитывается по формуле:
м.
Выбираем барабанную мельницу L D=3,0
7,1 м:
Проектная производительность, т/ч | 24,5 |
Рабочая скорость вращения, об/мин | 18,7 |
Тонкость помола (остаток на сите 008, %) | 18,0 |
Длина камеры, м: | 6,90 |
Масса мелющих тел, т | 53,0 |
Мощность привода, кВт | 800 |
Внутренние диаметр и длина барабана: ,
Поверочный расчет мельницы
1. Критическая и рабочая скорость вращения барабана мельницы:
nкр
;
nраб ;
где nкр и nраб – соответственно критическая и рабочая скорости вращения барабана, об/мин; D – внутренний диаметр барабана, м;
nкр
об/мин;
nраб ; об/мин;
2. Масса мелющих тел:
,
Где М – масса мелющих тел, т; D – внутренний диаметр барабана, м; L – внутренняя длина барабана, м; φ – коэффициент заполнения мельницы мелющими телами; при загрузке шарами в первой камере φ = 0,28 – 0,32, γн – насыпная плотность мелющих тел; для шаров – 4,4 – 4,8 т/м3 .
Масса шаров:
т.
3. Наибольший диаметр шаровой загрузки:
,
Где Dш – наибольший диаметр шара, мм; d – наибольший размер куска материала, подаваемого в мельницу, мм; d = 40 – 60мм.
мм.
4. Размольная производительность мельницы:
,
где Q – размольная производительность, т/ч; V – внутренний объем мельницы, м3; D – внутренний диаметр мельницы, м; М – масса мелющих тел, т; q – удельная производительность мельницы, т/(кВт∙ч) (табл. 1); K – поправочный коэффициент на тонкость помола (табл. 2); η – коэффициент использования мощности; при замкнутом цикле η = 1,1 1,3.
м3
т/ч.
.
5. Мощность привода мельницы:
,
где N – мощность привода, кВт; М – масса мелющих тел, т; D – внутренний диаметр мельницы, м; nраб – рабочая скорость вращения барабана мельницы, об/мин; ηпуск – коэффициент повышения мощности с учетом пускового момента; ηпуск=1,05 – 1,1; ηпр – коэффициент, учитывающий кпд привода мельницы; при переферийном приводе ηпр=0,85 – 0,88.
кВт.
6. Удельный расход мелющих тел и бронеплит:
,
где Р – удельный расход мелющих тел или бронеплит, кг/т; Рэ – то же для эталонного продукта, кг/т; q – удельная производительность мельницы, т/(кВт∙ч) (табл. 1); K – поправочный коэффициент на тонкость помола (табл. 2).
|
Значения Рэ для шаров принимается равным 0,25 и для бронеплит – 0,15кг/т измельчаемого материала.
Для шаров:
кг/т.
Для бронеплит:
кг/т
Тарельчатый питатель
Тип тарельчатого питателя выбирается по его объёмной производительности, а затем его массовая производительность проверяется по формуле:
,
где - производительность питателя, т/ч;
- радиус диска питателя, м;
- радиус верхней кромки конуса материала, м;
;
- высота кольца материала, сбрасываемого ножом с диска, м;
м;
- скорость вращения диска питателя, мин-1;
- насыпная масса материала, т/м3;
Для известняка:
Выбираем тарельчатый питатель ДЛ-10А со следующими характеристиками:
Параметр | Тип питателя |
ДЛ-10А | |
Диаметр диска, мм | 1000 |
Скорость вращения диска питателя, мин-1 | 7 – 11 |
Производительность, м3/ч | 28 |
Максимальный размер куска материала, мм | 50 |
Габаритные размеры, мм: | |
высота | 1300 |
длина | 1250 |
ширина | 1150 |
Мощность электродвигателя, кВт | 2,2 |
Масса питателя, т | 1,30 |
т/ч, что больше требуемой производительности (39,6 т/ч).
Для глины:
Выбираем тарельчатый питатель ДЛ-8А со следующими характеристиками:
Параметр | Тип питателя |
ДЛ-8А | |
Диаметр диска, мм | 800 |
Скорость вращения диска питателя, мин-1 | 7 – 11 |
Производительность, м3/ч | 13 |
Максимальный размер куска материала, мм | 40 |
Габаритные размеры, мм: | |
высота | 1150 |
длина | 1050 |
ширина | 1000 |
Мощность электродвигателя, кВт | 1,5 |
Масса питателя, т | 0,60 |
т/ч, т/ч, что больше требуемой производительности (13,7 т/ч)
Внутрицеховой транспорт
Для работы основного технологического оборудования необходимо обеспечить бесперебойный и непрерывный внутрицеховой транспорт перерабатываемых материалов. Выбор вида внутрицехового транспорта зависит от расстояния и направления транспортировки, а также от физических свойств перемещаемых материалов.
Наибольшее распространение в качестве внутрицехового транспорта в цементной промышленности получили ленточные конвейеры, скребковые транспортеры, ковшовые элеваторы, винтовые транспортеры (шнеки) и пневматические транспортные желоба (аэрожелоба).
Ленточный конвейер
Для транспортирования сыпучих и кусковых материалов в горизонтальной и наклонной плоскостях в цементной промышленности широко используют ленточные конвейеры с плоской и желобчатой лентой. Ширина ленточных конвейеров, выпускаемых промышленностью, нормализована: 400, 500, 650, 800, 1000, 1200, 1400, 1600, 2000, 2500 и 3000 мм.
Для транспортирования материалов после дозаторов выбираем конвейер с желобчатой лентой, так как при её использовании отсутствует риск просыпания материала в процессе движения.
|
Ширина желобчатой ленты рассчитывается по формуле:
, м
где ν – скорость движения ленты, м/с; γн – насыпная масса материала, т/м3;
Массовая производительность конвейера:
, т/ч
Расчетная производительность
, т/ч
, т/м3
, м
Выбираем транспортер с шириной ленты 400 мм.
Винтовой транспортер
Винтовые транспортеры (шнеки) применяются для транспортирования пылевидных, порошкообразных и мелкокусковых (реже) материалов на расстояние до 100 метров по горизонтали и под углом до 20˚ к горизонту. Шнеками нецелесообразно транспортировать липкие, уплотняющиеся, а также высокоабразивные материалы.
Внешний диаметр шнека нормализован. Промышленностью выпускаются шнеки диаметром 100, 125, 160, 200, 320, 400, 500, 600, 650 и 800 мм. Шаг винтовых лопастей составляет 0,8 – 1,0 от диаметра шнека. Диаметр шнека должен не менее чем в 4 раза превышать максимальные размеры куска транспортируемого материала.
Винтовой транспортер выбирается по диаметру шнека, а затем его производительность проверяется по формуле:
,
где Q – производительность транспортера, т/час; D – диаметр шнека, м; S – шаг шнека, м; n – число оборотов вала, мин-1; ψ – коэффициент заполнения желоба (0,25 – 0,40); γн – насыпная масса материала, т/м3; К – коэффициент, зависящий от угла наклона транспортера.
Выбираем шнек для транспортировки крупки из сепаратора в мельницу.
,
где Qвх – количество материала на входе в сепаратор; Qт.ф. – количество тонкой фракции (готового продукта); Ц – циркуляционная нагрузка сепаратора.
Qвинт. тр. = Qт.ф.(Ц – 1) = 52∙(1,5 – 1) = 26 т/ч.
Диаметр шнека 320 мм.
Производительность транспортера:
т/час
Выбираем шнек для транспортировки сырьевой муки из циклонов НИИОГаз и электрофильтра в силос..
Необходимая производительность транспортера Q = 52 т/ч
Расчетная производительность Qрасч = 52 ∙ 1,3 = 67,6 т/ч
Диаметр шнека 400 мм.
Производительность транспортера:
т/час
6.3.3 Пневмовинтовой насос.
Для подачи готовой сырьевой смеси в силос выбираем пневмовинтовой насос, т.к. он позволяет перемещать материал на расстояние до 450 м, и высоту до 35 м. Преимуществами пневмовинтового насоса являются герметичность и гибкость трасс, независимость от погодных условий, возможность полной автоматизации процесса и небольшие капитальные затраты на строительство. Также достоинствами этого устройства являются непрерывность процесса транспортирования, небольшие габариты, простота управления.
Необходимая производительность насоса Q = 52 т/ч
По данным таблицы 23 выбираем насос ТА–40. Его характеристики:
Производитель- ность, т/ч | Дальность транспортировки, м | Максимальная высота подачи, м | Диаметр трубопровода, мм | Давление воздуха, МПа | Мощность двигателя, кВт |
63 | 230 | 30 | 175 | 0,3 | 55 |
Сепаратор
Для разделения материала на фракции в помольно-сушильных установках используются воздушно-проходные и центробежные сепараторы. Важнейшими характеристиками сепаратора являются циркуляционная нагрузка и коэффициент полезного действия сепаратора. Циркуляционная нагрузка сепаратора определяется как отношение количества материала на входе в сепаратор Qвх. к количеству тонкой фракции Qтф., которая для большинства схем равна заданной производительности мельницы Q:
В данной схеме помола необходимо использовать воздушно-проходной сепаратор, т.к. материал из мельницы в сепаратор выносится потоком сушильного агента. Достоинством данного агрегата является крайняя простота устройства
Выбор воздушно-проходного сепаратора производится по его объему и диаметру входного патрубка, которые рассчитываются по формулам:
;
,
где – объем сепаратора, м3;
г – объем газов, проходящих через сепаратор, м3/ч;
г принимается равным часовому расходу сушильного агента; q – напряжение объема сепаратора по газу, м3/(м3∙ч); в зависимости от тонкости помола сырья при остатке на сите № 008 1-5% q = 2000, 5-10% - 2500, 10-15% - 3000 и 15-20% - 3500; d – диаметр входного патрубка, м; Vсек – скорость газов в верхней части внешнего корпуса сепаратора, м/с.
м3,
м.
Характеристики выбранного ВПС:
Объем сепаратора – 22 м3;
Диаметр сепаратора – 4 м;
Диаметр входного патрубка – 0,95 м
6.5 Оборудование для обеспыливания воздуха и газов
Дробильные, помольные, обжиговые и прочие агрегаты цементной промышленности снабжаются устройствами для очистки и обеспыливания аспирационного воздуха или отходящих газов. Гранулометрический состав пыли очень разнообразен. Наряду с крупными (более 100 мкм) частицами обычно присутствуют и мелкие (менее 1 – 10 мкм) частицы пыли, что делает необходимым установку нескольких обеспыливающих агрегатов, работающих последовательно. Применение того или иного обеспыливающего агрегата зависит от целого ряда факторов:
· объема обеспыливающего воздуха или газа;
· температуры, влажности и запыленности воздуха или газа;
· физико-химических свойств пыли;
· степени очистки газов в агрегате и т. п.
Все пылеулавливающие устройства характеризуются степенью очистки газа или коэффициентом полезного действия:
,
где и
– концентрация пыли в газах соответственно до и после аппарата, г/м3.
Циклоны
Циклоны используются, как правило, для предварительной очистки газов, хотя некоторые из них, например батарейные, имеют высокий коэффициент полезного действия и могут применяться для окончательной очистки запыленных газов.
Наибольшее распространение в цементной промышленности получили циклоны типа ЦККБ и НИИОГаз.
Циклоны типа ЦККБ устанавливают на первом этапе пылеочистки. Они характеризуются сравнительно малой высотой цилиндрической и конической части. Коэффициент полезного действия циклонов ЦККБ не превышает 75 – 80%.
6.5.1.1 Расчет камеры предварительной подсушки (циклон ЦККБ).
Внутренний диаметр:
м,
Высота циклона:
м,
Ширина входного патрубка циклона:
м.
Расчет циклонов НИИОГаз
Так как эффективность групповых циклонов выше по сравнению с одиночными, то выбираем группу из 4-х циклонов НИИОГаз.
Диаметр циклонов:
м.
Общая высота циклона составляет:
м.
Электрофильтр
Для окончательной очистки газов используем электрофильтр, т.к. газы содержат большое количество трехатомных газов (H2O, CO2), которые легко ионизируются, повышая эффективность пылеочистки.
Площадь активного сечения электрофильтра:
м2,
где W – скорость газов в сечении фильтра.
По данным таблицы 30 выбираем электрофильтр УГ2–3–37. Его характеристики:
Площадь активного сечения, м2 | Число полей | Площадь осадительных электродов, м2 | Габариты, длина×высота×ширина, м |
37 | 4 | 3150 | 18,6×15,4×6,0 |
Дымососы
Вентиляторы предназначены для эвакуации из дробилок, мельниц, силосов и т. п. запыленного воздуха. По принципу действия различают вентиляторы осевые и центробежные. Осевые применяют для перемещения относительно больших количеств воздуха при небольшом давлении (разрежении) – до 500 – 700 Па, а центробежные используются при значительных давлениях (разрежениях) – до 3 кПа. При выборе вентилятора или дымососа их производительность может быть увеличена за счет изменения числа оборотов ротора:
,
где – необходимая производительность, м3/час;
– паспортная производительность, м3/час; n2 – необходимое число оборотов ротора, мин-1; n1 – паспортное значение числа оборотов ротора, мин-1.
Выбираем мельничный вентилятор типа ДН–19,5. Технические характеристики вентилятора:
Тип вентилятора | ДН–19,5 |
Производительность, м3/ч | 82000 |
Напор, кПа | 270 |
Мощность двигателя, кВт | 72 |
Частота вращения ротора, мин-1 | 750 |
Необходимое число оборотов ротора дымососа
об/мин
ПОЯСНИТЕЛЬНАЯ ЗАПИСКА
к курсовому проекту на тему:
«Агрегатно-поточная линия помола сырья с одновременной сушкой производительностью 52 т/ч (схема №3)»
Выполнил:
студент гр. С-43
Котов В. А.
Проверил:
Сивков С. П.
Москва 2011
Содержание
| стр. | |||||
Введение | ……………………………………………………………………………………... | 3 | ||||
1 | Выбор рациональной технологической схемы помола сырьевых материалов……... | 4 | ||||
2 | Предварительный расчёт и выбор типоразмера помольно-сушильной установки… | 5 | ||||
3 | Проверочный расчёт мельницы………………………………………………………... | 6 | ||||
4 | Теплотехнический расчёт помольно-сушильной установки………………………… | 9 | ||||
4.1 | Расчёт процесса горения топлива………………………………………………... | 9 | ||||
4.2 | Расчёт параметров сушильного агента…………………………………………... | 10 | ||||
4.3 | Расчёт теплового баланса процесса сушки……………………………………… | 12 | ||||
5 | Технологическая схема помола сырья с одновременной сушкой…………………… | 16 | ||||
6 | Выбор и проверочный расчёт вспомогательного оборудования…………………….. | 17 | ||||
6.1 | Бункера для хранения материалов……………………………………………….. | 17 | ||||
6.2 | Дозаторы и питатели материалов………………………………………………… | 18 | ||||
6.2.1 | Тарельчатый питатель…………………………………………………….. | 18 | ||||
6.3 | Внутрицеховой транспорт………………………………………………………... | 20 | ||||
6.3.1 | Ленточный конвейер…...………………………………………………….. | 20 | ||||
6.3.2 | Винтовой транспортер…………………………………………………….. | 21 | ||||
6.3.3 | Пневмовинтовой насос……………………………………………………. | 22 | ||||
6.4 | Сепаратор………………………………………………………………………….. | 22 | ||||
6.5 | Оборудование для обеспыливания воздуха и газов…………………………….. | 23 | ||||
6.5.1 | Циклоны……………………………………………………………………. | 24 | ||||
| 6.5.1.1 | Расчет камеры предварительной подсушки (циклон ЦККБ)…... | 24 | |||
| 6.5.1.2 | Расчет циклонов НИИОГаз………………………………………. | 24 | |||
6.5.2 | Электрофильтр…………………………………………………………... | 24 | ||||
6.6 | Дымососы………………………………………………………………………….. | 25 | ||||
7 | Материальный баланс агрегатно-поточной линии…………………………………… | 26 | ||||
8 | Описание работы агрегатно-поточной линии………………………………………… | 28 | ||||
9 | Список литературы……………………………………………………………………... | 30 | ||||
Введение
Производство портландцемента слагается из следующих основных процессов: приготовление сырьевой смеси, ее обжига и размола обожженного продукта в порошок.
Существует два основных способа производства портландцемента – мокрый и сухой. Эти способы различаются по методу приготовления сырьевой смеси. По мокрому способу сырьевую смесь приготовляют путем измельчения и смешения сырьевых материалов с водой. Получаемая при этом сметанообразная жидкость, называемая шламом, содержит 32-45% воды. По сухому способу сырьевые материалы предварительно высушивают, а затем измельчают и смешивают; полученный тонкий сухой порошок называют сырьевой мукой.
При мокром способе производства для обжига сырьевой смеси применяют вращающиеся печи, а при сухом – как вращающиеся, так и шахтные.
При производстве портландцемента по сухому способу применяют не только вращающиеся печи с циклонными теплообменниками, но и вращающиеся печи с конвейерным кальцинатором, а также вращающиеся печи без запечных теплообменных устройств. При производстве портландцемента по сухому способу в шахтных печах топливо размалывается совместно с сырьевыми материалами, и сырьевая смесь, а также полученные из нее гранулы приобретают черный цвет.
При мокром способе производства наблюдается меньшее пылеобразование, но требуется значительно больший расход топлива. Этот способ применяется в том случае, если сырьевые материалы отличаются очень пестрым составом, высокой влажностью, мягкой структурой и легко диспергируется водой. Если в глине есть посторонние примеси, для удаления которых необходимо размучивание, целесообразен мокрый способ производства. Сухой способ применяют при сырье с меньшей влажностью и более однородным составом. Он же практикуется в случае, если вместо глины в сырьевую смесь вводится гранулированный основный доменный шлак. Главное преимущество сухого способа производства – значительно меньший расход топлива.
В последнее время удельный вес сухого способа производства все увеличивается. Объясняется это серьезными усовершенствованиями технологии и оборудования при этом способе производства. Наряду с меньшим расходом топлива появилась возможность получения однородной сырьевой смеси при более пестром химическом составе, использования тепла отходящих газов вращающихся печей для сушки сырьевых материалов, применения сырьевых материалов повышенной влажности и установки печей весьма большой производительности при сравнительно меньших размерах.
Выбор рациональной технологической схемы помола сырьевых материалов
Процесс тонкого измельчения (помол) увеличивает поверхность взаимодействия материалов и их реакционную способность. Чем тоньше измельчены сырьевые материалы, тем скорее происходят физико-химические процессы в зонах контакта взаимодействующих частиц.
Для тонкого измельчения материалов применяют различные типы мельниц: шаровые, вертикальные среднеходные, мельницы самоизмельчения. В настоящее время для помола с одновременной сушкой сырьевых материалов в цементной промышленности наиболее часто используют шаровые мельницы, работающие в открытом или замкнутом цикле. Причиной этого является традиционность и совершенство конструкции помольного агрегата, большое количество выпускаемых типоразмеров мельниц.
К недостаткам шаровых мельниц можно отнести низкий коэффициент полезного действия. По разным данным не более 20% энергии, потребляемой мельницей, идет непосредственно на измельчение материала; остальная энергия расходуется на перемещение мелющих тел, трение между элементами конструкции, генерацию тепла, звука, вибраций и т. п. По отношению длины корпуса к его диаметру различают трубные (отношение L:D изменяется в пределах 3:1 – 5:1) и барабанные (отношение L:D – в пределах 1,5:1 – 2,5:1) мельницы.
В технологических схемах помола, работающих по замкнутому циклу, весь размалываемый материал при прохождении через мельницу измельчается до заданной тонкости и выходит из нее в виде готового продукта. Применение открытого цикла помола не требует привлечения дополнительного оборудования, организация работы таких мельниц более проста. Однако для получения высокой тонкости измельчения сырья необходимо длительное время его пребывания в мельнице, что приведет либо к увеличению габаритов (длины) мельницы, либо к снижению ее производительности. Кроме того, измельченный материал имеет неоднородный зерновой состав, что отражается на его реакционной способности в процессах дальнейшей переработки. В технологических схемах, работающих по замкнутому циклу, помол материала сопровождается его классификацией в сепараторе с выделением грубо молотого (крупки) и тонкого продукта; при этом крупка возвращается в мельницу для домола.
Применение замкнутого цикла помола позволяет:
· Увеличить производительность мельницы на 25 – 50% из-за постоянного удаления тонкой фракции (она не мешает помолу);
· Улучшить зерновой состав измельчаемого продукта;
· Сократить удельный расход энергии на измельчение материала.
Но организация замкнутого цикла требует использования дополнительного оборудования – сепараторов, элеваторов, транспортеров и т. п., которые также потребляют определенное количество электроэнергии. Поэтому экономия электроэнергии при переходе с открытого на замкнутый цикл измельчения материала может быть сравнительно небольшой.
При сухом способе производства портландцементного клинкера влажность материала, подаваемого в силоса сырьевой муки, не должна превышать 1 – 2%. Высокая естественная влажность сырьевых компонентов, особенно глин, мелов, мергелей, вызывает необходимость их сушки, как перед помолом, так и в процессе его осуществления.
Предварительная сушка сырьевых материалов может осуществляться в сушильных барабанах, вихревых сушилках или сушилках кипящего слоя, а также в процессе дробления материала в молотковых или ударно-отражательных дробилках-сушилках. В качестве сушильного агента при этом используются дымовые газы вращающихся печей, избыточный вторичный воздух колосниковых клинкерных холодильников, а также газы, полученные в специальных так называемых выносных топках. Последний способ имеет ряд преимуществ, так как устраняет зависимость процессов функционирования вращающейся печи и помольно-сушильной установки, а также позволяет получать сушильный агент с желаемой температурой и прочими характеристиками, обеспечивающими более полную сушку материала. С другой стороны, использование отходящих газов вращающихся печей позволяет полнее утилизировать их тепло и приводит к существенной экономии топлива.
Температура сушильного агента на выходе из помольно-сушильной установки должна на 80 – 100 ˚С превышать температуру точки росы. Газоходы к сепараторам, обеспыливающему оборудованию, а в некоторых случаях и сами сепараторы обычно покрываются теплоизоляцией, чтобы избежать резкого снижения температуры сушильного агента и конденсации содержащихся в нем водяных паров. Практически температура сушильного агента на выходе из мельницы принимается 120 – 150 ˚С.
Предварительный расчет и выбор типоразмера помольно-сушильной установки
Типоразмер мельницы, используемой для процесса помола, определяется ее внешним диаметром D и длиной корпуса L. Предварительный выбор мельницы осущес
|
|
Историки об Елизавете Петровне: Елизавета попала между двумя встречными культурными течениями, воспитывалась среди новых европейских веяний и преданий...
Адаптации растений и животных к жизни в горах: Большое значение для жизни организмов в горах имеют степень расчленения, крутизна и экспозиционные различия склонов...
Особенности сооружения опор в сложных условиях: Сооружение ВЛ в районах с суровыми климатическими и тяжелыми геологическими условиями...
Типы сооружений для обработки осадков: Септиками называются сооружения, в которых одновременно происходят осветление сточной жидкости...
© cyberpedia.su 2017-2024 - Не является автором материалов. Исключительное право сохранено за автором текста.
Если вы не хотите, чтобы данный материал был у нас на сайте, перейдите по ссылке: Нарушение авторских прав. Мы поможем в написании вашей работы!