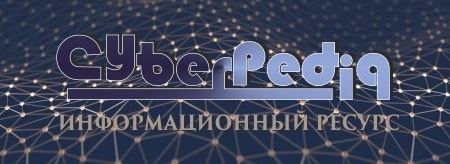
Индивидуальные очистные сооружения: К классу индивидуальных очистных сооружений относят сооружения, пропускная способность которых...
Механическое удерживание земляных масс: Механическое удерживание земляных масс на склоне обеспечивают контрфорсными сооружениями различных конструкций...
Топ:
Эволюция кровеносной системы позвоночных животных: Биологическая эволюция – необратимый процесс исторического развития живой природы...
Выпускная квалификационная работа: Основная часть ВКР, как правило, состоит из двух-трех глав, каждая из которых, в свою очередь...
Интересное:
Влияние предпринимательской среды на эффективное функционирование предприятия: Предпринимательская среда – это совокупность внешних и внутренних факторов, оказывающих влияние на функционирование фирмы...
Аура как энергетическое поле: многослойную ауру человека можно представить себе подобным...
Подходы к решению темы фильма: Существует три основных типа исторического фильма, имеющих между собой много общего...
Дисциплины:
![]() |
![]() |
5.00
из
|
Заказать работу |
|
|
Характерные неисправности: загрязнение и образование накипи на стенках водяной рубашки, а также баков и трубок радиатора, течь баков и трубок радиатора, трещины на стенках водяной рубашки, повреждение термостата, износ отдельных деталей вентилятора и водяного насоса. Эти неисправности приводят к нарушению теплового режима двигателя и его перегреву.
Перед ремонтом узлов внутренние полости системы охлаждения промывают специальными растворами.
После разборки машины радиатор и головку цилиндров дополнительно вываривают, чтобы удалить оставшуюся накипь.
Ремонт радиатора. Основные дефекты радиатора — изгиб и разрывы трубок, отпаивание трубок от опорных пластин, повреждение охлаждающих пластин, трещины на верхнем и нижнем баках. Большинство повреждений обнаруживают наружным осмотром и испытанием радиатора под давлением воздуха в ванне с водой.
В неразборных сердцевинах радиатора поврежденные трубки отпаивают от опорных пластин специальным паяльником или паяльной лампой. От охлаждающих пластин трубки отпаивают при помощи нагретого шомпола или нихромовой проволоки. В первом случае шомпол нагревают до температуры 800—900° С и вставляют в трубку. Затем отпаянную трубку вместе с шомполом вынимают из радиатора.
Для отпайки трубок при помощи нихромовой проволоки ее подключают ко вторичной обмотке сварочного трансформатора. Участок проволоки, расположенный в трубке, нагревается меньше, чем находящийся на воздухе. Поэтому для лучшего использования выделяющегося тепла проволоку необходимо перемещать относительно сердцевины.
Восстановленную трубку проверяют на герметичность. Если трубок повреждено больше, сердцевину радиатора выбраковывают или перебирают.
|
Трещины в верхних и нижних чугунных бачках радиаторов заваривают биметаллическим электродом или заделывают клеями на нове эпоксидных смол. После ремонта радиатор испытывают на герметичность.
Ремонт вентилятора и водяного насоса сводится к восстановлению посадочных мест, замене уплотнений, заварке или заделке трещин, правке крестовин и лопастей, подтяжке их креплений и статической балансировке. В процессе ремонта вентилятора необходимо охранять форму и заданный угол наклона лопастей.
Ремонт термостата. Основные дефекты термостата: коробление лапана, отрыв штока, появление трещин гофрированного элемента, изгиб пластины подвески. Указанные неисправности обнаруживают ри погружении термостата в нагретую воду.
В исправном термостате начало и полное открытие клапана олжно происходить при определенной температуре. Дефекты устраняют регулировкой длины хода штока, рихтовкой деталей и пайкой.
4. РЕМОНТ ОСНОВНЫХ УЗЛОВ, АГРЕГАТОВ И ПРИБОРОВ ЭЛЕКТРООБОРУДОВАНИЯ.
Неисправности деталей электрооборудования могут быть механического и электрического характера.
Механические неисправности устраняются ранее описанными технологическими приемами.
Ремонт электропроводки. Основные неисправности электропроводки —повреждения жил проводов, их наконечников, контактов, зажимов и нарушения изоляции.
Повреждения этих частей проводки приводят либо к полному прекращению тока при обрыве, либо к увеличению сопротивления при окислении контактов, не удовлетворительной затяжке зажима или пайке соединения. Нарушения изоляции могут вызвать короткие замыкания и утечки тока.
Место обрыва определяют контрольной лампой. По схеме электрооборудования выясняют путь тока к неработающему потребителю и проверяют этот участок цепи. Зажим лампы присоединяют к массе, а щупом последовательно касаются зажимов участка цепи от неработающего прибора до источника тока. Загорание контрольной лампы свидетельствует о том, что обрыв находится рядом с проверяемым зажимом. Место обрыва может быть определено шунтированием проверяемого участка. Проводку с обрывами восстанавливают пайкой.
|
Окисленные контакты с большим сопротивлением находят с помощью вольтметра.
Чтобы найти цепь потребителя с коротким замыканием, поочередно подключают потребители. Если контрольная лампа загорается, а потребитель не работает, это указывает на неисправность проверяемой цепи.
Короткое замыкание устраняют отведением участка провода с поврежденной изоляцией от массы и обматыванием его изоляционной лентой.
Испытание изоляции ведут на стенде КИ-968.
Испытание изоляции конденсатора. Наиболее оступна проверка конденсатора последовательно включенной лампой накаливания от сети переменного тока напряжением 220 В. При исправной изоляции обмоток конденсатора лампа не горит. В момент разрыва цепи должно быть искрение. Отсутствие искрения указывает на обрыв, а горение лампы — на пробой конденсатора.
Электрическую прочность изоляционных деталей в цепях высокого напряжения прерывателя-распределителя или магнето (крышка распределителя, ротор и т. п.) проверяют под напряжением 16000— 20000 В на стенде КИ-968.
Исследования показывают, что неисправности таких узлов, как вентилятор, дизельная топливная аппаратура, а также большая разница в массе нижних головок комплекта шатунов и т. п. тоже усиливают вибрацию двигателя. Если разность в массе одного комплекта шатунов в целом не превышает 10 г, то разность в массе шатунно-поршневой группы превышает 150 г, что служит одной из основных причин появления значительных упругих колебаний коленчатого вала и вибрации двигателя в целом.
На уравновешенность двигателя влияет и его тепловое состояние. Уравновешенность двигателя теряется при его охлаждении и вновь восстанавливается после прогрева до температуры, при которой проводилась балансировка. По этой причине балансировка двигателя должна выполняться при рабочих температурах двигателя, охлаждающей жидкости и масла.
Амплитуда вибрации двигателя также зависит от частоты вращения коленчатого вала.
Учитывая изложенные явления, заводы, выпускающие тракторные двигатели (СМД-14, и др.), проводят их балансировку при стендовых испытаниях.
|
Заводская балансировка уравновешенности, однако, нарушается после разборки, ремонта и замены деталей. Это подтверждается такими данными: более 50% отказов тракторов ДТ-75 происходит из-за повышенной вибрации двигателя. Вызываемые неуравновешенностью двигателя высокочастотные вибрации приводят к значительному износу не только деталей самого двигателя, но и деталей трансмиссии машины.
Благодаря балансировке, проводимой после ремонта, значительно снижается количество поломок, усталостных трещин, обрывов крепежных деталей и т. п. Надежность и долговечность двигателя в связи с этим возрастают примерно на 25%. За счет снижения непроизводительных затрат энергии на вибрацию и усиленное изнашивание деталей примерно на 10—12% повышается полезная мощность двигателя.
Неуравновешенность двигателя включает собственную неуравновешенность отдельных подвижных деталей и общую монтажную неуравновешенность вращающихся масс коленчатого вала с шатунами, маховиком и муфтой сцепления в сборе и других механизмов, вызванную неточностью изготовления отдельных деталей, их подбором по массе и сборкой узлов.
Если собственная неуравновешенность коленчатого вала двигателя СМД-14 допускается в среднем в пределах 40—50 г-см, маховика — 40—60 г-см, муфты сцепления — 400—500 г-см, что з сумме составляет 500—600 г-см, то суммарная неуравновешенность этого двигателя достигает 3000 г-см, что явно недопустимо.
Большая часть дисбаланса создается при сборке двигателя в основном за счет неуравновешенности и смещения муфты сцепления. Если у автомобильных двигателей коленчатый вал, маховик и муфты сцепления в сборе в условиях заводов-изготовителей и ремонтных заводов можно динамически сбалансировать, то у тракторных двигателей ввиду их конструктивных особенностей этого сделать не удается. Операция балансировки тракторного двигателя во время его испытания на стенде заключается в постановке (в специально предусмотренные на упорном диске муфты сцепления отверстия с резьбой) балансировочных грузов — в виде специальных болтов с большой головкой. Эти грузы компенсируют обнаруженный дисбаланс вращающихся деталей собранного двигателя.
|
Балансировка двигателей в условиях ремонтных предприятий выполняется на обычных электротормозных стендах конструкции ГОСНИТИ. Эти стенды оборудованы упругой подвеской испытываемого двигателя на опорах специальным уравновешиваемым приводом и виброметром ЭВМ-БП. Жесткость пружин подвески подобрана таким образом, что собственная частота горизонтальных колебаний двигателя на стенде (на листовых пружинах) составляет 4—6 Гц и вертикальных (на тарельчатых пружинах) — 6—8 Гп. Благодаря этому система двигатель—подвеска находится далеко в зарезонансной области, что обеспечивает большую виброизоляцию и высокую точность балансировки.
Двигатель удерживается на стенде собственным весом, без крепления.
Амплитуда его вибрации, а также вес и угловое расположение (фаза) балансирующего груза определяются виброметром ЭВМ-БП, устанавливаемым на задней опоре двигателя.
Собственная неуравновешенность приводного вала может существенно исказить результаты балансировки. Поэтому приводной вал стенда должен быть предварительно тщательно динамически отбалансирован путем ввертывания грузов в специально предусмотренные резьбовые отверстия на фланцах соединительной муфты вала, обращенной к двигателю.
Перед балансировкой двигатель должен быть прогрет, т. е. температура масла, воды и давление масла доведены до рабочих пределов, а частота вращения коленчатого вала постепенно доведена до максимальной (у СМД-14 до 1790—1850 об/мин) и проверена устойчивость работы двигателя на режиме холостого хода.
Далее виброщуп датчика устанавливают в горизонтальное положение и его конец упирают в картер маховика, тумблер прибора переключают в положение «датчик», измеряют амплитуду колебаний и по таблице, специально заранее составленной, подбирают массу груза, который следует ввернуть в отверстие диска муфты сцепления.
После этого тумблер виброметра переключают в положение «фазометр» и поворотом ручки лимба фазометра в ту или иную сторону от 0 до 360° по шкале определяют угловое расположение отверстия, куда должен быть ввернут подобранный балансирующий груз, соответствующий моменту максимального показания измерителя прибора. Для достоверности найденного угла эту операцию проделывают 2—3 раза. После этого двигатель постепенно останавливают, открывают защитный кожух приводного вала стенда и поворотом вала за вороток устанавливают найденный по фазометру угол на лимбе вала, используя отметку на крышке генератора против центра люка на крышке муфты сцепления. Открывают люк крышки муфты сцепления. Против отметки в люке должно стать одно из отверстий на упорном диске муфты сцепления, куда и ввертывают подобранный уравновешивающий груз.
|
В случае несовпадения одного из отверстий с центром люка уравновешивающий груз распределяют, пользуясь специальной номограммой, между двумя ближайшими отверстиями по обе стороны от центра люка. В эти отверстия ввертьнзают подобранные грузы, закрывают люк, запускают двигатель и повторно проверяют амплитуду колебаний, которая должна быть не более 30 мкм.
Если амплитуда колебаний по прибору превышает допустимое значение, операцию балансировки повторяют. Если в отверстии, куда нужно ввернуть подобранный балансировочный груз, уже есть груз, то его нужно вывернуть и повторить балансировку.
В тех случаях, когда двигатель не поддается балансировке и амплитуда колебаний превышает 300—350 мкм, двигатель отправляют на полную переборку.
Обкатка и испытание автотракторных и комбайновых двигателей. Для обкатки и испытания тракторных, комбайновых и автомобильных двигателей служат универсальные электротормозные обкаточные стенды СТЭ-40-1000 ГОСНИТИ; СТЭУ-28-1000 ГОСНИТИ; для пусковых двигателей — стенды СТЭ-7-1000 и СТ-2,8-1500.
Обкатку и испытание двигателей, согласно техническим условиям, рекомендуется проводить на основном (картерном) масле дизельных двигателей — на индустриальном 30, пусковых двигателей ПД-10 и ГІД-10М при холодной обкатке—на дизельном топливе, вводимом через систему питания, а горячую—на смеси, состоящей из 15 частей (по объему) автомобильного бензина и 1 части масла, применяемого для смазки основного двигателя.
Для улучшения и ускорения приработки трущихся поверхностей рекомендуется применение менее вязких жидкостей, чем заливаемых в картер двигателя. Так, для сталеалюминиевых вкладышей рекомендуется смесь из 80% масла Дп-11 и 20% индустриального 20. Для вкладышей из свинцовистой бронзы — смесь из 28% масла Дп-11 и 72% индустриального 20. Рекомендуется также масло веретенное 2, смесь веретенного 2 и дизельного масел в соотношении 1:1; 2-процентный раствор эмульсола в воде, добавление в масло серы 0,8—1%.
Режимы обкатки. Обкатка и испытание двигателей включают в себя несколько последовательных этапов: холодная обкатка, обкатка на газу без нагрузки, обкатка на газу под нагрузкой, испытание и контрольный осмотр.
Холодная обкатка двигателей начинается с медленного прокручивания коленчатого вала (500—600 об/мин) вначале с выключенной, а затем с включенной компрессией. Продолжительность холодной обкатки составляет от 20 мин (ПД-10, ПД-10М) до 100 мин (КДМ-100, Д-108). Частоту вращения коленчатого вала повышают постепенно.
Обкатка на газу без нагрузки характеризуется также постепенным повышением частоты вращения, начиная с минимальной. Продолжительность обкатки двигателей на газу без нагрузки составляет от 20 до 40 мин.
Обкатка на газу под нагрузкой продолжается от 20 мни (ПД-10, ПД-10М) до 1 ч 40 мин (КДМ-100, Д-108). Затем проводится испытание на мощность и расход топлива, контрольный осмотр и приемка двигателя из ремонта.
Испытание двигателей проводится для выявления качества ремонта, правильности регулировок механизмов и, кроме того, определения мощности, часового и удельного расходов топлива.
После обкатки и испытаний проводится контрольный осмотр двигателя: его устанавливают на стенд и снимают картер, масляный насос с приводом, крышки с вкладышами шатунных и коренных подшипников. При осмотре особое внимание обращают на состояние рабочих поверхностей цилиндров, шатунных и коренных шеек и их подшипников. Пользуются эталонами чистоты поверхности.
После проверки обнаруженные в процессе обкатки, испытаний и контрольного осмотра неисправности устраняют, собирают двигатель и проверяют при работе на газу без нагрузки в течение 10 мин. Если при контрольном осмотре были заменены основные детали кри-вошипно-шатунного механизма, то такой двигатель подвергают повторной обкатке, испытанию, а после этого контрольному осмотру.
Особенности процесса обкатки (приработки). В начальный период обкатки наблюдается ускоренный износ, рабочие фильтры быстро загрязняются и ухудшается очистка масла. Кроме того, повышенная работа трения вызывает нагрев трущихся поверхностей, а вместе с ними и масла. Поэтому на хорошо организованных испытательных станциях ремонтных предприятий применяют проточно-циркуляционную систему смазки, которая выполняется в нескольких вариантах.
В отличие от тракторных двигателей отремонтированные автомобильные двигатели во время обкатки не подвергают испытаниям. Вследствие этого предупреждается разрушение поверхностей трения, но ухудшается контроль качества ремонта.
Для исключения недостатков этих режимов обкатки применяется способ испытания двигателей после ремонта при тарированном ограничении мощности. На двигателе закрепляют ограничитель мощности, который снижает ее и изменяет удельный расход топлива.
Данные исследований показали, что двигатели следует испытывать при ограниченной мощности, равной 70—80% предельной. Ограничитель мощности полезно сохранять в течение всего срока обкатки (в течение 50—60 ч) для предохранения двигателя от перегрузок. Авторемонтные предприятия предпочитают двухстадийную обкатку: холодную без нагрузки и под нагрузкой или горячую без нагрузки и под нагрузкой.
ЛЕКЦИЯ №4
Тема: «Ремонт силовой передачи, механизмов управления и ходовой части тракторов»
Вопросы:
1. Ремонт осей и валов.
2. Ремонт шестерен и звездочек.
3. Ремонт подшипников качени я.
Ремонт осей и валов
Значительное количество тракторов, автомобилей, комбайнов сельскохозяйственных машин различных типов и марок приводит необходимости унификации технологии ремонта отдельных деталей и сопряжений.
Технология восстановления некоторых талей силовой передачи, ходовой части и механизмов управления тракторов и автомобилей.
Ремонт валов и осей. В тракторах и автомобилях применяют различные по конструкции, материалу и термической обработке валы и оси.
Для получения большей износостойкости валы, оси, полуоси другие детали подвергаются термической или термохимической работке.
Некоторые детали цементуют на глубину 1,0—1,5 мм, закаливают в еле и отпускают до получения твердости поверхностей НRС 40—62.
Детали, изготовленные из углеродистой стали с содержанием лерода 0,4% и более, закаливают с нагревом ТВЧ и отпускают.
Валы автомобилей, изготовленные из стали 40Х, цианируют глубину 0,2—0,3 мм до получения твердости НRС 48—53.
Основные дефекты валов: износ шпоночных (деформация и износ шпонок, канавок) и шлицевых соединений (износ боковой поверхности шлицев), посадочных мест, повреждение центровых отверстий и резьбы, а также изгиб.
Устранение дефектов. Изношенные валы восставливают разнообразными способами. Применение того или другого способа обусловливается наличием оборудования, технико-экономискими соображениями и ожидаемыми результатами при восстановлении деталей.
Небольшой износ шпоночных канавок устраняют вручную или станках (фрезерных, строгальных, долбежных или токарных), используя различные приспособления. После этого при сборке применяют шпонки увеличенных размеров. При значительном износе канавок их заваривают электродуговой сваркой, а в другом месте делают новые.
Если шпонка служит одновременно и для фиксации сопрягаемой детали в определенном положении, менять положение паза на валу нельзя.
Изношенные по ширине шлицы наплавляют электродуговой плавкой, вибродуговой наплавкой, наплавкой под слоем флюса; в среде защитных газов. При электродуговой наплавке шлицы плавляют электродами ЦН-250, ОЗН-300, ОЗН-350 и др.
При восстановлении валов диаметром 45—50 мм со шлицами шириной до 5—6 мм часто заваривают канавку шлица. У валов больших размеров наплавляют неизношенную сторону шлица. После наплавки деталь медленно охлаждают в песке или термостате, чтобы не допустить коробления. Валики накладывают поочередно с диаметрально противоположных сторон. Валик начинают наплавлять, в точке а (рис. 1), отступив от конца на 10—15 мм, и заканчивают в точке б. Наложение валиков в 3—4 слоя предупреждает образование закалочной зоны на границе с расплавленным металлом.
После наплавки шлицы обрабатывают на станках. Деталь на станке закрепляют по меткам, нанесенным на ее торцовой поверхности перед наплавкой. Это необходимо для того, чтобы снимать только наплавленный металл.
Шлицевые соединения восстанавливают постановкой дополнительной втулки. Для этого стачивают внутренние шлицы детали и растачивают на токарном станке так, чтобы диаметр отверстий был больше на 0,5—1,5 мм высоты шлицев вала. Затем вытачивают втулку по размерам сопрягаемой детали, нагревают и осаживают ее по валу.
Протачивают втулку на токарном станке до получения наружного диаметра, равного диаметру расточки в отверстии восстанавливаемой детали с учетом натяга; снимают фаски и приваривают в нескольких местах электросваркой (рис. 2). При обработке на станке в качестве оправки используют шлицевой вал.
Изношенные посадочные места под подшипники качения, шестерни, сальники и другие детали восстанавливают наплавкой, осталиванием, электронатиранием, хромированием, никелированием, металлизацией, с применением полимеров и электромеханической обработки и в редких случаях кузнечной осадкой или раздачей.
Иногда целесообразно восстанавливать валы напрессовкой втулок, колец, бандажей, т. е. способом использования дополнительных деталей. Предварительно валы протачивают и затем напрессовывают втулку, кольцо и т. п.
Размер проточки под дополнительную деталь должен обеспечить толщину ее стенки после обработки в пределах не менее 3—6 мм. Если эти детали воспринимают осевые нагрузки, то, кроме напрессовки с натягом, необходимо их закреплять штифтами толщиной 6—8 мм или приваривать электросваркой.
Высокую чистоту обработки и прочный поверхностный слой можно получить после накатки детали шариковыми или роликовыми накатками.
Изогнутые или скрученные валы правят в холодном или горячем состоянии.
При ремонте коробок передач обязательно надо проверять параллельность и перекосы осей валов, иначе эти дефекты вызывают износы шестерен.
Ремонт шестерен и звездочек
Ремонт шестерен и звездочек. Шестерни машин работают в условиях значительных нагрузок, перекосов в зацеплении, при большом количестве абразивных частиц и т. п. Абразивные частицы попадают в зазоры между зубьями из-за недостаточно надежного уплотнения выступающих концов валов и рычагов. В сопряжения также непрерывно попадают частицы продуктов износа трущихся деталей.
При перекосах зубчатые передачи работают в еще более тяжелых условиях. Перекосы в зацеплений возникают из-за многих причин. Одной из них служит несимметричное расположение венца шестерни по длине ступицы. Шестерни работают в весьма неблагоприятных условиях при одновременных перекосе и непараллельности валов. В этом случае напряжения увеличиваются значительно больше, чем только при перекосах или только при непараллельности.
Основные неисправности шестерен: износ зубьев по толщине, выкрашивание, скалывание и поломка зубьев, износ торцовой поверхности обода, ступицы и зубьев, износ кольцевой канавки под вилку переключения, шлицев и посадочных отверстий, трещины в ступице. Интенсивность шума повышается после 950—1000 ч работы зубчатой передачи вследствие выкрашивания зубьев.
Устранение неисправностей. При износе зубьев шестерни восстанавливают заменой венцов, давления и др.
Кроме того, у шестерен восстанавливают сопрягаемые поверхности. Венцы у шестерен заменяют в том случае, если имеется сменный венец, фиксируемый заклепками, или у блоков шестерен (например, блок шестерен коробки передач автомобиля ГАЗ-53), когда из-за поломки зубьев одного венца нецелесообразно выбраковывать дорогостоящие детали.
При замене венца срубают заклепки, спрессовывают изношенный и напрессовывают новый венец, обеспечивая совпадение канавок ступицы и венца, а также торцовых поверхностей.
Головки заклепок должны быть плотно прижаты к торцовым поверхностям венца и ступицы. Торцовое биение венцов со ступицами в сборе допускается не более 0,25 мм.
В отдельных случаях наплавляют изношенные зубья газовой или электродуговой сваркой. При наплавке цементованных шестерен пользуются присадочным металлом с более высоким содержанием углерода.
Хорошие результаты для повышения износостойкости и прочности наплавляемых зубьев шестерен получают в случае применения сормайта в качестве присадочного материала. Сормайт рекомендуется использовать для наплавки зубьев при торцовых износах, выкрашивании цементованного слоя или сколов. Справка сормайт 1 (сплав 3,1% углерода, 28% хрома, 3% никеля, 1,5% марганца, 3,5% кремния)
Наплавленные зубья фрезеруют, шлифуют или обрабатывают (электроэрозионным способом. Перед наплавкой шестерню отжигают, нагревая до температуры 850—900° С.
Разработана и успешно применяется специальная установка для механизированной наплавки зубьев под слоем флюса.
Шестерни, изношенные по толщине и имеющие на венце достаточный запас металла, можно восстанавливать методом горячей осадки. В этом случае изготовляют штампы для шестерен каждого вида.
Способом осадки могут быть восстановлены как блочные, так и одинарные цилиндрические шестерни без поломанных зубьев, сколов, трешин на ободе и ступице.
Сущность осадки сводится к следующему. Восстанавливаемую деталь нагревают и помещают в штамп (рис. 3). Кроме штампов, необходимо иметь гидравлические прессы (40—50-тонные) или горяче-штамповочные кривошипные прессы и термические печи.
Для того чтобы диаметр посадочного отверстия не менялся, используют оправку, имеющую форму и размеры такие же, как и у сопрягаемого вала. Шестерни, изготовленные из стали 18ХГТ, рекомендуется восстанавливать осадкой при нагреве до температуры 900—1160° С, а шестерни из стали 40Х — при нагреве до температуры 900—1000° С.
Шестерни из цементованных сталей нагревают в карбюризаторе, а шестерни из среднеуглеродистой стали — в соляных ваннах. При осадке перемещают металл с торцовых поверхностей обода к изношенным зубьям и посадочному отверстию.
Размеры штампа должны обеспечить получение припусков по толщине зуба 1,4—1,5 мм, по наружному диаметру 0,5—0,8 мм и по диаметру внутреннего отверстия 1,2—1,4 мм для последующей обработки.
Перед механической обработкой на токарных и зуборезных станках шестерню подвергают нормализации нагревая до температуры 830—850° С и охлаждая на воздухе.
После механической обработки проводят термообработку шестерни. Восстановленные этим способом шестерни должны отвечать тем же требованиям, что и новые детали.
Односторонне изношенные шестерни можно использовать для дальнейшей работы, если их перевернуть неработавшей стороной. Отдельные шестерни при этом требуют незначительной переделки. Например, шестерню с несимметричной ступицей подрезают с одной стороны (рис. 4 а), делая ступицу симметричной. Для правильного положения шестерни на вал при сборке надевают кольца с шириной, равной ширине отрезанной части, т. е. х. Остальные размеры соответствуют размерам сопрягаемого вала и других деталей.
Односторонне изношенные подвижные шестерни с кольцевыми проточками для вилок переключения передач не только переворачивают на 180° для работы иеизношенной стороной, но и резцом с пластиной из твердого сплава типа Т5К10 отрезают часть ступицы (рис. 4, б) и к противоположной стороне приваривают новую кольцевую муфту.
Конструкция отдельных шестерен позволяет использовать их для работы в качестве других деталей.
Например, при поломке зубьев венца третьей передачи шестерню трактора класса 60 кН с венцом четвертой передачи используют для шестерни реверса. Для этого резцом с пластиной из твердого сплава отрезают венец третьей передачи. Венец четвертой передачи соответствует по количеству зубьеа шестерне реверса (рис. 4, в).
Симметричное расположение шестерен дает возможность переворачивать их при одностороннем износе для работы неизношенной стороной зуба и позволяет значительно продлить технический ресурс деталей при нормальном зацеплении. После переворачивания венца торцы зубьев закругляют.
Изношенные пазы подвижных шестерен под вилку включения восстанавливают проточкой до выведения следов износа. Вилку переключения передач в этом случае наплавляют, а затем обрабатывают до размера проточенного паза. При износе шлицев шестерен рекомендуется запрессовывать в них шлицевые втулки (см. рис.2).
Ремонт подшипников качения
Ремонт подшипников качения. При работе подшипников качения из-за износа увеличиваются их осевые и радиальные зазоры, вследствие чего возникает шум, недопустимо нагреваются узлы и повышается износ других деталей.
На технический ресурс подшипников большое влияние оказывают непараллельность и перекос осей валов.
Основные неисправности подшипников качения: ослабление посадки в корпусах и на шейках валов, износ поверхностей качения (беговых дорожек), поломки, выкрашивание и трещины в кольцах, телах качения и сепараторах, их износ и поломки, а также перегрев, приводящий к появлению цветов побежалости.
Подшипники качения выбраковывают при появлении цветов побежалости, сколах металла или трещинах, выкрашивании или шелушении поверхностей качения, появлении раковин коррозийного характера.
Ремонтируют подшипники специализированные ремонтные предприятия. При ремонте выполняют следующие операции: разбирают подшипники, проверяют и сортируют детали, шлифуют поверхности колец, устраняют износ наружной и внутренней поверхностей хромированием или осталива-нием, шлифуют беговые дорожки, комплектуют подшипники шариками или роликами увеличенных размеров, подгоняют сепараторы и склепывают их.
Ремонт резьбовых соединений зависит от характера дефекта.
Основные дефекты резьбовых соединений: износ и срыв резьбы, ее выкрашивание, появление забоин и заусенцев.
Под резьбовые пробки резьбу нарезают только при помощи двух метчиков. Резьбовые пробки изготавливают из мягкой стали. Перед ввертыванием пробок их обмазывают масляной краской или клеем БФ-2. Ввертывают пробки в новые отверстия до отказа. В месте соприкосновения пробки с телом детали просверливают отверстия, в которые запрессовывают стальные стопорные штифты, обеспечивающие неподвижность этого соединения.
При восстановлении резьбы в нескольких отверстиях их рассверливают по кондуктору, чтобы обеспечить правильное взаимное расположение соединяемых деталей.
ВОССТАНОВЛЕНИЕ ДЕТАЛЕЙ ХОДОВОЙ ЧАСТИ ГУСЕНИЧНЫХ ТРАКТОРОВ
|
|
Таксономические единицы (категории) растений: Каждая система классификации состоит из определённых соподчиненных друг другу...
Особенности сооружения опор в сложных условиях: Сооружение ВЛ в районах с суровыми климатическими и тяжелыми геологическими условиями...
Биохимия спиртового брожения: Основу технологии получения пива составляет спиртовое брожение, - при котором сахар превращается...
Семя – орган полового размножения и расселения растений: наружи у семян имеется плотный покров – кожура...
© cyberpedia.su 2017-2024 - Не является автором материалов. Исключительное право сохранено за автором текста.
Если вы не хотите, чтобы данный материал был у нас на сайте, перейдите по ссылке: Нарушение авторских прав. Мы поможем в написании вашей работы!