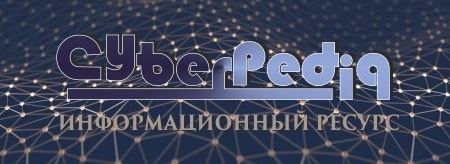
История развития хранилищ для нефти: Первые склады нефти появились в XVII веке. Они представляли собой землянные ямы-амбара глубиной 4…5 м...
Поперечные профили набережных и береговой полосы: На городских территориях берегоукрепление проектируют с учетом технических и экономических требований, но особое значение придают эстетическим...
Топ:
Эволюция кровеносной системы позвоночных животных: Биологическая эволюция – необратимый процесс исторического развития живой природы...
Процедура выполнения команд. Рабочий цикл процессора: Функционирование процессора в основном состоит из повторяющихся рабочих циклов, каждый из которых соответствует...
Основы обеспечения единства измерений: Обеспечение единства измерений - деятельность метрологических служб, направленная на достижение...
Интересное:
Что нужно делать при лейкемии: Прежде всего, необходимо выяснить, не страдаете ли вы каким-либо душевным недугом...
Влияние предпринимательской среды на эффективное функционирование предприятия: Предпринимательская среда – это совокупность внешних и внутренних факторов, оказывающих влияние на функционирование фирмы...
Лечение прогрессирующих форм рака: Одним из наиболее важных достижений экспериментальной химиотерапии опухолей, начатой в 60-х и реализованной в 70-х годах, является...
Дисциплины:
![]() |
![]() |
5.00
из
|
Заказать работу |
|
|
Одним из первых отечественных котлов, оборудованных топкой кипящего слоя с погруженными в него поверхностями нагрева, был опытно-промышленный котел КПВ-ПС-5,7-14-180, установленный на ТЭЦ ЦКТИ. При разработке котла за основу взят серийный котел ДКВр-2,5-14, выпускаемый Бийским котлостроительным заводом. После реконструкции котла без изменения остались верхний и нижний барабаны (рис. 33), а также экраны и котельный Пучок, сепарационные и обдувочные устройства, опорная рама, каркас и обмуровка котла [43].
При реконструкции котла ДКВр в нижней части топки установили газораспределительную решетку с колпачками. При размерах 1925x1500 мм решетка имела 169 отверстий диаметром 60 мм (шаг по фронту 140 мм, по глубине 110 мм). Воздушный канал каждого колпачка имел диаметр 44 мм, а в головке - по 10 отверстий диаметром 8 мм, направленных под углом 30° к плоскости решетки. Устройство для отвода золы и материала слоя расположено в центре газораспределительной решетки. На фронтовой стене, на 200 мм выше колпачков, расположены две фурмы для ввода топлива. В слой погружены змеевики теплофикационного экономайзера; выше слоя, на фронтовой стене, установлена растопочная газомазутная горелка, еще выше (в надслоевом пространстве топки)
Рис. 33. Котел КПВ ПС-5,7-14-180. с кипящим слоем [39]
- вторая ступень теплофикационного экономайзера.
Под решетку подавался горячий воздух после воздухоподогревателя (180-200°С), расчетное сопротивление решетки составляло 2,35 кПа, слоя 10,2 кПа. Для наполнения слоя использовался дробленый шамот и речной песок с размером кусков 0-10 мм. Проектная высота слоя в спокойном состоянии равнялась 690 мм, в рабочем 1000 мм. Температура в слое поддерживалась на уровне 880-900°С за.счет интенсивного отвода теплоты погруженной в слой поверхностью нагрева. Котел обеспечили необходимыми контрольно-измерительными приборами и системой автоматического регулирования.
|
После пробных пусков котла на березовском буром угле провели балансовые опыты на экибастузском каменном и ирша-бородинском буром углях. Эти опыты в основном подтвердили расчетные значения теплопроизводительности котла, которая увеличилась почти в 4 раза по сравнению с котлом,ДКВр-2^5-14.
Для растопки котла использовалась работающая под давлением предвключения камера сгорания, в которой сжигался газ. Продукты сгорания этой камеры с температурой до 650°С подавались под решетку до тех пор, пока материал слоя не нагревался до 450°С (при работе котла на буром угле) или до 550°С (при работе на каменном угле). Только после достижения этих температур в слой подавалось топливо. Газовая горелка, установленная над слоем, позволяла сократить время растопки.
Содержание горючих в уносе при сжигании ирша-бородинского угля составляло в зависимости от избытка воздуха 4-12%, а при сжигании экибастузского угля 14-26% [45]. Чтобы снизить недожог топлива, пришлось работать с повышенными избытками воздуха и уменьшенной высотой слоя. Дожигание уловленного в циклоне уноса при возврате его в низкотемпературный слой оказалось малоэффективным и поэтому для следующих котлов решено организовать специальную секцию кипящего слоя с повышенной температурой (1000-1100°С).
Важным достоинством топки явилось снижение вредных выбросов в атмосферу. Измерение содержания диоксида серы и оксидов азота в дымовых газах за котлом показало, что даже без добавки в слой присадок, только за счет щелочных компонентов минеральной массы топлива, выбросы S02 снижаются на 60-80% при сжигании ирша-бородинского угля и на 40-50% при сжигании экибастузского угля. Что касается оксидов азота, то их концентрация оказалась примерно на том же уровне, что и у крупных пылеугольных котлов: 340-450 мг/м3 при сжигании ирша-бородинского угля и 600-630 мг/м3 при сжигании экибастузского угля.
|
Пo данным [45] котел с кипящим слоем в течение года проработал 534 ч, причем максимальная непрерывная кампания
продолжалась 92 ч. Даже за столь непродолжительное время удалось обнаружить, что при сжигании экибастузского угля, и в меньшей степени - ирша-бородинского, происходит укрупнение слоя. Из-за этого, в частности на экибастузском угле, не удавалось проработать непрерывно более 41 ч. Обнаружили также, что попадающие в слой крупные куски (25-30 мм) залегают на поду. Это приводило к дополнительной агломерации кусков и к последующему аварийному останову котла.
Зондирование топки в поперечном направлении показало наличие значительных перекосов (до 100° по температуре и до 13-15% по концентрации кислорода и С02). Эти измерения опровергли предположение о том, что кипящий слой интенсивно перемешивает твердую фазу. Практический вывод из этого факта состоит в том, что при подаче топлива в слой площадь решетки, обслуживаемая одним питателем, не должна превышать 1-1,5 м2. Следовательно, для котла паропроизводительностью 420 т/ч подача топлива в слой потребует установки 120-160 вводов топлива.
Выводы, к которым пришли авторы [45], состояли в следующем:
эффективность сжигания топлива в кипящем слое определяется характеристикой угля и его дисперсным составом, а также избытком воздуха в слое;
для снижения потерь топлива с недожогом необходимо осуществлять возврат уноса на дожигание и иметь значительный объем надслоевого пространства;
необходимо создать эффективную и простую схему подачи топлива в топку и такую воздухораспределительную решетку, которая обеспечивала бы вывод крупных кусков из слоя.
В дальнейшем НПО ЦКТИ совместно с БиКЗ разработано несколько промышленных котлов с традиционным кипящим слоем для сжигания высокозольных топлив. Конструкции этих котлов базируются на существующей технологии Бийского котельного завода. Так, например, котел КЕ-10-14ПС разработан на базе котла КЕ-6,5-14, который можно транспортировать к месту установки одним блоком [46].
Котел ДЕ-10-14ПС специально спроектировали для кипящего слоя, но большинство его узлов аналогично котлам серии ДЕ, выпускаемым БиКЗ. Этот котел также может перевозиться железнодорожным транспортом.
|
В [46] приведены сведения об опытном образце более крупного котла с кипящим слоем Е-25-14ПС. Этот однобарабанный котел производительностью 25 т/ч с параметрами пара 1,35 МПа, 194°С создан на основе серийного котла КР-10-145 и предназначен для промышленных котельных. Котел не имеет воздухоподогревателя, но питательная вода, поступающая в котел с температурой 100°С нагревается в экономайзере. Оборудование котла топкой с кипящим слоем позволило уменьшить массу металла трубной системы с 26,9 до 15,7 т, но мощность вспомогательного оборудования возросла с 55,5 до 182 кВт.
Важные исследования были проведены на котле ДЕ-25-19ПС производительностью 18 т/ч с параметрами пара 1,9 МПа, 450°С [47]. Этот экспериментальный котел создали для проверки ряда технических решений, поэтому его конструкция допускала возможность замены отдельных узлов. В частности, на котле предполагалось проверить разные способы подачи топлива: забрасывание угля на слой, подача угля пневмотранспортом в слой через четыре-шесть наклонных патрубков на фронтовой стене и вертикальная подача топлива снизу', через стояки, пронизывающие решетку кипящего слоя.
Топка этого котла состояла из трех секций кипящего слоя, причем правая и левая отличались размерами (1,9 и 3,1 м2), а средняя секция (1,5 м2) служила для дожигания уловленного уноса. Воздухораспределительная решетка колпачкового типа имела проходное сечение 2,5%.
Пуск котла ДЕ-25-19ПС предполагал растопку средней секции без погруженных в слой поверхностей нагрева, с последующим перепуском материала слоя через специальные отверстия в соседние секции. Комбинация различных секций являлась дополнительным средством регулирования мощности котла. В слой поочередно устанавливали экономайзерную, испарительную (с принудительной циркуляцией) и пароперегревательную поверхности нагрева. Под воздухораспределительной решеткой каждой секции установили системы для удаления золы из слоя: одна - прямоточная и вторая - с затвором, работающим на принципе кипящего слоя.
Затем провели опыты при сжигании экибастузского и кузнецкого каменных углей, бурого угля Канско-Ачинского бассейна, а также смеси этих углей и мазута марки М100. В процессе испытаний, общая длительность которых составила 100 ч, котел растапливали около 80 раз. Длительность наиболее представительных опытов менялась от 3 до 15 ч.
|
Проведенные опыты показали, что при сжигании угля г: номинальной нагрузке котла потери с механической неполнотой сгорания увеличиваются от 2 до 11% по мере снижения насыпной высоты слоя Я0 от 1200 до 300 мм. В этом же диапазоне изменения Я0 потери с. химической неполнотой сгорания q3, наоборот, снижаются с 3 до 0,5%. В опытах с изменением коэффициента избытка воздуха ат было установлено, что приемлемые потери <?4 = 1,5-5-4% обеспечиваются только при ат > 1,2.'
Потери g3 появляются при ат <1,2. КПД котла на угле при оптимальном режиме оказался ниже 90% [43].
Наиболее крупным котлом, оборудованным топкой с обычным кипящим слоем, является котел ЕПр-420-140КС производительностью 420 т/ч. Этот котел создавался НПО ЦКТИ, ВТИ, ПО "Сибэнергомаш", СКВ ВТИ и ВНИПИЭнергопромом.
Котел имеет стандартные параметры барабанных пылеугольных котлов аналогичной паропроизводительности (13,4 МПа, 560°С), но масса металла под давлением у него в 1,5 раза, а общая масса металла в 2 раза меньше, чем у котла Е-420-140 с факельным сжиганием. Топка котла имеет четыре самостоятельных секции кипящего слоя, расположенные попарно одна над другой. Одна из четырех секций служит для дожигания уловленного в циклонах уноса. Котел рассчитан на сжигание бурых углей Канско-Ачинского бассейна, минеральная часть которых содержит оксид кальция. Это позволит значительно сократить выбросы сернистого ангидрида в атмосферу после установки котла ЕПр-420-140-КС на Барнаульской ТЭЦ-3.
|
|
Индивидуальные и групповые автопоилки: для животных. Схемы и конструкции...
Архитектура электронного правительства: Единая архитектура – это методологический подход при создании системы управления государства, который строится...
Своеобразие русской архитектуры: Основной материал – дерево – быстрота постройки, но недолговечность и необходимость деления...
Типы оградительных сооружений в морском порту: По расположению оградительных сооружений в плане различают волноломы, обе оконечности...
© cyberpedia.su 2017-2024 - Не является автором материалов. Исключительное право сохранено за автором текста.
Если вы не хотите, чтобы данный материал был у нас на сайте, перейдите по ссылке: Нарушение авторских прав. Мы поможем в написании вашей работы!