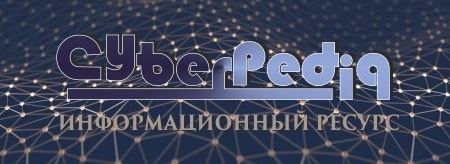
Семя – орган полового размножения и расселения растений: наружи у семян имеется плотный покров – кожура...
Организация стока поверхностных вод: Наибольшее количество влаги на земном шаре испаряется с поверхности морей и океанов (88‰)...
Топ:
Когда производится ограждение поезда, остановившегося на перегоне: Во всех случаях немедленно должно быть ограждено место препятствия для движения поездов на смежном пути двухпутного...
Оценка эффективности инструментов коммуникационной политики: Внешние коммуникации - обмен информацией между организацией и её внешней средой...
Интересное:
Что нужно делать при лейкемии: Прежде всего, необходимо выяснить, не страдаете ли вы каким-либо душевным недугом...
Берегоукрепление оползневых склонов: На прибрежных склонах основной причиной развития оползневых процессов является подмыв водами рек естественных склонов...
Принципы управления денежными потоками: одним из методов контроля за состоянием денежной наличности является...
Дисциплины:
![]() |
![]() |
5.00
из
|
Заказать работу |
|
|
Корпусная деталь состоит из стенок, ребер, бобышек, фланцев и других элементов, соединенных в единое целое.
При конструировании литой корпусной детали стенки следует по возможности выполнять одинаковой толщины. Толщину стенок литых деталей стремятся уменьшить до величины, определяемой условиями хорошего заполнения формы жидким металлом. Поэтому чем больше размеры корпуса, тем толще должный быть его стенки. Основной материал корпусов – серый чугун не ниже марки СЧ15.
Толщину стенки δ принимаем 7мм
Радиусы закруглений внешний R и внутренний r принимаем R=10мм; r=3.5мм исходя из выбранной толщины стенки.
Крышки подшипников изготавливаем из чугуна марки СЧ15.
Чтобы поверхность фланца крышки и торца корпуса сопрягались по плоскости, на цилиндрической центрирующей поверхности перед торцом фланца делаем канавку шириной b. Поле допуска диаметра центрирующего пояска принимаем Ø62h7, Ø100h7.
Определяющим при конструировании крышки является диаметр D отверстия в корпусе под подшипник. По нему определяют толщину δ стенки, диаметра d и числа z витков крепления крышки к корпусу (2,стр.148).
Для Ø62h7, принимаем 6мм,
6мм,
4мм.
Для Ø100h7 принимаем 7мм,
10мм,
4мм.
Размеры других конструктивных элементов крышки:
[2,стр.148]
δ1=1,2·δ;
δ2=(0,9…1)·δ;
Для Ø62h8:
δ1=1,2·6=6 мм;
δ2=(0,9…1)·6=5мм.
Для Ø100h8:
Dф=100+(4…4,4)·10=130 мм,
c≈d=10 мм,
δ1=1,2·7=8 мм;
δ2=(0,9…1)·7=7 мм.
На входном и выходном валу устанавливаем манжетное уплотнение.
К корпусным относят детали, обеспечивающие взаимное расположение деталей узла и воспринимающие основные силы, действующие в машине. Корпусные детали обычно имеют довольно сложную форму, поэтому их получают методом литья или методом сварки.
|
Корпусная деталь состоит из стенок, ребер, бобышек, фланцев и других элементов соединенных в целое.
При конструировании литой корпусной детали стенки следует по возможности выполнять одинаковой толщины. Толщину стенок литых деталей стремятся уменьшить до величины, определяемой условиями хорошего заполнения формы жидким металлом. Поэтому чем больше размеры корпуса, тем толще должны быть его стенки. Основной материал корпусов – серый чугун не ниже марки СЧ15.
Рис 4.1 Схема вида и установки крышки
Для редукторов толщину стенки, отвечающую требованиям технологии литья, необходимой прочности и жесткости корпуса вычисляют по формуле:
[2, стр.257]
где, Т – вращающий момент на выходном валу.
Плоскости стенок, встречающиеся под прямым углом, сопрягают дугами радиусом r и R.
[2, стр.257]
Толщины наружных ребер жесткости и их основания принимают равной 0,9…1,0 толщины основной стенки d. Толщина внутренних ребер из-за их более медленного охлаждения должна быть равной 0,8d. Высоту ребер принимают . Поперечное сечение ребер жесткости выполняют с уклоном.
Часто к корпусной детали прикрепляют крышки, фланцы, кронштейны. Для их установки и крепления на корпусной детали предусматривают опорные платики. Эти платики при неточном литье могут быть смещены. Учитывая это, размеры сторон опорных платиков должны быть на величину С больше размеров опорных поверхностей прикрепляемых к деталей. Для литых деталей средних размеров:
[2, стр.258]
При конструировании корпусных деталей следует отделять обрабатываемые поверхности от «черных». Обрабатываемые поверхности выполняют в виде платиков, высоту h которых можно принимать:
|
[2, стр.258]
С целью повышения жесткости прилив связывают ребрами с корпусом и крышкой редуктора.
Для соединения корпуса и крышки редуктора по всему контуру плоскости разъема выполняют специальные фланцы. На коротких базовых сторонах фланцы располагают внутрь от стенки корпуса. Вследствие погрешностей при изготовлении моделей крышки и корпуса, погрешностей при формовке и во время удаления моделей из формы размеры отливок получают с отклонениями от номинальных размеров. Это приводит к несовпадению внешних контуров крышки и корпуса, ухудшает внешний вид. Несовпадение станет незаметным, если крышку корпуса выполнить с напуском. Размеры конструктивных элементов:
[2, стр.263]
Конструктивное оформление приливов для подшипниковых гнезд:
Диаметр прилива принимают для привертной крышки:
[2, стр.263]
где, DФ – диаметр фланца крышки подшипника
Для диаметра 86h8
, принимаем 90мм
Для диаметра 130h8
, принимаем 135мм
Длину l подшипниковых гнезд определяют конструктивно. Она зависит от размеров устанавливаемых в гнезда деталей: ширины подшипника, высоты крышки, толщины кольца, осевого размера шайбы.
Крепление крышки редуктора к корпусу:
Для соединения крышки с корпусом используют болты с наружной шестигранной головкой. Размеры конструктивных элементов:
[2,стр.264]
где d – диаметр болтов крепления крышки принимают в зависимости от вращающего момента Т2Т на выходном валу редуктора:\
, тогда:
Расстояние между болтами:
Фиксирование крышки относительно корпуса редуктора
При сборке редуктора во время затяжки болтов, соединяющих корпус с крышкой, Возможно некоторое смещение крышки относительно корпуса, что вызовет деформацию наружных колец подшипников, имеющих малую жесткость. Кроме того торцы приливов у подшипниковых гнезд на крышке редуктора и корпусе могут не совпасть, что повлечет перекос крышек подшипников и наружных колец самих подшипников. Следовательно, при сборке редуктора нужно точно фиксировать положение крышки относительно корпуса. Необходимую точность фиксирования достигают штифтами, которые располагают на возможно большем расстоянии друг от друга. Диаметр штифтов:
|
, [2, стр.265]
где d - диаметр крепежного болта
Кроме фиксирования штифты предохраняют крышку и корпус при растачивании подшипниковых отверстий. Обычно применяют два конических штифта с внутренней резьбой, которые устанавливают по срезам углов крышки или в специально выполненных нишах. Резьбу используют для извлечения штифта при разборке редуктора.
Конструктивное оформление опорной части редуктора:
Для крепления корпуса редуктора к фундаменту применяют фундаментные болты. Диаметр болта крепления редуктора к плите(раме):
[2, стр.267]
где d – диаметр болта крепления крышки и корпуса редуктора.
, принимаем фундаментный болт М16.
Число болтов z принимается в зависимости от межосевого расстояния тихоходной ступени z=4 т.к. aWT < 315мм.
Оформление сливных отверстий:
При работе передач продукты изнашивания постепенно загрязняют масло. Поэтому масло залитое в редуктор периодически меняют. Для замены масло в корпусе предусматривают сливное отверстие, закрываемое пробкой с цилиндрической или конической резьбой.
Цилиндрическая резьба не создает надежного уплотнения, поэтому под пробку ставят уплотняющие прокладки из фибры или паронита. Для наблюдения за уровнем масла в корпусе установлен маслоуказатель жезловый (щуп).
При длительной работе в связи с нагревом повышается давление внутри корпуса. При интенсивном тепловыделении это приводит к просачиванию масла через уплотнения и стыки. Чтобы избежать этого, внутреннюю полость корпуса сообщают с внешней средой путем установки отдушины в его верхних точках.
5. Расчёт шпоночного соединения.
Быстроходный вал (муфта). [стр.168-175].
|
|
|
Таксономические единицы (категории) растений: Каждая система классификации состоит из определённых соподчиненных друг другу...
История развития пистолетов-пулеметов: Предпосылкой для возникновения пистолетов-пулеметов послужила давняя тенденция тяготения винтовок...
Папиллярные узоры пальцев рук - маркер спортивных способностей: дерматоглифические признаки формируются на 3-5 месяце беременности, не изменяются в течение жизни...
Индивидуальные и групповые автопоилки: для животных. Схемы и конструкции...
© cyberpedia.su 2017-2024 - Не является автором материалов. Исключительное право сохранено за автором текста.
Если вы не хотите, чтобы данный материал был у нас на сайте, перейдите по ссылке: Нарушение авторских прав. Мы поможем в написании вашей работы!