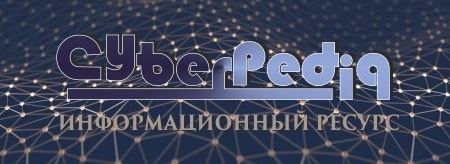
Автоматическое растормаживание колес: Тормозные устройства колес предназначены для уменьшения длины пробега и улучшения маневрирования ВС при...
Наброски и зарисовки растений, плодов, цветов: Освоить конструктивное построение структуры дерева через зарисовки отдельных деревьев, группы деревьев...
Топ:
Характеристика АТП и сварочно-жестяницкого участка: Транспорт в настоящее время является одной из важнейших отраслей народного хозяйства...
Оценка эффективности инструментов коммуникационной политики: Внешние коммуникации - обмен информацией между организацией и её внешней средой...
Интересное:
Берегоукрепление оползневых склонов: На прибрежных склонах основной причиной развития оползневых процессов является подмыв водами рек естественных склонов...
Распространение рака на другие отдаленные от желудка органы: Характерных симптомов рака желудка не существует. Выраженные симптомы появляются, когда опухоль...
Лечение прогрессирующих форм рака: Одним из наиболее важных достижений экспериментальной химиотерапии опухолей, начатой в 60-х и реализованной в 70-х годах, является...
Дисциплины:
![]() |
![]() |
5.00
из
|
Заказать работу |
|
|
СОДЕРЖАНИЕ
Введение
1. Общая часть
1.1 Краткая характеристика и сравнение способов производства КСl из сильвинита
1.2 Характеристика исходного сырья и готовой продукции
1.3 Описание технологического процесса производства хлористого калия по фабрике
1.4 Требования, предъявляемые к техническому обслуживанию и ремонту технологического оборудования
1.4.1 Требования, предъявляемые к техническому обслуживанию и ремонту стержневой мельницы МСЦ 3,2х4,5
1.5 Порядок сдачи оборудования в ремонт и прием оборудования после ремонта
2. Специальная часть
2.1 Описание технологического процесса отделения.
2.2 Назначение, устройство, принцип работы и техническая характеристика стержневой мельницы МСЦ 3200х4500
2.3 Технологический процесс капитального ремонта аппарата.
2.3.1 Составление необходимой документации на ремонт
2.3.2 Ремонт отдельных деталей аппарата.
2.4 Технологический расчет аппарата
2.5 Механический расчет аппарата
3. Правила безопасности при эксплуатации и проведении ремонтных работ
4. Охрана окружающей среды на калийных предприятиях
5. Экономическая часть.
5.1 Составление графика ППР
5.2 Расчет затрат на основные и вспомогательные материалы.
5.3 Расчет затрат на электроэнергию
5.4 Расчет затрат на амортизацию
5.5 расчет заработной платы и отчислений от фонда оплаты труда
5.6 Составление сметы затрат
5.7 Основные технико-экономические показатели
Литература
ВВЕДЕНИЕ
Рациональное использование минерально-сырьевых ресурсов, максимальное извлечение всех ценных компонентов из руд – главная задача обогатительной науки и практики.
Республиканское унитарное предприятие “ Производственное объединение “Беларуськалий” – один из крупнейших в мире и самый крупный на территории СНГ производитель и поставщик калийных минеральных удобрений.
|
Функционируя на базе Старобинского месторождения калийных солей ПО “Беларуськалий” включает в себя четыре рудоуправления, вспомогательные цеха и обслуживающие подразделения, в которых занято около 20 тысяч человек.
В состав каждого рудоуправления входят рудник для добычи калийной руды и обогатительная фабрика для ее переработки и выпуска минеральных калийных удобрений в форме мелкозернистого, мелкокристаллического и гранулированного концентрата хлористого калия, а также соли калийной смешанной. Кроме того, объединение выпускает техническую, пищевую и кормовую поваренную соль.
Располагая достаточной природной сырьевой базой, высоким производительным потенциалом, высококвалифицированными кадрами рабочих и специалистов, объединение имеет все возможности для дальнейшего повышения эффективности производства, внедрения новой техники и совершенствования технологических процессов, обеспечения высокого качества всех видов работ и конечного продукта.
Современные обогатительные фабрики - высокомеханизированные предприятия. Они оснащены большим числом сложных установок, машин и механизмов, составляющих в совокупности непрерывные технологические линии. Все оборудование этих линий связано между собой определенными технологическими зависимостями и предназначено для переработки или транспортировки руды и продуктов обогащения в едином технологическом процессе.
Эксплуатация оборудования в таких линиях предусматривает: контроль и регулировку производительности машин, контроль состояния смазочных систем, температуры трущихся частей механизмов и обмоток электродвигателей, предотвращение аварийных ситуаций, устранение возникающих неисправностей, пуск и останов оборудования.
Для облагораживания или увеличения поверхности фазового контакта минерала, применяемого в том или ином процессе, его подвергают измельчению. На разных производствах измельчают твердое минеральное сырье, полуфабрикаты, а также готовую продукцию. Измельчаемые материалы по своей структуре могут быть твердыми, мягкими, хрупким, вязкими, а также обладать различными химическими свойствами. От свойств материала и заданной степени измельчения зависят продолжительность процесса и тип измельчающего оборудования. Отличают следующие виды измельчения: дробление крупное (размер кусков после измельчения 250 мм); дробление среднее (20мм); дробление мелкое (1мм); помол грубый (0,1— 0,004мм); помол средний (0,005—0,015 мм); помол тонкий (0,001— 0,005мм); помол коллоидный (менее 0,001 мм).
|
Технологическое назначение операций дробления и измельчения заключается в том, чтобы раскрыть минералы при максимально возможной крупности, при минимальном переизмельчении, т.е. осуществить принцип «не дробить ничего лишнего».
Кроме того, от обслуживающего персонала требуется четкое выполнение графиков чистки и ремонта оборудования, работающего в тяжелых условиях непрерывного производства. Вследствие воздействия высоких механических нагрузок и химически агрессивной среды узлы и детали машин подвергаются высокоаброзивному износу. В некоторых случаях износ узлов машин влияет на качество продуктов обогащения.
Квалифицированное обслуживание оборудования обогатительной фабрики невозможно без знания устройства, принципа действия и возможных неисправностей машин и аппаратов.
Одним из важнейших условий эффективного использования промышленного оборудования, увеличения срока его службы и надежности в работе является правильная эксплуатация и высококачественный ремонт. Эти решаются с помощью разработанной в нашей стране системы планово – предупредительного ремонта (ППР), которая регламентирует периодичность, состав и объем работ по техническому обслуживанию и ремонту оборудования. В ремонтном деле важную роль играет слесарь, который должен иметь хорошую техническую подготовку. Он должен знать назначение и устройство сборочных единиц оборудования, распознавать признаки и причины износа деталей различных механизмов и владеть современными способами восстановления изношенных частей машины.
Постоянная работоспособность всякого оборудования, поддерживается его правильной эксплуатации и своевременным и качественным ремонтом. Поэтому бесспорно большое значение ремонтной службы для нормальной жизнедеятельности любого предприятия.
|
Повышение эффективности обогатительного производства требует разработки и внедрения новых технологических процессов и оборудования, обеспечивающих получения высоких технико-экономических показателей в условиях постепенного снижения качества исходного сырья. Технологические процессы должны совершенствоваться в направлении сокращения энергозатрат и материалов на производство концентратов, обеспечения наиболее полного использования в народном хозяйстве всех компонентов сырья, устранения вредного влияния обогатительного производства на окружающую среду.
ОБЩАЯ ЧАСТЬ
Флотация
Процесс флотации предназначен для максимального выделения KCl из руды и осуществляется в флотокамерах ФМ-6,3КСМ (10 шт.) и ФМ-6,3КСЛ (7 шт.) на одну секцию.
Процесс флотации состоит из основной, контрольной, трех перечистых операций и операции выщелачивания.
Питание сильвинитовой флотации являются пески перечитсных циклонов и камерный продукт машин шламовой флотации.
Пески перечитсных циклонов 5 ст. обесшламливания поступают в кантактный чан КЧ-3,15 (8 шт.),а камерный продукт шламовой флотации через 8-струйный пульподелитель распределяются по работающим станциям. Время основной флотации 5-6 мин. Время перечистных операций 3-5 мин. Для повышения массовой доли KCl в окончательном концентрате в желоб хлористого калия 3-й перечистки подается выщелачивающий раствор. Выщелачивающим раствором являются сливы сгустителей Г-2, С-9 мокрой стадии газоочистки отделения сушки и грануляции.
Флотационный концентрат и хвосты флотации поступают на обезвоживание в отделение фильтрации.
Сгущение и обезвоживание хвостов флотации.
Хвосты контрольной флотации блок-насосами перекачиваются на предварительное сгущение в гидроциклонах СВП-500. Пески гидроциклонов поступают в смесительные емкости, слив гидроциклонов поступает на сгущение в сгустители П-30. Сгущенный продукт насосами перекачивается в пульподелитель и совместно с песками хвостовых гидроциклонов распределяется по хвостовым вакуум-фильтрам БЛК-40 и на ленточный вакуум-фильтр.
|
Кек хвостов с влажностью не более 10% поступает на ленточный конвейер КЛС-1400 и через ПТС удаляется и складируется на солеотвале.
Фильтрат хвостовых вакуум-фильтров через повушку, ресивер, барометрические стаканы поступает в зумпф на отметку -3,6 метров, откуда насосами 8ГРК8 перекачивается на сгущение в сгустители.
Сгущение шлаков
Слив сгустителей обесшламливания вместе с пенным продуктом шламовых флотомашин насосами 20НДС распеделяется по шламовым сгустителям П-30 1 и 2 очереди для сгущения глинистых шламов. Для увеличения скорости осаждения гл. шламов в питание штамовых сгустителей подается раствор флокулянта. Осветвленный маточник насосами 20НДС с 1-ой очереди сгущения и 2-ой перекачиваются в коллектор чистого маточника гл. корпуса.
Сгущенные глинистые шламы разбавляются рассолом и откачиваются на шламохранилище насосами ГР400/40.
Сушка калия хлористого
Кек калия хлористого после центрифуг с влагой до 5% системой конвейеров распределяется по сушильным барабанам типа УСБ 3200х22000. После сушки концентрат с влагой не более 0,5% системой конвейеров складируется в склад готового продукта. В смесители конвейера концентрат обрабатывается 5% раствором омина для предотвращения слеживаемости.
Кек калия хлористого после вакуум-фильтров с влагой до 8,3% распределяется по сушильным барабанам, где высушивается до влажности 2%, часть кека транспортируется через сушильный барабан без теплоносителя и по конвейеру подается в лопастной смеситель для смешивания с циклонной пылью сухой стадии газоочистки и дополнительной обработки 10-20% раствором аммофоса.
Образовавшаяся при этом смесь с влагой 3-6% по конвейеру подается в отделение грануляции для получения гранулированного продукта и агломерации мелкого зерна.
Термическая сушка конвективным способом основана на испарении содержащейся в концентраторе избыточной массовой доли воды в окружающую его воздушную среду при нагреве высушиваемого калия хлористого.
В качестве теплоносителя в сушильных установках используются топочные газы, образующиеся при сжигании мазута факельным способом, путем его распыления с помощью форсунок. Во избежание конденсации паров температура на выходе из сушильного барабана поддерживается 90-180°С.
Отработанные дымовые газы, содержащие пыль KCl, отсасываются дымоотсосом и подвергаются двухстадийной очистке:
1 стадия – сухая очистка в циклонах;
2 стадия – мокрая очистка в комбинированном очистителе пыли.
В качестве орошающей жидкости используется техническая вода.
|
Дымовые газы после двух стадий очистки выбрасываются а атмосферу через 2 дымовые трубы: титановую – 80м, текстолитовую – 84м.
Приготовление реагентов
Режим приготовления реагентов (рабочих растворов) определяется режимными картами.
Облагораживание гранул.
Дополнительная обработка (облагораживание) гранулята предусматривает:
а) повышение прочности гранул;
б) улучшение гранулометрического состава;
в) снижение влагопоглощения.
Дополнительная обработка состоит из следующих стадий:
а) обработка водой с последующим перемешиванием в двухвальном смесителе;
б) сушка и охлаждение в аппаратах "кипящего слоя".
Гранулят выгружается на ленточный конвейер и в склады готовой продукции. Гранулят получается обеспыленный, окатанный и охлажденный до 60°.
Погрузка калия хлористого.
В погрузочно-складское хозяйство готовой продукции входят:
1. Два здания погрузки, оборудованные приемными бункерами, ленточными питателями и подвижными телескопическими течками, для загрузки вагонов через верхние токи;
2. Подвесные и подземные галереи, оборудованные 2 линиями автоматизированных ленточных конвейеров.
3. Склады арочного типа:
а) N2 – для мелкого калия хлористого с тремя кратцер-кранами, вместимость 18000 т;
б) N 3,4,5 – для гранулированного калия хлористого с кратцер-кранами, вместимостью склада №3 – 25000т; склада №4 – 30000т; склада №5 - 20000 т;
в) N 6 – для мелкого калия хлористого с портальным кратцер-краном, вместимостью 15000т.
Заполнение складов производится ленточными конвейерами с разгрузочной тележкой.
Обеспыленный и непылящий мелкий калий хлористый со склада №2 по системе конвейеров поступает на погрузку №1.
С целью снижения пылимости продукты обрабатываются пылеподавителями.
Мелкий KCl со склада №6 по системе конвейеров поступает на погрузку №2 и через телескопические течки направляется в железнодорожные вагоны.
Гранулированный KCl со складов №3,4,5 направляется на погрузку через цех классификации, где на ситах классифицируется на два продукта. Товарный гранулят посредством системы конвейеров и загрузочный течек загружается в железнодорожные вагоны. Подрешетный продукт (отсев) в количестве до 10% направляется вновь в цех грануляции и на погрузку.
Требования, предъявляемые к техническому обслуживанию и ремонту стержневой мельницы МСЦ 3,2 – 4,5
В течении первых десяти дней работы мельницы после ремонта следует останавливать не реже одного раза в смену и проверять состояние зацепления (контакт зубьев, отсутствие задиров), уплотнений, крепление венца, брони. Устранять выявленные недостатки.
Не допускать перегруза мельницы мелющими телами и работы мельницы при недостаточном питании измельчаемым материалом.
Планово-предупредительный осмотр привода производить не реже одного раза в шесть месяцев. Во время плановых осмотров проверяется параллельность соосность вал-шестерни с валом электродвигателя.
В соответствии с графиком плановых осмотров необходимо:
- следить за износом футеровки и не допускать случаев эксплуатации мельницы при неполном износе даже отдельных футеровочных плит;
- не допускать смещения футеровочных плит в барабане от их нормального положения;
- не допускать течи масла через в уплотнениях коренных подшипников, своевременно производить обтяжку и замену уплотнений;
- следить за состоянием и степенью износа баббита коренных подшипников, при зазоре между цапфой и корпусом тодшипника на зоне установки уплотнений менее 0,5 мм корпус подшипника заменить.
При работе мельниц необходимо следить за состоянием привода, не допуская его пульсации и ударов. Шум, создоваемый открытой зубчатой передачей, должен быть ровным, без периодического усилия и ослабления.
Не допускается перегрев коренных подшипников мельницы выше 60 ºС, так как повышение температуры выше нормы может привести к расплавлению баббитовых вкладышей.
СПЕЦИАЛЬНАЯ ЧАСТЬ
ЭКОНОМИЧЕСКАЯ ЧАСТЬ
5.1 Составление графика планово-предупредительных ремонтов
На предприятиях минеральных удобрений и химической промышленности проводиться эксплуатация, техническое обслуживание и ремонт оборудования на основе системы планово-предупредительных ремонтов ППР.
В основе составления графика планово-предупредительных ремонтов (ППР) лежат утвержденные ремонтные нормативы, отраженные в справочнике «Система технического обслуживания и ремонта оборудования» и структура ремонтного цикла.
Ремонтный цикл – это время работы оборудования между двумя капитальными ремонтами.
Структура ремонтного цикла – это количество и последовательность входящих в ремонтный цикл ремонтов и осмотров.
Для составления структуры ремонтного цикла необходимо определить:
1 Количество текущих ремонтов по формуле:
Дк
Т= ------ - К (5.1)
Дт
Где Дк – продолжительность работы в часах между капитальными ремонтами,
Дт – продолжительность работы в часах между текущими ремонтами
К – количество капитальных ремонтов, К=1.
2 Длительность ремонтного цикла определяется по формуле:
Дк
Ц= ------- (5.2)
8640
Где 8640 – общее число рабочих часов оборудования в год.
3 Время простоя оборудования во всех видов ремонтов определяется по формулам:
Ппк = Пк · Ргод.к (5.3)
Ппт = Пт· Ргод.т (5.4)
Пп = Ппк + Ппт (5.5)
где Пк и Пт – время простоя оборудования в капитальном и текущем ремонтах соответственно, в часах,
Ргод.к и Ргод.т – количество капитальных и текущих ремонтов соответственно.
4 Эффективный фонд времени работы оборудования определяется по формуле:
Фэф = 8760 – Пп (5.6)
Где 8760 – календарный годовой фонд времени в часах,
Пп – время простоя оборудования во всех видах ремонтов, в часах.
Приведем пример расчета:
1. Т=Дк / Дт- 1=5400 / 720 – 1=7 текущих ремонтов;
2. Ц=Дк / 8640=5400/ 8640=0,6 года;
3. Ппт=Пт·Ргод.т=7·8=56 часов;
4. Ппк=Пк·Ргод.к=72 · 1=72 часов;
5. Пп=Ппк+Ппт=56+72=128 часов;
6. Фэф=8760 – Пп=8760 – 128=8632 часов.
Таблица 5.1 – Годовой график ППР
Наименование оборудования | Норма времени непрерывной работы между ремонтами и время простоя в ремонте, часы | Условное обозначение ремонта | Годовой простой в ремонтах, часы (Пп) | Эффективный фонд времени работы оборудования, часы (Фэф) | ||||||||||||||
Дт | Пг | Дк | Пк | 1 | 2 | 3 | 4 | 5 | 6 | 7 | 8 | 9 | 10 | 11 | 12 | |||
Стержневая мельница МСЦ 3,2х4,5 | 720 | 8 | 5400 | 72 | т | т | т | т | т | т | к | т | т | т | т | т | 128 | 8632 |
ЛИТЕРАТУРА
1. Печковский В.В., Александрович Х.М. Технология калийных удобрений. – М.: Высшая школа, 1968
2. Инструкция по эксплуатации 3018 ИЭ, С.: 1990
3. Технологический регламент 2РУ – С.: 2006
4. Ермаков В.И. Шейн В.С. Ремонт и монтаж хим. оборудования. – М.: Химия, 1981
5. Тухто А.А. Правила охраны и безопасности труда при переработке соляных месторождений. – М.: ЦОТЖ, 1997.
6. Мельница стержневая МСЦ – 3200 х 4500. технические условия на капитальный ремонт. – Мн. 1990
7. Донченко А.С., Донченко В.А. Справочник механика рудообогатительной фабрики. – М.: Недра 1986
8. Зуев В.И. и Никитин А.В. Практикум по экономике, организации и планированию в горной промышленности: Учебное пособие для техникумов. – М.: НЕДРА, 1990
9. Зайцев Н.Л. Экономика промышленного предприятия. Практикум: Учебное пособие. – М.: ИНФРА-М, 2000
СОДЕРЖАНИЕ
Введение
1. Общая часть
1.1 Краткая характеристика и сравнение способов производства КСl из сильвинита
1.2 Характеристика исходного сырья и готовой продукции
1.3 Описание технологического процесса производства хлористого калия по фабрике
1.4 Требования, предъявляемые к техническому обслуживанию и ремонту технологического оборудования
1.4.1 Требования, предъявляемые к техническому обслуживанию и ремонту стержневой мельницы МСЦ 3,2х4,5
1.5 Порядок сдачи оборудования в ремонт и прием оборудования после ремонта
2. Специальная часть
2.1 Описание технологического процесса отделения.
2.2 Назначение, устройство, принцип работы и техническая характеристика стержневой мельницы МСЦ 3200х4500
2.3 Технологический процесс капитального ремонта аппарата.
2.3.1 Составление необходимой документации на ремонт
2.3.2 Ремонт отдельных деталей аппарата.
2.4 Технологический расчет аппарата
2.5 Механический расчет аппарата
3. Правила безопасности при эксплуатации и проведении ремонтных работ
4. Охрана окружающей среды на калийных предприятиях
5. Экономическая часть.
5.1 Составление графика ППР
5.2 Расчет затрат на основные и вспомогательные материалы.
5.3 Расчет затрат на электроэнергию
5.4 Расчет затрат на амортизацию
5.5 расчет заработной платы и отчислений от фонда оплаты труда
5.6 Составление сметы затрат
5.7 Основные технико-экономические показатели
Литература
ВВЕДЕНИЕ
Рациональное использование минерально-сырьевых ресурсов, максимальное извлечение всех ценных компонентов из руд – главная задача обогатительной науки и практики.
Республиканское унитарное предприятие “ Производственное объединение “Беларуськалий” – один из крупнейших в мире и самый крупный на территории СНГ производитель и поставщик калийных минеральных удобрений.
Функционируя на базе Старобинского месторождения калийных солей ПО “Беларуськалий” включает в себя четыре рудоуправления, вспомогательные цеха и обслуживающие подразделения, в которых занято около 20 тысяч человек.
В состав каждого рудоуправления входят рудник для добычи калийной руды и обогатительная фабрика для ее переработки и выпуска минеральных калийных удобрений в форме мелкозернистого, мелкокристаллического и гранулированного концентрата хлористого калия, а также соли калийной смешанной. Кроме того, объединение выпускает техническую, пищевую и кормовую поваренную соль.
Располагая достаточной природной сырьевой базой, высоким производительным потенциалом, высококвалифицированными кадрами рабочих и специалистов, объединение имеет все возможности для дальнейшего повышения эффективности производства, внедрения новой техники и совершенствования технологических процессов, обеспечения высокого качества всех видов работ и конечного продукта.
Современные обогатительные фабрики - высокомеханизированные предприятия. Они оснащены большим числом сложных установок, машин и механизмов, составляющих в совокупности непрерывные технологические линии. Все оборудование этих линий связано между собой определенными технологическими зависимостями и предназначено для переработки или транспортировки руды и продуктов обогащения в едином технологическом процессе.
Эксплуатация оборудования в таких линиях предусматривает: контроль и регулировку производительности машин, контроль состояния смазочных систем, температуры трущихся частей механизмов и обмоток электродвигателей, предотвращение аварийных ситуаций, устранение возникающих неисправностей, пуск и останов оборудования.
Для облагораживания или увеличения поверхности фазового контакта минерала, применяемого в том или ином процессе, его подвергают измельчению. На разных производствах измельчают твердое минеральное сырье, полуфабрикаты, а также готовую продукцию. Измельчаемые материалы по своей структуре могут быть твердыми, мягкими, хрупким, вязкими, а также обладать различными химическими свойствами. От свойств материала и заданной степени измельчения зависят продолжительность процесса и тип измельчающего оборудования. Отличают следующие виды измельчения: дробление крупное (размер кусков после измельчения 250 мм); дробление среднее (20мм); дробление мелкое (1мм); помол грубый (0,1— 0,004мм); помол средний (0,005—0,015 мм); помол тонкий (0,001— 0,005мм); помол коллоидный (менее 0,001 мм).
Технологическое назначение операций дробления и измельчения заключается в том, чтобы раскрыть минералы при максимально возможной крупности, при минимальном переизмельчении, т.е. осуществить принцип «не дробить ничего лишнего».
Кроме того, от обслуживающего персонала требуется четкое выполнение графиков чистки и ремонта оборудования, работающего в тяжелых условиях непрерывного производства. Вследствие воздействия высоких механических нагрузок и химически агрессивной среды узлы и детали машин подвергаются высокоаброзивному износу. В некоторых случаях износ узлов машин влияет на качество продуктов обогащения.
Квалифицированное обслуживание оборудования обогатительной фабрики невозможно без знания устройства, принципа действия и возможных неисправностей машин и аппаратов.
Одним из важнейших условий эффективного использования промышленного оборудования, увеличения срока его службы и надежности в работе является правильная эксплуатация и высококачественный ремонт. Эти решаются с помощью разработанной в нашей стране системы планово – предупредительного ремонта (ППР), которая регламентирует периодичность, состав и объем работ по техническому обслуживанию и ремонту оборудования. В ремонтном деле важную роль играет слесарь, который должен иметь хорошую техническую подготовку. Он должен знать назначение и устройство сборочных единиц оборудования, распознавать признаки и причины износа деталей различных механизмов и владеть современными способами восстановления изношенных частей машины.
Постоянная работоспособность всякого оборудования, поддерживается его правильной эксплуатации и своевременным и качественным ремонтом. Поэтому бесспорно большое значение ремонтной службы для нормальной жизнедеятельности любого предприятия.
Повышение эффективности обогатительного производства требует разработки и внедрения новых технологических процессов и оборудования, обеспечивающих получения высоких технико-экономических показателей в условиях постепенного снижения качества исходного сырья. Технологические процессы должны совершенствоваться в направлении сокращения энергозатрат и материалов на производство концентратов, обеспечения наиболее полного использования в народном хозяйстве всех компонентов сырья, устранения вредного влияния обогатительного производства на окружающую среду.
ОБЩАЯ ЧАСТЬ
Краткая характеристика и сравнение способов производства кс i из сильвинита
Флотация представляет собой метод обогащения полезных ископаемых, основанный на различии физико-химических свойств поверхности минералов, выражающимся в различной способности минералов смачиваться водой. Находясь в тонко-измельчонном состоянии в водной среде, частицы одних минералов не смачиваются водой, а прилипают к содержащимся в воде пузырькам воздуха и всплывают на поверхность, в то время как частицы других минералов смачиваются водой и тонут в ней или находятся во взвешенном состоянии.
Галургический способ производства основан на различной растворимости КСI u NaCI в воде с повышением температуры. С повышением температуры растворимость КСI резко повышается в то время как растворимость NaCl незначительна и при температуре около 100ºС наоборот из раствора наблюдается выпадение кристаллов NaCI. На процесс растворения КСI оказывает влияние примеси присутствующие в руде и в основном МgCI2 и н.о. (глинисто-карбонатная фракция крупностью менее 0.01 мм или 10 мкр). С повышением в руде этих примесей растворимость КСI снижается.
Каждый метод обогащения имеет преимущества и недостатки, появляющиеся в большей или меньшей степени в зависимости от состава руды. Флотационный метод характеризуется малым расходом тепла и воды, возможностью ведения процесса при нормальной температуре щелоков с получением готового продукта в виде природных зерен крупностью до 1-3 мм. К недостаткам его следует отнести более низкое качество готовой продукции, зависящее от крупности вкрапленности сильвина в руде, повышенный расход электроэнергии, необходимость применения для флотации KCl дорогих реагентов - первичных алифатических аминов С17 – С20.
Химический метод требует меньшего расхода электроэнергии, позволяет получать готовый продукт требуемого качества, однако при этом значительно возрастает расход тепла, процесс ведется при температуре щелоков 80 – 100 С, что повышает коррозию оборудования и ухудшает санитарные условия труда. Для получения кристаллов KCl с верхним пределом крупности 1 мм требуется применение дорогостоящего оборудования. При содержании MgCl2 в руде свыше 0,2% снижается селективность кристаллизации KCl, и технологическая схема требует дополнение операцией выпарки щелоков для вывода MgCl2 из процесса в виде насыщенного хлормагниевого щелока.
Сопоставление извлечения KCl в готовый продукт и расхода руды по химическому и флотационному методам переработки калийных руд показало, что при химическом методе наблюдается более высокая степень использования сырья, особенно при обогащении руд с высоким содержанием н.о.
В связи с этим наиболее рациональные методы переработки выбирались не только по затратам на обогащение, но и с учетом разницы в расходе руды для обеспечения заданной мощности фабрики. Галургический метод принимался как более эффективный в случаях, когда затраты на обогащение по этому методу оказывались ниже или равны затратам на флотационное обогащение.
|
|
Архитектура электронного правительства: Единая архитектура – это методологический подход при создании системы управления государства, который строится...
Эмиссия газов от очистных сооружений канализации: В последние годы внимание мирового сообщества сосредоточено на экологических проблемах...
Типы оградительных сооружений в морском порту: По расположению оградительных сооружений в плане различают волноломы, обе оконечности...
Таксономические единицы (категории) растений: Каждая система классификации состоит из определённых соподчиненных друг другу...
© cyberpedia.su 2017-2024 - Не является автором материалов. Исключительное право сохранено за автором текста.
Если вы не хотите, чтобы данный материал был у нас на сайте, перейдите по ссылке: Нарушение авторских прав. Мы поможем в написании вашей работы!