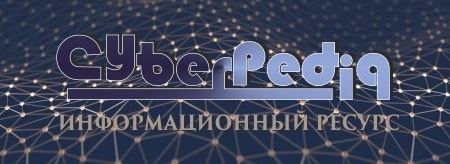
Индивидуальные очистные сооружения: К классу индивидуальных очистных сооружений относят сооружения, пропускная способность которых...
Автоматическое растормаживание колес: Тормозные устройства колес предназначены для уменьшения длины пробега и улучшения маневрирования ВС при...
Топ:
Комплексной системы оценки состояния охраны труда на производственном объекте (КСОТ-П): Цели и задачи Комплексной системы оценки состояния охраны труда и определению факторов рисков по охране труда...
Установка замедленного коксования: Чем выше температура и ниже давление, тем место разрыва углеродной цепи всё больше смещается к её концу и значительно возрастает...
Эволюция кровеносной системы позвоночных животных: Биологическая эволюция – необратимый процесс исторического развития живой природы...
Интересное:
Берегоукрепление оползневых склонов: На прибрежных склонах основной причиной развития оползневых процессов является подмыв водами рек естественных склонов...
Влияние предпринимательской среды на эффективное функционирование предприятия: Предпринимательская среда – это совокупность внешних и внутренних факторов, оказывающих влияние на функционирование фирмы...
Что нужно делать при лейкемии: Прежде всего, необходимо выяснить, не страдаете ли вы каким-либо душевным недугом...
Дисциплины:
![]() |
![]() |
5.00
из
|
Заказать работу |
|
|
Окончательная термическая обработка режущих инструментов заключается в трехступенчатой закалке и трехкратном отпуске.
Процесс закалки состоит в медленном нагреве инструмента, для предохранения от возникновения значительных внутренних напряжений, делается два подогрева. Первый производится в нагревательном колодце до температуры 500°С и второй - в соляной ванне до температуры 850°С.
При подогреве до 800-850°С из исходной структуры перлит + карбиды образуется структура аустенит + карбиды. Но аустенит при данной температуре малолегированный, т.к. основная масса карбидов находится вне твердого раствора. Для увеличения легированности аустенита производится окончательный нагрев до высокой температуры (закалки). Закалка производится в высокотемпературной соляной ванне до 1300°С.
Необходимость быстрого нагрева связана со способностью быстрорежущей стали легко окислятся при высоких температурах. Структура при 1000-1300°С аустенит + карбиды, т.е. такая же как и при 850°С но в связи с тем, что при нагреве в данном температурном интервале происходит растворение карбидов, аустенит при 1300°С получается значительно более легированным.
Полного растворения карбидов при нагреве до максимальной температуры не происходит, и крупные первичные карбиды остаются вне раствора. Выдержку при высокой температуре делают очень незначительную, только такую, которая необходима для прогрева рабочего объема инструмента.
Охлаждение нагретой быстрорежущей стали производиться в масляном закалочном баке. Охлаждение в масле делает инструмент более стойким в работе.
При охлаждении (закалке) происходит распад аустенита с образованием мартенсита. Но не весь аустенит распадается, а часть его (25-30%) сохраняется в виде остаточного аустенита. Поэтому структура после закалки представляет собой мартенсит закалки + карбиды + остаточный аустенит. Образующийся мартенсит настолько мелко игольчатый, что по внешнему виду структура закаленной быстрорежущей стали кажется состоящей только из аустенита и карбидов. Образование мартенсита при закалке происходит в определенном температурном интервале. Температуры начала (Мн) и конца (Мк) мартенситного превращения понижаются с повышением температуры закалки. При закалке от температуры выше 1100°С точка Мк располагается при температурах ниже нуля.
|
) Технология окончательной термической обработки фрезы дисковой.
первый подогрев инструмента производится в нагревательном газовом колодце до температуры 500°С. Продолжительность нагрева 35 мин
второй подогрев производится в соляной ванне до температуры 800-850°С. Продолжительность нагрева 15 мин
окончательный нагрев осуществляется в высокотемпературной соляной ванне до температуры 1210-1230°С. Продолжительность нагрева и выдержки 15 мин
охлаждение в масле
очистка инструмента.
Для стали 11М5Ф проводят закалку с трехступенчатым подогревом до температуры 1210-1230оС. Высокая температура закалки проводится для более полного растворения вторичных карбидов и получения при нагреве аустенита, высоколегированного хромом, молибденом и ванадием.
При трехкратном подогреве стали 11М5Ф, обеспечивается более равномерный прогрев стали и возможность предотвращения образования трещин.
Структура стали 11М5Ф после закалки представляет собой высоколегированный мартенсит, содержащий 0,3-0,4% нерастворенных-избыточных карбидов и остаточного аустенита примерно 28-34%. Остаточный аустенит понижает режущие свойства стали, и поэтому его присутствие в готовом инструменте не допустимо.
) Технология окончательной термической обработки сверла
Режущая часть:
первый подогрев инструмента производится в нагревательном газовом колодце до температуры 500°С. Продолжительность нагрева и выдержка 30 мин
|
второй подогрев производится в соляной ванне до температуры 800-850°С. Продолжительность нагрева и выдержка 10 мин.
окончательный нагрев производится в высокотемпературной соляной ванне при температуре 1200-1230°С. Продолжительность нагрева и выдержки 8-9 мин
охлаждение в масле
очистка инструмента.
Хвостовая часть:
погружение в электрическую соляную ванну СВГ-2.3.5/8,5 нагретую до температуры 820-840°С. Выдержка при температуре нагрева 15 мин.
охлаждение в 5% водном растворе NaCl до 150-200°С.
охлаждение на воздухе.
) Технология окончательной термической обработки для метчика
Режущая часть:
первый подогрев инструмента производится в нагревательном газовом колодце до температуры 500°С. Продолжительность нагрева и выдержка 30 мин
второй подогрев производится в соляной ванне до температуры 800-850°С. Продолжительность нагрева и выдержка 10 мин
окончательный нагрев производится в высокотемпературной соляной ванне при температуре 1200-1230°С. Продолжительность нагрева и выдержки 8-9 мин
охлаждение в масле
очистка инструмента.
Хвостовая часть:
погружение в электрическую соляную ванну СВГ-2.3.5/8,5 нагретую до температуры 820-840°С. Выдержка при температуре нагрева 15 мин.
охлаждение в 5% водном растворе NaCl до 150-200°С.
охлаждение на воздухе.
При нагреве инструментов нужно принимать все меры против обезуглероживания стали, которое в данном случае может быть очень сильным из-за высокой температуры нагрева. Поэтому соляные ванны должны быть хорошо раскислены.
Выдержка при температуре закалки обеспечивает растворение в аустените частиц карбидов в пределах их растворимости и прогрев рабочего объема инструментов. При выдержке происходит увеличение зерен аустенита и увеличение количества растворенных карбидов.
Охлаждение проводится в масле, но перед этим необходимо подстудить на воздухе до температуры 900-1000оС (желтый цвет каления) и после этого опустить в масло. При охлаждении в масле без подстуживания могут получиться закалочные трещины. Охлаждение в масле осуществляется до температуры 150-200оС, после чего закаленный инструмент вынимают из закалочного бака и дают остыть на спокойном воздухе.
После закалки быстрорежущая сталь должна быть обязательно подвергнута отпуску. При нагреве до 100-200°С уменьшается степень тетрагональности мартенсита. В интервале 300-400°С наблюдается снижение твердости, что объясняется снятием внутренних напряжений, возникших в процессе закалки.
|
При дальнейшем повышении температуры отпуска твердость повышается, достигая максимума при 550°С.
По сравнению с твердостью после закалки твердость после отпуска при 550°С получается более высокой. Эта максимальная высокая твердость способна сохранятся при последующих нагревах во время работы инструмента и обусловливает его теплостойкость.
В результате отпуска происходит превращение остаточного аустенита в мартенсит.
Характерной особенностью отпуска быстрорежущий стали, является то, что полученный в результате закалки остаточный аустенит превращается в мартенсит не при нагреве и не при выдержке при отпуске, а во время охлаждения. Такой характер превращения носит название вторичной закалки быстрорежущей стали. Мартенсит отпуска (полученный при распаде остаточного аустенита при отпуске) отличается от мартенсита закалки тем, что в результате распада остаточного аустенита образуется не первичный мартенсит, а вторичный, кроме того, в связи с обеднением остаточного аустенита легирующими элементами образующейся мартенсит будет также менее легирован по сравнению с мартенситом закалки. В связи с большой устойчивостью остаточного аустенита лучший результат в отношении более легкого и полного его распада с получением более высоких режущих свойств дает трехкратный отпуск.
1) Технология отпуска фрезы дисковой:
- двухкратный нагрев производится в печи шахтной электрической СШЗ - 6.6/7 до температуры 580°С. Продолжительность каждого отпуска 20 мин.
охлаждение на воздухе.
Стандартный отпуск безвольфрамовой быстрорежущей стали двухкратный при температуре 520оС по 1 часу. Однако использование многократного отпуска с выдержкой по 1 часу (плюс время, необходимое для прогрева садки) с обязательным охлаждением между отпусками до нормальной температуры в производственных условиях усложняет цикл термообработки. С целью сокращения цикла рекомендуется провести высокотемпературный сокращённый отпуск. Для стали 11М5Ф применяем двухкратный отпуск при температуре 580оС и продолжительность каждого отпуска 20 мин. При таких отпусках достигается более высокая вторичная твёрдость, сопротивление изгибу, улучшается шлифуемость за счёт меньшей шероховатости поверхности по сравнению с этими характеристиками после стандартных отпусков.
|
Технология отпуска сверла
Режущая часть:
трехкратный нагрев производится в печи шахтной электрической СШЗ - 6.6/7 до температуры 540-560°С. Продолжительность каждого отпуска 1-1,5 ч
охлаждение на воздухе.
Хвостовая часть:
нагрев до температуры 450-500°С в электродной селитровой ванне. Продолжительность отпуска 30-40 мин
охлаждение на воздухе.
Технология отпуска метчика
Режущая часть:
трехкратный нагрев производится в печи шахтной электрической СШЗ - 6.6/7 до температуры 540-560°С. Продолжительность каждого отпуска 1-1,5 ч
охлаждение на воздухе.
Хвостовая часть:
нагрев до температуры 450-500°С в электродной селитровой ванне. Продолжительность отпуска 30-40 мин
охлаждение на воздухе.
ВЫВОДЫ
В результате прохождения практики получены навыки:
применения безопасных приёмов обслуживания оборудования и приборов лаборатории, использования индивидуальных средств защиты, первичных средств тушения пожара;
работы в изготовлении образцов для металлографических исследований; работы с оборудованием и приборами; в проведении испытаний для определения свойств материала;
применения полученных теоретических знаний к решению конкретных задач в условиях реального производства;
использования научно-технической литературы и информации;
безопасной работы на технологическом оборудовании.
СПИСОК ИСПОЛЬЗОВАННОЙ ЛИТЕРАТУРЫ
1. Луганские локомотивы: люди, годы, факты. Кол. авторов: - Луганск, 1996. - 403 с. (в полит.), - вкладки - 40 с.
. Гуляев А.П. Металловедение. М.: Металлургия, 1978. - 646 с.
. Золоторевский В.С. Механические свойства металлов. М.: Металлургия, 1983. - 352 с.
. Лившиц Б.Г., Крапошин В.С., Линецкий Я.Л. Физические свойства металлов и сплавов. М.: Металлургия, 1980. - 320 с.
. Приборы для неразрушающего контроля материалов и изделий. Справочник. / М.: Машиностроение, 1986. - 484 с.
. Райцес В.Б., Литвин В.М. Техника безопасности в термических цехах. К.: Техника, 1988. - 160 с.
|
|
Эмиссия газов от очистных сооружений канализации: В последние годы внимание мирового сообщества сосредоточено на экологических проблемах...
Индивидуальные и групповые автопоилки: для животных. Схемы и конструкции...
Автоматическое растормаживание колес: Тормозные устройства колес предназначены для уменьшения длины пробега и улучшения маневрирования ВС при...
Кормораздатчик мобильный электрифицированный: схема и процесс работы устройства...
© cyberpedia.su 2017-2024 - Не является автором материалов. Исключительное право сохранено за автором текста.
Если вы не хотите, чтобы данный материал был у нас на сайте, перейдите по ссылке: Нарушение авторских прав. Мы поможем в написании вашей работы!